PU油涂装常见弊病及处理方法
常见涂装弊病及防止措施
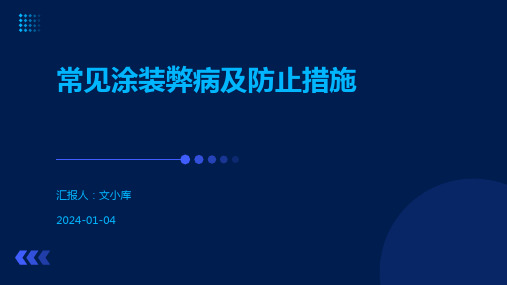
选择合适的涂料
总结词
选择合适的涂料是防止涂装弊病的关键。
详细描述
根据涂装需求和涂装对象的特点,选择符合要求的涂料类型和品牌,确保涂料的质量和性能满足使用 要求。同时,要注意涂料的配套性和相容性,避免因涂料不匹配导致涂层起泡、开裂等问题。
控制涂装环境
总结词
控制涂装环境是保证涂装质量的重要措施。
详细描述
涂装环境应保持清洁、干燥、无尘,温度和湿度要适宜。过高的温度、过低的湿度或灰尘污染都可能导致涂层表 面出现颗粒、不平整等问题。同时,要避免在雨天、雾天或强风中进行涂装作业,以免影响涂层质量。
提高涂装技术水平
总结词
提高涂装技术水平是防止涂装弊病的根 本途径。
VS
详细描述
加强涂装工人的技能培训和技术交流,提 高他们的操作水平和责任心。采用先进的 涂装技术和设备,如静电喷涂、自动涂装 线等,提高涂装的均匀性和平整度。同时 ,要严格执行涂装工艺规程,确保每道工 序的质量控制。
加强涂装后保养
总结词
加强涂装后保养是防止涂装弊病的重要环节 。
详细描述
按照保养要求定期对涂层进行保养和维护, 保持涂层的完整性和美观度。避免硬物刮擦 、高温烘烤和化学腐蚀等损害涂层的行为, 及时修复损坏的涂层,延长涂层的使用寿命 。同时,要注意对保养材料的选用和质量把 控,确保保养效果。
04
涂装弊病的修复方法
THANKS
谢谢您的观看
常见涂装弊病及防止措施
汇报人:文小库 2024-01-04
目录
• 涂装弊病概述 • 常见涂装弊病 • 防止涂装弊病的措施 • 涂装弊病的修复方法
01
涂装弊病概述
涂装弊病的定义
01
涂装弊病是指在涂装过程中出现 的质量问题,如表面缺陷、颜色 不均、起泡、脱落等。
PU油涂装常见弊病及处理方法

PU油涂装常见弊病及处理方法1.喷涂面积不均匀:在PU油涂装过程中,由于喷枪与被喷涂面的距离不一致、喷枪喷射角度不正确等原因,导致喷涂面积不均匀。
解决方法是调整喷涂距离和喷涂角度,保持一定的喷枪与被喷涂面之间的距离,并且始终保持垂直喷涂。
2.皱纹和起泡:PU油涂装中常见的问题是产生皱纹和起泡。
这通常是由于涂装过程中涂料膜的流动受到限制,或者底材的湿度过高等原因引起的。
处理方法是在涂装前要确保底材的湿度适当,并控制好涂装环境的温度和湿度;此外,涂装时要保持一定的速度和涂装厚度,以免涂料膜流动不畅导致皱纹和起泡。
3.色差:PU油涂装过程中,由于施工工艺和材料的差异,可能会出现色差问题。
对于家具、地板等大面积产品,色差可能会影响产品的外观质量及市场竞争力。
解决方法是选择合适的涂料配方和材料,使用相同的施工工艺和条件涂装,确保涂装前底材的质量均匀,避免涂料分层和色差的发生。
4.不良粘附和剥离:PU油涂装中,不良粘附和剥离是常见的问题。
通常是由于涂料和底材之间的附着力不好导致的。
处理方法是在涂装前要对底材进行适当的处理,如磨砂、除尘等,以提高涂料和底材之间的附着力;此外,在涂装过程中要严格控制涂料的涂装厚度,避免过厚导致涂料的粘附力减弱。
5.细纹和裂纹:PU油涂装过程中,细纹和裂纹是常见的问题,特别是在涂装后的干燥阶段。
这通常是由于涂料的收缩性或者环境的干燥程度不当导致的。
解决方法是在涂装前,对底材进行适当的处理,提高涂料的附着力和弹性。
在涂装过程中,要控制好涂料的厚度,避免涂装层过厚,同时要控制好涂装后的干燥环境,保持适当的湿度和温度。
总结起来,PU油涂装常见的弊病有喷涂面积不均匀、皱纹和起泡、色差、不良粘附和剥离、细纹和裂纹等。
解决这些问题的关键是在涂装前正确处理底材,选择合适的涂料配方和工艺,并严格控制涂装过程和环境条件。
只有在涂装过程中做到细致入微的管理,才能保证PU油涂装的质量和效果。
PU油涂装常见弊病及处理方法

弊病类别
弊病原因
排除对策
1、泛白/白化
L施工环境湿度大。
L调整施工环境湿度或温度,如
空气湿度太大,
2、环境温度高,溶剂挥发
温湿度特别大,应停止施工。
涂膜中溶剂挥
太快,导致涂膜表面干
2、容器与涂料避免混入水份,涂
发吸收热量,使
燥速度太快。
料稀释剂避免露天存放会侵入
涂膜表面空气
3、稀释剂溶解力不够。
2、选用配套固化剂,避免增加或
时间或规定时
NCO不能完全接触发生
减少固化剂。
间后涂膜尚未
化学交联反应。
3、注意施工环境的湿度,增设空
完全硬化。
2、反应型体系固化剂添加 不够,有剩余树脂未参 加反应或树脂类型与硬 化剂成分类型不匹配,
气抽湿装置或强制干燥,提高
施工环境温度或延长干燥时
问。
4、采用2次或多次喷涂延长层涂
3、调配好涂料的施工粘度适量调 整稀释剂和固化剂的添加量。
4、选择合适口径的喷枪。
5、做最后一道面漆使用时粘度要 低。
6、避免在高温或风速太快的环境 中涂装。
面。
7、选用配套稀释剂,被涂物表面
4、涂装环境过度通风,被 涂物温度太高时溶剂挥 发过快流展性不良。
5、被涂物表面处理不平 整,影响流平性,稀释 剂不配套,溶解力不 良,涂料放置时间太 久。
或似火山口有
被涂物距离太近。
效果。
如麻脸状模样。
6、被涂物表面被污染,有
6、处理好油水分离器,防止水份
油渍.
混入其中,
弊病类别
弊病原因
排除对策
6、下陷
1、涂料固含低。
1、下涂要充分干燥后再进行上
PU防水涂料应用中常见的质量问题及防治

PU防水涂料应用中常见的质量问题及防治1.沉淀问题:是PU防水涂料使用中反映最多的问题,产生的原因在于涂料中的填料因密度大于聚氨酯胶液的密度。
沉淀分两种,硬沉淀和软沉淀。
硬沉淀是指填料已经和胶液混凝成固体,成为废料;软沉淀指经过在分散(搅拌)填料可以重新均匀地回到胶液中,仍是合格产品。
防止沉淀的措施:1.科学的生产配方和工艺;2.工地存放可采用倒放;3.定期翻桶或使用前翻桶;4.采用机械搅拌之后在使用,并保证在40MIN内用完。
2.结膜问题:PU结膜的根本原因在于包装桶密封不严或漏气。
双组份聚氨酯由A/B组份产生化学反映,反应后的产物是固体极为涂膜。
单组份聚氨酯与空气中的水分发生化学反应而成膜。
结膜的防治:1.生产工艺严禁带入水分;2.采用质量较好的包装桶;3.倒置放置;4.尽量装满;5.避免暴晒。
3.与基层粘接不好,鼓泡:粘接不好的原因1.基层处理达不到要求;2.基层含水率太高,双组份聚氨酯遇水化学反应,生成气体产生气泡;单组份聚氨酯在基面太潮,水分大于化学反应所需,成膜之后,在涂膜下面尚存多余水分,受热汽化,体积膨胀形成空鼓。
3.施工操作不当,前遍涂料未干,即涂后一遍、或一次涂抹太厚,下面的液体或基层中的水分挥发,使涂膜粘接不良,甚至空鼓。
4.乱接稀释剂,为了涂刮快速和省力,在涂料中加入一定稀释剂。
稀释剂在挥发过程中回事涂膜起泡。
避免和治理粘接不良的措施:1.基层凹凸不平、蜂窝麻面等用水泥砂浆修补平整,浮浆杂物清除干净;2.基层干燥,含水率小于8%(含水率检查可同热熔卷材施工),单组份聚氨酯对基层含水率的要求不如双组份聚氨酯严格;3.分遍刮涂,一次不得刮涂太厚且待前一遍干后在刮涂下一遍;4.慢干和不干或不凝:可能是配方问题或生产工艺不当还可能是施工工艺不规范。
聚氨酯涂料的施工要点及缺陷产生的原因及预防措施

聚氨酯涂料的施工要点及缺陷产生的原因及预防措施摘要:夏季使用聚氨酯类油漆进行涂装施工或进行涂层修补时,漆膜经常出现暗泡、针孔等弊病,俗称“热痱”、“痱子”。
为减少针孔产生,一般喷漆后进入烘干室前,都要保证湿漆膜有10min左右的溶剂挥发时间(称为闪干时间或流平时间),这样就可能使有些人认为增加闪干时聚氨酯树脂涂料在很多领域都有着广泛的应用,它有着优良的性能,种类也非常的多。
聚氨酯涂料属反应性涂料,涂饰质量还涉及涂饰施工的种种客观因素,需要注意一些施工要点,使涂饰质量良好。
在涂饰后,会有一些缺陷产生,分析其缺陷产生的原因并对之提出预防措施。
关键词:聚氨酯涂料;施工要点;缺陷及其产生的原因;预防措施。
聚氨酯树脂是第二次世界大战时期发展起来的树脂,但直到近几十年来,由于生产的主要原料二异氰酸酯的价格在不断下降,所以使聚氨酯树脂在涂料、胶料、塑料、橡胶等行业得到越来越广泛的应用。
我国从1958年开始研制聚氨酯树脂涂料,1968年上海地区家具行业研制出685聚氨酯树脂涂料进行试用,取得很好的涂饰效果,便很快在上海地区家具行业普遍推广试用。
到1980年后逐步在全国家具行业获得广泛应用。
因聚氰酸酯具有较活泼的化学反应性,可与不同的聚酯、聚醚、多元醇及其他合成树脂配合使用,制出很多种类的聚氨酯涂料。
聚氨酯涂料在飞机、船舶、车辆、木材、塑料、橡胶、皮革、建筑物涂装、防腐涂装等都有着广泛的应用。
本文主要介绍其在木器产品中的施工要点及缺陷产生原因和预防措施。
1、聚氨酯涂料简述聚氨酯树脂涂料是聚氨基甲酯树脂涂料的简称。
它是以多异氰酸酯跟多羟基化合物反应而制得的,含有氨基甲酸酯为主要成膜物质的涂料,是一种含有氨基甲酸酯链节的高分子化合物。
聚氨酯树脂的涂膜具有优良弹性、坚韧、耐磨、耐候、耐腐蚀及较好的装饰性,可根据使用要求制成多种新型涂料,应用十分广泛。
聚氨酯涂料的种类很多,在木制品中常用的有聚氨脂油、潮气固化聚氨酯和双组分聚氨酯。
涂装常见缺陷及处理方法

B. 1.不要使用在最后一道2.使用時粘度要低.
C.氣溫高,香蕉水揮發快,涂料流展性不佳
C. 1.避免在高溫環境下涂裝2.使用揮發性慢之香蕉水
D.過度通風
D. 0.5-1.0m/sec風速最適當
E.被涂物溫度太高時,溶劑急速揮發流展性不佳
E.應使溫差變小
7.垂流(Sags):涂膜下垂或流涎,尤其是在邊緣部分.
發生原因
對策
A.涂料缺乏搖變性
A.賦與適當之搖變性
B.干燥太慢
B.使香蕉水及樹脂加速干燥
C.涂料比重太大
C.注意顏料比重
D.溫度低時易發生
D.涂裝室保持15℃-30℃
E.干燥室中充滿溶劑蒸氣
E.加強換氣設備
F.一次涂太厚,涂布不均勻,距離太近,粘度低,噴出量過多
對策
A.油性涂料添加天然樹脂,很容易形成割裂
A.添加太多天然樹脂之涂料,涂膜硬且脆
B.涂裝時溫度太低
B.避免溫度太低時涂裝
C.木材中含太多的油脂,雖會被涂料中之溶劑溶解,但在不安定狀態下涂膜容易收縮
C.先用溶劑洗去樹脂或使用封閉樹脂之下涂涂料,如PU頭度底漆
D.收縮度大之木材,因涂膜收縮不同步易形龜裂
1.針孔(pinhole):涂膜表面出現微細小孔.
發生原因
對策
A.涂膜溶劑尚未充分揮發即行加溫,干燥.
A.避免一次涂膜過厚,否則就要使用蒸發遲緩的稀釋劑.
B.強製干燥后,被涂物尚回複常溫即進行下階段涂裝,溶劑因急速揮發而生針孔.
B.涂裝時通常涂料被涂物及環境之溫度要一致,避免溫差過大.
C.導管纖維細孔中存有空氣,而涂料尚在半干燥狀態,空氣擠出而生針孔.
PU油涂装常见弊病及处理方法
PU油涂装常见弊病及处理方法
首先是起泡问题。
起泡通常是由于施工操作不当或基材表面存在污染物导致的。
处理方法如下:
1.确保施工环境清洁整洁。
去除空气中的尘埃和其他杂质。
2.涂装前,对基材表面进行充分的清洗和打磨,确保表面光滑。
3.温湿度适宜,避免高温高湿的环境。
其次是颜色不匀问题。
PU油涂装在施工过程中易出现色差。
处理方法如下:
1.涂装前进行试样,确认颜色是否符合要求。
2.在批量涂装前对颜料进行充分的搅拌,确保颜色均匀。
3.将颜色不匀的部分重新涂装,涂装时注意均匀施工。
再次是粘连问题。
PU油涂装出现粘连通常是涂装层干燥不完全引起的。
处理方法如下:
1.适量调整涂料的稀释剂比例,确保涂料干燥时间适中。
2.涂装后保持适当的通风,促进涂料的干燥。
3.在使用PU油涂装时,可以添加干燥剂来加速涂料干燥。
最后是发白问题。
PU油涂装出现发白通常是由于施工环境温度过低引起。
处理方法如下:
1.涂装前检查施工环境温度,确保温度适宜。
2.如果环境温度过低,可以使用加热设备提高温度。
3.在涂装前使用底漆进行底层处理,能够有效预防发白问题。
总之,PU油涂装常见的弊病有起泡、颜色不匀、粘连和发白。
针对这些问题,需要加强施工操作、调整涂料稀释剂比例、保持适宜的温湿度以及添加干燥剂等。
只有确保涂装过程的规范和细致,才能避免这些问题的发生,从而得到理想的涂装效果。
涂料基础知识-涂装弊病解决
5、桔皮
• • • • 涂料施工粘度过高,流平不好。 涂料施工粘度过高,流平不好。 一次性厚涂 喷涂时枪与板面距离太近。 喷涂时枪与板面距离太近。 被涂物表面处理不平整, 被涂物表面处理不平整,影响 涂料流平。 涂料流平。 • 施工温度过高,涂膜表干快, 施工温度过高,涂膜表干快, 导致桔皮。 导致桔皮。 • • • • 调节合适的施工粘度。 调节合适的施工粘度。 一次涂装不宜过厚。 一次涂装不宜过厚。 调整喷涂距离至15 30CM。 15调整喷涂距离至15-30CM。 将被涂物表面处理平整。 将被涂物表面处理平整。
涂料基础知识
-----涂装弊病原因分析与对策 涂装弊病原因分析与对策
1、流挂
将被涂物表面打磨粗糙。 将被涂物表面打磨粗糙。 调配好涂料粘度 涂层干膜厚度一次不能超过 30um 。 喷涂距离为150 300mm, 150• 喷涂距离太近,喷枪移动 • 喷涂距离为150-300mm,并控 喷涂距离太近, 制适当的喷枪移动速度。 制适当的喷枪移动速度。 速度太慢。 速度太慢。 • • • 被涂物表面过于光滑。 被涂物表面过于光滑。 涂料施工粘度低。 涂料施工粘度低。 一次性施工涂层过厚。 一次性施工涂层过厚。 • • •
• 避免在高温天气(施工温度 避免在高温天气( >35度 下施工。 >35度)下施工。
6、起皮
• 木材中含水率太高。 木材中含水率太高。 • 底材过于疏松或光滑导致附 着力不好。 着力不好。 • PU漆层间未打磨或打磨不彻 PU漆层间未打磨或打磨不彻 底。 • 修色时涂料粘度太低。 修色时涂料粘度太低。 • 底擦色后未用封闭底封闭, 底擦色后未用封闭底封闭, 导致透明底的附着力不好。 导致透明底的附着力不好。 • 将木材进行干燥处理。 将木材进行干燥处理。 • 底材要坚固并打磨至一 定的粗糙度。 定的粗糙度。 • 层间打磨至表面无亮点。 层间打磨至表面无亮点。 • 提高修色涂料的粘度。 提高修色涂料的粘度。 • 底着色后进行封闭。 底着色后进行封闭。
常见的20种涂装弊病术语及处理技巧
施涂好的漆膜在表 干或经过一段时间 后即出现不连续或 不规则的外观变化, 形成裂纹的漆膜表 面现象。(地板漆案例)
★漆膜老化而引起 ★油漆干燥速度过快 ★涂层一次性过厚 ★受底材本身收缩或 变形引起
剥离、脱落
症状 原因分析
★底材含有较多的油脂 ★底层漆膜未彻底打磨 好 ★已经打磨好的底层间 隔时间太长再上面 层 ★底层漆膜上有污染
涂料及其涂膜产生的病态
俗话说;三分油漆七分施工,再好 的油漆也需要好的手艺才能做出好的效 果来。其涂装弊病可以在涂料施工之前 产生,也可以在施工期间或施工后出现, 因此产生病态的因素很多。主要有以下 几点要素:
涂料本身的质量问题
涂料所用基料及其性质;基料与颜、 填料的比例;颜、填料的细度及在基料中 的分散状况;助剂的选择及用量是否合适 等。
漆膜干燥后,呈 现出一道或多道涂 层脱离其下涂层, 或与涂层完全脱离 底材的一种附着不 牢现象。
起颗粒
症状 原因分析 ★施工环境不清洁 ★遇到刮风下雨的天气 施工 ★刷涂工具不洁 ★固化剂增稠或变质 ★底层没有处理干净 ★调配好的油漆没有经 过滤即施工
在已施工好的漆 膜表面上呈现有 大面积或局部颗 粒,其表现为透 明晶状体和不透 明状两种。
原因分析
1、 ★涂料粘度过高 ★油漆表干时间过快
★强力搅拌没有静止好
2、 ★环境施工高温、高湿 ★底材含水率过高 ★固化剂加入太多 ★涂层漆膜一次性过厚 3、 ★施工环境湿度大 ★油漆混入过多的水份 4、 ★底面层附着力不佳 ★板材含水率过大
起针孔
症状 原因分析
★固化剂加入太多 ★底层灰尘处理不干净 ★一次性涂装太厚 ★涂膜表干时间太快 ★施工环境温度过高
★墙体长期受到水分 的袭击,永久性属 于半干不干状态, 尤其是靠近卫生间 部位 ★涂料本身防霉性能 不佳 ★新墙面保养不够
水性聚氨酯(PU)容易出现的问题和特点
水性聚氨酯(PU)容易出现的问题和特点水性聚氨酯是以水代替有机溶剂作为分散介质的聚氨酯体系,也称水分散聚氨酯、水系聚氨酯或水基聚氨酯。
水性聚氨酯以水为溶剂在涂料、胶粘剂、皮革涂饰剂、纸张表面处理剂等都有着广阔的应用,但是因为内含有多种助剂,机械设备的搅拌运转使大量的空气混入水性聚氨酯中,由于水性聚氨酯的粘度较高,导致气体难以溢出,因此形成泡沫,泡沫过多容易影响生产的效率。
那么水性聚氨酯消泡剂就可以避免这一现象的发生。
(-)水性聚氨酯产生泡沫的原因:1、水性聚氨酯中的水与异富酸酯相互之间发生化学反应,容易产生泡沫2、在涂覆水性聚氨酯时由于施工底材不平整、存在空隙,导致孔隙内的空气自涂膜内部上溢,气泡上升不到表面,从而形成泡沫3、在水性聚氨酯的生产中会添加各类化学助剂来保证其性能与质量,这类助剂大多属于表面活性剂,具有起泡特性4、机械设备的搅拌运转使大量的空气混入水性聚氨酯中,由于水性聚氨酯的粘度较高,导致气体难以逸出,因此形成泡沫(二)如果泡沫得不到处理会有什么危害:1、泡沫过多会溢出调和系统,导致周围施工环境的污染2、起泡的产生使生产操作困难,拖慢了水性聚氨酯的生产进度,降低了其生产效率,使水性聚氨酯的生产成本增加3、泡沫的产生阻碍了水性聚氨酯中颜料与填料的调和分散,使其分布不均匀,影响产品美观度4、泡沫过多会影响水性聚氨酯的光泽度、粘结强度、耐磨性、通透性等性能(三)水性聚氨酯消泡剂的特点:水性聚氨酯消泡剂是经过特殊工艺精制而成的消泡剂,它具有:1、消泡能力强,具有自乳化、易分散等特性2、使用时不会产生表面缺陷,也不会影响到成膜性3、对水性涂料体系有特别效果,易溶于水4、可以直接原液添加也可以分批添加5、不会对周围环境造成影响。
- 1、下载文档前请自行甄别文档内容的完整性,平台不提供额外的编辑、内容补充、找答案等附加服务。
- 2、"仅部分预览"的文档,不可在线预览部分如存在完整性等问题,可反馈申请退款(可完整预览的文档不适用该条件!)。
- 3、如文档侵犯您的权益,请联系客服反馈,我们会尽快为您处理(人工客服工作时间:9:00-18:30)。
3、被涂物表面过于光滑。
4、涂料中溶剂挥发太慢。
5、涂装环境充满溶剂蒸气。
6、环境温度太低时更易发生,涂装室涂料及被涂物温差大。
1、调整合适粘度,一次喷涂厚度不超过30微米。
2、控制好喷涂出油量,保持稳定的空气压力,掌握好重涂间隔时间。
3、保持被涂物表面适当的粗糙度各层重涂之间要仔细打磨。
3、注意施工环境的湿度,增设空气抽湿装置或强制干燥,提高施工环境温度或延长干燥时间。
4、采用2次或多次喷涂延长层涂间隔时间。
5、选用恰当型号的砂纸,按木版纹理方向顺木版纹打磨。
6、适当通风。
10、结块/沉淀
颜料、树脂等形成硬沉淀结余罐底。
1、储存时间过长。
2、稀释剂溶解力不当。
3、防沉淀效果不佳。
4、涂料自身成分搭配不佳。
4、涂料或稀释剂含水量高。
5、一次涂装太厚。
6、空压机中油水分离器未定时放水,水份随空气带入涂料。
7、涂装室通风太快。
1、调整施工环境湿度或温度,如温湿度特别大,应停止施工。
2、容器与涂料避免混入水份,涂料稀释剂避免露天存放会侵入湿气。
3、湿度高时避免厚涂。
4、定时排放空压机中的水份。
5、避免雨天或高温环境下施工。避免傍晚施工。
1、涂料先进先出,勿超过储存期。
2、稀释剂的溶解力作适当调整。
3、涂料调配时要充分搅拌均匀,避免局部胶凝,防沉剂类型,用量进行调整。
4、调整涂料各成分之搭配。
2、底层一次涂装不超过30微米。
3、要底层实干后再上涂面漆,底层涂料要硬化充分。
4、留在基材孔外的填充剂要处理干净。
7、流挂/垂流
被涂物垂直或倾斜,面涂装时涂料的粘度与干燥度不平衡或涂装要领不佳,涂膜呈长柱或淋幕状垂直下垂或流涎尤其在边缘部分有流痕。
1、稀释剂添加过量,涂料施工粘度低,一次喷涂太厚或间隔时间太短。
4、施工环境空气湿度太大,导致稀释剂挥发太慢,温度太低从而影响反应速度。
5、一次喷涂太厚或层涂间隔时间短,以至下涂不干燥。
6、砂纸回潮,砂纸型号不恰当,打磨方法不当。
7、通风不足,稀释剂的蒸气充慢整个空间使溶剂挥发缓慢影响干燥。
1、选用溶解力强挥发稍快的稀释剂。
2、选用配套固化剂,避免增加或减少固化剂。
1、涂料自身流平差。
2、被涂物施工环境温度过高。
3、涂料粘度过高或过低。
4、被涂物表面粗糙打磨不完整。
5、空气压力太大,喷枪与被涂物距离太近。
6、被涂物表面被污染,有油渍。
1、涂料中适当添加流平剂。
2、调整施工环境温度,不能低于10℃。
3、调整施工粘度。
4、检查被涂物表面是否平整,确保表面无异物附着。
PU油涂装常见弊病及处理方法
PU油涂装常见弊病及处理方法
弊病类别
弊病原因
排除对策
1、泛白/白化
空气湿度太大,涂膜中溶剂挥发吸收热量,使涂膜表面空气温度降低,而达到露点水蒸气渗入涂膜,造成局部或全部泛白。
1、施工环境湿度大。
2、环境温度高,溶剂挥发太快,导致涂膜表面干燥速度太快。
3、稀释剂溶解力不够。
3、调配好涂料的施工粘度适量调整稀释剂和固化剂的添加量。
4、选择合适口径的喷枪。
5、做最后一道面漆使用时粘度要低。
6、避免在高温或风速太快的环境中涂装。
7、选用配套稀释剂,被涂物表面处理平整。
8、待下层涂料充分干燥后在上涂。
9、尽量避免不良环境下施工,温度尽量保持25±5℃。
弊病类别
弊病原因
排除对策
1、下涂要充分干燥后再进行上涂。
2、改用稍快干的稀释剂,不能让稀释剂残留在涂膜中。
3、使用强力头度底漆将木材固化。
4、木材涂装前需完全干燥,选用含水率及收缩性合适的木材。
6、咬底
上涂后底涂局部或全部被溶解而隆起。
1、底层与面层涂料不配套。
2、底面涂层间隔时间短,底层未处理好,底层硬化太多。
1、底层与面层涂料要配套。
4、加强换气设备减少涂装室,室内涂料及被涂物之间的温差。
5、施工中涂料应多次充分搅拌均匀。
8、桔皮
涂膜干燥硬化时涂膜表面发生局部或全部桔子皮状的凹凸面。
1、施工环境温度高,溶剂挥发
涂料流平不好,稀释剂添加少施工粘度高。
2、固化剂添加过量,涂膜干燥太快。
3、喷枪口径选择不当,喷涂距离不当或过快,空气压力不够太大或太低雾化不良,喷涂时喷雾粒子附着喷板运行速度太快且不均匀,一次喷量太少不够覆盖被涂面。
9、干燥不良
打磨粘砂纸涂装后经过一点时间或规定时间后涂膜尚未完全硬化。
1、PU稀释剂溶解力不够,不能完全溶解PU涂料,使PU涂料中OH和NCO不能完全接触发生化学交联反应。
2、反应型体系固化剂添加不够,有剩余树脂未参加反应或树脂类型与硬化剂成分类型不匹配,不能在常温下完全交联反应。
3、施工环境空气湿度太大,或涂料溶剂含水率高。
2、避免高温高湿环境施工及放置刚喷涂过的物件,一次喷涂不要太厚,不超过30微米,调整稀释剂挥发速度,避免表干太快。
3、定时定期排放压缩机中的水份。
4、喷涂前做好对底材的封固填充。
3、回粘
涂膜干燥后经重叠或包装一段时间后,发现涂膜表面局部或全部粘附有包装纸的痕迹。
1、途层未干透即重叠或包装。
2、涂料溶剂中慢干溶剂过多,挥发不彻底。
4、涂装环境过度Βιβλιοθήκη 风,被涂物温度太高时溶剂挥发过快流展性不良。
5、被涂物表面处理不平整,影响流平性,稀释剂不配套,溶解力不良,涂料放置时间太久。
6、下层涂膜干燥不完全,上层涂料侵蚀下层涂料。
1、合理配套使用稀释剂,适量添加慢干水,溶解力和挥发速度适宜。
2、通过合理调整涂料中各成分的比例及选择添加合适的流平剂改善涂料流平性。
2、气泡、起痱子
涂膜干燥后,涂膜内及表面局部或全部出现微小气泡。
1、硬化剂加入体系搅拌后静置时间不够,空气压力过高,涂料中混入过多空气。
2、施工环境温度太高,湿度太大。涂膜太厚,表干太快。
3、压缩空气中水混入涂膜被涂物表面有油污或水份。木材或被涂物含水量过高。
4、木材表面封固填充不良,产生气泡。
1、调配搅拌均匀涂料静置15分钟,调整好空气压力。
3、固化剂添加量不够。
4、气候冲突温度过高或雨季施工。
1、待涂层干透后才包装。
2、合理使用稀释剂,慢干水不要添加过量。
3、正确调合比例配套油漆。
4、保证环境通风,保证涂膜中溶剂挥发完全。
5、延长涂膜的干燥时间或适当加温。
4、缩孔/火山口
被涂面上有栗状,至小豆粒大之凹穴且不均匀附着成点状,或似火山口有如麻脸状模样。
5、调整空气压力,保证良好雾化效果。
6、处理好油水分离器,防止水份混入其中。
弊病类别
弊病原因
排除对策
6、下陷
涂膜干燥后或长时间后,肉身光泽及平坦性丧失,涂膜凹陷。
1、涂料固含低。
2、稀释剂慢干。
3、木材含水率太多,收缩性太大,柔软木材吸进涂料太多。
4、各涂层间干燥不完全,就进行涂装。
5、整个涂层过程涂膜喷涂太薄。