PU油涂装常见弊病及处理方法
喷涂涂层常见的弊病及排除方法

喷涂涂层常见的弊病及排除方法1.涂层起泡造成涂层起泡的原因有多种,主要包括涂装前表面处理不当、涂装环境湿度过高、涂料粘度过低、涂层固化不充分等。
解决方法:(1)加强涂装前的表面处理,确保基材表面干燥、清洁和粗糙度适宜;(2)控制涂装环境湿度,避免过高湿度对涂层的不利影响;(3)调整涂料的粘度,一般情况下应适度增加涂料的粘度;(4)确保涂层充分固化,避免固化时间过短或过长。
2.涂层脱落涂层脱落的原因可能是涂装前基材表面处理不当、涂料粘度过低、涂装厚度不均匀、涂装环境温度过低等。
解决方法:(1)加强涂装前的表面处理,确保基材表面干燥、清洁和粗糙度适宜;(2)增加涂料的粘度,增强涂料与基材的附着力;(3)控制涂装厚度均匀,避免涂层厚度不均匀导致附着力不足;(4)控制涂装环境温度,避免涂料在过低温度下固化不完全。
3.涂层裂纹涂层出现裂纹的原因可能是涂装厚度过大、涂装环境湿度过大或温度过高、涂料固化时间过短等。
解决方法:(1)控制涂装厚度,避免过大的涂层压力导致裂纹;(2)控制涂装环境湿度和温度,避免过大的温度或湿度对涂料的不良影响;(3)确保涂料充分固化,避免固化时间过短而导致裂纹。
4.色差涂层出现色差的原因可能是涂料的颜料混合不均匀、涂装厚度不均匀、涂装环境湿度或温度变化大等。
解决方法:(1)充分搅拌涂料中的颜料,确保颜料混合均匀;(2)控制涂装厚度均匀,避免出现浅或深的涂层颜色;(3)控制涂装环境湿度和温度的变化,避免湿度和温度的变化对颜色产生影响。
5.涂层粘度过高或过低涂层粘度过高或过低可能是涂料配方不当、溶剂挥发速度过快或过慢等原因。
解决方法:(1)调整涂料的配方,确保涂料粘度适宜;(2)控制涂料中溶剂的挥发速度,避免过快或过慢导致粘度异常。
常见涂装弊病及防止措施
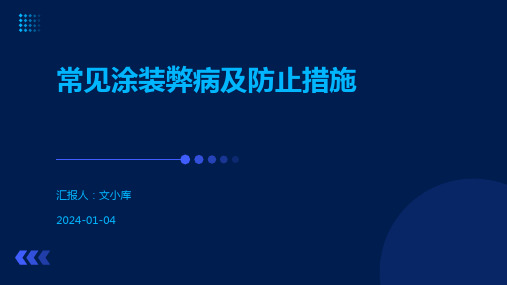
选择合适的涂料
总结词
选择合适的涂料是防止涂装弊病的关键。
详细描述
根据涂装需求和涂装对象的特点,选择符合要求的涂料类型和品牌,确保涂料的质量和性能满足使用 要求。同时,要注意涂料的配套性和相容性,避免因涂料不匹配导致涂层起泡、开裂等问题。
控制涂装环境
总结词
控制涂装环境是保证涂装质量的重要措施。
详细描述
涂装环境应保持清洁、干燥、无尘,温度和湿度要适宜。过高的温度、过低的湿度或灰尘污染都可能导致涂层表 面出现颗粒、不平整等问题。同时,要避免在雨天、雾天或强风中进行涂装作业,以免影响涂层质量。
提高涂装技术水平
总结词
提高涂装技术水平是防止涂装弊病的根 本途径。
VS
详细描述
加强涂装工人的技能培训和技术交流,提 高他们的操作水平和责任心。采用先进的 涂装技术和设备,如静电喷涂、自动涂装 线等,提高涂装的均匀性和平整度。同时 ,要严格执行涂装工艺规程,确保每道工 序的质量控制。
加强涂装后保养
总结词
加强涂装后保养是防止涂装弊病的重要环节 。
详细描述
按照保养要求定期对涂层进行保养和维护, 保持涂层的完整性和美观度。避免硬物刮擦 、高温烘烤和化学腐蚀等损害涂层的行为, 及时修复损坏的涂层,延长涂层的使用寿命 。同时,要注意对保养材料的选用和质量把 控,确保保养效果。
04
涂装弊病的修复方法
THANKS
谢谢您的观看
常见涂装弊病及防止措施
汇报人:文小库 2024-01-04
目录
• 涂装弊病概述 • 常见涂装弊病 • 防止涂装弊病的措施 • 涂装弊病的修复方法
01
涂装弊病概述
涂装弊病的定义
01
涂装弊病是指在涂装过程中出现 的质量问题,如表面缺陷、颜色 不均、起泡、脱落等。
PU油涂装常见弊病及处理方法

PU油涂装常见弊病及处理方法1.喷涂面积不均匀:在PU油涂装过程中,由于喷枪与被喷涂面的距离不一致、喷枪喷射角度不正确等原因,导致喷涂面积不均匀。
解决方法是调整喷涂距离和喷涂角度,保持一定的喷枪与被喷涂面之间的距离,并且始终保持垂直喷涂。
2.皱纹和起泡:PU油涂装中常见的问题是产生皱纹和起泡。
这通常是由于涂装过程中涂料膜的流动受到限制,或者底材的湿度过高等原因引起的。
处理方法是在涂装前要确保底材的湿度适当,并控制好涂装环境的温度和湿度;此外,涂装时要保持一定的速度和涂装厚度,以免涂料膜流动不畅导致皱纹和起泡。
3.色差:PU油涂装过程中,由于施工工艺和材料的差异,可能会出现色差问题。
对于家具、地板等大面积产品,色差可能会影响产品的外观质量及市场竞争力。
解决方法是选择合适的涂料配方和材料,使用相同的施工工艺和条件涂装,确保涂装前底材的质量均匀,避免涂料分层和色差的发生。
4.不良粘附和剥离:PU油涂装中,不良粘附和剥离是常见的问题。
通常是由于涂料和底材之间的附着力不好导致的。
处理方法是在涂装前要对底材进行适当的处理,如磨砂、除尘等,以提高涂料和底材之间的附着力;此外,在涂装过程中要严格控制涂料的涂装厚度,避免过厚导致涂料的粘附力减弱。
5.细纹和裂纹:PU油涂装过程中,细纹和裂纹是常见的问题,特别是在涂装后的干燥阶段。
这通常是由于涂料的收缩性或者环境的干燥程度不当导致的。
解决方法是在涂装前,对底材进行适当的处理,提高涂料的附着力和弹性。
在涂装过程中,要控制好涂料的厚度,避免涂装层过厚,同时要控制好涂装后的干燥环境,保持适当的湿度和温度。
总结起来,PU油涂装常见的弊病有喷涂面积不均匀、皱纹和起泡、色差、不良粘附和剥离、细纹和裂纹等。
解决这些问题的关键是在涂装前正确处理底材,选择合适的涂料配方和工艺,并严格控制涂装过程和环境条件。
只有在涂装过程中做到细致入微的管理,才能保证PU油涂装的质量和效果。
涂膜常见弊病的形成原因及解决措施

一致的观点。
为了研究磷化膜的抗碱性能,为人们提供一种选择阴极电泳涂装前磷化液的方法,日本学者在对锌系磷化膜成份进行分析的基础上,提出P比概念。
所谓“P”比,即P比=P/(P+H)×100%,其中:P=磷酸锌铁(Zn2Fe(PO4)2·4H2O)的(100)晶面X射线衍射峰强度;H=磷酸锌(Zn3(PO4)2·4H2O)的(020)晶面X射线衍射峰强度。
P和H两种磷化膜成份,在pH值大于11以后的溶解程度相关很大。
(如图所示)。
H成份的溶解度直线上升,而P成份的溶解度几乎没有变化。
根据这一规律,磷化膜的P含量高,即P比值大,磷化膜的抗碱性能就好,在阴极电泳过程中磷化膜的溶解程度就低,与阴极电泳漆膜的附着力就好,耐蚀性就高。
那么,磷化膜的P比应是多少才能满足阴极电泳涂装的需要呢?理论研究和实践证明,P比应大于85%。
其磷化膜的微观结构呈柱状或粒状。
所谓柱状是指磷化膜晶体呈小柱;所谓粒状是指磷化膜晶体呈小圆粒。
这两种晶体磷化膜的共同特点是:膜层薄,重量轻,机械性能好,与漆膜结合力强。
获得柱状或粒状磷化膜的常用方法是从以下几个方面入手:①选用低锌磷化液,最好是低锌含锰磷化液。
因为这种磷化液所形成的多晶结构复合层,与普通低锌磷化液比较其抗碱性、漆膜附着力、耐蚀性和机械性均更好;②磷化温度在50-60℃。
需要指出的是,不能把P比作为检验阴极电泳涂装前磷化膜质量的唯一标准。
这是因为:①P比是在特定分析条件下所产生的独特X射线衍射强度比率,按照Miawahi的定义,P比值是精密的,不应与从磷化膜中的H和P的实际容量的比相混淆;②磷化液中加入某些元素,如Mn、Ni、Ca等元素也能改善磷化膜的耐蚀性;③磷化方式、槽液温度、槽液变化、促进剂种类及含量等都有可能影响磷化膜耐蚀性;④实践中远有出现磷酸锌膜的抗碱性也良好的现象;⑤高P比磷化膜与阴极电泳涂装后,并不能肯定等于整个涂层就有良好的耐蚀性。
PU防水涂料应用中常见的质量问题及防治

PU防水涂料应用中常见的质量问题及防治1.沉淀问题:是PU防水涂料使用中反映最多的问题,产生的原因在于涂料中的填料因密度大于聚氨酯胶液的密度。
沉淀分两种,硬沉淀和软沉淀。
硬沉淀是指填料已经和胶液混凝成固体,成为废料;软沉淀指经过在分散(搅拌)填料可以重新均匀地回到胶液中,仍是合格产品。
防止沉淀的措施:1.科学的生产配方和工艺;2.工地存放可采用倒放;3.定期翻桶或使用前翻桶;4.采用机械搅拌之后在使用,并保证在40MIN内用完。
2.结膜问题:PU结膜的根本原因在于包装桶密封不严或漏气。
双组份聚氨酯由A/B组份产生化学反映,反应后的产物是固体极为涂膜。
单组份聚氨酯与空气中的水分发生化学反应而成膜。
结膜的防治:1.生产工艺严禁带入水分;2.采用质量较好的包装桶;3.倒置放置;4.尽量装满;5.避免暴晒。
3.与基层粘接不好,鼓泡:粘接不好的原因1.基层处理达不到要求;2.基层含水率太高,双组份聚氨酯遇水化学反应,生成气体产生气泡;单组份聚氨酯在基面太潮,水分大于化学反应所需,成膜之后,在涂膜下面尚存多余水分,受热汽化,体积膨胀形成空鼓。
3.施工操作不当,前遍涂料未干,即涂后一遍、或一次涂抹太厚,下面的液体或基层中的水分挥发,使涂膜粘接不良,甚至空鼓。
4.乱接稀释剂,为了涂刮快速和省力,在涂料中加入一定稀释剂。
稀释剂在挥发过程中回事涂膜起泡。
避免和治理粘接不良的措施:1.基层凹凸不平、蜂窝麻面等用水泥砂浆修补平整,浮浆杂物清除干净;2.基层干燥,含水率小于8%(含水率检查可同热熔卷材施工),单组份聚氨酯对基层含水率的要求不如双组份聚氨酯严格;3.分遍刮涂,一次不得刮涂太厚且待前一遍干后在刮涂下一遍;4.慢干和不干或不凝:可能是配方问题或生产工艺不当还可能是施工工艺不规范。
聚氨酯涂料的施工要点及缺陷产生的原因及预防措施

聚氨酯涂料的施工要点及缺陷产生的原因及预防措施摘要:夏季使用聚氨酯类油漆进行涂装施工或进行涂层修补时,漆膜经常出现暗泡、针孔等弊病,俗称“热痱”、“痱子”。
为减少针孔产生,一般喷漆后进入烘干室前,都要保证湿漆膜有10min左右的溶剂挥发时间(称为闪干时间或流平时间),这样就可能使有些人认为增加闪干时聚氨酯树脂涂料在很多领域都有着广泛的应用,它有着优良的性能,种类也非常的多。
聚氨酯涂料属反应性涂料,涂饰质量还涉及涂饰施工的种种客观因素,需要注意一些施工要点,使涂饰质量良好。
在涂饰后,会有一些缺陷产生,分析其缺陷产生的原因并对之提出预防措施。
关键词:聚氨酯涂料;施工要点;缺陷及其产生的原因;预防措施。
聚氨酯树脂是第二次世界大战时期发展起来的树脂,但直到近几十年来,由于生产的主要原料二异氰酸酯的价格在不断下降,所以使聚氨酯树脂在涂料、胶料、塑料、橡胶等行业得到越来越广泛的应用。
我国从1958年开始研制聚氨酯树脂涂料,1968年上海地区家具行业研制出685聚氨酯树脂涂料进行试用,取得很好的涂饰效果,便很快在上海地区家具行业普遍推广试用。
到1980年后逐步在全国家具行业获得广泛应用。
因聚氰酸酯具有较活泼的化学反应性,可与不同的聚酯、聚醚、多元醇及其他合成树脂配合使用,制出很多种类的聚氨酯涂料。
聚氨酯涂料在飞机、船舶、车辆、木材、塑料、橡胶、皮革、建筑物涂装、防腐涂装等都有着广泛的应用。
本文主要介绍其在木器产品中的施工要点及缺陷产生原因和预防措施。
1、聚氨酯涂料简述聚氨酯树脂涂料是聚氨基甲酯树脂涂料的简称。
它是以多异氰酸酯跟多羟基化合物反应而制得的,含有氨基甲酸酯为主要成膜物质的涂料,是一种含有氨基甲酸酯链节的高分子化合物。
聚氨酯树脂的涂膜具有优良弹性、坚韧、耐磨、耐候、耐腐蚀及较好的装饰性,可根据使用要求制成多种新型涂料,应用十分广泛。
聚氨酯涂料的种类很多,在木制品中常用的有聚氨脂油、潮气固化聚氨酯和双组分聚氨酯。
PU油涂装常见弊病及处理方法
PU油涂装常见弊病及处理方法
首先是起泡问题。
起泡通常是由于施工操作不当或基材表面存在污染物导致的。
处理方法如下:
1.确保施工环境清洁整洁。
去除空气中的尘埃和其他杂质。
2.涂装前,对基材表面进行充分的清洗和打磨,确保表面光滑。
3.温湿度适宜,避免高温高湿的环境。
其次是颜色不匀问题。
PU油涂装在施工过程中易出现色差。
处理方法如下:
1.涂装前进行试样,确认颜色是否符合要求。
2.在批量涂装前对颜料进行充分的搅拌,确保颜色均匀。
3.将颜色不匀的部分重新涂装,涂装时注意均匀施工。
再次是粘连问题。
PU油涂装出现粘连通常是涂装层干燥不完全引起的。
处理方法如下:
1.适量调整涂料的稀释剂比例,确保涂料干燥时间适中。
2.涂装后保持适当的通风,促进涂料的干燥。
3.在使用PU油涂装时,可以添加干燥剂来加速涂料干燥。
最后是发白问题。
PU油涂装出现发白通常是由于施工环境温度过低引起。
处理方法如下:
1.涂装前检查施工环境温度,确保温度适宜。
2.如果环境温度过低,可以使用加热设备提高温度。
3.在涂装前使用底漆进行底层处理,能够有效预防发白问题。
总之,PU油涂装常见的弊病有起泡、颜色不匀、粘连和发白。
针对这些问题,需要加强施工操作、调整涂料稀释剂比例、保持适宜的温湿度以及添加干燥剂等。
只有确保涂装过程的规范和细致,才能避免这些问题的发生,从而得到理想的涂装效果。
涂装作业过程常见的弊病及应对方法
涂装作业过程常见的弊病及应对方法⑴流挂:指涂料施于垂直面时,由于其抗流挂性差或施涂不当,漆膜过厚等原因而使湿漆膜向下移动,形成各种形状下边缘厚而不均匀涂层。
导致原因:①操作不好,喷枪口枪太大;②涂料太稀;③涂装物表面太平整;④涂层太厚,薄刷多遍。
⑵发白:指有光涂料干燥过程中,漆膜上有时呈现乳白色现象。
导致原因:①水分浓度过高;②溶剂解析力不够;③基材本身水分含量过高。
⑶起皱:指漆膜呈现多少有规律的小波幅波纹式的皱纹,它可深及部分或全部膜厚。
导致原因:①底漆、面漆干燥速度不一致;②涂层太厚,黏度过高;③喷嘴未调节好;④PU类的涂料固化剂加太多,干燥速度太快。
⑷桔皮:指漆膜呈现桔皮状外观的表面病态。
导致原因:①流平性不好;②温度低;③NC类稀释剂过多或不配套;④基材不平或处理不好。
⑸咬底:指在干漆膜上施涂其同种或不同种涂料时,在涂层施涂或干燥期间使其下的干燥膜发生软化,隆起或从底材上脱离的现象。
导致原因:①两种不配套的底漆和面漆(通常含量高的做底漆);②底未完全干燥就上面漆;③底漆的涂层太厚。
⑹针孔:指在漆膜中存在着类似于针刺的细孔。
导致原因:①搅拌均匀,涂料内部有空气;②油污水分污染;③被涂物表面不平整;④喷太厚,溶剂不好挥发。
⑺起泡:指涂料在施涂过程中形成的空气或溶剂蒸气等气体或者兼有的泡。
导致原因:①被涂物有水分;②涂料有水分;③空气湿度大;④油污;⑤稀释剂、固化剂不配套;⑥搅拌不均匀,表面不平。
⑻表面粗糙:导致原因:①施工环境太脏,不够清洁;②涂物中本身细度不够,被涂物表面有赃物;③涂层不够。
⑼开裂:指漆膜出现不连续的外观变化。
导致原因:①涂层太厚,涂料过期;②涂料太厚,涂料本身硬度高,较脆;③促进剂含量过高;④面漆固含量低,树脂本身有问题以及外部环境。
⑽起皮:导致原因:①被涂物面层水分太高;②未经过封油处理;③底漆未干涂面漆;④两种不配套的底漆和面漆。
⑾跑油:导致原因:①涂料中有水或油渣;②被涂物有油渣,蜡质;③涂料黏度过高或过低。
常见涂装弊病及防止措施
(3)选用的漆刷太大、毛太长、太软或刷油 时蘸太多,使漆面厚薄不一,较厚处就要流淌。
因 (4)刷涂面凹凸不平或物体的棱角、转弯、
线角的凹槽处,容易造成涂刷不均厚薄不一, 较厚下就要流淌。
(5)被刷涂表面不洁,有油、水等污物,刷 涂后不能很好地附着而流淌
油漆流坠(流挂、流淌)
(2)木材质地不同,着色不均匀,局部着色
因 过深。木材材质软者易着色。材质硬者不易着
色。
(3)操作技术不熟练,重刷处色深,刷毛太 硬或太软也容易造成色泽不一致。
木纹浑浊
(1)使用底、面着色剂时,应将其搅拌 对 均匀,以保证其颜色均匀一致。
(2)对于不同的材质基层,应选用不同 策 施工方法着色,操作要熟练重叠反复刷涂,
八、透 底
刷涂时涂层未能将基材表面或上道涂层表面覆盖严实, 而露出基材颜色或底层涂料颜色的现象,称为透底
(1) 涂料太稀,遮盖力差,一次性刷涂量 原 过少。
(2) 基层表面太光滑油污等 ,漆膜难以覆 因 盖。
(3) 基层表面或上道涂层颜色较深,表面 刷涂浅色涂料时覆盖不住,使底色显露。
在雨雾、潮湿、黑暗、烈日曝晒等恶劣条件下施工。施工
场所要保持空气流通。
(6)漆膜有轻微慢干或发粘时,可加强通风,适当升高 环境温度,加强保护,观察一段时间,如确实不能干燥结 膜,再做处理。若慢干、回粘严重时要用强溶剂洗掉刮净,
重新刷涂。
十、桔 皮、鸡皮
涂膜表面呈现许多半圆形突起,形似桔皮斑纹状
残碱等,影响了漆膜的附着力,漆膜的表面张力 使漆膜收缩”发笑”。
因 (3)涂层太薄或溶剂选用不当,挥发过快,涂
层来不及流平。 (4)涂料粘度小,对底层润湿性差,刷涂时不
聚氨酯喷涂施工时常见问题及其发生的原因
聚氨酯喷涂施工中常常会遇到许多的问题,那么这些问题有哪些呢?又是如何发生的呢?这里主要指泡沫表现的问题,现分述如下。
1.泡沫表面粗糙不整。
引起这种现象的原因主要是雾化不良,尤其是国产气混式喷涂机较常见,可适量调整空压机的背压和距基材的距离,有条件的话可以适当加长气混喷头及减小嘴径。
进口高压喷涂机则可适当远离基材。
另一原因是发泡时间太快以及黑白料黏度差异过大。
2.泡沫软。
检查一下黑白料比例,一般是白料过多引起的。
建议先按照正确的比例做一个自由发泡试验,如果仍偏软,则可适当提高黑料比例;如果仍然软,则需检查白料使用的原料中是否应适当增加胺醚(即乙二胺为起始剂的聚醚)的量。
3.泡沫酥脆。
此时的泡孔一般比较粗大,引起的原因是体系中水分含量过大。
如果是仅仅表面部分酥脆,则考虑料温和环境温度差异是否太大,料温高、环境温度低。
另一个原因是黑白料黏度差异过大,黑料过量较多。
4.泡沫与基材的剥离强度低。
出现的原因有:基材表面不洁净,有浮灰或油污;基材未于透,这种剥离可见到界面的水分;另外还有基材温度过低,发泡速度太快;喷涂时没有“打底”(即首先快速喷上薄薄底层),而是一次就喷得较厚也会造成张力过大而剥离。
5.泡沫开裂。
现场可明显看到裂开的缝隙,这种现象主要是由发泡体系中使用的聚醚支化度和官能度较低而引起的,可适当加入蔗糖、甘露醇及山梨糖醇为起始剂的聚醚。
另外在施工时适当增加喷涂层数,避免一遍起发的现象。
6.层与层之间脱离。
在每一遍喷涂相连接的界面上出现的不粘接现象。
这一现象的出现与发泡料的体系有关,比如有些阻燃剂与发泡体系不太相容,发泡时在表面像增塑剂那样,当然也有其他的物料会引起这种现象。
另外发泡的时问太快或太慢都可能会引起这种现象。
只是程度不至于这么严重而已。
还有时是由于发泡体系中加入的硅油表面活性剂过量产生的。
7.泡沫表面起泡。
这一现象有时在完成喷涂后即可出现,也有的在数小时之后才出现,严重的会凸起一个个较大的“包”,这是由于发泡料中发泡剂种类与体系不相容,在发泡完成后又聚积第二次发泡,应该使发泡剂与聚醚及助剂相配套使用,在施工现场遇到这种现象的权宜之计是适当增加发泡层数,降低热量聚积。
- 1、下载文档前请自行甄别文档内容的完整性,平台不提供额外的编辑、内容补充、找答案等附加服务。
- 2、"仅部分预览"的文档,不可在线预览部分如存在完整性等问题,可反馈申请退款(可完整预览的文档不适用该条件!)。
- 3、如文档侵犯您的权益,请联系客服反馈,我们会尽快为您处理(人工客服工作时间:9:00-18:30)。
2、施工环境温度太高,湿度太大。涂膜太厚,表干太快。
3、压缩空气中水混入涂膜被涂物表面有油污或水份。木材或被涂物含水量过高。
4、木材表面封固填充不良,产生气泡。
1、调配搅拌均匀涂料静置15分钟,调整好空气压力。
PU油涂装常见弊病及处理方法
弊病类别
弊病原因
排除对策
1、泛白/白化
空气湿度太大,涂膜中溶剂挥发吸收热量,使涂膜表面空气温度降低,而达到露点水蒸气渗入涂膜,造成局部或全部泛白。
1、施工环境湿度大。
2、环境温度高,溶剂挥发太快,导致涂膜表面干燥速度太快。
3、稀释剂溶解力不够。
4、涂料或稀释剂含水量高。
5、一次涂装太厚。
3、调配好涂料的施工粘度适量调整稀释剂和固化剂的添加量。
4、选择合适口径的喷枪。
5、做最后一道面漆使用时粘度要低。
6、避免在高温或风速太快的环境中涂装。
7、选用配套稀释剂,被涂物表面处理平整。
8、待下层涂料充分干燥后在上涂。
9、尽量避免不良环境下施工,温度尽量保持25±5℃。
弊病类别
弊病原因
排除对策
2、底层一次涂装不超过30微米。
3、要底层实干后再上涂面漆,底层涂料要硬化充分。
4、留在基材孔外的填充剂要处理干净。
7、流挂/垂流
被涂物垂直或倾斜,面涂装时涂料的粘度与干燥度不平衡或涂装要领不佳,涂膜呈长柱或淋幕状垂直下垂或流涎尤其在边缘部分有流痕。
1、稀释剂添加过量,涂料施工粘度低,一次喷涂太厚或间隔时间太短。
4、涂装环境过度通风,被涂物温度太高时溶剂挥发过快流展性不良。
5、被涂物表面处理不平整,影响流平性,稀释剂不配套,溶解力不良,涂料放置时间太久。
6、下层涂膜干燥不完全,上层涂料侵蚀下层涂料。
1、合理配套使用稀释剂,适量添加慢干水,溶解力和挥发速度适宜。
2、通过合理调整涂料中各成分的比例及选择添加合适的流平剂改善涂料流平性。
5、调整空气压力,保证良好雾化效果。
6、处理好油水分离器,防止水份混入其中。
弊病类别
弊病原因
排除对策
6、下陷
涂膜干燥后或长时间后,肉身光泽及平坦性丧失,涂膜凹陷。
1、涂料固含低。
2、稀释剂慢干。
3、木材含水率太多,收缩性太大,柔软木材吸进涂料太多。
4、各涂层间干燥不完全,就进行涂装。
5、整个涂层过程涂膜喷涂太薄。
3、固化剂添加量不够。
4、气候冲突温度过高或雨季施工。
1、待涂层干透后才包装。
2、合理使用稀释剂,慢干水不要添加过量。
3、正确调合比例配套油漆。
4、保证环境通风,保证涂膜中溶剂挥发完全。
5、延长涂膜的干燥时间或适当加温。
4、缩孔/火山口
被涂面上有栗状,至小豆粒大之凹穴且不均匀附着成点状,或似火山口有如麻脸状模样。
1、涂料先进先出,勿超过储存期。
2、稀释剂的溶解力作适当调整。
3、涂料调配时要充分搅拌均匀,避免局部胶凝,防沉剂类型,用量进行调整。
4、调整涂料各成分之搭配。
6、空压机中油水分离器未定时放水,水份随空气带入涂料。
7、涂装室通风太快。
1、调整施工环境湿度或温度,如温湿度特别大,应停止施工。
2、容器与涂料避免混入水份,涂料稀释剂避免露天存放会侵入湿气。
3、湿度高时避免厚涂。
4、定时排放空压机中的水份。
5、避免雨天或高温环境下施工。避免傍晚施工。
2、气泡、起痱子
2、避免高温高湿环境施工及放置刚喷涂过的物件,一次喷涂不要太厚,不超过30微米,调整稀释剂挥发速度,避免表干太快。
3、定时定期排放压缩机中的水份。
4、喷涂前做好对底材的封固填充。
3、回粘
涂膜干燥后经重叠或包装一段时间后,发现涂膜表面局部或全部粘附有包装纸的痕迹。
1、途层未干透即重叠或包装。
2、涂料溶剂中慢干溶剂过多,挥发不彻底。
9、干燥不良
打磨粘砂纸涂装后经过一点时间或规定时间后涂膜尚未完全硬化。
1、PU稀释剂溶解力不够,不能完全溶解PU涂料,使PU涂料中OH和NCO不能完全接触发生化学交联反应。
2、反应型体系固化剂添加不够,有剩余树脂未参加反应或树脂类型与硬化剂成分类型不匹配,不能在常温下完全交联反应。
3、施工环境空气湿度太大,或涂料溶剂含水率高。
2、喷涂距离太近移动速度慢,喷涂出油量大,喷涂空气压力不均匀。
3、被涂物表面过于光滑。
4、涂料中溶剂挥发太慢。
5、涂装环境充满溶剂蒸气。
6、环境温度太低时更易发生,涂装室涂料及被涂物温差大。
1、调整合适粘度,一次喷涂厚度不超过30微米。
2、控制好喷涂出油量,保持稳定的空气压力,掌握好重涂间隔时间。
3、保持被涂物表面适当的粗糙度各层重涂之间要仔细打磨。
1、下涂要充分干燥后再进行上涂。
2、改用稍快干的稀释剂,不能让稀释剂残留在涂膜中。
3、使用强力头度底漆将木材固化。
4、木材涂装前需完全干燥,选用含水率及收缩性合适的木材。
6、咬底
上涂后底涂局部或全部被溶解而隆起。
1、底层与面层涂料不配套。
2、底面涂层间隔时间短,底层未处理好,底层硬化太多。
1、底层与面层涂料要配套。
1、涂料自身流平差。
2、被涂物施工环境温度过高。
3、涂料粘度过高或过低。
4、被涂物表面粗糙打磨不完整。
5、空气压力太大,喷枪与被涂物距离太近。
6、被涂物表面被污染,有油渍。
1、涂料中适当添加流平剂。
2、调整施工环境温度,不能低于10℃。
3、调整施工粘度。
4、检查被涂物表面是否平整,确保表面无异物附着。
4、施工环境空气湿度太大,导致稀释剂挥发太慢,温度太低从而影响反应速度。
5、一次喷涂太厚或层涂间隔时间短,以至下涂不干燥。
6、砂纸回潮,砂纸型号不恰当,打磨方法不当。
7、通风不足,稀释剂的蒸气充慢整个空间使溶剂挥发缓慢影响干燥。
1、选用溶解力强挥发稍快的稀释剂。
2、选用配套固化剂,避免增加或减少固化剂。
4、加强换气设备减少涂装室,室内涂料及被涂物之间的温差。
5、施工中涂料应多次充分搅拌均匀。
8、桔皮
涂膜干燥硬化时涂膜表面发生局部或全部桔子皮状的凹凸面。
1、施工环境温度高,溶剂挥发
涂料流平不好,稀释剂添加少施工粘度高。
2、固化剂添加过量,涂膜干燥太快。
3、喷枪口径选择不当,喷涂距离不当或过快,空气压力不够太大或太低雾化不良,喷涂时喷雾粒子附着喷板运行速度太快且不均匀,一次喷量太少不够覆盖被涂面。
3、注意施工环境的湿度,增设空气抽湿装置或强制干燥,提高施工环境温度或延长干燥时间。
4、采用2次或多次喷涂延长层涂间隔时间。
5、选用恰当型号的砂纸,按木版纹理方向顺木版纹打磨。
6、适当通风。
10、结块/沉淀
颜料、树脂等形成硬沉淀结余罐底。
1、储存时间过长。
2、稀释剂溶解力不当。
3、防沉淀效果不佳。
4、涂料自身成分搭配不佳。