末件确认规范
首末检管理规定
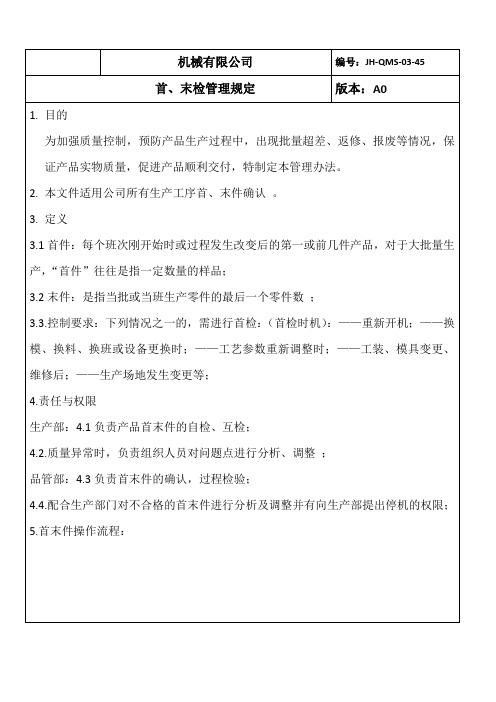
4.2.质量异常时,负责组织人员对问题点进行分析、调整 ;
品管部:4.3 负责首末件的确认,过程检验;
4.4.配合生产部门对不合格的首末件进行分析及调整并有向生产部提出停机的权限;
5.首末件操作流程:
流程图 产前准备
首件生产
NG
自检
OK NG
组长确认
机械有限公司
编号:JH-QMS-03-45
首件流程图
生产部
操作工对首件生产的产品进行检验,确认符 合技术要求和工序要求,填写《自检记录表》 并签名(尺寸需填写具体测量数值)
生产部
《自检记录表》
班组长确认操作工每个首件都有做检验,并 对操作工的首件检验结果做确认签字
生产部
《自检记录表》
OK OK
QC 确认
QC 对生产的《自检记录表》做确认,确认 车间有正常进行首件自检工作,并核对检验 结果后在《自检记录表》签字
版本:A0
说明
责任部门
相关记录
班、组长对操和工进行必须的岗前培训,准 备好生产所需的技术文件和工装治具,并确 认文件和治具正确性和适用后,派发给操作 工,作业前对人、机、料、法、环进行确认
生产部
《作业准备验证记录表》
经培训合格的员工允许上岗,并按照技术资 料和步骤,第个独立的作业单位首先生产第 一件产品
产,“首件”往往是指一定数量的样品;
3.2 末件:是指当批或当班生产零件的最后一个零件数 ;
3.3.控制要求:下列情况之一的,需进行首检:(首检时机):——重新开机;——换
模、换料、换班或设备更换时;——工艺参数重新调整时;——工装、模具变更、
维修后;——生产场地发生变更等;
4.责任与权限
生产部:4.1 负责产品首末件的自检、互检;
首中末件检验规范 (1)

首中末件检验规范(IATF16949-2016/ISO9001-2015)1.0目的和范围本办法规定了生产线首、中、末件的定义以及检查要求。
本办法适用于各车间/生产线的整个生产过程。
2.0定义本办法采用下列定义:2.1首件为以下情况下生产的第一件产品:(a)每班开始操作时;(b)设备调整时;(c)加工方法变化时;(d)加工条件变化时;(e)作业方法变化时;(f)更换模具时;(g)设备故障修理后再次运转时;(h)更换操作人员时。
(i)容量为每机台/3件。
(h)首检时间为接班后半小时内.2.2中件每班午休后生产的第一件产品。
正常生产时中检容量为每机台/3件,巡检时间为下午13:00。
2.3末件正常生产时的最后一件产品。
正常容量为每机台/3件2.4如发生(b)-(h)中任何一项变化,需重新按本定义对产品进行行首,中,末检查。
3.0职责3.1品质部对本办法负管理职责,并保证贯彻执行;3.2生产线班长、操作人员和检验员对正确执行本办法负责。
4.0实施办法4.1 首、中、末件检查文件编制4.1.1产品/过程开发工程师负责根据产品质量特性的重要性编写首、中、末件检查文件。
4.1.2首、中、末件检查文件由质量部检验员校对,质量工程师审核、品质部长批准后实施。
4. 2首、中、末件检查基准文件更改首、中、末件检查基准文件发生更改时,过程工程师填写更改单一式三份,经检验员校对,质量工程师审核,品质部长批准后实施更改,更改单由车间、品质部和管理员各保存一份。
4.3检查的实施4.3.1正常生产情况下每班应检查首、中、末件。
4.3.2在每半班发生2.1中(b)~(h)规定情况时,只检查首件、末件。
4.3.3操作工按照检查文件规定的项目对各工序产品/试件进行逐项检查,将检查的实际测量结果记录在三检表内。
4.3.4检查完毕后,针对有关键工序,例如注塑工序,应将产品/试件整齐地放在首、中、末件检查台上;其它工序,有检具的应放置在检具上,没有检具的可在适当位置放置,首件用黄色夹子,中件用白色夹子,末件用蓝色夹子标识,下料和包装工序可以整包标识,单独存放。
末件确认规范

1/2名 称3.2 注塑部----负责提供末件样品送检;3.3 模具车间---- 负责模具出入库的末件样品保管;作 业 规 范末件确认作业规范编 号Q/QJN375.005A-20121 目的 明确注塑制程中末件确认的方法与步骤,使制程作业规范,确保产品状态与模具异常能得到及时确认。
2 范围适用于注塑成型制程的末件检查确认;4 内容版 本A/1类 别页 码3 职责权限3.1 质量部---对末件进行确认,信息反馈,留样;4.2 末件确认时机:4.3 末件的检查容量一般为1模(若客户有特殊要求时,则按检验标准规定的容量);C ,计划性停机:计划性的切换停机;A ,突发性故障停机:如设备出现故障,短时间内不能再生产时;B ,任务完成停机: 本批订单任务完成时停机;存,样品交注塑部随模具一起入库,修模部负责将样品与模具一起存放;C,品管员确认NG时,品管员将NG品随同《制程异常通知单》应立即交注塑部处理,并追溯到异常产生的时间节点,班次等,对追溯到的可疑品应立即做好隔离标识,同时跟踪和监督整个过程,注塑部将已生产的可疑品根据最终的判定执行分拣,返工或报废处理;4.4 生产准备卸模时A,注塑部在决定卸模前,须将最后2模产品交品管员进行末件确认,即:依《制程检验标准书》、 图纸、留样进行确认(一般以外观,关键尺寸,实际的装配等为优先检查项);B,品管员确认OK时,签样1份,贴上样品标签,并填写《末件确认单》一份,交主管审核,内部自6 相关记录《末件确认单》《制程异常通知单》5 文件 《品质异常处理程序》D,确认产品需要改善但没有客户拒收的缺陷以外,即:影响过程控制的一些的轻微缺陷,或者依靠后道工序加工等,务必在末件确认之后,填写《制程异常通知单》随附需改善的样品交注塑部进行处理(如通知修模部改善模具);4.5 末件样品随模具一起入模具库保管,在下批生产随模具一起领出进行首件确认对比;。
首末件管理规定

首末件管理规定
1.目的
为防止正常生产时产生批量不合格,确保生产过程得到有效控制以及对产品标准中不能用文字表达或虽用文字表达,还不确切而又必须用实样来说明规定要求。
2.适用范围
适用于公司所有经客户认可、已批量供货的产品(包括半成品)。
3.职责
质量部归口管理。
4.名词解释
4.1首件:是换摸后调试后符合检验规范的第一个产品,此调试过程中产生的报废件不超过10个;
4.2末件:产品批次注塑结束前,正常生产状态时的产品。
5.程序
5.1在下列情况下需进行首件确认
5.1.1每批连续生产前;
5.1.2工艺更改后;
5.1.3原材料(油漆)更改后;
5.1.4生产流程更改后;
5.1.5设备或工装维修后;
5.1.6采用新的工装;
5.1.7其它能较大影响产品质量的情况。
5.2每班生产开始/批量生产开始由操作工检验,过程检验员参照生产样件和过程检验规范
对首件检验确认,并签字,做好首件产品检验记录。
5.3首件检验如出现不合格,生产部门应查明原因,采取纠正措施,然后重新进行首件确认,直到首件合格后才可批量生产。
5.4每班生产结束/批量生产结束前或批量生产意外中断,应做末件产品检验记录,具体操
作同首件检验;若末件产品合格,合格首件不加特别标识流入批量中。
5.5每班生产开始/批量生产开始或批量生产意外中断的再生产,若首件产品合格,合格末
件不加特别标识流入批量中。
5.6不合格末件由制造部保存,直到合格首件产生后进行其它处理。
6.相关文件
产品标识和可追溯规定
7.使用表单。
首末件管理规定

首末件管理规定
1.目的:
为加强产品质量控制,预防产品在生产过程中出现批量不良,在下次前处理好本次生产
过程中的问题点,确保下次生产时顺利进行,以达到降低成本、提高效率。
特制定本管
理规定。
2.
3.1
“首3.2
4
4.1
4.2
5.
5.1生产开始时根据本规定的第3.1条款,需要制作首件时,由生产部领班提供产品通报当班质检员进行首件检验。
5.1.1当班质检员接到生产部领班通知后,根据《生产指令单》和《检验指导书》对该机台的
产品进行检验判定。
5.1.2质检员需在10分内做出外观判定,20分钟内做出最终判定。
——仅供参考
5.1.3若检验结果符合要求的要及时做好首件样品(样品包括:日期、时间、质检员签名)和
加工样品并挂于相应的机台上,检验结果不符合标准要求的,质检员需立即通报生产
领班重新调试,重新报检。
5.2首件再确认:当首件确认合格后生产了1.5-2小时时,质检员要对生产中的产品进行一次再
确认,并做好样件。
5.3
5.5
——仅供参考。
首件尾件确认作业规范

4.0权责
4.1生产领班:制作首件、尾件,自行确认后通知IPQC进行再确认。
4.2品质IPQC﹕负责产线产品的首件、尾件确认并做好记录。
5.0作业内容
5.1首件确认时机
5.1.1批量正常量产的第一件或前几件;
5.1.2出现异常处理后正常生产的第一件或前几件;
5.4.2当品质IPQC确认首件、尾件发现不合格时,应立即通知产线停止生产并开出《品质异常单》,具体处置依据《不合格品管理程序》文件要求执行。
6.0相关文件
序号
文件名称
文件编号
6.1
《不合格品管理程序》
QEP-品-010
7.0相关表单
序号
表单名称
表单编号
文件/记录保存部门
文件/记录
保存期限
7.1
【前工序首件记录表】
【剥料首件/自主检查记录表】
QER-品-033
品管部
3年
7.13
【切脚自主/首件检查记录表】
QER-品-042
品管部
3年
7.14
【电性、外观自主首件检查记录表】
QER-品-043
品管部
3年
7.15
【编带首件自主检查记录表】
QER-品-044
品管部
3年
7.16
【品质异常单】
钉钉系统单
品管部
3年
5.3.2工序领班制作首件、尾件,自行确认后填写对应的首件、尾件记录单,并通知检验员进行再确认。
5.3.3品质IPQC接到产线的首件、尾件后,依照检验指导书进行确认并做好检验记录,经过品质IPQC确认合格后方可继续生产。
5.4异常处置
首中末件检验规范

首中末件检验办法1.目的和范围本办法规定了生产线首、中、末件的定义以及检查要求。
本办法适用于各车间/生产线的整个生产过程。
2.定义本办法采用下列定义:2.1首件为以下情况下生产的第一件产品:(a)每班开始操作时;(b)设备调整时;(c)加工方法变化时;(d)加工条件变化时;(e)作业方法变化时;(f)更换模具时;(g)设备故障修理后再次运转时;(h)更换操作人员时。
(i)容量为每机台/3件。
(h)首检时间为接班后半小时内.2.2中件每班午休后生产的第一件产品。
正常生产时中检容量为每机台/3件,巡检时间为下午13:00。
2.3末件正常生产时的最后一件产品。
正常容量为每机台/3件2.4如发生(b)-(h)中任何一项变化,需重新按本定义对产品进行行首,中,末检查。
3.职责3.1品质部对本办法负管理职责,并保证贯彻执行;3.2生产线班长、操作人员和检验员对正确执行本办法负责。
4.实施办法4.1 首、中、末件检查文件编制4.1.1产品/过程开发工程师负责根据产品质量特性的重要性编写首、中、末件检查文件。
4.1.2首、中、末件检查文件由质量部检验员校对,质量工程师审核、品质部长批准后实施。
4. 2首、中、末件检查基准文件更改首、中、末件检查基准文件发生更改时,过程工程师填写更改单一式三份,经检验员校对,质量工程师审核,品质部长批准后实施更改,更改单由车间、品质部和管理员各保存一份。
4.3检查的实施4.3.1正常生产情况下每班应检查首、中、末件。
4.3.2在每半班发生2.1中(b)~(h)规定情况时,只检查首件、末件。
4.3.3操作工按照检查文件规定的项目对各工序产品/试件进行逐项检查,将检查的实际测量结果记录在三检表内。
4.3.4检查完毕后,针对有关键工序,例如注塑工序,应将产品/试件整齐地放在首、中、末件检查台上;其它工序,有检具的应放置在检具上,没有检具的可在适当位置放置,首件用黄色夹子,中件用白色夹子,末件用蓝色夹子标识,下料和包装工序可以整包标识,单独存放。
首中末件检验规范
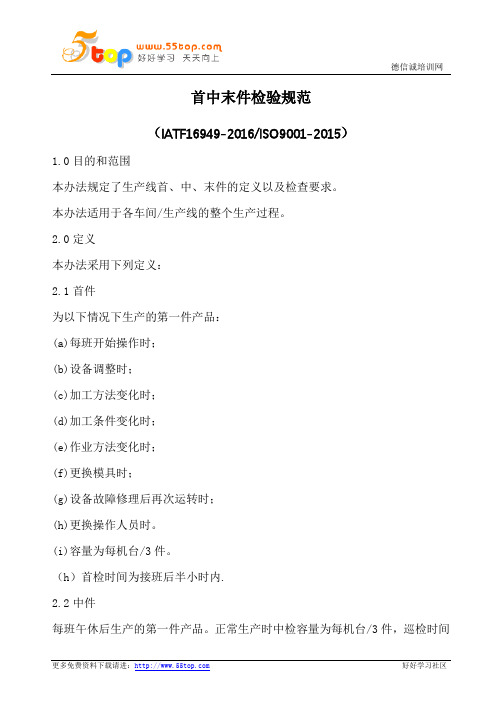
首中末件检验规范(IATF16949-2016/ISO9001-2015)1.0目的和范围本办法规定了生产线首、中、末件的定义以及检查要求。
本办法适用于各车间/生产线的整个生产过程。
2.0定义本办法采用下列定义:2.1首件为以下情况下生产的第一件产品:(a)每班开始操作时;(b)设备调整时;(c)加工方法变化时;(d)加工条件变化时;(e)作业方法变化时;(f)更换模具时;(g)设备故障修理后再次运转时;(h)更换操作人员时。
(i)容量为每机台/3件。
(h)首检时间为接班后半小时内.2.2中件每班午休后生产的第一件产品。
正常生产时中检容量为每机台/3件,巡检时间为下午13:00。
2.3末件正常生产时的最后一件产品。
正常容量为每机台/3件2.4如发生(b)-(h)中任何一项变化,需重新按本定义对产品进行行首,中,末检查。
3.0职责3.1品质部对本办法负管理职责,并保证贯彻执行;3.2生产线班长、操作人员和检验员对正确执行本办法负责。
4.0实施办法4.1 首、中、末件检查文件编制4.1.1产品/过程开发工程师负责根据产品质量特性的重要性编写首、中、末件检查文件。
4.1.2首、中、末件检查文件由质量部检验员校对,质量工程师审核、品质部长批准后实施。
4. 2首、中、末件检查基准文件更改首、中、末件检查基准文件发生更改时,过程工程师填写更改单一式三份,经检验员校对,质量工程师审核,品质部长批准后实施更改,更改单由车间、品质部和管理员各保存一份。
4.3检查的实施4.3.1正常生产情况下每班应检查首、中、末件。
4.3.2在每半班发生2.1中(b)~(h)规定情况时,只检查首件、末件。
4.3.3操作工按照检查文件规定的项目对各工序产品/试件进行逐项检查,将检查的实际测量结果记录在三检表内。
4.3.4检查完毕后,针对有关键工序,例如注塑工序,应将产品/试件整齐地放在首、中、末件检查台上;其它工序,有检具的应放置在检具上,没有检具的可在适当位置放置,首件用黄色夹子,中件用白色夹子,末件用蓝色夹子标识,下料和包装工序可以整包标识,单独存放。
- 1、下载文档前请自行甄别文档内容的完整性,平台不提供额外的编辑、内容补充、找答案等附加服务。
- 2、"仅部分预览"的文档,不可在线预览部分如存在完整性等问题,可反馈申请退款(可完整预览的文档不适用该条件!)。
- 3、如文档侵犯您的权益,请联系客服反馈,我们会尽快为您处理(人工客服工作时间:9:00-18:30)。
1/2名 称3.2 注塑部----负责提供末件样品送检;
3.3 模具车间---- 负责模具出入库的末件样品保管;
作 业 规 范末件确认作业规范编 号
Q/QJN375.005A-2012
1 目的 明确注塑制程中末件确认的方法与步骤,使制程作业规范,确保产品状态与模具异常能得到及时确认。
2 范围
适用于注塑成型制程的末件检查确认;
4 内容
版 本
A/1类 别页 码
3 职责权限
3.1 质量部---对末件进行确认,信息反馈,留样;
4.2 末件确认时机:
4.3 末件的检查容量一般为1模(若客户有特殊要求时,则按检验标准规定的容量);
C ,计划性停机:计划性的切换停机;
A ,突发性故障停机:如设备出现故障,短时间内不能再生产时;
B ,任务完成停机: 本批订单任务完成时停机;
存,样品交注塑部随模具一起入库,修模部负责将样品与模具一起存放;
C,品管员确认NG时,品管员将NG品随同《制程异常通知单》应立即交注塑部处理,并追溯到异常产
生的时间节点,班次等,对追溯到的可疑品应立即做好隔离标识,同时跟踪和监督整个过程,注塑部将已生产的可疑品根据最终的判定执行分拣,返工或报废处理;
4.4 生产准备卸模时
A,注塑部在决定卸模前,须将最后2模产品交品管员进行末件确认,即:依《制程检验标准书》、 图纸、留样进行确认(一般以外观,关键尺寸,实际的装配等为优先检查项);
B,品管员确认OK时,签样1份,贴上样品标签,并填写《末件确认单》一份,交主管审核,内部自6 相关记录
《末件确认单》《制程异常通知单》
5 文件 《品质异常处理程序》
D,确认产品需要改善但没有客户拒收的缺陷以外,即:影响过程控制的一些的轻微缺陷,或者依靠后道工序加工等,务必在末件确认之后,填写《制程异常通知单》随附需改善的样品交注塑部进行处理(如通知修模部改善模具);
4.5 末件样品随模具一起入模具库保管,在下批生产随模具一起领出进行首件确认对比;。