氨法脱硫工艺及操作运行简述
氨法脱硫 (2)

氨法脱硫1. 引言氨法脱硫是一种常用的烟气脱硫方法,广泛应用于各类工业排放源和燃煤工业。
该方法通过将氨与烟气中的二氧化硫反应生成氮化合物,从而实现脱硫的目的。
本文将对氨法脱硫的原理、工艺流程和应用进行详细介绍。
2. 氨法脱硫的原理氨法脱硫的原理是基于氨与二氧化硫的反应生成硫酸铵或亚硫酸铵。
反应方程式如下:SO2 + 2NH3 + H2O → (NH4)2SO3SO2 + 4NH3 + O2 → (NH4)2SO4氨法脱硫的核心反应是硫酸铵或亚硫酸铵的生成,这些化合物在水中呈现亲水性,能够很容易地被吸收或被塔内的液相吸附剂捕集。
3. 氨法脱硫的工艺流程氨法脱硫的工艺流程一般包括烟气处理和液相吸附剂再生两个主要步骤。
3.1 烟气处理烟气处理是氨法脱硫过程的关键步骤,主要包括烟气与氨的混合、反应和脱硫产物的分离三个阶段。
(注意:这里可以根据实际情况添加更多的细节描述,例如具体的设备和操作步骤)3.1.1 烟气与氨的混合烟气与氨在脱硫塔内进行混合,通常使用喷射方式进行。
喷射器喷入的氨能够与烟气充分接触,实现脱硫反应的进行。
3.1.2 反应烟气中的二氧化硫与氨在反应器内发生反应,生成硫酸铵或亚硫酸铵。
反应装置通常采用多级反应器或者喷雾式反应器,以提高反应效率。
3.1.3 脱硫产物的分离在脱硫过程中生成的硫酸铵或亚硫酸铵溶液需要与烟气分离。
分离装置通常采用沉淀器或过滤器,将固体脱硫产物分离出来,然后进一步进行处理或处置。
3.2 液相吸附剂再生液相吸附剂再生是指将吸附剂中的脱硫产物从吸附剂中解吸或者还原出来,使吸附剂重新可用于脱硫过程。
吸附剂的再生可以通过几种方式实现,如加热、稀释和脱水等方法。
4. 氨法脱硫的应用氨法脱硫广泛应用于各种工业排放源和燃煤工业,例如电厂、钢铁厂、化工厂等。
其主要优点包括脱硫效率高、设备投资低、适用性广等。
然而,氨法脱硫也存在着一些缺点,如对环境污染、产生二次污染等问题。
5. 结论氨法脱硫是一种常用的烟气脱硫方法,通过氨与二氧化硫的反应生成硫酸铵或亚硫酸铵来实现脱硫的目的。
焦化厂氨法脱硫方案
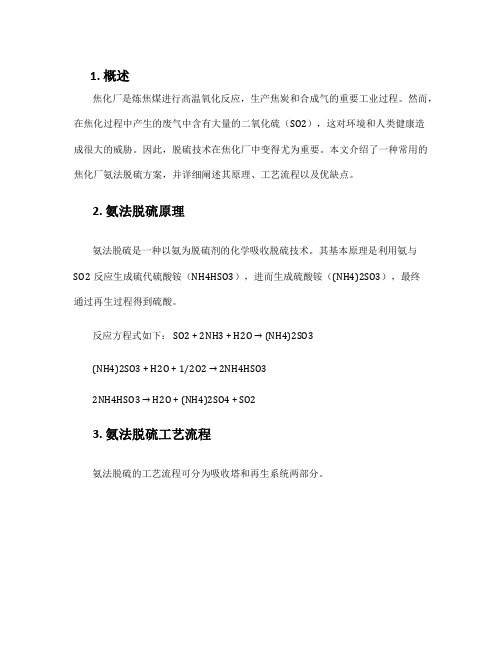
1. 概述焦化厂是炼焦煤进行高温氧化反应,生产焦炭和合成气的重要工业过程。
然而,在焦化过程中产生的废气中含有大量的二氧化硫(SO2),这对环境和人类健康造成很大的威胁。
因此,脱硫技术在焦化厂中变得尤为重要。
本文介绍了一种常用的焦化厂氨法脱硫方案,并详细阐述其原理、工艺流程以及优缺点。
2. 氨法脱硫原理氨法脱硫是一种以氨为脱硫剂的化学吸收脱硫技术。
其基本原理是利用氨与SO2反应生成硫代硫酸铵(NH4HSO3),进而生成硫酸铵((NH4)2SO3),最终通过再生过程得到硫酸。
反应方程式如下: SO2 + 2NH3 + H2O → (NH4)2SO3(NH4)2SO3 + H2O + 1/2O2 → 2NH4HSO32NH4HSO3 → H2O + (NH4)2SO4 + SO23. 氨法脱硫工艺流程氨法脱硫的工艺流程可分为吸收塔和再生系统两部分。
3.1 吸收塔吸收塔是实现氨法脱硫的核心设备,其结构一般为填料塔或喷淋塔。
废气在塔内与氨水进行接触吸收,将SO2转化为硫代硫酸铵。
吸收塔内还需要加入适量的催化剂,并保持适宜的温度和压力,以提高脱硫效果。
3.2 再生系统再生系统主要包括还原和吹扫两个工序。
在还原工序中,通过加热氨法脱硫液,使硫代硫酸铵分解为硫化氢(H2S),并进一步通过氧化反应生成硫酸。
吹扫工序利用气体吹扫方式将已生成的硫酸从吸收塔中移除,同时也将塔内吸收液中余留的SO2一起带走。
4. 氨法脱硫方案的优缺点4.1 优点•脱硫效率高:氨法脱硫可以将焦化厂废气中的SO2去除率达到90%以上。
•脱硫产物资源化利用:氨法脱硫产生的硫酸可以用于生产肥料等产品。
•设备相对简单:氨法脱硫设备结构相对简单,易于运维和维修。
4.2 缺点•进料水质需求高:氨法脱硫对进料水质要求较高,水质差会影响脱硫效果。
•产生氨气和硫化物:氨法脱硫过程中会产生氨气和硫化物等有害物质,需要适当处理以符合环保要求。
•需要大量的氨气:为了保证脱硫效果,氨法脱硫需要大量的氨气作为脱硫剂,这增加了成本和安全风险。
氨法脱硫工艺流程
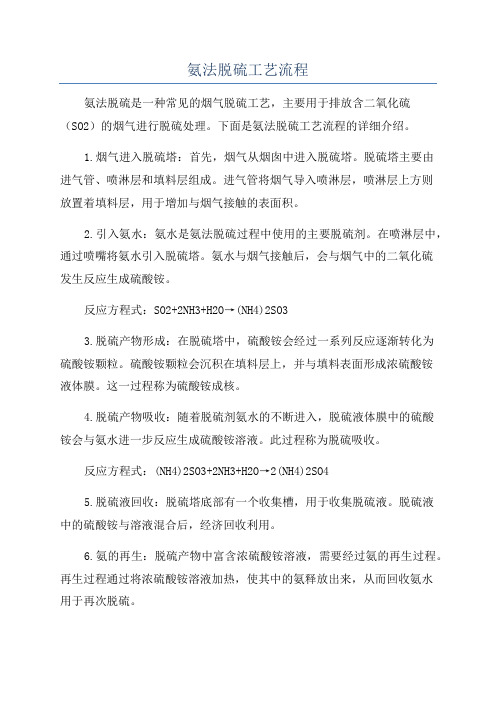
氨法脱硫工艺流程氨法脱硫是一种常见的烟气脱硫工艺,主要用于排放含二氧化硫(SO2)的烟气进行脱硫处理。
下面是氨法脱硫工艺流程的详细介绍。
1.烟气进入脱硫塔:首先,烟气从烟囱中进入脱硫塔。
脱硫塔主要由进气管、喷淋层和填料层组成。
进气管将烟气导入喷淋层,喷淋层上方则放置着填料层,用于增加与烟气接触的表面积。
2.引入氨水:氨水是氨法脱硫过程中使用的主要脱硫剂。
在喷淋层中,通过喷嘴将氨水引入脱硫塔。
氨水与烟气接触后,会与烟气中的二氧化硫发生反应生成硫酸铵。
反应方程式:SO2+2NH3+H2O→(NH4)2SO33.脱硫产物形成:在脱硫塔中,硫酸铵会经过一系列反应逐渐转化为硫酸铵颗粒。
硫酸铵颗粒会沉积在填料层上,并与填料表面形成浓硫酸铵液体膜。
这一过程称为硫酸铵成核。
4.脱硫产物吸收:随着脱硫剂氨水的不断进入,脱硫液体膜中的硫酸铵会与氨水进一步反应生成硫酸铵溶液。
此过程称为脱硫吸收。
反应方程式:(NH4)2SO3+2NH3+H2O→2(NH4)2SO45.脱硫液回收:脱硫塔底部有一个收集槽,用于收集脱硫液。
脱硫液中的硫酸铵与溶液混合后,经济回收利用。
6.氨的再生:脱硫产物中富含浓硫酸铵溶液,需要经过氨的再生过程。
再生过程通过将浓硫酸铵溶液加热,使其中的氨释放出来,从而回收氨水用于再次脱硫。
7.排放净化烟气:在脱硫后,氨法脱硫工艺会产生一小部分残留氨和硫化氢,需要进行二次净化。
这通常通过添加其他氧化剂,如过氧化钙(CaO2)或过氧化氢(H2O2),将残余的氨和硫化氢氧化成氮气和水蒸气,从而实现对脱硫后烟气的净化处理。
这就是氨法脱硫工艺的基本流程。
尽管这种方法具有较高的脱硫效率,但也存在一些问题,如氨泄漏、能源消耗和脱硫产物处理等。
因此,在实际应用中,需要根据具体情况选择最适合的脱硫工艺,并采取相应的措施来解决以上问题。
氨法脱硫脱硝工艺流程
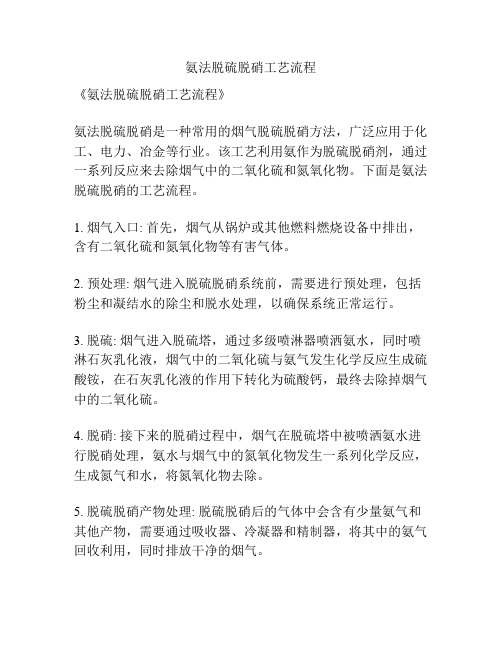
氨法脱硫脱硝工艺流程
《氨法脱硫脱硝工艺流程》
氨法脱硫脱硝是一种常用的烟气脱硫脱硝方法,广泛应用于化工、电力、冶金等行业。
该工艺利用氨作为脱硫脱硝剂,通过一系列反应来去除烟气中的二氧化硫和氮氧化物。
下面是氨法脱硫脱硝的工艺流程。
1. 烟气入口: 首先,烟气从锅炉或其他燃料燃烧设备中排出,含有二氧化硫和氮氧化物等有害气体。
2. 预处理: 烟气进入脱硫脱硝系统前,需要进行预处理,包括粉尘和凝结水的除尘和脱水处理,以确保系统正常运行。
3. 脱硫: 烟气进入脱硫塔,通过多级喷淋器喷洒氨水,同时喷淋石灰乳化液,烟气中的二氧化硫与氨气发生化学反应生成硫酸铵,在石灰乳化液的作用下转化为硫酸钙,最终去除掉烟气中的二氧化硫。
4. 脱硝: 接下来的脱硝过程中,烟气在脱硫塔中被喷洒氨水进行脱硝处理,氨水与烟气中的氮氧化物发生一系列化学反应,生成氮气和水,将氮氧化物去除。
5. 脱硫脱硝产物处理: 脱硫脱硝后的气体中会含有少量氨气和其他产物,需要通过吸收器、冷凝器和精制器,将其中的氨气回收利用,同时排放干净的烟气。
通过以上流程,氨法脱硫脱硝工艺可以有效地去除燃煤和燃气燃烧过程中产生的有害气体,符合环保要求,是一种成熟稳定的脱硫脱硝技术。
氨法脱硫工艺流程
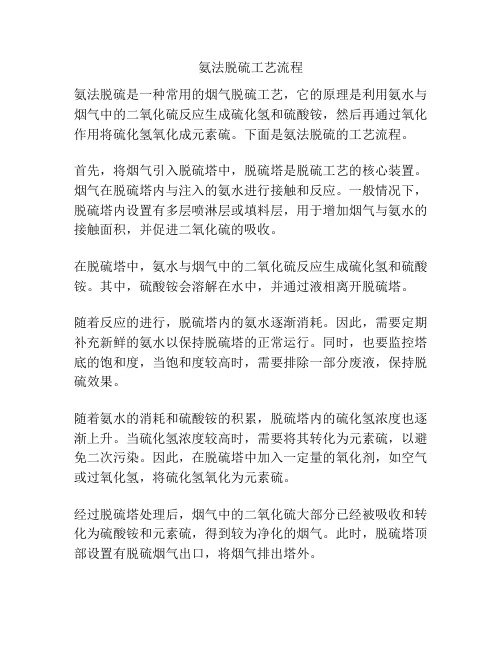
氨法脱硫工艺流程
氨法脱硫是一种常用的烟气脱硫工艺,它的原理是利用氨水与烟气中的二氧化硫反应生成硫化氢和硫酸铵,然后再通过氧化作用将硫化氢氧化成元素硫。
下面是氨法脱硫的工艺流程。
首先,将烟气引入脱硫塔中,脱硫塔是脱硫工艺的核心装置。
烟气在脱硫塔内与注入的氨水进行接触和反应。
一般情况下,脱硫塔内设置有多层喷淋层或填料层,用于增加烟气与氨水的接触面积,并促进二氧化硫的吸收。
在脱硫塔中,氨水与烟气中的二氧化硫反应生成硫化氢和硫酸铵。
其中,硫酸铵会溶解在水中,并通过液相离开脱硫塔。
随着反应的进行,脱硫塔内的氨水逐渐消耗。
因此,需要定期补充新鲜的氨水以保持脱硫塔的正常运行。
同时,也要监控塔底的饱和度,当饱和度较高时,需要排除一部分废液,保持脱硫效果。
随着氨水的消耗和硫酸铵的积累,脱硫塔内的硫化氢浓度也逐渐上升。
当硫化氢浓度较高时,需要将其转化为元素硫,以避免二次污染。
因此,在脱硫塔中加入一定量的氧化剂,如空气或过氧化氢,将硫化氢氧化为元素硫。
经过脱硫塔处理后,烟气中的二氧化硫大部分已经被吸收和转化为硫酸铵和元素硫,得到较为净化的烟气。
此时,脱硫塔顶部设置有脱硫烟气出口,将烟气排出塔外。
最后,脱硫塔底部的废液经过处理后可回收利用。
一般来说,废液中含有一定的硫酸铵,在经过脱水处理后可以得到硫酸铵结晶,作为化肥的原料。
总之,氨法脱硫工艺是一种有效的烟气脱硫方法。
通过脱硫塔中的反应和氧化过程,能够将二氧化硫转化为硫酸铵和元素硫,达到环保净化烟气的目的。
与此同时,也能够回收和利用废液中的硫酸铵,实现资源的循环利用。
氨法脱硫工艺
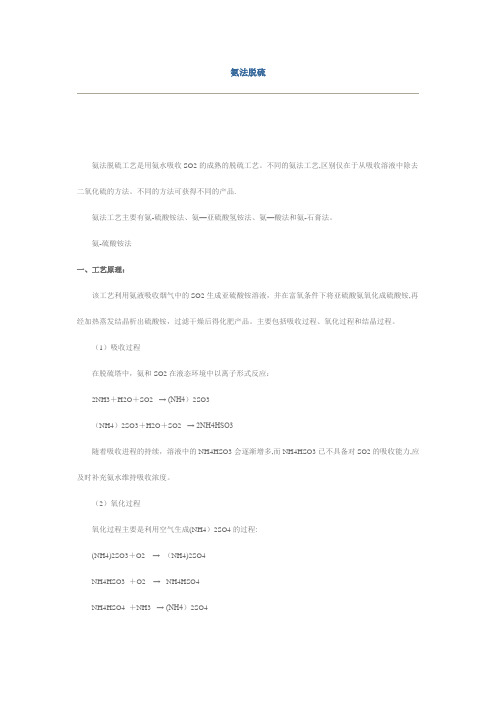
氨法脱硫氨法脱硫工艺是用氨水吸收SO2的成熟的脱硫工艺。
不同的氨法工艺,区别仅在于从吸收溶液中除去二氧化硫的方法。
不同的方法可获得不同的产品.氨法工艺主要有氨-硫酸铵法、氨—亚硫酸氢铵法、氨—酸法和氨-石膏法。
氨-硫酸铵法一、工艺原理:该工艺利用氨液吸收烟气中的SO2生成亚硫酸铵溶液,并在富氧条件下将亚硫酸氨氧化成硫酸铵,再经加热蒸发结晶析出硫酸铵,过滤干燥后得化肥产品。
主要包括吸收过程、氧化过程和结晶过程。
(1)吸收过程在脱硫塔中,氨和SO2在液态环境中以离子形式反应:2NH3+H2O+SO2 → (NH4)2SO3(NH4)2SO3+H2O+SO2 → 2NH4HSO3随着吸收进程的持续,溶液中的NH4HSO3会逐渐增多,而NH4HSO3已不具备对SO2的吸收能力,应及时补充氨水维持吸收浓度。
(2)氧化过程氧化过程主要是利用空气生成(NH4)2SO4的过程:(NH4)2SO3+O2 → (NH4)2SO4NH4HSO3 +O2 →NH4HSO4NH4HSO4 +NH3 → (NH4)2SO4(3)结晶过程氧化后的(NH4)2SO4经加热蒸发,形成过饱和溶液,(NH4)2SO4从溶液中结晶析出,过滤干燥后得到化肥产品硫酸铵。
二、工艺流程三、运行参数对脱硫效率的影响(1)氨水量;(2)氨水浓度;(3)反应温度。
四、值得注意的问题氨-硫酸铵法脱硫工艺存在的主要问题是存在二次污染的隐患,净化后的烟气含有微量的NH3和亚硫酸铵、硫酸铵气溶胶.氨法脱硫中的氨损失主要包括液氨蒸气损失和脱硫塔雾沫夹带损失两部分。
亚硫酸铵、硫酸铵气溶胶一旦形成,很难去除。
所以国外公司(如美国GE公司等)在脱硫塔出口设置电除雾器,以消除逃逸的氨损耗和亚硫氨气溶胶。
本公司采用独特的MW微雾净化系统可高效去除逃逸的氨损耗和亚硫氨气溶胶。
且空间及额外投资小。
氨-硫酸铵回收法具有丰富的原料,可以是液氨、氨水和碳铵,氨是人工合成,不像石灰石是天然资源,氨是化肥原料,脱硫后副产品为化肥,我国是人口、粮食和化肥大国,氨法很适合中国国情。
氨法脱硫工艺及操作运行简述
本工程项目是为动力中心配备一套完整的氨法脱硫工艺系统,一炉一塔配置,采用塔内结晶方式,塔外配置湿式电除尘器。
主要工艺系统包括:烟气系统、脱硫塔系统、塔顶湿式电除尘器系统、吸收剂储存及供应系统、硫铵后处理系统、氯离子控制及油灰分离系统、事故排放系统等。
1工艺简介1.1 烟气系统简介脱硫烟气系统的主要作用是进行脱硫装置的投入和切除,为脱硫运行提供烟气通道。
烟气系统包括以下设备及其系统:烟道、净烟气挡板门,挡板门密封风系统、非金属补偿器、脱硫塔、湿式电除尘器等。
原烟气从脱硫入口烟道先进入反应塔浓缩段,对热烟气进行喷淋降温,同时热烟气对硫铵浆液进行蒸发浓缩。
降温后的烟气经浓缩段除雾器后进入吸收段进行脱硫反应,经脱硫吸收后的烟气进入水洗段,通过水洗除去烟气中携带的微小硫铵晶体及氨逃逸,水洗后的净烟气进入塔外湿式电除尘器,经湿电出去剩余的粉尘、气溶胶、液滴后进入烟囱排放。
1.2 脱硫塔系统简介烟气进入脱硫塔浓缩段后,经洗涤、降温至50-60 C后进入脱硫塔吸收段烟气自下而上与喷淋液逆流接触反应,生成的(NH)2SO落入吸收液收集托盘进入循环浆液箱。
为氧化循环浆液箱浆池内的亚硫酸氨,设置了氧化空气系统,本脱硫系统共配有六台氧化风机(四用两备)。
氧化空气经氧化风分布管注入循环浆液箱浆池,对中间产物进行强制氧化生成脱硫副产品硫铵(NH4)2SO。
氨气通过氧化风管、氧化喷枪供给系统。
经过脱硫吸收后的净烟气,进入水洗段,通过水洗喷淋通过部分气溶胶和氨逃逸,再进入湿电系统。
循环浆液箱循环液经循环泵输送至喷淋层,在喷嘴处雾化成细小的液滴,自上而下地落下。
在液滴落回吸收液收集托盘的过程中,实现了对烟气中的二氧化硫、三氧化硫、氯化氢和氟化氢等酸性成份的吸收过程。
硫铵溶液经浓缩泵送入脱硫塔浓缩段,洗涤高温烟气,使烟气温度降到50-60 C,经浓缩泵循环喷淋,反复蒸发浓缩,最后形成固含量约10%-20%的硫铵溶液去硫铵缓冲箱。
按设计条件,循环浆液箱的pH为5.5〜6,如果氨加入过量,脱硫塔喷淋液中游离氨较多,其pH直将大于6,造成浪费;如果供氨量不足,脱硫塔喷淋液中含硫酸氢铵,pH小于5.5,此时脱硫效率将降低。
氨法脱硫方案
氨法脱硫工艺(一)、工艺概述二氧化硫和氮氧化物是大气污染物中影响较大的气态污染物,对人体、环境和生态系统有极大危害。
随着环保要求的日益严格,SO2排放的问题越来越受到关注。
二氧化硫主要源自于煤、石油等石化燃料的燃烧过程,以及矿石的焙烧、冶炼过程的烟气排放。
其中各种燃烧锅炉特别是火电厂锅炉排烟具有浓度低、烟气量大、浮尘多等特点而难以治理。
传统技术中,排放烟气中二氧化硫和氮氧化物净化技术通常是将脱硫和脱硝分开进行,这造成了排放烟气净化系统的复杂庞大、初始投资大、运行费用高等缺陷,严重制约了排放烟气脱硫脱硝的实际实施。
烟气脱硫技术主要以石灰石—石膏湿法、湿式氨法、旋转喷雾半干祛、炉内喷钙尾部增温活化、海水脱硫、电子束脱硫、烟气循环流化床脱硫等为主,其中石灰石法是现今世界上应用最为广泛的尾部烟气脱硫技术,其主要问题在于吸收剂(石灰或石灰石)的溶解度小,利用率低,废渣量大等。
自2002年,中国在电力行业内开展了大规模的SO 2治理工程。
随着电厂脱硫治理的开始,一大批国外烟气脱硫技术被不同的脱硫公司引进到国内,这其中的绝大部分是石灰石-石膏法。
随着烟气脱硫在国内电力行业的大规模使用,其他烟气脱硫方法也逐渐被使用、被认识,包括海水法、氨法、镁法、双碱法等,这其中,氨法正受到越来越广泛的关注。
氨法烟气脱硫工艺是采用氨做吸收剂除去烟气中的SO 2的工艺。
70年代初,日本与意大利等国开始研制氨法脱硫工艺并相继获得成功。
但由于技术经济等方面的原因在世界上应用较少。
进入90年代后,随着技术的进步和对氨法脱硫观念的转变,氨基脱硫技术的应用呈逐步上升的趋势。
1氨法FGD的主要特点1. 1脱硫塔不易结垢由于氨具有更高的反应活性,且硫酸铵具有极易溶解的化学特性,因此氨法脱硫系统不易产生结垢现象。
1. 2氨法对煤中硫含量适应性广氨法脱硫对煤中硫含量的适应性广,低、中、高硫含量的煤种脱硫均能适应,特别适合于中高硫煤的脱硫。
采用石灰石ö石膏法时,煤的含硫量越高,石灰石用量就越大,费用也就越高;而采用氨法时,特别是采用废氨水作为脱硫吸收剂时,由于脱硫副产物的价值较高,煤中含硫量越高,脱硫副产品硫酸铵的产量越大,也就越经济。
氨法脱硫工艺流程
氨法脱硫工艺流程1. 引言氨法脱硫是一种常用的烟气脱硫技术,通过在烟气中注入氨水,利用氨与烟气中的二氧化硫(SO2)发生化学反应来去除硫化物。
本文将详细描述氨法脱硫的工艺流程步骤和流程。
2. 工艺流程氨法脱硫主要包括烟气净化和吸收液再生两个主要步骤。
下面将详细介绍每个步骤的流程。
2.1 烟气净化烟气净化是指将燃煤等含有高浓度二氧化硫的烟气经过预处理后,使其达到适合进行后续吸收反应的条件。
2.1.1 烟道减压烟道减压是为了保证后续除尘设备的正常运行。
通过设置减压装置,将烟道内部压力降低至大气压以下。
2.1.2 粉尘除尘利用静电除尘器、布袋除尘器等设备,将烟气中的颗粒物除去,以保证后续吸收液的清洁度。
2.1.3 烟气预处理•温度调节:通过加热或冷却等方式,使烟气温度达到适宜吸收反应进行的范围。
•湿度调节:通过加湿或除湿等方式,使烟气湿度适合吸收液的工作条件。
•烟气脱硝:使用催化剂或选择性催化还原(SCR)装置,将烟气中的氮氧化物(NOx)转化为无害物质。
2.2 吸收液再生吸收液再生是指将吸收液中与二氧化硫反应生成的硫酸盐离子再生为二氧化硫,以便循环使用。
2.2.1 吸收塔在吸收塔内,将烟气与注入的稀释剂和饱和溶液进行接触和混合。
稀释剂一般为清水或稀硫酸溶液。
通过这一步骤,二氧化硫被溶解在吸收液中生成硫代硫酸盐。
2.2.2 氧化塔将吸收塔中的硫代硫酸盐氧化为硫酸盐,同时生成二氧化硫。
在氧化塔中,通过加入氧气或过氧化氢等氧化剂,使硫代硫酸盐转变为硫酸盐。
2.2.3 还原塔在还原塔中,通过向氧化后的溶液中通入二氧化硫,使硫酸盐还原为硫代硫酸盐,同时生成新的吸收液。
这一步骤实现了吸收液的再生。
2.2.4 后处理对于产生的二氧化硫进行处理,以达到排放标准。
常见的后处理方式包括催化转化、干燥吸附等。
3. 结论以上就是氨法脱硫工艺的详细步骤和流程。
通过烟气净化和吸收液再生两个主要步骤,可以有效去除烟气中的二氧化硫,并实现吸收液的循环利用。
氨-酸法治理so2的工艺流程及方程式
氨-酸法治理so2的工艺流程及方程式下载温馨提示:该文档是我店铺精心编制而成,希望大家下载以后,能够帮助大家解决实际的问题。
文档下载后可定制随意修改,请根据实际需要进行相应的调整和使用,谢谢!并且,本店铺为大家提供各种各样类型的实用资料,如教育随笔、日记赏析、句子摘抄、古诗大全、经典美文、话题作文、工作总结、词语解析、文案摘录、其他资料等等,如想了解不同资料格式和写法,敬请关注!Download tips: This document is carefully compiled by theeditor.I hope that after you download them,they can help yousolve practical problems. The document can be customized andmodified after downloading,please adjust and use it according toactual needs, thank you!In addition, our shop provides you with various types ofpractical materials,such as educational essays, diaryappreciation,sentence excerpts,ancient poems,classic articles,topic composition,work summary,word parsing,copy excerpts,other materials and so on,want to know different data formats andwriting methods,please pay attention!氨-酸法治理二氧化硫(SO2)的工艺流程及化学反应方程式详解氨-酸法,也称为氨法脱硫,是一种广泛应用于化工和能源行业中的二氧化硫(SO2)治理技术。
- 1、下载文档前请自行甄别文档内容的完整性,平台不提供额外的编辑、内容补充、找答案等附加服务。
- 2、"仅部分预览"的文档,不可在线预览部分如存在完整性等问题,可反馈申请退款(可完整预览的文档不适用该条件!)。
- 3、如文档侵犯您的权益,请联系客服反馈,我们会尽快为您处理(人工客服工作时间:9:00-18:30)。
本工程项目是为动力中心配备一套完整的氨法脱硫工艺系统,一炉一塔配置,采用塔内结晶方式,塔外配置湿式电除尘器。
主要工艺系统包括:烟气系统、脱硫塔系统、塔顶湿式电除尘器系统、吸收剂储存及供应系统、硫铵后处理系统、氯离子控制及油灰分离系统、事故排放系统等。
1工艺简介1.1 烟气系统简介脱硫烟气系统的主要作用是进行脱硫装置的投入和切除,为脱硫运行提供烟气通道。
烟气系统包括以下设备及其系统:烟道、净烟气挡板门,挡板门密封风系统、非金属补偿器、脱硫塔、湿式电除尘器等。
原烟气从脱硫入口烟道先进入反应塔浓缩段,对热烟气进行喷淋降温,同时热烟气对硫铵浆液进行蒸发浓缩。
降温后的烟气经浓缩段除雾器后进入吸收段进行脱硫反应,经脱硫吸收后的烟气进入水洗段,通过水洗除去烟气中携带的微小硫铵晶体及氨逃逸,水洗后的净烟气进入塔外湿式电除尘器,经湿电出去剩余的粉尘、气溶胶、液滴后进入烟囱排放。
1.2 脱硫塔系统简介烟气进入脱硫塔浓缩段后,经洗涤、降温至50-60℃后进入脱硫塔吸收段烟气自下而上与喷淋液逆流接触反应,生成的(NH4)2SO3落入吸收液收集托盘进入循环浆液箱。
为氧化循环浆液箱浆池内的亚硫酸氨,设置了氧化空气系统,本脱硫系统共配有六台氧化风机(四用两备)。
氧化空气经氧化风分布管注入循环浆液箱浆池,对中间产物进行强制氧化生成脱硫副产品硫铵(NH4)2SO4。
氨气通过氧化风管、氧化喷枪供给系统。
经过脱硫吸收后的净烟气,进入水洗段,通过水洗喷淋通过部分气溶胶和氨逃逸,再进入湿电系统。
循环浆液箱循环液经循环泵输送至喷淋层,在喷嘴处雾化成细小的液滴,自上而下地落下。
在液滴落回吸收液收集托盘的过程中,实现了对烟气中的二氧化硫、三氧化硫、氯化氢和氟化氢等酸性成份的吸收过程。
硫铵溶液经浓缩泵送入脱硫塔浓缩段,洗涤高温烟气,使烟气温度降到50-60℃,经浓缩泵循环喷淋,反复蒸发浓缩,最后形成固含量约10%-20%的硫铵溶液去硫铵缓冲箱。
按设计条件,循环浆液箱的pH为5.5~6,如果氨加入过量,脱硫塔喷淋液中游离氨较多,其pH值将大于6,造成浪费;如果供氨量不足,脱硫塔喷淋液中含硫酸氢铵,pH小于5.5,此时脱硫效率将降低。
因此,根据喷淋液的pH值,可调节氨的加入量。
由浓缩段排出的硫铵溶液pH值在3~4左右。
为防止脱硫塔浓缩段浆液混入循环箱,造成循环箱浆液密度升高,脱硫效率下降,脱硫塔浓缩段设置一级除雾器,设置二层喷淋层冲洗、降温烟气,浆液自身得到蒸发浓缩,脱硫塔吸收段设置二级除雾器、二层喷淋层。
由于浓缩段浆液中正常运行期间存在硫铵晶体,为防止硫铵晶体沉淀形成大晶块,同时也为给硫铵晶体颗粒与过饱和浆液充分接触从而长大创造条件,防止浆池中浆液密度不均匀,在浓缩段底部设置脉冲悬浮泵进行搅拌。
正常运行期间,通过CEMS在线监测净烟气出口SO2含量、温度、压力等参数,并通过调节氨加入量、增减浆液循环泵投入量来控制脱硫效率、净烟气中SO2的含量、氨的逃逸率、脱硫塔浆液PH值等。
脱硫塔浓缩段出口温度高于70℃时报警,并自动打开事故冷却水排放阀,事故冷却水来自水洗槽。
在吸收二氧化硫期间,消耗的水量由工艺水补偿。
1.3公用系统1.3.1 硫铵结晶脱水系统简介硫铵结晶脱水系统为公用系统,#1~#4脱硫装置浓缩产生10~20%含固量的浆液,由浓缩泵旁路送至硫铵缓冲箱,再经硫铵旋流泵送至旋流器中进行浓缩,使底流固含量提高到50%左右,旋流器溢流浆液与离心机滤液汇集后进入料液返回箱,通过料液返回泵回到脱硫塔系统,底流进入离心机进行液固分离,得到含水率约为4%的硫铵固体湿物料,经螺旋输送机进入干燥机进行干燥,干燥后硫铵含水率在1.0%以下,进入硫铵成品料斗,经计量包装,送入仓库。
经离心机分离后的硫铵晶体再经振动流化床干燥机干燥,得到含水率≤1.0%的硫铵产品。
干燥过程中,通过调节蒸汽的流量控制进入干燥机中的热风温度,控制热空气进口温度为140~160℃,控制床温在150℃左右,出口温度在60~80℃;还可通过调节引风机风口、控制加料量和进风量来控制风温;当进料少时除以上调节措施外,还可打开冷风口,增加风量来保持风温。
1.3.2 液氨储存及蒸发系统简述液氨由液氨槽车送来,利用槽车罐自身压力和氨卸料压缩机增压的方式将液氨由槽车输入至液氨储罐内储存。
液氨储罐内液氨依靠自身压力或通过液氨泵加压的方式送至蒸发器与厂区来的过热蒸汽换热后蒸发为气氨,通过气氨缓冲罐稳定其压力后送至脱硫系统。
液氨储罐及气氨蒸发系统紧急排放的气氨以及管线氮气置换时排出的残留氨气均排入氨气稀释罐中,经水吸收后排入废水池,再经废水泵送至脱硫塔区,进行回收利用。
本系统液氨储存规模:2×200m3;配置3套液氨蒸发器,每台蒸发器的蒸发能力:1500㎏/h。
液氨系统主要的设备包括陆用流体装卸臂、氨卸料压缩机、液氨卧式储罐、液氨蒸发器、气氨缓冲罐、氨气稀释罐、废水输送泵、压缩空气储存罐及一些安全辅助设施。
1.3.3 工艺水系统简介工艺水系统由工艺水箱、三台工艺水泵与管道阀门组成。
工艺水系统由主体工程的生产水接入脱硫装置的工艺水箱,由工艺水泵送至脱硫装置各处。
工艺水系统的作用是满足FGD装置正常运行(除雾器、管道冲洗水等)用水,工艺水系统还为FGD装置提供各生产部件正常工作所需冷却水。
工艺水主要以除雾器冲洗水途径来补充脱硫装置运行时发生的水损失。
脱硫系统产生水损失的主要原因是冷却烟气蒸发的水分从净烟气排出。
氨区安全运行所需水源引自动力中心生产水和消防水。
1.3.4地坑及事故排放系统简介每2套脱硫公用设置1套地坑系统,设置2台地坑泵,脱硫系统内的冲洗水、冷却水、排放浆液通过地沟汇集到地坑内,再通过地坑泵返回脱硫系统。
4套脱硫设置1座公用的检修槽,设置1台事故浆液返回泵将事故浆液返回各个脱硫系统中。
1.3.5 控制系统简介脱硫控制系统采用DCS分散集中控制方式,集中控制室和工程师站布置在脱硫综合楼内。
同时还设有控制通信设备,可通过通信方式将一部分信号传送到机组单元控制室,工艺楼内部设低压配电间、变压器室、DCS现场机柜室、工程师站、运行值班室、4.5m~8.5层为电缆夹层。
在脱硫控制室内布置有FGD-DCS操作员站及打印机、火灾报警等。
脱硫装置的自动化控制系统采用集散控制系统DCS。
整套FGD装置(脱硫装置和辅助系统)的运行是完全自动化的,其主要功能系统包括:数据采集系统(DAS)、顺序控制系统(SCS)、模拟量控制系统(MCS)、电气控制系统(ECS)。
在集中控制室内能够完成对FGD及其附属系统的正常启、停,运行的监视、连锁保护和紧急事故处理,以及FGD的效率、性能计算等,保证FGD安全,可靠,经济地运行。
操作人员在集中控制室将通过DCS画面、键盘及鼠标对FGD系统进行监视和控制操作。
操作台上装有旁路挡板门紧急打开按钮,以保证FGD在紧急情况下安全快速打开。
热工仪表系统还包括:压力、温度、浓度、密度、液位、流量、烟气连续排放监测系统等。
烟气连续排放监测系统(CEMS)用于监测原烟气和烟塔排出的净烟气流量、压力、温度、二氧化硫含量、粉尘含量、氮氧化物、氧量及净烟气氨含量。
脱硫工业电视系统:满足运行人员可在控制室内对生产现场的主要设备运行情况进行必要的监视。
2工艺原理2.1氨法脱硫工艺反应原理烟气中S02的吸收过程是在脱硫塔内以水溶液中的NH3与锅炉烟气中的S02反应为基础,在脱疏塔的吸收段,氨水与烟气中的S02发生化学反应,将烟气中的S02吸收,得到亚硫酸铵溶液。
在烟气吸收过程中形成的亚硫酸铵(NH4)2SO3,需进一步氧化为硫酸铵(NH4)2SO4才是最终的副产品。
我公司烟气湿式氨法脱硫工艺采用的是氨/硫酸铵法,其主要化学反应式如下:吸收反应为:(1)SO2+NH3+H2O=NH4HSO3(2)SO2+2NH3+H2O=(NH4)2SO3(3)SO2+(NH4)2SO3+H2O=2NH4HSO3(4)NH3+ NH4HSO3=(NH4)2SO3氧化反应为:(5)2(NH4)2SO3+O2 = 2(NH4)2SO42.2 脱硫装置工艺流程本工程按每炉配置一座反应塔+ 一座循环浆液箱+一座水洗槽设计,原烟气从脱硫入口烟道先进入反应塔浓缩段,浓缩段设有1层喷淋层,设3台浓缩泵(2用1备)进行循环喷淋,对热烟气进行喷淋降温,同时热烟气对硫铵浆液进行蒸发浓缩。
降温后的烟气经浓缩段除雾器后进入吸收段,吸收塔上部布置有2层浆液喷淋层,烟气自下而上与喷淋液逆流接触反应,生成的NH4SO3经过收集托盘落入循环浆液箱内,经脱硫吸收后的烟气经屋脊式除雾器后进入水洗段,水洗段设置一层喷淋层,设2台水洗循环泵(1用1备)进行循环喷淋,通过水洗可除去烟气中携带的微小硫铵晶体及氨逃逸,水洗后的净烟气经过屋脊式除雾器除去部分液滴后,进入塔外湿式电除尘器,通过湿电电场荷电,脱除净烟气中的气溶胶颗粒、微细粉尘及液滴后,通过烟囱排往大气。
3 参数规范3.1脱硫装置规范FGD装置主要技术经济指标和保证值表2-1 FGD装置主要技术经济指标和保证值3.2液氨品质参数本系统采用氨气为脱硫剂,以液氨的形态储存,设有蒸发系统,将液氨蒸发为氨气供给脱硫系统,液氨采取外购、槽车运输的方式补充到储存系统。
氨的性质如下:性状:氨为无色、有刺激性恶臭气体。
在适当压力下可以液化,同时放出大量的热量。
当压力降低时则汽化,同时吸收周围大量的热。
氨有毒,空气中最高允许浓度为30mg/m 3。
氨蒸汽与空气混合物的爆炸极限为16-25%(最易引燃浓度17%)。
氨极易溶于水(在20℃水中溶解度34%),氨的水溶液呈碱性,0.1mol/L 水溶液的PH 值为11.1。
表2-2 理化常数3.3硫酸铵品质参数湿式氨法脱硫工艺的脱硫产品为硫酸铵,其性质如下:硫酸铵为白色晶体,分子量M=132.13,密度P=1769Kg/m3,熔点mp=235℃.硫铵饱和溶液的性质:沸点bp=108.9℃;硫酸铵的溶解度可见,硫铵的溶解度随温度略有增加,但变化很小,因此硫铵结晶都以蒸发结晶、饱和结晶为主,较少采用降温结晶的办法。
本系统采用浓缩段塔内蒸发结晶的工艺生产硫铵。
表2-4 硫酸铵产品标准:GB535-95注:硫酸铵作农业用时可不检验铁、砷、重金属和不溶物含量等指标。
100%纯度的硫铵的N含量21.2%,因此20.5%N含量相当于硫铵纯度为96.6%。
4脱硫各系统运行控制调整4.1 脱硫塔主要参数控制:1.浓缩段液位控制:5.0m-6m。
2.浓缩段PH值控制:3 -4,为保证PH计灵敏度,在PH值较大偏差时,及时冲洗PH计,及时根据需要通知检修检查标定PH计。
3.浓缩段密度控制:1300kg/m3左右,为保持脱水出力及结晶颗粒,必须严格控制脱硫塔密度,密度偏高时,加大脱水出力,必要时可切换工艺水冲洗。