深孔电镀孔无铜缺陷成因探讨及改善
提高小孔,深孔接触件电镀中孔内镀层质量的方法

提高小孔,深孔接触件电镀中孔内镀层质量的方法
1、改善电镀前处理工艺:尤其是深孔接触件,电镀前处理工艺更为重要,需要对孔内表面进行化学或机械研磨,以提高接触件表面的洁净度和光洁度,大大提高孔内电镀质量。
2、优化电流密度分布:要想在周边的深孔中获得更加均匀的电流密度分布,应采取有效的措施,比如改变极极板的形状,改变电流流向或强度,或者利用有效的可逆表面效应。
3、选用质量优良的电解质:需要选用质量优良的电解质,确保电解质的稳定性,使电流稳定,并减少容易形成析出物的电解质。
4、合理设置电镀参数:要得到质量高的电镀层,应根据实际情况合理地设置电镀电流和时间等参数,使电镀层的厚度均匀,尤其是深孔接触件的电镀层。
160-电镀品质改善专案报告

1、孔破改善 2、板面及孔内铜丝(渣)改善
报告目录
一 孔破改善 1、品质改善背景。 2、孔破原因分析 3、改善行动 4、效果验证 二 电镀铜丝(渣)改善 1、品质改善背景。 2、电镀铜丝(渣)原因分析 3、改善行动 4、效果验证
一、孔破改善
1、品质改善背景
自新沉铜线和板电线投入生产后,在蚀检电测 统计良率数据发现孔破不良高居不下,达到 0.15%。为改善此不良降低报废和品质潜在风 险,特成立此专案进行改善。
振动马达没有开启
孔 内 气 泡
振动马达损坏 振动幅度不够
振动马达弹簧或螺丝损坏, 震动无法传递到飞靶
从上述分析可以确定,孔内气泡残留主要是震动马达没有 发挥应有的作用。属于设备异常。
3、改善行动
针对设备问题,征询设备商的改善建议,改用新型的“低频震动机组”
新型低频震动机组与传统震动马达优劣对比
产品
3、改善行动
(1)原先提出对员工进行培训,每次添加铜球由组 /课长在现场指导监督。但是效果不明显,因为每 次添加的铜球量比较大,但是靠人员监督是无法 有效的杜绝此类事件。
(2)采用铜球自动添加方式来达到此目的。
设备实际运作效果
4、效果验证
对比项目
铜球添加效 率
自动添加
传统手动添加
(1)快,每条电镀线只需 慢,整条电镀线都要停产而且 要2-3人在走道上即可完成。 员工要爬到缸体上进行添加。
新型低频震动机组
传统震动马达
机械结构强度 500小时无螺丝或弹簧脱落 500小时后出现螺丝脱落 损坏问题
噪音
噪音小于65分贝
噪音小于90分贝
使用寿命
供应商保固1年
供应商保固6个月
电镀品缺陷及原因分析
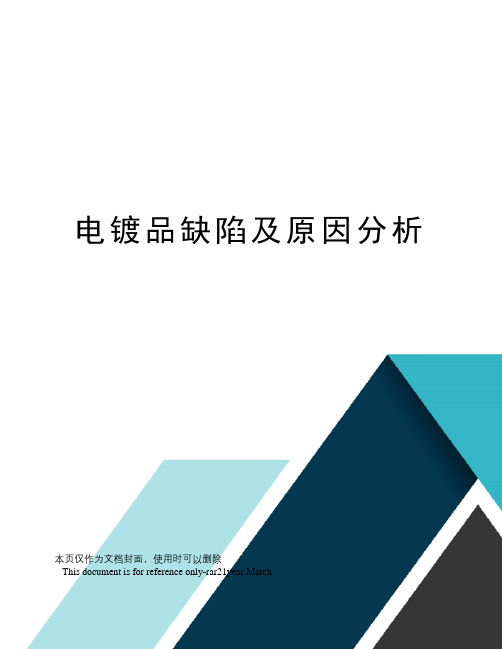
电镀品缺陷及原因分析本页仅作为文档封面,使用时可以删除This document is for reference only-rar21year.March电镀品缺陷及原因分析一、电镀品缺陷分类:1、前处理造成的缺陷:漏镀、起泡、漏油、绝缘处沉上镍、擦花2、电镀过程中造成的缺陷起砂、麻点、发蒙、镀层烧焦、发黄、发灰、针孔、毛刺、脱落、发雾、发花二、原因分析:电镀品缺陷一般在电镀过程中电镀出故障才会出现电镀品缺陷,因此,要对电镀故障分析找到问题点,才能对症下药,解决问题1、判断产生电镀故障原因属于镀液因素,还是非电镀因素,从电镀科学和生产规律而言,电镀溶液是生产的主体或必要因素,是获得正常镀层的必要条件,镀液成份不正常其它条件再好也不能获得优质镀层,而非电镀因素,如温度、PH值、电流密度等工艺条件是生产的客体或偶然因素,是获得正常镀层的充分条件,只有在具备条件下才能充分发挥作用。
镀液因素属于不可逆性,其成份调整时,加入容易除去难,如果判断一旦不当,虽然纠正但费力,后果严重,而非镀液因素则具有可逆性,万一判断不当,比较容易纠正,不产生严重后果。
1.1镀液因素:是指电镀环节中由于镀液成份偏离规定范围,而引起镀液性能恶化,从而造成相应的电镀故障,镀液因素包括:1)镀液中的主盐、络合剂、导电盐、阳极活化剂、缓冲液以及各种添加剂等成份失调2)镀液中受到各种有害金属离子,氧化剂以及有机杂质感污3)水质不符,如Ca、Mg离子超标等因素等等1.2非电镀因素:是指电镀环节中除镀液因素外的其它各种因素1)镀液温度、PH值、电流密度等工艺条件失控2)工件抛、磨不符,基体表面状态不良3)工件镀前处理不当4)受镀时导电不良5)镀件周转发生沾污、氧化6)镀后处理中清洗不净7)干燥不符、工件受潮等等非电镀因素引起的故障缺陷,正是由于其偶然性诱发原因,而使电镀故障具有特征、程度不一,而且故障往往表面为时有时无,时轻时重等非规律性特征1.3镀液因素的故障原因确定方法镀液因素造成的故障,通常要通过镀液成份调整,或除杂净化来解决,如判断不当,在初步判断后未经确定,即加料处理,若未能消除故障,不仅造成人力、财力的浪费,而且使故障处理复杂化而延误生产,镀液因素确定方法:1)镀液成分失调:是电镀故障生产常见原因之一,诸如:镀液主盐浓度过低或铬合剂浓度过高,会使沉积速度降低,镀层容易烧焦,主盐浓度过高或铬合剂浓度过低,会造成镀层粗糙,导电盐过低易导致槽电压升高,溶液失调应采取镀液分析方法来检查确认故障原因,对症下药。
PCB镀层缺陷成因分析及其对策

PCB鍍層缺陷成因分析及其對策[摘要]分析了金属化孔镀层的主要缺陷及产生原因,从各主要工序出发,提出了如何优化工艺参数,进行严格的工艺及生产管理,以保证孔化质量的方法。
[关键词]多层印制板,金属化孔,镀层缺陷1 前言金属化孔质量与多层板质量及可靠性息息相关。
金属化孔起着多层印制线路电气互连的作用。
孔壁镀铜层质量是印制板质量的核心,不仅要求镀层有合适的厚度、均匀性和延展性,而且要求镀层在288℃热冲击10秒不能产生断裂。
因为孔壁镀铜层热冲击断裂是一种致命的缺陷,它将造成内层线路间和内层与外层线路之间断路;轻者影响线路断续导电,重者引起多层板报废。
目前,印制板生产中经常出现的金属化孔镀层缺陷主要有:金属化孔内镀铜层空洞、瘤状物、孔内镀层薄、粉红圈以及多层板孔壁与内层铜环连接不良等。
这些缺陷的绝大多数将导致产品报废,造成严重的经济损失,影响交货期。
2 金属化孔镀层主要缺陷的产生原因及相应对策我们首先简单回顾一下多层印制板的制造工艺过程。
下料→制板→蚀刻→黑化→层压→钻孔→去沾污及凹蚀处理→孔金属化→全板电镀→制板→图形电镀→脱膜→蚀刻→丝印阻焊→热风整平→丝印字符本文将从钻孔工序、孔壁去树脂沾污及凹蚀处理工序、电镀及多层板层压工序等几个方面,分析金属化孔镀层的主要缺陷及产生原因,阐述如何优化工艺参数,进行严格的工艺及生产管理,以保证孔化质量。
2.1 钻孔工序大多数镀层空洞部位都伴随出现钻孔质量差引起的孔壁缺陷,如孔口毛刺、孔壁粗糙、基材凹坑及环氧树脂腻污等。
由此造成孔壁镀铜层空洞,孔壁基材与镀层分离或镀层不平整。
下面,将对孔壁缺陷的成因及所采取的措施进行阐述:2.1.1 孔口毛刺的产生及去除无论是采用手工钻还是数控钻,也无论是采用何种钻头和钻孔工艺参数,覆铜箔板在其钻孔过程中,产生毛刺总是不可避免的。
孔口毛刺对于金属化孔质量的影响历来不被人们所重视,但对于高可靠性印制板的金属化孔质量来讲,它却是一个不可忽视的因素。
针对FPC电镀孔无铜事件的分析

针对电镀近期孔无铜事件分析报告一、主要原因分析:1、活化处理不良,活化液活性不够,温度太低,孔内不清洁,药液受到污染。
2.活化剂中钯离子含量不足,导致在活化过程中无法形成足够的胶体钯沉积在基材表面,在后续沉铜过程中,缺少钯离子催化而导致孔壁沉铜不良,引起孔内无金属缺陷。
二.次要原因:1.生产中管理者安排不到位,没有人来监控与管理,生产线处于失控状态。
2..图形转移与COV前处理时,微蚀次数过多,咬蚀底铜。
3..预浸与活化比重无法分析,导致无添加依据比重严重超标。
4..工艺操作条件控制不在范围内.5..生产中化学铜的PH值过低,活性太弱,沉铜速率过慢,由于化学铜需要强碱条件下才能进行,PH过低时甲醛还原能力下降,影响沉铜反应速率,造成沉铜不良。
6..钻孔质量太差,由于钻头不锋利,在钻孔过程中有大量的覆箔板切屑和钻渣残留在孔壁上至使这些部位沉积不上铜。
7..化学镀铜液组分浓度配比失调,PTH药液和镀液负载过大.三.改善预防措施:改善时间:(10.18-10.21)1..将负载过大和以污染的预侵药水更换。
2.在PTH生产过程中,对于活化缸及沉铜缸,应保证缸内各个组分维持在正常的浓度范围内,以保证化学反应的有序进行,除此之外,缸内PTH值及温度等也会影响孔壁内侧沉铜效果,应持续对其监控,要求每班开班和生产中每4小时分析一次,并做好相关记录。
3.PTH生产过程中适当提高活化缸及沉铜缸电振幅度,将原来的19º调为23º。
4.严格管控钻孔钻刀的使用时间以减少孔内切屑与杂质。
(需要钻孔工序控制)5.立即申购比重计,每班分析一次预浸,活化的比重,调整比重范围,始终控制在17Beº以上。
6.PTH后板电流密度从原来的1.6ASF改为1.5ASF,采用小电流长时间镀法,以保证孔内铜离子足够,保证孔壁电镀效果达到最佳。
7.减少图形与COV前处理微蚀次少,返工次数控制在2次以下。
8.增强员工的专业技能培训,每月至少培训3次以上。
孔无铜缺陷判读及改善

缺陷描述11
整孔无铜,而且大孔、小孔均无铜:
失效分析
➢ 特点:表面只有一层电镀层,孔内整孔无铜, ➢ 主要原因:
板件未沉铜就直接进行平板或图形电镀, 图形电镀时由于吊车故障等原因在微蚀缸停留时间 过长,平板层被全部蚀掉(从内层铜层形成负凹蚀 的情况进行确认)。
➢ 措施:对异常停机情况进行纠正,及时吊出微 蚀缸板件。
性差等原因,填胶不满导致碱蚀药水进入造成 孔内无铜; 措施:改用流动性较好B片,如高树脂含量等。
第四部分:纠正行动及改善方案
采用D-M-A-I-C改进模式: 界定(Define):对切片缺陷进行认真界定 测量(Measure):通过通断、BB机和切片 分析(Analyze):根据具体流程进行分析 改进(Improve):针对存在问题进行改进 控制(Control):有效控制形成文件指导生产
缺陷描述6
无铜处全部发生在树脂部位:
失效分析
特点:孔内无铜位置全部发生在树脂部位; 原因:除胶渣不够,树脂蜂窝状结构尚未形成; 措施:检查凹蚀段条件,提高除胶渣能力(如:
提高浓度、温度或延长时间等)
缺陷描述7
电镀层包住平板层,切片从孔口向孔中央平板层逐渐消失:
失效分析
➢ 特点:图形层包住平板层,切片从孔口向孔中 央平板层逐渐变薄并最后消失;
孔无铜缺陷判读及预 防
课程目标
帮助学员对切片缺陷进行判读; 通过案例对原因进行分析并预防; 降低孔定义 第二部分:原因分析 第三部分:缺陷现象及失效分析 第四部分:纠正行动及改善方案
第一部分:孔无铜定义
孔无铜是指印制板金属化孔孔内开路; 在通断检测时失去电气连接性能; 金属化孔包括:通孔、盲孔和埋孔; 孔壁不导通也称“破孔”或“孔内开路”。
电镀不良之原因与对策

電鍍不良之原因與對策鍍層品質不良的發生多半為電鍍條件、電鍍設備或電鍍藥水的異常.及人為疏忽所致。
通常在現場發生不良時比較容易找出原因克服.但電鍍後經過一段時間才發生不良就比較棘手.然而日後與環境中的酸氣、氧氣、水分等接觸.加速氧化腐蝕作用也是必須注意的。
以下對電鍍不良的發生原因及改善的對策加以探討說明。
鍍層檢驗在電鍍業界的鍍層檢驗.一般包括外觀檢查、膜厚測試、附著能力測試、抗腐蝕能力測試、抗老化能力測試等。
1.外觀檢查:一般廠家在檢查外觀比較多使用目視法.較嚴格則會使用4倍或10倍放大鏡檢查(在許多國際標準規範也是如此.如ASTM)。
建議作業人員先用目視法檢查.一旦看到有疑慮的外觀時.再使用放大鏡觀察。
而技術人員則建議必須以50~100倍來檢查(倍數越高.外觀瑕疵越多).甚至分析原因時還得借助200倍以上的顯微鏡。
在電鍍層的外觀判定標準.一般並無一定的規範.都需要由買賣雙方協議。
當然表面完全沒有瑕疵最好.但這是高難度.不過一般人們對色澤均勻這個定義比較能達成共識.因此匯整以下經常發生的一些外觀異常.供參考:(1)色澤不均.深淺色.異色(如變黑.發紅.發黃.白霧等)(2)光澤度不均勻.明亮度不一.暗淡粗糙(3)沾附異物(如水分.毛屑.土灰.油污.結晶物.纖維等)(4)不平滑.有凹洞.針孔.顆粒物等(5)壓傷.刮傷.磨痕.刮歪等各種變形現象及鍍件受損情形(6)電鍍位置不齊.不足.過多.過寬等(7)裸露底層金屬現象(8)有起泡.剝落.掉金屬屑等2.膜厚測試:鍍層膜厚測試方法有顯微鏡測試法、電解測試法、X 光螢光測試法、β射線測試法、渦流測試法、滴下測試法等。
其中以顯微鏡測試法最為正確.不過需要時間、設備、技術等支援.不適合檢驗用.一般用來做分析研究之用。
現在大部分都使用X光螢光測試法.因為準確度高.速度快(幾十秒)。
目前業界使用X-RAY 螢光膜厚儀的廠牌有德國的FISCHER、美國的CMI、日本的SEIKO.其測試原理與方法大同小異.但由於廠牌不同.多少會有少許誤差.只要使用標準片作好檢量線.作好定位工作.作好底材修正.即可將誤差降低到最小。
pcb板孔无铜原因分析--深联电路板

PCB板孔无铜原因分析—深联电路作者:深圳市深联电路有限公司PCB板孔无铜是印制电路板厂普遍头痛的问题,此种不良属于功能性问题,是深联电路一直严格监控关键点,同时,把好每道工序的品质检验关,以防不良品流出。
下面印制电路板厂将对PCB板孔无铜的原因做简要分析。
一、鱼骨图分析孔无铜产生原因二、案例分析1、钻孔导致的孔无铜孔未钻穿造成的孔无铜,切片特征:孔口有底铜未钻穿有钻咀断在孔内导致的孔无铜,切片特征:孔内有明显的断钻咀孔内残留钻粉导致的孔无铜整体图沉铜气泡导致的孔无铜,切片特征:断铜较对称,且图电层比板电层长。
整体图特写图,板电气泡导致的孔无铜,切片特征:面铜及孔内铜层都偏薄,孔内板电层从孔口至断口处呈拉尖趋势,且断口处板电层被图电层包裹住;孔内板电铜薄孔无铜---面铜板电层正常,但孔壁板电层从孔口至断口处呈拉尖趋势,且断口处板电层被图电层包裹住在D/F的制作过程中,孔中塞有火山灰或膜渣等异物,图电时影响药水的贯孔性能而产生孔无铜,或孔壁上沾有膜类油状物等抗镀物质,在电镀时影响镀铜及镀锡,蚀刻后产生孔无铜,切片特征:孔口两段板电铜及图电铜断口整齐,图电层未将板电层包住;或孔口一端断口拉尖,另一端断口整齐,图电层未将板电层包住。
5、图电孔无铜整体图1特写图1整体图2特写图2图电镀锡不良导致的孔无铜,切片特征:断铜较对称或板电与图电层断口较整齐,图电层未将板电层包住,即板电层比图电层长。
下面红色字体是赠送的精美网络散文欣赏,不需要的朋友可以下载后编辑删除!!谢谢!!!一一条猎狗将兔子赶出了窝,一直追赶他,追了很久仍没有捉到。
牧羊看到此种情景,讥笑猎狗说‘你们两个之间小的反而跑得快得多。
‘猎狗回答说:‘你不知道我们两个的跑是完全不同的!我仅仅为了一顿饭而跑,他却是为了性命而跑呀!目标二这话被猎人听到了,猎人想:猎狗说的对啊,那我要想得到更多的猎物,得想个好法子.于是,猎人又买来几条猎狗,凡是能够在打猎中捉到兔子的,就可以得到几根骨头,捉不到的就没有饭吃.这一招果然有用,猎狗们纷纷去努力追兔子,因为谁都不愿意看着别人有骨头吃,自已没的吃.就这样过了一段时间,问题又出现了.大兔子非常难捉到,小兔子好捉.但捉到大兔子得到的奖赏和捉到小兔子得到的骨头差不多,猎狗们善于观察发现了这个窍门,专门去捉小兔子.慢慢的,大家都发现了这个窍门.猎人对猎狗说:最近你们捉的兔子越来越小了,为什么?猎狗们说:反正没有什么大的区别,为什么费那么大的劲去捉那些大的呢?动力三猎人经过思考后,决定不将分得骨头的数量与是否捉到兔子挂钩,而是采用每过一段时间,就统计一次猎狗捉到兔子的总重量.按照重量来评价猎狗,决定一段时间内的待遇.于是猎狗们捉到兔子的数量和重量都增加了.猎人很开心.但是过了一段时间,猎人发现,猎狗们捉兔子的数量又少了,而且越有经验的猎狗,捉兔子的数量下降的就越利害.于是猎人又去问猎狗.猎狗说‘我们把最好的时间都奉献给了您,主人,但是我们随着时间的推移会老,当我们捉不到兔子的时候,您还会给我们骨头吃吗?‘四猎人做了论功行赏的决定.分析与汇总了所有猎狗捉到兔子的数量与重量,规定如果捉到的兔子超过了一定的数量后,即使捉不到兔子,每顿饭也可以得到一定数量的骨头.猎狗们都很高兴,大家都努力去达到猎人规定的数量.一段时间过后,终于有一些猎狗达到了猎人规定的数量.这时,其中有一只猎狗说:我们这么努力,只得到几根骨头,而我们捉的猎物远远超过了这几根骨头.我们为什么不能给自己捉兔子呢?‘于是,有些猎狗离开了猎人,自己捉兔子去了骨头与肉兼而有之……五猎人意识到猎狗正在流失,并且那些流失的猎狗像野狗一般和自己的猎狗抢兔子。
- 1、下载文档前请自行甄别文档内容的完整性,平台不提供额外的编辑、内容补充、找答案等附加服务。
- 2、"仅部分预览"的文档,不可在线预览部分如存在完整性等问题,可反馈申请退款(可完整预览的文档不适用该条件!)。
- 3、如文档侵犯您的权益,请联系客服反馈,我们会尽快为您处理(人工客服工作时间:9:00-18:30)。
深孔电镀孔无铜缺陷成因探讨及改善摘要随着线路板技术的不断发展,深孔电镀正逐渐成为线路板电镀技术的发展方向及目标,而由于深孔电镀产品纵横比高的特点,PTH流程极易出现孔内无金属现象,造成后续孔内电镀不佳等缺陷。
本文针对多层线路板尤其是高纵横比线路板在PTH加工制造过程中容易出现的孔内无金属问题进行详细分析,并针对不同类型的PTH孔内无金属现象确定改善措施,以应对高纵横比PCB产品对PTH工序所带来的挑战。
关键词深孔电镀 PTH 高纵横比孔内无金属Causes and Improvement of Hole Without Copper during DeepHole PlatingZHANG Yan-sheng DENG Dan ZHU Tuo TIAN Wei-feng ZHOU Yi CUI Qing-pengAbstract: As the circuit board technology unceasing development, deep-hole plating is gradually becoming the direction and target. PTH (plated throw hole) prone to no metal hole because of the high aspect ratio features, causing the defects such as poor hole-plating. This paper analyzed the poor hole-plating during PTH manufacturing process based on the multilayer circuit board, especially high aspect ratio wiring board. Improvement measures to different poor hole-plating types were put forward to cope with the high aspect ratio PCB products on the PTH process challenges.Key words: deep-hole plating; PTH; high aspect ratio; hole without metal1前言随着电子产品与技术的不断发展创新,电子产品的设计概念逐渐走向轻薄、短小,印刷电路板(PCB)的设计也在向小孔径、高密度、多层数、细线路的方向发展。
而伴随线路板层数厚度增加和孔径的减小,产品通孔厚径比增加明显,PTH加工难度逐渐加大,易导致孔内无金属现象频发。
针对此类问题,本文通过药水异常、特殊设计及生产操作等方面介绍深孔电镀在PTH过程中孔内无金属现象产生的具体原因,并根据不同原因确定预防及改善措施,确保PTH良好,保证后续深孔电镀效果。
2线路板PTH原理PTH也称电镀通孔,主要作用是通过化学方法在绝缘的孔内基材上沉积上一层薄铜,为后续电镀提供导电层,从而达到内外层导通的作用。
PTH主要流程如下图1所示:图1 PTH 流程图其中,涉及化学反应如下所示:活化:Pd 2++2Sn 2+→[PdSn]2+ —— 在溶液中反应形成不稳定络合物[PdSn]2+→Pd+ Sn 4++ Sn 2+ ——大部分络合物被还原成金属钯SnCl 2+H 2→Sn(OH)Cl+HC l ——活化后水洗时SnCl 2水解生成碱式锡酸盐沉淀随着SnCl 沉淀,Pd 核也一起在活化的基材表面沉积沉铜:HCHO+OH -→H 2+HCHOO - ——Pd 作为催化剂时,该步反应才能得以进行Cu+H 2+OH -→Cu+2H 2O ——铜离子在碱性条件下被还原成金属铜 PTH 后孔内结构如下图2所示:图2 化学镀铜沉积示意图 3 PTH 孔内无金属产生原因分析及改善措施由于深孔电镀产品纵横比较高,导致在PTH 过程中,孔内药水交换困难,极易出现孔内无金属现象。
线路板PTH 流程孔内无金属切片形态明显,不同原因所造成孔内无金属现象相近,需仔细分析区分才能辨别出造成该缺陷真正原因,根据不同切片形态,可将PTH 孔内无金属分为如表3.1中三大类:表1 不同PTH 类别孔内无金属切片形态表原因 药水异常 特殊设计 生产操作典型切片图钯金属微粒 基材 不连续镀层连续镀层3.1药水异常类药水异常所造成PTH孔内无金属缺陷主要表现为孔内星点装PTH不良,缺陷处图电铜包裹板电铜,缺陷示意图如下图3:图电铜图电铜包裹板电铜板电铜基材图3 药水异常PTH孔内无金属示意图3.1.1产生原因A、活化剂中钯离子含量不足,导致在活化的过程中无法形成足够的胶体钯沉积在基材表面,在后续沉铜过程中,缺少钯离子催化从而导致孔壁沉铜不良,引起孔内无金属缺陷。
B、活化缸内渗入微小气泡,引起缸内胶体钯水解,使活化缸丧失活化功能,孔内无法沉积铜层。
C、溶液内PH值过低,由于化学沉铜需要在强减性条件下才能进行,PH过低时甲醛还原能力下降,影响沉铜反应速率,造成沉铜不良。
D、沉铜缸内络合剂不足,导致部分铜离子生成氢氧化铜沉淀,铜缸内没有足够的铜离子进行反应来沉积到孔壁内侧,导致沉铜不良发生。
3.1.2改善措施在PTH生产过程中,对于活化缸及沉铜缸,应保证缸内各个组分维持在正常的工艺浓度范围内,以保证化学反应的有序进行。
除此之外,缸内PH及温度等也会影响孔壁内侧沉铜效果,应持续对其监控。
活化缸内胶体钯受细小气泡影响,极易产生水解,因此,应保证缸内管道无漏气现象,保证胶体钯的正常反应。
3.2特殊设计类此类原因所造成孔内无金属切片形态主要表现为缺陷处明显图电铜包裹板电铜,同时缺陷处存在内层铜被电镀加厚现象,如下示意图4:图4 特殊设计孔内无金属示意图3.2.1产生原因 对于深孔电镀产品,纵横比往往较大,在这种情况下,孔内药水交换速率下降明显,导致PTH 过程中孔中心部沉铜层往往不够致密。
在这种情况下,若板内孔存在如下图5所示设计,则在PTH 后板电过程中,内层铜A 处因纵横比过大沉铜层相比于B 处不够致密,导致在板电通电后电势高于B 处,因B 处通过内层铜与C 相导通,故虽然A 较C 更接近孔口,但电势仍较高,吸收铜离子能力小于C 点。
另深孔电镀在板电过程中,孔内溶液交换速度较慢,孔内铜离子相对较少。
基于以上两点,在板电过程中,A 处在原本铜离子相对较少的情况下,因电势原因吸收铜离子能力再次下降,直接导致其电镀铜层厚度不足,A 处在后续工序(外层图形及图形电镀)前处理因损铜造成孔内开路,从而引起孔内无金属缺陷。
图5 孔内沉铜厚度差异示意图3.2.2预防措施 针对此类设计上的问题,在保证设计原稿不变更的情况下,可以适当调整沉铜及板电参数,以保证A 处铜厚足够,避免在后续流程中损铜开路。
主要方法可以将原沉铜时间延长或在完成一次沉铜后,将板从预浸缸再次进板沉铜,保证沉铜层厚度;还可以在一次沉铜后,小电流短时间(8ASF*30min )板电,板电后从除油缸进板再次进行沉铜,然后在板电将孔铜加厚至足够;此外还可以在沉铜条件不变的情况下,适当降低板电电流密度,延长电镀时间,保证孔内铜离子足够及镀层均匀。
Cu 2+Cu 2+ Cu 2+ Cu 2+ 图电铜板电铜内层铜处图电铜包裹板电铜 BA CC A3.3生产操作类生产操作类造成PTH孔内无金属主要为设备异常及违规操作,切片特点主要有孔内残存异物、孔内缺陷处图电铜包裹板电铜等,其缺陷示意图如下图6:振动气顶异常异物堵孔图6 生产操作孔内无金属示意图3.3.1产生原因生产操作所造成孔内无金属主要为PTH前去毛刺和PTH过程中活化及沉铜缸设备异常所造成,主要异常有:PTH前去毛刺段后处理高压水洗异常,导致孔内钻屑铜粉等异物无法及时排出,造成后续PTH过程中,孔内药水无法正常交换,从而导致孔内沉铜不良;此外,在PTH过程中,活化缸及沉铜缸内振动及气顶异常停止或振动幅度频率不合格也会造成孔内气泡无法及时排出,影响孔内药水交换,导致沉铜异常,从而引起孔内无金属缺陷。
3.3.2改善措施针对高纵横比产品,在PTH及前处理去毛刺过程中务必保证设备处于正常工作状态,此外,对于此类深孔电镀产品,可是当更改工艺参数,以保证孔内清洁和足够的药水交换。
在前处理去毛刺可采用正常去一次毛刺后再额外进行高压摇摆水洗,对产品孔内进行再次清洁;此外可在加工高纵横比产品时适当提高PTH活化缸及沉铜缸电振幅度,可将原2.5m/s提高至3m/s,从而保证在PTH过程中,孔内无气泡残存。
4总结针对深孔电镀产品板厚较厚,孔径较小,纵横比高的特点,为保证在PTH过程中消除孔内无金属缺陷,需对设备、工艺参数以及工艺流程等进行适当调整,以保证孔内PTH质量。
具体措施如下:A、PTH前去毛刺后,再多进行一次高压摇摆水洗,以清除孔内钻屑等异物。
B、PTH过程中保证各缸尤其是活化及沉铜缸药水、温度计PH参数都处在正常工艺范围内。
C、PTH过程中适当提高活化缸及沉铜缸电振幅度,由原2.5m/s提高至3m/s。
D、一次PTH后将板从预浸缸再次进板,额外沉铜一次;或者在PTH一次后,板电用8ASF电镀30NIN后再次从除油缸进板沉铜;保证孔内铜层均匀性。
E、PTH后板电需采用小电流长时间,以保证孔内铜离子足够保证孔壁电镀效果。
参考文献[1]罗卓生,盲孔无铜之树脂杂物空洞分析[J].印制电路信息.2009年S1期.[2]李林宏,图形电镀孔内无铜的产生原因分析[J].印制电路信息. 2012/04.[3]冯绍彬,铜箔表面电镀铜粗化工艺[J].材料保护.2010/07.。