汽车塑料件设计要求
塑料产品结构设计注意事项
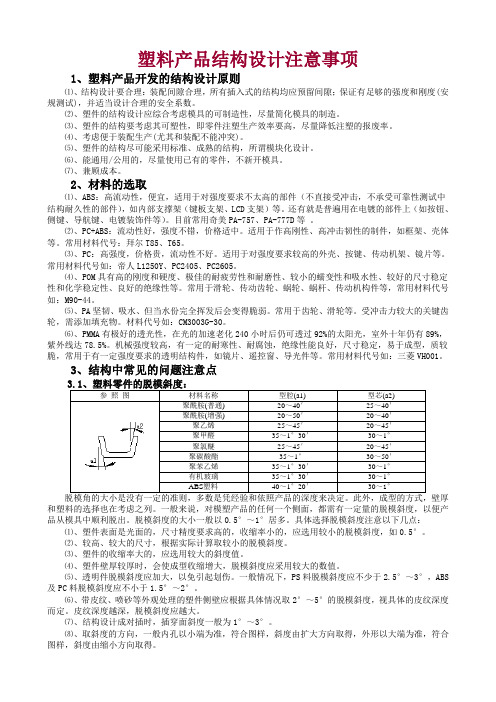
塑料产品结构设计注意事项1、塑料产品开发的结构设计原则⑴、结构设计要合理:装配间隙合理,所有插入式的结构均应预留间隙;保证有足够的强度和刚度(安规测试),并适当设计合理的安全系数。
⑵、塑件的结构设计应综合考虑模具的可制造性,尽量简化模具的制造。
⑶、塑件的结构要考虑其可塑性,即零件注塑生产效率要高,尽量降低注塑的报废率。
⑷、考虑便于装配生产(尤其和装配不能冲突)。
⑸、塑件的结构尽可能采用标准、成熟的结构,所谓模块化设计。
⑹、能通用/公用的,尽量使用已有的零件,不新开模具。
⑺、兼顾成本。
2、材料的选取⑴、ABS:高流动性,便宜,适用于对强度要求不太高的部件(不直接受冲击,不承受可靠性测试中结构耐久性的部件),如内部支撑架(键板支架、LCD支架)等。
还有就是普遍用在电镀的部件上(如按钮、侧键、导航键、电镀装饰件等)。
目前常用奇美PA-757、PA-777D等。
⑵、PC+ABS:流动性好,强度不错,价格适中。
适用于作高刚性、高冲击韧性的制件,如框架、壳体等。
常用材料代号:拜尔T85、T65。
⑶、PC:高强度,价格贵,流动性不好。
适用于对强度要求较高的外壳、按键、传动机架、镜片等。
常用材料代号如:帝人L1250Y、PC2405、PC2605。
⑷、POM具有高的刚度和硬度、极佳的耐疲劳性和耐磨性、较小的蠕变性和吸水性、较好的尺寸稳定性和化学稳定性、良好的绝缘性等。
常用于滑轮、传动齿轮、蜗轮、蜗杆、传动机构件等,常用材料代号如:M90-44。
⑸、PA坚韧、吸水、但当水份完全挥发后会变得脆弱。
常用于齿轮、滑轮等。
受冲击力较大的关键齿轮,需添加填充物。
材料代号如:CM3003G-30。
⑹、PMMA有极好的透光性,在光的加速老化240小时后仍可透过92%的太阳光,室外十年仍有89%,紫外线达78.5%。
机械强度较高,有一定的耐寒性、耐腐蚀,绝缘性能良好,尺寸稳定,易于成型,质较脆,常用于有一定强度要求的透明结构件,如镜片、遥控窗、导光件等。
汽车产品塑料保险杠技术条件
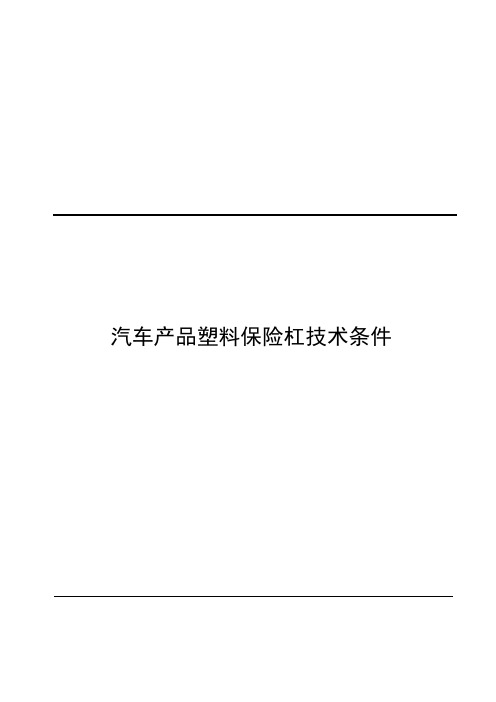
汽车产品塑料保险杠技术条件前 言为满足设计、生产和检验的需要,保证产品质量,制定了本标准。
本标准是参照国内汽车生产企业的先进经验而编制的。
本标准规定了本公司设计开发的汽车改性PP注塑保险杠和SMC模压保险杠的技术要求、试验方法、检验规则、标志、包装、运输和贮存等内容,并对各类汽车产品明确了差别化要求。
汽车产品塑料保险杠技术条件1 范围本标准规定了保险杠的技术要求、试验方法、检验规则、标志、包装、运输和贮存的内容。
本标准适用于本公司设计开发的各类以改性PP注塑塑料和SMC模压工艺生产的汽车用保险杠(以下简称保险杠)。
2 规范性引用文件下列标准所包含的条文,通过在本标准中引用而构成为本标准的条文。
本标准修订时,所示版本均为有效。
所有标准都会被修订,使用本标准的各方应探讨使用下列标准最新版本的可能性。
GB 7258-2012 机动车运行安全技术条件GB 11566-2009 乘用车外部凸出物GB 17354-1998 汽车前、后端保护装置GB 7063-2011 汽车护轮板GB 15741-1995号牌板(架)及其位置GB/T 1033 塑料密度和相对密度试验方法GB/T 1040 塑料拉伸性能试验方法GB/T 1447 纤维增强塑料拉伸性能试验方法GB/T 1449 纤维增强塑料弯曲性能试验方法GB/T 1451 纤维增强塑料简支梁式冲击韧性试验方法GB/T 1462 纤维增强塑料吸水性试验方法GB/T 1463 纤维增强塑料密度和相对密度试验方法GB/T 1634.1 塑料 负荷变形温度的测定 第1部分:通用试验方法GB/T 1764 漆膜厚度测定法GB/T 1843 塑料悬臂梁冲击试验方法GB/T 2828.1 计数抽样检验程序 第1部分:按接收质量限(AQL)检索的逐批检验抽样计划GB/T 6739 色漆和清漆 铅笔法测定漆膜硬度GB/T 9286 色漆和清漆 漆膜的划格试验GB/T 9341 塑料弯曲性能试验方法GB/T 9342 塑料洛氏硬度试验方法GB/T 15568 通用型片状模塑料(SMC)GB/T 16422.2 塑料实验室光源曝晒试验方法 第2部分 氙弧灯GB/T 30512 汽车禁用物质要求QC/T 15—1992 汽车塑料制品通用试验方法QC/T 17—1992 汽车零部件耐候性试验一般规则QC/T 518 汽车用螺纹紧固件紧固扭矩QC/T 625 汽车用涂镀层和化学处理层QC/T 966—2014 汽车塑料件涂层技术条件Q/J B070 汽车塑料件涂漆技术条件Q/J B076—2006 零部件电镀铬层和化学处理层技术条件Q/FD TSA5 001 汽车产品零部件可追溯性标识要求3 技术要求3.1 一般要求保险杠应按经规定程序批准的图样、数学模型及技术文件制造,并应符合本标准的规定;其材料、外形尺寸及安装尺寸符合产品图样和数学模型,保险杠总成必须满足以下强制法规要求。
PP塑料(塑件设计)

PP塑料(塑件设计)简介聚丙烯(PP)塑料是一种常见的塑料材料,具有优异的耐腐蚀性、绝缘性和耐温性。
在塑件设计中,PP塑料常被用于制造各种零部件和产品,广泛应用于汽车、电子器件、医疗设备等领域。
本文将介绍PP塑料的特性、塑件设计的要点以及常用的加工工艺。
PP塑料特性PP塑料具有以下几个显著的特性:1.耐腐蚀性:PP塑料对酸、碱、盐等化学物质具有较好的耐受性,能够在多种腐蚀性环境中稳定工作。
2.绝缘性:PP塑料是优良的绝缘材料,具有很高的击穿电压和绝缘阻抗,适用于电子器件等需要电绝缘的应用。
3.耐温性:PP塑料具有较高的熔点和玻璃化转变温度,可以在较高温度下保持稳定的力学性能。
4.轻质、刚性:PP塑料是一种轻质且刚性良好的材料,可以在满足强度要求的前提下减轻产品的重量。
塑件设计要点在使用PP塑料进行塑件设计时,需要注意以下几个要点:1. 材料选择选择适合的PP塑料材料对于塑件的性能和工艺至关重要。
根据具体的应用场景和要求,可以选择不同级别的PP塑料,如通用级PP、增强级PP以及耐高温级PP等。
2. 强度设计在进行塑件设计时,需要注意强度的设计。
PP塑料具有一定的弹性模量和屈服强度,因此在设计过程中要考虑到受力部位的承载能力,避免出现塑件变形或破裂的情况。
3. 壁厚设计合理的壁厚设计能够提高PP塑件的刚性和强度。
在选择壁厚时,要综合考虑材料的收缩率、成型工艺和产品的使用要求,以保证塑件在使用中不会发生开裂、变形等问题。
4. 几何设计尽量避免尖角和过于复杂的几何结构,在设计过程中注意避免应力集中,以提高PP塑件的使用寿命。
同时,合理的放样和倒角设计有助于提高产品的成型性和外观质量。
5. 模具设计在进行塑件设计时,需要充分考虑到模具的制造和成本。
合理的模具设计能够提高产品的成型效率和质量,降低生产成本。
常用的加工工艺在PP塑件设计中,常用的加工工艺主要有以下几种:1.注塑成型:注塑成型是制造PP塑件最常用的工艺方法。
汽车注塑件(塑料件)设计时需要遵循的14个基本原则

(2)拔模角和高度 通常,筋的拔模角在1-1.5度,最小不能小于0.5度,否则会导致零件脱模困
难。越高的筋顶部往往很薄,导致注塑过程中难以充满也就失去了筋的意义。筋 的顶端厚度一般不低于1毫米,高度一般为零件壁厚的2.5-3倍。当然也会有例外, 需要具体分析。
0.5 deg min 筋厚
Байду номын сангаас
1 min 壁厚
D min D min
塑料件中的柱销也是我们常用到的结构,主要用于提供连接和定位。 • 设计要点:
(1)像筋的设计一样要考虑拔模角度、出模方向、根部厚度与基本壁厚的比 例等。
(2)另外,我们还有一个相互矛盾的问题需要考虑。一方面,我们希望销柱 的厚度(B)尽量薄些,以防止表面出现缩痕。另一方面,我们希望其厚度能厚 一些,以增加结构强度。最终,我们要根据产品结构和材料等综合分析确定。
塑料件翻边结构十分重要,它能够明显提高制件的结构刚度控制变形,是很 有用的结构,我们设计时必须尽量考虑增加翻边结构。 • 设计要点:
(1)翻边的厚度应该与基本壁厚一致。 (2)考虑到零件花纹,我们对翻边的拔模角度有特殊的要求,一般在3-6度之 间。但是不同的花纹会有不同的要求,设计时应根据花纹要求及制造和质量要求 选择适当的拔模角。
P/L P/L
8 有许多种类型的花纹可以用于零件表面的装饰。我们设计时需要针对不同的
花纹选择合适的设计结构。 • 设计要点:
(1)拔模角—总的规则是每增加0.025毫米的花纹深度,需要增加至少1度的拔 模角。关于花纹和拔模角需要设计者和花纹供应商共同检查和确认,并得到 OEM的认可。
(2)翻边—对于翻边结构,花纹和拔模角的关系是最突出的。翻边结构就需 要一定的脱摸角度,以便零件从模具内移出。越长的翻边需要越大的脱模角度, 越深的花纹,也需要越大的脱模角度。如果不注意这点就会产生零件脱模困难, 甚至擦伤零件花纹表面。
Q-FPT 4001005-2012 汽车用聚丙烯材料要求
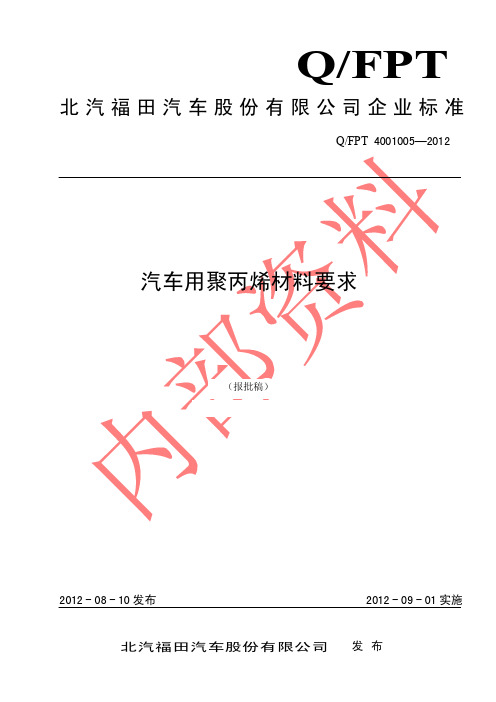
Q/FPT 北汽福田汽车股份有限公司企业标准Q/FPT 4001005—20122012-08-10发布2012-09-01实施前言本标准是根据GB/T 1.1-2009给出的规则起草。
本标准由北汽福田汽车股份有限公司工程研究总院提出并归口。
本标准起草单位:北汽福田汽车股份有限公司工程研究总院分析中心材料工程所。
本标准主要起草人:尚红波、王洪杰。
本标准于2012年9月首次颁布。
本标准由北汽福田汽车股份有限公司工程研究总院分析中心材料工程所负责解释。
汽车用聚丙烯材料要求1 范围本标准规定了汽车用聚丙烯类材料分类、性能要求和检测方法。
本标准适用于一般汽车制品用聚丙烯类材料的性能检验。
2 规范性引用文件下列文件对于本文件的应用是必不可少的。
凡是注日期的引用文件,仅所注日期的版本适用于本文件。
凡是不注日期的引用文件,其最新版本(包括所有的修改单)均适用于本文件。
GB 8410 汽车内饰材料的燃烧特性GB/T 26988 汽车部件可回收利用性标识的规定Q/FT A144 汽车内饰件冷凝组分试验方法Q/FT A146 汽车内饰件甲醛含量试验方法Q/FT A148 汽车内饰件有机物散发试验方法Q/FT A201 汽车内饰材料气味性的测试方法Q/FT B212 常用非金属件的材料标识和标记Q/FT T007 汽车产品禁限用物质检测方法Q/FT T013 汽车产品中禁/限用物质限值要求Q/FPT 4002001 落球冲击测试方法Q/FPT 4002003 内饰塑料件耐刮擦性测试方法Q/FPT 4002004 汽车内部非金属部件及材料氙灯老化试验方法Q/FPT 4005001 汽车外购件概述:首批供货和更改的批准ISO 75-2 塑料负荷变形温度的测定第2部分:塑料、硬橡胶和长纤维增强复合材料ISO 105-A02 织品色牢度试验第A02部分:颜色变化评定用灰度标ISO 178 塑料弯曲性能的测定ISO 180 塑料悬臂梁冲击强度的测定ISO 291 塑料试样状态调节和试验的标准环境ISO 527-2 塑料拉伸性能的测定第2部分:模塑和挤塑料的试验条件ISO 1133 塑料热塑性塑料的熔化质量流速和熔化体积流速的测定ISO 1172 纺织玻璃纤维和矿物添充物含量的测定.煅烧法ISO 1183-1 塑料非泡沫塑料密度的测定第1部分浸渍法、液体比重瓶法和滴定法ISO 2039-1 塑料硬度测定球压痕法ISO 3451-1 灰分的测定第1部分:通用方法SAE J2527 用可控制不发光的水冷氙弧灯进行汽车外饰件的快速暴露试验3 材料分类材料分类见表1。
塑胶件设计准则较全
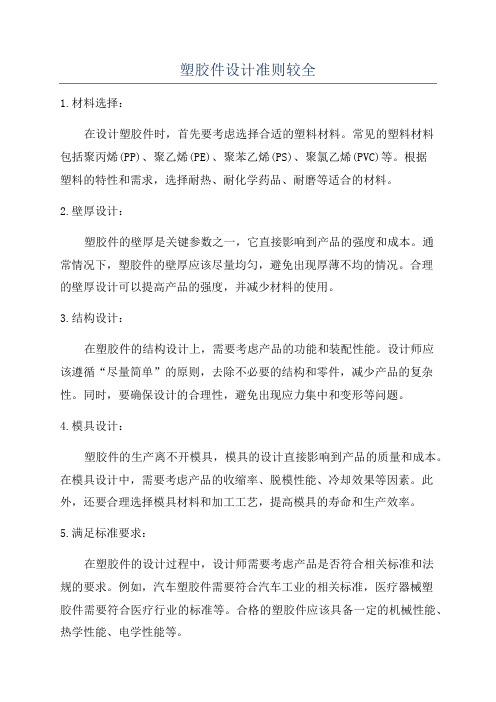
塑胶件设计准则较全1.材料选择:在设计塑胶件时,首先要考虑选择合适的塑料材料。
常见的塑料材料包括聚丙烯(PP)、聚乙烯(PE)、聚苯乙烯(PS)、聚氯乙烯(PVC)等。
根据塑料的特性和需求,选择耐热、耐化学药品、耐磨等适合的材料。
2.壁厚设计:塑胶件的壁厚是关键参数之一,它直接影响到产品的强度和成本。
通常情况下,塑胶件的壁厚应该尽量均匀,避免出现厚薄不均的情况。
合理的壁厚设计可以提高产品的强度,并减少材料的使用。
3.结构设计:在塑胶件的结构设计上,需要考虑产品的功能和装配性能。
设计师应该遵循“尽量简单”的原则,去除不必要的结构和零件,减少产品的复杂性。
同时,要确保设计的合理性,避免出现应力集中和变形等问题。
4.模具设计:塑胶件的生产离不开模具,模具的设计直接影响到产品的质量和成本。
在模具设计中,需要考虑产品的收缩率、脱模性能、冷却效果等因素。
此外,还要合理选择模具材料和加工工艺,提高模具的寿命和生产效率。
5.满足标准要求:在塑胶件的设计过程中,设计师需要考虑产品是否符合相关标准和法规的要求。
例如,汽车塑胶件需要符合汽车工业的相关标准,医疗器械塑胶件需要符合医疗行业的标准等。
合格的塑胶件应该具备一定的机械性能、热学性能、电学性能等。
6.通气设计:塑胶件在注塑过程中需要排除气体,否则会产生气泡和内部缺陷。
因此,在塑胶件的设计中,需要考虑通气的问题。
设计师可以在塑胶件的壁厚较大的地方设置气脱模系统,提高产品的质量。
7.可回收性设计:在现代社会,环保意识日益增强,可回收性成为塑胶件设计的一个重要考虑因素。
设计师应该尽量选择可回收的塑料材料,并设计可分解、可回收利用的产品。
总结起来,塑胶件设计准则涉及到材料选择、壁厚设计、结构设计、模具设计、标准要求、通气设计和可回收性设计等方面。
设计师在进行塑胶件设计时,应根据具体的产品需求和行业要求,合理应用这些准则,确保塑胶件的质量和性能,提高产品的竞争力。
浅谈汽车外饰塑料件设计缺陷
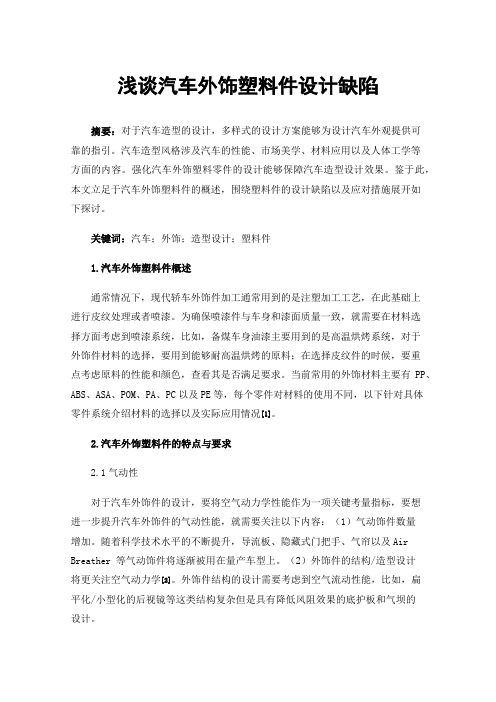
浅谈汽车外饰塑料件设计缺陷摘要:对于汽车造型的设计,多样式的设计方案能够为设计汽车外观提供可靠的指引。
汽车造型风格涉及汽车的性能、市场美学、材料应用以及人体工学等方面的内容。
强化汽车外饰塑料零件的设计能够保障汽车造型设计效果。
鉴于此,本文立足于汽车外饰塑料件的概述,围绕塑料件的设计缺陷以及应对措施展开如下探讨。
关键词:汽车;外饰;造型设计;塑料件1.汽车外饰塑料件概述通常情况下,现代轿车外饰件加工通常用到的是注塑加工工艺,在此基础上进行皮纹处理或者喷漆。
为确保喷漆件与车身和漆面质量一致,就需要在材料选择方面考虑到喷漆系统,比如,备煤车身油漆主要用到的是高温烘烤系统,对于外饰件材料的选择,要用到能够耐高温烘烤的原料;在选择皮纹件的时候,要重点考虑原料的性能和颜色,查看其是否满足要求。
当前常用的外饰材料主要有PP、ABS、ASA、POM、PA、PC以及PE等,每个零件对材料的使用不同,以下针对具体零件系统介绍材料的选择以及实际应用情况[1]。
2.汽车外饰塑料件的特点与要求2.1气动性对于汽车外饰件的设计,要将空气动力学性能作为一项关键考量指标,要想进一步提升汽车外饰件的气动性能,就需要关注以下内容:(1)气动饰件数量增加。
随着科学技术水平的不断提升,导流板、隐藏式门把手、气帘以及Air Breather 等气动饰件将逐渐被用在量产车型上。
(2)外饰件的结构/造型设计将更关注空气动力学[2]。
外饰件结构的设计需要考虑到空气流动性能,比如,扁平化/小型化的后视镜等这类结构复杂但是具有降低风阻效果的底护板和气坝的设计。
2.2装饰性Panoz 与 Feynlab 合作将一种记忆聚合物涂层应用于油漆中,这种材料的使用能够在受热时恢复原始结构,从而将表面划痕除去。
这种涂层通常用来处理漩涡痕迹或者轻微划痕。
车漆自修复技术用到的是一种特殊的涂层保护剂,这种密度较高的透明合成树脂,将其以网状结构涂在汽车油漆外层,能够增强汽车表层抗划伤能力,即便出现划痕,基于超强的网状树脂也能够快速修复划痕。
汽车转向灯手柄本体塑料模具设计说明书

汽车转向灯手柄本体塑料模具设计说明书设计说明书:汽车转向灯手柄本体塑料模具一、项目背景汽车转向灯手柄本体是汽车座舱内重要的控制装置之一,用于操控汽车的转向灯信号。
为了提高生产效率和产品质量,设计并制造一个适用于大规模生产的汽车转向灯手柄本体塑料模具是非常必要的。
二、项目目标设计一款适用于大规模生产的汽车转向灯手柄本体塑料模具,以满足以下要求:1.确保模具制造的工艺精度和质量稳定性;2.提高模具的生产效率和使用寿命;3.设计美观简洁、符合人机工程学的手柄本体。
三、结构设计1.手柄本体整体结构设计1.1 材料选择1.2 外形尺寸规格1.3 结构组成1.4 细节设计要点2.模具结构设计2.1 模具类型选择2.2 模具材料选择2.3 模具零件设计2.4 模具加工工艺四、注塑工艺设计1.注塑设备选择1.1 型腔和型芯的设计 1.2 射嘴和喷嘴的选择1.3 注塑工艺参数设定2.模具试模与调试2.1 初期试模2.2 产品质量检验2.3 二次调试与优化五、模具制造工艺1.模具零件加工1.1 模具零件加工工艺流程 1.2 加工工具和设备选择1.3 加工工艺及加工精度控制2.模具组装与调试2.1 模具组装流程2.2 模具调试与零件拆卸六、质量控制与检验1.模具制造过程质量控制1.1 设计阶段质量控制1.2 零件加工过程质量控制1.3 模具装配过程质量控制2.模具成品质量检验2.1 模具外观检查2.2 尺寸测量2.3 功能测试附件:1.《汽车转向灯手柄本体塑料模具设计图纸》2.《汽车转向灯手柄本体塑料模具零件清单》3.《模具加工工艺参数表》4.《模具装配工艺流程图》法律名词及注释:1.模具:指用于制造产品的工具或设备,包括制造产品所必需的模具以及用于检查、测量或测试产品的设备。
2.塑料模具:用于塑料制品加工的特种工具或设备,能够将熔融的塑料材料注入到特定形状中。
- 1、下载文档前请自行甄别文档内容的完整性,平台不提供额外的编辑、内容补充、找答案等附加服务。
- 2、"仅部分预览"的文档,不可在线预览部分如存在完整性等问题,可反馈申请退款(可完整预览的文档不适用该条件!)。
- 3、如文档侵犯您的权益,请联系客服反馈,我们会尽快为您处理(人工客服工作时间:9:00-18:30)。
二、壁厚均一的设计原则
• 在确定壁厚尺寸时,壁厚均一是一个重要原则。 该原则主要是从工艺角度以及由工艺导致的质量 方面的问题而提出来的。均匀的壁厚可使制件在 成型过程中,熔体流动性均衡,冷却均衡。壁薄 部位在冷却收缩上的差异,会产生一定的收缩应 力,内应力会导致制件在短期之内或经过一个较 长时期之后发生翘曲变形。 • 塑料件最通用料厚是2.5mm,大件适当增加,小件 减小,强烈建议通过增加翻边及加强筋的方式而 不是增加料厚来保证零件强度; PP塑料的壁厚范 围是0.6—3.5mm。
② 受模具活动部分影响的尺寸 b,如图所示,它是 指可活动的模具零件共同作用所构成的尺寸。例 如壁厚和底厚尺寸;受动模零件、定模零件和滑 块共同影响的尺寸。
塑料件连接结构
塑料件的螺钉连接1:
簧片螺母连接,应用于板类零件与塑料件之间的 连接;
板类零件与塑料件之间 大量使用簧片螺母连接
塑料件的螺钉连接2:
②模具
• 对于小尺寸的塑料件,模具的制造误差占塑料公 差的1/3。
• 与模具上运动的零件有关的塑件尺寸,其精度较 低。
• 模具上浇注系统和冷却系统设计不当,会使成型 塑件的收缩不均匀。 • 脱模系统的作用力不当,会使被顶出塑件变形。
③塑件结构
• 塑料件壁厚均匀一致,形体又对称,可使 塑件收缩均衡。提高塑料件的刚性,如加 强筋的合理设置或采用金属嵌件,能减小 塑件翘曲变形,都有利于提高塑件精度。
塑料螺母连接;应用于板类零件与钣金件之间的 连接。(钣金件方孔开口7*7)
板类零件与钣金件 之间大量使用塑料 螺母连接
塑料件的螺钉连接3:
自攻螺钉柱及螺钉沉台的连接;应用于机壳类塑 料件之间的连接;
机壳类塑料件通过自 攻螺钉柱及螺钉 沉台连接
塑料件的弹片夹子连接:
应用于最后安装的需要经常拆装的面板类塑料件 于主体间之间的连接;
汽车塑料产品结 构设计的一般原则及精度
理想的产品简洁化设计基本原则:
(1) 结构简单,形状对称,避免不规则的几 何图形;
(2) 产品侧孔和侧壁内表面的凹凸形状成型 困难,需要在产品成型后进行二次加工, 设计时应避免。
(3) 尺寸设计要考虑成型的可能性,不同的 成型工艺对制件的尺寸设计,包括尺寸大 小,尺寸变化会有一定的限制。
采用加强筋来防止框形结构变形
U 形注塑件由于熔体流动过程中热扩散 不均,引起直角方向上的收缩,因而会 产生如图(a)所示的翘曲变形。解决 这种现象的办法除设加强筋之外也可如 (b)所示,在直角部位开一小槽。
(二)抗热变形设计
• 温度对制件的影响与材料的耐热性直接有 关。 • 当材料确定之后,在产品设计时,应采取 各种有效措施,来减少和避免温度对制品 使用性能的影响,延长产品的使用寿命。
• 前述的避免应力集中以及刚性设计的一些 措施,也都有助于防止或者降低制件的变 形。此外,设计时考虑防止产品变形,在 形状上进行规避。
矩形的薄壁容器的侧壁容易发生内凹变 形,为此可将侧壁设计得稍微外凸一些
深度较浅的盒类制品,为避免翘曲变形, 可将其底边设计成倒角形状
因壁厚不同,壁厚处的塑料完全固化后, 会对先行固化的薄壁部位施以拉力,导 致制件出现变形
(1)厚薄交接处的平稳过渡,当制件厚度不 可避免需设计成不一致时,在厚薄交接处 应逐渐过渡,避免突变,厚度比例变化在 一合适的范围(一般不超过3:1)。
壁厚过渡形式
(2)将尖角改为圆角处理,两个壁厚相同的 壁面成直角的连接,破坏了壁厚均一的原 则。
转角处的最大厚度是壁厚的1.4倍,如果将内角处 理成圆角而外角仍是直角,则在转角处的最大厚 度(W)可增加到壁厚的1.6-1.7 倍。正确的设计 应是内外角均进行圆角处理,以确保壁厚均匀。 圆角处理还可避免应力集中,以及改善塑料成型 时熔体的流动性和成型性。
• 标准规定了模塑收缩率VS,在常温下模塑件与所用 模具相应尺寸的差,同模具相应尺寸之比,以百 分数表示。
• LF……模塑成型后标准环境下放置24h 后的塑料件 尺寸,mm; • LW ……模具的相应尺寸,mm;
• 标准对成型模塑尺寸分成两类: ① 不受模具活动部分影响的尺寸a,如图所示,它 是指在同一动模或定模的零件中成型的尺寸。
(3)嵌件的加强作用
• 在制件中设置金属嵌件,可以提高塑料制件局部 或整体的强度。
如汽车方向盘、活动手柄、塑料门窗框、 带有金属嵌件的塑料齿轮等。
(4)结构上的设计,在产品设计中,有几种 结构具有比较高的刚性/质量比。 ① 蜂窝夹层结构:刚性的设计效果好,缺点 是工艺上比较复杂,成本和价格较高。
• 避免应力集中最直接最有效的方法就是在 拐角、棱边、凹槽灯等轮廓过渡与厚薄交 接处采用圆弧过渡。
根据不同的壁厚和圆角半径对应的应力集中系数, 得出应力集中系数与半径R 与壁厚T之比的关系
图中曲线表明,半径R 与壁厚T之比,即R/T 在 0.6 以后,曲线趋于平缓,由此可知,内圆角之 半径应至少为壁厚的一半,最好为壁厚的0.60.75。
(3)厚壁部位减薄,使厚壁趋于一致,壁厚 差异大的制件可通过增设工艺孔、开槽或 设置加强筋的方式,使厚壁部位减薄,厚 薄趋于一致。
厚壁减薄
开槽
设置加强筋
三、避免应力集中
• 对制件上有孔洞、切口、拐角等几何不连续部位 施加一定的力,在这个部位的断面上将产生远比 给予的表观应力大得多的应力,这个现象称为应 力集中。局部产生的很大应力对于表现应力之比 为应力集中系数。 • 后果:塑料是对缺口和尖角之类比较敏感的材料, 在应力作用下,这些部位会逐渐产生微细裂纹, 随后逐步扩展到大的裂纹,而裂纹的不断延伸终 将导致制件的损坏。
四、加强刚度的设计
材料 加强刚度
几何形状的改变
形状和结 构
加强筋
嵌件的加强作用
(1)几何形状的改变
• 薄壳状的平板制件,将其表面设计成波纹 形、瓦楞形、拱形、球形、抛物面,其刚 性比同样重量的平板要高得多
(2)加强筋的设计和运用
通过加强筋提高轴套扭转刚 性和弯曲刚性
容器沿口部位的设计起到了边缘增强 的作用,实质上这种突变的边缘可以 看作是加强筋的变异。
②结构泡沫:具有致密表皮层和呈微孔结构 的芯部,这种结构具有高的比强度,可应用 在受力结构中。
③口字形结构、T 形结构以及工字梁结构,与 矩形截面的实心结构比较,这种结构既能 节省材料,又不降低刚性。
④圆锥体结构,相对圆柱体结构,这种结构 能承受很大的压缩载荷,弯曲稳定性好。
⑤双壁结构,有不少工艺可成型具有双壁结 构的制件,这种结构的制件有较高的刚性 、冲击韧性和抗弯能力。
主体塑料件上 开装配方孔 弹片夹子卡装在面板 类塑料件上
塑料件的卡扣连接:
1. 卡扣连接是塑料件结构优势之一:结构简单 ,不需要增加零件,制造成本低廉,连接可 靠,装配简易; 2. 缺点:拆卸困难,卡扣损坏后难以修复; 3. 应用与小型塑料件之间的连接;
小型塑料件之 间大量使用 卡扣连接
④工艺
• 注射周期各阶段的温度、压力和时间会影 响塑件的收缩、取向和残余应力,存在对 于塑件精度要求的最佳工艺。保证注塑件 精度更重要的是工艺参数的稳定性。成型 条件波动所造成的误差占塑件公差的1/3。
⑤使用
• 塑料材料对时间、温度、湿度和环境条件 的敏感性,在注射成型制品长期使用后, 会有显现。注塑件的尺寸和形位精度的稳 定性差。
2、模塑塑料件尺寸公差
• 工程塑料模塑塑料件尺寸公差 标准GB/T14486-93 ,模塑尺寸公差代号为MT。பைடு நூலகம்差等级分为七级。
• 该标准规定了热固性和热塑性工程塑料模塑塑料 件的尺寸公差。 • 它适用于注塑、压塑、传递和浇铸成型的工程塑 料模塑的塑料件,不适用于挤塑成型、吹塑成型 、烧结和泡沫制品。 • 此标准只规定公差,基本尺寸的上、下偏差可根 据工程的实际需要分配。
五、抗变形设计
(一)由内应力引起的制件变形
• 这种变形由制件内的内应力所导致。
• 通常不均匀的内应力分布是翘曲变形的主 要原因,而内应力的不均匀分布则可能是 加工条件(如温度、压力的不均匀分布, 收缩率的各向异性等)、材料组成(结晶 型材料的百年形倾向较大)、模具结构( 特别是浇口设计)和制品形状共同作用的 结果。
避免受热部位过热导致变 形的几种设计方案
六、注塑件的精度
1、影响因素
① 材料
• 注塑模塑的塑料在高温高压的熔融状态下充模流 动。常见的各种熔体温度为170-300℃。然后被冷 却固化,通常脱模温度在20-100℃。 • 下表 列出了常用的注射塑料的成型收缩率。 • 用无机填料填充、用玻璃纤维增强的塑料有较低 的成型收缩率。