退补料流程
物料退补管理制度
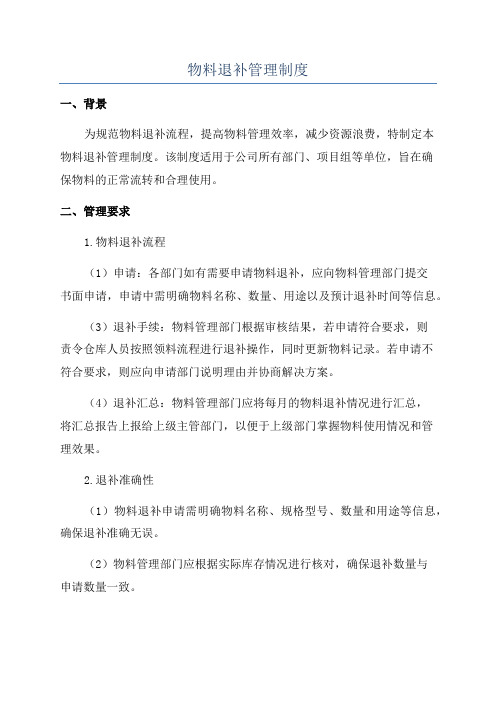
物料退补管理制度一、背景为规范物料退补流程,提高物料管理效率,减少资源浪费,特制定本物料退补管理制度。
该制度适用于公司所有部门、项目组等单位,旨在确保物料的正常流转和合理使用。
二、管理要求1.物料退补流程(1)申请:各部门如有需要申请物料退补,应向物料管理部门提交书面申请,申请中需明确物料名称、数量、用途以及预计退补时间等信息。
(3)退补手续:物料管理部门根据审核结果,若申请符合要求,则责令仓库人员按照领料流程进行退补操作,同时更新物料记录。
若申请不符合要求,则应向申请部门说明理由并协商解决方案。
(4)退补汇总:物料管理部门应将每月的物料退补情况进行汇总,将汇总报告上报给上级主管部门,以便于上级部门掌握物料使用情况和管理效果。
2.退补准确性(1)物料退补申请需明确物料名称、规格型号、数量和用途等信息,确保退补准确无误。
(2)物料管理部门应根据实际库存情况进行核对,确保退补数量与申请数量一致。
(3)物料管理部门应在退补操作完成后进行盘点,将退补情况记录在盘点表中,以便于核准和管理。
3.退补监督与考核(1)上级主管部门应定期对物料退补情况进行抽查,以确保操作的合规性和规范性。
(2)物料管理部门应建立完善的物料追踪和监控机制,及时发现退补过程中的问题和隐患,并提出改进意见和措施。
(3)根据物料退补情况和管理效果对物料管理部门进行考核,将考核结果作为部门绩效考核的重要参考依据。
4.退补使用原则(1)退补的物料应按照合理用途进行使用,不得私自挪用或转借。
(2)如需更换或调整退补物料的用途,需事先向物料管理部门申请并获得批准。
(3)不符合质量要求的物料不得退补或使用,应及时通知供应商或退回原仓库。
三、制度执行1.对于违反本制度的行为,物料管理部门有权进行纠正,并向上级主管部门汇报处理情况。
2.上级主管部门有权对违规行为进行处理,并视情况给予相应的纪律处分。
3.物料管理部门应定期对本制度进行评估和修订,确保其符合公司实际需要和管理要求。
退补料管理规定退补料工作流程

1.0目的为了确保工厂的退补料工作顺利实施开展,保证退料能及时供给生产线,加速订单的生产进程,按期供货给客户,特制定本规定。
2.0范围适用于本公司的退补料作业3.0定义3.1来料不良3.1.1经品质部判定供应商来料不良;3.1.2因存放条件太差,仓库发料时发现变质、破损不良物料;3.1.3生产现场发现不良物料。
3.2制程产生不良3.2.1在生产过程中造成物料的损坏导致的不良。
4.0工作职责4.1品质部4.1.1负责来料的检验,对检验的不良数据做出判定;4.1.2将检验出的不良参数反馈到相关部门,并跟进不良处理的结果;4.1.3对生产制程中出现的不良物料由做出判定何种原因造成,分清权责,要求生产部门其分开标识、摆放;4.1.4不良物料(五金/硅胶/电源线/外购)经由品质部IQC检验确认后方可退料;塑胶不良物料由装配IPQC确认(包括确认何种原因造成)后方可退料。
4.2采购部4.2.1负责对品质部判定出的来料不良进行处理;4.2.2负责退料相关程序的协调与处理;4.2.3要求供应商及时将退货给予补回;4.2.4对于在生产制程中发现的来料的不良要及时进行处理;4.2.5对生产车间损坏、遗失的补料,协助及时购买。
4.3生产部(各车间)4.3.1将品质部判定出的不良品作好标识并返工;4.3.2在制程过程发现来料不良的物料,经品质部判定后退仓处理;4.3.3对上序退料返工,相应的物料供应部门应在8小时内将退料补齐;4.3.4在生产过程中因本部门原因导致的物料不良损坏,应开据补料单进行补料;4.3.5因存放条件、库存时间久导致的不良,相应的部门应积极配合,及时处理不良物料;4.3.6对生产车间损坏、遗失的补料要及时协助补回。
4.4仓库4.4.1将品质部判定出的不良物料进行的标识,区分存放;4.4.2督促采购和相对应的物料供应部门及时将不良物料退回;4.4.3接收车间经品质判定的不良物料的退仓。
4.5 PMC部4.5.1跟进车间不良物料的处理结果;4.5.2督促相关部门对退料的补回的情况;4.5.3对不良物料的补料情况时进行统计汇总;4.5.4当物料来料不良时,根据生产的上线时间和物料的不良程度;做出是否可挑选的命令。
生产车间退补料管理制度

一、目的为了规范生产车间退补料管理,提高物料利用率,确保生产顺利进行,特制定本制度。
二、适用范围本制度适用于公司生产车间内所有退补料活动。
三、退补料管理原则1. 退补料活动应遵循“及时、准确、节约、合理”的原则。
2. 退补料活动应确保产品质量,不得影响生产进度。
3. 退补料活动应严格控制成本,降低损耗。
四、退补料流程1. 退料申请(1)生产过程中,如因原材料、辅料、半成品等原因造成不合格,需退料的,由操作员填写《退料申请单》。
(2)《退料申请单》经组长审核后,报生产主管审批。
(3)生产主管审批通过后,将《退料申请单》及退料物品送至仓库进行退料。
2. 补料申请(1)生产过程中,如因原材料、辅料、半成品等原因造成短缺,需补料的,由操作员填写《补料申请单》。
(2)操作员将《补料申请单》报组长审核,组长审核通过后,报生产主管审批。
(3)生产主管审批通过后,将《补料申请单》及所需补料物品送至仓库进行补料。
3. 退补料审核(1)仓库管理人员对退补料申请单进行审核,确认退补料物品与申请单相符。
(2)仓库管理人员对退补料物品进行验收,确保质量合格。
4. 退补料入库(1)仓库管理人员将退补料物品进行入库,并做好记录。
(2)入库后,仓库管理人员将《退料申请单》及《补料申请单》返回给操作员。
五、退补料责任1. 操作员负责填写退补料申请单,确保信息准确。
2. 组长负责审核退补料申请单,确保退补料活动合理。
3. 生产主管负责审批退补料申请单,确保退补料活动符合公司规定。
4. 仓库管理人员负责退补料物品的验收和入库,确保质量合格。
六、附则1. 本制度由生产部负责解释。
2. 本制度自发布之日起实施。
3. 如有未尽事宜,由公司另行规定。
领料、退补料管理执行办法
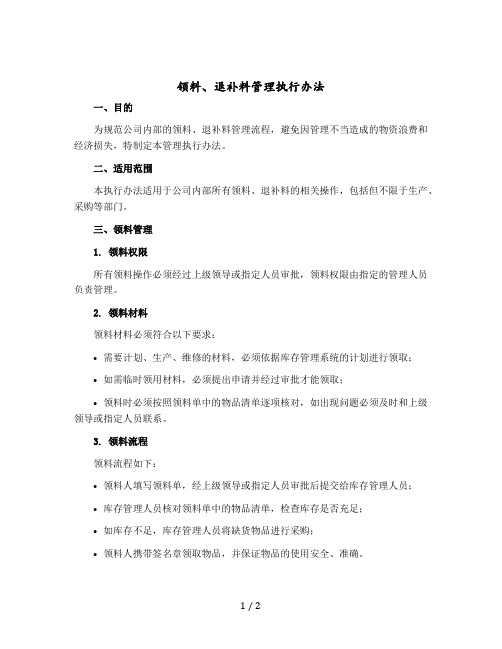
领料、退补料管理执行办法一、目的为规范公司内部的领料、退补料管理流程,避免因管理不当造成的物资浪费和经济损失,特制定本管理执行办法。
二、适用范围本执行办法适用于公司内部所有领料、退补料的相关操作,包括但不限于生产、采购等部门。
三、领料管理1. 领料权限所有领料操作必须经过上级领导或指定人员审批,领料权限由指定的管理人员负责管理。
2. 领料材料领料材料必须符合以下要求:•需要计划、生产、维修的材料,必须依据库存管理系统的计划进行领取;•如需临时领用材料,必须提出申请并经过审批才能领取;•领料时必须按照领料单中的物品清单逐项核对,如出现问题必须及时和上级领导或指定人员联系。
3. 领料流程领料流程如下:•领料人填写领料单,经上级领导或指定人员审批后提交给库存管理人员;•库存管理人员核对领料单中的物品清单,检查库存是否充足;•如库存不足,库存管理人员将缺货物品进行采购;•领料人携带签名章领取物品,并保证物品的使用安全、准确。
4. 领料单管理领料单应当在领取物品后及时存档管理,以备审计需要。
四、退补料管理1. 退补料申请如出现库存过剩或者是材料变质,必须及时申请退补料,所有退补料申请必须经过上级领导或指定人员审批才可进行。
2. 退补料流程退补料流程如下:•退补料人填写退补料单,经上级领导或指定人员审批后提交给库存管理人员;•库存管理人员核对退补料单中的物品清单,检查库存是否充足;•如库存充足,库存管理人员收回物品并进行相应处理;•如库存不足,库存管理人员将缺货物品进行采购。
3. 退补料单管理退补料单应当在收回物品后及时存档管理,以备审计需要。
五、其他注意事项•领料、退补料人应当妥善处理相关物品,保证物品的使用安全、准确。
•库存管理人员应当经常开展库存清点、差异分析等工作,保证库存数据的准确性。
•领料、退补料操作应当遵守公司有关规定和操作流程,如发现违规者视情节轻重进行相应处理。
以上就是本执行办法的全部内容,如有其他需要请指出。
物料退补管理制度

物料退补管理制度物料退补管理制度一、引言物料退补是指对于企业生产过程中产生的废品、退货、报废物料等进行归还或补充的管理流程。
为了规范和优化物料退补管理工作,提高物料利用率和减少浪费,制定本《物料退补管理制度》。
二、管理目标1. 管理物料退补流程,确保物料回收、补充工作的规范性和及时性;2. 提高物料利用率,减少物料浪费;3. 持续改进物料退补管理流程,提高工作效率。
三、适用范围本制度适用于企业内所有部门和员工。
四、物料退补流程1. 提交退补申请- 员工在发现物料需要退补时,填写《物料退补申请单》,明确物料名称、规格、数量等信息,并注明退补原因。
- 填写完毕后,将申请单交给部门主管审批。
2. 部门主管审批- 部门主管审核退补申请单。
- 检查申请单上填写的物料信息是否准确,并对退补原因进行评估和确认。
- 若退补申请符合规定,部门主管签字同意;若不符合规定,部门主管要提出修改意见或驳回申请。
3. 物料退补执行- 部门主管审核通过的退补申请单交给仓库管理员执行。
- 仓库管理员根据申请单上的物料信息,进行库存查询,并将需要退补的物料准备好。
- 仓库管理员将退补的物料交给申请人,并在《物料退补记录》上记录退补信息,包括物料名称、规格、数量、退补时间等。
4. 物料补充执行- 部门主管审核通过的退补申请单交给采购部门执行。
- 采购部门根据申请单上的物料信息,进行供应商选择和采购流程,确保及时补充所需物料。
- 采购部门将补充的物料送达仓库,仓库管理员根据《物料补充记录》进行验收,并将补充的物料入库。
五、责任与义务1. 部门主管责任与义务- 审核退补申请单的准确性和合规性;- 及时审批退补申请;- 监督物料退补流程的执行。
2. 仓库管理员责任与义务- 根据申请单上的物料信息准备退补物料;- 记录退补物料的相关信息;- 及时入库补充的物料。
3. 采购部门责任与义务- 根据申请单上的物料信息选择供应商;- 按照采购程序及时补充物料;- 确保补充的物料及时送达仓库。
领料、退料、补料程序

领料、退料、补料管理办法一、领料1、生产线根据订单领料,原则上提前一至两天开具《材料出库单》,领料单必须经生产线主管、仓库主管审批、财务审核后生效,领料单必须注明物品名称、料号、型号、颜色、数量以及区分合同号。
2、仓库接到《领料单》根据生产线进度提前备料,生产线需提前三个小时到仓库完成领料。
3、通用配件生产部门根据车间生产线库存情况自行决定领用数量,专用配件领用必须根据订单数量,不允许多领,仓库进行监督。
4、小件配件原则上一次性领完,若因库存不够等其他原因不能一次性领完,可分批领料。
5、大件物料或跟线物料第一次领料时,应考虑生产单的产能和区域空间情况,以备足一天的用量为原则。
6、不能一次性领完的物料,生产线可根据生产进度情况进行领料。
7、生产线领料时,领料员对物料数量务必与仓管员当面点清数量并签字确认。
8、因特殊原因需先借物料的,所借物料必须在24小时内开具《领料单》。
9、生产线如整包装数量缺少时须立即通知仓库确认后才能补料。
二、退料1、生产线在生产过程当中出现的不良物料应与正常物料区分开,标识清楚,并且当天退料。
2、生产线退料时,《退料单》必须经部门主管、品质部主管审核、财务部核准后,仓库才可接受退料。
3、生产线退料时,品质部应对不良物料进行判断,在《退料单》上标识属于制程不良还是来料不良,如属于制程不良因注明不良率的百分比。
4、外购不良物料统一退仓库,由仓库通知采购部,采购部通知供应商,仓库负责办理退货手续。
5、仓库退货给供应商时,《退货单》需经品质部主管确认,品质部注明退货原因,方可退货。
三、补料1、生产线作损需补料时,务必先开具《补料单》,经部门主管、品质主管审批后,仓库再进行补料,补料原则上一次性补完。
2、补料实行“先补后退”的原则,即生产线先领料,等生产完成后,生产再将不良品退回仓库,补料数量和退料数量必须一致,仓库给予监督。
3、仓库接到《补料单》应第一时间安排补料,以不影响正常生产为原则。
物料退补管理制度
物料退补管理制度一、制度目的本制度的目的是为了规范和管理企业物料的退补流程,确保物料的合理使用和减少浪费,提高企业的管理效率。
二、适用范围本制度适用于所有企业的物料退补管理流程,包括进货、库存和退补环节。
三、退补流程1. 提交退补申请当物料需要退补时,由相关部门或人员填写退补申请表,详细说明退补原因、数量和规格。
2. 申请审批退补申请表由相关部门负责人审批,审批人需核实退补原因的合理性,并根据公司的预算、库存情况和实际需求来决定是否批准退补。
3. 物料退回如果退补申请获得批准,相关部门需将物料按照要求退回给供应商或将其归入库存,确保物料的安全和完整。
4. 补货针对退回的物料,相关部门需要重新评估需要补货的数量和规格,并在供应商处进行补货申请。
5. 补货审批补货申请需要由相关部门负责人审批,审批人需考虑企业的实际需求、物料的重要性以及公司的预算情况来决定是否批准补货申请。
6. 物料补货如果补货申请获得批准,相关部门需及时向供应商下单,并确保物料按时到货。
7. 更新库存补货物料到达后,相关部门需及时更新库存信息,确保物料的安全存放和管理。
四、责任和义务1. 相关部门负责人需确保退补申请的合理性和准确性,并及时审批。
2. 相关部门负责人负责补货申请的审批,并确保补货的合理性和及时性。
3. 相关部门负责人需负责库存的管理和更新,确保物料的流转和安全。
4. 所有员工都有义务按照本制度的规定进行物料的退补操作,保证物料的合理使用和减少浪费。
五、制度执行和监督1. 相关部门应定期对退补管理制度的执行情况进行检查和监督,并及时纠正不当行为。
2. 若发现违反退补管理制度的行为,相关部门负责人有权进行相应的处罚和追责。
六、附则本制度的解释权归企业相关部门负责人及公司管理团队所有,并可根据实际情况对其进行修改和调整。
以上为物料退补管理制度,对企业物料的退补流程、责任和义务进行了详细的规定,希望能够帮助企业提高物料管理的效率和减少浪费,确保物料的合理使用和延长使用寿命。
生产领料、补料、退料作业流程
仓库
1、退仓物料质检判定退供应商时,仓库开具《出库单》,《 出库单》一联仓管员存底,做为出库的依据,一联交由仓库 统计员做为打印《退货单》的依据,一联交采购。 2、《退货单》需经质管员确认,采购经理核准。 3、《退货单》一联交由供应商、一联交由财务,做为对账的 依据、一联仓管员存底。
仓库
1、因生产制程造成的不良或人为损坏的物料质检判定报废的
生产中心
《周生产计划》 《产品生产单》
原材料仓库接到厂长开出的《产品生产单》时,依研发制定 的《材料(BOM)清单》,制作出各工序的材料清单并备好 料,物料有异常时需及时反馈给生产中心、生管科、采购部 。
仓库
《产品生产单》 《材料(BOM)清单》
1、生产车间组长依厂长开出的《产品生产单》到仓库领料。 2、领料时依据《产品生产单》的品名、规格、数量核对仓库 生产中心 打印的《材料清单》物料是否齐套。
依报废流程处理。
2
、合格入库的由仓管员办理入库手续入库。
仓库
《退仓单》 《退仓单》 《退仓单》
《出库单》 《退货单》 《退仓单》
仓管员办理相应的入库手续后根据《退仓单》/《退料单》进 行更新手工账本,仓库统计员需更新电脑系统数据。
仓库
《退仓单》 《退料单》
《产品生产单》 《材料清单》
1、生产组长依核对后的《材料清单》对物料进行点收,点收 时需核对物料的品名、规格、数量。在核对过程中发现少数 的需知会仓管员确认并补数,核对无误后同仓库仓管员进行 签收《材料清单》,离开仓库后发现数量短少,应由领料人 员自行负责。 2、实际领料数不可超出《材料清单》上的应发数量。 3、仓库碰到所发物料为整捆或其它原因不可拆包时,应遵循 整捆或整包发料,多出的数量需记录在所发的材料清单上, 生产中心工单完结后需退回仓库或仓库在下一工单上进行扣 除。
食品生产企业退料补货的程序的规定
食品生产企业退料补货的程序的规定
1.退料的类型
通常物料退库的对象包括下列几项。
(1)与产品规格不符的物料。
(2)超发的物料。
(3)不良的物料。
(4)呆料。
(5)报废的物料。
2.退料补货的程序
退料补货的程序如图2-2所示。
图2-2 退料补货程序
(1)退料汇总。
生产部门将不良物料分类汇总后,填写“退料单”送至品管部IQC 组(见表2-3)。
表2-3 退料单
退料部门: 退料部门编号: 收料库: 收料库编号: 原发料编号: 日期: 物料 编号 品名 规格 单位 金额 数量 品管 鉴定 退料 原因 备注
退货 实收
仓管员: 品管员: 退料员:
退料汇总 品管鉴定
退货 补货 登账
(2)品管鉴定。
品管检验后,将不良品分为报废品、不良品与良品三类,并在“退料单”上注明数量。
对于规格不符的物料、超发的物料及呆料退料,退料员在“退料单”上备注:不必经过品管而直接退到货仓。
(3)退货。
生产部门将分好类的物料送至货仓,货管员根据“退料单”上所注明的分类数量清点无误后,分别收入不同的仓位,并挂上相应的“物料卡”。
(4)补货。
因退料而需补货的,需开“补料单”,退料后办理补货手续(见表2-4)。
表2-4 补料单
制造单号:产品名称: No.:
生产领料员:仓管员: PMC:
(5)登账记录。
仓管员应及时将各种单据凭证入账。
(6)表单的保存与分发。
仓管员将当天的单据分类归档或集中分送到相关部门。
仓库退和补和超领物料作业流程
退料处理:分 类、整理、登 记,并提交相
关部门处理
退料处理
退料原因:物料损坏、数量不足、质量问题等 退料流程:填写退料单、审核退料单、办理退料手续、退回仓库 退料要求:及时、准确、完整 退料记录:记录退料时间、数量、原因等信息,便于追溯和管理
超领物料作业流程
章节副标题
超领申请
申请条件:物料短缺或损坏 申请流程:填写超领申请表,提交给相关部门 审批流程:相关部门审核,批准或拒绝超领申请 超领处理:批准后,领取超领物料,并记录在案
操作设备时,确 保设备处于良好 状态,避免故障
操作过程中,注 意个人防护,避 免受伤
保证物料质量
物料入库前,必须进行质量检查,确保符合标准 物料出库时,必须核对数量和规格,确保无误 物料存放时,必须按照规定进行分类、堆放和保管,确保物料不受潮、不损坏 物料退补和超领时,必须严格按照规定进行,确保物料的质量和数量不受影响
章节副标题
核对物料信息
核对物料名称、规格、数量等 信息是否与订单一致
核对物料的保质期、生产日期 等信息是否在可接受范围内
核对物料的包装、标签等信息 是否完整、清晰
核对物料的存放位置、环境等 信息是否符合要求
遵循安全操作规程
确保物料放置在 安全位置,避免 滑落或碰撞
操作过程中,注 意保持通道畅通, 避免堵塞
THEME TEMPLATE
20XX/01/01
学院
仓库退补和超 领物料作业流
程
单击此处添加副标题
汇报人:小无名
目录
CONTENTS
退补物料作业流程 超领物料作业流程 退补和超领物料作业注意事项
退补物料作业流程
章节副标题
退料申请
- 1、下载文档前请自行甄别文档内容的完整性,平台不提供额外的编辑、内容补充、找答案等附加服务。
- 2、"仅部分预览"的文档,不可在线预览部分如存在完整性等问题,可反馈申请退款(可完整预览的文档不适用该条件!)。
- 3、如文档侵犯您的权益,请联系客服反馈,我们会尽快为您处理(人工客服工作时间:9:00-18:30)。
车间退补料管理流程
制定: 批准:
会签:日期:(生产一部)
(生产二部)① 将生产装配过程中产生的不良品整理;
② 针对批量性不良或需要相关部分整改或纠正的交品管判定,使其了解其不良原由;
③ 不属批量的不良品,装配时发现零部件(A 类件)局部不良的应及时用红色的记号笔标识,以便及时返修处理;
④ 将不良品的品名和数量统计交车间文员统一开具系统<退\补料单>;装同一型号规格产品的流水线可汇总开单补料⑤ 在规定时间内,车间专员将物与单同时交达仓管员时,仓管员应核实退、补料明细是否相符,符合即将需要补的物料即时发放;⑥ 仓管员对退库存的不良品应隔离存放;
⑦ 不良品应定期进行分类汇总,并退到相关部门进行返修、退货处理,接收部门对收到不良品须先确认再签收;流程说明:。