3月份不合格品统计分析报告
每月不合格品统计分析报告

累计400000 350000 300000 250000 200000 150000 100000
50000 0
382191.61 93%
十一车间
100%
26070.24
九车间
100%
981.15
十车间
累计百分比% 93% 100% 100% 100%
累计百分比% 100% 100%
255.8
十二车间
80% 名称
从排列图中在可以看出本月十一车间废品报废数量较大,其主要原因是 由于2904064-JA零件工艺更改,造成库存零件大量报废,报废金额达381054.81元,其报 废属于非正常报废。其他均属于正常报废。
2 原因分析:
环
材料
人员
球
储备超量
头
材料供应不及时
顾客未能及 时通知我厂
销
计划失策
零
件
工
艺
更
装配工位防磕碰措施差
改
造
设备台数少
成
大
法
设备
量
结论:影响该零件大量报废的主要原因是:顾客未能及时通我
报
厂,造成我厂未能及时调整生产计划。
3 纠正措施: 及时与顾客沟通,确保信息讯速传递。
编制:
审核:
批准:
废品: 1统计 废品金额:409498.8
序号 1 2 3 4
金额
12月份不合格品统计分析报告
责任废品率:0.322
废品指标:0.6
主要项目
金额
累计频次
十一车间
382191.61
382191.61
九车间
26070.24
408261.85
十车间
不合格品报告范文

不合格品报告范文标题:不合格品报告摘要:本报告旨在分析和总结公司生产过程中出现的不合格品现象,并提出改进建议,以提高产品质量和减少不合格品的发生。
1.引言不合格品是指在生产过程中出现的不符合质量标准要求的产品或零部件。
不合格品的存在不仅会造成经济损失,还会影响公司声誉,给客户带来负面影响。
因此,对不合格品的存在进行深刻的分析和总结,寻找问题的根源,并提出改进措施是十分必要的。
2.不合格品现象分析分析公司生产过程中出现的不合格品数量和种类,确定其发生的原因,以及对公司的影响。
通过统计数据和实地调查,发现不合格品主要有以下几个方面的问题:2.1原材料不合格:部分供应商提供的原材料不符合质量标准要求,经过生产后的产品也会出现不合格现象;2.2设备故障:生产线上的设备老化或维护不到位,导致在生产过程中出现一系列不合格品;2.3人为操作失误:员工在操作过程中因为疏忽或缺乏培训而造成误操作,进而导致不合格品的产生。
3.不合格品对公司的影响分析不合格品会导致以下几方面的负面影响:3.1经济损失:不合格产品需要重新生产或修复,增加了公司的生产成本;3.2回款延迟:客户对不合格品的投诉会导致以后的收款延迟,影响公司的资金流动;3.3客户满意度降低:当客户收到不合格品后,会对公司的产品进行质疑,降低了客户对公司的信任和满意度。
4.不合格品改进策略通过对不合格品现象进行分析,提出以下改进策略:4.1严格供应商评估:与供应商建立长期合作关系,并对供应商进行全面的质量评估,确保其提供的原材料符合质量标准;4.2设备维护与更新:加强对生产设备的维护工作,及时更新老化的设备,以确保生产过程的稳定性;4.3员工培训与意识提升:加强对员工的培训,提高员工对操作规程和质量标准的认知和理解,防止操作失误;4.4建立质量管理体系:建立完善的质量管理体系,包括质量控制点的设立和制度的宣导,以确保产品质量达到标准要求。
5.结论不合格品的存在对公司的质量和经济都会带来负面影响,因此,公司需要加强对生产过程的监控和管理,针对不合格品现象提出改进措施,以提高产品质量,降低不合格品的发生率。
调查不合格品分析报告

调查不合格品分析报告一、背景介绍不合格品是指在生产制造、工程施工和服务过程中,未能满足规定的质量标准和技术要求,存在缺陷或无法达到预期功能的产品。
不合格品的存在不仅给企业带来经济损失,也可能影响到用户的正常使用和权益保障。
为了提高产品质量和满足用户需求,本次调查旨在深入分析不合格品的原因,并提出相应的改进措施。
二、调查方法本次调查以ABC制造企业为对象,采用实地调查和问卷调查相结合的方式进行。
实地调查主要通过对不合格品的生产环境、工艺流程和生产设备进行观察和检查,了解实际生产情况。
问卷调查则通过向相关人员发放问卷,了解其对不合格品问题的认识和看法。
三、不合格品现状分析通过实地调查和问卷调查,我们发现不合格品的主要表现为以下几个方面:1. 设备问题:部分生产设备老化,存在性能不稳定、故障率高等问题,导致生产过程中出现品质波动。
2. 原材料问题:部分原材料的质量不稳定,存在成分变异、含杂质过多等情况,直接影响产品的品质和稳定性。
3. 工艺问题:生产工艺流程较为复杂,操作人员技术水平参差不齐,缺乏有效的工艺规范和培训,导致工艺操作不规范和质量波动。
4. 质量控制问题:质量检验不严格,存在抽样检验不足、检验标准不明确等问题,无法及时发现和排除不合格品。
四、问题分析与解决方案针对不合格品现状分析中提到的问题,我们提出以下解决方案: 1. 设备问题解决方案:加强设备维护和更新,定期检查设备性能,确保设备处于良好状态;加强设备操作培训,提高操作人员的技术水平和操作规范性。
2. 原材料问题解决方案:建立稳定的供应链管理机制,与供应商建立长期合作关系,确保原材料的质量稳定可靠;对原材料进行严格的进货检验,确保原材料符合质量标准。
3. 工艺问题解决方案:制定规范的工艺操作规程,明确每一道工序的操作要求和质量检验点,加强工艺培训,提高操作人员的技术水平和工艺规范性。
4. 质量控制问题解决方案:完善质量管理体系,明确质量控制流程和标准,加强质量检验的全程监控,增加抽样检验的频率和数量,确保及时发现和排除不合格品。
每月质量分析报告
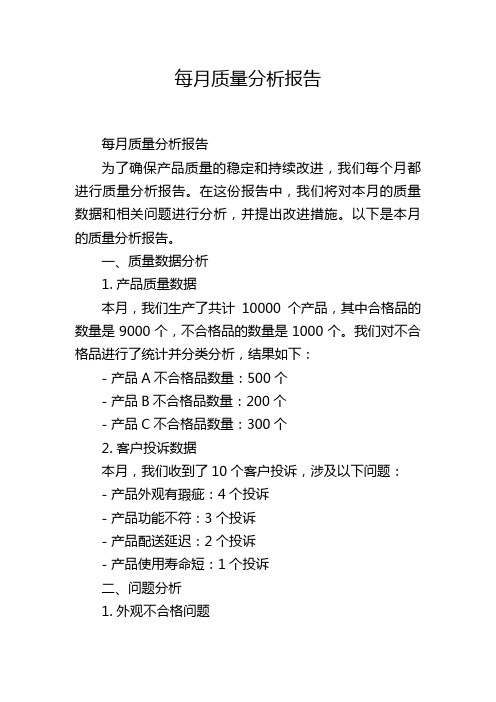
每月质量分析报告每月质量分析报告为了确保产品质量的稳定和持续改进,我们每个月都进行质量分析报告。
在这份报告中,我们将对本月的质量数据和相关问题进行分析,并提出改进措施。
以下是本月的质量分析报告。
一、质量数据分析1. 产品质量数据本月,我们生产了共计10000个产品,其中合格品的数量是9000个,不合格品的数量是1000个。
我们对不合格品进行了统计并分类分析,结果如下:- 产品A不合格品数量:500个- 产品B不合格品数量:200个- 产品C不合格品数量:300个2. 客户投诉数据本月,我们收到了10个客户投诉,涉及以下问题:- 产品外观有瑕疵:4个投诉- 产品功能不符:3个投诉- 产品配送延迟:2个投诉- 产品使用寿命短:1个投诉二、问题分析1. 外观不合格问题外观不合格问题主要集中在产品A,导致客户投诉和产品退货率上升。
我们初步分析认为可能是生产过程中出现了某个环节的误操作,造成产品外观不满足规定的质量标准。
我们将对生产线进行检查,并加强对员工的培训和监督,确保生产过程的操作准确无误。
2. 功能不符问题功能不符问题主要发生在产品C上。
经过对问题产品的分析,我们发现在生产过程中可能存在关键零件的质量问题,导致产品功能不符合要求。
我们将与供应商沟通,要求他们提供符合规定的零件,并加强对零件的抽检工作,以确保其质量。
3. 配送延迟问题配送延迟可能是由于物流部门的工作流程不够高效,导致产品无法按时送达客户。
我们将与物流部门进行沟通,并优化配送流程,提高送货效率,减少延迟的可能性。
4. 使用寿命短问题产品使用寿命短问题可能与产品设计和材料选择有关。
我们将组织跨部门的讨论和研讨会,找出使用寿命短的原因,并加强产品设计和材料选择的质量控制,以提高产品的使用寿命。
三、改进措施基于以上问题分析,我们提出以下改进措施:1. 加强员工培训和监督,确保产品外观质量满足要求。
2. 与供应商沟通,要求提供符合规定的关键零部件,并加强对零部件的质量控制。
不合格品处置报告

不合格品处置报告尊敬的XX领导:我写此报告是关于近期发现的一批不合格品的处置情况。
经过我部门的检验工作和相关部门的协助,我们已经完成了对不合格品的处置工作。
以下是具体情况的汇报:1.发现情况:在最近的检验工作中,我们发现了一批不合格品,涉及产品型号为XXX,总计共有XXX个,货值约XXX万元。
这些产品因存在以下问题被判定为不合格品:(1)外观瑕疵:产品表面存在划痕、凹陷等问题,不符合质量标准要求;(2)功能故障:产品在使用过程中出现频繁的故障,无法正常工作;(3)安全问题:产品存在电气漏电、易起火等安全隐患。
2.处置过程:在发现不合格品之后,我们及时组织了相关部门进行了深入的调查和分析。
经过与供应商和生产工厂的交流,我们了解到不合格品的主要原因是生产过程中存在的质量控制不严格以及原材料供应的问题。
针对这些问题,我们采取了以下处置措施:(1)与供应商协商,协商退货并要求其承担相应的赔偿责任;(2)调整产品检验标准,加强对现货和采购样品的抽检力度;(3)对生产过程中的质量控制进行全面检查,加强培训和引进先进的生产设备;(4)与原材料供应商进行沟通,要求其提供更加稳定可靠的产品。
3.处置结果:经过我们的不懈努力,与供应商的合作以及各方的支持,我们已成功退回了所有不合格品,并得到了相应的赔偿。
供应商也表示会加强质量管理,确保不再产生类似问题。
4.效益分析:通过这次不合格品的处置工作,我们认识到了质量管理的重要性,并在此基础上制定了一系列的改进措施。
这些改进措施有助于提升产品质量和客户满意度,保护公司的声誉和利益。
5.改进措施:针对此次不合格品的发现和处置,我们计划采取以下改进措施:(1)加强供应商的质量评估和管理,确保与其合作的产品符合标准要求;(2)进一步完善产品检验标准,确保产品出厂质量;(3)加强对生产工艺的控制,建立严格的质量管理体系;(4)定期开展产品抽检工作,及时发现和处理不合格品;(5)加强员工培训,提高质量意识和质量管理水平。
造成不良品分析报告

造成不良品分析报告1. 引言本报告旨在对公司生产中出现的不良品进行详细分析,并提供解决方案以减少不良品产生率,提高产品质量。
通过分析不良品的主要原因,我们能够更好地理解并控制生产过程中的问题,从而降低产品质量风险,提高客户满意度。
2. 背景公司一直致力于生产高质量的产品,但最近一段时间发现不良品产生率有所上升。
在此报告中,我们将重点分析不良品的主要原因,并提出一些建议和解决方案。
3. 不良品分析3.1 不良品定义我们首先需要明确不良品的定义。
在此报告中,不良品指的是生产过程中无法达到预期产品质量标准的产品。
3.2 不良品分类根据不良品的性质和原因,我们将不良品分为以下几个类别:1.外观缺陷:产品外观存在瑕疵、划痕、气泡等问题。
2.功能异常:产品在使用过程中出现缺陷,无法正常工作。
3.尺寸偏差:产品尺寸与设计要求不符合。
4.材料问题:产品使用的材料存在质量问题。
3.3 不良品原因分析通过对不良品的进一步分析,我们得出以下主要原因:1.工艺不稳定:生产过程中存在工艺参数不稳定的情况,导致产品质量波动较大。
2.操作不当:操作人员在生产过程中未按照标准操作规程进行操作,导致产品质量下降。
3.设备故障:生产设备存在故障或老化现象,导致产品质量无法保证。
4.材料质量问题:供应商提供的材料存在质量问题,影响了产品的质量。
5.质检失误:质检部门未能及时发现不良品,导致不良品流入市场。
3.4 解决方案为了降低不良品产生率,我们提出以下解决方案:1.工艺优化:通过优化生产工艺参数和流程,确保生产过程的稳定性和一致性,减少不良品的产生。
2.培训与培养操作人员:加强对操作人员的培训,提高其操作技能和质量意识,确保按照规程进行操作。
3.设备维护与更新:定期对生产设备进行维护保养,及时更换老化设备,确保设备正常运行,降低故障率。
4.严格供应商管理:加强对材料供应商的质量管理,确保材料的质量符合要求。
5.强化质检控制:加强对质检工作的监管和管理,提高质检员的质量意识和技术水平,确保不良品能够及时发现并进行处理。
品质月报表
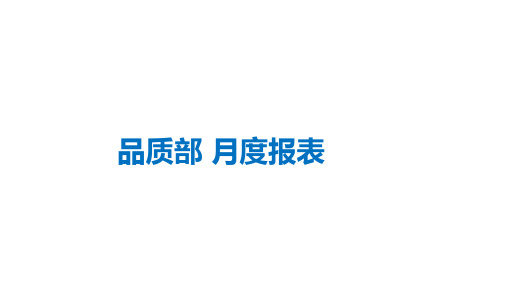
98%
98%
100% 90%
95.61%
2022年成品入库质量合格率趋势图
97.41%
97.92%
80%
70%
60%
50%
1月
2月
3月
4月
5月
6月
合格率
总结:3月份入库合格率为97.92%,成品 合格率每月呈上升趋势,已接近目标,主 要不良还是外观为主。
3月份成品入库质量报告汇总
类别
入库检验数
合格数
来料
627
572
55
10
26
19
挑选批次 /(工时)
5H
批合格率 目标值
91.23%
99%
按物料类别分类数据如下:包材类合格率最低,塑胶类合格率较 低。
序号 类别
来料批数 不良批
合格率
2022年3月来料类别合格率图
1
电子类
315
2
五金类
118
3
塑胶类
107
4
包材类
87
18
94.29%
7
94.07%
12
原因分析 待分析
经确认是没有保护膜,表面刮花造成的 员工装箱后未对照BOM核对配件
改善对策 待分析
F1出货需带保护膜,保护镜片 1.包装工序和入库检验增加录像;2.增加配件核对点检表
总结:3月份
80%
1月
2月
3月
4月
5月
6月
批合格率
总结: 本月来料合格率91.23%;来料共627
批,合格批数572批,不合格批数55批。 本月不良前三的分别为:昆明来料11
批不良,其中6批漏O型圈;鑫隆4批不 良、鑫达4批不良
产品不良原因分析报告模板范文

产品不良原因分析报告模板范文一、引言本报告旨在对产品不良原因进行全面分析,帮助企业了解造成产品不良的根本原因,以便采取相应的措施来改进产品质量和生产过程。
通过深入分析产品的不良现象和可能的原因,可以为企业提供有针对性的解决方案,从而提高产品质量和客户满意度。
二、背景在市场竞争日益激烈的环境下,产品质量已经成为企业竞争力的重要组成部分。
然而,某公司的部分产品出现了不良情况,给企业声誉和市场份额带来了负面影响。
因此,进行产品不良原因分析是非常必要的,以便及时纠正问题并提供改进措施。
三、研究方法为了分析产品不良的原因,我们采用了以下研究方法:1.数据收集:收集了相关的产品不良数据,包括不良率、不良类型、生产批次等信息。
2.实地调查:对生产现场进行实地调查,了解生产流程、设备状况、操作规范等情况。
3.产品检测:对不良产品进行详细检测和测试,以确定不良情况和可能的原因。
4.数据分析:通过统计分析和数据挖掘技术,对收集到的数据进行分析,找出可能的原因。
四、问题描述经过数据收集和实地调查,我们发现以下问题:1.不良率较高:部分产品的不良率超过了正常范围,严重影响了产品质量和市场竞争力。
2.不良类型多样:不良产品涉及多个类型,如外观缺陷、功能异常等,需要综合考虑问题。
五、不良原因分析通过对数据分析和实地调查,我们综合考虑了以下可能的原因:1.供应链问题:部分不良产品可能与供应链环节出现问题相关,例如原材料的质量未得到有效控制,或者供应商提供的零部件存在质量问题。
2.设备故障:生产设备可能存在故障或不稳定性,导致产品在制造过程中出现问题,而工人未能及时发现。
3.人为操作失误:由于操作规范不明确或缺乏培训,工人在生产过程中可能存在误操作或不良操作,导致产品质量下降。
4.生产工艺问题:某些生产工艺可能不够完善或不适用于某些产品,导致产品不良率较高。
5.质量控制不严格:生产过程中缺乏有效的质量控制措施,导致不良产品未及时发现和剔除。
- 1、下载文档前请自行甄别文档内容的完整性,平台不提供额外的编辑、内容补充、找答案等附加服务。
- 2、"仅部分预览"的文档,不可在线预览部分如存在完整性等问题,可反馈申请退款(可完整预览的文档不适用该条件!)。
- 3、如文档侵犯您的权益,请联系客服反馈,我们会尽快为您处理(人工客服工作时间:9:00-18:30)。
2 原因分析: 环
材料
人员
序号
零件号
报废数量
报废金额
报废主要原因
3 纠正措施:
尽早采用热挤压加工工艺,确保零件合格。
4 对我厂金额最高的前10个品种统计分析:
由于零件2902476-01零件裂纹数量较大,报废金额达7232.16元,占九车间废品总数的48%。
3月份不合格品统计分析报告
废品:1统计
结论:影响该零件大量报废的主要原因是:采用冷挤压加工工艺。
裂
纹
12902476-01278612704.16淬火裂纹2CQ353422371943.4中径大
33003032-15119931.11淬火裂纹42919173-13233495
52912161-5H34458.08
62912471-0349356.72
73502082-4E16289.6
8W3003032-1555289.3
92912481-0331242.13
102403061-B121234.57
编制: 周金铭 审核:牟洪祥批准:孙明文
指标:0.6
%
纠正措施责任单位
富奥标准件分公司九车间
富奥标准件分公司。