切削温度测量方法综述
金属切削原理与刀具 课题13 切削温度的分布

切削温度的测量方法
2、辐射测温法
辐射测温法是一种非接触式测量方法。它是利用高温辐射能 量来测量工件表面温度的。 作为测量用的传感器有光电传感器及热敏射测温法
光电传感器可以用锗光电二极 管或硫化铅光电池。在刀片上 打一个小的锥孔,一直通到刀 具的前面上,从切屑底面测定 辐射能,通过标定求得切屑底 面该点的温度。
(1)自然热电偶法
热电偶的热端
切削过程中,工件、刀具通常是由两种不同的金属材料组成的。 在刀具与切屑和刀具与工件接触区总存在着相当高的切削温度
热电偶的冷端 离接触区较远的工件与刀具处一般保持在室温状态
切削温度的测量方法
1、热电偶法 热电偶法包括自然热电偶法和人工热电偶法。
(1)自然热电偶法
可用导线将工件与刀具的冷端接到仪表上,即可将切削热电势显示和 记录下来。根据事先作出热电偶的标定曲线(温度与毫伏值的对应关 系曲线),即可求得刀具与切屑和刀具与工件接触面的平均温度,即 切削温度。
1—激光管; 2—光栅; 3、4—透镜; 5—光敏元件; 6—刀片; 7—刀体
用光电传感器测量刀具与切屑接触面 温度分布的示意图
切削温度的测量方法
用辐射测温法测量工件与刀具侧面的 温度分布的示意图
热敏电阻传感器
优点 测定区域的直径只有0.15 mm,因此, 可缩小不同测定点之间的距离。
缺点 只能测量刀具侧面的温度而不能测量垂 直切削刃工作部位中间剖面的温度。
切削温度
切削温度是指切削区域的平均温度。 切削温度的高低取决于产生热量的多少和热量传散的快慢。
切削温度
(1)切削温度计算
用实验方法得到的计算切削温度的指数公式为:
C
v z c
机床可编程控制系统中的切削温度测量与控制研究
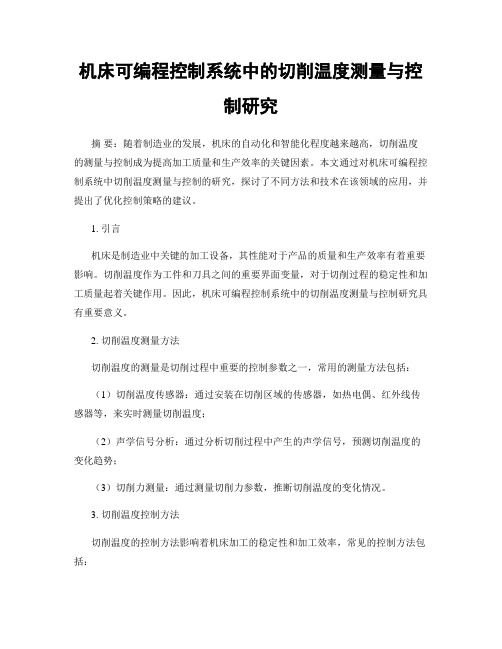
机床可编程控制系统中的切削温度测量与控制研究摘要:随着制造业的发展,机床的自动化和智能化程度越来越高,切削温度的测量与控制成为提高加工质量和生产效率的关键因素。
本文通过对机床可编程控制系统中切削温度测量与控制的研究,探讨了不同方法和技术在该领域的应用,并提出了优化控制策略的建议。
1. 引言机床是制造业中关键的加工设备,其性能对于产品的质量和生产效率有着重要影响。
切削温度作为工件和刀具之间的重要界面变量,对于切削过程的稳定性和加工质量起着关键作用。
因此,机床可编程控制系统中的切削温度测量与控制研究具有重要意义。
2. 切削温度测量方法切削温度的测量是切削过程中重要的控制参数之一,常用的测量方法包括:(1)切削温度传感器:通过安装在切削区域的传感器,如热电偶、红外线传感器等,来实时测量切削温度;(2)声学信号分析:通过分析切削过程中产生的声学信号,预测切削温度的变化趋势;(3)切削力测量:通过测量切削力参数,推断切削温度的变化情况。
3. 切削温度控制方法切削温度的控制方法影响着机床加工的稳定性和加工效率,常见的控制方法包括:(1)切削速度调整:通过调整切削速度来控制切削温度的升降;(2)冷却剂的喷射与控制:通过喷射冷却剂来控制切削区域的温度;(3)刀具材料与涂层选择:通过选择合适的刀具材料和涂层来提高切削效率和降低温度。
4. 切削温度测量与控制系统的设计机床可编程控制系统在切削温度测量与控制中扮演着重要的角色。
对于系统的设计,需要考虑以下几个方面:(1)传感器的选择与布置:根据不同的测量方法,选择合适的切削温度传感器,并合理布置在切削区域;(2)数据采集与处理:采用合适的数据采集设备和算法,实时采集和处理切削温度数据;(3)控制策略的优化:根据不同的控制方法和系统需求,设计合理的控制策略,提高切削温度的测量与控制精度。
5. 优化控制策略的建议为了进一步提高机床可编程控制系统中切削温度的测量与控制效果,可尝试以下优化策略:(1)多传感器融合:利用多种不同的传感器进行切削温度测量,通过数据融合算法得到更加准确的温度结果;(2)智能控制算法:运用人工智能和机器学习算法,根据实时的温度数据,自动调整切削参数和控制策略;(3)在线监测与预警:实时监测切削温度的变化趋势,提前预警可能出现的异常情况,保证加工质量和安全;(4)创新材料与涂层技术:不断研发新型刀具材料和涂层技术,提高工具的散热能力和耐磨性。
切削温度测量方法

切削温度测量方法
嘿,你问切削温度咋测量啊?这事儿咱得好好聊聊。
先说说热电偶法吧。
这就像给切削过程装个小温度计。
找个合适的热电偶,把它放在切削的地方附近。
热电偶能感应温度变化,然后把温度信号传出来。
不过放的时候可得小心,不能影响切削过程,也不能被切坏喽。
而且还得选对热电偶的类型,不然测出来的温度可不准。
还有辐射测温法。
就像用个小望远镜看切削时发出的热辐射。
通过测量辐射的强度啥的,就能算出温度。
这方法不用直接接触切削的地方,挺方便的。
但是得注意周围环境的影响,不能有别的热源干扰。
另外呢,硬度法也可以试试。
切削后看看工件的硬度变化,因为温度会影响材料的硬度。
不过这方法不是特别直接,得通过一些经验公式来推算温度。
还有一种叫金相法。
切削完了看看材料的金相组织,不同温度下金相组织会不一样哦。
这就像给材料做个小体检,通过观察组织变化来判断温度。
但是这方法比较麻烦,需要专业的设备和知识。
我给你讲个事儿吧。
有一次我们车间要测切削温度,一开始大家都不知道咋弄。
后来找了个老师傅,他用热电偶法测了一下,发现温度有点高。
于是大家就想办法调整切削参数,降低温度。
后来再测的时候,温度就正常了。
从那以后,我们就知道了切削温度测量的重要性,也学会了用不同的方法来测量。
总之呢,切削温度测量有好几种方法,你可以根据实际情况选择合适的。
只要你用心去做,肯定能测出准确的温度。
加油吧!。
切削温度测定实验报告总结

切削温度测定实验报告总结首先,我们使用了切削温度测定仪器对不同材料进行切削实验,包括钢、铜、铝等常见的金属材料。
通过调整仪器的参数,如进给速度、切削深度和切削速度,我们对不同条件下的切削温度进行了测定。
实验结果显示,在相同的切削条件下,切削温度随着材料的不同而有所差异。
钢材的切削温度较高,铜材的切削温度较低,铝材的切削温度则介于两者之间。
其次,我们对实验结果进行了分析和总结。
首先,切削温度的高低与材料的导热性密切相关。
导热性越差的材料,切削温度越高,反之亦然。
其次,切削温度受切削速度的影响较大。
在其他条件相同的情况下,切削速度越大,切削温度越高。
进给速度和切削深度对切削温度的影响相对较小。
最后,我们发现切削温度的高低对切削过程中的刀具磨损和加工表面质量有重要影响。
切削温度过高会导致刀具磨损加剧和加工表面质量下降。
在实验过程中,我们还注意到了切削润滑剂对切削温度的影响。
切削润滑剂的使用可以有效降低切削温度,减少切削过程中的热损耗,提高切削效率和加工质量。
因此,在实际生产过程中,合理选择和使用切削润滑剂是非常重要的。
综上所述,切削温度测定实验是一项非常有价值的实验技术,对于金属加工和切削领域中的研究和应用具有重要意义。
通过对材料、切削条件和切削润滑剂等因素的分析和总结,可以为加工过程的优化和质量的提高提供理论和实践依据。
在今后的研究和应用中,我们可以进一步深入探索切削温度与刀具寿命、切削力和加工表面质量等指标之间的关系,以进一步提高切削过程的可靠性和效率。
实验三-切削温度实验

实验三切削温度实验一、实验目的和要求1.了解车削时自然热电偶的构成以及采用自然热电偶进行切削温度实验的原理和方法;2.掌握自然热电偶现场快速标定的原理和方法,并获得其标定公式;3.进行切削温度单因素实验或正交实验,了解切削用量对切削温度的影响规律,获得切削温度的实验公式;4.认知计算机辅助实验硬、软件的系统构成,并熟悉自然热电偶标定与切削温度实验软件的具体操作。
二、实验原理与测量方法1. 切削温度实验与标定系统的组成切削温度实验系统由切削系统、切削温度实验仪器和计算机系统三大部分组成(图1、图3)。
切削系统包括组成自然热电偶的工件(切屑)和硬质合金刀片,以及水银集电器、专用测温车刀等。
切削温度实验仪器包括室温采集与数显板、三路高精度高倍率线性放大板以及为自然热电偶快速标定提供加热电源与控制的元器件等。
计算机系统包含12位A/D板、计算机主机及其外设。
此外,本系统还设置了自然热电偶标定附件。
系统使用接插线缆连接:1)切削系统⇔切削温度实验仪器;2)标定电源连接;3)切削温度实验仪器⇔计算机系统之间有两组扁平线接插件。
4)仪器电源线与普通的计算机电源线相同。
5)切削温度实验仪器接地螺钉位于其背面的钢板上,请务必将切削温度实验仪器用电线连接到符合标准的地线上!图1 自然热电偶测温系统框图图2 在车床上的切削温度实验系统全貌2. 切削温度的测量方法在切削过程中,硬质合金刀片和工件(切屑)组成了自然热电偶,切削温度实验就是将这个自然热电偶作为传感器来测量切屑温度的。
切削时,自然热电偶产生的是温差热电势和温差热电流,“刀-屑”及“刀-工”接触区的高温端温度与硬质合金刀片另一端的冷端温度之差相当显著,所以,产生的热电势可以测量得到。
硬质合金刀片作为自然热电偶的一个热电极,工件和切屑作为另一极。
再将工件和切屑组成的这一极分成两部分,前者包括被切削加工的工件和与其紧密相连的一段切屑,后者就是一段切屑,这两段切屑端部的电压就是实验的检测对象——自然热电偶的热电势值。
切削温度测量方法综述
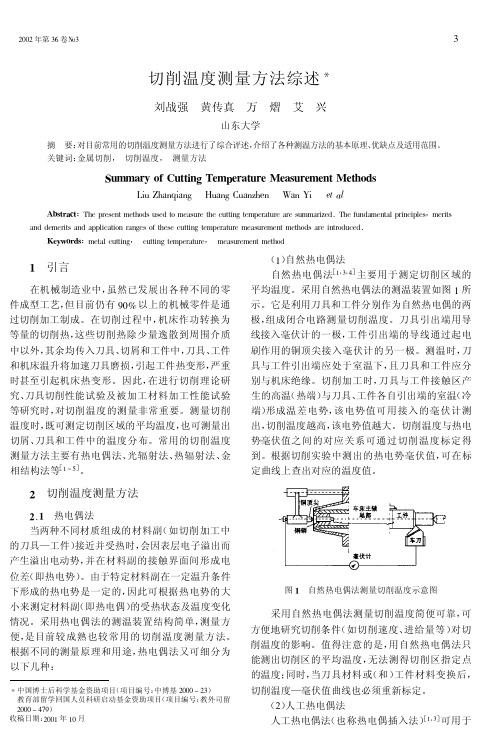
电敏感材料金属丝 (如康铜) 焊在待测温点上作为一 极、 以工件材料或刀具材料作为另一极而构成的热 电偶。采用该方法测量切削温度的工作原理与自然 热电偶法和人工热电偶法相同 (见图 3) 。由于半人 工热电偶法测温时采用单根导线连接, 不必考虑绝 缘问题, 因此得到了较广泛的应用。
图! 红外辐射测温示意图
律求出辐射单元表面的温度分布场及动态变化。虽 然红外热像仪所测温度为相对温度, 滞后于实际切 削温度, 但根据传热反求算法可准确求得切削过程 中工件 (或刀具) 的温度变化规律及动态分布。红外 热像仪测温法具有直观、 简便、 可远距离非接触监测 等优点, 在恶劣环境下测量物体表面温度时具有较 大优越性。 此外, 测量切削温度的光、 热辐射方法还有红外
Liu Zhangiang Huang Cuanzhen Wan Yi !" #$
Abstract:The present methods used to measure the cutting temperature are summarized. The fundamentaI principIes,merits and demerits and appIication ranges of these cutting temperature measurement methods are introduced. Keywords:metaI cutting, cutting temperature, measurement method
[9, l0]
式中
— —物 体 辐 射 单 元 单 位 面 积 的 辐 射 能 量 !— (W / m2) — —物体辐射单元表面辐射率 (取决于物 !— 体表面性质) — —斯 蒂 芬—波 尔 兹 曼 常 数 (" = 5.76 > "— -8 2 4 l0 W / m ・ K) — —物体辐射单元的表面温度 (K) "— 切削时, 红外热像仪通过光机扫描机构探测工
切削温度的测量
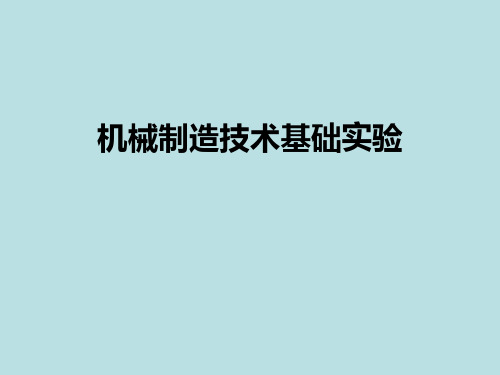
四、实验报告的要求
(一)实验名称 (二)实验目的 (三)实验条件 (四)数据记录与整理 (五)实验结果 1.切削速度 对切削温度的影响 a. 实验参数:工件直径 ;ap= ;f= ; γo = ; b. 在双对数坐标纸上绘出曲线 c. 计算 2.进给量 对切削温度的影响 a. 实验参数:工件直径 ;ap= ;f= ; γo= ; b.在双对数坐标纸上绘出曲线 c.计算 d.求出经验公式
三、实验内容及步骤
自然热电偶法是利用工件和刀具材料化学 成份的不同,分别将工件、刀具与机床绝缘 后组成热电偶的两极。当工件与刀具接触区 的温度升高后,形成热电偶的热端,工件的 引出端和刀具的尾端保持室温形成热电偶的 冷端,这样在刀具与工件的回路中(见图31)便产生了温差电动势,且热电势的大小 与温度的高低有一定的关系。实验前刀具— 工件热电偶应进行标定,求出温度与热电势 的标定曲线。实验时根椐切削过程中测到的 电动势毫伏值,在标定曲线上即可查出相对 应的温度值。自然热电偶法测到的温度仅是 刀—屑、刀—工件摩檫面的平均温度,不 能测量切削区指定点的切削温度。
1)改变切削速度vC;记录电动势的毫伏值;在标定曲线上 查出对应温度;将数据填入记录表。
2)在双对数坐标纸上画出θ-vC线,求出表达切削区平均温 度同切削速度vC的单项切削温度指数关系:
c(v2)cz
其中: θ -切削温度;cθv-对单因素vC的切削温度公式的系 数;一般, z θ =0.26-0.41,进给量越大, z θ值越小.
123456
(六) 分析 分析比较各因素对切削温度的影响。
1)改变进给量f;记录电动势的毫伏值;将数据填入记录表 ;在标定曲线上查出对应温度。
2)在双对数坐标纸上画出θ -f线,求出表达切削区平均温 度与进给量 的单项切削
高速切削过程测温方法综述
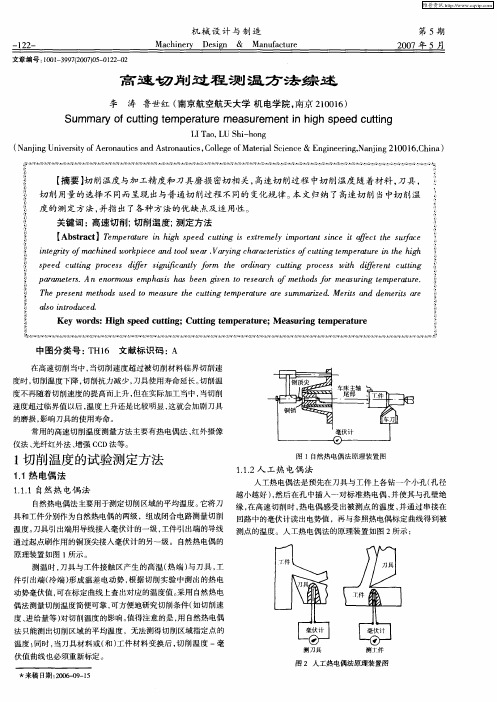
高 速 切 削 过 程 测 温 方 法 综 述
李 涛 鲁 世红 ( 京航 空航 天大学 机 电学院 。 京 20 1 ) 南 南 106
Su mmar fc t n e y o u t g t mp r t r a u e n i p e u t g i e a u e me s r me ti hgh s e d c ti n n
效果 。
光纤红 外测温仪传感 头小 , 电路 简单 , 积小 , 体 价格 经济
测 刀具 测工 件
且易于安装 , 输出信号可直接接 人数据采集器 , 响应时 间快 ( 最 快已达 到 l s o因此 , m 采用光纤红外测温法对高速切削加工中 温度进行实施监测是可行而有效 的 ,它能快速反映工件温度场 的变化 , 其准确度 可达 ±1 完全满足要求。 ℃,
原 理 装置 如 图 1 示 。 所
测 温时 . 刀具与工件接触 区产生 的高温 ( 热端 ) 与刀具 , 工 件引出端 ( 冷端 ) 形成温差 电动势 , 根据切 削实验 中测 出的热 电 动势毫伏值 , 可在标定 曲线上查 出对应的温度值 。 采用 自然 热电 偶法测量切削温度简便可靠 , 可方便地研 究切 削条件 ( 如切 削速 度、 进给量等 ) 对切削温度的影响。 值得注意的是 , 自然热 电偶 用 法 只能测出切 削区域 的平均温度 ,无法测得切削 区域指定点的
合金 和涂层材料 , 钻孔 比较困难 , 因此限定 了该方法 的应用。
可测得温度场的分布和最高温度 的位置。对于特定 的人工热 电
光密介质。 上诉角度称为全反射临界角 , 光就在纤 芯中曲折反射
前 进而不会泄漏f 3 1 。
一
11 .. 3半人 工热 电偶 法
- 1、下载文档前请自行甄别文档内容的完整性,平台不提供额外的编辑、内容补充、找答案等附加服务。
- 2、"仅部分预览"的文档,不可在线预览部分如存在完整性等问题,可反馈申请退款(可完整预览的文档不适用该条件!)。
- 3、如文档侵犯您的权益,请联系客服反馈,我们会尽快为您处理(人工客服工作时间:9:00-18:30)。
3中国博士后科学基金资助项目(项目编号:中博基2000-23)教育部留学回国人员科研启动基金资助项目(项目编号:教外司留2000-479)收稿日期:2001年10月切削温度测量方法综述3刘战强 黄传真 万 熠 艾 兴山东大学摘 要:对目前常用的切削温度测量方法进行了综合评述,介绍了各种测温方法的基本原理、优缺点及适用范围。
关键词:金属切削, 切削温度, 测量方法Summary of Cutting T emperature Measurement MethodsLiu Zhanqiang Huang Cuanzhen Wan Y i et alAbstract :The present methods used to measure the cutting temperature are summarized.The fundamental principles ,merits and demerits and application ranges of these cutting temperature measurement methods are introduced.K eyw ords :metal cutting , cutting temperature , measurement method 1 引言在机械制造业中,虽然已发展出各种不同的零件成型工艺,但目前仍有90%以上的机械零件是通过切削加工制成。
在切削过程中,机床作功转换为等量的切削热,这些切削热除少量逸散到周围介质中以外,其余均传入刀具、切屑和工件中,刀具、工件和机床温升将加速刀具磨损,引起工件热变形,严重时甚至引起机床热变形。
因此,在进行切削理论研究、刀具切削性能试验及被加工材料加工性能试验等研究时,对切削温度的测量非常重要。
测量切削温度时,既可测定切削区域的平均温度,也可测量出切屑、刀具和工件中的温度分布。
常用的切削温度测量方法主要有热电偶法、光辐射法、热辐射法、金相结构法等[1~5]。
2 切削温度测量方法2.1 热电偶法当两种不同材质组成的材料副(如切削加工中的刀具—工件)接近并受热时,会因表层电子溢出而产生溢出电动势,并在材料副的接触界面间形成电位差(即热电势)。
由于特定材料副在一定温升条件下形成的热电势是一定的,因此可根据热电势的大小来测定材料副(即热电偶)的受热状态及温度变化情况。
采用热电偶法的测温装置结构简单,测量方便,是目前较成熟也较常用的切削温度测量方法。
根据不同的测量原理和用途,热电偶法又可细分为以下几种:(1)自然热电偶法自然热电偶法[1,3,4]主要用于测定切削区域的平均温度。
采用自然热电偶法的测温装置如图1所示。
它是利用刀具和工件分别作为自然热电偶的两极,组成闭合电路测量切削温度。
刀具引出端用导线接入毫伏计的一极,工件引出端的导线通过起电刷作用的铜顶尖接入毫伏计的另一极。
测温时,刀具与工件引出端应处于室温下,且刀具和工件应分别与机床绝缘。
切削加工时,刀具与工件接触区产生的高温(热端)与刀具、工件各自引出端的室温(冷端)形成温差电势,该电势值可用接入的毫伏计测出,切削温度越高,该电势值越大。
切削温度与热电势毫伏值之间的对应关系可通过切削温度标定得到。
根据切削实验中测出的热电势毫伏值,可在标定曲线上查出对应的温度值。
图1 自然热电偶法测量切削温度示意图采用自然热电偶法测量切削温度简便可靠,可方便地研究切削条件(如切削速度、进给量等)对切削温度的影响。
值得注意的是,用自然热电偶法只能测出切削区的平均温度,无法测得切削区指定点的温度;同时,当刀具材料或(和)工件材料变换后,切削温度—毫伏值曲线也必须重新标定。
(2)人工热电偶法人工热电偶法(也称热电偶插入法)[1,3]可用于测量刀具、切屑和工件上指定点的温度,并可测得温度分布场和最高温度的位置。
人工热电偶法测温装置如图2所示。
在刀具或工件被测点处钻一个小孔(孔径越小越好,通常<<015mm ),孔中插入一对标准热电偶并使其与孔壁之间保持绝缘。
切削时,热电偶接点感受出被测点温度,并通过串接在回路中的毫伏计测出电势值,然后参照热电偶标定曲线得出被测点的温度。
图2 人工热电偶法测量切削温度示意图人工热电偶法的优点是:对于特定的人工热电偶材料只需标定一次;热电偶材料可灵活选择,以改善热电偶的热电敏感性和动态响应速度,提高热电偶传感质量。
但由于将人工热电偶埋入超硬刀具材料(如陶瓷、PC BN 、PC D 等)内比较困难,因此限制了该方法的推广应用。
(3)半人工热电偶法将自然热电偶法和人工热电偶法结合起来即组成了半人工热电偶法[3]。
半人工热电偶是将一根热电敏感材料金属丝(如康铜)焊在待测温点上作为一极、以工件材料或刀具材料作为另一极而构成的热电偶。
采用该方法测量切削温度的工作原理与自然热电偶法和人工热电偶法相同(见图3)。
由于半人工热电偶法测温时采用单根导线连接,不必考虑绝缘问题,因此得到了较广泛的应用。
图3 半人工热电偶法测量切削温度示意图 (4)等效热电偶法采用自然热电偶法测量切削温度时,由于温升的影响,导线引出点的温度已不是标定时的室温,因此需要进行冷端温度补偿。
但冷端温度补偿在原理和具体实现方法上均存在一定问题,如测量PC BN 刀具的切削温度时,由于作为热电偶一端的PC BN 复合片尺寸小、导热系数大,导线引出点的温升较大,影响测量精度,需要予以消除,但采用接长刀片消除法在PC BN 刀具上不易实现,若采用附加电势消除法则因刀片引出点有温升,所测电动势也难以反映真正的切削温度。
此时,可采用等效热电偶法[6,7]测量PC BN 焊接车刀外圆车削的切削温度,其工作原理如图4所示。
刀片与工件组成自然热电偶的两极,热端为刀—屑接触部分A (其平均温度即为需要测量的切削温度θ);冷端分别为工件与刀具的引出端。
工件引出点C 处的温度为室温θ0,刀具引出点B 由于距离刀尖较近而有温升,由于B 点温度是测量计算切削温度所必须的,因此需同时测量B 点温度θ′。
测量时,采用一标准热电偶(NiCr 2NiSi )测量B 点温度θ′(其中NiCr 端也是主测量回路C 2A 2B 的引出端)。
测量得到两个热电动势:E 1为工件—刀具—导线(NiCr )所构成的主测量回路产生的热电动势;E 2为标准热电偶(NiCr 2NiSi )产生的热电动势。
通过标定装置获得各材料间的热电特性曲线,求出其斜率,再由测得的E 1、E 2计算出切削温度θ为θ=1b WTE 1+b bw +b WTb b b WTE 2+θ0(1)式中 b WT ———工件—刀具的热电特性曲线斜率b bw ———导线—工件的热电特性曲线斜率b b ———刀具引出点测量热电偶热电特性曲线斜率图4 等效热电偶法测量切削温度示意图2.2 光、热辐射法采用光、热辐射法测量切削温度的原理是:刀具、切屑和工件材料受热时都会产生一定强度的光、热辐射,且辐射强度随温度升高而加大,因此可通过测量光、热辐射的能量间接测定切削温度[8]。
(1)辐射高温计法使用红外辐射高温计可测定刀具或工件表面的温度分布。
红外探测器将接收的红外线转换为电信号,经线性化处理后即可获得相应的温度值[9,10]。
红外辐射高温计的测温方法如图5所示。
但采用红外辐射高温计只限于测量刀具或工件外表面的温度。
图5 红外辐射测温示意图(2)红外照相法采用红外照相法[2]的车削温度测量装置如图6所示。
测温装置安装于车床横溜板的机座板上,使刀具、照相机相对于工件排成一线;照相机配有专门的红外辐射聚焦调节装置;刀夹可使照相机镜头尽可能接近工件表面;为避免切屑溅射的影响,照相机镜头用有机玻璃罩子罩住,镜头与工件表面之间设计了挡屑板,透过板上的小孔可对刀具和工件表面摄影(采用高温红外胶卷)。
测量温度前,首先用热电偶进行定标校准,即热电偶由电加热并在不同温度下照相,所需曝光时间通过预试验确定,显影后的胶卷用显微光密度计读数,得到高温红外胶卷在不同曝光时间下光密度与温度的对应关系。
根据此对应关系,可以确定切削过程中工件或刀具的温度。
用红外照相法测定的切削温度可用于研究切削温度的分布情况。
图6 红外照相法测温装置示意图(3)红外热像仪法红外热像仪[11]的基本工作原理是利用了斯蒂芬—波尔兹曼定律,即E =εσT4(2)式中 E ———物体辐射单元单位面积的辐射能量(W/m 2)ε———物体辐射单元表面辐射率(取决于物体表面性质)σ———斯蒂芬—波尔兹曼常数(σ=5176×10-8W/m 2・K 4)T ———物体辐射单元的表面温度(K )切削时,红外热像仪通过光机扫描机构探测工件(或刀具)表面辐射单元的辐射能量,并将每个辐射单元的辐射能量转换为电子视频信号,通过对信号进行处理,以可见图像的形式进行显示,显示的热像图代表被测表面的二维辐射能量场,若辐射单元的表面辐射率已知,则可通过斯蒂芬—波尔兹曼定律求出辐射单元表面的温度分布场及动态变化。
虽然红外热像仪所测温度为相对温度,滞后于实际切削温度,但根据传热反求算法可准确求得切削过程中工件(或刀具)的温度变化规律及动态分布。
红外热像仪测温法具有直观、简便、可远距离非接触监测等优点,在恶劣环境下测量物体表面温度时具有较大优越性。
此外,测量切削温度的光、热辐射方法还有红外干板法、红外聚光法、PbS 光能电池法[1,3]、高速切削双色高温计测量法[12]等。
2.3 金相结构法(1)金相结构法金相结构法[2]是基于金属材料在高温下会发生相应的金相结构变化这一原理进行测温的。
该方法通过观察刀具或工件切削前后金相组织的变化来判定切削温度的变化,主要适用于高速钢刀具,因为当温度超过600℃时,高速钢的红硬性下降,组织结构发生一系列变化,可通过经抛光、腐蚀后的金相磨片来检查其金相组织变化。
但这种方法的应用范围局限于金属材料制成的刀具,并且只有在高温下才能观察到材料明显的组织结构变化;此外,观测和分析的工作量也较大。
(2)扫描电镜法扫描电镜法测量切削温度是用扫描电镜观测刀具预定剖面显微组织的变化,并与标准试样对照,从而确定刀具切削过程中所达到的温度值。
应用扫描电镜法首先需要制取样件和对照样件,考虑到在不同温度和不同保温时间条件下材料的显微组织不同,对照样件需要多制取一些;得到对照样件的显微组织照片后即可确定被测刀具某一部位的切削温度。
扫描电镜法测定切削温度的分辨率和确定温度分布的准确性均很高。
但扫描电镜法也存在以下缺点:①只能测量600℃以上的温度;②样件制作相当繁琐;③属事后破坏性测量,不便于在生产现场推广应用;④所确定的切削温度分布状态属于定量分析;⑤设备复杂,技术难度高,实际应用受到一定限制。