轴类零件的自动检测装置设计
轴类零件圆柱度误差自动检测系统的设计学位论文
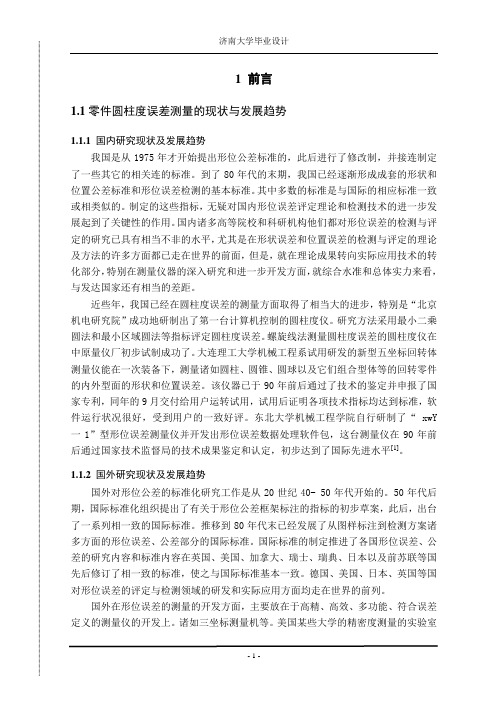
1前言1.1零件圆柱度误差测量的现状与发展趋势1.1.1国内研究现状及发展趋势我国是从1975年才开始提出形位公差标准的,此后进行了修改制,并接连制定了一些其它的相关连的标准。
到了80年代的末期,我国已经逐渐形成成套的形状和位置公差标准和形位误差检测的基本标准。
其中多数的标准是与国际的相应标准一致或相类似的。
制定的这些指标,无疑对国内形位误差评定理论和检测技术的进一步发展起到了关键性的作用。
国内诸多高等院校和科研机构他们都对形位误差的检测与评定的研究已具有相当不非的水平,尤其是在形状误差和位置误差的检测与评定的理论及方法的许多方面都已走在世界的前面,但是,就在理论成果转向实际应用技术的转化部分,特别在测量仪器的深入研究和进一步开发方面,就综合水准和总体实力来看,与发达国家还有相当的差距。
近些年,我国已经在圆柱度误差的测量方面取得了相当大的进步,特别是“北京机电研究院”成功地研制出了第一台计算机控制的圆柱度仪。
研究方法采用最小二乘圆法和最小区域圆法等指标评定圆柱度误差。
螺旋线法测量圆柱度误差的圆柱度仪在中原量仪厂初步试制成功了。
大连理工大学机械工程系试用研发的新型五坐标回转体测量仪能在一次装备下,测量诸如圆柱、圆锥、圆球以及它们组合型体等的回转零件的内外型面的形状和位置误差。
该仪器已于90年前后通过了技术的鉴定并申报了国家专利,同年的9月交付给用户运转试用,试用后证明各项技术指标均达到标准,软件运行状况很好,受到用户的一致好评。
东北大学机械工程学院自行研制了“ xwY 一1”型形位误差测量仪并开发出形位误差数据处理软件包,这台测量仪在90年前后通过国家技术监督局的技术成果鉴定和认定,初步达到了国际先进水平[1]。
1.1.2国外研究现状及发展趋势国外对形位公差的标准化研究工作是从20世纪40- 50年代开始的。
50年代后期,国际标准化组织提出了有关于形位公差框架标注的指标的初步草案,此后,出台了一系列相一致的国际标准。
轴心轨迹检测仪结构设计
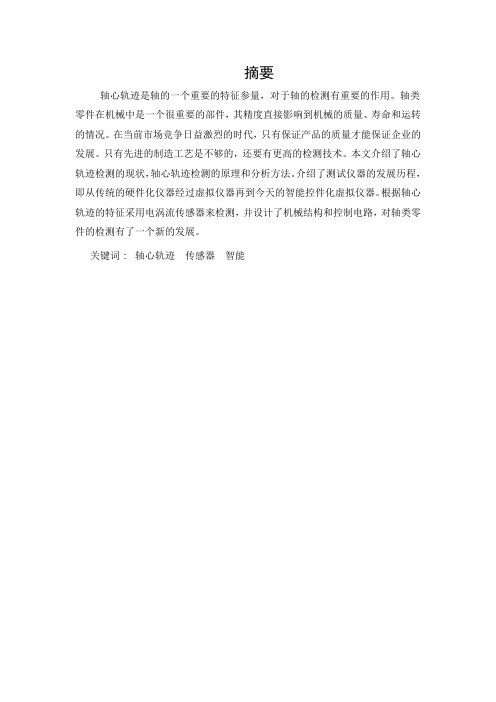
摘要轴心轨迹是轴的一个重要的特征参量,对于轴的检测有重要的作用。
轴类零件在机械中是一个很重要的部件,其精度直接影响到机械的质量、寿命和运转的情况。
在当前市场竞争日益激烈的时代,只有保证产品的质量才能保证企业的发展。
只有先进的制造工艺是不够的,还要有更高的检测技术。
本文介绍了轴心轨迹检测的现状,轴心轨迹检测的原理和分析方法。
介绍了测试仪器的发展历程,即从传统的硬件化仪器经过虚拟仪器再到今天的智能控件化虚拟仪器。
根据轴心轨迹的特征采用电涡流传感器来检测,并设计了机械结构和控制电路,对轴类零件的检测有了一个新的发展。
关键词:轴心轨迹传感器智能ABSTRACTOrbit is an important axis of the characteristic parameters for the detection axis play an important role. Shaft in machinery is a very important component, the precision of a direct impact on mechanical quality of life and functioning of the situation. In the current era of increasingly competitive market, only to ensure the quality of products can ensure the development of enterprises. Only advanced manufacturing technology is not enough, but also has a higher detection technology. This article describes the detection of core path status, orbit test of the theory and analysis. Describes the development process of testing instruments, from traditional hardware-based devices through virtual machines to today's intelligent control of virtual instruments. According to the characteristics of orbits with eddy current sensors to detect and design the mechanical structure and control circuitry, the detection of the shaft with a new development.Key words: Axis Orbit Intelligent Sensor第1章绪论1.1研究目的和意义随着经济的发展,世界贸易日益频繁,各国之间的竞争日趋激烈。
电机轴轴向、径向窜动检测装置研究要点

摘要本设计主要研究电机轴轴向径向窜动的检测方法。
首先提出对电机轴窜动监测的重要性,分析其轴向径向窜动的原因。
考察了目前电机轴窜动监测的手段和装置的现状,设计出了一套比较完善的在线监测系统。
根据测量原理,考虑电机轴窜动的频率和特点,综合考虑各种检测系统的优缺点,提出适合本系统的方案设计:采用非接触性位移传感器来作为测量器件,导出轴窜动的电压信号,分析此信号的特征,选用相匹配的模数转换器。
由于本系统中有轴向和径向两路信号,需选择相适应的多路模拟开关,再把数据送单片机进行处理,并进行显示,如果所采集的数据超出工业要求,系统会自动报警。
系统的各种功能都由软件来实现。
软件的设计包括主程序,定时中断服务程序,数据的采集,显示子程序,键盘子程序。
关键词:电机轴,窜动,单片机,传感器,模数转换器AbstractThe examination method of electricity engine shaft axial radial direction shakes is mainly researched in this design. First, proposed the importance of examination the electricity engine shaft moves the monitor, analyzes the reasons why its axial radial direction can vibrate. To study the situation of the methods and the equipment and set of quite perfect on-line control systems has been designed. According the principle of surveying, and considering the frequency and the characteristic of the electricity engine shaft shakes, the synthesis considered each kind of examination system the good and bad points, proposed the design plan which suits this system: The non-contact transmitter to survey signal is used, derives voltage which the axis shakes. The characteristic of this signal is analyzed, and to select A/D switch which matches. Because of in this system has two groups signals of axial and the radial direction, the multichannel analog switch which adapts is choused, the last delivers the data to the mcu is carried on processing, and carried on the demonstration, if the data surpasses the industry request, the system can auto-alarms. Each kind of function of the system all realized by the software. The main routine, interrupt service program, data gathering, the demonstration program and the keyboard program are included in the software design.Keywords: electricity engine shaft, shake, mcu, transmitter, A/D switch0 引言电机是工农业及各行各业中使用最广泛的动力设备,其种类繁多,数量极大,是电气工作者在维修中涉及最多的电气设备。
机电一体化毕业设计-轴类零件概要【范本模板】
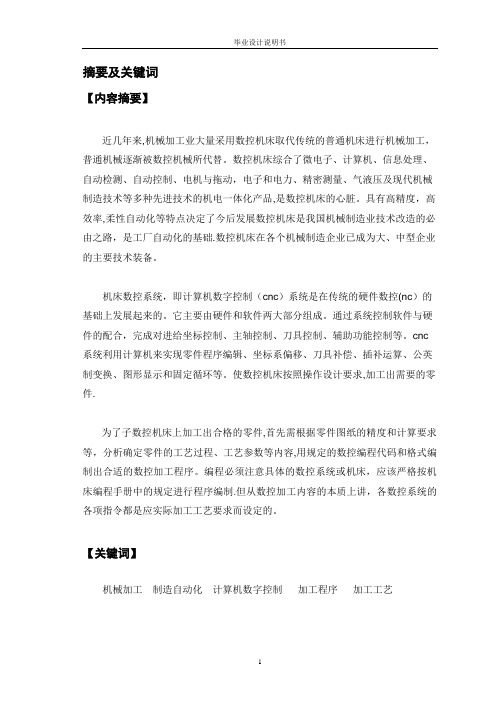
摘要及关键词【内容摘要】近几年来,机械加工业大量采用数控机床取代传统的普通机床进行机械加工,普通机械逐渐被数控机械所代替。
数控机床综合了微电子、计算机、信息处理、自动检测、自动控制、电机与拖动,电子和电力、精密测量、气液压及现代机械制造技术等多种先进技术的机电一体化产品,是数控机床的心脏。
具有高精度,高效率,柔性自动化等特点决定了今后发展数控机床是我国机械制造业技术改造的必由之路,是工厂自动化的基础.数控机床在各个机械制造企业已成为大、中型企业的主要技术装备。
机床数控系统,即计算机数字控制(cnc)系统是在传统的硬件数控(nc)的基础上发展起来的。
它主要由硬件和软件两大部分组成。
通过系统控制软件与硬件的配合,完成对进给坐标控制、主轴控制、刀具控制、辅助功能控制等。
cnc 系统利用计算机来实现零件程序编辑、坐标系偏移、刀具补偿、插补运算、公英制变换、图形显示和固定循环等。
使数控机床按照操作设计要求,加工出需要的零件.为了子数控机床上加工出合格的零件,首先需根据零件图纸的精度和计算要求等,分析确定零件的工艺过程、工艺参数等内容,用规定的数控编程代码和格式编制出合适的数控加工程序。
编程必须注意具体的数控系统或机床,应该严格按机床编程手册中的规定进行程序编制.但从数控加工内容的本质上讲,各数控系统的各项指令都是应实际加工工艺要求而设定的。
【关键词】机械加工制造自动化计算机数字控制加工程序加工工艺一、数控机床的简介:数控机床是数字控制机床(Computer numerical control machine tools)的制编码或其他符号指令规定的程序,并将其译码,从而使机床动作数控折弯机并加工零件。
1.1数控系统的发展趋势从目前世界上数控技术及其装备发展的趋势来看,数控系统正在向电气化、电子化、高速化、精密化等方面高速发展,其主要研究热点有以下几个方面:1.1。
1 高精高速高效化效率、质量是先进制造技术关键的性能指标,是先进制造技术的主体。
死顶尖定位无鸡心夹头驱动轴类零件旋转装置的研究
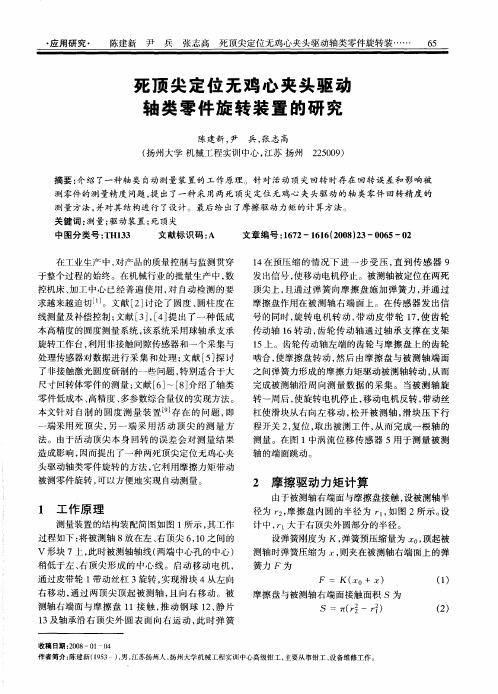
第3 7卷
第2 3期
图 l 测量装置装配示意图
运动 , 恢复初 始状态 。
3 结 束 语
轴类 零件 回转精 度测 量 采用 两死 顶尖 定位 方
式 , 以克服外 因素对测 量的影 响 , 可 提高测 量精度 。
本文提 出的这种方 法避 开了鸡心 夹头 , 于实现 自 便 动化 。文 中关 于摩 擦驱 动力矩 的计 算公式 , 为合理
传动轴 l 6转动 , 轮传 动 轴通 过 轴 承支 撑在 支架 齿
线测量及 补偿控制 ; 文献 [ ] [ ] 出 了一种 低成 3 ,4 提 本高精度 的 圆度 测量 系统 , 系统 采用球 轴承 支承 该 旋转工作 台 , 利用 非接触 间隙传感 器和一 个采集 与 处理传 感器对数 据进 行采 集 和处 理 ; 献 [ ] 讨 文 5探
设 弹簧 刚度 为 K , 弹簧预压 缩量为 z , 被 。顶起
测轴 时弹簧压缩 为 z, 夹在被测 轴右端 面上 的弹 则 簧 九 F为
F = K( n+z) z () 1
V形块 7上 , 时被测轴 轴线 ( 端 中心孔 的 中心 ) 此 两
稍低 于左 、 顶尖 形 成 的 中心线 。启 动移 动 电机 , 右 通过皮 带轮 1 动丝杠 3旋转 , 带 实现滑块 4从左 向 右移 动 , 过 两顶 尖顶 起 被测轴 , 向右移 动 。被 通 且 测轴右端 面 与摩 擦 盘 1 1接触 , 动钢 球 1 、 片 推 2静 l 3及轴 承沿右 顶 尖 外 圆表 面 向右 运 动 , 时 弹 簧 此
关 键词 : 量 ; 测 驱动 装置 ; 死顶 尖 中图分类号 : HI 3 T 3 文献标 识码 : A 文章编 号 :6 2—1 1 (0 8 2 17 6 6 2 0 )3—0 6 一O 05 2
轴盘类件超声自动探伤机数字样机设计-任务书
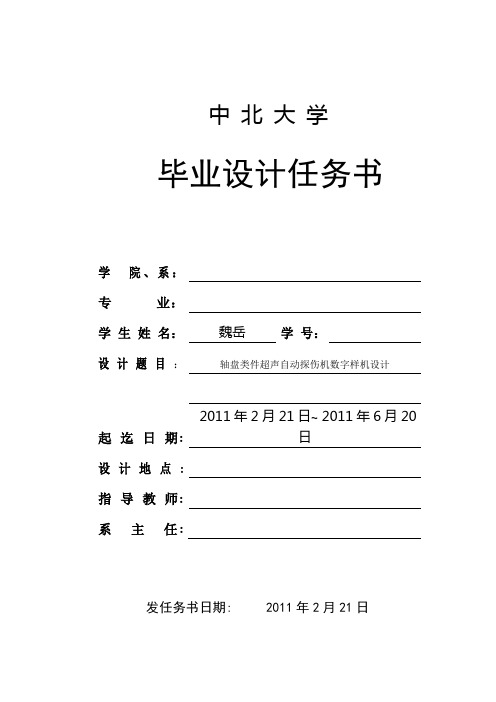
中北大学毕业设计任务书学院、系:专业:学生姓名:魏岳学号:设计题目:轴盘类件超声自动探伤机数字样机设计起迄日期: 2011年2月21日~2011年6月20日设计地点:指导教师:系主任:发任务书日期: 2011年2月21日毕业设计任务书1.毕业设计课题的任务和要求:该同学承担“轴盘类件超声自动探伤机数字样机设计”任务。
设计要求:设计出轴盘件超声自动检测装置三维装配模型并进行运动学和动力学仿真。
该检测装置能实现工件旋转,探头沿工件的径向和轴向进给扫描,超声的耦合采用水浸耦合方式。
2.毕业设计课题的具体工作内容(包括原始数据、技术要求、工作要求等):技术要求:(1)系统功能实现一定尺寸范围内各种轴、盘类金属零件自动超声检测的功能,重点实现各种型号小汽车变速箱各种规格齿轮、轴的毛坯和成品内部缺陷检测。
它可以发现齿轮和轴类毛坯中各种缺陷及缺陷的位置,按规范要求自动判别是否报废或返修,并予以显示。
除了装、卸料外和更换探头外,全部操作过程在计算机的控制下自动完成。
(2)被测工件的基本技术参数:1>盘类零件:外径<ф250mm,厚度<50mm.2>轴类零件:长度<400mm,直径ф20mm~ф50mm(3)检测要求的运动方式及运动参数1> 运动方式:工件旋转(C 轴),探头沿工件的径向(X 轴)和轴向进给(Z 轴)扫描;2> C 轴和X 轴、C 轴和Z 轴可以实现联动;3> 探头径向和轴向最大进给量:盘类250mm×400mm和250mm×100mm轴类250mm×400mm和100mm×450mm4> 主轴转速范围为:5~60r/min;5> 进给速度:0.5~10mm/r(这里的每转是指工件旋转一周的进给量)(4)其它要求超声检测要用水进行耦合,工件和探头都要浸在水中,要有供水和排水机构,也要考虑防锈问题。
具体工作内容:(1)制定总体方案;(2)设计工作台装配图(3) 设计工作台外观图(4) 设计重要非标零件(5)设计检测装置三维装配图;(6)对检测装置三维装配体进行运动学和动力学仿真;(7)设计重要零件工程图;(8)翻译外文资料。
轴类零件中心找正器的原理
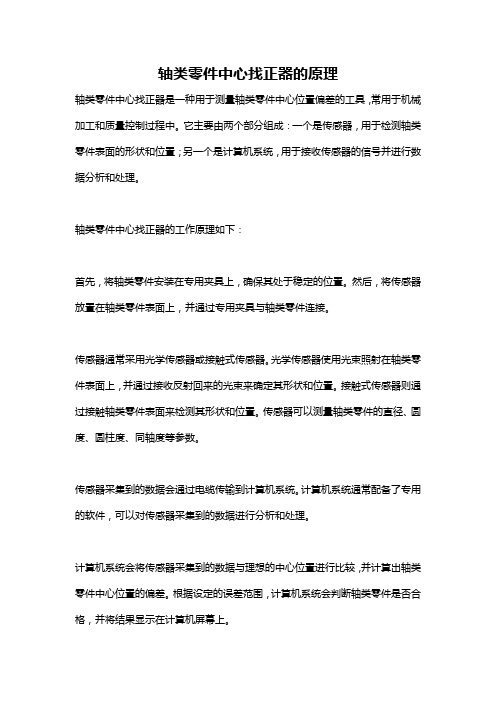
轴类零件中心找正器的原理轴类零件中心找正器是一种用于测量轴类零件中心位置偏差的工具,常用于机械加工和质量控制过程中。
它主要由两个部分组成:一个是传感器,用于检测轴类零件表面的形状和位置;另一个是计算机系统,用于接收传感器的信号并进行数据分析和处理。
轴类零件中心找正器的工作原理如下:首先,将轴类零件安装在专用夹具上,确保其处于稳定的位置。
然后,将传感器放置在轴类零件表面上,并通过专用夹具与轴类零件连接。
传感器通常采用光学传感器或接触式传感器。
光学传感器使用光束照射在轴类零件表面上,并通过接收反射回来的光束来确定其形状和位置。
接触式传感器则通过接触轴类零件表面来检测其形状和位置。
传感器可以测量轴类零件的直径、圆度、圆柱度、同轴度等参数。
传感器采集到的数据会通过电缆传输到计算机系统。
计算机系统通常配备了专用的软件,可以对传感器采集到的数据进行分析和处理。
计算机系统会将传感器采集到的数据与理想的中心位置进行比较,并计算出轴类零件中心位置的偏差。
根据设定的误差范围,计算机系统会判断轴类零件是否合格,并将结果显示在计算机屏幕上。
如果轴类零件中心位置的偏差在允许范围之内,那么轴类零件被认为是合格的;如果偏差超出允许范围,那么轴类零件被认为是不合格的。
不合格的轴类零件可能需要进行修正或重新加工。
轴类零件中心找正器具有以下优点:1. 准确度高:传感器可以高精度地测量轴类零件中心位置的偏差,保证了加工质量的稳定性。
2. 自动化程度高:计算机系统能够自动计算偏差并进行判断,减少了人工干预的可能性,提高了工作效率。
3. 数据化管理:计算机系统可以将测量数据存储在数据库中,方便后续的数据分析和质量控制。
4. 多功能性:轴类零件中心找正器不仅可以测量轴类零件的中心位置,还可以测量其他形状和位置参数,如直径、圆度、同轴度等,提供了更全面的质量控制。
总结起来,轴类零件中心找正器通过传感器测量轴类零件的形状和位置,然后通过计算机系统对测量数据进行分析和处理,最终确定轴类零件中心位置的偏差。
机电一体化专业教案:轴类零件的检测

教案实习训练二轴类零件的检测姓名:班级:学号:一、实训目的掌握千分尺、百分表的使用方法,测量轴类零件尺寸及径向圆跳动误差。
二、被测工件三、量具、工具千分尺、百分表、偏摆仪等四、量具的维护与保养(1)不可以把千分尺拿在手中任意挥动或摇转,这样会使精密的测微螺杆受到损伤。
(2)不能用千分尺测量正在旋转的工件或带有磁性的工件。
(3)百分表要轻拿轻放,上上好防锈油,放入指定的盒内(4)使用时表架要放稳,以免百分表跌落损坏。
(5)严防水、油等进入表内,不允许随便拆卸表的后盖。
(6)如果不是长期不用,测量杆不准涂凡士林或其他油类,以免影响测量杆移动的灵活性。
五、测量方法及步骤六、完成测量,判断零件合格性生产实习课题化教学教案首页教学环节教学内容与过程师生活动教学方法设计目的课堂组织:检查学生出勤、装束、精神状态。
师生互相问候。
调动学生激情,调节课堂气氛师生互动提醒学生做好上课准备一、复习旧知识1、游标卡尺的作用?答:可以测量外形尺寸、内径、深度。
2、万能角度尺组合测量范围有哪些?(1) 由基尺、角尺、直尺组合,可以测量可测量0°~50°(2) 由基尺、直尺组合,可以测量可测量50°~140°(3) 由基尺、角尺组合,可以测量可测量140°~230°(4) 由基尺可以测量可测量230°~320°二、导入新课1、播放视频2、思考一、轴类零件的用途是什么?思考二、如何判断轴类零件的合格性?思考问题回答提问积极响应启发式教学巩固已学知识,使学生在掌握旧知的基础上,拓展知识面,加强对旧知的应用,并由旧知导入新课,给学生设置悬念,明确新学知识的作用。
5一、外径千分尺1.外径千分尺结构外径千分尺如图所示,主要由尺架、固定测砧、测微螺杆、固定套筒、微分筒、测力装置、隔热片、锁紧装置等组成。
2. 刻线原理千分尺应用螺旋副的传动原理,将角位移转变为直线位移。
- 1、下载文档前请自行甄别文档内容的完整性,平台不提供额外的编辑、内容补充、找答案等附加服务。
- 2、"仅部分预览"的文档,不可在线预览部分如存在完整性等问题,可反馈申请退款(可完整预览的文档不适用该条件!)。
- 3、如文档侵犯您的权益,请联系客服反馈,我们会尽快为您处理(人工客服工作时间:9:00-18:30)。
轴类零件的自动检测装置设计徐莹1易琨21重庆工商大学2嘉陵)本田发动机公司摘要:设计了一套轴类零件的自动检测装置,该装置能检测轴类零件的直径、圆度和圆跳动。
本装置的测量方法为3S90b,且为定点测量,可同时对三个截面进行测量。
介绍了总体方案设计、部件设计和软件设计。
关键词:轴类零件,自动检测,部件设计,摩擦驱动,界面Design of Automatic Checkout Equipment Used for Axle PartX u Ying Yi KunAbstr act:A suit of the automatic checkou t equip ment used for the axle parts is desig ned.The equip ment can check automat2 ically the diameter,circle degree and circle jumpiness.The3S90b measure metho d is used for the equipment and the measure points are fixed,the equipment can measure parameters i n three sections at the same time.The project design in the g eneral,as2 semblies design and software design are mainly presen ted.Keywor ds:axle part,automatic checkout,assemblies design,rubbing drive,interface1引言本仪器检测的轴类零件为某部件的传动轴。
该零件的轴上有一些螺旋槽和通孔;其长径比较大,长度一般为300~500mm,直径为15~30mm。
在部件装配中,它要和孔接触且配合精度要求较高,故该零件的尺寸精度、圆度和圆跳动均要求较高。
另外,零件的外圆磨削加工是在无心外圆磨床上进行的,采用贯穿磨削法,每分钟大约加工6~10件,所以要求检测方法简单、高效。
由于缺乏合适的专用检测设备,工厂里工件尺寸精度与形位精度的检测不是由工人通过测量器具手工完成,就是采用价格昂贵的通用量仪进行测量。
对前者,当工件批量比较大时,需要花大量的人力、物力和时间,且人为误差大;对后者,其仪器调整过程繁琐,测量时间长,效率低。
此外由于通用量仪大多属于计量型仪器,对环境和操作人员要求高,故不适用于生产现场。
因此,有必要研制一套使用范围广、测量成本低的自动检测装置。
2原始测量方法211圆度的测量测量圆度的方法有单点法、二点法、三点法与坐标法,本设计采用的是三点法。
三点法是对被测实际轮廓在两个固定测量支承和一个可在测量方向上移动的测头之间所进行的测量。
测头位于固定测量支承夹角(A或180b-A)之外的,称为顶式三点测量,如图1a、图1b、图1c、图1d所示;测头位于固定测量支承夹角(A或180b-A)之内的,称为鞍式三点测量,如图1e、图1f所示,我们采用的是图1a方式。
图1三点法测量圆度212径向圆跳动的测量根据GB1958)80的有关规定,圆跳动的检测方法有三类,即用同心套、V形块和两顶尖,本设计采用V形块。
当圆跳动\0101mm时,采用此法较为得当。
而精度较高时用这种方法,其检测精度要受V形块精度和实际基准要素形状误差的综合影响。
3装置的总体设计及其主要部件的功用装置的总体设计如图2所示,由图可看出本装置主要由工件传送装置、工件装夹装置、测量装置和工件驱动装置四部分组成。
311工件传送装置工件传送装置的作用是将被测工件自动地从其堆放位置输送到工件装夹装置中的V形块上,它包括上料装置、皮带传送装置和送料装置三部分。
832005年第39卷l5收稿日期:2004年8月11工件传送装置21工件驱动装置31测量装置41工件装夹装置图2检测装置的装配图(1)上料装置上料装置的功能是把被加工零件整理好,按照一定的方向排列起来,并以一定的节拍逐个地输送出去。
上料装置的工作原理是由电机经蜗杆蜗轮减速后带动与轮相连的连杆运动,从而带动与连杆相连的上料板上下运动,将被测工件上升到一定的高度后,再将其送到皮带传送装置上。
(2)皮带传送装置皮带传送装置将从上料装置送来的被测工件送到送料板上。
(3)送料装置送料装置的工作原理是电机经蜗杆蜗轮减速后,带动轮转动,从而带动与轮相连的摇杆摆动,经滑块使送料板在工作台上往复运动,将被测工件送到工件装夹装置中的V型块上。
312工件装夹装置工件装夹装置的功用是利用两个V形块对工件进行轴向定位,以保证在测量过程中,工件被驱动装置中的压紧轮压紧后,不会存在轴向串动。
此时工件卧放,用两个V形块对工件进行定位,是轴类零件检测时常用的定位方式。
它用外圆柱面体现其基准,结构简单,安装方便,易于实现自动上料和送料。
但因为该零件是细长轴,卧放时会因工件的自重而产生变形,当其旋转后会形成鼓状。
不过,只要调节好两个V形块之间的距离,就可以解决这个问题。
313工件驱动装置工件驱动装置是利用步进电机通过减速器带动摩擦轮,摩擦轮再驱动工件旋转,以实现对轴截面的测量。
摩擦轮放在V形块内侧,且可浮动。
在工件上方有两个小轮对工件施加一定的力(作用在V形块上),这个力不宜多大,只要使工件与摩擦轮可靠接触即可。
与一般的驱动方式相比,其特点是摩擦轮为圆柱体,加工简单、精度高,可以无间隙地实现正反向传动,可以在动力连续传递情况下无级地调节传动比。
当摩擦轮之一为非金属材料时,噪声较低。
314工件测量装置工件测量装置的工作原理是当工件到达测量位置后,发出信号,液压缸的上腔进油,推动活塞及活塞杆下行,与活塞杆相连的压板随之下行,使得固定在横梁上的传感器沿立柱向下运动;当其到达设定位置后,压下行程开关,使得液压缸停止进油,并保持此状态直到测量结束,以便实现传感器的读数操作;当测量结束后,液压缸的下腔进油,使得传感器又向上移动,离开检测位置,方便工件的取放。
传感器测得的信号经数据采集卡处理后再传送到软件中进行运算,以实现对轴类零件三个指标的自动检测。
4软件设计本检测软件用来对传感器测得的数据进行处理,以实现对直径、圆度和圆跳动的检测,并判断其是否超差,同时还要作出误差曲线图。
411用户界面的设计主窗口界面如图3所示。
图3主窗口界面/传感器读数0是传感器测得的数据。
/实时半径0则是根据传感器读数,采用3点求圆的办法,求得该截面的实时半径值,配合工件旋转的相位关系,扫描出该截面的廓形。
传感器使用一段时间后,可能会出现测头的磨损,如果不对其进行处理,必将影响检测结果,造成在验收工作中出现/误收0与/误废0现象,故必须对传感器进行校准。
校准方法是:在V形块上放入标准心轴,然后按下/传感器校准0按钮后,仪器执行补84工具技术偿动作,自动记录补偿值,对测量读数进行补偿修正,回显在自动补偿对话框中。
直径的误差曲线图是根据传感器测得的数据转换成直径误差值后,再结合工件转动的相位形成的图形。
在该图形中,可根据出现正弦波的个数来判断出所测截面的棱边数,这对采用3S90b这种测量方法来说是很重要的,因为要采用这种方法测量圆度时必须知道圆的棱边数。
412评价(1)圆度误差圆度误差f的评价采用的是f=E$i n其中$i=r i-r0式中r i)))各测量点所在处的半径值r0)))理论半径值n)))测量点的个数(2)径向圆跳动误差径向圆跳动误差f的评价采用的是F=max(r i)-min(r i)式中r i)))各测量点所在处的半径值max(r i))))各测量点所在处的最大半径值min(r i))))各测量点所在处的最小半径值参考文献1机电一体化技术手册编委会.机电一体化技术手册.北京:机械工业出版社,20042成大先.机械设计手册.北京:化学工业出版社,20043于汶.零件尺寸的自动检测.河北:中国计量出版社, 19894曾宪铮.形位误差测量.北京:国防工业出版社,19795卢文祥,杜润生.工程测试与信息处理.武汉:华中理工大学出版社,1994第一作者:徐莹,重庆工商大学机械工程学院,400067重庆市收稿日期:2004年8月用MOD法评价齿轮精度指标的测量效率裴玲李峰冯佩兰湖北汽车工业学院摘要:介绍了模特排时法(MO D)的基本原理,用M OD法测定和评价了各项齿轮精度检测项目的测量效率,提出了合理选择齿轮精度检测项目的原则和方法。
关键词:齿轮,精度指标,模特排时法,测量效率,评价Evaluation of Measuring Efficiency of Gear Accuracy Item by MODPei Ling Li Feng Feng PeilanAbstr act:The basic principle o f Modular Arrangement o f Predetermined Ti me Standard(MOD)is introd uced.By using MO D,the measuring efficiency of inspection items about gear accuracy are determined and evaluated.The principle and method of reaso nably selecting inspection i tems about gear accuracy are presented.Keywor ds:gear,accuracy item,MOD,measuring efficiency,evaluatio n1引言精益生产方式的特点是消除一切浪费,追求精益求精和不断改善。
/精简0是精益生产的核心原则之一,要精简产品开发、设计、生产、管理中一切不产生附加值的工作,旨在以最优品质、最低成本和最高效率对市场需求作出最迅速的响应。
从质量角度来讲,精益生产追求高品质,要求不良产品为/零0,而且/零0废品不是在检验工位检测出来的,而应在不良产品产生的源头就予以消除。
从某种意义上来说,质量检验以精益生产方式的理念看来是一项不增加价值的生产活动。
当出现不良产品时,临时的补救措施是治标不治本的行动。
所以,加工完毕后的被动检验本身就是一种浪费。
在齿轮的精益生产方式中,在保证质量稳定的前提下,实现高标准、高可靠性、低成本的齿轮精度检验,是进一步降低生产成本、保证按时交货需要解决的问题。
运用工业工程(IE)的方法,研究齿轮各项精度指标的作业标准与测量效率,是减少废品、降低各种质量成本(如材料的损失、设备和人员工时的损失、额外的修复、挑选和追加检查、额外的检查员及检查工位等)的科学而有效的途径。