LF炉造渣工艺
LF炉造渣工艺优化

。
30 2 4
2 2 62
:
,
。
脱硫 情况 通过 跟 踪 精 炼造 渣 工 艺 优化 后 的 2 0 炉 种 经 统 计分 析 表 明 脱 硫 率有 明显 提 高
4 4
, ,
。
.
H R B 4 0 0E
钢
表
址 小谊 一 址 大 值 平均位
5
脱硫 情 况
:
脱硫率
:
,
,
,
雀羁 翼 矍 州
:
些 望瓷 … 斋互
4 3
, , ,
.
:
表
4
,
,
。
氧 含 量分布
p p。
。
}
项目
址小 值~ 址 大值
一
优 化前全 氧含 最
15 27 ~ 36 夕0
.
}
优化后 全氧含 景
1 7 4 6~ 2 5 80
. . .
pp。
}
3
3
.
精 炼渣 渣 系 及渣 量 制 定
1 影 响精 炼 渣 系 1 ) 熔 渣载 度 :
,
的 因 素有 以 下 几 点 ( 精 炼 过 程 中 熔 渣 载 度 直 接 影 响钢 渣反 应 的 速度 适 当 的 熔渣 载 度 影 响整个精 炼 效果 ( 2 ) 脱 硫程 度 L F 精 炼过 程 中适 当的渣料 配 比能 时熔 渣 的 硫容 量控 制到 最高 使 得 脱 硫效 果最 为 明 显 ( 3 ) 钢 水 过 氧 化 程 度 在 转 炉 补 吹 炉 次 钢 水 的过 氧 化 程度 较 严 重 出 钢 过 程 中或 精 炼 过 程 中需 要 加 人 大 量 的 脱 氧剂 降 低钢 水 中 的 自 由 氧 并 生 成 大 量 的 脱氧 产 物 影 响钢 水 的 纯净 度 因 此需 要调 整 渣系 提 高 熔 渣 吸附 夹杂 物 能力 3 2 精 炼 渣 系制 定 根据 以上 条件 我 厂 精 炼 目标渣 系 设 定如 下
LF精炼炉白渣工艺操作

LF精炼炉造白渣操作实践李军辉赵文勇沈桂根(杭州钢铁集团公司转炉炼钢厂杭州310022)摘要:本文主要介绍杭钢转炉厂在LF精炼炉生产过程中的白渣操作方法,总结适合本厂转炉LF精炼炉的白渣冶炼工艺。
关键词:炼钢LF精炼、白渣、操作前言杭钢转炉炼钢厂现有2座600吨混铁炉,4座40吨顶吹转炉,4座40吨LF精炼炉,部分钢水经LF精炼脱氧、脱硫、去夹杂、喂钙线对钢水进行钙处理。
主要精炼钢种为40Cr、ML40Cr、SWRCH35K、、50#系列、U71Mn、HML10、QD08、1008、T07A、440QZ、10#、20#等,要求每炉钢精炼均为白渣化操作。
1、白渣冶炼操作分析本厂精炼炉白渣冶炼操作方法主要可以归纳为以下三点:一分(对转炉厂现有的钢种进行分类,不同类别分别对待);二调(调整精炼吹氩参数,不同精炼时期采用不同的吹氩控制);三稳(稳定精炼的通电参数)。
1.1 一分对转炉目前所冶炼的钢种进行简单分类,主要分成三大类:第一类主要是以HML10、1008、T07A为代表的低碳低硅钢系列;第二类是以QD08、10#、20#、1018、1012等为代表的优质普碳钢系列;第三类主要是以40Cr、50#、SWRCH35K、U71Mn为代表的中高碳钢系列。
根据不同的类别制定一个基本的加料制度(见表1)。
表1 不同类别造渣料的加入量造渣料第一类第二类第三类石灰7kg/t 6kg/t 5kg/t萤石适量适量适量高性能精炼剂 1.5~2.5kg/t 1.5kg/t 1kg/t合成渣 2.5kg/t 2kg/t 2kg/t碳化硅适量0.25~0.5kg/t 0.25~0.5kg/t含铝合金 1.5~2kg/t 1~1.5kg/t 1~1.5kg/t同时根据出钢下渣情况,对加料顺序进行合理安排。
如不管钢水的下渣情况,渣子的干稀状况,只是将已经准备好的造渣料一次性加入钢包进行通电精炼。
往往造成精炼结束后造渣料不能化开,不能发挥精炼的脱硫、脱氧、去夹杂的功能。
LF炉精炼快速造白渣工艺研究与实践

LF炉精炼快速造白渣工艺研究与实践摘要:根据钢厂LF炉精炼造渣工艺的特点,利用炉渣组元CaO、SiO2、Al2O3、CaF2进行分析研究,制定出合理的渣系配比和快速造白渣制度,尽快形成炉内还原性气氛。
通过实践取得了稳定的脱硫、脱氧效果,成分和温度控制精度较高,充分发挥了LF炉精炼的效果。
关键词:LF炉精炼白渣1 前言随着用户对钢材质量的要求越来越高,LF炉精炼作为提升钢材质量的手段得到了迅速的发展。
在LF炉精炼过程中,通过合理快速的造白渣,尽快营造出炉内稳定的还原性气氛,可以达到脱硫、脱氧的目的,可以吸收钢中的夹杂物以及控制夹杂物的形态,可以精确控制成分;通过形成的白泡沫渣,埋弧效果好,热效率高,减少了耐火材料侵蚀。
我厂在原有造渣工艺的基础上,制定出如何快速造白泡沫渣,控制好埋弧、脱硫、脱氧、精确控制成分和温度等主要精炼环节,充分发挥LF炉精炼效果尤为重要。
2 主要设备基本参数钢包运输车:行走速度2~20m/min,最大载重量180t。
加热装置:电极直径Φ400mm,电极最大行程2700mm,电极分布圆直径680mm,升温速度4~6℃/min。
电炉变压器:额定容量18000KVA,一次电压35KV,二次电压335-295-235V,二次额定电流35.23KA。
氩气系统:供气压力 1.2MPa,工作压力0.25~1.0MPa。
冷却水系统:工作压力0.4~0.6MPa,回水压力0.2~0.3MPa,进/回水温度≤32/55℃。
3 精炼快速造白渣工艺制定3.1 转炉渣对精炼造渣的影响3.1.1 渣中碳粒对精炼造渣及钢中碳含量的影响冶炼中、高碳钢时,在转炉出钢合金化的过程中,由于加入增碳剂,有部分碳粒混入钢渣中,且加入顶渣后温降较大,使熔渣变稠甚至硬化结壳。
其结果导致就位成分碳含量不准确,并且熔渣中的碳粒参与脱氧,由于熔渣中的碳粒难以量化,使得造渣过程中脱氧程度难以控制。
为了解决这一问题,采用钢包在线吹氩,增加碳粉的回收率,钢包进入LF位后增加供氩气强度,确保混入熔渣中的碳粒完全熔化。
LF精炼工艺制度及钢水处理效果
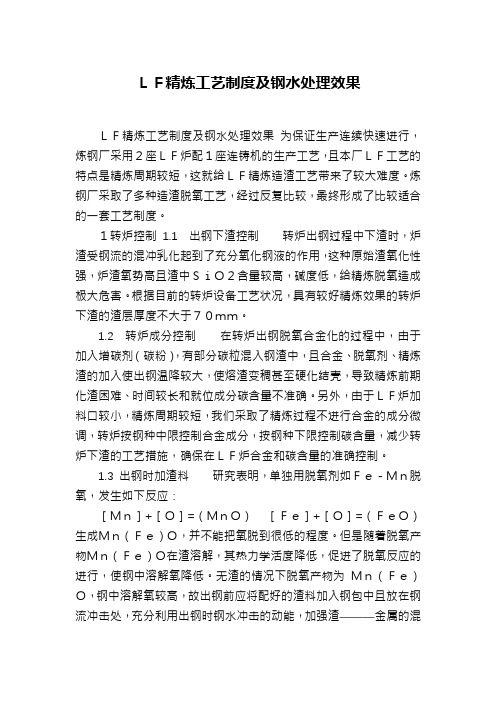
LF精炼工艺制度及钢水处理效果LF精炼工艺制度及钢水处理效果为保证生产连续快速进行,炼钢厂采用2座LF炉配1座连铸机的生产工艺,且本厂LF工艺的特点是精炼周期较短,这就给LF精炼造渣工艺带来了较大难度。
炼钢厂采取了多种造渣脱氧工艺,经过反复比较,最终形成了比较适合的一套工艺制度。
1转炉控制1.1出钢下渣控制转炉出钢过程中下渣时,炉渣受钢流的混冲乳化起到了充分氧化钢液的作用,这种原始渣氧化性强,炉渣氧势高且渣中SiO2含量较高,碱度低,给精炼脱氧造成极大危害。
根据目前的转炉设备工艺状况,具有较好精炼效果的转炉下渣的渣层厚度不大于70mm。
1.2转炉成分控制在转炉出钢脱氧合金化的过程中,由于加入增碳剂(碳粉),有部分碳粒混入钢渣中,且合金、脱氧剂、精炼渣的加入使出钢温降较大,使熔渣变稠甚至硬化结壳,导致精炼前期化渣困难、时间较长和就位成分碳含量不准确。
另外,由于LF炉加料口较小,精炼周期较短,我们采取了精炼过程不进行合金的成分微调,转炉按钢种中限控制合金成分,按钢种下限控制碳含量,减少转炉下渣的工艺措施,确保在LF炉合金和碳含量的准确控制。
1.3 出钢时加渣料研究表明,单独用脱氧剂如Fe-Mn脱氧,发生如下反应:[Mn]+[O]=(MnO)[Fe]+[O]=(FeO)生成Mn(Fe)O,并不能把氧脱到很低的程度。
但是随着脱氧产物Mn(Fe)O在渣溶解,其热力学活度降低,促进了脱氧反应的进行,使钢中溶解氧降低。
无渣的情况下脱氧产物为Mn(Fe)O,钢中溶解氧较高,故出钢前应将配好的渣料加入钢包中且放在钢流冲击处,充分利用出钢时钢水冲击的动能,加强渣———金属的混合,达到脱氧、脱硫的目的。
为此,我们采取了出钢过程加精炼渣的工艺制度,采取的精炼渣渣系为:CaO-Al2O3-MgO,主要成分见表1:表1精炼渣系的主要成分成分W(CaO) W(Al2O3) W(MgO) W(Fe2O3) W(TiO2) 精炼渣% 45.9 29.5 1.9 1.3 1.6 钢包中的w(Mn)/%2加热制度钢包精炼炉的二次测电压范围为150V~加热制度215V,分为4档,调方式为有载或无载。
LF炉造渣

造渣1、LF精炼渣的功能组成LF精炼渣的基本功能:深脱硫;深脱氧、起泡埋弧;去非金属夹杂,净化钢液;改变夹杂物形态;防止钢液二次氧化和保温。
精炼渣的成分及作用:CaO:调整渣碱度及脱硫;SiO2:调整渣碱度及黏度;Al2O3:调整三元渣系处于低熔点位置;CaCO3:脱硫剂、发泡剂;MgCO3、BaCO3、NaCO3:脱硫剂、发泡剂、助熔剂;Al:强脱氧剂;Si-Fe:脱氧剂;CaC2、SiC、C:脱氧剂及发泡剂;CaF2:助熔、调黏度。
在炉外精炼过程中,通过合理地造渣,可以达到脱硫、脱氧、脱磷甚至脱氮的目的;可以吸收钢中的夹杂物;可以控制夹杂物形态;可以形成泡沬渣淹没电弧,提高热效率,减少耐火材料侵蚀。
2、LF炉溶渣的泡沬化LF炉用3根电极加热,为了减少高温电弧对炉衬耐火材料和炉盖的辐射所引起的热损失和侵蚀,要进行埋弧操作。
为使电极能稳定埋在渣中,需调整基础渣以达到良好的发泡性能,使炉渣能发泡并保持较长的埋弧时间。
但是在精炼条件下,由于钢水已经进行了深度不同的脱氧操作,钢中的碳和氧含量都较低,不会产生大量的气体,要形成泡沬渣有一定的困难,因此要加入一定数量的发泡剂,如碳酸盐、碳化物、碳粉等,使炉渣发泡。
影响熔渣发泡效果的主要因素分析(1)熔渣碱度。
熔渣碱度低时发泡效果较好。
(2)基础渣中ω(CaF2)。
实验结果表明:CaF2是表面活性物质,适当配加一定量的萤石,渣容易起泡。
ω(CaF2)=8%时,熔渣发泡效果最好。
但当CaF2过高时,熔渣黏度降低,这不利于泡沬渣的稳定,使发泡持续时间减少。
因此,ω(CaF2)不宜超过10%。
3、白渣精炼(1)白渣精炼,一般采用CaO- SiO2- Al2O3系炉渣,控制渣中ω(FeO+MnO)≤1.0%,保持熔渣良好的流动性和较高的渣温,保证脱硫、脱氧效果。
(2)适当搅拌,避免钢液裸露,并保证熔池内具有较高的传质速度。
总之,LF炉造渣要求“快”、“白”、“稳”、“快”就要在较短时间内造出白渣,处理周期一定,白渣形成越早,精炼时间越长,精炼效果越好;“白”就是要求ω(FeO+MnO)降到1.0%以下,形成强还原性炉渣;“稳”有两方面含义,一是炉与炉之间渣子的性质要稳,不能时好时坏;二是同一炉次的白渣造好后,要保持渣中ω(FeO+MnO)≤1.0%,提高精炼效果。
210吨LF精炼炉高效造渣技术的研究与应用

210吨LF精炼炉高效造渣技术的研究与应用LF精炼炉是钢铁冶炼过程中的重要设备,其主要作用是通过精炼处理,使钢液中的杂质得以除去,从而提高钢水的质量。
而造渣技术则是LF精炼炉操作中的重要环节,能够影响到炉内的化学反应和钢液的质量,因此如何提高LF精炼炉的造渣技术,成为了钢铁行业关注的焦点。
近年来,随着我国钢铁行业对钢水质量和生产效率要求的不断提高,LF精炼炉高效造渣技术的研究与应用受到了广泛关注。
本文将就LF精炼炉高效造渣技术的研究与应用进行深入探讨,以期为相关领域的研究与实践提供一定的参考和借鉴。
一、LF精炼炉高效造渣技术的研究现状LF精炼炉高效造渣技术的研究,主要集中在造渣剂的选择、加入方式及作用机理等方面。
造渣剂是LF精炼炉造渣过程中的关键物质,它能够吸附、包裹和还原钢液中的氧化物、硫化物等杂质,从而提高造渣的效果。
当前,常见的造渣剂主要包括生石灰、石灰石粉、石灰石等,它们能够在造渣过程中脱除氧化铁、硫化铁等有害元素,是LF精炼炉造渣的重要辅助材料。
在造渣剂的选择上,研究人员主要关注其吸附性能、还原能力和成本等因素,通过对造渣剂的物理化学性质进行分析,优化其配比比例和加入方式,以期提高LF精炼炉的造渣效果。
还有很多专家学者从理论角度出发,通过建立数学模型和仿真实验,探讨造渣剂的作用机理,进一步指导LF精炼炉的造渣操作。
研究人员还在LF精炼炉高效造渣技术中开展了大量的实验研究和工程应用,在不断积累经验的基础上,总结了一系列适合不同工艺条件的造渣方案,为钢铁企业提高生产效率、降低生产成本提供了重要的技术支持。
LF精炼炉高效造渣技术的研究成果已经得到了广泛的应用。
目前,我国钢铁企业普遍采用了先进的LF精炼炉高效造渣技术,通过合理选择造渣剂、优化造渣操作,不断提高了钢液的质量,提高了钢水的成材率和合格率,降低了钢材的氧化铁含量,改善了钢材的表面质量和力学性能。
在应用中,LF精炼炉高效造渣技术还得到了多个方面的推广。
LF炉精炼造白渣工艺研究与实践

科学技术S cience and technology LF炉精炼造白渣工艺研究与实践张志辉(新兴铸管新疆有限公司,新疆 和静841300)摘 要:随着我国科学技术的快速发展,我国经济也得到了提高。
根据我国钢厂LF炉精炼造白渣工艺技术的相关特点,充分的利用了炉渣的相应组元SIO2,CAO,CAFA2进行相关的分析研究,从而制定出科学合理的白渣系配比与快速造白渣的相关规章制度,从而快速形成钢炉中的还原性气氛。
本文主要是通过分析实践来取得安全稳定的脱氧和脱硫的实际效果,其钢炉内的温度控制精度和成分相对较高,能够在一定程度上将发挥出LF炉精炼的全部效果,让LF炉精炼造白渣工艺的能够更好的为钢厂所服务,从而提高钢材的质量。
关键词:LF炉精炼;造白渣工艺;研究;实践中图分类号:TF769.4 文献标识码:A 文章编号:11-5004(2018)05-0139-2伴随着用户对钢材质量要求的变高,LF炉精炼是作为提高钢材质量的主要手段之一,其在当前钢厂炼制钢材中可以有效的提高钢材质量。
LF炉精炼在炼制过程当中,是可以通过科学合理的造白渣工艺来提高钢材出炉中稳定的还原性气氛,还能快速达到脱氧,脱硫的主要目的,造白渣工艺还能在炼制中吸收钢材中的杂物和控制杂物的相关形态。
我们通过所形成的白泡沫渣和热效率的效率相对较高,从而在一定程度上去减少钢材耐火材料的相应侵蚀能力。
我国大多钢材是在原有造白渣工艺当中,指定出了怎样稳定快速造白泡沫渣,脱氧,脱离,温度控制等相关精炼阶段的,在某种程度上能够充分发挥出LF炉精炼的全部作用。
1 精炼造白渣工艺的制定1.1 转炉渣对精炼造白渣的具体影响转炉渣对精炼造渣的相关影响。
转炉在钢材出港的过程当中会出现下渣,所起到的充分氧化钢液的作用,从而在一定程度上让钢材的成分与脱硫,脱氧元素不断的进行相应的变化。
对于这种原始渣的氧化性相对较强,其在一定程度上延长了LF精炼脱硫的时间。
我们通过实践,可以准确的发现,在转炉钢材包之内的下渣厚度大多都是小于50毫米的,在这个厚度当中,精炼大多可以持续5-7分钟,在这个时间段之内,是可以获得流动性的效果让其熔渣的质量变得更好,其熔渣中的SIO2含量也会较少,这种情况的出现是能够让白渣形成的速度变快。
300吨LF炉工艺技术理论培训
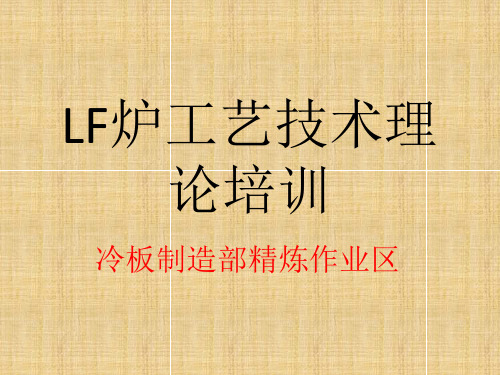
多或渣子没化透,渣子发黏,应加入萤石并通电化渣处理。
g、渣层厚度要>100—200mm为佳,一则易脱硫去夹杂,二则 保温隔热,减少温降,提高升温效率。 h、当渣子变成墨绿或白色,搅拌5-8min,关闭Ar气旁通阀, 并测温取样,根据所测温度与目标出站温度,送电使钢水温
度高于目标值10-15℃,以满足喂丝,弱吹时的温降。
Ls(渣中硫的分配系数)显著增加,脱硫效果增加。由于原
料中不可避免会带入部分Si02,因而CaO-Al203-CaF2渣系
实际上为Ca0-Al203-CaF2-Si02四元渣系。对该渣系进行研
究后得出w ( Ca0 ) /w (Si02)大于0.15后,脱硫效果比较理 想。
Ca0-Si02-Mg0-Al203 渣系
铁活度(αFeO)的高低。熔渣的碱度对αFeO数值的影响起着
重要的调整作用。当w(FeO+MnO)<1.0%时,还原很充分, 很利于反应进行。由于钢渣之间的扩散关系,氧在钢渣间存 在着平衡分配关系。但在初炼时期两者并没有立即平衡,需 要搅拌和反应时间。通过钢渣接触、氩气搅拌,钢中[Al]也直
接同渣中的(FeO)起反应。更有效的办法是将颗粒状的Al粒
国外LF精炼渣的特点是高碱度(有时渣中的Ca0含量高达65%),
并能获得较好的精炼效果;而国内普遍采用的是中(R=2.2-3.0),
低(R=1.6-2.2)水平碱度的精炼渣,在这种碱度范围内,也同样显 著提高了钢液的质量。实验中发现,碱度越高反而越不易于脱硫, 一般将碱度控制在2.5-3.5之间,硫的分配比较高,精炼结束时可 达到80以上。据相关文献介绍渣的碱度控制在2.5 -3.0时熔渣具有
含氧向钢水传递,把钢水实际的脱氧任务提前到LD出钢过程中来完 成,减轻LF精炼负荷。精炼渣系采用表中Ca0-A1203-CaF2 渣系,该 一般LD出钢硫在0.040%以上,在较短的时间内,可以将钢中硫含量
- 1、下载文档前请自行甄别文档内容的完整性,平台不提供额外的编辑、内容补充、找答案等附加服务。
- 2、"仅部分预览"的文档,不可在线预览部分如存在完整性等问题,可反馈申请退款(可完整预览的文档不适用该条件!)。
- 3、如文档侵犯您的权益,请联系客服反馈,我们会尽快为您处理(人工客服工作时间:9:00-18:30)。
LF炉造渣工艺摘要本文根据本钢炼钢厂炉外精炼LF生产的实际情况,从渣系的选择,渣料的加入量,加入方式以及影响脱硫效果的因素等各方面,总结了本钢炼钢厂脱硫制度。
关键词LF炉脱硫炉渣Technology of slag for LFAbstract The writing basis of LF product of practice. From slag system change、material amount、how to add and influence element of desulphurization.Key words LF Desulphurization Slag1 前言随着用户对钢材质量的要求越来越高,炉外精炼作为提升钢材质量的手段得到了迅速的发展。
在炉外精炼过程中,通过合理地造渣可以达到脱硫、脱氧甚至脱氮的目的;可以吸收钢中的夹杂物;可以控制夹杂物的形态;可以形成泡沫渣淹没电弧提高热效率,减少耐火材料侵蚀。
因此,在炉外精炼工艺中要特别重视造渣。
在我厂现有LF设备的基础上制定合理的造渣工艺,控制好埋弧、脱硫、脱氧等主要精炼环节,充分发挥LF精炼效果尤为重要。
2 LF炉的设备特点和能力本钢炼钢厂的LF&IR炉设备,引进于意大利·达涅利公司,是一座双工位处理站,于2001年11月进行热试、投产,现年处理钢水量在160万吨以上。
LF炉变压器的功率为28MV A,最高升温速率可达5℃/min,LF炉盖的微正压设计,可有效减少处理过程的吸氮现象、二次氧化现象及电极的侧面氧化。
LF整个处理过程可控制增氮量0.0010%以下;经LF炉造渣深脱硫处理后钢中全氧在0.0030%以下;LF炉的电极消耗≤0.01kg/kWh。
采用LF 炉造还原渣处理或LF炉改渣+喷粉处理,可将钢中[S]脱至0.0010%以下。
3造渣脱硫原理分析3.1 热力学原理造渣脱硫过程中,常采用石灰做为脱硫剂,其脱硫反应按离子理论可写做(O2-)+[S]=(S2-)+[O] (3-1)△Gº=71965-38T,J/molK S=[a S2-·a O]/ [a O2-·a S]=[(%S)·γS2-]/[ao2-·[%S]f S]或[%S]=1/ K S([(%S)·γS2- ·a O])/([a O2-·f S] (3-2) 由式(3-2)可以看出,强化脱硫的热力学条件是:高碱度的渣(即增大ao2-);低氧位或强还原性(即降低a O);降低(%S)(即换渣);以及高温操作(因△H≈71965>0,提高温度使K S值变大)。
3.2 炉渣脱硫反应的限制性环节炉渣脱硫可分为以下几个环节:①钢液中[S]向钢渣界面扩散;②渣中(O2-)向钢渣界面扩散;③扩散到钢渣界面的[S]与(O2-)在发生反应;④反应产物(S2-)向炉渣扩散;⑤反应产物[O]向钢液中扩散。
在以上五个环节中,步骤③、⑤速度很快,不是反应的限制环节;当钢中[S]含量较低时,步骤①将成为反应的限制性因素;当炉渣碱度低时,步骤②将成为反应的限制性因素;当炉渣粘度高、流动性差时,步骤④将成为反应的限制性因素。
所以在生产实践的控制中,应控制炉渣具有较高的碱度、较好的流动性、足够的吹氩搅拌来满足动力学条件。
4精炼造渣工艺制定4. 1转炉渣对精炼效果的影响4.1 1渣中碳粒对钢中碳含量的影响在转炉出钢合金化的过程中,由于加入增碳剂(沥青焦),有部分碳粒混入钢渣中,且白灰、合金的加入温降较大,使熔渣变稠甚至硬化结壳。
其结果导致精炼前期化渣困难时间较长和就位成份碳含量不准确。
为了解决这一问题,采取了转炉按钢种下限碳含量控制,减少转炉下渣和LF送电5~8min后取样的措施,确保在LF碳含量的准确控制。
4.1 2转炉下渣对精炼效果的影响转炉出钢过程中下渣时,炉渣受钢流的混冲乳化起到了充分氧化钢液(消耗脱氧剂和铁合金)的作用。
到精炼的运输过程中对钢包中钢液起到长时间的氧化作用,使钢成份、脱氧元素不断变化[1]。
这种原始渣氧化性强,炉渣氧势高且渣中SiO2含量较高、碱度低,给LF精炼脱氧造成极大危害,造渣时间延长,精炼与铸机匹配不畅。
在LF精炼过程中发现钢包内转炉下渣超过100mm时加入较大数量的渣料和脱氧剂及熔剂都难以使熔渣获得良好的流动性及良好的白渣化程度,白渣化困难的主要原因是渣中FeO含量高,脱氧剂很难在粘稠的渣中扩散,脱氧时间长。
取渣样分析的结果表明渣中(FeO+MnO)含量较高,这种熔渣吸收夹杂物的能力也较差。
渣厚在50~10mm之间时,化渣仍然较慢,熔渣流动性一般,白渣化程度一般,较难形成粉白渣,停电后熔渣在2~3min后粘度迅速增大,这种熔渣吸收夹杂物的能力也较差。
渣厚小于50mm时,化渣迅速,送电5~8min后熔渣便能获得良好的流动性,也具有良好的埋弧作用,熔渣SiO2含量也较少,熔渣过程粘度变化小,能较早形成白渣。
分析结果表明渣中(FeO+MnO)含量较低。
搞好出钢末期的挡渣,尽可能地减小转炉渣进入钢包是发挥LF精炼作用的基本前提,这一点要引起高度地重视。
4.2合理的脱硫渣系炉渣的精炼能力决定于炉渣的化学性能和物理性能。
为确保熔渣具有较好的流动性、发泡埋弧作用、脱硫及吸收夹杂物的能力,钢液脱硫常用的渣系主要有 CaO—CaF2、CaO—CaF2—AL2O3、CaO—AL2O3—SiO2等渣系。
①CaO—CaF2渣系中,从脱硫考虑,CaF2含量在40%左右为最佳组成,但该渣系对耐材寿命影响较大。
②CaO—CaF2—AL2O3渣系硫容量比CaO—CaF2低,据报道,该渣系的组成在CaO≥50%,CaF2≥20%,AL2O3≤25%范围,特别是CaO:30~60%,CaF2:45~55%,AL2O3<10%范围为最佳组成。
③CaO—AL2O3—SiO2渣系是人们研究最多,应用最广泛的一个基本渣系渣样成分CaO% MgO%SiO2% TFeO AL2O3范围19~3728 8~12107~20%144~15%9.520~30%25从表四可以看出,本钢炼钢厂精炼前渣系属于CaO—AL2O3—SiO2渣系,因此在脱硫渣系的选择上应以此渣系为基础进行研究。
根据生产实践和研究资料介绍,我们选择表2所示渣系为我厂应选择的LF精炼目标渣系。
表2 LF精炼目标渣系(%)CaOSiO2 Al2O3 MgOFeOMnOCaF2 R45~55 10~20 15~20 5~10 <0.8 <0.3 7~12 2.9~3.6 5 LF造渣脱硫实践5.1炉渣改质的方法通常转炉出钢时会有一定的氧化性转炉渣随钢流进入钢包中,在脱氧及合金化后钢包顶渣的氧化性会有所下降,但对LF炉造渣脱硫来说,其氧化性还是很高的。
同时由于渣中SiO2的含量较高,炉渣的碱度较低,不能满足LF炉进一步深脱硫的需要。
要实现深脱硫或较高的脱硫率就必须将低碱度的氧化渣改成高碱度的还原渣。
这一目的可通过两种方法实现。
方法一:转炉出钢前后不对炉做任何处理,直接到LF炉加入大量造渣材料及扩散脱氧剂,进行供电造还原渣。
方法二:在转炉出钢前和出钢过程中向钢包中加入钢包改性渣(具有脱氧及调节炉渣成分的作用),然后在LF加入适量造渣材料和扩散脱氧剂,进行供电造还原渣。
两种方法都可实现深脱硫的效果,但方法二具有成渣快、脱硫速度快、脱氧剂消耗少、处理周期短的优点。
按方法二对炉渣成分进行改质,转炉出钢过程不加改性渣与出钢过程中加改性渣及LF炉处理后的最终炉渣成分的变化对比情况如表3所示。
钙前 5.33 30.96 47.46 0.01 1.03 0.24 14.13 0.24 98.90 9.66 2.84 钙后 5.32 33.26 44.90 0.01 1.02 0.27 14.53 0.18 99.49 8.53 2.62 从表1可以看出,转炉出钢后碱度较低而氧化性很高,若在出钢过程中加入改性渣,则可使碱度明显提高、氧化性明显降低,经过LF炉继续造渣处理后,炉渣变成十分有利于的高碱度的还原渣。
5.2 炉渣氧化性与脱硫率的关系由式(3-1)可知,在脱硫反应过程中会在反应界在产生[O],若炉渣中含有较多的(FeO+MnO)将会直接阻止脱硫反应的进行。
因此在实际生产中必须严格控制炉渣的氧化性,尽可能降低炉渣中的(FeO+MnO)含量,并持续保持。
图1从图1可看出,随着炉渣中的(FeO+MnO)含量的降低,脱硫率呈明显上升趋势。
当炉渣中的(FeO+MnO)含量大于是2.9%时,脱硫率小于25%;当炉渣中的(FeO+MnO)含量小于是1.9%时,脱硫率大于55.6%;当炉渣中的(FeO+MnO)含量为1.5%时,脱硫率为69.7%。
因此在实际生产中若取得深脱硫效果或较高的脱硫率,应将当炉渣中的(FeO+MnO)含量控制在1.5%以下的水平。
5.3 炉渣碱度的控制炉渣中的(O2-)为脱硫反应的反应物,因此需要向炉渣中提供足够的(O2-),同时还要减少炉渣中的(SiO2),以减少二氧化硅络离子对(O2-)的争夺。
炉渣中的(O2-)主要由向(CaO)、(MgO)提供,转炉出钢后通常炉渣中的(MgO)含量为8~13%,随着造渣材料的加入,炉渣中(MgO)的含量逐渐降低,但应注意适当保持其含量,否则会影响钢包的使用寿命。
而炉渣中的(CaO)含量也不能太高,过高的(CaO)含量会导致炉渣熔点升高、流动性变差,使脱硫的动力学条件变差,对脱硫效果的影响很大。
合适的炉渣成分控制为(CaO)50~55%、(MgO)7~9%、(SiO2)<10%。
随着CaO的加入炉渣碱度升高,炉渣硫容量增大,脱硫能力增强。
当碱度达到一定值时,随着炉渣碱度增大,渣中CaO含量升高,熔渣粘度增大,渣钢界面硫扩散成为限制环节,使炉渣脱硫的动力学条件变差,再继续提高炉渣碱度,脱硫率反而下降。
5.4 SiO2对脱硫、脱氧的影响熔渣中SiO2含量普遍较高,主要是转炉下渣较多。
含Si、Mn较高的钢原始渣中CaO低、SiO2高,熔渣基本成中性,渣中SiO2高达20%以上,精炼后FeO<0 5%的较少,而在1 0%左右的较多且脱硫效果差。
原因在于渣量多、精炼新加CaO等渣料熔化时间长使渣中脱氧剂扩散困难,SiO2含量高,碱度低,熔渣组元活度受到影响。
5.5Al2O3含量对脱硫的影响脱硫率随Al2O3含量的增加呈下降趋势。
这是由于渣中Al2O3是两性氧化物,在碱性还原渣中Al2O3呈酸性,随着Al2O3含量的增加炉渣碱度降低,使炉渣的脱硫能力降低。
但从生产中可以看出,渣中适当添加Al2O3可以明显降低渣系熔点,促进化渣。
因此,要获得良好的冶金性能兼顾其脱硫能力和物理性能,即渣中应添加一定量的Al2O3。