机电液课程设计
机电液控制系统课程设计
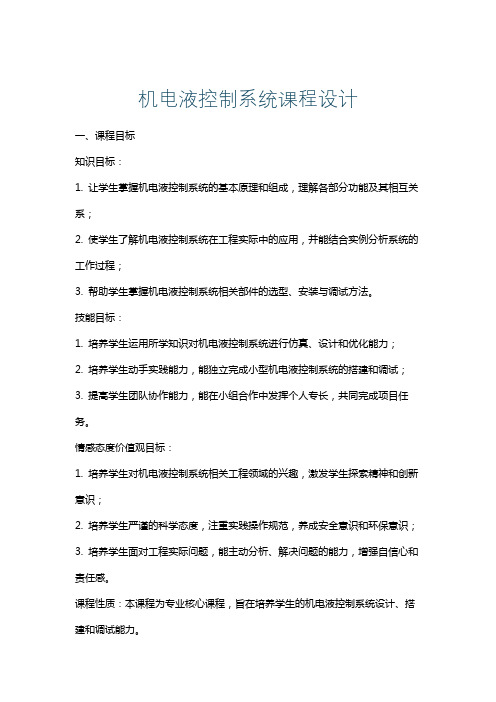
机电液控制系统课程设计一、课程目标知识目标:1. 让学生掌握机电液控制系统的基本原理和组成,理解各部分功能及其相互关系;2. 使学生了解机电液控制系统在工程实际中的应用,并能结合实例分析系统的工作过程;3. 帮助学生掌握机电液控制系统相关部件的选型、安装与调试方法。
技能目标:1. 培养学生运用所学知识对机电液控制系统进行仿真、设计和优化能力;2. 培养学生动手实践能力,能独立完成小型机电液控制系统的搭建和调试;3. 提高学生团队协作能力,能在小组合作中发挥个人专长,共同完成项目任务。
情感态度价值观目标:1. 培养学生对机电液控制系统相关工程领域的兴趣,激发学生探索精神和创新意识;2. 培养学生严谨的科学态度,注重实践操作规范,养成安全意识和环保意识;3. 培养学生面对工程实际问题,能主动分析、解决问题的能力,增强自信心和责任感。
课程性质:本课程为专业核心课程,旨在培养学生的机电液控制系统设计、搭建和调试能力。
学生特点:学生具备一定的机电基础知识和实践技能,具有较强的学习兴趣和探究欲望。
教学要求:结合课本内容,注重理论联系实际,提高学生的实践操作能力和工程素养。
通过课程学习,使学生能够达到上述课程目标,为后续专业课程和未来职业发展打下坚实基础。
二、教学内容1. 机电液控制系统概述:介绍机电液控制系统的基本概念、发展历程、应用领域,使学生建立整体认识。
教材章节:第一章 绪论2. 机电液控制系统组成及原理:讲解各组成部分(电机、执行机构、传感器、控制器等)的工作原理及相互关系。
教材章节:第二章 机电液控制系统组成及原理3. 控制系统数学模型:分析机电液控制系统的数学模型,为学生进行系统分析和设计提供理论基础。
教材章节:第三章 控制系统数学模型4. 机电液控制系统设计与仿真:介绍系统设计方法、仿真软件应用,培养学生设计、仿真和优化能力。
教材章节:第四章 系统设计与仿真5. 机电液控制系统搭建与调试:讲解系统搭建、调试方法及注意事项,提高学生实践操作能力。
机电液课程设计机械手

机电液课程设计机械手一、教学目标本节课的教学目标是让学生掌握机电液课程中机械手的基本原理和设计方法。
具体包括以下三个方面的目标:1.知识目标:使学生了解机械手的工作原理、结构特点和控制方法,理解机电液系统在机械手中的应用,为学生提供扎实的理论基础。
2.技能目标:通过实例分析,培养学生分析和解决实际问题的能力,使学生能够运用所学知识进行机械手的设计和调试。
3.情感态度价值观目标:激发学生对机电液课程的学习兴趣,培养学生的创新意识和团队合作精神,使学生在实际项目中能够充分发挥自己的专业技能。
二、教学内容本节课的教学内容主要包括以下几个部分:1.机械手的基本原理:介绍机械手的工作原理、分类和应用领域,使学生了解机械手在现代工业生产中的重要性。
2.机电液系统在机械手中的应用:讲解机电液系统的工作原理及其在机械手中的具体应用,包括液压系统、电气系统和控制系统等。
3.机械手的设计方法:介绍机械手的设计方法和步骤,引导学生掌握设计要点,培养学生实际操作能力。
4.实例分析:分析具体机械手项目,使学生能够将所学知识应用于实际问题的解决。
三、教学方法为了实现本节课的教学目标,将采用以下教学方法:1.讲授法:讲解基本概念、原理和设计方法,使学生掌握理论知识。
2.案例分析法:分析具体机械手项目,培养学生解决实际问题的能力。
3.实验法:学生进行实验,使学生能够亲身感受机电液系统在机械手中的应用,提高学生的实践操作能力。
4.小组讨论法:分组讨论,培养学生的团队合作精神和沟通能力。
四、教学资源为了保证本节课的教学质量,将准备以下教学资源:1.教材:选用权威、实用的教材,为学生提供理论学习的依据。
2.参考书:提供相关参考书籍,丰富学生的知识体系。
3.多媒体资料:制作精美的PPT,直观展示机械手的工作原理和设计方法。
4.实验设备:准备充足的实验设备,保证学生能够进行实际操作。
5.网络资源:利用网络资源,为学生提供更多的学习资料和案例分析。
机电液课程设计plc

机电液课程设计plc一、教学目标本节课的教学目标是让学生掌握PLC(可编程逻辑控制器)的基本原理和应用,培养学生具备PLC编程和调试的能力。
具体包括以下三个方面的目标:1.知识目标:使学生了解PLC的发展历程、工作原理、编程语言和常见应用领域;掌握PLC的基本指令、功能指令及其应用;了解PLC的硬件结构和软件系统。
2.技能目标:培养学生具备PLC编程的基本技能,能够独立完成简单的PLC程序设计、调试和故障排查;使学生能够运用PLC解决实际工程问题,如自动化生产线、控制系统等。
3.情感态度价值观目标:培养学生对机电液行业的兴趣和热情,增强学生的创新意识和团队合作精神,提高学生的人文素养和社会责任感。
二、教学内容本节课的教学内容主要包括以下几个部分:1.PLC概述:介绍PLC的定义、发展历程、工作原理和应用领域。
2.PLC硬件结构:讲解PLC的硬件组成,包括中央处理单元、输入/输出模块、电源模块、通信模块等。
3.PLC编程基础:介绍PLC的编程语言,如梯形图、指令表、功能块图等,以及基本指令和功能指令的使用。
4.PLC应用案例:分析典型的PLC应用案例,如自动化生产线、控制系统等,使学生能够将理论知识应用于实际工程。
5.PLC编程实践:引导学生进行PLC编程实践,培养学生具备实际操作能力。
三、教学方法为了实现本节课的教学目标,采用以下几种教学方法:1.讲授法:教师讲解PLC的基本原理、编程方法和应用案例,引导学生掌握知识点。
2.案例分析法:分析典型的PLC应用案例,让学生了解PLC在实际工程中的应用。
3.实验法:安排实验室实践环节,让学生动手操作PLC,提高学生的实际操作能力。
4.讨论法:学生进行小组讨论,分享学习心得和经验,培养学生团队合作精神。
四、教学资源为了支持本节课的教学内容和教学方法,准备以下教学资源:1.教材:选用权威、实用的PLC教材,为学生提供理论知识的学习依据。
2.参考书:提供相关的PLC参考书籍,丰富学生的知识体系。
机电液控课程设计
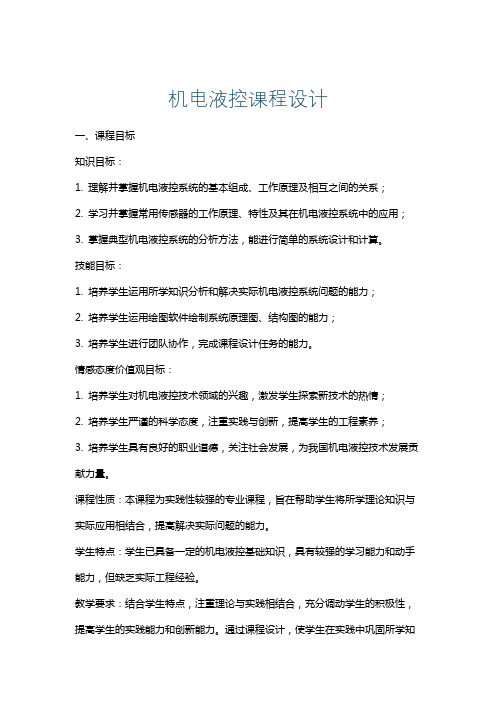
机电液控课程设计一、课程目标知识目标:1. 理解并掌握机电液控系统的基本组成、工作原理及相互之间的关系;2. 学习并掌握常用传感器的工作原理、特性及其在机电液控系统中的应用;3. 掌握典型机电液控系统的分析方法,能进行简单的系统设计和计算。
技能目标:1. 培养学生运用所学知识分析和解决实际机电液控系统问题的能力;2. 培养学生运用绘图软件绘制系统原理图、结构图的能力;3. 培养学生进行团队协作,完成课程设计任务的能力。
情感态度价值观目标:1. 培养学生对机电液控技术领域的兴趣,激发学生探索新技术的热情;2. 培养学生严谨的科学态度,注重实践与创新,提高学生的工程素养;3. 培养学生具有良好的职业道德,关注社会发展,为我国机电液控技术发展贡献力量。
课程性质:本课程为实践性较强的专业课程,旨在帮助学生将所学理论知识与实际应用相结合,提高解决实际问题的能力。
学生特点:学生已具备一定的机电液控基础知识,具有较强的学习能力和动手能力,但缺乏实际工程经验。
教学要求:结合学生特点,注重理论与实践相结合,充分调动学生的积极性,提高学生的实践能力和创新能力。
通过课程设计,使学生在实践中巩固所学知识,提高综合运用能力。
二、教学内容1. 机电液控系统概述- 了解机电液控系统的基本概念、分类及发展趋势;- 掌握机电液控系统的基本组成、工作原理及性能指标。
2. 常用传感器及其应用- 学习常用传感器的工作原理、特性及选型;- 掌握传感器在机电液控系统中的应用。
3. 液压与气动技术- 熟悉液压与气动系统的基本原理、主要元件及系统设计;- 学习液压与气动系统在机电液控系统中的应用。
4. 电机与驱动技术- 学习电机的工作原理、特性及选型;- 掌握电机驱动在机电液控系统中的应用。
5. 机电液控系统分析与设计- 掌握机电液控系统的分析方法;- 学习机电液控系统设计的一般步骤和方法。
6. 课程设计实践- 结合实际案例,进行机电液控系统的设计;- 完成系统原理图、结构图的绘制及分析报告的撰写。
机电液综合课程设计 完整版

机电液课程设计一、任务书现有一台卧式铣削专用机床。
1、技术参数(1)运动部件重量为20000N,最大铣削力为16000N(采用平面导轨),夹紧力为35000N。
(2)快进、快退速度为10m/min,工进速度为100~200mm/min。
(3)主液压缸最大行程为450mm,其中工进行程为220mm;夹紧缸行程为30mm。
(4)夹紧时间为2s。
(5)平面导轨与工作台之间的摩擦系数f jing=0.2,f dong=0.12、要求液压系统完成的工作循环工件夹紧→工作台快进→工作台工进→工作台快退→工件松开具体要求:(1)每一次循环结束,主轴电机和液压电机不停止。
(2)机床具有“半自动”和“调整”两种工作状态,机床处于“调整”工作循环时,可分别实现对液压滑台的单独点动控制。
3、需完成的设计任务如下:(1)计算主运动的切削力、并选择动力部件。
(2)计算液压系统(进给系统)各工作阶段的负载,并选择液压系统的电机、泵和阀。
(3)绘制液压系统原理图。
(4)根据工作循环确定电磁阀磁铁的动作表,选择液压控制系统的输入和输出设备,绘制PLC(C型)的端子接线图。
(5)PLC的梯形图控制程序。
(6)编写设计说明书(5000字以上)。
参考书:(1)章宏甲等,液压与气压传动,北京;机械工业出版社,2003(2)赵永成等,机电传动控制,北京;中国计量出版社(3)液压手册(4)可编程序控制器二、液压系统设计1、分析负载 1.1主液压缸负载 外负载:F g =16000N 惯性负载:200010/0.15602222.22m vF mt∆==••=∆N 阻力负载:法向力 F n =mg =20000N静摩擦阻力 F=f jing Fn =4000N 动摩擦阻力F=f dong Fn =2000N由此得出主液压缸在各工作阶段的负载如表1所示表1 主液压缸各工作阶段负载1.2夹紧缸负载外负载:F g =35000N 惯性负载:200010/260166.67m vF mN t∆==••=∆ 阻力负载:法向力 F n =mg =20000N静摩擦阻力 F=f jing Fn =4000N 动摩擦阻力 F=f dong Fn =2000N由此得出夹紧液压缸在各工作阶段的负载如表2所示表2 夹紧液压缸各工作阶段负载2、确定执行件主要参数2.1主液压缸内径D 及活塞杆外径d滑台快进快进速度相等,液压可选用单活塞杆式,快进时差动连接,空载启动压力P min =0.3Mpa 。
机电液综合课程设计
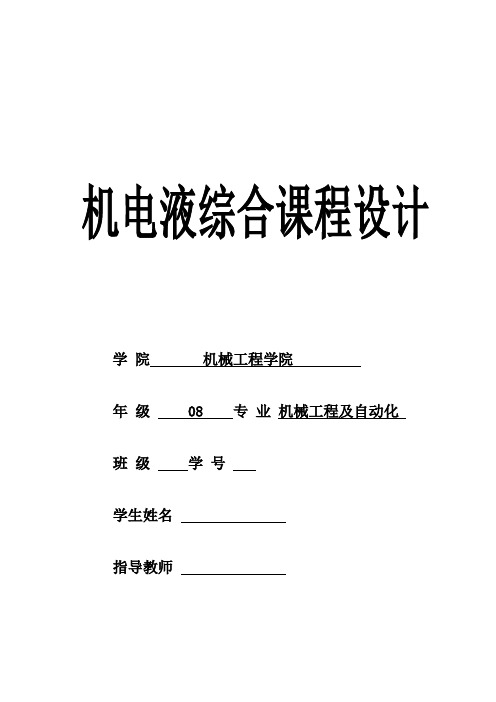
学院机械工程学院年级 08 专业机械工程及自动化班级学号学生姓名指导教师3.2液压元件表表8 液压元件表4、液压系统性能估算4.1验算系统压力损失并确定溢流阀的调整值4.1.1主液压缸快进滑台快进时,主液压缸差动连接,进油路上的元件有三位五通阀,回油路上油液通过二位二通阀,由原理图及表6可以推算出通过的流量分别为48L/min 和97.8L /min ,忽略去溢流损失,可得进油路上的总压降为:0.5(48/63)0.3(97.8/100)0.576vpM pa ∆=+=∑<0.6Mpa较合理,可实现差动运动。
在回油路上油液经过阀4和阀3流过的流量是48L/min,进入无杆腔:22210.2(48/80)0.3(48/63)0.242p p p M pa ∆=-=+=接近0.3Mpa 所以基本符合。
4.1.2主液压缸工进滑台工进时,油液在进油路上通过电磁换向阀进入油缸的无杆腔,流量为15.6L/min ,油液在回油路上通过电磁换向阀的流量为7.8L/min ,在节流阀处的压力损失为0.6Mpa 后 这时,液压缸回油腔的压力的p 2为2220.60.5(15.6/100)0.5(7.8/100)0.6053p M pa =++=与之前所设值0..6Mpa 略大。
0.0053p Mpa ∆= 该值可以忽略所以不需修改。
4.1.3主液压缸快退滑台快退时,油液在进油路上通过电磁换向阀的流量为48L/min ,然后流入有杆腔。
回油路上流过电磁换向阀的流量为94.2 L/min ,然后流入油箱。
在进油路上的压力损失220.5(48/100)0.5(94.2/100)0.56v p M pa ∆=+=∑与估计的值相近不必重算,所以快退是的工作压力1 1.34p p p p M pa =+∑∆= 以此溢流阀的卸荷应大于1.34Mpa.4.1.4 夹紧缸夹紧夹紧缸在夹紧时,进油路上油液通过二位二通阀的流量为9L/min ,在单向阀处的压力损失为0.3Mpa ,为保证电磁继电器能正常工作,需要有一定的压差,为0.5Mpa ,通过三位四通电磁换向阀的流量为18 L/min ,在调速阀处的压力损失为0.7Mpa ,同时还有溢流损失。
机电液课程设计报告(全套)
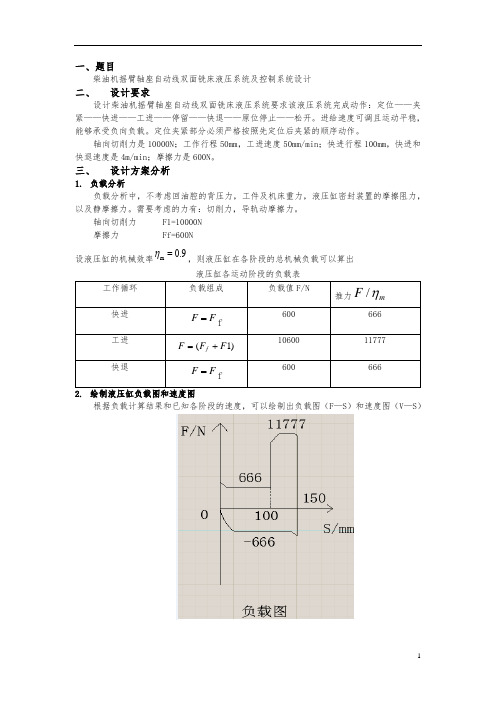
一、题目柴油机摇臂轴座自动线双面铣床液压系统及控制系统设计二、 设计要求设计柴油机摇臂轴座自动线双面铣床液压系统要求该液压系统完成动作:定位——夹紧——快进——工进——停留——快退——原位停止——松开。
进给速度可调且运动平稳,能够承受负向负载。
定位夹紧部分必须严格按照先定位后夹紧的顺序动作。
轴向切削力是10000N ;工作行程50mm ,工进速度50mm/min ;快进行程100mm ,快进和快退速度是4m/min ;摩擦力是600N 。
三、 设计方案分析1. 负载分析负载分析中,不考虑回油腔的背压力,工件及机床重力,液压缸密封装置的摩擦阻力,以及静摩擦力。
需要考虑的力有:切削力,导轨动摩擦力。
轴向切削力 F1=10000N 摩擦力 Ff=600N 设液压缸的机械效率9.0m =η,则液压缸在各阶段的总机械负载可以算出工作循环 负载组成负载值F/N推力m Fη/快进 F F =f600 666 工进 )1(F F F f +=10600 11777 快退F F =f600666根据负载计算结果和已知各阶段的速度,可以绘制出负载图(F —S )和速度图(V —S )3.初步确定液压缸参数组合机床液压系统的最大负载约为12000N ,初选液压缸的设计压力P1=3MPa ,为了满足工作台快速进退速度相等,并减小液压泵的流量,这里的液压缸选用单杆式的,液压缸无杆腔与有杆腔的等效面积A1与A2应满足A1=2A2(即液压缸径D 和活塞杆直径d 应满足:d=0.707D 。
为防止铣削后工件突然前冲,液压缸需保持一定的回油背压,暂取背压为0.5MPa ,并取液压缸机械效率9.0m =η。
则液压缸上的平衡方程F P A F A P A P +=+=21221121故液压缸无杆腔的有效面积:CMA D CM P P F A 38.783.424483.42105.05.010*******11266211=⨯===⨯⨯-⨯=-=ππ 液压缸径:按标准值取D=80mm ;因为A1=2A2,故活塞杆直径d=0.707D=56mm 。
机电液综合设计课程设计
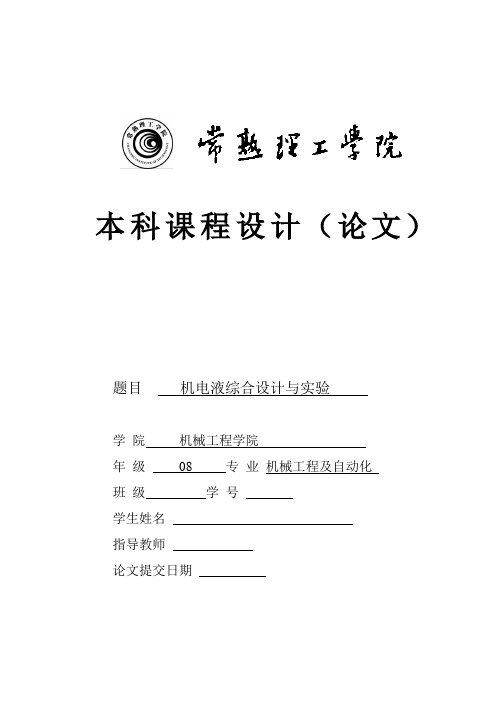
本科课程设计(论文)题目 机电液综合设计与实验学 院 机械工程学院 年 级 08 专 业 机械工程及自动化 班 级 学 号学生姓名 指导教师 论文提交日期目录1 任务书1.1实验目的1.2实验任务2 液压传动系统的设计计算及元件选型 2.1 选用液压元件2.2计算和选择液压元件3 液压缸的设计计算3.1 液压缸主要零件的材料3.2 液压缸的内径D和活塞杆直径d的计算 3.3 液压缸壁厚的计算3.4 校核d3.5 缸盖固定螺栓d3的计算3.6 缸体与缸盖采用螺纹连接时的计算3.7 活塞与活塞杆采用螺纹连接时的计算4 实验安装及调试4.1 电器控制系统的设计4.2 基本工作过程5 心得体会参考文献附录1 任 务 书1.1实验目的:1. 熟悉、了解本实验台的组成2. 掌握常见典型液压回路的设计、安装及调试3. 掌握继电器控制电路的设计;PLC 控制程序的设计、安装及调试4. 培养学生综合运用机械、液压、电气等知识及设计、安装调试等综合技能1.2实验任务(一)机械动作要求┏━━━━→┓┃ ┃工 进50┃快 退 ━━━━━━━━━━━→┓━━┛(二)设计参数工作是最大负载F=3000N;液压缸工作压力为P1=1.5M;快进、快退速度V 快=5m/min;工进速度V=0.8m/min;油缸内径与活塞杆直径比d/D=0.75;回油腔背压P2=0.5Mpa;油路压力损失∑ΔP=0.3Mpa;Qmin=0.2L/min 。
(三)设计内容(1)绘制液压缸总图和绘制端盖零件图 (2)液压泵及匹配的电动机选择 (3)液压元件的选择(4)按规定机械动作要求,设计液压传动系统原理图,设计电器控制系统 (5)液压传动装置的安装及电气控制系统的连接 (6)调试2 液压传动系统的设计2.1 选用液压元件如下表2-1:表2-1根据动作要求和提供的元件,设计液压传动系统,其工作情况由表2-2所示 油路中用到的上述提供的元器件有:二位二通电磁换向阀、调速阀、先导式溢流阀、三位四通电磁换向阀。
- 1、下载文档前请自行甄别文档内容的完整性,平台不提供额外的编辑、内容补充、找答案等附加服务。
- 2、"仅部分预览"的文档,不可在线预览部分如存在完整性等问题,可反馈申请退款(可完整预览的文档不适用该条件!)。
- 3、如文档侵犯您的权益,请联系客服反馈,我们会尽快为您处理(人工客服工作时间:9:00-18:30)。
机电液综合课程设计学校:大连交通大学院系:机械工程学院机械电子专业班级:设计者:指导教师:2015年7月目录摘要 (3)一、设计内容及要求 (3)1.1设计目的 (3)1.2平台动作循环要求 (3)1.3平台升降对液压传动系统的具体参数要求 (3)二、液压系统的初步设计 (4)三、电气控制部分设计 (6)四、机械系统的设计与计算 (7)4.1工况分析 (7)4.2工作腔有效工作面积和活塞直径计算 (7)五、液压系统设计与计算 (9)5.1流量功率计算 (9)5.2液压泵设计与校核 (9)5.3阀类元件及辅助元件 (10)5.4油管 (12)5.5油箱 (13)六、PLC设计方案 (14)6.1可编程控制器控制系统I/O点数估算 (14)6.2结构形式考虑 (14)6.3PLC语句表 (15)七、课程设计心得体会 (17)参考文献 (18)摘要本次课程设计内容为1500kg平台升降液压、电控、机械系统综合设计。
平台升降的动力来自于液压缸,充分利用了液压传动结构简单,体积小,质量轻,输出功率大及其易于操纵控制的优点;控制系统主要利用西门子PLC编程控制器。
此次设计主要是将自己所学的知识结合辅助材料运用到实际中,主要设计过程有:明确传动过程,计算相关数据,绘制液压系统原理图,并且结合相关PLC技术最终实现所要设计的平台升降要求。
关键词:同步运动蓄能器保压电液比例调速阀PLC一、设计内容及要求1.1设计目的课程设计是培养学生综合运用所学的基础理论和专业理论知识,独立解决实际设计问题能力的一个重要的实践性教学环节,因此,通过设计应达到下述目的:(1)初步掌握正确的设计思想和设计的基本方法,步骤,巩固,深化和扩大所学的知识,培养理论联系实际的工作方法和独立工作能力;(2)获得平台升降总体设计,结构设计,零件计算,编写说明书。
绘制液压系统图1张;(3)熟悉有关标准、规格、手册和资料的应用;(4)完成PLC选型及硬件电路设计,绘制PLC端子接线图1张。
并完成软件设计,绘制梯形图与列出主要控制程序指令语句1张。
1.2平台动作循环要求设计一套升降机的液压系统,该系统能使平台保持一定的精度,同步、平稳地上升、下降,并可在0.8m的行程范围内任意高度停留。
系统结构紧凑,安全可靠。
本次设计要求四个液压缸同步运动。
停止时采用蓄能器保压,泵卸荷,同步要求高。
动作过程:能够实现“同步上升—停止—保压—同步下降—停止”的工作循环。
1.3平台升降对液压传动系统的具体参数要求平台重量1500kg,平台升降速度是0.3~0.5 m/s,平台上升高度0.8m。
二、液压系统的初步设计通过对系统设计的要求的分析,确定系统需要同步回路,锁紧回路,平衡回路和保压回路。
(1)使两个或两个以上的液压缸同步动作的回路称为同步回路。
液压基本同步回路有:机械联结的同步回路,采用同步液压马达的同步回路。
各回路的优缺点:①机械联结同步回路虽然存在有齿侧隙和齿轮轴的扭转变形引起的误差但同步可靠。
缺点是结构复杂,两缸布置的位置受到限制。
串联液压缸的同步回路结构简单,不需要同步元件,其同步精度取决于两液压缸的制造精度和密封性能。
由于油缸不可避免的存在内泄漏,所以每次往复运动都将增加两缸的位置误差,从而出现同步失调。
带补偿装置的串联液压缸同步回路解决了串联液压缸的同步回路由于油缸内泄漏引起的同步失调的问题,其缺点是该回路只适用于负载较小的液压系统。
调速阀的同步回路可以实现多缸同步但同步精度受调速阀性能和油满影响,而且个个调速阀比较难调到相同流量,所以误差化较大。
比例调速阀同步回路的同步精度虽然没有采用伺服阀的回路高,但仍然具有比较高的精度,而且相对伺服阀闭低很多。
综上所诉及系统要求,本系统采用相同的4个液压缸相并联,用比例调速阀实现同步。
②液压基本锁紧采用液控单向阀单向锁紧回路,当换向阀在中位时,液压泵卸荷活塞被液控单向阀锁紧,当换向阀切换至上升或下降位置时,液控单向阀即被打开,由于液控单向阀没有泄露,故活塞可被较长时间锁紧,不会因自重而下滑。
③在液压系统要设置平衡回路,其方法是在立式液压缸下行回路上设置一个适当阻力,使液压缸的回油腔产生一定的背压,以平衡其自重,在本设计中采用单向顺序阀平衡回路。
④再执行元件液压缸终止运动时要求液压缸能继续保持一段时间的压力在这段时间内不再继续前进,同时也暂时不回程,这时就要采用保压回路,以保持那些暂不继续运动的执行元件的系统油压。
常用的保压方法有定量泵和溢流阀的保压,压力由溢流阀调定并保持,与定量泵构成恒压源,采用液控单向阀保压等,并设计选用蓄能器保压。
各回路优缺点:液控单向阀保压结构简单,密封性好,但是阀类元件的泄露使得保压时间不能维持太久。
采用定量泵和溢流阀的保压,压力由几乎全经溢流阀流回油箱,系统功率损失大,发热严重,故只在小功率且保压时间较短的场合使用。
综上考虑,绘制出图所示液压传动系统草图:图2-1 液压系统工作原理图1—液压缸;2—液控单向阀;3—电液比例调速阀;4—蓄能器;5—压力计;6—压力继电器;7—单向顺序阀;8—三位四通电磁换向阀;9—背压阀;10—两位两通电磁换向阀;11—溢流阀;12—定量泵;13—滤油器+空气过滤器;14—油箱表2-1 电磁铁动作顺序表动作名称1YA 2YA 3YA同步上升+ _ -停止_ _ +保压_ _ +同步下降_ + -停止_ _ +三、电气控制部分设计电路图如下所示:图3-1 电气控制电路图SB1启动按钮SB2停止按钮SB3上升按钮SB4下降按钮SB4下降按钮SB5上升停止按钮SB6下降停止按钮SQ1上升极位开关SQ2下降极位开关四、机械系统的设计与计算4.1工况分析液压缸的输出力由工作压力p 和活塞有效面积A 决定;液压缸的输出速度v 是由输入液压缸的流量q 和活塞有效面积A 决定。
即: vAq PA F == (4-1) 主机工作过程中,其执行机构所要克服的负载包括工作负载、惯性负载和阻力负载。
(1)工作负载 N F W 36754/8.91500=⨯=(2)惯性负载 37502.0/5.01500=⨯=a F N取Δt=0.2s Δv=0.5m/s (4-2)(3)密封阻力启动时 N A P F s 1600008.010251eq =⨯⨯== (4-3) 运动时 N A P F eq 8002/1s =•= (4-4)(4)导轨摩擦阻力 N F f F w d f 5.367=•= (4-5) 初步估计有杆腔活塞面积mm A 2240=取a b MP P 1=N A P F b 40001040101462b =⨯⨯⨯==- (4-6)(5)启动阶段NF F F F F F bf a w 5.1339240005.367160037503675S =++++=++++= (4-7)由表《各类液压设备常用工作压力》查得工作压力:P=3Mpa (4-8)4.2工作腔有效工作面积和活塞直径计算F=13392.5N (4-8)m 1026100496.035.13392=⨯=•=m P FA η(4-9)D=m A 079.000496.0441=⨯=ππ (4-10) 往返速度比 67.13.05.0==λ 取 62.0d ==Dϕ d=0.62D=0.0049m圆整后 D=80mm d=50mm液压缸两腔的实际有效面积m mm D A 222210050265.05.50268044==⨯==ππ (4-11) m mm D A 22222220030631.01.3063)5080(4)d (4==-⨯=-=ππ(4-12)复算执行元件的工作压力无杆腔进油工作阶段:MPa P A A A F P 97.2105.00050265.00030631.00050265.05.133926b 121=⨯⨯+=+=(4-13) 有杆腔进油阶段:MPa P A A A F P b 19.5105.00030631.00050265.00030631.05.133926212=⨯⨯+=+=(4-14)五、液压系统设计与计算5.1流量功率计算(1)上升时,s A v /m 10508.10050265.03.0q 33111-⨯=⨯== (5-1)MPa A A P F P m 26.30050265.0/)0030631.0105.09.05.13392(/)/(61221=⨯⨯+=+=η (5-2)KW q P P 92.410508.11026.336111=⨯⨯⨯==- (5-3)(2)下降时s m A v q /1053.10030631.05.033222-⨯=⨯== (5-4)MPa A A P F P m 68.50030631.0/)0050265.0105.09.05.13392(/)/(62112=⨯⨯+=+=η (5-5) KW q P P 69.81053.11068.536222=⨯⨯⨯==- (5-6)5.2液压泵设计与校核取油路压力损失0.3Mpa.取调整压力高于系统最大工作压力0.3Mpa,整个过程中最大工作压力:MPa P P 28.63.03.02max =++= (5-7)整个过程中最大流量为:m in /8.9160101053.1q 33max L =⨯⨯⨯=- (5-8)取泄露系数1.1=Kmin /92.40348.911.1q max L q K p =⨯⨯=•= (5-9)溢流阀的最小稳定流量为3/min L查《YB-Ea 型叶片泵技术参数》选择YB-Ea315叶片泵,其中min /1500n r p =,92.0=η,液压泵排量为316ml/r,额定压力10MPa.min /08.4361000/92.03161500q L p =⨯⨯= (5-10)由于液压缸在快速工进时输入功率最大,这时液压泵的工作压力为 6.28Mpa ,流量为91.8/min L ,查表《液压泵的总功率》取总效率92.0=η,液压泵驱动电动机所需功率:KW q P P p p43.1176.069.8p ==⨯=η (5-11)根据表《Y 系列(IP44)α型三相异步电动机技术参数》选取Y16L-4电动机额定功率15KW 额定转速1460r/min 效率88.5%功率因数0.85。
5.3阀类元件及辅助元件根据阀类及辅助元件所有油路的最大压力和通过最大试验流量,选出这些液压元件。
1.叶片泵(1)定流量436.08L/min ;( 2 ) 额定压力10 Mpa ;( 3) 型号规格 YB-Ea315(4)工作原理:叶片泵转子旋转时,叶片在离心力和压力油的作用下,尖部紧贴在定子内表面上。
这样两个叶片与转子和定子内表面所构成的工作容积,先由小到大吸油后再由大到小排油,叶片旋转一周时,完成一次吸油与排油。