质量技术岗位培训教材
质量部培训教材

第一节:品管基础知识:1.什么是品质?如何评价产品品质?公司产品流程+.产品标准客户对产品满意程度的感受.2.作为QC员应具备基本的素质.积极性、主动性、原则性、责任感、客观判断力、沟通协调能力.3.QC(IQC、IPQC、QA)岗位的作用及职责..IQC:来料品质检验与控制:作用:预防和控制来料异常的产生;IPQC:制程品质检验与控制:作用:预防和控制制程异常,判定制程中的不良品及发现制程异常隐患. FQC: 品质保证. 作用:出货前品质保证.防止不良品流出公司..职责见指导书4.QC(IQC、IPQC、FQC)作业流程.见作业指导书5.本公司采用的何种抽样检验方式,抽样比例是多少?采用随机抽样的方式;抽样比例为:10箱/包以下开箱/包率为100%.10箱/包以上开箱/包率为大于50%.6.产品缺陷分几类等级,分别是什么?如何定义缺陷等级?产品缺陷分3类等级;分别为:严重缺陷(致命缺陷)CR、主要缺陷(功能缺陷)Maj、次要缺陷(轻微缺陷)Min.定义为:严重缺陷:产品在使用或装配过程中对使用者或装配者造成人身安全之缺陷.主要缺陷:影响产品性能,导致产品无法正产使用或导致产品性能失效之缺陷.次要缺陷:影响产品外观,不影响产品性能之缺陷.7. 物料/产品的抽样标准及判定标准.美国军用标准MIL-STD-105E LEVEL II级单次抽样计划判定标准IQC AQL CR:0 maj:0.65 min:2.5.QA AQL CR:0 maj:0.40 min:2.58.品质管理的原则预防重于修理:防患于未然9.品质管制的特性:是应用科学,而非理论科学;是手段不是目的;过程重于结果;重视数据的特性.10. 自主管理三原则,即:A、操作员知道他(她)需要做什么?B、操作员知道他(她)正做什么?C、操作员知道调节行动符合上述原则,操作者责任20%;不符合上述原则,管理者责任80%。
第二节:来料异常处理:1.IQC:正常来料检验时发现物料异常如何处理?a.标识不良品、区分缺陷等级.与合格品隔离.b统计不良数量,不良率c.填写来料检验报告并提供不良样品,交组长审核;由质量、工程、PMC、生产负责人签署判定.最终由质量经理以上领导签署判定处理结果,判定结果分为:特采、加工、挑选、退货.d.根据最终处理结果贴相对应的贴纸于物料包装上.将检验报告附件发给PMC、仓库、生产、工程等部门.e.出具《来料异常通知单》知会供应商改善,并跟进后期来料改善状况的验证.2.IQC:当IQC正常检验判定为合格后,物料上线组装时发现物料异常的情况下应如何处理?a.首先将生产线反馈的物料进行再次检验,确认是否是检验失误。
质量检验知识培训教材
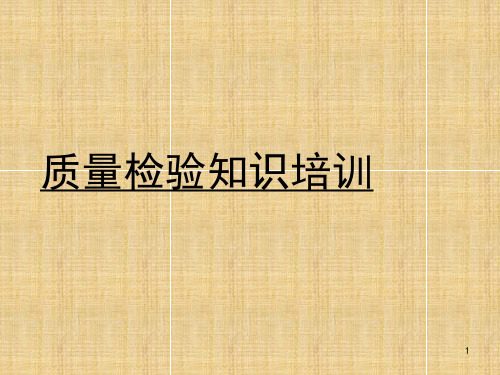
第二部分 质量检验的主要管理制度
1. 三检制 2. 签名制 3. 质量复查制 4. 追溯制 5. 质量统计 6. 不合格品管理 7. 质量检验的考核
1、三检制
所谓三检制就是实行操作者的自检、工人之间的互检和专职检验 人员的专检相结合的一种检验制度。
1. 自检:生产者对自己所生产的产品,按照作业指导书规定的技术标准 自行进行检验,并作出是否合格的判断。工人参与质量管理的重要形 式。
返工、返修、原样使用);不合适品的现场管理。
7、质量检验的考核
检验误差及其分类: 1. 技术性误差:检验人员缺乏检验技能造成的误差 2. 情绪性误差:检验员马虎大意、工作不细心造成的检验误差 3. 程序性误差:生产不均衡、加班突击及管理混乱所造成的误差 4. 明知故犯误差:检验人员动机不良造成的检验误差 检验误差的指标及考核方法 1. 检验误差概括分为漏检、错检 2. 测定和评价检验误差的方法:重复检查、复核检查、建立标准品 3. 考核注意事项:质量检验部门和人员不能承包企业或车间的产品质
6、不合格品管理
不合格品和废品是完全不同的两个概念,不合格品(或称不良品) ,其中包括废品、返修品和回用品三类。
在不合格品管理中,需要做好以下几项工作: 1. “三不放过”的原则:不查清原因不放过;不查清责任者不放过;
不落实改进措施不放过。 2. 两种“判别”职能:符合性判别;适用性判别;分类处理(报废、
关和预防作用的关键,也是检验部门参与提高产品质量的具体体现。
4、质量检验的三性
检验“三性”是指检验工作的公正性、科学性和权威性。这也 是对检验工作的基本要求,对发挥检验工作的作用十分重要。 1. 公正性:检验工作的公正性是对质量检验最主要的要求,没有公正 性,检验就失去了意义,也就谈不上把关的职能。 2. 科学性:这里说的是要通过科学的检测手段,提供准确的检测数据 ,按照科学合理的判断标准,客观地评价产品质量。 3. 权威性:权威性是正确进行检验的基础。所谓检验的权威性实质上 是对检验人员和检验结果的信任感和尊重程度。
质量检验员培训教材
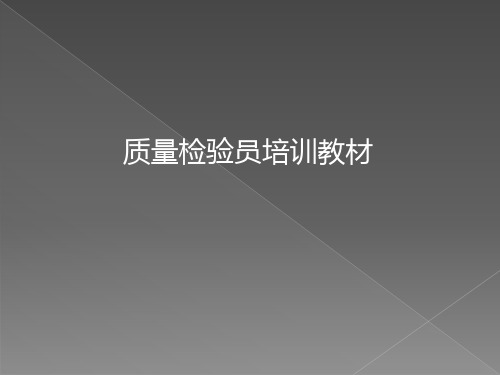
第三部分:不合格控制
二、不合格品(质量事故)的处理
(1)不合格品的概念:未满足规定要求的产品 (2)不合格品的类型
a.返工 b.返修 c.让步接收 d.降级 e.报废
第三部分:不合格控制
(3)不合格品的处理程序 a.标识 b.隔离 c.记录 d.评审 e.处置 f.重新检验
第四部分:纠正预防措施
•误差=测量结果-真值=(测量结果-总体均值)+(总体均值-真值)=随机误差+系统 误差 任何一个误差,都可以分解为随机误差和系统误差。
•随机误差:测量结果与在重复性条件下,对同一被测量进行无限多次测量所得的结果的平均 值之差,称为随机误差。随机误差大抵来源于影响量的变化,这种变化在时间上和空间上是 不可预知的或随机的。
电荷[量] 电压,电动势,电位,(电势)
电容 电阻 电导 磁通[量] 磁通[量]密度,磁感应强度 电感 摄氏温度 光通量 [光]照度 [放射性]活度 吸收剂量,比授[予]能,比释动能 剂量当量
单位名称
弧度 球面度 赫[兹] 牛[顿] 帕[斯卡] 焦[耳] 瓦[特] 库[仑] 伏[特] 法[拉] 欧[姆] 西[门子] 韦[伯] 特[斯拉] 亨[利] 摄氏度 流[明] 勒[克斯] 贝可[勒尔] 戈[瑞] 希[沃特]
第三部分:不合格控制
一、不合格的严重性分级 (1). 不合格的定义:未满足要求. (2按此)其实. 不对 施合产管格品理严适. 重用性性分影级响,的就不是同将进产行品分质类量,可列能出出具现体的的不分合级格,据, (3)不合格分级的作用 a.可以明确检验的重点 b.有利于选择更好的验收抽样方案 c.便于综合评价产品质量 d.对检不验合职格能进的行有分效级性并都实有施重管要理作,对用发. 挥质量综合管理和质量
质量检验员培训教材PPT52页

32
⑥.规定 检查严格度(宽严程度)
本标准规定有正常检查、加严检查和放宽检查 三种不同程度的检查严格度; 除非另有规定,在检查开始时,应使用正常检 查; 检查严格度的调整按转移规则进行。 ⑦.选择 抽样方案类型
做好记录并保存好检验结果; 做好产品状态的标识; 进行不合格品统计和控制; 异常信息反馈.
注:只有质量计划中规定的所有检验项目都完成且合格之 后,产品才能转序或入库.
21
七、出货检验(OQC)
1 、主要职责: 按质量策划的结果(如质量计划、出货检验指导书)实
施检验; 做好记录并保存好检验结果; 做好产品状态的标识; 对不合格品进行登记、隔离并采取措施; 对采取措施的结果进行验证; 异常信息反馈. 2 、主要内容: 产品; 标识; 包装.
6
2000版ISO9000族标准中,对质量策划的定义是: “质量管理的一部分,致力于设定质量目标并规定必要 的作业过程和相关资源以实现其质量目标.”
注:编制质量计划可以是质量策划的一部分.
7
可以看出: 1 、新标准明确了“质量策划”的范畴; 例如:对合同要求复杂的产品,为满足合同的质
量要求,组织需根据现有的设计、制造能力,提出 生产技术组织措施计划(包括引进设备和技术、工 艺攻关、设备改造、人员培训等),为此开展的一 系列筹划和组织活动,都属于“质量策划”的范畴。
11
2.抽样检验适用于: 检验是破坏性的; 被检对象是连续批
质量员岗位知识与专业技能知识教材

质量员岗位知识与专业技能知识教材质量员是企业中重要的职业之一,在企业中承担着保证产品质量、改善生产工艺、提升企业竞争力的重要责任。
因此,质量员需要掌握一系列的专业技能和岗位知识,以便能够更好地履行自己的职责。
针对这一需求,有必要开发一本质量员岗位知识与专业技能知识教材。
一、质量员岗位知识1. 质量管理体系:了解ISO9001等体系要求、企业品质管理的方法和流程、各种工具和技术,掌握制定和实施质量管理手册和程序的方法和步骤。
2. 质量控制:了解如何根据产品的特性、使用目的和市场需求制定和执行检测、测试、优化和改进工作。
3. 质量保证:掌握如何制定和执行验证、调试、文档化和程序化的过程、方法和流程,以保证产品的质量。
4. 客户满意度管理:了解如何识别和满足客户的需求、期望、反馈和抱怨,掌握周期性的评价和改进技术和方法,以增强客户的满意度。
5. 管理质量成本:了解如何将制造、检测、质量保证等方面的成本与产品的质量发生关系的情况进行了解和掌握,并针对各项成本进行调整。
6. 供货方管理:了解如何与外部供货方进行有效的交流和合作,建立起信任和合作的关系,以便于保证供货方的品质质量。
二、质量员专业技能知识1. 统计过程控制(SPC):了解如何针对产品或者服务的特性,运用SPC技术进行生产过程的控制,确保生产的一致性和精度。
2. 六西格玛(Six Sigma)质量管理:了解如何运用六西格玛质量管理方法分析、改进和控制生产流程,以质量达到改善、稳健、优化的水平。
3. 设计质量工具:了解如何根据顾客要求,运用设计工具制定需要的产品或产业解决方案,以满足顾客的需求。
4. 战略质量规划(QSP):了解如何将质量规划作为企业的重要策略之一,并将其与企业的业务战略结合起来,以进一步提升企业的竞争力。
5. 制造过程工程(MPE):了解如何将MPE技术应用于制造过程,以创建和管理制造流程,提高产品质量和生产效率。
6. 整体质量管理(TQM):掌握如何运用整体质量管理的理论和方法,使之成为企业文化中的一部分,以实现企业质量的整体提升。
《QC-F》培训教材
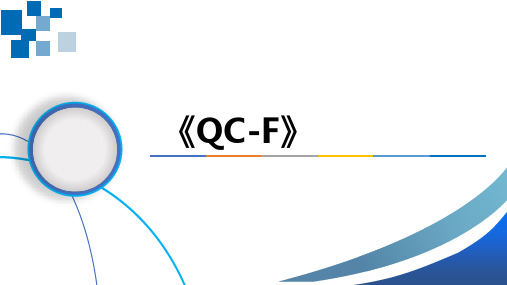
问题原因的 深度
眼睛里面进入脏东西、患眼疾的人增多 吹春风
真正的原因对策
(Statistical Quality 用KKD(经验、直觉、 胆量)可以提出解 决方法
用KKD直接解决不了
× 的部分,因为不能明 确真正原因而导致不 断累积 ↓ 不能反映到源流
QC-F基 础课程
工人
1、理解和掌握作业标准书的要求,并按要求操作 2、掌握问题改善方法-QC工具
QC-J
学习在质量领域 业务推进中必要 的专业手法和思 考方式,并运用 到实际工作中
学习在生产现场 所需要的质量管 理手法,并运用 到日常工作中
理解按标准作业 的重要性,在作 业中落实“三不 原则”,发现异 常能准确报告
《QC-F》
·QC课程体系
岗位 厂部长
品质管理能力要求
课程设置
课程目的
1、规划公司整体质量管理体系 2、制定公司质量领域中长期规划和年度事业计划 3、主导跨部门跨领域复合品质问题的解决
QC-F高 级课程
培养能够全面推 进质量管理活动 的专家
课程目标
1、能对工厂的工序保证能力进行系统的评价,并通 过实践大幅度提高工厂的工序品质保证能力 2、熟练运用QC工具解决工厂的重大质量课题
全员
三个阶段之间既有区别又有联系,每一个新阶段都是在前一阶段的基础上发展起来的,是吸收了前一阶 段的精华,弥补了不足之处而逐步形成的,因此,仍然保留着前阶段行之有效的方法。
10
1.1 质量管理和TQM
品质不仅仅指产品的品质,也要考虑服务、工作的品质,对其品质进行管理也属于品质管理。
全面质量管理(Total Quality Management:TQM)的定义
品质检验员培训教材ppt课件

B
1.2
1
L(P)
0.8
0.6
系列1
OC曲线
0.4
0.2
0 0 0.005 0.01 0.02 0.03 0.04 0.05 P%
AQL
LQ
曲线位置随n,Ac的变化 而变化
方案越严,曲线越往下移。
精选PPT课件
18
两种风险:
1,生产方风险是指生产方所承担的不接收 质量合格批的风险。
2,使用方风险是指使用方所承担的接收质 量不合格批的风险。
随机抽样—使构成总体的每一个个体都以同等概率出现在 样本中。
随机抽样也可以在生产流程中进行。
精选PPT课件
25
5.随机抽样方法
1、简单随机抽样 常用的简单工具:
◦ 随机数表法(乱数表法)
◦ 掷骰法(适用于生产现场) 2、周期系统抽样
当对总体实行上述单纯随机抽样有困难时(如连续作业时抽样或产品为连 续体时抽样),可采用一定间隔进行抽取的抽样方法。 3、分层抽样 从一个可以分成不同子批(或称作层)的检验批中,按规定的比例从不同 的层中抽取样本。
精选PPT课件
23
3,若N=2000,AQL=1.5(%)不合格品,检验 水平为Ⅱ,求二次正常抽样方案
4,设产品批量N=100,规定AQL=10(%),并 采用检验水平S-4,要求给出二次正常,加 严,放宽抽样方案.
精选PPT课件
24
4.如何抽取样本?
人工挑选取样法—由于有人的主观因素在起作用,不能正 确反映整批产品的实际分布状态;
精选PPT课件
8
质量检验的几种形式
一,查原始质量凭证 二,实物检验 三,派员驻厂验收
精选PPT课件
9
公司技术质量部培训计划

公司技术质量部培训计划一、培训目的技术质量部是公司质量管理体系的重要部分,其主要职责是负责产品质量管理、生产过程控制、技术支持等工作。
为了提升技术质量部门的整体素质,提高员工的专业水平和工作效率,公司特制定了此次培训计划。
二、培训对象技术质量部全体员工。
三、培训内容1. 质量管理体系知识培训2. 产品质量管理和质量控制技术3. 生产过程控制技术4. 数据分析与质量改进方法5. 技术支持知识和技能培训四、培训方式1. 理论知识讲解2. 案例分析与讨论3. 培训实践操作五、培训时间本次培训计划为期一个月,每周安排两次培训,每次培训时间为2小时。
六、培训教材1. 《ISO质量管理体系标准解读》2. 《产品质量管理与控制技术》3. 《生产过程控制与改进方法》4. 《数据分析与质量改进方法》5. 《技术支持与售后服务技能培训手册》七、培训考核1. 知识测试2. 实际操作考核八、培训后续跟踪1. 定期组织复习2. 每季度开展一次质量管理知识竞赛3. 定期组织技术经验交流会议九、评估与总结1. 培训结束后,将对员工进行综合评估,评定培训效果。
2. 将总结本次培训的经验和不足,及时调整并完善今后的培训计划。
十、预期成果通过本次培训,技术质量部员工将具备以下能力和素质:1. 具备扎实的质量管理体系知识;2. 掌握有效的产品质量管理和质量控制技术;3. 熟悉生产过程控制技术,能有效提高生产效率和产品质量;4. 具备数据分析和质量改进的能力;5. 提升技术支持水平,提高客户满意度。
十一、意见和建议技术质量部培训计划制定是为了提高员工的综合素质和业务水平,同时也为公司的发展和创新提供了坚实的保障。
希望各位员工能够认真参加培训,主动学习,将所学知识应用到实际工作中,取得更好的成绩。
同时也欢迎大家对培训计划提出宝贵的意见和建议,共同推动公司的发展和进步。
- 1、下载文档前请自行甄别文档内容的完整性,平台不提供额外的编辑、内容补充、找答案等附加服务。
- 2、"仅部分预览"的文档,不可在线预览部分如存在完整性等问题,可反馈申请退款(可完整预览的文档不适用该条件!)。
- 3、如文档侵犯您的权益,请联系客服反馈,我们会尽快为您处理(人工客服工作时间:9:00-18:30)。
内容:一、质量管理发展过程二、质量检验基础知识三、质量管理体系四、统计技术基础五、自方图及应用六、过程能力调查七、抽样检验标准及应用八、检验误差及数据处理(数据修约)第一讲:质量管理发展过程简介质量管理是在质量检验的基础上发展起来的,质量检验有随着质量管理的发展而发展,到目前为止发展成三个阶段,即从最初的创传统质量检验阶段,到统计质量控制阶段,最后发展为全面质量管理阶段。
一、传统质量检验阶段单纯靠检验或检查来保证产品或工作质量;是事后把关而非事先预防,是不经济的质量管理;经历了操作者检验、工长检验、专职检验三个小阶段。
二、统计质量控制阶段通过应用数理统计(统计抽样和控制图),捕捉生产过程中的异常先兆(苗头),经过分析找出异常原因并消除异常,使生产过程的各个环节处于正常生产状态;统计抽样必须在经过过程统计控制,保证过程处于稳定受控状态下进行;是事先的预防、控制;但忽略了产品质量在设计阶段、生产制造阶段、售后服务阶段各个环节的作用,以及质量体系的作用;三、全面质量管理阶段全面质量管理强调“三全”管理,即全员参与、全过程质量管理、全企业(全面)质量管理;由管结果转化为管因素。
第二讲检验的基础知识一、在ISO9000标准中检验的定义为,通过观察和判定,适当时结合测量、试验所进行的符合性评价。
因此检验人员的主要工作内容时对产品进行符合性评价。
二、对质检员的要求及工作内容1、要求熟悉标准目前在实施的标准有技术标准、管理标准、工作标准,其中要求大家熟悉的标准为技术标准,包括产品标准(有国家的、行业的、企业的及技术协议),检验标准、分析方法标准。
对标准中与产品要求密切相关条款要求做到应知应会。
2、测量——采用仪器工具对产品的一项或多项特性进行定量的测量、检查、试验或度量。
要求应知应会知识:了解设备的使用方法/性能;了解设备的检定状态;了解抽样方案;抽样;样品存储保护;样品制作;检测。
3、比较——与调令要求、标准/协议要求比较;4、判定分为符合性判定和适用性判定符合性判定是根据比较的结果,进行合格与否的判定,符合性判定是质检部门质检人员的职责;适用性判定是对经过符合性判定为不合格的产品或原辅材料进一步确认能否适用的判断。
原辅材料的适用性判断是技术部门的职能;最终产品的适用性判断只能有顾客判断,经顾客作出适用性判断的产品加以特殊标识并定向销售。
5、处理合格品——入库/投入下一道工序/出厂;不合格品——严格按照不合格品控制程序进行评审处置;对不合格品进行标识隔离处理,防止不合格品混入合格品中流入下一道工序或出厂6、记录、标识、出具检验报告等三、质检职能发挥1、鉴别职能2、把关职能使不合格原料不投产;不合格半成品不转序;不合格成品不出厂。
3、预防职能通过检验获取大量数据信息,为质量控制及异常因素分析提供依据,对过程异常因素进行加以控制,实现预防为主的方针。
4、报告职能形成质量月报、周报、季报5、监督职能监督职能包括产品质量监督和工艺技术监督。
四、检验的分类1、按生产过程的顺序分类进货检验;过程检验;最终检验;最终检验也叫成品检验,是成品入库前的一次,是比较重要的一个检验关口,一般要求对产品进行全面检验,对质检员的素质要求也较高。
对首次检验不合格经返工、返修后的产品必须再次进行全面检验,质检员要做好放工、返修产品的检验记录,保证产品质量具有可追溯性。
2. 按检验方法分有理化检验;感官检验;实验性使用鉴别;前两者是我们常用的检验方法。
3. 按被检产品的数量分有全数检验;抽样检验;免检。
目前铝箔产品基本上进行全数检验,圆片、风管、餐盒、纸品等将进行抽样检验。
4.按质量特性的数据性质分有计量值检验;计数值检验。
目前我们主要采用计量值检验。
5. 按检验后样品的状态分有破坏性检验和非破坏性检验;目前两者都有。
如进行尺寸方面的检验为非破坏性检验,进行力学性能、腐蚀试验为破坏性检验。
6. 按供需关系分有第一方(供方)检验;第二方(需方/顾客)检验;第三方(检验机构)检验。
7. 按检验人员分 有自检、互检、专检 8.按检验效果分有判定性检验;信息性检验;寻因性检验 第三讲、质量管理体系与检验工作相关的ISO9001标准条款 4.2.4 记录的控制 质检职责 7.4.3采购产品验证 质检职责 7.5.3标识和可追溯性 7.5.5产品防护监视和测量装置的检测8.2.4 产品的监视和测量 (质检的主要职责) 不合格品控制 (质检的主要职责) 改进第四讲、统计技术基础一、 质量数据统计的观念从长期的统计观点看待质量,质量有两个观念 1. 质量具有变异性(不均匀性)2. 质量变异具有规律性(质量数据分布具有规律,如正态分布等) 二、 数据的种类质量数据按数据性质的不同,对量化的数字数据可分为计量值数据和计数值数据。
计量值数据可在一个区域内连续取值,可取无穷多个数据,如长度、面积、重量等;计量值数据服从正态分布。
计数值数据在一定区域内只能取有限个数值,计数值根据计数对象不同可分为计件值数据和记点值数据,计件值数据如不合格品件数;产品件数;记点值数据如针孔数,印痕数等;计件值数据服从二项分布;记点值数据服从泊松分布。
三、 数据特征性1. 平均数、中位数——反映的是数据的集中位置(集中趋势)公式:平均值:nXX ni i∑==1中位数:X ~值取值原则将一组数据由大到小进行排序,排序后,当数字个数为奇数时,中位数X~取排列数组的中间一个,当数字个数为偶数时,中位数X ~取中间的两个数字的平均值。
2. 极差(R )、方差(2S )、标准差(S)——反映数据的离散程度(差异大小)公式:R=Xmax-Xmin()()1/22--=∑n X X S i()()∑--=1/2n X XS i=()1/22--∑∑n nXi X i例子1:某零件尺寸要求,Φ20±,现在从该批零件尺寸检测数据中随机收集10个数据(实际生产中至少需要20个数据,数据如下表1,请判断该批零件尺寸目前的控制水平。
令Yi=(Xi-20)*10经整理如上表 得 n=10,∑=4y ,1122=∑Y ,求y 和Syy =4.010/4==∑ny ()()∑--=1/2n X X Sy i=()1/22--∑∑n nXi X i=()1/22--∑∑n nYi Y i=91016112-=还原求x 和Sx04.202010/4.02010/=+=+=y xSx=35.0101=Sy 过程能力Cpk 值判定Cpk=476.035.0*60.16min max 6==-=S T T S T <查过程能力评价表2,过程能力控制水平处于非常不足状态, 应采取紧急措施,例子2计算:10,14,13,12,10,11,12,11,12,13的平均值,中位数,极差,标准差值。
由大到小排序:10,10,11,11,12,12,12,13,13,14令Y=X-12,经整理,n=10 ,∑Y=-2, 162=∑Y ,0~=Y ,2.0-==∑nY Y 1212~~=+=Y X , 8.1112=+=Y X , ()422min max =--=-=Y Y R()()32.194.016122=-=-+=∑∑n nY Y S第五讲 直方图见教材(略)第六讲 过程能力 一、过程能力过程:是一组将输入转化为输出的相互关联或作用的活动。
过程能力:指将过程在正常状态下,加工产品质量能够满足技术质量标准的能力。
过程能力记为:B=6б=6S 二、过程能力指数Cp过程能力指数:是指过程能力满足质量要求的程度。
符号为:Cp 。
Cp=S Tl Tu Tl Tu B T 66-=-=δ 三、Cp 值计算1. 当控制指标为双侧控制指标时(即同时控制Tu 和Tl ) a .当数据分布中心(即X )与规格中心M 相等时,即X =M则 Cp=ST 6 b .当X ≠M 时,偏离量M X -=ε,偏离系数k=Tε2 则 Cpk=ST 62ε- 2. 当控制指标为单侧时a. 当控制指标为Tl 时(Tl 为控制下限)则 Cpl=STlX 3- b. 当控制指标为Tu 时(Tu 为控制上限)则 Cpu=SXTu 3- 3. 例子某材料抗拉强度数值要求≥33kg/cm2,先抽取38个样品,测得样品平均值为,标准差S 为.,试问该材料的过程控制水平。
已知:Tl=33,8.37=X ,S=则 Cpl = ()95.068.1*3338.37=-=-S T X L , 抗拉强度应属于重要特性值,Cpl 值偏低,过程控制存在中等风险,需要对过程强化质量检验和严加监控,在采取纠正预防措施提高Cp 值。
四、利用Cp 、Cpu 和Cpl 估计不合格品率1. 当控制指标为双侧控制指标时(即同时控制Tu 和Tl ) a .当数据分布中心(即X )与规格中心M 相等时,即X =M则 总不合格率:P=2ф(-3Cp )b .当X ≠M 时,偏离量M X -=ε,偏离系数k=Tε2 则 总不合格率:P=ф[]Cp k )1(3--+ф[]Cp k )1(3+-2. 当控制指标为单侧时 a. 已知Cpl则 总不合格率:P=ф(-3Cpl )b. 已知Cpu则 总不合格率:P=ф(-3Cpu )如上述例子材料抗拉强度值的过程能力指数Cpl=,则可能出现的不合格品率P=ф(-3Cpl )=ф(-3*)=ф() 查正态分布表得 P==%上述计算结果出来后,可以通过查询正态分布表得出总不合格品率。
四、 过程能力指数评价第七讲 抽样检验标准及应用 参见(GB/)第八讲 检验误差及数据处理(数据修约) 一、四舍六入原则 4要舍,6要入,5后有数进一位,5后无数看奇偶, 5前为奇进一位,5前为偶全舍掉。
例: 将以下数据保留至四位有效数字 → → → → →负数修约,先将其绝对值按上述原则进行修约,再在修约后的数值前加上“-”二、不允许连续修约1. 不允许对数据连续修约,如下列为不正确的做法: →→→→2. 在实际生产中,为了避免连续修约,对修约后报出的数值,最右非零的数字为5时,应在数值的右上角加“+”或“-”或不加符号,分别表明已进行过舍,进或未舍未进。
例如 +50.16表示实际值大于,经过修约后舍弃为;-50.16表示表示实际值小于,经过修约后进一为。
3.若对报出的数值仍需要修约时,当拟舍弃数字的最左一位数字为5,切其后无数字或皆为零时,数值右上角有“+”者进一,有”-“者舍去,其他按四舍六入原则进行。
1. 0.5单位修约定义:按指定修约的间隔对拟修约的单位修约。
方法:将拟修约值X乘以2,按指定修约间隔对2X依据四舍六入原则修约,所得的值(2X修约值)再除以2。
例如1:将下列数据修约到“个”数位的单位修约(即修约后的数字必须是的单2. 0.2单位修约定义:按指定修约的间隔对拟修约的单位修约。