中英文翻译机器人
Robots机器人 中英文翻译
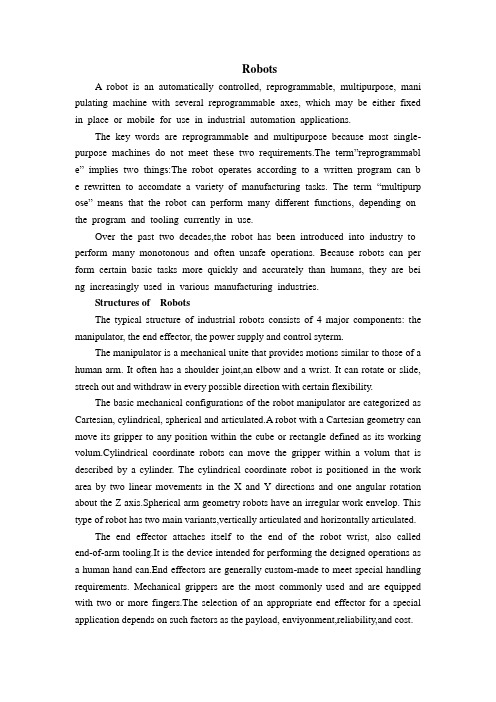
RobotsA robot is an automatically controlled, reprogrammable, multipurpose, mani pulating machine with several reprogrammable axes, which may be either fixed in place or mobile for use in industrial automation applications.The key words are reprogrammable and multipurpose because most single-purpose machines do not meet these two requirements.The term”reprogrammabl e” implies two things:The robot operates according to a written program can b e rewritten to accomdate a variety of manufacturing tasks. The term “multipurp ose” means that the robot can perform many different functions, depending on the program and tooling currently in use.Over the past two decades,the robot has been introduced into industry to perform many monotonous and often unsafe operations. Because robots can per form certain basic tasks more quickly and accurately than humans, they are bei ng increasingly used in various manufacturing industries.Structures of RobotsThe typical structure of industrial robots consists of 4 major components: the manipulator, the end effector, the power supply and control syterm.The manipulator is a mechanical unite that provides motions similar to those of a human arm. It often has a shoulder joint,an elbow and a wrist. It can rotate or slide, strech out and withdraw in every possible direction with certain flexibility.The basic mechanical configurations of the robot manipulator are categorized as Cartesian, cylindrical, spherical and articulated.A robot with a Cartesian geometry can move its gripper to any position within the cube or rectangle defined as its working volum.Cylindrical coordinate robots can move the gripper within a volum that is described by a cylinder. The cylindrical coordinate robot is positioned in the work area by two linear movements in the X and Y directions and one angular rotation about the Z axis.Spherical arm geometry robots have an irregular work envelop. This type of robot has two main variants,vertically articulated and horizontally articulated.The end effector attaches itself to the end of the robot wrist, also called end-of-arm tooling.It is the device intended for performing the designed operations as a human hand can.End effectors are generally custom-made to meet special handling requirements. Mechanical grippers are the most commonly used and are equipped with two or more fingers.The selection of an appropriate end effector for a special application depends on such factors as the payload, enviyonment,reliability,and cost.The power supply is the actuator for moving the robot arm, controlling the joints and operating the end effector. The basic type of power sources include electrical,pneumatic, and hydraulic. Each source of energy and each type of motor has its own characteristics, advantages and limitations. An ac-powered motor or dc-powered motor may be used depending on the system design and applications. These motors convert electrical energy into mechanical energy to power the robot.Most new robots use electrical power supply. Pneumatic actuators have been used for high speed. Nonservo robots and are often used for powering tooling such as grippers. Hydraulic actuators have been used for heavier lift systems, typically where accuracy was not also requied.The contro system is the communications and information-processing system that gives commands for the movements of the robot. It is the brain of the robot; it sends signals to the power source to move the robot arm to a specific position and to the end effector.It is also the nerves of the robot; it is reprogrammable to send out sequences of instructions for all movements and actions to be taken by the robot.A open-loop controller is the simplest for of the control system, which controls the robot only by foolowing the predetermined step-by-step instructions.This system dose not have a self-correcting capability.A close-loop control system use feedback sensors to produce signals that reflct the current states of the controed objects. By comparing those feedback signals with the values set by the programmer, the close-loop controller can conduct the robot to move to the precise position and assume the desired attitude, and the end effector can perform with very high accuracy as the close-loop control system can minimize the discrepancy between the controlled object and the predetermined references.Classification of RobotIndustrial robots vary widely in size,shape, number of axes,degrees of freedom, and design configuration. Each factor influence the dimensions of the robot’s working envelop or the volume of space within which it can move and perform its designated task. A broader classification of robots can been described as below.Fixed-and Variable-Sequence Robots. The fixed-sequence robot (also called a pick-and place robot) is programmed for a specific sequence of operations. Its movements are form point to point, and the cycle is repeated continuously.The variable-sequence robot can be programmed for a specific sequence of operations but can be programmed to perform another sequence of operation.Playback Robot. An operator leads or walks the playback robot and its end effector through the desired path. The robot memorizes and records the path and sequence of motions and can repeat them continually without any further action or guidance by the operator.Numerically Controlled Robot. The numerically controlled robot is programmed and operated much like a numerically controlled machine. The robot is servocontrolled by digital data, and its sequence of movements can be changed with relative ease.Intelligent Robot. The intelligent robot is capable of performing some of the functions and tasks carried out by huanbeings.It is equipped with a variety of sensors with visual and tactile capabilities.Robot ApplicationsThe robot is a very special type of productin tool; as a result, the applications in which robots are used are quite broad. These applications can be grouped into three categories: material processing, material handling and assembly.In material processing, robots use tools to process the raw material. For example, the robot tools could include a drill and the robot would be able to perfor drilling operaytions on raw material.Material handling consists of the loading, unloading, and transferring of workpieces in manufacturing facilities. These operations can be performed relatively and repeatedly with robots, thereby improving quality and scrap losses.Assembly is another large application area for using robotics. An automatic assembly system can incorporate automatic testing, robot automation and mechanical handling for reducing labor costs, increasing output and eliminating manual handling concers.机器人机器人是一种自动控制的、可重复编程的、多功能的、由几个可重复编程的坐标系来操纵机器的装置,它可以被固定在某地,还可以是移动的以在工业自动化工厂中使用。
机器人技术发展中英文对照外文翻译文献
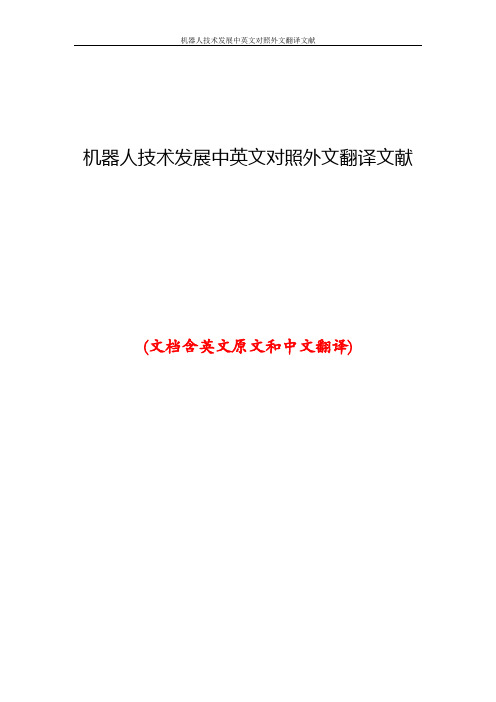
机器人技术发展中英文对照外文翻译文献(文档含英文原文和中文翻译)外文资料:RobotsFirst, I explain the background robots, robot technology development. It should be said it is a common scientific and technological development of a comprehensive results, for the socio-economic development of a significant impact on a science and technology. It attributed the development of all countries in the Second World War to strengthen the economic input on strengthening the country's economic development. But they also demand the development of the productive forces the inevitable result of human development itself is the inevitable result then with the development of humanity, people constantly discuss the natural process, in understanding and reconstructing the natural process, people need to be able to liberate a slave. So this is the slave people to be able to replace the complex and engaged in heavy manual labor, People do not realize right up to the world's understanding and transformation of this technology as well as people in the development process of an objective need.Robots are three stages of development, in other words, we are accustomed to regarding robots are divided into three categories. is a first-generation robots, also known as teach-type robot, it is through a computer, to control over one of a mechanical degrees of freedom Through teaching and information stored procedures, working hours to read out information, and then issued a directive so the robot can repeat according to the people at that time said the results show this kind of movement again, For example, the car spot welding robots, only to put this spot welding process, after teaching, and it is always a repeat of a work It has the external environment is no perception that the force manipulation of the size of the work piece there does not exist, welding 0S It does not know, then this fact from the first generation robot, it will exist this shortcoming, it in the 20th century, the late 1970s, people started to study the second-generation robot, called Robot with the feeling that This feeling with the robot is similar in function of a certain feeling, for instance, force and touch, slipping, visual, hearing and who is analogous to that with all kinds of feelings, say in a robot grasping objects, In fact, it can be the size of feeling out, it can through visual, to be able to feel and identify its shape, size, color Grasping an egg, it adopted a acumen, aware of its power and the size of the slide.Third-generation robots, we were a robotics ideal pursued by the most advanced stage, called intelligent robots, So long as tell it what to do, not how to tell it to do, it will be able to complete the campaign, thinking and perception of this man-machine communication function and function Well, this current development or relative is in a smart part of the concept and meaning But the real significance of the integrity of this intelligent robot did not actually exist, but as we continued the development of science and technology, the concept of intelligent increasingly rich, it grows ever wider connotations.Now I have a brief account of China's robot development of the basic profiles. As our country there are many other factors that problem. Our country in robotics research of the 20th century the late 1970s. At that time, we organized at the national, a Japanese industrial automation products exhibition. In this meeting, there are two products, is a CNC machine tools, an industrial robot, this time, our country's many scholars see such a direction, has begun to make a robot research But this time, are basically confined to the theory of phase .Then the real robot research, in 7500 August 5, 1995, 15 nearly 20 years of development, The most rapid development, in 1986 we established a national plan of 863 high-technology development plan, As robot technology will be an important theme of the development of The state has invested nearly Jiganyi funds begun to make a robot, We made the robot in the field quickly and rapid development.At present, units like the CAS ShenYng Institute of Automation, the original machinery, automation of the Ministry, as of Harbin Industrial University, Beijing University of Aeronautics and Astronautics, Qinghua University, Chinese Academy of Sciences, also includes automation of some units, and so on have done a very important study, also made a lot of achievements Meanwhile, in recent years, we end up in college, a lot of flats in robot research, Many graduate students and doctoral candidates are engaged in robotics research, we are more representative national study Industrial robots, underwater robots, space robots, robots in the nuclear industry are on the international level should be taking the lead .On the whole of our country Compared with developed countries, there is still a big gap, primarily manifested in the We in the robot industry, at present there is no fixed maturity product, but in theseunderwater, space, the nuclear industry, a number of special robots, we have made a lot of achievements characteristics.Now, I would like to briefly outline some of the industrial robot situation. So far, the industrial robot is the most mature and widely used category of a robot, now the world's total sales of 1.1 million Taiwan, which is the 1999 statistics, however, 1.1 million in Taiwan have been using the equipment is 75 million, this volume is not small. Overall, the Japanese industrial robots in this one, is the first of the robots to become the Kingdom, the United States have developed rapidly. Newly installed in several areas of Taiwan, which already exceeds Japan, China has only just begun to enter the stage of industrialization, has developed a variety of industrial robot prototype and small batch has been used in production.Spot welding robot is the auto production line, improve production efficiency and raise the quality of welding car, reduce the labor intensity of a robot. It is characterized by two pairs of robots for spot welding of steel plate, bearing a great need for the welding tongs, general in dozens of kilograms or more, then its speed in meters per second a 5-2 meter of such high-speed movement. So it is generally five to six degrees of freedom, load 30 to 120 kilograms, the great space, probably expected that the work of a spherical space, a high velocity, the concept of freedom, that is to say, Movement is relatively independent of the number of components, the equivalent of our body, waist is a rotary degree of freedom We have to be able to hold his arm, Arm can be bent, then this three degrees of freedom, Meanwhile there is a wrist posture adjustment to the use of the three autonomy, the general robot has six degrees of freedom. We will be able to space the three locations, three postures, the robot fully achieved, and of course we have less than six degrees of freedom. Have more than six degrees of freedom robot, in different occasions the need to configure.The second category of service robots, with the development of industrialization, especially in the past decade, Robot development in the areas of application are continuously expanding, and now a very important characteristic, as we all know, Robot has gradually shifted from manufacturing to non-manufacturing and service industries, we are talking about the car manufacturer belonging to the manufacturing industry, However, the services sector including cleaning, refueling, rescue, rescue,relief, etc. These belong to the non-manufacturing industries and service industries, so here is compared with the industrial robot, it is a very important difference. It is primarily a mobile platform, it can move to sports, there are some arms operate, also installed some as a force sensor and visual sensors, ultrasonic ranging sensors, etc. It’s surrounding environment for the conduct of identification, to determine its campaign t o complete some work, this is service robot’s one of the basic characteristics.For example, domestic robot is mainly embodied in the example of some of the carpets and flooring it to the regular cleaning and vacuuming. The robot it is very meaningful, it has sensors, it can furniture and people can identify, It automatically according to a law put to the ground under the road all cleaned up. This is also the home of some robot performance.The medical robots, nearly five years of relatively rapid development of new application areas. If people in the course of an operation, doctors surgery, is a fatigue, and the other manually operated accuracy is limited. Some universities in Germany, which, facing the spine, lumbar disc disease, the identification, can automatically use the robot-aided positioning, operation and surgery Like the United States have been more than 1,000 cases of human eyeball robot surgery, the robot, also including remote-controlled approach, the right of such gastrointestinal surgery, we see on the television inside. a manipulator, about the thickness fingers such a manipulator, inserted through the abdominal viscera, people on the screen operating the machines hand, it also used the method of laser lesion laser treatment, this is the case, people would not have a very big damage to the human body.In reality, this right as a human liberation is a very good robots, medical robots it is very complex, while it is fully automated to complete all the work, there are difficulties, and generally are people to participate. This is America, the development of such a surgery Lin Bai an example, through the screen, through a remote control operator to control another manipulator, through the realization of the right abdominal surgery A few years ago our country the exhibition, the United States has been successful in achieving the right to the heart valve surgery and bypass surgery. This robot has in the area, caused a great sensation, but also, AESOP's surgical robot, In fact, it through some equipment to some of the lesions inspections, through amanipulator can be achieved on some parts of the operation Also including remotely operated manipulator, and many doctors are able to participate in the robot under surgery Robot doctor to include doctors with pliers, tweezers or a knife to replace the nurses, while lighting automatically to the doctor's movements linked, the doctor hands off, lighting went off, This is very good, a doctor's assistant.We regard this country excel, it should be said that the United States, Russia and France, in our nation, also to the international forefront, which is the CAS ShenYang Institute of Automation of developing successful, 6,000 meters underwater without cable autonomous underwater robot, the robot to 6,000 meters underwater, can be conducted without cable operations. His is 2000, has been obtained in our country one of the top ten scientific and technological achievements. This indicates that our country in this underwater robot, have reached the advanced international level, 863 in the current plan, the development of 7,000 meters underwater in a manned submersible to the ocean further development and operation, This is a great vote of financial and material resources.In this space robotics research has also been a lot of development. In Europe, including 16 in the United States space program, and the future of this space capsule such a scheme, One thing is for space robots, its main significance lies in the development of the universe and the benefit of mankind and the creation of new human homes, Its main function is to scientific investigation, as production and space scientific experiments, satellites and space vehicles maintenance and repair, and the construction of the space assembly. These applications, indeed necessary, for example, scientific investigation, as if to mock the ground some physical and chemical experiments do not necessarily have people sitting in the edge of space, because the space crew survival in the day the cost is nearly one million dollars. But also very dangerous, in fact, some action is very simple, through the ground, via satellite control robot, and some regularly scheduled completion of the action is actually very simple. Include the capsule as control experiments, some switches, buttons, simple flange repair maintenance, Robot can be used to be performed by robots because of a solar battery, then the robot will be able to survive, we will be able to work, We have just passed the last robot development on the application of the different areas ofapplication, and have seen the robots in industry, medical, underwater, space, mining, construction, service, entertainment and military aspects of the application .Also really see that the application is driven by the development of key technologies, a lack of demand, the robot can not, It is because people in understanding the natural transformation of the natural process, the needs of a wide range of robots, So this will promote the development of key technologies, the robot itself for the development of From another aspect, as key technology solutions, as well as the needs of the application, on the promotion of the robot itself a theme for the development of intelligent, and from teaching reappearance development of the current local perception of the second-generation robot, the ultimate goal, continuously with other disciplines and the development of advanced technology, the robot has become rich, eventually achieve such an intelligent robot mainstream.Robot is mankind's right-hand man; friendly coexistence can be a reliable friend. In future, we will see and there will be a robot space inside, as a mutual aide and friend. Robots will create the jobs issue. We believe that there would not be a "robot appointment of workers being laid off" situation, because people with the development of society, In fact the people from the heavy physical and dangerous environment liberated, so that people have a better position to work, to create a better spiritual wealth and cultural wealth.译文:机器人首先我介绍一下机器人产生的背景,机器人技术的发展,它应该说是一个科学技术发展共同的一个综合性的结果,同时,为社会经济发展产生了一个重大影响的一门科学技术,它的发展归功于在第二次世界大战中各国加强了经济的投入,就加强了本国的经济的发展。
Robots机器人 中英文翻译
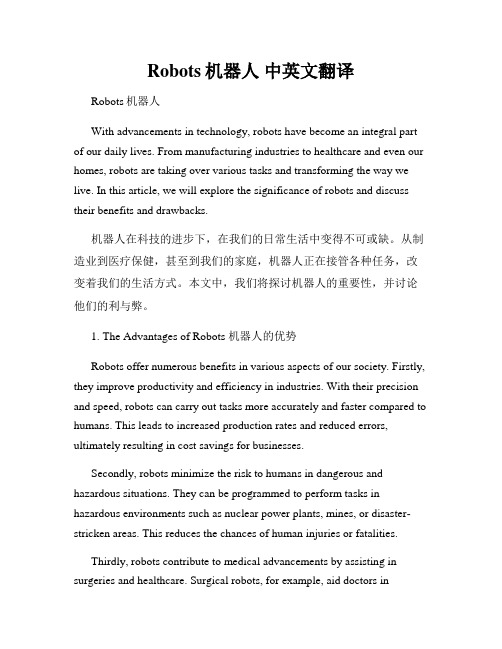
Robots机器人中英文翻译Robots机器人With advancements in technology, robots have become an integral part of our daily lives. From manufacturing industries to healthcare and even our homes, robots are taking over various tasks and transforming the way we live. In this article, we will explore the significance of robots and discuss their benefits and drawbacks.机器人在科技的进步下,在我们的日常生活中变得不可或缺。
从制造业到医疗保健,甚至到我们的家庭,机器人正在接管各种任务,改变着我们的生活方式。
本文中,我们将探讨机器人的重要性,并讨论他们的利与弊。
1. The Advantages of Robots 机器人的优势Robots offer numerous benefits in various aspects of our society. Firstly, they improve productivity and efficiency in industries. With their precision and speed, robots can carry out tasks more accurately and faster compared to humans. This leads to increased production rates and reduced errors, ultimately resulting in cost savings for businesses.Secondly, robots minimize the risk to humans in dangerous and hazardous situations. They can be programmed to perform tasks in hazardous environments such as nuclear power plants, mines, or disaster-stricken areas. This reduces the chances of human injuries or fatalities.Thirdly, robots contribute to medical advancements by assisting in surgeries and healthcare. Surgical robots, for example, aid doctors inperforming intricate procedures with enhanced precision and control. Furthermore, robots can also assist with patient care, such as providing support to the elderly or individuals with disabilities.机器人在我们社会的各个方面都提供了众多的优势。
机器人的作文英文版带翻译

机器人的作文英文版带翻译Title: The Role of Robots in Modern Society。
With the rapid advancement of technology, robots have become an increasingly integral part of modern society. From manufacturing industries to household chores, robots are revolutionizing the way we live and work. In this essay, we will explore the various roles that robots play in our society and discuss their impact on different aspects ofour lives.One of the primary roles of robots is in the manufacturing industry. With their precision and efficiency, robots have significantly increased productivity in factories. They can perform repetitive tasks withconsistent accuracy, leading to higher quality products and reduced production costs. This not only benefits manufacturers but also consumers who get access to better products at lower prices.In addition to manufacturing, robots are also making strides in the field of healthcare. Surgical robots, for example, are being used in hospitals to perform minimally invasive procedures with greater precision than human surgeons. This results in shorter recovery times and reduced risk of complications for patients. Furthermore, robots are being developed to assist elderly and disabled individuals with everyday tasks, enabling them to live more independently.Furthermore, robots are playing a crucial role in disaster response and exploration. In situations where it's too dangerous for humans to intervene, robots can be deployed to search for survivors or assess the extent of damage. For instance, unmanned aerial vehicles (UAVs) equipped with cameras and sensors can provide valuable information to emergency responders during natural disasters or humanitarian crises.Moreover, robots are increasingly being used in agriculture to improve efficiency and sustainability. Autonomous tractors and drones equipped with advancedimaging technology can help farmers monitor crop health, optimize irrigation, and apply fertilizers with precision. This not only increases yields but also reduces the environmental impact of farming practices.Despite their numerous benefits, the widespreadadoption of robots also raises concerns about job displacement and ethical implications. As robots becomemore capable of performing tasks traditionally done by humans, there is a fear that they will replace human workers, leading to unemployment and economic inequality. Additionally, questions arise regarding the ethical use of robots, particularly in areas like warfare and surveillance.However, it's essential to recognize that robots can complement human labor rather than replace it entirely. By automating repetitive and dangerous tasks, robots free up humans to focus on more creative and complex endeavors. Furthermore, as technology advances, new job opportunities emerge in the design, maintenance, and programming of robots.In conclusion, robots play a multifaceted role in modern society, from revolutionizing manufacturing and healthcare to aiding in disaster response and agriculture. While their widespread adoption raises legitimate concerns, the benefits they offer in terms of efficiency, productivity, and safety cannot be overlooked. It's crucial to strike a balance between harnessing the potential of robots and addressing the societal challenges they pose to ensure a future where humans and robots coexist harmoniously.标题,机器人在现代社会中的角色。
机器人外文文献翻译、中英文翻译
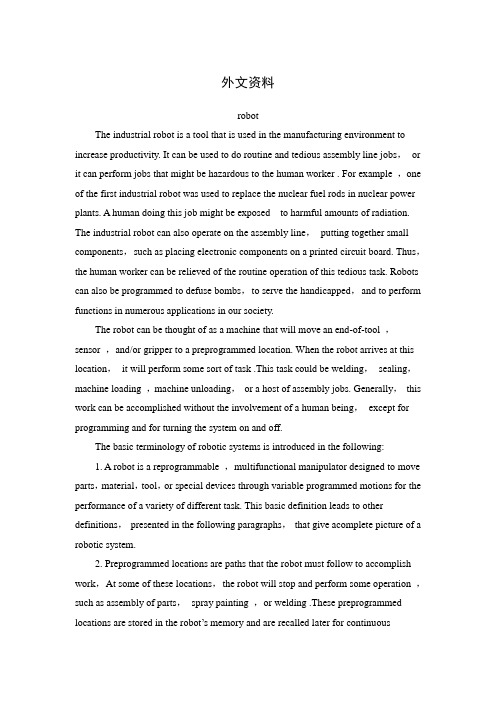
外文资料robotThe industrial robot is a tool that is used in the manufacturing environment to increase productivity. It can be used to do routine and tedious assembly line jobs,or it can perform jobs that might be hazardous to the human worker . For example ,one of the first industrial robot was used to replace the nuclear fuel rods in nuclear power plants. A human doing this job might be exposed to harmful amounts of radiation. The industrial robot can also operate on the assembly line,putting together small components,such as placing electronic components on a printed circuit board. Thus,the human worker can be relieved of the routine operation of this tedious task. Robots can also be programmed to defuse bombs,to serve the handicapped,and to perform functions in numerous applications in our society.The robot can be thought of as a machine that will move an end-of-tool ,sensor ,and/or gripper to a preprogrammed location. When the robot arrives at this location,it will perform some sort of task .This task could be welding,sealing,machine loading ,machine unloading,or a host of assembly jobs. Generally,this work can be accomplished without the involvement of a human being,except for programming and for turning the system on and off.The basic terminology of robotic systems is introduced in the following:1. A robot is a reprogrammable ,multifunctional manipulator designed to move parts,material,tool,or special devices through variable programmed motions for the performance of a variety of different task. This basic definition leads to other definitions,presented in the following paragraphs,that give acomplete picture of a robotic system.2. Preprogrammed locations are paths that the robot must follow to accomplish work,At some of these locations,the robot will stop and perform some operation ,such as assembly of parts,spray painting ,or welding .These preprogrammed locations are stored in the robot’s memory and are recalled later for continuousoperation.Furthermore,these preprogrammed locations,as well as other program data,can be changed later as the work requirements change.Thus,with regard to this programming feature,an industrial robot is very much like a computer ,where data can be stoned and later recalled and edited.3. The manipulator is the arm of the robot .It allows the robot to bend,reach,and twist.This movement is provided by the manipulator’s axes,also called the degrees of freedom of the robot .A robot can have from 3 to 16 axes.The term degrees of freedom will always relate to the number of axes found on a robot.4. The tooling and frippers are not part the robotic system itself;rather,they are attachments that fit on the end of the robot’s arm. These attachments connected to the end of the robot’s arm allow the robot to lift parts,spot-weld ,paint,arc-weld,drill,deburr,and do a variety of tasks,depending on what is required of the robot.5. The robotic system can control the work cell of the operating robot.The work cell of the robot is the total environment in which the robot must perform itstask.Included within this cell may be the controller ,the robot manipulator ,a work table ,safety features,or a conveyor.All the equipment that is required in order for the robot to do its job is included in the work cell .In addition,signals from outside devices can communicate with the robot to tell the robot when it should parts,pick up parts,or unload parts to a conveyor.The robotic system has three basic components: the manipulator,the controller,and the power source.A.ManipulatorThe manipulator ,which does the physical work of the robotic system,consists of two sections:the mechanical section and the attached appendage.The manipulator also has a base to which the appendages are attached.Fig.1 illustrates the connectionof the base and the appendage of a robot.图1.Basic components of a robot’s manipulatorThe base of the manipulator is usually fixed to the floor of the work area. Sometimes,though,the base may be movable. In this case,the base is attached to either a rail or a track,allowing the manipulator to be moved from one location to anther.As mentioned previously ,the appendage extends from the base of the robot. The appendage is the arm of the robot. It can be either a straight ,movable arm or a jointed arm. The jointed arm is also known as an articulated arm.The appendages of the robot manipulator give the manipulator its various axes of motion. These axes are attached to a fixed base ,which,in turn,is secured to a mounting. This mounting ensures that the manipulator will in one location.At the end of the arm ,a wrist(see Fig 2)is connected. The wrist is made up of additional axes and a wrist flange. The wrist flange allows the robot user to connect different tooling to the wrist for different jobs.图2.Elements of a work cell from the topThe manipulator’s axes allow it to perform work within a certain area. The area is called the work cell of the robot ,and its size corresponds to the size of the manipulator.(Fid2)illustrates the work cell of a typical assembly ro bot.As the robot’s physical size increases,the size of the work cell must also increase.The movement of the manipulator is controlled by actuator,or drive systems.The actuator,or drive systems,allows the various axes to move within the work cell. The drive system can use electric,hydraulic,or pneumatic power.The energy developed by the drive system is converted to mechanical power by various mechanical power systems.The drive systems are coupled through mechanical linkages.These linkages,in turn,drive the different axes of the robot.The mechanical linkages may be composed of chain,gear,and ball screws.B.ControllerThe controller in the robotic system is the heart of the operation .The controller stores preprogrammed information for later recall,controls peripheral devices,and communicates with computers within the plant for constant updates in production.The controller is used to control the robot manipulator’s movements as well as to control peripheral components within the work cell. The user can program the movements of the manipulator into the controller through the use of a hard-held teach pendant.This information is stored in the memory of the controller for later recall.The controller stores all program data for the robotic system.It can store several differentprograms,and any of these programs can be edited.The controller is also required to communicate with peripheral equipment within the work cell. For example,the controller has an input line that identifies when a machining operation is completed.When the machine cycle is completed,the input line turn on telling the controller to position the manipulator so that it can pick up the finished part.Then ,a new part is picked up by the manipulator and placed into the machine.Next,the controller signals the machine to start operation.The controller can be made from mechanically operated drums that step through a sequence of events.This type of controller operates with a very simple robotic system.The controllers found on the majority of robotic systems are more complex devices and represent state-of-the-art eletronoics.That is,they are microprocessor-operated.these microprocessors are either 8-bit,16-bit,or 32-bit processors.this power allows the controller to be very flexible in its operation.The controller can send electric signals over communication lines that allow it to talk with the various axes of the manipulator. This two-way communication between the robot manipulator and the controller maintains a constant update of the end the operation of the system.The controller also controls any tooling placed on the end of the robot’s wrist.The controller also has the job of communicating with the different plant computers. The communication link establishes the robot as part a computer-assisted manufacturing (CAM)system.As the basic definition stated,the robot is a reprogrammable,multifunctional manipulator.Therefore,the controller must contain some of memory stage. The microprocessor-based systems operates in conjunction with solid-state devices.These memory devices may be magnetic bubbles,random-access memory,floppy disks,or magnetic tape.Each memory storage device stores program information fir or for editing.C.power supplyThe power supply is the unit that supplies power to the controller and the manipulator. The type of power are delivered to the robotic system. One type of power is the AC power for operation of the controller. The other type of power isused for driving the various axes of the manipulator. For example,if the robot manipulator is controlled by hydraulic or pneumatic drives,control signals are sent to these devices causing motion of the robot.For each robotic system,power is required to operate the manipulator .This power can be developed from either a hydraulic power source,a pneumatic power source,or an electric power source.There power sources are part of the total components of the robotic work cell.中文翻译机器人工业机器人是在生产环境中用以提高生产效率的工具,它能做常规乏味的装配线工作,或能做那些对于工人来说是危险的工作,例如,第一代工业机器人是用来在核电站中更换核燃料棒,如果人去做这项工作,将会遭受有害放射线的辐射。
机器人文言文翻译

夫机器人之源,始于西方。
彼时,工匠制器,精妙绝伦,巧夺天工。
其中,有制人形之器,能行能言,虽不能如人,然亦颇得人心。
此器之初,不过用以助人劳作,如耕田、织布、烧陶等。
然随着时间的推移,工匠们逐渐发现,此器之能,远不止于此。
于是,机器人之制,日新月异。
有者,能行走如飞,有者,能言善辩,有者,能洞察人心,有者,能治国理政。
种种奇能,令人瞠目结舌。
乃至有机器人之王,统治一国,使国势强盛,百姓安居乐业。
然而,机器人之兴,亦带来诸多争议。
有人言,机器人之制,夺人之工,使天下失业。
有人言,机器人之能,胜过人力,将导致人不如器。
更有甚者,言机器人之心,不可测度,恐有反叛之日。
于是,世人纷纷研究机器人之道。
有者,欲以机器人之力,造福人类;有者,欲以机器人之智,制服机器;更有者,欲以机器人之心,探求真理。
在我国,机器人之制,亦逐渐兴起。
有者,制出人形机器,能行能言,如诸葛亮之木牛流马;有者,制出机械战车,威震四方,如赵匡胤之虎翼车;更有者,制出火药机器,攻城掠地,如李善长之火龙炮。
然而,机器人之制,亦非一帆风顺。
有者,因机器人之事,丧命丧家;有者,因机器人之争,国破家亡。
然世人皆知,机器人之制,实为人类文明之进步。
若能善用机器人之力,必将造福后世。
今日,机器人之制,已臻巅峰。
有者,能飞行如鹰,有者,能潜行如鱼,有者,能感知千里之外,有者,能穿越时空。
种种奇能,令人叹为观止。
然机器人之道,亦非止于此。
未来,机器人之制,必将更加精妙。
有人言,机器人之心,将融入人类之心;有人言,机器人之力,将超越人力。
届时,人类与机器人之界限,将愈发模糊。
总之,机器人之事,实为人类文明之瑰宝。
吾辈当以敬畏之心,对待机器人之制。
使其为人类造福,而非祸害。
如此,方不负机器人之名,不负人类之望。
(注:本文以文言文形式翻译机器人文,其中部分内容为虚构,仅供参考。
)。
机器人外文翻译外文翻译、中英文翻译、外文文献翻译

外文翻译机器人The robot性质: □毕业设计□毕业论文教学院:机电工程学院系别:机械设计制造及其自动化学生学号:学生姓名:专业班级:指导教师:职称:起止日期:机器人1.机器人的作用机器人是高级整合控制论、机械电子、计算机、材料和仿生学的产物。
在工业、医学、农业、建筑业甚至军事等领域中均有重要用途。
现在,国际上对机器人的概念已经逐渐趋近一致。
一般说来,人们都可以接受这种说法,即机器人是靠自身动力和控制能力来实现各种功能的一种机器。
联合国标准化组织采纳了美国机器人协会给机器人下的定义:“一种可编程和多功能的,用来搬运材料、零件、工具的操作机;或是为了执行不同的任务而具有可改变和可编程动作的专门系统。
2.能力评价标准机器人能力的评价标准包括:智能,指感觉和感知,包括记忆、运算、比较、鉴别、判断、决策、学习和逻辑推理等;机能,指变通性、通用性或空间占有性等;物理能,指力、速度、连续运行能力、可靠性、联用性、寿命等。
因此,可以说机器人是具有生物功能的三维空间坐标机器。
3.机器人的组成机器人一般由执行机构、驱动装置、检测装置和控制系统等组成。
执行机构即机器人本体,其臂部一般采用空间开链连杆机构,其中的运动副(转动副或移动副)常称为关节,关节个数通常即为机器人的自由度数。
根据关节配置型式和运动坐标形式的不同,机器人执行机构可分为直角坐标式、圆柱坐标式、极坐标式和关节坐标式等类型。
出于拟人化的考虑,常将机器人本体的有关部位分别称为基座、腰部、臂部、腕部、手部(夹持器或末端执行器)和行走部(对于移动机器人)等。
驱动装置是驱使执行机构运动的机构,按照控制系统发出的指令信号,借助于动力元件使机器人进行动作。
它输入的是电信号,输出的是线、角位移量。
机器人使用的驱动装置主要是电力驱动装置,如步进电机、伺服电机等,此外也有采用液压、气动等驱动装置。
检测装置的作用是实时检测机器人的运动及工作情况,根据需要反馈给控制系统,与设定信息进行比较后,对执行机构进行调整,以保证机器人的动作符合预定的要求。
Robots机器人 中英文翻译
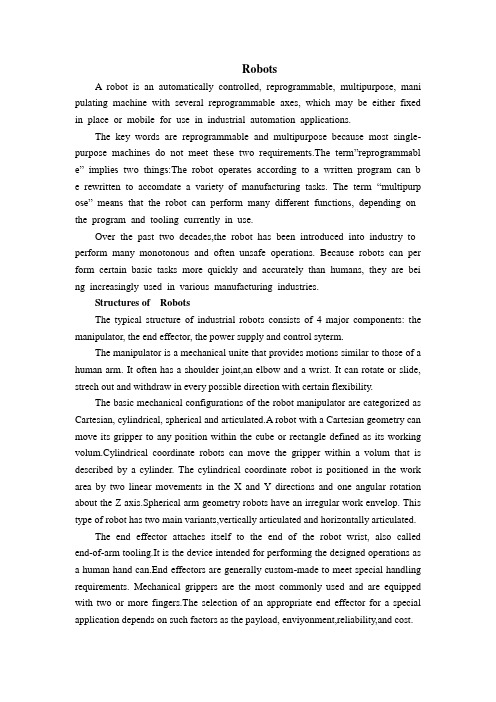
RobotsA robot is an automatically controlled, reprogrammable, multipurpose, mani pulating machine with several reprogrammable axes, which may be either fixed in place or mobile for use in industrial automation applications.The key words are reprogrammable and multipurpose because most single-purpose machines do not meet these two requirements.The term”reprogrammabl e” implies two things:The robot operates according to a written program can b e rewritten to accomdate a variety of manufacturing tasks. The term “multipurp ose” means that the robot can perform many different functions, depending on the program and tooling currently in use.Over the past two decades,the robot has been introduced into industry to perform many monotonous and often unsafe operations. Because robots can per form certain basic tasks more quickly and accurately than humans, they are bei ng increasingly used in various manufacturing industries.Structures of RobotsThe typical structure of industrial robots consists of 4 major components: the manipulator, the end effector, the power supply and control syterm.The manipulator is a mechanical unite that provides motions similar to those of a human arm. It often has a shoulder joint,an elbow and a wrist. It can rotate or slide, strech out and withdraw in every possible direction with certain flexibility.The basic mechanical configurations of the robot manipulator are categorized as Cartesian, cylindrical, spherical and articulated.A robot with a Cartesian geometry can move its gripper to any position within the cube or rectangle defined as its working volum.Cylindrical coordinate robots can move the gripper within a volum that is described by a cylinder. The cylindrical coordinate robot is positioned in the work area by two linear movements in the X and Y directions and one angular rotation about the Z axis.Spherical arm geometry robots have an irregular work envelop. This type of robot has two main variants,vertically articulated and horizontally articulated.The end effector attaches itself to the end of the robot wrist, also called end-of-arm tooling.It is the device intended for performing the designed operations as a human hand can.End effectors are generally custom-made to meet special handling requirements. Mechanical grippers are the most commonly used and are equipped with two or more fingers.The selection of an appropriate end effector for a special application depends on such factors as the payload, enviyonment,reliability,and cost.The power supply is the actuator for moving the robot arm, controlling the joints and operating the end effector. The basic type of power sources include electrical,pneumatic, and hydraulic. Each source of energy and each type of motor has its own characteristics, advantages and limitations. An ac-powered motor or dc-powered motor may be used depending on the system design and applications. These motors convert electrical energy into mechanical energy to power the robot.Most new robots use electrical power supply. Pneumatic actuators have been used for high speed. Nonservo robots and are often used for powering tooling such as grippers. Hydraulic actuators have been used for heavier lift systems, typically where accuracy was not also requied.The contro system is the communications and information-processing system that gives commands for the movements of the robot. It is the brain of the robot; it sends signals to the power source to move the robot arm to a specific position and to the end effector.It is also the nerves of the robot; it is reprogrammable to send out sequences of instructions for all movements and actions to be taken by the robot.A open-loop controller is the simplest for of the control system, which controls the robot only by foolowing the predetermined step-by-step instructions.This system dose not have a self-correcting capability.A close-loop control system use feedback sensors to produce signals that reflct the current states of the controed objects. By comparing those feedback signals with the values set by the programmer, the close-loop controller can conduct the robot to move to the precise position and assume the desired attitude, and the end effector can perform with very high accuracy as the close-loop control system can minimize the discrepancy between the controlled object and the predetermined references.Classification of RobotIndustrial robots vary widely in size,shape, number of axes,degrees of freedom, and design configuration. Each factor influence the dimensions of the robot’s working envelop or the volume of space within which it can move and perform its designated task. A broader classification of robots can been described as below.Fixed-and Variable-Sequence Robots. The fixed-sequence robot (also called a pick-and place robot) is programmed for a specific sequence of operations. Its movements are form point to point, and the cycle is repeated continuously.The variable-sequence robot can be programmed for a specific sequence of operations but can be programmed to perform another sequence of operation.Playback Robot. An operator leads or walks the playback robot and its end effector through the desired path. The robot memorizes and records the path and sequence of motions and can repeat them continually without any further action or guidance by the operator.Numerically Controlled Robot. The numerically controlled robot is programmed and operated much like a numerically controlled machine. The robot is servocontrolled by digital data, and its sequence of movements can be changed with relative ease.Intelligent Robot. The intelligent robot is capable of performing some of the functions and tasks carried out by huanbeings.It is equipped with a variety of sensors with visual and tactile capabilities.Robot ApplicationsThe robot is a very special type of productin tool; as a result, the applications in which robots are used are quite broad. These applications can be grouped into three categories: material processing, material handling and assembly.In material processing, robots use tools to process the raw material. For example, the robot tools could include a drill and the robot would be able to perfor drilling operaytions on raw material.Material handling consists of the loading, unloading, and transferring of workpieces in manufacturing facilities. These operations can be performed relatively and repeatedly with robots, thereby improving quality and scrap losses.Assembly is another large application area for using robotics. An automatic assembly system can incorporate automatic testing, robot automation and mechanical handling for reducing labor costs, increasing output and eliminating manual handling concers.机器人机器人是一种自动控制的、可重复编程的、多功能的、由几个可重复编程的坐标系来操纵机器的装置,它可以被固定在某地,还可以是移动的以在工业自动化工厂中使用。
- 1、下载文档前请自行甄别文档内容的完整性,平台不提供额外的编辑、内容补充、找答案等附加服务。
- 2、"仅部分预览"的文档,不可在线预览部分如存在完整性等问题,可反馈申请退款(可完整预览的文档不适用该条件!)。
- 3、如文档侵犯您的权益,请联系客服反馈,我们会尽快为您处理(人工客服工作时间:9:00-18:30)。
中英文翻译机器人机器人工业机器人是在生产环境中用以提高生产效率的工具,它能做常规的装配线工作,或能做那些对于工人来说是危险的工作,例如,第一代工业机器人是用来在核电站中更换核燃料棒,如果人去做这项工作,将会遭受有害放射线的辐射。
工业机器人亦能工作在装配线上将小元件装配到一起,如将电子元件安装在电路印刷板,这样,工人就能从这项乏味的常规工作中解放出来。
机器人也能按程序要求用来拆除炸弹,辅助残疾人,在社会的很多应用场合履行职能。
机器人可以认为是将手臂末端的工具、传感器和(或)手爪移到程序指定位置的一种机器。
当机器人到达位置后,他将执行某种任务。
这些任务可以是焊接、密封、机器装料、拆卸以及装配工作。
除了编程以及系统的开停之外,这些工作可以在无人干预下完成。
如下叙述的是机器人系统基本术语:机器人是一个可编程、多功能的机器手,通过给要完成的不同任务编制各种动作,它可以移动零件、材料、工具以及特殊装置。
这个基本定义引导出后续段落的其他定义,从而描绘出一个完整的机器人系统。
预编程位置点是机器人为完成工作而必须跟踪的轨迹。
在某些位置点上机器人将停下来做某写操作,如装配零件、喷涂油漆或焊接。
这些预编程点贮存在机器人的贮存器中,并为后续的连续操作所调用,而且这些预编程点像其他程序数据一样,可在日后随工作需要而变化。
因而,正是这种可编程的特征,一个工业机器人很像一台计算机,数据可在这里储存、后续调用与编辑。
机械手上机器人的手臂,它使机器人能弯曲、延伸、和旋转,提供这些运动的是机器手的轴,亦是所谓的机器人的自由度。
一个机器人能有3—16 轴,自由度一词总是与机器人轴数相关。
工具和手爪不是机器人自身组成部分,但它们安装在机器人手臂末端的附件。
这些连在机器人手臂末端的附件可使机器人抬起工件、点焊、刷漆、电弧焊、钻孔、打毛刺以及根据机器人的要求去做各种各样的工作。
机器人系统还可以控制机器人的工作单元,工作单元是机器人执行任务所处的整体环境,包括控制器、机械手、工作平台、安全保护装置或者传输装置。
所有这些为保证机器人完成自己任务而必需的装置都包括在这一工作单元中。
另外,来自外设的信号与机器人通讯,通知机器人何时装配工件、取工件或放工件到传输装置上。
机器人系统有三个基本部件:机械手、控制器和动力源。
A.机械手机械手做机器人系统中粗重工作,它包括两个部分:机构和附件,机械手也有联接附件基座,图 1 表示了一机器人基座与附件之间的联接情况。
图 1 机械手基座通常在工作区域的地基上,有时基座也可以移动,在这种情况下基座安装在导轨或轨道上,允许机械手从一个位置移动到另外一个位置。
正如前面所提到的那样,附件从机器人基座上延伸出来,附件就是机器人的手臂,它可以是直接型,也可以是轴节型手臂,轴节型手臂也是大家所知的关节型手臂。
机械臂使机械手产生各轴的运动。
这些轴连在一个安装基座上,然后再连到托架上,托架确保机械手停留在某一位置。
在手臂的末端上,连接着手腕(图1),手腕由辅助轴和手腕凸缘组成,手腕是让机器人用户在手腕凸缘上安装不同工具来做不同种工作。
机械手的轴使机械手在某一区域内执行任务,我们将这个区域为机器人的工作单元,该区域的大小与机器手的尺寸相对应,(图2)列举了一个典型装配机器人的工作单元。
随着机器人机械结构尺寸的增加。
工作单元的范围也必须相应增加。
图2 机械手的运动由执行元件或驱动系统来控制。
执行元件或驱动系统允许个轴在工作单元内运动。
驱动系统可用电气、液压和气压动力,驱动系统所产生的动力经机构转变为机械能,驱动系统与机械传动链相匹配。
有链、齿轮和滚珠丝杠组成的机械传动链驱动着机器人的各轴。
B. 控制器机器人控制器是工作单元的核心。
控制器储存着预编程序供调用、控制外设,及与厂内计算进行通讯以满足产品经常更新的需要。
控制器用于控制机器手运动和在工作单元内控制机器人外设。
用户可通过手持的示教盒将机械手运动的程序编入控制器。
这些信息储存在控制器的存储器中以备后续调用,控制器储存了机器人系统的所有编程数据,它能储存几个不同的程序,并且所有这些程序均能编辑。
控制器要求能够在工作单元内外设进行通信。
例如控制器有一个输入端,它能标识某个机加工操作何时完成。
当该加工循环完成后,输入端接通,告诉控制器定位机械手以便能抓取已加工工件,随后,机械手抓取一未加工件,将其放置在机床上。
接着,控制器给机床发出开始加工的信号。
控制器可以由根据事件顺序而步进的机械式轮鼓组成,这种类型的控制器可用在非常简单的机械系统中。
用于大多数人系统中的控制器代表现代电子学的水平,是更复杂的装置,即它们是由微处理器操纵的。
这些微处理器可以是8 位,16 位或32 位处理器。
它们可以使得控制器在操纵工程中显非常柔性。
控制器能通过通信线发送信号,使它能与机械手各轴交流信息,在机器人的机械手和控制器之间的双向交流信息可以保持操作和位置经常更新,控制器亦能控制安装在机器人手腕上的任何工具。
控制器也有与厂内各计算机进行通信的任务,这种通信联系使机器人成为计算机辅助制造(CAM)系统的一个组成部分。
存储器。
基于微处理器的系统运行时要与固态的存储装置相连,这些存储装置可以是磁泡,随机存储器、软盘、磁带等。
每种记忆存储装置均能贮存、编辑信息以备后续调用和编辑。
C. 动力源动力源是给机器人和机器手提供动力的单元。
传给机器人系统的动力源有两种,一种是用于控制器的交流电,另一种是用于驱动机械手各轴的动力源,例如,如果机器人的机械手是有液压和气动驱动的,控制信号便传送到这些装置中,驱动机器人运动。
对于每一个机器人系统,动力是用来操纵机械手的。
这些动力可来源与液压动力源、气压动力源或电源,这些能源是机器人工作单元整体的一部分。
robot The industr ial robot is a tool t hat is used in t he manufact ur ing environment to increase product ivit y. It can be used to do rout ine and tedious assembly line jobs, or it can per form jobs t hat might be hazardous to t he human worker . For example ,one of t he first indust r ial robot was used to replace t he nuclear fuel rods in nuclear power plant s. A human doing t his job might be exposed to har mful amount s of radiat ion. The indust r ial robot can also operat e on t he assembly line, putt ing toget her small component s, such as placing electronic component s on a pr int ed circuit board. Thus, t he human worker can be relieved of t he rout ine operat ion of t his t edious t ask. Robot s can also be programmed to defuse bombs, to serve t he handicapped, and to per for m funct ions in numerous applicat ions in our societ y. The robot can be t hought of as a machine t hat will move an end - of-tool , sensor , and/or gr ipper to a preprogrammed locat ion. When t he robot arr ives at t his locat ion, it will perform some sort of t ask . This task could be welding, sealing, machine loading , machine unloading, or a host of assembly jobs. Generally, t his work can be accomplished wit hout t he involvement of a human being, except for programming and for t urning t he syst em on and off. The basic t er minology of robot ic syst ems is introduced in t he following: 1. A robot is a reprogrammable , mult ifunct ional manipulator designed to move part s, mat erial, tool,or special devices t hrough var iable programmed mot ions for t he performance of a var iet y of different t ask. This basic definit ion leads t o ot her definit ions, present ed in t he following paragraphs, t hat give a complet e pict ure of a robot ic syst em. 2. Preprogrammed locat ions are pat hs t hat t he robot must follow to accomplish work, At some of t hese locat ions, t he robot will stop and per for m some operat ion , such as assembly of part s, spray paint ing ,or welding .These preprogrammed locat ions are stored in t he robot ’s memonr y and are recalled lat er for cont inuous operat ion. Fort her more,t hese preprogrammed locat ions, as well as other program dat a, can be changed lat er as t he work requirement s change.Thus, wit h regard to t his programming feat ure, an indust r ial robot is ver y much like a comput er , wher e dat a can be stoned and lat er recalled and edit ed. 3. The manipulator is t he ar m of t he robot .It allows t he robot to bend,reach, and t wist .This movement is provided by t he manipulator ’s axes, also called t he degrees of freedom of t he robot . A robot can have from 3 to 16 axes. The t erm degrees of freedom will always relat e to t he number of axes found on a robot. 4. The tooling and fr ippersare not part t he robot ic syst em it self;rat her,t hey are attachment s t hat fit on t he end of t he robot ’s ar m. These att achment s connect ed to t he end of t he robot ’s ar m allow t he robot to lift part s, spot -weld ,paint, arc-weld, drill, deburr, and do a var iet y of t asks, depending on what is required of t he robot. 5. The robot ic syst em can cont rol t he work cell of t he operat ing robot. The work cell of t he robot is t he tot al environment in which t he robot must perfor m it s task.Included wit hin t his cell may be t he cont roller ,t he robot manipulator , a work t able , safet y features,or a conveyor. All t he equipment t hat is required in order for t he robot to do it s job is included in t he work cell . In addit ion, signals from out side devices can communicat e wit h t he robot to t ell t he robot when it should part s, pick up part s, or unload parts to a conveyor. The robot ic syst em has t hree basic component s : t he manipulator, t he cont roller, and t he power sourse. A. Manipulator The manipulator , which does t he physical work of t he robot ic syst em, consist s of t wo sect ions:t he mechanical sect ion and t he att ached appendage. The manipulator also has a base to which t he appendages are att ached. Fig. 1 illustrat es the connect ion of t he base and t he appendage of a robot. Photo 1. Basic component s of a robot ’s manipulator The base of t he manipulator is usually fixed to t he floor of t he work area. Somet imes, t hough, t he base may be movable. In t his case, t he base is att ached to eit her a rail or a track, allowing t he manipulator to be moved from one locat ion to ant her. As ment ioned previously ,t he appendage ext ends from t he base of t he robot. The appendage is t he ar m of t he r obot. It can be eit her a st raight , movable ar m or a joint ed ar m. The joint ed ar m is also known as an art iculat ed ar m. The appendages of t he robot manipulator give t he manipulator it s var ious axes of mot ion. These axes are att ached to a fixed base , which, in t urn, is secured to a mount ing. This mouning ensures t hat t he manipulator will in one locat ion. At t he end of t he ar m , a wr ist(see Fig 2) is connect ed. The wr ist is made up of addit ional axes and a wrist flange. The wr ist flange allows t he robot user to connect different t ooling to t he wrist for different jobs. 8 The manipulator ’s axes allow it to per for m work wit hin a cert ain area. The area is called t he work cell of t he robot , and it s size corresponds to t he size of t he manipulator. (Fid2) illust rat es t he work cell of a t ypical assembly robot. As t he robot ’sphysical size increases,t he size of t he work cell must also increase. Photo2. Element s of a work cell from t he t op The movement of t he manipulator is controlled by act uator,or dr ive syst ems.The act uator,or dr ive syst ems, allows t he var ious axes to move wit hin t he work cell. The dr ive syst em can use electr ic, hydraulic,or pneumat ic power.The energy developed by t he dr ive syst em is convert ed to mechanical power by var ious mechanical power syst ems. The dr ive syst ems are coupled t hrough mechanical linkages. These linkages, in t urn, dr ive t he different axes of t he robot. The mechanical linkages may be composed of chain, gear, and ball screws. B. Cont roller The cont roller in t he robot ic syst em is t he heart of t he operat ion . The cont roller stores preprogrammed infor mat ion for lat er recall, controls per ipheral devices, and communicat es wit h comput ers wit hin t he plant for const ant updat es in product ion. The cont roller is used to cont rol t he robot manipulator ’s movement s as well as to cont rol per ipheral component s wit hin t he work cell. The user can program t he movement s of t he mamipulator into t he cont roller t hrough t he use of a har d-held t each pendant .This infor mat ion is stored in t he memory of t he controller for lat er recall. The controller stores all program data for t he robot ic syst em. It can store several different programs, and any of t hese programs can be edit ed. The cont roller is also required to communicat e wit h per ipheral equipment wit hin t he work cell. For example,t he contr oller has an input line t hat ident ifies when a machining operat ion is complet ed. When t he machine cycle is complet ed,t heinput line t urn on telling t he controller to posit ion t he manipulator so t hat it can pick up t he finidshed part .Then , a new part is picked up by t he manipulator and placed into t he machine. Next,t he controller signals t he machine to srart operat ion. The cont roller can be made from mechanically operat ed drums t hat st ep t hrough a sequence of enent s.This t ype of controller operates wit h a ver y simple robot ic syst em. The comtrollers found on t he major it y of robot ic syst ems are more complex devices and represent st at e-of-t he-art eletronoics.That is,t hey are microprocessor - operat ed.t hese microprocessors are eit her 8-bit , 16-bit ,or 32-bit processors. t his power allows t he controller to be ver y flexible in it s operat ion. The cont roller can send elect ric signals over communicat ion lines t hat allow it to t alk wit h t he var ious axes of t he manipulator. This t wo-way communicat ion bet ween t he robot manipulator and t he cont roller maint ains a const ant updat e of t he end t he operat ion of t he syst em. The cont roller also controls any tooling placed on t he end of t he robot ’s wr ist . The cont roller also has t he job of communicat ing wit h t he different plant comput ers. The communicat ion link est ablishes t he robot as part a comput er -assist ed manufact ur ing (CAM) syst em. As t he basic definit ion st at ed, t he robot is a reprogrammable, mult ifunct ional manipulator.Therefore, t he controller must contain some of memor y stot age. The microprocessor-based syst ems operates in conjunct ion wit h solid-st at e divices. These memor y devices may be magnet ic bubbles, random-access memony, floppy disks,or magnet ic tape.Each memor y storage device stores program infor mat ion fir or for edit ing. C.power suppy The power supply is t he unit t hat supplies power to t he controller and t he manipulator. The t ype of power are delivered to t he robot ic syst em. One t ype of power is t he AC power for operat ion of t he cont roller. The ot her t ype of power is used for dr iving t he var ious axes of t he manipulator. For example, if t he robot manipulator is cont rolled by hydraulic or pneumat ic drives, cont rol singals are sent to t hese devices causing mot ion of t he robot . For each robot ic syst em, power is required to operat e t he manipulator .This power can be developed from eit her a hydraulic power source, a pneumat ic power source,or an elect ric power source.There power sources are part of t he total component s of t he robot ic work cell.。