切削实验报告
金属切削原理实验报告

一、实验目的1. 了解金属切削的基本原理和过程;2. 掌握切削用量对切削力和切削温度的影响;3. 熟悉金属切削实验设备和实验方法;4. 提高对金属切削加工工艺的认识。
二、实验原理金属切削是指用切削工具将金属工件上的多余材料去除,使其达到一定形状、尺寸和表面质量的过程。
金属切削实验主要研究切削用量(切削速度、切削深度、进给量)对切削力和切削温度的影响。
三、实验仪器与设备1. 金属切削实验台;2. 刀具;3. 金属工件;4. 切削力传感器;5. 温度传感器;6. 计算机及数据采集软件。
四、实验步骤1. 安装刀具:将刀具安装在实验台上,确保刀具安装牢固;2. 安装工件:将工件安装在夹具上,调整工件位置,确保工件与刀具对准;3. 设置切削参数:根据实验要求设置切削速度、切削深度和进给量;4. 开启实验台:启动实验台,进行金属切削实验;5. 数据采集:通过切削力传感器和温度传感器采集切削力和切削温度数据;6. 实验结束:关闭实验台,清理实验场地。
五、实验结果与分析1. 切削力与切削速度的关系:在切削深度和进给量不变的情况下,随着切削速度的增加,切削力逐渐增大。
这是因为切削速度提高,切削温度升高,切削材料软化,导致切削力增大;2. 切削力与切削深度的关系:在切削速度和进给量不变的情况下,随着切削深度的增加,切削力逐渐增大。
这是因为切削深度增加,切削面积增大,切削力增大;3. 切削力与进给量的关系:在切削速度和切削深度不变的情况下,随着进给量的增加,切削力逐渐增大。
这是因为进给量增加,切削速度提高,切削力增大;4. 切削温度与切削速度的关系:在切削深度和进给量不变的情况下,随着切削速度的增加,切削温度逐渐升高。
这是因为切削速度提高,切削热增加,切削温度升高;5. 切削温度与切削深度的关系:在切削速度和进给量不变的情况下,随着切削深度的增加,切削温度逐渐升高。
这是因为切削深度增加,切削热增加,切削温度升高;6. 切削温度与进给量的关系:在切削速度和切削深度不变的情况下,随着进给量的增加,切削温度逐渐升高。
切削加工实验实验报告

一、实验目的1. 了解切削加工的基本原理和工艺过程。
2. 掌握切削加工的基本操作方法和刀具选择。
3. 掌握切削参数的合理选择,以提高加工效率和工件质量。
二、实验器材1. 数控车床:CK-400Q型一台2. 刀具:车刀一把3. 工件:铝棒工件一根4. 测量仪器:游标卡尺一把5. 毛刷一把三、实验步骤1. 工件安装(1)利用三爪卡盘钥匙拧开卡盘,送入工件的部分,留出适当的长度,再用钥匙拧紧卡盘,卡住工件,必要时可采用加力杆进行加力拧紧。
(2)取出工件,同样也是如此操作,按照上面的方法,可以将工件夹紧,完成工件的安装。
2. 刀具安装(1)数控车床的刀具安装跟普通车床的刀具安装类似,都是利用螺钉将刀具压紧在四方刀架上,卡住数控车床车刀至少要用两个螺钉,并轮流逐个拧紧,拧紧力量要适当。
3. 对刀操作(1)通过刀具试触切削工件样品棒料边缘,读入相应位置坐标,可以得出相应的X、Z轴的对刀零点。
(2)载入相应数据到控制面板,完成机床的工件坐标零点设置。
4. 数控系统操作面板的熟悉及操作(1)机床MDI操作:可以简单输入编程指令,运行机床,试看机床是否能够按照指令进行加工。
5. 切削加工(1)选择合适的切削参数,包括切削速度、切削深度、进给量等。
(2)启动数控车床,进行切削加工。
6. 测量与评价(1)使用游标卡尺测量加工后的工件尺寸,与设计尺寸进行对比,评估加工精度。
(2)观察加工表面质量,评估加工表面粗糙度。
四、实验结果与分析1. 工件加工尺寸与设计尺寸的对比根据实验数据,工件加工尺寸与设计尺寸的误差在允许范围内,说明加工精度较高。
2. 加工表面质量通过观察加工表面,发现表面粗糙度较小,加工表面质量较好。
3. 切削参数对加工效果的影响(1)切削速度:切削速度的提高可以降低切削温度,减少工件变形,提高加工效率,但过高的切削速度可能导致刀具磨损加剧。
(2)切削深度:切削深度的增加可以提高加工效率,但过大的切削深度可能导致工件变形和刀具磨损。
切削金属实验总结汇报
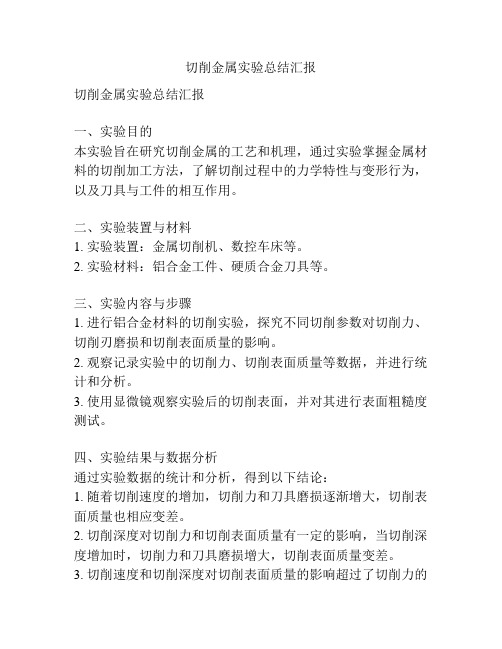
切削金属实验总结汇报切削金属实验总结汇报一、实验目的本实验旨在研究切削金属的工艺和机理,通过实验掌握金属材料的切削加工方法,了解切削过程中的力学特性与变形行为,以及刀具与工件的相互作用。
二、实验装置与材料1. 实验装置:金属切削机、数控车床等。
2. 实验材料:铝合金工件、硬质合金刀具等。
三、实验内容与步骤1. 进行铝合金材料的切削实验,探究不同切削参数对切削力、切削刃磨损和切削表面质量的影响。
2. 观察记录实验中的切削力、切削表面质量等数据,并进行统计和分析。
3. 使用显微镜观察实验后的切削表面,并对其进行表面粗糙度测试。
四、实验结果与数据分析通过实验数据的统计和分析,得到以下结论:1. 随着切削速度的增加,切削力和刀具磨损逐渐增大,切削表面质量也相应变差。
2. 切削深度对切削力和切削表面质量有一定的影响,当切削深度增加时,切削力和刀具磨损增大,切削表面质量变差。
3. 切削速度和切削深度对切削表面质量的影响超过了切削力的影响。
五、实验结论通过本次实验,我们了解了切削金属的工艺和机理,熟悉了金属切削的基本过程,掌握了切削参数对切削力、刃磨损和切削表面质量的影响,进一步认识了机械加工中的金属切削技术,对切削金属领域的应用有了更深入的了解。
六、实验心得体会通过本次实验,我深刻认识到切削金属过程中各个参数的重要性,合理选取切削参数是保证加工效率和加工质量的关键。
同时,我也发现切削金属是一项综合性实践技术,需要我们熟悉材料的性质和刀具的特点,并结合实际情况进行合理的参数调整。
通过实验的反复实践,我不断提高了自己的实践能力和创新思维,对切削金属技术有了更深的认识。
七、展望在今后的学习和工作中,我将继续加强对金属切削工艺和机理的研究,不断提高自己的技术水平,不断完善和创新切削金属的方法和工艺,为我国制造业的发展做出贡献。
同时,我也希望能够与同行交流切削金属技术,在实践中互相学习、共同进步,推动这一领域的发展。
数控工艺切削过程模拟实验报告
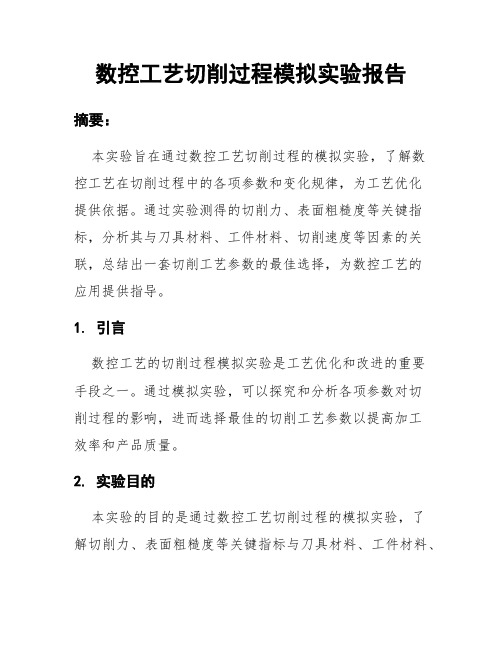
数控工艺切削过程模拟实验报告摘要:本实验旨在通过数控工艺切削过程的模拟实验,了解数控工艺在切削过程中的各项参数和变化规律,为工艺优化提供依据。
通过实验测得的切削力、表面粗糙度等关键指标,分析其与刀具材料、工件材料、切削速度等因素的关联,总结出一套切削工艺参数的最佳选择,为数控工艺的应用提供指导。
1. 引言数控工艺的切削过程模拟实验是工艺优化和改进的重要手段之一。
通过模拟实验,可以探究和分析各项参数对切削过程的影响,进而选择最佳的切削工艺参数以提高加工效率和产品质量。
2. 实验目的本实验的目的是通过数控工艺切削过程的模拟实验,了解切削力、表面粗糙度等关键指标与刀具材料、工件材料、切削速度等因素之间的关系,为优化切削工艺参数提供依据。
3. 实验设备和材料本实验使用的设备为数控加工中心,刀具材料选用硬质合金,工件材料选用无碳钢。
实验中使用的刀具包括铣刀和钻头。
4. 实验内容4.1 实验步骤:1) 将工件固定在数控加工中心工作台上;2) 设定刀具类型、切削速度和进给速度等数控工艺参数;3) 进行模拟切削,记录切削过程中的切削力;4) 完成切削后,测量工件的表面粗糙度。
4.2 实验结果:1) 记录了不同切削参数下的切削力数据;2) 测量了不同切削参数下工件的表面粗糙度。
5. 结果分析通过分析实验得到的数据,绘制切削力与切削速度、切削速度与表面粗糙度之间的关联曲线。
在数控切削过程中,切削力与切削速度呈正相关关系,切削速度与表面粗糙度呈负相关关系。
5.1 切削力与切削速度关系分析实验结果显示,在相同刀具和工件材料的条件下,切削力随着切削速度的增加而增加。
这是因为切削速度的增加会导致刀具与工件之间的摩擦增加,从而导致切削力的增加。
在一定范围内,切削力与切削速度大致呈线性关系。
5.2 切削速度与表面粗糙度关系分析通过实验数据分析,可以看出切削速度与表面粗糙度之间存在着一定的负相关关系。
在其他切削参数相同的情况下,随着切削速度的增加,表面粗糙度逐渐降低。
切削力实验报告

切削力实验报告切削力实验报告引言:切削力实验是机械加工领域中重要的研究内容之一。
通过测量切削力的大小和方向,可以评估刀具性能、优化切削工艺以及提高加工效率。
本实验旨在通过实际操作和数据分析,深入了解切削力的变化规律和影响因素。
实验装置与方法:本次实验采用数控车床进行切削力的测量。
首先,选择适当的刀具和工件材料,并确定切削参数,如进给速度、切削深度和切削速度。
接着,安装刀具和工件,调整好机床的切削参数。
在实验过程中,通过力传感器测量切削力的大小和方向,并将数据记录下来。
最后,根据实验数据进行分析和总结。
实验结果与分析:在实验过程中,我们记录了不同切削参数下的切削力数据,并进行了分析。
首先,我们发现切削速度对切削力有着显著影响。
随着切削速度的增加,切削力呈现出逐渐增加的趋势。
这是因为切削速度增加会导致切削温度升高,材料的塑性变形能力下降,从而增加了切削力的大小。
此外,切削速度的增加也会引起切削过程中的振动,进而增加了切削力的变化幅度。
其次,切削深度也对切削力有着明显的影响。
随着切削深度的增加,切削力呈现出逐渐增加的趋势。
这是因为切削深度的增加会导致切削面积增大,从而增加了切削力的大小。
此外,切削深度的增加也会引起切削过程中的切削力方向的变化,进而影响了切削力的分布情况。
最后,进给速度也对切削力有一定的影响。
我们观察到,随着进给速度的增加,切削力呈现出先增加后减小的趋势。
这是因为进给速度的增加会导致切削过程中的切削面积增大,从而增加了切削力的大小。
然而,当进给速度过大时,切削力会受到切削液的冲击和切削过程中的振动的影响,进而导致切削力的减小。
结论:通过本次实验,我们深入了解了切削力的变化规律和影响因素。
切削速度、切削深度和进给速度都对切削力有着明显的影响。
切削速度的增加会导致切削力的增加,切削深度的增加也会增加切削力的大小,而进给速度的变化则会引起切削力的先增加后减小的变化趋势。
这些实验结果对于优化切削工艺、提高加工效率具有重要的指导意义。
切削原理实验报告
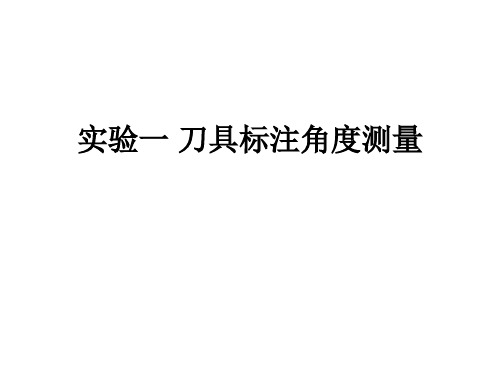
一、实验目的
1、熟悉车刀切削部分的构造要素,掌握车刀 标注角度参考系及相应的角度定义 2、了解量角台的构造,学会使用量角台测量 刀具标注角度 3、根据测得的标注角度,绘制车刀角度图
二、实验设备与工具
车刀角度测量仪(车刀量角பைடு நூலகம்) 车刀 实验台
三、设备参数工作原理说明
四、实验记录
• 测量正交平面参考系的基本角度
车刀名称 刀杆尺寸 主前角 主后角 主偏角 副偏角 刃倾角 副后角
• 计算出下列派生角度
车刀名称 刀尖角εr 余偏角r 楔 角
p
f
,
n
p
f
, n
五、思考题
1、用车刀量角台测量正交平面(主剖面)前角和后 角时,为什么要让工作台从原始位置起,逆时针 方向旋转的角度? 2、参照测量车刀主剖面前角和后角的方法,怎样 利用车刀量角台测量出车刀副刀刃上的副前角和 副后角?为什么车刀工作图上不标注副前角? 3、怎样利用车刀量角台测量出车刀背平面及假定工 作平面的前角和后角?
切削加工实验报告
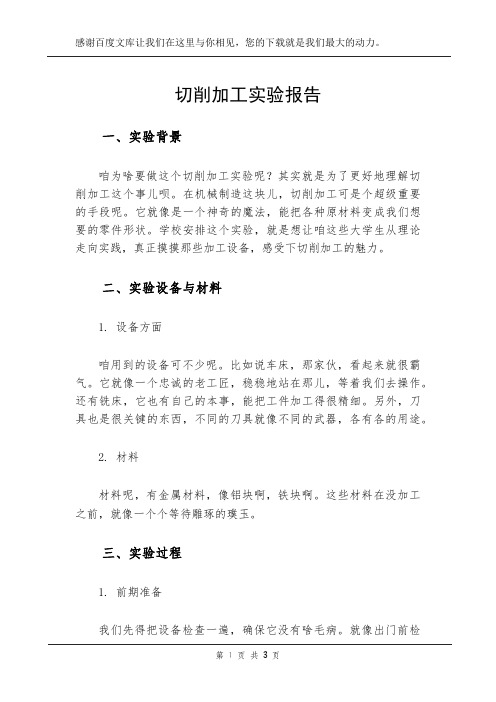
切削加工实验报告一、实验背景咱为啥要做这个切削加工实验呢?其实就是为了更好地理解切削加工这个事儿呗。
在机械制造这块儿,切削加工可是个超级重要的手段呢。
它就像是一个神奇的魔法,能把各种原材料变成我们想要的零件形状。
学校安排这个实验,就是想让咱这些大学生从理论走向实践,真正摸摸那些加工设备,感受下切削加工的魅力。
二、实验设备与材料1. 设备方面咱用到的设备可不少呢。
比如说车床,那家伙,看起来就很霸气。
它就像一个忠诚的老工匠,稳稳地站在那儿,等着我们去操作。
还有铣床,它也有自己的本事,能把工件加工得很精细。
另外,刀具也是很关键的东西,不同的刀具就像不同的武器,各有各的用途。
2. 材料材料呢,有金属材料,像铝块啊,铁块啊。
这些材料在没加工之前,就像一个个等待雕琢的璞玉。
三、实验过程1. 前期准备我们先得把设备检查一遍,确保它没有啥毛病。
就像出门前检查自己的鞋带系好了没一样。
然后把材料稳稳地固定在设备上,这一步可不能马虎,要是没固定好,在加工的时候材料飞出去了,那可就危险了。
2. 加工操作我就先拿车床来说吧。
当我启动车床的时候,那声音就像是它在跟我打招呼呢。
我慢慢地调整着刀具的位置和速度,看着金属屑一点点地从工件上掉下来,心里可激动了。
就像是看着自己精心培育的种子一点点发芽似的。
铣床的操作也有它的门道,得小心地控制铣刀的走向,不然加工出来的工件就不达标了。
3. 数据记录在加工的过程中,我们还得记录好多数据呢。
比如说刀具的转速、进给量啊这些。
这些数据就像是密码一样,能告诉我们加工过程中的秘密。
要是不记录好,就没法分析实验结果了。
四、实验结果1. 加工精度加工出来的工件呢,有的精度比较高,这说明我们在操作过程中控制得还不错。
但也有一些工件精度不太理想,这时候就得分析是哪个环节出了问题。
2. 表面粗糙度表面粗糙度也是一个重要的指标。
有些工件表面很光滑,摸起来就很舒服,就像婴儿的皮肤似的。
但有些就比较粗糙,这就需要我们改进加工的参数。
金属切削实习报告
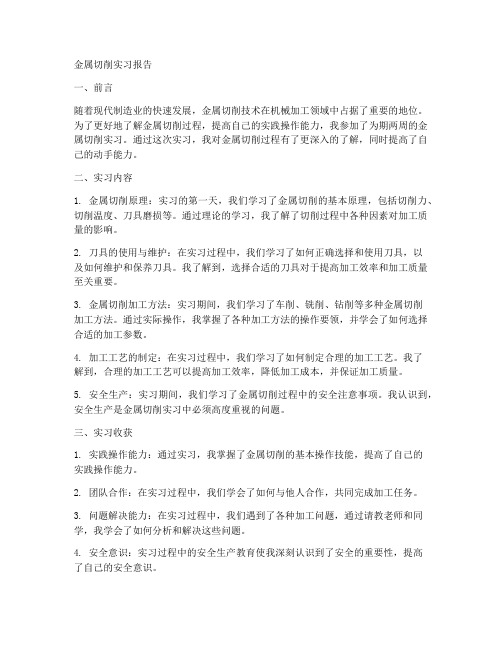
金属切削实习报告一、前言随着现代制造业的快速发展,金属切削技术在机械加工领域中占据了重要的地位。
为了更好地了解金属切削过程,提高自己的实践操作能力,我参加了为期两周的金属切削实习。
通过这次实习,我对金属切削过程有了更深入的了解,同时提高了自己的动手能力。
二、实习内容1. 金属切削原理:实习的第一天,我们学习了金属切削的基本原理,包括切削力、切削温度、刀具磨损等。
通过理论的学习,我了解了切削过程中各种因素对加工质量的影响。
2. 刀具的使用与维护:在实习过程中,我们学习了如何正确选择和使用刀具,以及如何维护和保养刀具。
我了解到,选择合适的刀具对于提高加工效率和加工质量至关重要。
3. 金属切削加工方法:实习期间,我们学习了车削、铣削、钻削等多种金属切削加工方法。
通过实际操作,我掌握了各种加工方法的操作要领,并学会了如何选择合适的加工参数。
4. 加工工艺的制定:在实习过程中,我们学习了如何制定合理的加工工艺。
我了解到,合理的加工工艺可以提高加工效率,降低加工成本,并保证加工质量。
5. 安全生产:实习期间,我们学习了金属切削过程中的安全注意事项。
我认识到,安全生产是金属切削实习中必须高度重视的问题。
三、实习收获1. 实践操作能力:通过实习,我掌握了金属切削的基本操作技能,提高了自己的实践操作能力。
2. 团队合作:在实习过程中,我们学会了如何与他人合作,共同完成加工任务。
3. 问题解决能力:在实习过程中,我们遇到了各种加工问题,通过请教老师和同学,我学会了如何分析和解决这些问题。
4. 安全意识:实习过程中的安全生产教育使我深刻认识到了安全的重要性,提高了自己的安全意识。
四、实习总结通过两周的金属切削实习,我对金属切削过程有了更深入的了解,提高了自己的实践操作能力。
同时,我也认识到了自己在团队合作、问题解决和安全意识等方面的不足,需要在今后的学习和工作中不断改进。
总之,这次实习让我受益匪浅,为我将来的职业发展奠定了基础。
- 1、下载文档前请自行甄别文档内容的完整性,平台不提供额外的编辑、内容补充、找答案等附加服务。
- 2、"仅部分预览"的文档,不可在线预览部分如存在完整性等问题,可反馈申请退款(可完整预览的文档不适用该条件!)。
- 3、如文档侵犯您的权益,请联系客服反馈,我们会尽快为您处理(人工客服工作时间:9:00-18:30)。
切削实验
一、实验目的
1 观察切削变形的过程,以及所出现的现象。
2 研究切削速度、刀具前角和走刀量等因素对切削变形的影响规律。
在金属切削过程中,由于产生塑性变形,使切屑的外形尺寸发生变化,即与切削层尺寸比较,切屑的长度偏短,厚度增加,这种现象称为切屑收缩。
一般情况下,切屑收缩的大小能反映切削变形的程度。
二、实验内容
1、切削速度υ对切削变形的影响
刀具参数:κr=45°;κr '= 8°;λs= 0°;γo =10°;αo =7°;r =0.1 mm 切削用量:f= 0.39 mm /r , ap=40mm。
改变切削速度,从低速到高速,可先取
υc= 5; 10; 20; 25; 30; 40; 60; 80; 110 m /min ;
n= 53;106;212;265;318;424;636;848;1166r/min ;
用每一种转速切削一段试棒,停车收集切屑并观察切削颜色(注意安全,防止烫伤)。
测量并将结果填入表2-1 中。
2、刀具前角对切削变形的影响
刀具参数:κr = 45°;κr '= 8°;λs = 0°;αo = 7°; r = 0.1 mm 。
切削用量: f= 0.39 mm /r , ap =40 mm υc= 60 m /min 。
改变车刀前角:γo = 0°; 15°; 30°。
用不同前角的车刀分别切削一段试棒,停车收集切屑并观察切削颜色(注意安全,防止烫伤)。
3、进给量 f 对切削变形的影响
刀具参数:κr=45°;κr'=8°;λs=0°;γo=10°;αo=7°;r=0.1 mm 。
切削用量: ap = 40 mm υc= 60 m /min 。
改变进给量: f= 0.2 ; 0.36 ; 0.51 ; 0.66 ( mm/r )。
用不同的进给量分别切削一段试棒,停车收集切屑并观察切削颜色(注意安全,防止烫伤)。
三.实验总结
(1)切削速度
切削塑性材料时,切削速度是通过切削温度和积屑瘤影响切削形变的.在切削45钢时,从实验求得切削速度对切削变形的影响.
切削铸铁等脆性材料时,一般不形成积屑瘤.当切削速度逐渐增大时,切屑变形压缩比相应减小,变形减小.
在实际生产中,高速切削即是利用提高切削速度来减小切屑变形,减小切削力,提高生产率.
(2)进给量
进给量增大时,切削厚度随之增大,切屑变形减小
(3)前角
前角的大小直接影响切屑的变形,前角比较小的时候,被切削金属变形比较大,切削力大,如果前角增大,被切削金属变形减少,可以使切削力有所下降,刀具前角一般取-5°~
25°,另外前角增大,产生的切削热也会相应减少,例如使用高速钢车刀时,前角从10°增大到18°时,切削温度会减小15%。
当以中等切削速度(5~60m/min)切削塑韧性金属材料时,由于切屑底面与前刀面得挤压和剧烈摩擦,会使切屑底层的流动速度低于其上层的流动速度。
当此层金属与前刀面之间的摩擦力超过切屑本身分子间结合力时,切屑底层的一部分新鲜金属会粘结在刀刃附近,形成一个硬块,称为积屑瘤。
积屑瘤可增大刀具实际的工作前角,使切削力减少,相应的变形减少,但积屑瘤会影响工件表面质量。
因此,粗加工可利用积屑瘤保护刀尖;精加工时应避免产生,保证加工质量。
可使用高速(100m/min以上)或低速(5m/min以下)切削,避免积屑瘤。