[VIP专享]航天炉工艺及主要设备参数
气化炉型-航天炉
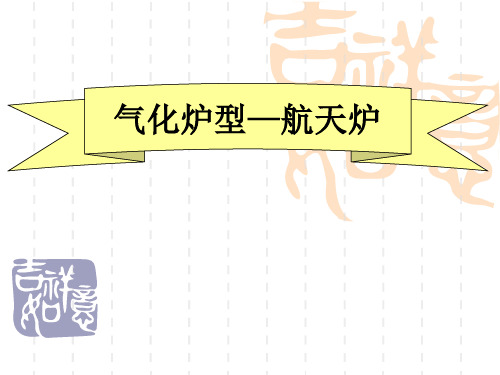
电机功率 kW 5.5~22 22~55 160~315
首批 使用 年代 1988 1991 1993
四、特点
航天炉的优点 1、具有较高的热效率(可 达95%)和碳转化率(可达 99%); 2、气化炉为水冷壁结构,能承受1500℃至1700℃的高温; 3、对煤种要求低,可实现原料的本地化; 4、拥有完全自主知识产权,专利费用低,关键设备已经全 部国产化,投资少,生产成本低。据专家测算,应用航天 炉建设年处理原煤25万吨的气化工业装置,一次性投资可 比壳牌气化炉少3亿元,比德士古气化炉少5440万元;每 年的运行和维修费用比壳牌气化炉少2500万元,比德士古 气化炉少500万元。 它与壳牌、德士古等国际同类装置相比,有三大优势: 一是投资少,比同等规模投资节省三分之一; 二是工期短,比壳牌炉建设时间缩短三分之一; 三是操作程序简便,适应中国煤化工产业的实际,易于大面 积推广。
状态 固 气体 气体 气体 气体 气体
关键设备
破渣机
序号 1 2 3 4 5 6 7 8 9 10 使用单位 上海焦化厂 浩良河化肥厂 德州化肥厂 金陵化肥厂 南京大化 上海惠生 湖北双环 柳州化工 云天化 云占化 数量(台) 1 2+1 2+3 3 1+1 3 1 1 1 1 应用时间 94.12 04.4 04.10 04.10交货 05.2交货 05.3订货 04.3交货 05.3交货 05.4订货 05.5订货 备注 德士古 德士古 德士古 德士古 德士古 德士古 壳牌 壳牌 壳牌 壳牌
二、工艺介绍
HT-L粉煤气化技术工艺原理为原料煤经过磨煤、干燥后, 用N2进行加压输送,将粉煤输送到气化炉烧嘴。干煤粉 (80℃)、纯氧气(200℃)、过热蒸汽(420℃)一同 进入气化炉气化室,瞬间发生升温、挥发分裂解、燃烧及 氧化还原等物理和化学过程。生成的1400℃~1600℃的 合成气经过冷却后,出气化炉的温度为210℃~220℃, 再经过文丘里洗涤器增湿、洗涤,和洗涤塔进一步降温、 洗涤,产出温度约为204℃、粉尘含量小于10×10-6的粗 合成气。
航天炉粉煤加压气化技术分析

航天炉粉煤加压气化技术分析摘要:本文主要介绍了航天炉粉煤加压气化技术的工艺原理、技术特点及控制技术,以供参考。
关键词:航天炉;技术特点;结构一、航天炉煤气化的工艺原理原料煤经过磨煤、干燥后储存在低压粉煤储罐,然后用N2(正常生产后用CO2输送)通过粉煤锁斗加压、粉煤给料罐加压输送,将粉煤输送到气化炉烧嘴。
干煤粉(80℃)、纯氧气(200℃)、过热蒸汽(420℃)一同通过烧嘴进入气化炉气化室,瞬间发生升温、挥发分裂解、燃烧及氧化还原等物理和化学过程(1—10 s)。
该反应系统中的放热和吸热的平衡是自动调节的,既有气相间反应,又有气固相间的反应。
1400—1600℃的合成气出气化室通过激冷环、下降管被激冷水激冷冷却后,进入激冷室水浴洗涤、冷却,出气化炉的温度为210~220℃,然后经过文丘里洗涤器增湿、洗涤,进入洗涤塔进一步降温、洗涤,温度约为204℃、粉尘含量小于10×10-6的粗合成气送到变换、净化工段。
[1]二、航天炉的主要设备1、气化炉HT—L炉的核心设备是气化炉。
HT—L炉分上下两个部分:上部是气化室,由内筒和外筒组成,包括盘管式水冷壁、环行空间和承压外壳。
盘管式水冷壁的内侧向火面焊有许多抓钉,抓钉上涂抹一层耐火涂层,其作用是保护水冷壁盘管、减少气化炉热鼍损失。
盘管式水冷壁的结构简单,材质为碳钢,易制作且造价较低。
水冷壁盘管内的水采用强制密闭循环,在这循环系统内,有一个废热锅炉生产5.4MPa(G)的中压蒸汽,将热量迅速移走,使水冷壁盘管内水温始终保持一恒定的范围。
下部为激冷室,包括激冷环、下降管、破泡条和承压外壳。
激冷室为一承压空壳,外径和气化室一样,上部和水冷壁相连的为激冷环,高温合成气经过激冷环和下降管煤气温度骤降。
向下进入激冷室,激冷室下部为一锥形,内充满水,熔渣遇冷固化成颗粒落入水中,顺锁斗循环水排入灰锁斗。
粗合成气从激冷室上部引出。
2、烧嘴HT—L炉烧嘴是一个组合烧嘴,由一个主烧嘴、一个点火烧嘴和一个开工烧嘴组成。
气化炉型-航天炉教材
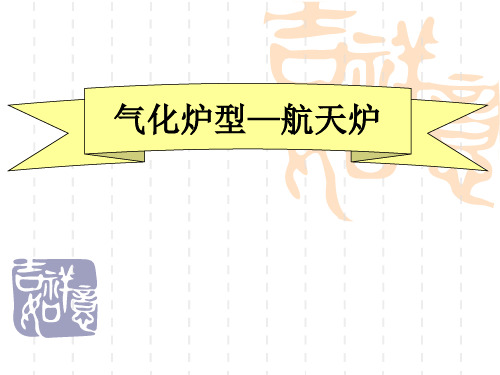
04年
04年 04年 04年 04年 04年
4台
4台 4台 4台 4台 4台
目前正在为下列用户:陕西神木甲醇厂、南京化学工业公司化肥厂、上海焦化总厂 生产黑水调节阀产品,其中南化公司化肥厂的阀门最高单级压降达8MPa,阀体及内件材料为 超级双相钢2507和碳化钨硬质合金。
关键设备
激冷水循环泵
型号
流量 m3/h 20 100 27 220
气化炉的核心部件是气化炉燃烧喷嘴,该喷 嘴必须具有超强的耐高温特性,这个特性要实现 起来难度较大。而与此类似,火箭上天时喷嘴所 经受的温度也很高,而且比气化炉燃烧喷嘴要经 受的温度高得多。如果把航天技术“嫁接”到煤 化工产业,那就有点像杀鸡用上宰牛刀,技术难 度上是没有问题的。 航天长征化学工程股份有限公司(简称“ 航 天工程公司”)前身为北京航天万源煤化工工程 技术有限公司,主营业务是以航天粉煤加压气化 技术为核心,专业从事煤气化技术及关键设备的 研发、工程设计、技术服务、设备成套供应及工 程总承包。航天工程公司目前拥有自主知识产权 的航天(HT-L)粉煤加压气化技术,该技术可广 泛应用于煤制合成氨、煤制甲醇、煤制烯烃、煤 制乙二醇、煤制天然气、煤制油、煤制氢、IGCC 发电等领域。
3、气化及净化 烧嘴设计同GSP,采用单烧嘴顶烧式气化,气化炉采用 TEXACO激冷工艺,气化炉升压到1MPa时,煤粉及氧、蒸汽混合以 一定的氧煤比进入气化炉,稳压1小时挂渣,炉膛内设置有8个温度 检测点,可以作为气化温度的参考点,也可以判断挂渣的状态。设计 气化温度1400-1600℃,气化压力4.0MPa。热的粗煤气和熔渣一起 在气化炉下部被激冷,也由此分离,激冷过程中,激冷水蒸发,煤气 被水蒸汽饱和,出气化炉为199℃ ,经文丘里洗涤器、洗涤塔洗涤后, 194℃、固体含量小于0.2mg/m3的合成气送去变换。 4、渣及灰水处理系统 渣及灰水处理系统的工艺流程、运行原理、控制参数都与TEXACO 工艺相同。渣经破渣机,高压变低压锁斗,排到捞渣机,进行渣水分 离,水回收处理利用;灰水经高压闪蒸、真空闪蒸后到沉降池,清水 作为激冷水回收利用 ,浆水经真空抽滤后制成滤饼。
航天炉工艺流程

航天炉工艺流程下载温馨提示:该文档是我店铺精心编制而成,希望大家下载以后,能够帮助大家解决实际的问题。
文档下载后可定制随意修改,请根据实际需要进行相应的调整和使用,谢谢!Download tips: This document is carefully compiled by theeditor. l hope that after you downloadthem,they can help yousolve practical problems. The document can be customized andmodified afterdownloading,please adjust and use it according toactual needs, thank you!航天炉工艺流程:①原料准备:原煤经过破碎、筛分、干燥,制备成适合气化的粉煤。
②煤粉输送:将制备好的粉煤通过密封的输送系统送入气化炉。
③氧气准备:高压氧气通过空分装置制备并压缩至所需压力。
④气化反应:粉煤与高压氧气、蒸汽在气化炉内混合,在高温高压条件下发生快速部分氧化反应,生成含CO、H2等成分的合成气。
⑤热量回收:气化炉的高温合成气流经热回收系统,如废锅,回收热量产生高压蒸汽,供工厂其他用途。
⑥合成气冷却与洗涤:高温合成气经过急冷、冷却后,进入气体洗涤塔,去除硫化物、氯化物等杂质。
⑦合成气净化:通过变换反应、脱碳、精馏等步骤进一步净化合成气,提高氢气或甲烷的纯度。
⑧产品回收与利用:净化后的合成气可作为合成氨、甲醇、烯烃等化学品的原料,或用作IGCC(整体煤气化联合循环)发电的燃料。
⑨灰渣处理:气化过程中产生的灰渣经冷却、破碎后,根据其性质进行综合利用或安全处置。
《航天炉工艺介绍》课件

2 气体炉的工作原理
利用特定气氛中的化学反应来对材料进行处理。
3 感应炉的工作原理
利用变化磁场诱导电流,使材料加热。
炉子的结构和组成
炉膛结构
通常由耐火材料构成, 以容纳待处理的材料。
加热装置
包括加热元件或火焰等, 用于提供热能。
冷却装置
用于控制炉子内部温度, 防止过热。
3 炉子节能绿色化的方向
探索使用可再生能源和更环保的材料来减少炉子的能耗和排放。
废气处理系统
用于处理炉子排出的废 气,以保护环境。
炉子的工艺参数
1 温度控制
确保炉膛内部达到精确温度要求。
2 气氛控制
控制炉子内的气氛成分,以实现不同的处理效果。
3 压力控制
在某些工艺中,通过调节炉子内外的压力差来实现处理目标。
炉子的使用和维护
1
使用注意事项
正确操作炉子,遵守安全规范,防止事故发生。
航天炉工艺介绍
本课件将介绍航天炉的种类、工作原理、结构与组成,以及工艺参数、使用 维护和未来发展等方面内容。
炉子的种类
真空炉
通过排除气氛,在高温下进行材料处理和烧结。
气体炉
利用特定气氛来进行材料处理和退火。
感应炉
通过感应电流来加热材料,广泛用于金属熔炼和加热处理。
炉子的工作原理
1 真空炉的工作原理
火箭发动机的制造
发动机燃烧室的制造
使用航天炉对燃烧室材料进行高 温处理和焊接。
发动机喷管的制造
利用航天炉的高能热处理技术制 造高效喷管。
发动机整体组装
将制造好的部件组装成完整的火 箭发动机。
炉子的未来发展
1 新型炉子的研究
航天炉煤气化工艺

航天炉煤气化工艺概述航天炉煤气化工艺是一种将煤炭等碳质物质转化为合成气的高效工艺。
它充分利用煤炭资源,通过高温和压力条件下的化学反应,将固体的煤炭转化为气体燃料,用于发电、炼油、化工等领域。
航天炉煤气化工艺由中国航天科技集团公司提出并持续改进,已经取得了重大突破和应用。
工艺流程航天炉煤气化工艺主要包括煤炭预处理、气化反应、气体分离和净化四个步骤。
下面将详细介绍每个步骤的工艺流程。
1. 煤炭预处理在煤炭进入航天炉气化反应器之前,需要进行预处理以提高气化效率和产气质量。
煤炭预处理主要包括粉碎、干燥和除尘等步骤。
首先,将原煤经过粉碎机细碎成适当的粒度,以增加煤炭与气化剂的接触面积。
然后,通过干燥设备将煤炭中的水分蒸发,减少气化过程中的能量损耗。
最后,利用除尘器去除煤炭中的灰分和杂质,以保证气化反应的稳定进行。
2. 气化反应煤炭预处理后,进入航天炉气化反应器进行气化反应。
气化反应是将煤炭中的碳氢化合物在高温(1000℃以上)和高压(10-30兆帕)条件下与氧气和水蒸气发生化学反应,产生合成气的过程。
航天炉气化反应器采用的是间接加热式气化反应器,具有高效和稳定的特点。
通过控制气化反应的温度、压力和气化剂的供应量,可以调整合成气的成分和产气量,满足不同领域的需求。
3. 气体分离在气化反应后,产生的气体混合物需要进行分离,以获取纯净的合成气和其他有用气体。
航天炉煤气化工艺中常用的气体分离技术有压力摩尔分数差异法和吸附分离法。
通过控制压力和温度等参数,可以使合成气和其他气体在分离设备中分离出来,并获得高纯度的合成气。
4. 气体净化在气体分离后,合成气中可能还存在一些杂质和有害物质,需要进行净化处理。
航天炉煤气化工艺中常用的气体净化技术有吸收、吸附和膜分离等。
通过选择合适的吸收剂、吸附剂和膜材料,可以将合成气中的硫化氢、氨、苯酚等物质去除,提高合成气的纯度和品质。
应用领域航天炉煤气化工艺具有广泛的应用领域,主要包括以下几个方面:1. 发电将合成气用作燃料,通过燃烧发电。
气化炉型-航天炉
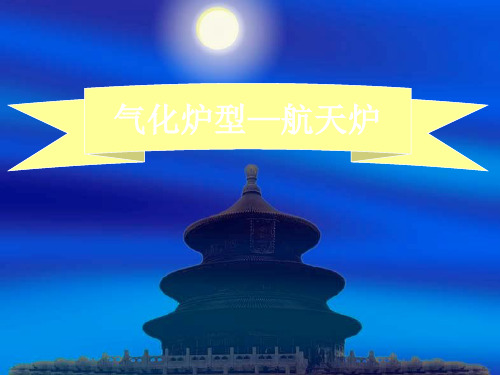
Q-1401/V-1411 捞渣机
T-1401 灰水罐
S-1401 沉降槽
污水
HT-L粉煤气化炉为航天粉煤加压气化装置核心、关键专利设备。粉煤、氧气蒸汽 按一定比例通过燃烧器进入气化炉,在气化室中进行燃烧气化反应,生成的含有高温 熔渣的粗合成气,一部分高温熔渣挂在复合水冷壁上,形成稳定的抵抗高温的渣层, 其余熔渣和粗合成气进入激冷室。粗合成气在激冷室中被激冷水激冷降温,并蒸发水 蒸气到饱和,同时熔渣迅速固化,通过分离装置实现合成气、液态水、固渣的分离。 合成气通过管口输出进入后续工段,主要成分为一氧化碳和氢气。固渣通过排渣口进 入破渣机中,并断续排出。含有细灰的黑水通过管口进入渣水处理系统。
扬程 m 35 130 26 120 80 20 17 47 27 140 21 120 20 140 21 88
入口压力 电机功率 数
bar(G)
kW
量
使用日期/厂家
33
7.5
4 93/鲁南化肥厂
29
75
4
41
7.5
4
04/
41
132
4 浩良河化肥厂
20
18.5
2
98/天津碱厂
67
15
2 97 /渭河化肥厂
№
工程名称
主要技术参数及项目概况
24万吨复合磷 1 肥装置磷铵干
燥机热风炉
24万吨复合磷 2 肥装置磷铵干
燥机热风炉
36万吨复合磷 3 肥装置磷铵干
燥机热风炉
20万吨复合磷 4 肥装置磷铵干
燥机热风炉
15万吨复合磷 5 肥装置磷铵干
燥机热风炉
30万吨复合磷 6 肥装置干燥机
热风炉
【VIP专享】1.航空专用真空炉系列(单晶炉、细晶炉、定向炉)

ZGD-8单晶炉
ZGD-10单晶炉
ZGD-50定向炉照片
1-2真空感应离心铸造/细晶炉系列
主要用途:本设备广泛应用于航空、航天、民用工业精密铸造领域。 主要特点: 1.配置合理的真空系统,具有高抽速之特点。 2.双室结构,即加料测温室,熔炼保温室,结构紧凑合理。 3.具有独特的可升降保温炉加热器,设计新颖。 4.大直径水冷转盘,大功率高性能液压马达驱动。 5.也可根据用户要求定制
50/4000
熔炼温度1600
50
6.67×10-2
保温温度1500
100/4000
ZGZ-50L
熔炼温度1600
50
7×10-2
保温温度1500
100/2500
100/2500
230
6.6×6.3×5.3
PLC
100/2500
280
6.6×6.3×6.0
PLC
100/1000
260
5.6×3.2×3.5
8.0×7.0×10.5
PC+PLC
ZGD-100
100
6.67×10-2
1600
250
160~250
400~500
8.5×8.0×11.5
PC+PLC+触摸屏
ZGD-150
150
6.67×10-2
1600
250
160~250
450~550
9.0×8.5×12
PC+PLC+触摸屏
GXD-150 大型真空感应熔铸炉
1.航空专用真空炉系列
1-1:单晶炉 1-2:定向炉 1-3:细晶炉
1-1真空感应单晶炉、定向炉(HRS法)系列
- 1、下载文档前请自行甄别文档内容的完整性,平台不提供额外的编辑、内容补充、找答案等附加服务。
- 2、"仅部分预览"的文档,不可在线预览部分如存在完整性等问题,可反馈申请退款(可完整预览的文档不适用该条件!)。
- 3、如文档侵犯您的权益,请联系客服反馈,我们会尽快为您处理(人工客服工作时间:9:00-18:30)。
航天炉工艺及主要设备参数介绍1、生产工艺介绍本装置为HT-L粉煤加压气化装置,是由北京航天院设计的示范装置,设计日消耗原料煤约929.64吨,消耗氧气约48.6万立方米。
在4.0MPa条件下通过气化反应,生产CO+ H2为1.22×106Nm3/d,经洗涤后送变换。
HT-L粉煤气化工艺是一种以干煤粉为原料,采用激冷流程生产粗合成气的工艺。
HT-L粉煤气化工艺采用了盘管式水冷壁气化炉,顶喷式单烧嘴,干法进料及湿法除渣,在较高温度(1400~1700℃)及压力(4.0 MPa左右)下,以纯氧及少量蒸汽为气化剂的气化炉中对粉煤进行部分气化,产生以CO、H2为主的湿合成气,经激冷和洗涤后,饱和了水蒸汽并除去细灰的合成气,送入变换系统。
该HT-L粉煤加压气化装置包括1500、1600、17000、1800四个单元:其中1500单元为磨煤单元、1600单元为粉煤加压及输送单元、1700单元为气化及合成气洗涤单元、1800单元为渣及灰水处理单元。
1500单元、1600单元、1700单元、均为双套装置、1800单元为单套装置。
1.1航天炉工艺原理航天炉属于粉煤加压气流床,利用纯氧和少量蒸汽为气化剂,二氧化碳或氮气输送粉煤,有特质的粉煤烧嘴送入高温高压的气化室完成气化反应,生成以CO和H2为主要成分的合成气,气室多余的热量由水冷壁吸收产生中压蒸汽,煤中的灰分形成熔渣,与高温合成气一同进入激冷室进行水激冷后排出气化炉。
1.2气化炉主要结构气化炉主要由气化炉外壳、螺旋盘管和水冷壁和激冷室内件组成,气化炉外壳为三类压力容器,螺旋盘管和水冷壁由气化室主盘管、渣口盘管、炉盖盘管三部分组成,盘管内水循环为强制循环,通过汽包副产中压饱和蒸汽,水冷壁向火侧敷有耐火材料一方面为了减少热损失,另一方面为了挂渣,充分利用渣层的隔热功能,以渣抗渣保护炉壁,气化炉上部为气化段,下部为熔渣激冷段,气化段位圆柱形反应室,激冷段内有激冷环、下降管、上升管和渣池水分离挡板等主要部件。
1.3航天炉主要特点1、干粉进料,煤被磨制成20-100μm粉煤颗粒,并经过热气干燥,惰性气体输送,介质为CO2或N2,加压气化强化燃烧,提高单位体积产气率,与常压炉相比在同样生产能力下航天炉气化强度高、设备尺寸小、结构紧凑、占地面积小、燃烧效率高。
2、一般操作温度为1400-1850℃,煤种适应范围广,对煤的灰熔点要求范围宽,碳转化率99%,有效气CO﹢H2体积比90%左右,CH4气体体积仅有几十至几百PPm3、水冷壁结构为多头并联结构可以保证管程流阻分布均匀,强制循环可以防止局部传热恶化发生爆管故障。
1.4气化炉正常生产时主要测定和控制的参数1.4.1气化煤种的煤质分析,已确定合理的氧煤比等操作条件1.4.2合成气分析,通过分析了解合成气的品质和炉内的反应情况1.4.3灰渣的产量和残炭分析,了解炉内工况和气化效率1.4.4粉煤、氧的温度、压力和消耗情况1.4.5气化炉温度测量、包括炉膛温度,上锥段温度,合成气出口温度,环腔温度,气化炉外壁温度1.4.6渣口压差,判断渣口是否堵渣1.4.7排渣状况,判断炉温和碳转化情况1.4.8激冷室液位,判断激冷室工作状态1.4.9盘管出口水密度,判断炉温及盘管工作状况1.4.9软化水分析包括烧嘴冷却水、盘管冷却水和激冷水,水质的好坏对稳定运行和炉子的寿命有影响。
2.1、磨煤及干燥单元(1500单元)该单元使用常规的煤研磨及干燥,来自原料煤贮仓的碎煤在磨煤机内磨成煤粉,并由高温惰性气流烘干。
粉煤的颗粒尺寸分布规格和粉煤的水分含量要满足以下要求:颗料尺寸≤90μm占90%(重量)颗料尺寸≤ 5 μm占10%(重量)水分含量典型值<2%(wt)2.1.1、任务磨煤及干燥单元的任务是将输煤单元送来的原料煤,经过磨煤机研磨、热惰性气体干燥、在粉煤袋式过滤器内进行风粉分离等工序加工,生产出充足而合格的煤粉输送到1600单元,同时尽可能的降低各项消耗。
2.1.2、工艺流程本单元主要是将从贮存和运输系统送来的粒度小于30mm的原料煤,每小时60T的负荷贮存在原料煤贮仓中,运输系统间断运行,原料煤贮仓中的煤量少时,通知煤场启动运输系统开始输煤,原料煤贮仓的重量高时,通知煤场停运运输系统。
原料煤再经过本单元的加工处理,每小时生产出38.735T、106℃的粉煤送到1600单元,贮存在粉煤贮罐中。
在磨煤的过程中产生少量的废料送渣场。
来自原料煤贮仓的碎煤经振动料斗、称重给煤机计量以46.48t/h(根据生产负荷进行调整)的量送入到磨煤机中,被轧辊在研磨台上将原煤磨成粉状,并由来自惰性气体发生器(56000Nm³/h、260℃)的高温惰性气体进入磨煤机进行干燥和输送,出磨煤机的温度为104~110℃。
由惰性气体输送干燥的粉煤进入粉煤袋式过滤器进行风粉分离后,每小时约38.735T、104~110℃的粉煤经旋转卸料阀、粉煤振动筛、粉煤螺旋输送机送至1600单元的粉煤贮罐中;分离出的惰性气体部分排放至大气,剩余部分经循环风机进入惰性气体发生器循环使用。
惰性气体发生器的燃料气正常情况下来自合成驰放气(燃料气0.3~0.5MPa)与助燃空气(由燃烧鼓风机K-1505送入)按一定比例的进行燃烧反应。
2.1.3、本单元主要发生的反应化学变化:驰放气与助燃空气进行燃烧放热反应CH4+2O2=CO2+2H2O+Q 2H2+O2=2H2O+Q物理变化:2.3、气化及合成气洗涤单元(1700单元)2.3.1、任务粉煤分三条煤粉管线进入气化炉的烧嘴。
氧气经预热后先在混合器内按一定的比例与蒸汽混合,然后也进入烧嘴。
煤粉与氧气在炉膛内发生部分氧化反应,生成合成气的主要成分为CO和H2。
在激冷室,合成气被激冷并被饱和,熔渣迅速固化。
出气化炉的合成气再经文丘里洗涤器和合成洗涤塔用水进一步润湿洗涤,炉膛内气化反应的部分热量,通过水冷壁产生中压饱和蒸汽回收热量。
2.3.2、工艺流程由空分生产出的氧气(5.0MPaG、25℃)进入氧气缓冲罐。
氧气由氧气缓冲罐出来先进入氧气预热器E-1709,被中压汽包循环水加热到180℃。
预热后的氧气进入氧气/蒸汽混合器X-1721。
汽包副产的中压饱和蒸汽(5.4MPaG、270℃)先通过蒸汽电加热器E-1701过热至300℃,然后进入蒸汽过滤器S-1703以确保没有铁锈颗粒(>10μm)进入不锈钢的氧气管道中,然后按蒸汽与氧气的比例控制(通常对应于每种煤是固定的比例,一般取H2O/O2:0.5~0.1,根据具体项目和煤种变化)送入氧气/蒸汽混合器进行混合,混合器(4.1MPaG、197℃)去粉煤烧嘴A-1701.从粉煤给料罐下部三个充气锥送出来的粉煤(4.7MPaG、80℃)进入粉煤加料器X-1701A-F,由调节阀17FV-1101/1201/1301控制粉煤质量流量,该阀主要由氧气/煤比例控制(一般为O2/C:0.6~1.0),并参照合成气中的二氧化碳(一般为5.0~16.0V%,干基)或者甲烷(<500ppm)的含量进行调节。
由调节阀17FV-1102/1202/1302控制加入粉煤加料器的二氧化碳(开车时为氮气)(5.1MPaG、100℃)的流量来调节粉煤悬浮速度。
然后悬浮粉煤(4.1MPaG、80℃)去粉煤烧嘴。
在开车和停车时,悬浮粉煤可通过三通阀17XV-1108/1208/1308循环至低压的粉煤贮罐。
粉煤和氧气/蒸汽混合器经粉煤烧嘴喷入气化炉F-1701气化炉中混合,进行部分氧化反应,反应在4.0MPaG、1500℃左右下进行,反应生成合成气,其主要成分为CO、H2、CO2以及少量的H2S、COS、N2、Ar、CH4等。
未反应的呈熔融状态的灰渣与粗合成气一起进入均布激冷水的激冷环,合成气被激冷水冷却并饱和后,向上穿过多层破泡条和旋流板分离器进行汽流分离,分离后的合成气由激冷室上部的合成气出口管线并加入喷淋后,导出去文丘里进一步洗涤;而灰渣被水激冷后沿下降管进入激冷室的水浴中冷却。
熔融状态的灰渣经过冷却固化,落入激冷室底部,经破渣机H-1701破碎除去大块渣后排入渣锁斗V-1703.激冷水进入下降管顶部的激冷环之后,一部分喷入高温气体,一部分均匀在下降管壁面先下流进激冷室,激冷室中的激冷水含有少量固体,在流量的控制下排出送到黑水处理系统的高压闪蒸罐对热量进行回收,并对水循环系统的固体含量进行控制。
粉煤烧嘴通过在其水夹套中通入冷却水来进行降温保护。
粉煤烧嘴冷却水(4.5MPaG、150℃)流入烧嘴,出烧嘴时温度升高(4.0MPaG、155℃),送至烧嘴冷却水泵P-1702加压,经烧嘴冷却水过滤器S-1702过滤、循环进入粉煤烧嘴。
烧嘴冷却水的补充为锅炉给水,其先经锅炉给水过滤器S-1704进入烧嘴冷却水缓冲罐V-1707,利用控制缓冲罐中水面上的压力,自动将锅炉给水补充至烧嘴冷却水循环系统中。
通过中压锅炉循环水泵P-1701将锅炉循环水加压打入气化炉水冷壁盘管内维持水冷壁盘管内大流量的强制水循环。
管内流动的水吸收炉内气化反应热后部分汽化,流入中压汽包V-1702(3.8~5.0MPaG、269℃)在中压汽包内进行汽液分离,饱和蒸汽送至蒸汽氧气混合器,多余的蒸汽送到厂蒸汽管道,水去循环水泵。
水的补充由锅炉给水总管送来,其流量受中压汽包液位控制。
(正常操作中一定要保证蒸汽的压力高于氧气压力,)开车时,首先点燃点火烧嘴的燃料气和氧气,然后点燃开工烧嘴的燃料气和氧气,对气化炉炉膛进行升温、升压,与此同时,利用开工引射器Z-1703抽出烟气放空,一旦燃烧升温稳定及烟气氧含量<0.5%(超过1分钟)后可将烟气倒向火炬。
气化炉在升温升压阶段待压力升至1.0MPaG,温度达到800℃后,可启动粉煤烧嘴控制程序。
锁斗循环系统的作用主要是将气化后的固体灰渣从激冷室定期排出,以保证气化炉的连续、稳定生产,固体灰渣主要是煤中的灰分高温熔融、冷却后生产的固体。
固体灰渣在激冷室底部,经破渣机(H-1701)破碎,经过两个锁斗阀(17XV-1613/17XV-1602)进入锁斗(V-1703)。
两个锁斗阀中下面一个是锁斗阀为锁斗进口阀(17XV-1602),锁斗收渣期间内,该阀打开,接受激冷室中排入的灰渣,当锁斗排渣时,该阀关闭,从而周期性地将锁斗和气化炉隔开。
固体灰渣除了靠重力排除,还通过锁斗循环泵(P-1704)帮助排渣。
锁斗循环泵从渣锁斗顶部抽水,送回激冷室底部,从而建立了锁斗循环系统。
固体进入锁斗后,大颗粒固体沿锁斗内部折流挡板沉降至锁斗底部。
通常一个锁斗循环周期为25分钟。
锁斗一旦准备排渣,水循环线路中锁斗循环泵进口阀(17XV-1608)关闭,锁斗循环泵循环阀(17XV-1609)打开使锁斗循环泵自循环,关闭锁斗进口阀(17XV-1613),将锁斗与气化炉隔开,然后打开锁斗泄压阀(17XV-1605)由泄压管线向渣池进行泄压,并打开泄压冲洗水阀(17XV-1605)冲洗泄压管线中的固体,当锁斗压力降到0.18MPa以下时,关闭锁斗泄压阀,打开锁斗冲洗水阀(17XV-1604)进行锁斗冲洗。