电子束焊
电子束焊接原理

电子束焊接原理
电子束焊接是一种高能束流焊接技术,其原理是利用电子束对工件进行熔化和焊接。
电子束是通过对金属丝进行高电压电子轰击产生的,产生的电子束具有高速度和高能量,可在纳秒时间内将焊接部位加热到高温。
其焊接原理主要包括以下几个步骤:
1.电子发射与准直:将阴极表面加热,使其发射出电子,然后
通过电场和磁场的作用,使电子束准直成为直线束。
2.聚焦:利用磁场将电子束聚焦成细束,以增加束流密度和功
率密度。
3.定向和控制:通过磁场控制电子束的方向和位置,使其对准
焊接部位。
4.熔化和焊接:电子束轰击工件表面时,其动能会转化为热能,使焊接部位瞬间升温到熔化温度,形成熔池。
焊接材料进入熔池后,通过冷却凝固形成焊缝。
5.控温和控速:在焊接过程中,通过控制电子束的功率和移动
速度,来控制焊接温度和焊接速度,以实现理想的焊接效果。
电子束焊接具有焊接速度快、精度高、热影响区小等优点,适用于对高强度和高精度焊接要求的工件,如航空航天零部件、汽车零部件等。
电子束焊接

1.3.1 焊前准备
焊前清理:真空电子束焊前必须对焊件表面
进行严格清理,否则将导致焊缝产生缺陷, 接头的力学性能降低,不清洁的表面还会延 长抽真空时间,影响电子枪工作的稳定性, 降低真空泵的使用寿命。
1.3.1 焊前准备
观察窗口通常由三重玻璃组成,里层为普通玻璃;中层 的铅玻璃是防护X射线的作用;外层的钢化玻璃是承受 真空室内外压力差的。
采用工业电视可以使操作者能连续观察焊接过程,防止 肉眼受强烈光线刺激的危害。
1.2.2 电子束焊机的选用
选用电子束焊机通常考虑以下几个方面: 焊接化学性能活泼的金属(如W、Ta、Mo等)及其合金应
零件装配: 对于无锁底的对接接头,板厚δ<1.5mm时,局部最
大间隙不应超过0.07 mm;随板厚增加,间隙略增。 板厚超过3.8mm时,局部最大间隙可到0.25 mm。
焊薄工件时,一般装配间隙不应大于0.13mm。
1.3.1 焊前准备
非真空电子束焊时,装配间隙可以放宽到0.75mm。 深熔焊时,装配不良或间隙过大,会导致过量收缩、 咬边、漏焊等缺陷。
1.1.2 电子束焊的特点及分类
2.电子束焊的缺点 设备比较复杂,投资大,费用较昂贵; 电子束焊要求接头位置准确,间隙小而且均匀,
焊前对接头加工、装配要求严格; 真空电子束焊接时,被焊工件尺寸和形状常常受到
工作室的限制; 电子束易受杂散电磁场的干扰,影响焊接质量; 电子束焊接时产生X射线,需要操作人员严加防护。
由电子枪、工作室(也 称真空室)、电源及电 气控制系统、真空系统、 工作台以及辅助装置等 几大部分组成。
1.2.1 电子束焊机的组成
电子束焊

电子束焊焊接方法基本概念电子束焊是利用加速和聚焦的电子束轰击置于真空或非真空中的焊件所产生的热能进行焊接的方法。
基本原理和分类电子束焊接因具有不用焊条、不易氧化、工艺重复性好及热变形量小的优点而广泛应用于航空航天、原子能、国防及军工、汽车和电气电工仪表等众多行业。
电子束焊接的基本原理是电子枪中的阴极由于直接或间接加热而发射电子,该电子在高压静电场的加速下再通过电磁场的聚焦就可以形成能量密度极高的电子束,用此电子束去轰击工件,巨大的动能转化为热能,使焊接处工件熔化,形成熔池,从而实现对工件的焊接。
电子束焊的分类方法很多。
按被焊工件所处的环境的真空度可分为三种:高真空电子束焊,低真空电子束焊和非真空电子束焊。
1.高真空电子束焊是在10-4~10-1Pa的压强下进行的。
良好的真空条件,可以保证对熔池的“保护”防止金属元素的氧化和烧损,适用于活性金属、难熔金属和质量要求高的工件的焊接。
2.低真空电子束焊是在10-1~10Pa的压强下进行的。
压强为4Pa时束流密度及其相应的功率密度的最大值与高真空的最大值相差很小。
因此,低真空电子束焊也具有束流密度和功率密度高的特点。
由于只需抽到低真空,明显地缩短了抽真空时间,提高了生产率,适用于批量大的零件的焊接和在生产线上使用。
3.在非真空电子束焊机中,电子束仍是在高真空条件下产生的,然后穿过一组光阑、气阻和若干级预真空小室,射到处于大气压力下的工件上。
在压强增加到7~15Pa 时,由于散射,电子束功率密度明显下降。
在大气压下,电子束散射更加强烈。
即使将电子枪的工作距离限制在20~50mm,焊缝深宽比最大也只能达到5:1。
目前,非真空电子束焊接能够达到的最大熔深为30mm。
这种方法的优点是不需真空室,因而可以焊接尺寸大的工件,生产率较高。
工艺特点和应用范围1.工艺特点①电子束穿透能力强(功率密度可达106W/cm2),焊缝深宽比大(可达50:1),易于实现厚度差极大的焊件之间的接。
电子行业电子束焊
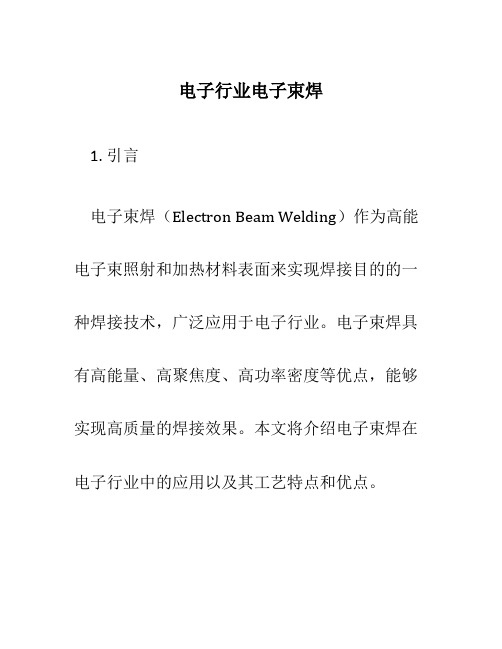
电子行业电子束焊1. 引言电子束焊(Electron Beam Welding)作为高能电子束照射和加热材料表面来实现焊接目的的一种焊接技术,广泛应用于电子行业。
电子束焊具有高能量、高聚焦度、高功率密度等优点,能够实现高质量的焊接效果。
本文将介绍电子束焊在电子行业中的应用以及其工艺特点和优点。
2. 电子束焊在电子行业中的应用电子束焊作为一种高精度、高效率的焊接方法,被广泛应用于电子行业。
其主要应用包括以下几个方面:2.1 集成电路的封装在集成电路封装过程中,需要将封装芯片与引线焊接在一起。
电子束焊因其高能量的特点可以快速将引线和芯片焊接到一起,而不会造成局部过热的问题。
这对于保证芯片的性能和稳定性非常重要。
2.2 电子器件的组装电子器件的组装过程中,通常需要将不同的零件焊接在一起。
电子束焊因其高能量的特点可以快速将不同材料的零件焊接在一起,而不会对零件产生过多的热影响。
这种焊接方法可以确保焊点的质量和稳定性。
2.3 超导材料的制备在电子行业中,超导材料的制备是一项非常重要的工作。
电子束焊因其高能量的特点可以在材料表面形成高密度的热源,以实现超导材料的制备和改性。
2.4 电子元器件的修复在电子行业中,电子元器件的修复是一项常见的任务。
电子束焊因其高能量的特点可以将受损的电子元器件与其他部件焊接在一起,以实现修复的目的。
3. 电子束焊的工艺特点电子束焊作为一种特殊的焊接方法,具有以下工艺特点:3.1 高能量密度电子束焊使用高能电子束进行焊接,电子束能量密度非常高,可以使焊接过程中的热输入量和焊接速度得到很好的控制,从而实现高质量的焊接效果。
3.2 高聚焦度电子束焊使用电磁透镜系统聚集电子束,使其能量集中在很小的焦点上。
这种高聚焦度使得焊接过程中的热影响区域非常小,对焊接材料的热影响较小,可以减少变形和应力的产生。
由于电子束焊的高能量密度和高聚焦度特点,可以在很短的时间内完成焊接过程。
这种高速度的焊接可以提高生产效率,减少生产成本。
电子行业电子束焊接

电子行业电子束焊接简介电子束焊接是一种常用于电子行业的高精度焊接技术。
它利用电子束的高能量特性,将焊接材料加热至高温,快速融化并连接在一起。
电子束焊接具有精度高、焊接速度快和热影响区小等优点,广泛应用于半导体、电子元件和电路板的制造过程中。
工艺流程电子束焊接的工艺流程包括以下几个步骤:1.准备工作:对焊接材料进行清洁处理,确保表面不含杂质和氧化物。
同时,需要根据焊接要求确定焊接参数,包括电子束功率、聚焦电压和聚焦电流等。
2.对焊接材料进行定位和夹持:将待焊接的材料放置在焊接台上,并使用夹具进行固定,以确保焊接过程中的稳定性和准确性。
3.开始焊接:启动电子束装置,将电子束聚焦并瞄准焊接位置。
电子束穿过电子枪并聚焦在工件上,加热焊接材料达到融化温度并实现焊接。
4.焊接结束:完成焊接后,关闭电子束装置,等待焊接区域冷却。
同时,对焊接区域进行检查,确保焊接质量符合要求。
特点和优势电子束焊接在电子行业中得到广泛应用,主要受益于以下几个特点和优势:•高精度:电子束焊接能够提供非常精确的焊接结果,焊接位置和焊缝的尺寸控制非常准确,有助于保证电子产品的稳定性和可靠性。
•焊接速度快:电子束焊接的加热速度非常快,因为电子束本身具有高能量,能够迅速将焊接材料加热至融化温度。
相比传统焊接方法,电子束焊接能够大大缩短焊接时间,提高生产效率。
•热影响区小:电子束焊接时,焊接区域受热的时间非常短,因此在焊接过程中产生的热量对材料周围的影响非常小。
这意味着电子束焊接可以避免或减少由于热应力引起的变形和损坏,提高焊接质量。
•适用范围广:电子束焊接可以应用于各种材料的焊接,包括金属、陶瓷和非金属材料。
它在不同类型的电子元件、半导体和电路板的制造过程中都有重要的应用价值。
•自动化程度高:电子束焊接可以与自动化设备相结合,实现工艺的自动化和智能化。
通过编程和机器控制,可以实现焊接参数的精确控制和焊接过程的自动化控制。
应用案例LED封装在LED封装过程中,电子束焊接被广泛应用于焊接LED芯片和良好导热性能的基座之间的连接。
电子束焊
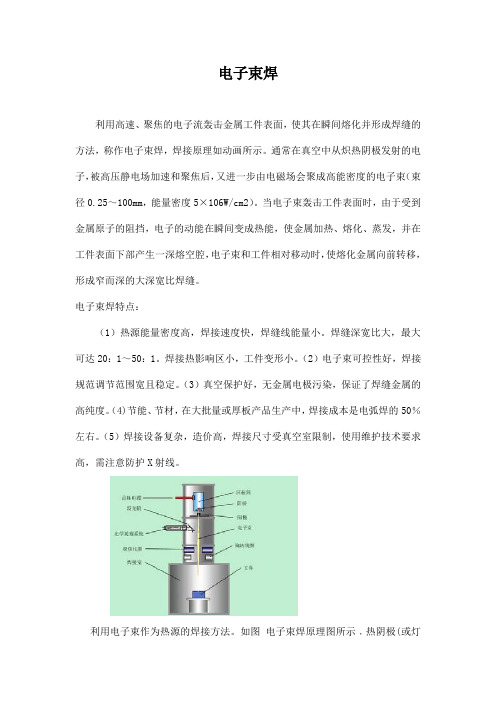
电子束焊利用高速、聚焦的电子流轰击金属工件表面,使其在瞬间熔化并形成焊缝的方法,称作电子束焊,焊接原理如动画所示。
通常在真空中从炽热阴极发射的电子,被高压静电场加速和聚焦后,又进一步由电磁场会聚成高能密度的电子束(束径0.25~100mm,能量密度5×106W/cm2)。
当电子束轰击工件表面时,由于受到金属原子的阻挡,电子的动能在瞬间变成热能,使金属加热、熔化、蒸发,并在工件表面下部产生一深熔空腔,电子束和工件相对移动时,使熔化金属向前转移,形成窄而深的大深宽比焊缝。
电子束焊特点:(1)热源能量密度高,焊接速度快,焊缝线能量小。
焊缝深宽比大,最大可达20:1~50:1。
焊接热影响区小,工件变形小。
(2)电子束可控性好,焊接规范调节范围宽且稳定。
(3)真空保护好,无金属电极污染,保证了焊缝金属的高纯度。
(4)节能、节材,在大批量或厚板产品生产中,焊接成本是电弧焊的50%左右。
(5)焊接设备复杂,造价高,焊接尺寸受真空室限制,使用维护技术要求高,需注意防护X射线。
利用电子束作为热源的焊接方法。
如图电子束焊原理图所示﹐热阴极(或灯丝)发射的电子﹐在真空中被高压静电场加速﹐经磁透镜產生的电磁场聚集成功率密度高达1.5×105瓦/厘米2的电子束(束径为0.25~1毫米)﹐轰击到工件表面上﹐释放的动能转变为热能﹐熔化金属﹐焊出既深又窄的焊缝(深/宽比可达10﹕1~30﹕1)﹐焊接速度可达125~200米/时﹐工件的热影响区和变形量都很小。
电子束的焊接工作室一般处於高真空状态﹐压力为10-1~100帕﹐称为高真空电子束焊。
处於低真空状态时压力为100~10000帕﹐称为低真空电子束焊。
在大气中焊接的称为非真空电子束焊。
真空工作室为焊接创造高纯洁的环境﹐因而不需要保护气体就能获得无氧化﹑无气孔和无夹渣的优质焊接接头。
随著工作室气压的增加﹐电子束散焦程度增大﹐焊缝的深/宽比减小。
电子束焊机有两类﹕低压电子束焊机的加速电压为30~60千伏﹔高压电子束焊机的加速电压可达175千伏。
电子束焊
压的系统,都必须采取有效的安全防护措施。
(2) X射线辐射 焊接时大量的X射线是由高速运动的电子束与焊 件撞击所产生的,在枪体和工作室内电子束与气体分 子或金属蒸气相撞时,也会产生相当数量的X射线。
24
(3) 烟雾与气体 电子束焊接时会产生有害的金属蒸气、烟雾、臭 氧及氧化氮等。因此,要有通风或排气措施,以确保 真空室内和工作场所的有害气体含量降低到安全水准
焊缝
1
2、电子束焊的分类
1)按照真空度不同
高真空、低真空、非真空
2)按照工件所处环境
全真空、局部真空
3)按照电子束功率
大、中、小功率
4)按照深穿特点
普通、脉冲
2
3、电子束焊的特点
(1)穿透能力强,焊缝深宽比大,可达50:1;
(2) 焊接速度快,热影响区小,焊接变形小;
(3) 真空环境利于提高焊缝质量; (4) 焊接可达性好; (5) 电子束易于控制 ; (6) 设备复杂,费用比较昂贵 (7) 接头装配要求严格,接头间隙小而且均匀 ; 不足 (8) 被焊工件尺寸和形状常常受到真空室的限制 ; (9) 电子束易受电磁场的干扰,影响焊接质量 ; (10)产生X射线需要严格防护以保证操作人员的安全
19
9、电子束焊接缺陷
(1) 焊偏: a) 引起焊偏的原因: 一是设备不良,使对中不准确可靠; 二是焊件发生变形; 三是静电力和磁力干扰使电子束发生偏转。 b) 防止措施: 从设备方面应提高传动系统精度;提高对焊件夹持 的刚性。 从工艺方面,焊前将所有铁磁焊件退磁和采用非磁 性材料夹具。
20
(2)塌陷
22
(5)冷隔
是焊缝金属本身的不完善熔合,出现在根部焊缝
金属的层状线上,由于熔融金属的受热波动所造成。 防止产生冷隔的工艺措施是减小电子束功率密度 和迚行电子束的横向摆动,以减小深宽比值和增大根 部缝宽。
焊接高级技师培训教材电子束焊
第一节 电子束焊概述 二.电子束焊的特点
(7)焊接金属质量高 在真空环境中焊接,不仅可以 防止熔化金属受到氢、氧、氮等有害气体的污染, 而且还有利于焊缝金属的除气和净化。
(8)电子束容易受控 焊接参数易于精确调节,通过 控制电子束的偏移,可以实现对复杂焊缝的自动焊 接,在焊接过程中可以通过电子束扫描熔池来消除 缺陷,从而提高焊接接头质量。
三.铝及铝合金的电子束焊
③ 焊接含有锌、镁元素的高强度铝合金时,为防止 过量的金属蒸汽,应该适当降低电子束的能量密度。 铝及铝电子束焊的焊接参数见表9-2。
铝及铝电子束焊的焊接参数
第四节 常用材料的电子束焊
四.纯铜的电子束焊
纯铜电子束焊的焊接参数
第四节 常用材料的电子束焊
五.钛及钛合金的电子束焊
第二节 电子束焊的焊接设备 五.运动系统
运动系统由工作台、转台及夹具组成。 目的是使电子束与焊件循焊接路线实行相对 (焊件不动,电子枪动,或反之)运动。
第二节 电子束焊的焊接设备 六.电气控制系统
电气控制系统目前已大都采用程控技 术,焊接过程已可实现全自动化。
第二节 电子束焊的焊接设备 七.辅助系统
1)焊前用化学方法,仔细清洗待焊处及对接边缘的油、 污、锈、垢及氧化膜。 2)填充焊丝或填片在焊前要进行真空退火除氢。 3)薄板焊接时,应采用卷边接头形式。 4)对于高温条件下使用的钛合金焊件,其工艺流程是: 退火-焊接-固熔处理-时效。 5)对于在其他条件下使用的钛合金焊件,其工艺流程是: 固熔处理-时效-焊接。
第一节 电子束焊概述 二.电子束焊的特点
深宽比通常在50:1
第一节 电子束焊概述 二.电子束焊的特点
(4)焊接速度快 电子束焊能量集中,熔化速度快, 一般焊接速度在1000mm/min以上。
电子束焊接新工艺介绍
电子束焊接新工艺介绍电子束焊接是一种高能束焊接工艺,利用高速电子束来熔化和连接金属材料。
它具有高效、高精度和无污染等优点,因此在航空航天、能源、电子和汽车制造等领域得到了广泛的应用。
本文将介绍电子束焊接的原理、应用以及其在新工艺中的创新。
1. 电子束焊接原理电子束焊接利用高速电子束的热能将焊件加热到熔点,并通过材料的自身表面张力形成液态金属池,从而实现焊接。
电子束产生器通过热发射电子枪发射高速电子束,通过电子光学系统将电子束聚焦到焊接点上。
在焊接过程中,焊件表面与电子束相互作用,将大部分电子能量转化为热能,使焊接点迅速升温并熔化。
2. 电子束焊接的应用电子束焊接广泛应用于如下领域:2.1 航空航天领域航空航天领域对焊接接头的质量和可靠性要求非常高。
电子束焊接由于其高能量聚焦和熔池稳定性的特点,成为航空航天部件的首选焊接工艺,能够确保接头的强度和密封性。
2.2 能源领域电子束焊接广泛应用于核电站中的管道和容器的焊接,能够保证焊缝的强度和耐高温性能。
同时,在太阳能光伏领域,电子束焊接可以高效地连接光伏电池片和电池组件,提高太阳能电池的转换效率。
2.3 电子领域电子束焊接可以用于连接微电子器件和半导体材料。
其高能量聚焦和熔池稳定性使得焊缝的尺寸控制精度高,适用于微尺寸器件的焊接,如微芯片、集成电路和MEMS。
2.4 汽车制造领域电子束焊接在汽车制造中常用于焊接车身结构和发动机部件。
电子束焊接可以实现高强度焊缝和减少变形,提高汽车的结构强度和安全性能。
3. 电子束焊接新工艺创新近年来,电子束焊接工艺在不断创新发展中引入了一些新的技术和方法。
以下是一些典型的创新应用:3.1 多束电子束焊接多束电子束焊接利用多个电子束同时对焊件进行加热,可以提高焊接速度和效率,同时减少焊接变形。
这种方法广泛应用于大批量零件的快速焊接,如汽车车身焊接和飞行器结构焊接。
3.2 电子束熔覆电子束熔覆是一种利用电子束加热将金属粉末加热到熔点,并喷射到基体表面形成涂层的工艺。
电子束焊的工作原理
电子束焊的工作原理
电子束焊是利用高速电子束的冲击力和热能将金属材料加热至熔点,达到焊接效果的一种焊接技术。
其工作原理如下:
1.电子束产生:在电子束焊设备中,通过电子枪或加速器向钨丝施加高压电流,使其产生极高的热能。
热能会使钨丝进入高温状态,并释放出大量的自由电子。
2.电子束聚焦:利用磁铁或电磁场将自由电子束聚焦为一束高速电子流,从而形成电子束。
3.电子束加速:通过加速器施加电场,将电子束加速至一定的速度。
速度越高,电子束的穿透力和热能也越强。
4.电子束照射:将加速后的电子束照射到需要焊接的金属材料上。
由于电子束的高速冲击力和热能,金属材料的表层会被加热至熔点。
5.金属熔化和焊接:由于金属材料表层被高速电子束加热至熔点,金属原子开始进入高度活跃的状态。
金属原子在熔化状态下,会发生相互扩散和融合,从而实现焊接的效果。
6.焊接完成:电子束焊接完成后,焊接区域会快速冷却,形成牢固的焊缝。
电子束焊技术由于其高能量、高速度和高密度的特点,具有焊
接速度快、熔深浅可控、焊缝质量好等优点。
它在航天航空、汽车工业、电子工业等领域有着广泛的应用。
- 1、下载文档前请自行甄别文档内容的完整性,平台不提供额外的编辑、内容补充、找答案等附加服务。
- 2、"仅部分预览"的文档,不可在线预览部分如存在完整性等问题,可反馈申请退款(可完整预览的文档不适用该条件!)。
- 3、如文档侵犯您的权益,请联系客服反馈,我们会尽快为您处理(人工客服工作时间:9:00-18:30)。
• 电子束电流:(简称束流)与加速电压一起决定着
电子束焊的功率。 • 增加电子束流,热输入增大,熔深和熔宽都会增加。 • 在电子束焊中,由于加速电压基本保持不变,所以
为满足不同的焊接工艺需要,常常要调整电子束电
流值。
• 焊接速度:电子束焊接的一个基本工艺参数,其影响 焊缝的熔深、熔宽以及被焊材料的熔池行为(冷却、 凝固及焊缝熔合线形状)。 • 通常随着焊接速度的增大,熔宽变窄,熔深减小 • 热输入与电子束焊接能量成正比,与焊接速度成反比。
• 低真空电子束焊:在真空度为10-1~10Pa范围内进行。由于 只需要抽到低真空,减小了抽真空的时间,从而加速焊接过
程,提高了生产效率。
• 适用于大批量零件的焊接和生产线上使用。 • 非真空电子束焊接:电子束是在真空条件下产生的,然后穿 过一组光阑、气阻通道和若干级预真空小室,射到处于大气 压力下的工件上。非真空电子束焊接能够达到的最大熔深为
时很快在被焊焊件上“钻”出一个匙孔,小孔的周围被
液态金属包围。 • 随着子束与焊件的相对移动,液态金属沿小孔周围流向 熔池后部,逐渐冷却、凝固形成了焊缝。
• 在电子束焊接过程中,焊接熔
池始终存在一个匙孔。匙孔的
存在,从根本上改变了焊接熔 池的传质、传热规律,由一般 熔焊方法的“热导焊”转变为 “穿孔焊”。
• 电子束焊接的角接头:
• 电子束焊接T形接头:
• 搭接接头:常用于焊接厚度小于1.6mm的焊件。
8.主要焊接参数及其选择
• 加速电压:电子束焊接的一个重要工艺参数;
• 提高加速电压可增加焊缝的熔深。在大多数电子束
焊过程中,加速电压参数往往不变,但当电子枪的
工作距离较大或者要求获得深穿透的平行焊缝时, 应提高加速电压(选用高压型设备)。 • 通常电子束焊机工作在额定电压下,通过调节其他 参数来实现焊接参数的调整。
• 单道焊接厚度超过100mm的碳素钢,厚度超过400mm的铝
板,焊接时无需开坡口和填充金属; • 焊薄件的厚度可小于2.5mm,甚至薄到0.025mm • 可焊厚薄相差悬殊的焊件。 • 非真空电子束焊不受此限制,可以焊接大型焊接结构,但 必须保证电子枪底面出口到焊件上表面的距离,一般在 12~50mm之间,其可焊厚度单面焊时一般很少超过10mm。
30mm。
• 由于不需真空室,因而可以焊接尺寸大的工件,生产率较高。
5.电子束焊的适用范围
• 应用领域:由于电子束焊接具有焊接深度大、焊缝性能好、焊接变形小、焊
接精度高、并有较高的生产率等特点。因此,在航空航天、汽车制造、压力
容器、电力及电子等工业领域中得到了广泛地应用,能够实现特殊难焊材料 的焊接。
• 电子束焊的接头形式:对接、角接、T形、搭接和端接。
电子束直径细,能量集中,焊接时一般不加焊丝,所
以电子束焊接头设计应按无间隙接头考虑。 • 设计的原则:便于接头的准备、装配和对中,减少收 缩应力,保证获得所需熔透深度。 • 如果电子束的功率不足以一次穿透焊件,也可采用正 反两面焊的方法来完成。对重要承力结构,焊缝位置 应避开应力集中区。
• 真空电子束焊机组成: 由电子枪、工作室(也 称真空室)、电源及电 气控制系统、真空系统、 工作台以及辅助装置等
几大部分组成。
7.焊接工艺
焊前准备
• 接合面的加工: • 电子束焊接头属于无坡口对接形式,装配时力求使零 件紧密接触。电子束焊要求接合面经过机械加工,其 表面粗糙度由被焊材料、接头设计而定,在 1.5~25um间选定。 • 一般电子束焊接不用填充金属;只在焊接异种金属或
• 真空电子束焊接时,被焊工件尺寸和形状常常受到 工作室的限制;
• 电子束易受杂散电磁场的干扰,影响焊接质量; • 电子束焊接时产生X射线,需要操作人员严加防护。
3.电子束焊接独有的两种缺陷
3.1.针尖 • 产生部位:常发生在部分熔透焊缝的根部 • 形成原因:电子束功率的脉动,液态金属表面张力和冷却速度过大,而液相 金属来不及流入所致 • 解决措施:接头采用垫板,将缺陷引出;偏转扫描电子束;
气进入枪体中造成放电现象;
• 在不影响电子枪稳定工作的前提下,可以采用尽可
能短的工作距离。
3. 电子束焊的分类
• 根据被焊工件所处环境的真空度可将电子束焊分为:高真空电子束焊、低真
空电子束焊和非真空电子束焊 三种。
• 高真空电子束焊接是在真空度为10-4~10-1Pa的环境
下进行,具有良好的真空条件,电子束很少发生散
射,可以保证对熔池的“保护”,防止金属元素的 氧化和烧损。 • 适用于活性金属、难熔金属和质量要求高的工件焊 接,也适用于各种形状复杂零件的精密焊接。
• 电子束聚焦状态:对焊缝的熔深及其成形影响较大。
• 焦点变小可使焊缝变窄,熔深增加。 • 根据被焊材料的焊接速度、接头间隙等决定聚焦位置,进而确定电子束斑点 大小。
• 工作距离:应在设备最佳范围内。
• 工作距离变小时,电子束的斑点直径变小,电子束
的压缩比增大,使电子束斑点直径变小,增加了电
子束功率密度。但工作距离过小会使过多的金属蒸
3.2.冷隔 • 产生部位:厚件焊缝根部和稍高处会出现较大的空洞,把上下熔化金属分隔 开来。 • 形成原因:厚件中气孔的一种特殊表现形式,与电子束焊缝形成机制有关。 厚板焊接时,金属蒸汽和其它气体逸出受阻,在较快冷却速度下留在焊缝中。 • 解决措施:减少工件产生气体的来源;降低加速电压,适当降低焊速;采用 扫描束。
• 上世纪60年代后,我国开始从事电子束焊接研究;
2.电子束焊的概述
• 电子束焊(Electronic Beam Welding,EBW)是指在真空或非真空环境中,
利用汇聚的高速电子流轰击焊件接缝处所产生的热能,使被焊金属熔合的一
种焊接方法。电子束焊是一种高能束流焊接方法。
3.电子束焊的基本原理
4.电子束焊的特点及分类
1.电子束焊的优点
• 电子束穿透能力强,焊缝深宽比大。 • 焊接速度快,热影响区小,焊接变形小。 • 焊缝纯度高,接头质量好。 • 再现性好,工艺适应性强。 • 可焊材料多。
2.电子束焊的缺点 • 设备比较复杂,投资大,费用较昂贵; • 电子束焊要求接头位置准确,间隙小而且均匀,焊 前对接头加工、装配要求严格;
• 可焊接的材料:除含有大量高蒸气压元素的材料外, 一般熔焊能焊的金属,都可以采用电子束焊,如铁、
铜、镍、铝、钛及其合金等。此外,还能焊接稀有
金属、活性金属、难熔金属和非金属陶瓷等;焊接
熔点、热导率、溶解度相差很大的异种金属。焊接
热处理强化或冷作硬化的材料,而接头的力学性能 不发生变化。
• 焊件的结构形状和尺寸:
• 电子束的产生:电子束从电
子枪中产生。一定功率的电 子束经透镜聚焦后,电子束 电流为20 ~ 1000mA,焦点直 径约为0.1 ~ 1mm,功率密度 可达106 W/cm2以上,比普通 电弧功率密度高100 ~ 1000倍, 属于高能束流。
Байду номын сангаас
• 电子束撞击到焊件表面,电子的动能就转变为热能,使
金属迅速熔化和蒸发。在高压金属蒸气的作用下熔化的 金属被排开,电子束就能继续撞击深处的固态金属,同
• 有特殊要求或特殊结构的焊件:
• 焊接内部需保持真空度的密封件,靠近热敏元件的焊件,
形状复杂而且精密的零部件;
• 施焊具有两层或多层接头的焊件,这种接头层与层之间
可以有几十毫米的空间间隔。
6.电子束焊机的组成
• 电子束焊机可按真空状态和加速电压分类:
• 按真空状态:真空型、局部真空型、非真空型;在实际 应用中以真空电子束焊机居多。 • 按电子枪加速电压:高压型(60~150kV)、中压型 (40~60kV)、低压型(≤40kV)。
1.电子束焊接起源与发展
电子束的发现迄今已有100多年的历史: • 电子束焊接技术起源于德国,1948年前西德 物理学家K.H.Steigerwald首次 提出用电子书焊接的设想; • 1954年法国J.A.Stohr博士成功焊接了核反应堆燃料包壳,标志电子束焊接 金属获得成功; • 1957年11月,在法国巴黎召开的国际原子能燃料元件技术大会上公布了该 技术,电子束焊接被确认为一种新的焊接方法; • 1958年开始,美国、英国、日本及前苏联开始进行电子束焊接方面的研究;
合金时,可根据需要使用填充金属。
• 焊件清理:真空电子束焊前必须对焊件表面进行严格清
理,否则将导致焊缝产生缺陷,接头的力学性能降低,
不清洁的表面还会延长抽真空时间,影响电子枪工作的 稳定性,降低真空泵的使用寿命。
• 焊前预热:对需要预热的工件,根据一定的形状、尺寸及所需要的预 热温度,选择一定的加热方法(如气焊枪、加热炉、感应加热、红外 线辐射加热等),在工件装入真空室前进行。 • 如果工件较小,加热引起的变形不会影响工件质量时,可在真空室内 用散焦电子束来进行预热。