高炉炼铁工序能耗计算方法
钢铁烧结工序能耗计算公式
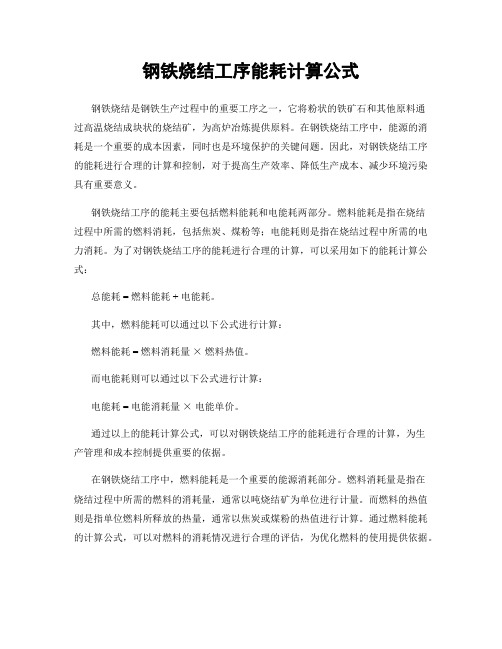
钢铁烧结工序能耗计算公式钢铁烧结是钢铁生产过程中的重要工序之一,它将粉状的铁矿石和其他原料通过高温烧结成块状的烧结矿,为高炉冶炼提供原料。
在钢铁烧结工序中,能源的消耗是一个重要的成本因素,同时也是环境保护的关键问题。
因此,对钢铁烧结工序的能耗进行合理的计算和控制,对于提高生产效率、降低生产成本、减少环境污染具有重要意义。
钢铁烧结工序的能耗主要包括燃料能耗和电能耗两部分。
燃料能耗是指在烧结过程中所需的燃料消耗,包括焦炭、煤粉等;电能耗则是指在烧结过程中所需的电力消耗。
为了对钢铁烧结工序的能耗进行合理的计算,可以采用如下的能耗计算公式:总能耗 = 燃料能耗 + 电能耗。
其中,燃料能耗可以通过以下公式进行计算:燃料能耗 = 燃料消耗量×燃料热值。
而电能耗则可以通过以下公式进行计算:电能耗 = 电能消耗量×电能单价。
通过以上的能耗计算公式,可以对钢铁烧结工序的能耗进行合理的计算,为生产管理和成本控制提供重要的依据。
在钢铁烧结工序中,燃料能耗是一个重要的能源消耗部分。
燃料消耗量是指在烧结过程中所需的燃料的消耗量,通常以吨烧结矿为单位进行计量。
而燃料的热值则是指单位燃料所释放的热量,通常以焦炭或煤粉的热值进行计算。
通过燃料能耗的计算公式,可以对燃料的消耗情况进行合理的评估,为优化燃料的使用提供依据。
另外,电能耗也是钢铁烧结工序中的重要能耗部分。
电能消耗量是指在烧结过程中所需的电能的消耗量,通常以千瓦时为单位进行计量。
而电能单价则是指单位电能的价格,通常以元/千瓦时为单位进行计算。
通过电能耗的计算公式,可以对电能的使用情况进行合理的评估,为降低电能消耗提供依据。
除了能耗的计算,钢铁烧结工序中还可以采取一系列的节能措施,进一步降低能耗。
例如,可以优化燃料的配比和燃烧条件,提高燃料的利用率;可以采用先进的烧结设备和技术,提高生产效率;可以采用余热回收技术,充分利用余热资源。
通过这些节能措施的实施,可以进一步降低钢铁烧结工序的能耗,减少生产成本,提高经济效益。
高炉铁合金冶炼主要技术经济指标计算方法

高炉铁合金冶炼主要技术经济指标计算方法一、锰铁合格率锰铁合格率是指报告期内锰铁检验合格量与锰铁检验总量的百分比。
其计算公式为:锰铁合格率(%) = 锰铁检验合格量(吨)×100%锰铁送检总量(吨)计算说明:高炉开工后,不论任何原因产生的出格锰铁,均应参加锰铁合格率的计算;式中子、母项单位为标准吨。
二、低硅锰铁率低硅锰铁率是指低硅锰铁量占合格锰铁总量的百分比。
其计算公式为:低硅锰铁率(%)= 低硅锰铁总量(吨)×100%合格锰铁总量(吨)计算说明:低硅锰铁是指符合现行国标一组硅要求的锰铁;式中子、母项单位为标准吨。
三、燃料比燃料比是指每炼1吨合格锰铁(标准吨)所消耗的入炉燃料的数量。
它反映燃料的节约或浪费以及高炉操作水平的高低。
燃料全部以扣除水分的干基计算,其计算公式为:燃料比(千克/吨) = 入炉焦炭耗用量(千克)+入炉喷吹燃料耗用量(千克)合格锰铁生产量(吨)入炉焦比(千克/吨) = 入炉焦炭耗用量(千克)合格锰铁生产量(吨)煤粉消耗(千克/吨)= 喷入高炉内的煤粉数量(千克)合格锰铁生产量(吨)计算说明:式中母项单位为标准吨。
高炉铁合金工序单位能耗参照高炉炼铁工序单位能耗计算公式计算。
四、入炉锰矿消耗入炉锰矿消耗是指每炼一吨合格锰铁(标准吨)所消耗的入炉锰矿石的数量,包括天然矿石和人造块矿。
天然矿石按扣除水分的干基计算。
其计算公式为:锰矿石消耗(千克/吨)=入炉天然矿石消耗量(千克)+入炉人造块矿消耗是(千克)合格锰铁生产量(吨)计算说明:式中母项单位为标准吨。
五、入炉熔剂消耗入炉熔剂消耗是指每炼一吨合格锰铁(标准吨)所消耗的入炉熔剂数量,它包括石灰石、白云石、生石灰,萤石等用于造渣的碱性化合物。
这一指标综合反映炉料质量好坏及造渣操作的合理性。
其计算公式为:熔剂消耗(千克/吨)=入炉熔剂消耗总量(千克)合格锰铁生产量(吨)其中:熟料消耗(千克/吨)=入炉熟料消耗量(千克)合格锰铁生产量(吨)计算说明;(1)各种熔剂入炉消耗都不扣水分;(2)熟料包括生石灰及焙烧后的白云石;(3)式中母项单位为标准吨。
工序能耗

工序能耗工序能耗企业的某一生产环节(生产工序)在统计期内的综合能耗。
它根据该工序的能源消耗及能耗工质实物量消耗的统计计量折算成一次能源后进行计算。
当工序有外供二次能源时,则按规定的折算系数折算成一次能源后,从能耗中扣除相应的量。
燃料比高炉采用喷吹煤粉、重油或自然气后,折合每炼一吨生铁所消耗的燃料总量。
每吨生铁的喷煤量和喷油量分别称为煤比和油比。
此时燃料比即是焦比加煤比加油比。
根据喷吹的煤和油置换比的不同,分别折合成焦炭(公斤),再和焦比相加称为综合焦比。
燃料比和综合焦比是判别冶炼一吨生铁总燃料消耗量的一个重要指标。
要在降低炼铁燃料比上下功夫炼铁学理论是:高炉利用系数=冶炼强度÷燃料比。
也就是说,提高利用系数有两个办法。
一个是提高冶炼强度,另一个是降低燃料比。
我国中小高炉实现高利用系数主要是采用提高冶炼强度的办法。
采用配备大风机、大风量操作高炉,进行高冶炼强度生气,来实现高利用系数。
这种做法就带来高炉的能耗高。
不符合钢铁工业要节能降耗的工作思路,应当予以纠正。
目前大型高炉吨铁所消耗的风量在1200m3以下。
而一些小高炉的吨铁风耗是在1400m3左右,甚至有大于1500m3的现象。
燃烧1kg标准煤要2.5m3的风,鼓风机产生1m3的风要消耗0.85kg标准煤。
大风量,高冶炼强度操作炉,燃料比就要升高。
所以说小高炉的燃料比要比大高炉高30~50kg/t。
钢铁工业要实现“十一五”期间GDP能耗降低20%,主要工作方向就是要在降低炼铁燃料比上下功夫!因为高炉炼铁工序的能耗要占联合企业总能耗的50%左右。
国际先进水平的炼铁燃料比是在500kg/t以下,领先水平是在450kg/t左右。
2007年我国重点钢铁企业高炉炼铁燃料比为529kg/t,最高达到673kg/t。
这说明,我国已掌握了先进的高炉炼铁技术,但是炼铁企业发展不平衡,尚有较大的节能潜力。
高炉炼铁的燃料比是:入炉焦比+喷煤比+小块焦比。
喷煤比是不计算量换比,这样企业之间进行对比才合理科学。
炼铁铁料单耗计算
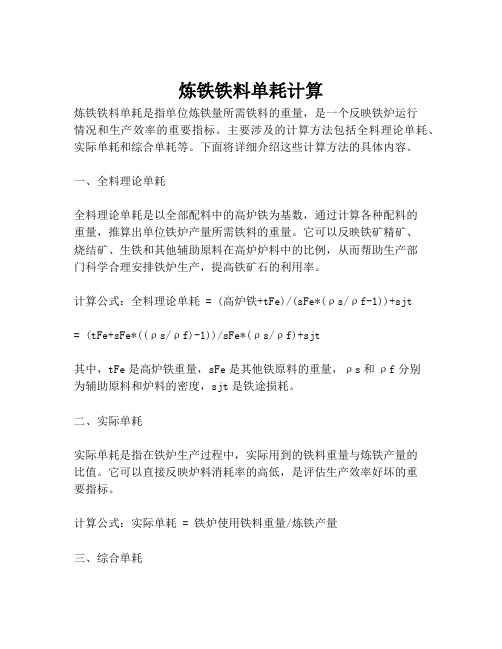
炼铁铁料单耗计算炼铁铁料单耗是指单位炼铁量所需铁料的重量,是一个反映铁炉运行情况和生产效率的重要指标。
主要涉及的计算方法包括全料理论单耗、实际单耗和综合单耗等。
下面将详细介绍这些计算方法的具体内容。
一、全料理论单耗全料理论单耗是以全部配料中的高炉铁为基数,通过计算各种配料的重量,推算出单位铁炉产量所需铁料的重量。
它可以反映铁矿精矿、烧结矿、生铁和其他辅助原料在高炉炉料中的比例,从而帮助生产部门科学合理安排铁炉生产,提高铁矿石的利用率。
计算公式:全料理论单耗 = (高炉铁+tFe)/(sFe*(ρs/ρf-1))+sjt= (tFe+sFe*((ρs/ρf)-1))/sFe*(ρs/ρf)+sjt其中,tFe是高炉铁重量,sFe是其他铁原料的重量,ρs和ρf分别为辅助原料和炉料的密度,sjt是铁途损耗。
二、实际单耗实际单耗是指在铁炉生产过程中,实际用到的铁料重量与炼铁产量的比值。
它可以直接反映炉料消耗率的高低,是评估生产效率好坏的重要指标。
计算公式:实际单耗 = 铁炉使用铁料重量/炼铁产量三、综合单耗综合单耗是全料理论单耗和实际单耗相结合的综合指标。
它要考虑到铁炉运行的各种因素,包括料型、炉温、喷煤、风量等。
只有达到全料单耗,又达到实际单耗的要求,才能说明铁炉生产达到最佳状态。
计算公式:综合单耗 = 铁炉使用铁料重量/炼铁产量 + (实际单耗-全料理论单耗)/全料理论单耗四、注意事项1.计算时应严格按照各种原料的实际重量进行计算;2.不同企业的计算方法可能有所不同,要根据自身的情况选择合适的计算方法;3.计算的过程中需要关注铁途损耗的影响,进行正确的调整和计算;4.每个铁炉的生产情况都不同,要根据实际情况进行相应的计算和分析。
总之,炼铁铁料单耗的准确计算对于评估铁炉生产效率、优化炉料配比、提高铁矿石利用率等方面均具有重要意义。
需要在实际生产中采用合适的计算方法,确保数据的准确性和科学性。
粗钢生产工序能耗计算

设备性能
总结词
设备性能的优劣直接关系到能耗的高低。
详细描述
设备的效率、维护状况以及设备老化程度等都会影响能耗。高效的设备可以降 低能耗,而设备维护不当或老化严重则可能导致能耗增加。
直接能耗计算方法是根据实际消耗的能源量和相应的能耗系数,计算出直 接能耗量。
直接能耗计算需要考虑不同生产工艺和设备对能源消耗的影响,以及能源 利用效率和能源品质等因素。
间接能耗计算
01
间接能耗是指在粗钢生产过程中,为保证生产正常运
行而消耗的能源,如供热、通风、照明等。
02
间接能耗计算方法是根据实际消耗的能源量和相应的
。
推广节能操作方法
03
总结和推广各生产工序中的节能操作方法,规范员工的操作行
为。
提高员工节能意识
开展节能宣传教育
通过宣传栏、内部刊物、培训等方式,普及节 能知识,提高员工的节能意识。
组织节能培训
定期组织节能培训和交流活动,让员工学习节 能技术和经验,提高节能技能。
鼓励员工提出节能建议
建立员工建议征集制度,鼓励员工提出节能意见和建议,激发全员参与节能的 积极性。
能耗系数,计算出间接能耗量。
03
间接能耗计算需要考虑生产工艺和设备对能源消耗的
需求,以及能源利用效率和能源品质等因素。
总能耗计算
01
总能耗是指粗钢生产过程中直 接和间接消耗的能源总量。
02
总能耗计算方法是将直接能耗 和间接能耗相加,得出总能耗 量。
03
总能耗计算需要考虑不同生产 工艺和设备对能源消耗的影响 ,以及能源利用效率和能源品 质等因素。
高炉炼铁工序能耗计算方法

高炉炼铁工序能耗计算方法日前,中国钢铁企业网特邀专家顾问王维兴就高炉炼铁工序能耗计算方法作了以下解析:1.高炉炼铁工序能耗计算统计范围原燃料供给:矿槽卸料、称量料斗和计量、料车或皮带上料、仪表显示和控制、照明等用电;空调用电、冬季取暖用蒸汽等能源用量。
高炉本体:焦炭(包括小块焦)、煤粉、电力、蒸汽、压缩空气、氧气、氮气、水(新水、软水等)等。
渣铁处理:炉渣处理用电和水,冲渣水余热要进行回收利用。
鼓风:分电力鼓风或气动鼓风。
鼓风能耗一般占炼铁总能耗的10%。
1m?风需要用能耗0.030kgce/ m?.正常冶炼条件下,高炉消耗1吨燃料,需要2400m?的风量。
热风炉:要求漏风率≤2%、漏风损失应≤5%、总体热效率≥80%、风温大于1200℃,寿命大于25年。
烧炉用高炉煤气折标煤系数0.1143kgce/m³;转炉煤气折标煤系数0.2286kgce/m³;焦炉煤气折标煤系数0.6kgce/m³。
热风炉用电力和其它能源工质:蒸汽、压缩空气、水等。
煤粉喷吹:煤粉制备干燥介质,宜优先采用热风炉废气;用电力、氮气、蒸汽、压缩空气、空调和采暖用能等。
设计喷煤能力要大于180kg/t.碾泥:用电力和其它能源工质。
除尘和环保:主要是电力(大企业环境保护用电力占炼铁用电的30%左右)、水等。
, 铸铁机:电力、水等。
扣除项目:回收利用的高炉煤气,热值按实际回收量计算;TRT余压发电量(电力0.1229kgce/kwh)2.炼铁工序能耗计算方法炼铁工序能耗=(C+I+E-R)÷T式中:T-合格生铁产量,铸造铁产量要用折算系数进行计算(见表1);C-焦炭(干全焦,包括小块焦)用量。
折热量,28435kJ。
标煤量0.9714kgce/t焦炭.I-喷吹煤折热量,20908kJ ; 折标煤量0.7143kgce/t原煤。
E-加工能耗(煤气、电、耗能工质等)折标煤量:煤气折标煤系数见热风炉栏目。
高炉常用计算公式审批稿
高炉常用计算公式 YKK standardization office【 YKK5AB- YKK08- YKK2C- YKK18】炼铁用计算公式1、根据焦炭负荷求焦比焦比=1000/(负荷×综合品位)=矿批/(负荷×理论焦比)2有效容积利用系数=每昼夜生铁产量/高炉有有效容积3焦比=每昼夜消耗的湿焦量×(1-水分)/每昼夜的生铁产量4理论出铁量=(矿批×综合焦比)/=矿批×综合品位×不考虑进去渣中的铁量因为焦炭也带入部分铁5富氧率=-×富氧量/60×风量=×富氧量/风量6煤比=每昼夜消耗的煤量/每昼夜的生铁含量7 综合焦比=焦比+煤比×8 综合燃料比=焦比+煤比+小块焦比9 冶炼强度=每昼夜消耗的干焦量/高炉有效容积10 矿比=每昼夜加入的矿的总量/每昼夜的出铁量11 风速=风量(1-漏风率)/风口总面积漏风率20%12 冶炼周期=(V有 -V炉缸内风口以下的体积)/(V球+V烧+V矿)×88%=(V球+V烧+V矿)×88%13 综合品位=(m烧×烧结品位+m球×球品位+m矿×矿品位)/每昼夜加入的矿的总量14 安全容铁量=×ρ铁×1/4πd2hh取风口中心线到铁口中线间高度的一半15 圆台表面积=π/2(D+d)体积=π/12×h×(D2+d2+Dd)16 正方角锥台表面积S=a2 +b2 +4( a+b/2)hV=h/3(a2+b2+ab)=h/3(S1+S2+√S1S)17、圆锥侧面积M=πrl=πr√r2+h2体积V=1/3πr2h18、球S=4πr2=πd2V=4/3πr3=π/6d319、风口前燃烧1kg碳素所需风量(不富氧时)V风=24×1/+ f为鼓风湿度20、吨焦耗风量V风=(+)×1000×85%f为鼓风湿度 85%为焦炭含碳量21、鼓风动能(1)E=(764I2-3010I+3350)dE-鼓风动能 I-冶炼强度(2)E=1/2mv2=1/2×Q×r风/(60gn)v风实2Q-风量 r风-风的密度 g= n-风口数目22、石灰的有效容剂性CaO有效=CaO熔-SiO2×R23、洗炉墙时,渣中CaF2含量控制在2%-3%,洗炉缸时可掌控在5%左右,一般控制在%每批料萤石加入量X=P矿×TFe×Q×(CaF2)/([Fe]×N)P矿-矿批重 TFe-综合品位 [Fe]-生铁中含铁量Q-吨铁渣量 (CaF2)-渣中CaF2含量 N-萤石中CaF2含量24、风口前燃烧1kg碳素的炉缸煤气量V煤气=(+)/(+)××C风C风-风口前燃烧的碳素量,kg25、理论出渣量渣量批=QCaO批/CaO渣渣量批-每批炉料的理论渣量,tQCaO批-每批料带入的CaO量,tCaO渣-炉渣中CaO的含量,%25、喷吹煤粉热滞后时间t=V总/(V批×n)V总-H2参加反应区起点处平面(炉身温度1100℃~1200℃处)至风口平面间的容积,m3V批-每批料的体积,m3n-平均每小时的下料批数,批/h26、高炉某部位需要由冷却水带走的热量称为热负荷,单位表面积炉衬或炉壳的热负荷称为冷却强度Q=CM(t-t0)×103Q-热负荷 kJ/hM-冷却水消耗量,t/hC-水的比热容,kJ/(kg.℃)t-冷却水出水温度℃t0-冷水进水温度,℃。
工序单位能耗的计算方法、及企业吨钢可比能耗计算方法
一、各工序单位能耗计算方法:二、其它能耗计算方法的资料中国8个钢铁企业产量达千万吨近几年中国钢铁工业生产规模明显扩大,年产钢1000万吨以上的企业已有8家,年产钢500万吨以上的共有1 7家,年产钢300万吨以上的有30多家。
2005年产钢1000万吨以上企业由2000年的1家(宝钢)上升到8家(宝钢、鞍钢、唐钢、武钢、首钢、沙钢、济钢、莱钢),合计产钢11191.9万吨,占全国钢产量的31.76%。
产钢大于500万吨小于1000万吨企业由2000年的3家(鞍钢、首钢、武钢)上升到2005年的9家 (马钢、华菱钢铁、包钢、邯钢、攀钢、安阳钢铁、太钢、酒钢、建龙钢铁),合计产钢6051.21万吨,占全国钢产量的17. 17%。
产钢300万吨以上企业共30家,合计产钢22079.65万吨,占全国钢产量的62.65%。
据介绍,中国钢产量已由2000年的1.28亿吨上升到2005年的3.52亿吨,钢产量占世界钢产量的比例由2000年的15.2%上升至2005年的31.1%。
标准煤系数就是把某一能源品种的实物量折合成标准量时所采用的系数,换句话说,就是单位能源的实际发热值与7000千卡的比率:即:单位能源的实际发热值7000千卡=该能源品种折标准煤系数例如:1公斤焦炭的平均低位发热量为6800千卡,其折标准煤系数为:6800千卡÷7000千卡=0.9714。
也就是说,1公斤焦炭相当于0.9714公斤标准煤,1000吨焦炭相当于971.4吨标准煤。
在企业内部同一能源品种,由于到货时间、供货单位的不同,其实际发热值也不一样。
在此情况下,确定企业标准煤系数,一般采用“加权算术平均数”的计算方法,加权算术平均数是反映次数结构影响的算术平均数,它的计算方法是总体各标志值(变量值)乘以相应的次数(权数)之和与总次数(总权数)的比。
例如:某企业2002年5月份先后从枣庄、肥城、山西、兖州等地购入原煤的实际数量分别为150吨、175吨、250吨、250吨,每次到货后实测发热值分别为4910千卡/公斤、4509千卡/公斤、5101千卡/公斤、5250千卡/公斤,这些原煤在本月全部消耗,那么该企业5月份消耗煤炭折标准煤587.62吨,折标准煤系数为0.7123。
高炉炼铁技术主要工艺参数计算公式
高炉炼铁技术主要工艺参数计算公式一、常用计算公式1.工艺计算(1)风口标准风速:式中v 标--风口标准风速,m/s ;Q ――风量,m 3/min ; F ――风口送风总面积,m 2。
(2)风口实际风速:式中 v 实--风口实际风速,m/s ;v 标--风口标准风速,m/s ;T --风温,℃; p --鼓风压力,MPa 。
(3)鼓风动能:式中 E --鼓风动能,J/s ;60⨯=F Q v 标)20273()1013.0(1013.0)273(+⨯+⨯+⨯=p T v v 标实20223)()273(1412.0p p T F Q n E ++⨯⨯⨯=Q --风量,m 3/min ;n --风口数目,个;F --风口总截面积,m 3; T --热风温度,℃;P --热风压力,Pa ;P 0--标准大气压,等于101325Pa 。
(4)富氧率:1)氧气兑入口在冷风管道孔板前面,即富氧量流经流量孔板,考虑鼓风湿度时富氧率公式为:不考虑鼓风湿度时富氧率公式为:2)氧气兑入口在冷风管道孔板后面,即富氧量未流经流量孔板,考虑鼓风湿度时富氧率公式为:不考虑鼓风湿度时富氧率公式为:()()%10021.029.021.0⨯⎥⎦⎤⎢⎣⎡-++⨯-=风氧氧风Q b Q f Q Q B ()%10021.0⨯-=风氧Q Q b B ()%10021.029.021.0⨯⎥⎥⎦⎤⎢⎢⎣⎡-+++⨯=氧风氧风Q Q b Q f Q B ()%10021.0⨯+⨯-=氧风氧Q Q Q b B式中 B --富氧率,%;Q 风--风量(冷风流量孔板显示值),m 3/min ;Q 氧--富氧量,m 3/min ;0.21--鼓风中含氧率;b --氧气中含氧率,%; f --鼓风湿度,%。
(5)冶炼周期: 式中t --冶炼周期,h ;V ′--由料线到风口中心线的容积,m 3; n --每天料批数,批;V --每批料体积,m 3/批;c --炉料在高炉内压缩率,一般为12~15%。
高炉常用计算公式
炼铁用计算公式1、根据焦炭负荷求焦比焦比=1000/(负荷×综合品位)=矿批/(负荷×理论焦比)2有效容积利用系数=每昼夜生铁产量/高炉有有效容积3焦比=每昼夜消耗的湿焦量×(1-水分)/每昼夜的生铁产量4理论出铁量=(矿批×综合焦比)/=矿批×综合品位×不考虑进去渣中的铁量因为焦炭也带入部分铁5富氧率=-×富氧量/60×风量=×富氧量/风量6煤比=每昼夜消耗的煤量/每昼夜的生铁含量7 综合焦比=焦比+煤比×8 综合燃料比=焦比+煤比+小块焦比9 冶炼强度=每昼夜消耗的干焦量/高炉有效容积10 矿比=每昼夜加入的矿的总量/每昼夜的出铁量11 风速=风量(1-漏风率)/风口总面积漏风率20%12 冶炼周期=(V有 -V炉缸内风口以下的体积)/(V球+V烧+V矿)×88%=(V球+V烧+V矿)×88%13 综合品位=(m烧×烧结品位+m球×球品位+m矿×矿品位)/每昼夜加入的矿的总量14 安全容铁量=×ρ铁×1/4πd2hh取风口中心线到铁口中线间高度的一半15 圆台表面积=π/2(D+d)体积=π/12×h×(D2+d2+Dd)16 正方角锥台表面积S=a2 +b2 +4( a+b/2)h V=h/3(a2+b2+ab)=h/3(S1+S2+√S1S)17、圆锥侧面积M=πrl=πr√r2+h2体积V=1/3πr2h18、球S=4πr2=πd2V=4/3πr3=π/6d319、风口前燃烧1kg碳素所需风量(不富氧时)V风=24×1/+ f为鼓风湿度20、吨焦耗风量V风=(+)×1000×85%f为鼓风湿度 85%为焦炭含碳量21、鼓风动能(1)E=(764I2-3010I+3350)dE-鼓风动能 I-冶炼强度(2)E=1/2mv2=1/2×Q×r风/(60gn)v风实2Q-风量 r 风-风的密度 g= n-风口数目22、石灰的有效容剂性 CaO 有效=CaO 熔-SiO 2×R23、洗炉墙时,渣中CaF 2含量控制在2%-3%,洗炉缸时可掌控在5%左右,一般控制在%每批料萤石加入量X=P 矿×TFe ×Q ×(CaF 2)/([Fe]×N) P 矿-矿批重 TFe-综合品位 [Fe]-生铁中含铁量 Q-吨铁渣量 (CaF 2)-渣中CaF 2含量 N-萤石中CaF 2含量24、风口前燃烧1kg 碳素的炉缸煤气量 V 煤气=(+)/(+)××C 风 C 风-风口前燃烧的碳素量,kg25、理论出渣量 渣量批=QCaO 批/CaO 渣渣量批-每批炉料的理论渣量,t QCaO 批-每批料带入的CaO 量,t CaO 渣-炉渣中CaO 的含量,%25、喷吹煤粉热滞后时间 t=V 总/(V 批×n )V 总-H 2参加反应区起点处平面(炉身温度1100℃~1200℃处)至风口平面间的容积,m ³V 批-每批料的体积,m ³ n-平均每小时的下料批数,批/h26、高炉某部位需要由冷却水带走的热量称为热负荷,单位表面积炉衬或炉壳的热负荷称为冷却强度Q=CM(t-t)×103Q-热负荷 kJ/hM-冷却水消耗量,t/hC-水的比热容,kJ/(kg.℃) t-冷却水出水温度℃-冷水进水温度,℃t。
- 1、下载文档前请自行甄别文档内容的完整性,平台不提供额外的编辑、内容补充、找答案等附加服务。
- 2、"仅部分预览"的文档,不可在线预览部分如存在完整性等问题,可反馈申请退款(可完整预览的文档不适用该条件!)。
- 3、如文档侵犯您的权益,请联系客服反馈,我们会尽快为您处理(人工客服工作时间:9:00-18:30)。
高炉炼铁工序能耗计算方法
日前,中国钢铁企业网特邀专家顾问王维兴就高炉炼铁工序能耗计算方法作了以下解析:
1.高炉炼铁工序能耗计算统计范围
原燃料供给:矿槽卸料、称量料斗和计量、料车或皮带上料、仪表显示和控制、照明等用电;空调用电、冬季取暖用蒸汽等能源用量。
高炉本体:焦炭(包括小块焦)、煤粉、电力、蒸汽、压缩空气、氧气、氮气、水(新水、软水等)等。
渣铁处理:炉渣处理用电和水,冲渣水余热要进行回收利用。
鼓风:分电力鼓风或气动鼓风。
鼓风能耗一般占炼铁总能耗的10%。
1m?风需要用能耗0.030kgce/ m?.正常冶炼条件下,高炉消耗1吨燃料,需要2400m?的风量。
热风炉:要求漏风率?2%、漏风损失应?5%、总体热效率?80%、风温大于1200?,寿命大于25年。
烧炉用高炉煤气折标煤系数0.1143kgce/m?;
转炉煤气折标煤系数0.2286kgce/m?;
焦炉煤气折标煤系数0.6kgce/m?。
热风炉用电力和其它能源工质:蒸汽、压缩空气、水等。
煤粉喷吹:煤粉制备干燥介质,宜优先采用热风炉废气;
用电力、氮气、蒸汽、压缩空气、空调和采暖用能等。
设计喷煤能力要大于180kg/t.
碾泥:用电力和其它能源工质。
除尘和环保:主要是电力(大企业环境保护用电力占炼铁用电的30%左右)、水等。
,
铸铁机:电力、水等。
扣除项目:回收利用的高炉煤气,热值按实际回收量计算;
TRT余压发电量(电力0.1229kgce/kwh)
2.炼铁工序能耗计算方法
炼铁工序能耗=(C+I+E-R)?T
式中:T-合格生铁产量,铸造铁产量要用折算系数进行计算(见表1);
C-焦炭(干全焦,包括小块焦)用量。
折热量,28435kJ。
标煤量0.9714kgce/t 焦炭. I-喷吹煤折热量,20908kJ ; 折标煤量0.7143kgce/t原煤。
E-加工能耗(煤气、电、耗能工质等)折标煤量:
煤气折标煤系数见热风炉栏目。
电力折标煤系数0.1229kgce/kwh.. 耗能工质折标煤系数:氧气0.1796kgce/m?;氮气0.0898 kgce/kwh. 压缩空气0.040
kgce/m?,新水0.257 kgce/kwh
软水0.500 kgce/m?,蒸汽0.12 kgce/kwh.
R-回收高炉煤气、电力折热量. 高炉煤气折标煤系数0.1143kgce/Nm? 电力折标煤系数0.1229kgce/kwh。
3.高炉炼铁工序能耗设计指标
2010年国家建设部和质量监督局公布《钢铁企业节能设计规范》(GB50632-2010)中提
出不同容积高炉工序能耗的要求,具体内容如下:
1000M?级高炉?400kgce/t, 2000 M?级高炉?395kgce/t ,
3000 M?级高炉?390kgce/t,4000M?级以上高炉?385kgce/t。
《高炉炼铁工艺设计规范》各种高炉燃料比、焦比要求见表2.
2011年工信部发布《关于印发?铸造生铁企业认定规范条件?的通知》,规定铸造铁高炉
焦比(含小块焦)不大于510kg/t,工序能耗不大于520 kgce/t,吨铁新水消耗不大于2.6吨。
.
4.高炉炼铁能源平衡情况
4.1.高炉炼铁能源收入:
o 高炉内铁矿石还原热量收入: 77.70%来自碳素(焦炭和煤粉)燃烧, 19.49%来自热风带人,
2.32%是炉料化学反应,
0.06%是成渣热,
0.43%炉料带人热量。
o 高炉生产需要能源:
2011年前5个月重点钢铁企业炼铁工序能耗为406.41 kgce/t .
2009年重点钢铁企业平均炼铁电耗为68.96kgce/t;工序水耗21.57m?/t, 耗新水1.09
m?/t。
大型高炉用蒸汽0.049~46.58m?/t,压缩空气4.80~73.36m?/t,新水
0.20~3.m?/t,氧气
13.42~54.20 m?/t。
4.2. 高炉炼铁能源支出:
氧化物分解及去硫 76.38%;
碳酸盐分解热 0.06%;
水分分解热 2.10%;
游离水蒸发热 0.51%;
喷吹物分解热 1.21%;
铁液显热 11.94%;
炉渣显热 5.55%;
煤气带走热量 4.39%;(高炉煤气产生量1400~1800m?/t)
冷却水及其它散热 6.86%。
5.说明
5.1.一些企业炼铁工序能耗统计不规范,只算到高炉本体,没将外围(原燃料供应、热风炉、碾泥、鼓风、铸铁等)统计在内。
5.2.企业之间用蒸汽、鼓风风量、耗水量、耗新水量、氧气、氮气、压缩空气等能源工质消耗量差距较大,要统计在炼铁工序能耗内。
注意各能源工质折标煤系数的规范和统一。
5.3.企业之间高炉煤气产出量差距较大,主要是与燃料比有关。
燃料比高,煤气量大、热值高。
扣除部分只计算回收利用部分,不能将热风炉利用的煤气也计算在内。
因高风温替代燃料,已在降低燃料比中体现了。
煤气用于发电,要用电力折标煤系数0.1229kgce/kwh.用煤气热值去计算数值会偏大。
因煤气去发电要消耗大部分能量,其能源转换率只有32%~45%。
所以,我们提倡煤气要在企业内充分利用,不得以,才去发电。
5.4.目前,一些企业炼铁工序能耗失真,统计不规范。
燃料比高的企业一般应工序能耗高。
因炼铁用能有77.70%是来自碳素燃烧。
个别企业燃料高,但工序能耗低,使人有疑问。
影响燃料比的主要因素是:炼铁矿石品位、热风温度、焦炭质量等。
要用生产条件论的观点去具体分析企业炼铁工序能耗高低。
(中国钢铁企业网,作者:王维兴,系中国金属学会高级工程师、中国钢铁企业网特邀专家顾问)。