5S现场改善图片案例[1]
合集下载
5S现场管理培训系列之现场改善篇(PPT 71张)

整顿(Seiton):“零时间”能找到需 要
方法九
看板管理 让所有人一看就知道怎样做
公示类:岗位职责、人员配置、安全规程 作业类:工艺流程、交货期限、工作进程 设备类:平面布置、点检要求、维修计划 品质类:质量统计、不良处理、成品等级 事务类:去向显示、通知通告、文体娱乐
整顿(Seiton):“零时间”能找到需 要
整顿(Seiton):“零时间”能找到需 要
方法七
色彩管理
主 通 道:暗 红 色 运输设施:桔黄色 自来水管:黑色色环 蒸气管道:大红色环
直观透明
废 品 区:大 红 色 起重设施:黄黑相间 煤气管道:中黄色环 暖气管道:银灰色环
整顿(Seiton):“零时间”能找到需 要
方法八
愚巧化:改善工具,使“愚人”能象“巧匠”一样 工作。 手工配钥匙需要很高的技巧,用一台仿形机任何人 都能把它做得又快又好。 用手数小螺钉又慢又差,做一个定数器就能数得又 快又好。
卫生间的清扫
无蛛网、灰尘 无积垢、污迹 无明显气味 无乱涂乱划 墙面、地面、便沟内瓷砖整洁无破损 Seiso):规格化的清除工作
办公室的清扫
桌、椅、文件柜、电脑、花草等排列整齐 除茶杯外,不应有其他生活用品出现 门窗玻璃整洁明亮、桌椅沙发保持本色 桌面上面不应有太多的摆放,话机保持本色 茶杯、烟缸等客用品做到人走场清 报架、纱窗、遮阳蓬整齐无破旧 除装饰外,墙壁上不应有与工作无关的张贴
注 意
整理(Seiri) 区分“要”与“不要”
正常流转的原料、在制品 工位器具、周转箱 加工工具和检验用具 种类看板、工艺文件 办公桌椅、办公用品 安全消防用品 清洁清扫用品
要
5S改善案例(经典作品)

检验区和作业区分开,慎防混料
文件未加以分类定置,易丢失
有了位置线,放错也不容易
车间规划清晰,一尘不染
物料置于车间通道,阻碍物流,影响效率
在制物料未标示清楚,易使产线弄错
整洁车间现场一览
车间整洁,员工战斗力高
流动红旗简单有效,你也可试
2019/3/22
26/46
2019/3/22
态度 习惯
2019/3/22
行为 人格
命运
45/46
想改变自己命运的时候,就从态度开始。
谢谢大家!
2019/3/22
46/46
27/46
2019/3/22
28/46
2019/3/22
29/46
222
31/46
2019/3/22
32/46
2019/3/22
33/46
2019/3/22
34/46
2019/3/22
35/46
2019/3/22
36/46
不好
2019/3/22
37/46
好
◎形迹定位管理 自 己 制 作
2019/3/22
38/46
2019/3/22
39/46
2019/3/22
40/46
2019/3/22
41/46
2019/3/22
42/46
2019/3/22
43/46
2019/3/22
44/46
安冈正笃
名言-----日本汉学大师
心态变则态度变; 态度变则习惯跟着变; 习惯变则人格随之变; 人格一变则人生也就变。
5S的实例图片
2019/3/22
1/46
干部自已未遵守,怎能要求员工遵守
5S现场管理实例图片

5S现场管理实例(shílì) 图片
2021/11/8
第一页,共56页。
第二页,共56页。
第三页,共56页。
第四页,共56页。
第五页,共56页。
第六页,共56页。
第七页,共56页。
第八页,共56页。
第九页,共56页。
第十页,共56页。
第十一页,共56页。
第十二页,共56页。
第十三页,共56页。
第二十七页,共56页。
第二十八页,共56页。
第二十九页,共56页。
第三十页,共56页。
第三十一页,共56页。
第三十二页,共56页。
生活用品集中(jízhōng) 定位
第三十三页,共56页。
第三十四页,共56页。
第三十五页,共56页。
第三十六页,共56页。
第三十七页,共56页。
第三十八页,共56页。
第三十九页,共56页。
第四十页,共56页。
第四十一页,共56页。
第四十二页,共56页。
第四十三页,共56页。
第四十四页,共56页。
第四十五页,共56页。
第四十六页,共56页。
餐厅(cāntīng)管理
第四十七页,共56页。
第四十八页,共56页。
第四十九页,共56页。
第五十页,共56页。
第五十一页,共56页。
第五十二页,共56页。
宿舍(sùshè)管理
第五十三页,共56页。
第五十四页,共56页。
第五十五页,共56页。
第五十六页,共56页。
第十四页,共56页。
第十五页,共56页。
第十六页,共56页。
第十七页,共56页。
第十八页,共56页。第二十一页,共56页。
2021/11/8
第一页,共56页。
第二页,共56页。
第三页,共56页。
第四页,共56页。
第五页,共56页。
第六页,共56页。
第七页,共56页。
第八页,共56页。
第九页,共56页。
第十页,共56页。
第十一页,共56页。
第十二页,共56页。
第十三页,共56页。
第二十七页,共56页。
第二十八页,共56页。
第二十九页,共56页。
第三十页,共56页。
第三十一页,共56页。
第三十二页,共56页。
生活用品集中(jízhōng) 定位
第三十三页,共56页。
第三十四页,共56页。
第三十五页,共56页。
第三十六页,共56页。
第三十七页,共56页。
第三十八页,共56页。
第三十九页,共56页。
第四十页,共56页。
第四十一页,共56页。
第四十二页,共56页。
第四十三页,共56页。
第四十四页,共56页。
第四十五页,共56页。
第四十六页,共56页。
餐厅(cāntīng)管理
第四十七页,共56页。
第四十八页,共56页。
第四十九页,共56页。
第五十页,共56页。
第五十一页,共56页。
第五十二页,共56页。
宿舍(sùshè)管理
第五十三页,共56页。
第五十四页,共56页。
第五十五页,共56页。
第五十六页,共56页。
第十四页,共56页。
第十五页,共56页。
第十六页,共56页。
第十七页,共56页。
第十八页,共56页。第二十一页,共56页。
5S现场改善实战

2020/5/2
区域清楚明了
16
二、生产现场改善前后对比图片
钣金车间改善成果展
改善前
改善后
这材料都是有用的吗, 怎么区分呢
分类标识摆放
2020/5/2
17
二、生产现场改善前后对比图片
钣金车间改善成果展
改善前
改善后
机台和工具摆放未规 划
2020/5/2
规划后,空间多了
18
二、生产现场改善前后对比图片
8
二、生产现场改善前后对比图片
钣金车间改善成果展
改善前
改善后
物品堆放杂乱的生产 车间一角
整齐分类并标识,一 目了然
2020/5/2
9
二、生产现场改善前后对比图片
钣金车间改善成果展
改善前
改善后
生产车间一角
2020/5/2
规划后生产车间一角
10
二、生产现场改善前后对比图片
钣金车间改善成果展
改善前
改善后
有用的分类摆放了
21
二、生产现场改善前后对比图片
钣金车间改善成果展
改善前
改善后
机台漏水了
2020/5/2
注意机台细节,分区 了,干净了
22
二、生产现场改善前后对比图片
钣金车间改善成果展
改善前
改善后
这是通道哦,都是摆 放的都是杂物
2020/5/2
通道有了,物品摆放 整齐了
23
二、生产现场改善前后对比图片
35
二、生产现场改善前后对比图片
喷涂车间改善成果展
改善前
改善后
报废的?
2020/5/2
清理了,通道明了
36
二、生产现场改善前后对比图片
区域清楚明了
16
二、生产现场改善前后对比图片
钣金车间改善成果展
改善前
改善后
这材料都是有用的吗, 怎么区分呢
分类标识摆放
2020/5/2
17
二、生产现场改善前后对比图片
钣金车间改善成果展
改善前
改善后
机台和工具摆放未规 划
2020/5/2
规划后,空间多了
18
二、生产现场改善前后对比图片
8
二、生产现场改善前后对比图片
钣金车间改善成果展
改善前
改善后
物品堆放杂乱的生产 车间一角
整齐分类并标识,一 目了然
2020/5/2
9
二、生产现场改善前后对比图片
钣金车间改善成果展
改善前
改善后
生产车间一角
2020/5/2
规划后生产车间一角
10
二、生产现场改善前后对比图片
钣金车间改善成果展
改善前
改善后
有用的分类摆放了
21
二、生产现场改善前后对比图片
钣金车间改善成果展
改善前
改善后
机台漏水了
2020/5/2
注意机台细节,分区 了,干净了
22
二、生产现场改善前后对比图片
钣金车间改善成果展
改善前
改善后
这是通道哦,都是摆 放的都是杂物
2020/5/2
通道有了,物品摆放 整齐了
23
二、生产现场改善前后对比图片
35
二、生产现场改善前后对比图片
喷涂车间改善成果展
改善前
改善后
报废的?
2020/5/2
清理了,通道明了
36
二、生产现场改善前后对比图片
5S改善图片1(PPT42页)

第二次改善
物品已有定量管理,但布局欠佳,不能节约空间
第三次改善
整合2个柜子后,现已节约1个工具柜的空间,后续加工标识牌实 行颜色管理。
工具柜内物品摆放再整理,对小刀进行数量管理,方便拿取
5改善事例
事例⑩:油柜的改善 改善前
第一次改善
问题概述:油类标识不清晰,油瓶没盖,摆放混乱,无法区分适 用的油瓶
整顿事例—标签
P16
标签放置杂乱
用标签架进行分层放置, 目视化管理
未实施整理、整顿: 1.标签等物品放置凌乱,使用使需要查找 2.不能马上把握在库量。
实施整理、整顿后: 1.容易找到、容易取出、容易返还。 2.在库量能“一眼识别”。
目视化改善事例—成型机标识
P17 正面
改善中
无机台标识,存在查找浪费及误送 料等品质隐患。
共同改善 共同进步
---5S改善事例集
李小伍
5改善事例
事例①:成形机改善
改善前
改善后
事例②:清扫工具的改善
改善前
改善后
改善前: 成形机编号及顿数不能一眼判断 改善后: 成形机前方使用V型揭示板揭示成 形机编号及顿数,成形机后方同 时标示。
<效果> 不管从哪个方向都能看到标示
改善前: 清扫工具随意放置,正常异常 不能一眼判断。破损严重的工具 不能有效达到清扫效果。 改善后: 1、制定清扫工具放置场所及清 扫工具所需量,使用颜色及号码 清扫工具进行管理。 2、制定并揭示清扫工具更换标 准。
对油柜实施整理、整顿。不同油类用 颜色识别,并管理油壶数量,能一眼 判断油壶数量、放置状态的正常·异常
整顿事例—作业指导书
P15
《作业指导书》按客户别管理,但 颜色杂乱放置,查找及返还时“不 能一眼识别”。
物品已有定量管理,但布局欠佳,不能节约空间
第三次改善
整合2个柜子后,现已节约1个工具柜的空间,后续加工标识牌实 行颜色管理。
工具柜内物品摆放再整理,对小刀进行数量管理,方便拿取
5改善事例
事例⑩:油柜的改善 改善前
第一次改善
问题概述:油类标识不清晰,油瓶没盖,摆放混乱,无法区分适 用的油瓶
整顿事例—标签
P16
标签放置杂乱
用标签架进行分层放置, 目视化管理
未实施整理、整顿: 1.标签等物品放置凌乱,使用使需要查找 2.不能马上把握在库量。
实施整理、整顿后: 1.容易找到、容易取出、容易返还。 2.在库量能“一眼识别”。
目视化改善事例—成型机标识
P17 正面
改善中
无机台标识,存在查找浪费及误送 料等品质隐患。
共同改善 共同进步
---5S改善事例集
李小伍
5改善事例
事例①:成形机改善
改善前
改善后
事例②:清扫工具的改善
改善前
改善后
改善前: 成形机编号及顿数不能一眼判断 改善后: 成形机前方使用V型揭示板揭示成 形机编号及顿数,成形机后方同 时标示。
<效果> 不管从哪个方向都能看到标示
改善前: 清扫工具随意放置,正常异常 不能一眼判断。破损严重的工具 不能有效达到清扫效果。 改善后: 1、制定清扫工具放置场所及清 扫工具所需量,使用颜色及号码 清扫工具进行管理。 2、制定并揭示清扫工具更换标 准。
对油柜实施整理、整顿。不同油类用 颜色识别,并管理油壶数量,能一眼 判断油壶数量、放置状态的正常·异常
整顿事例—作业指导书
P15
《作业指导书》按客户别管理,但 颜色杂乱放置,查找及返还时“不 能一眼识别”。
5S现场管理整改前后对比图
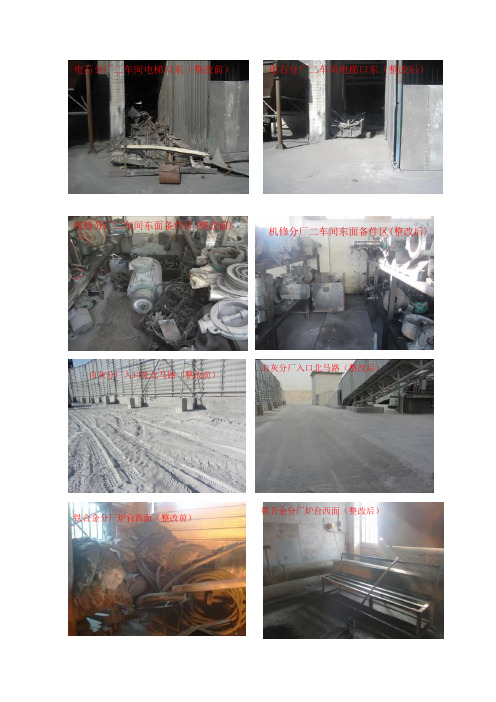
机修分厂二车间东面备件区(整改前)
机修分厂二车间东面备件区(整改后)白灰分厂入口处北马路(整改前)
白灰分厂入口北马路(整改后)
铁合金分厂炉台西面(整改前)铁合金分厂炉台西面(整改后)
电石分厂二车间电梯口东(整改前)电石分厂二车间电梯口东(整改后)
电石分厂原料车间煤泥池西侧(整改前)电石分厂原料车间煤泥池西侧(整改后)
电石分厂三车间西侧(整改前)
电石分厂三车间西侧(已整改)
电石二车间成品库周围(整改前)电石分厂二车间成品库周围(整改后)电石分厂一车间后小院。
《现场改善5S实践》课件
素养(Shitsuke)
素养的定义
通过教育培训、宣传推广等手段 ,提高员工的素质和遵守规定的
意识。
素养的目的
培养员工良好的工作习惯和团队 合作精神。
实施要点
制定培训计划,定期开展培训活 动,建立奖惩制度。
03 5S的实践案例
案例一:某制造企业的5S实践
总结词
全面推进、持续改进
详细描述
该制造企业通过全面推行5S管理,实现了生产现场的整洁、有序,提高了工作 效率和产品质量。企业通过制定5S推行计划,分阶段实施,不断优化5S管理方 案,确保了5S管理的持续改进。
制定清扫计划,注意死角的清理,使 用适当的清洁工具。
清扫的目的
保持工作场所的干净整洁,防止污染 和故障的发生。
清洁(Seiketsu)
清洁的定义
对清扫后的整洁状态进行维护, 并防止污染和脏污的产生。
清洁的目的
维持工作场所的长期整洁,提高工 作效率。
实施要点
定期检查清洁情况,建立检查制度 ,及时处理问题。
。
在中国,随着企业对于现场管理 的重视程度不断提高,5S已经 成为许多企业的基础管理手段。
5S在现代制造业中的重要性 Nhomakorabea提高工作效率
通过整理、整顿和清扫 ,消除工作场所中的混 乱和浪费,使工作更加
有序和高效。
降低成本
减少浪费和错误,降低 生产成本和维修成本。
提高产品质量
整洁有序的工作环境有 助于减少不良品和次品
03
数字化工厂需要高标准的现场管理,5S的实施有助于满足这些
要求。
5S的持续改进和创新
定期评估与改进
定期对5S的实施效果进行评估,针对不足之处进行改进,确保 持续优化。
精选5S改善图片1PPT42页
P1
整顿事例—清扫工具2
清扫工具摆放凌乱,拿取不方便,不能判断状态的正常·异常。
规范清扫工具的摆放,明确管理担当,能一眼判断清扫工具摆放及返还状态的正常·异常。
P2
清扫工具摆放凌乱,拿取不方便,不能判断状态的正常·异常。
规范清扫工具的摆放,明确管理担当,能一眼判断清扫工具摆放及返还状态的正常·异常。
设计、作成新的作业台(只允许放置需要使用数量的东西),并标识、定位。能一眼判断正常·异常。
整顿事例—作业台
P13
油壶摆放凌乱,存在混用隐患,不能一目了然地看到油壶的在库状态及返还状态,不能判断油壶的正常·异常
对油柜实施整理、整顿。不同油类用颜色识别,并管理油壶数量,能一眼判断油壶数量、放置状态的正常·异常
作业台简化改善
改善前
改善后
作业台垃圾桶放置改善
作业区域包材限高改善及定位改善
手套回收基准明确改善
各种改善事例
5改善事例
扳手形状定位改善
工具柜物品放置标示改善
垃圾分类改善
安全帽3定管理
安全管理规定明确
成品放置标示改善
安全—防撞铁角
P24
『异常』配线杂乱缠绕,且直接落在地面上,既影响环境美观,又不方便清扫,且存在安全隐患。
『正常』实施配线整理后,既美观、干净,又方便清扫,安全隐患消除。
配线整理事例1
P25
配线整理事例2
『异常』配线杂乱缠绕,且直接落在地面上,既影响环境美观,又不方便清扫,且存在安全隐患。
『正常』实施配线整理后,既美观、干净,又方便清扫,安全隐患消除。
第二次改善
第三次改善
事例⑩:油柜的改善
5改善事例
问题概述:油类标识不清晰,油瓶没盖,摆放混乱,无法区分适用的油瓶
整顿事例—清扫工具2
清扫工具摆放凌乱,拿取不方便,不能判断状态的正常·异常。
规范清扫工具的摆放,明确管理担当,能一眼判断清扫工具摆放及返还状态的正常·异常。
P2
清扫工具摆放凌乱,拿取不方便,不能判断状态的正常·异常。
规范清扫工具的摆放,明确管理担当,能一眼判断清扫工具摆放及返还状态的正常·异常。
设计、作成新的作业台(只允许放置需要使用数量的东西),并标识、定位。能一眼判断正常·异常。
整顿事例—作业台
P13
油壶摆放凌乱,存在混用隐患,不能一目了然地看到油壶的在库状态及返还状态,不能判断油壶的正常·异常
对油柜实施整理、整顿。不同油类用颜色识别,并管理油壶数量,能一眼判断油壶数量、放置状态的正常·异常
作业台简化改善
改善前
改善后
作业台垃圾桶放置改善
作业区域包材限高改善及定位改善
手套回收基准明确改善
各种改善事例
5改善事例
扳手形状定位改善
工具柜物品放置标示改善
垃圾分类改善
安全帽3定管理
安全管理规定明确
成品放置标示改善
安全—防撞铁角
P24
『异常』配线杂乱缠绕,且直接落在地面上,既影响环境美观,又不方便清扫,且存在安全隐患。
『正常』实施配线整理后,既美观、干净,又方便清扫,安全隐患消除。
配线整理事例1
P25
配线整理事例2
『异常』配线杂乱缠绕,且直接落在地面上,既影响环境美观,又不方便清扫,且存在安全隐患。
『正常』实施配线整理后,既美观、干净,又方便清扫,安全隐患消除。
第二次改善
第三次改善
事例⑩:油柜的改善
5改善事例
问题概述:油类标识不清晰,油瓶没盖,摆放混乱,无法区分适用的油瓶
精益5S改善图例(大全三)
• 工装使用和保养方法明确标识 • 按指定位置存放,清洁无灰尘、杂物
各类工装备件分类标识,说明具体用 途,附图片以避免备件防错位置
温度计
压力表
现物上如有标志,即不必每次对照标准书,任谁都可以 知道正常与否。
18. 人员素养
每班班前会重申5S、设备TPM、劳保用品穿戴、工艺纪律等要求
通过简单易懂的图片,将5S要求、员工自ຫໍສະໝຸດ 提出的5S改进内容张 贴在工厂门口
目视墙上将所有正在改进的5S项目公布于众,跟踪进度
员工5S宣言书,张贴在人人都能看到的通道旁,宣言书中有此员 工负责的5S具体项目和完成时间,小组成员等
管理人员定期对5S的推行效果进行评估
5S 图例集
红色使用区域
• 灭火机箱 • 50mm 红色胶带 实心线
红色使用区域
• 消火拴 • 50mm红色胶带 实心线 • 开门处1M内无障碍物,25cm为 一格分成四格
红色使用区域
• 禁止通行 • 50mm红色胶带 实心线
红色使用区域
• 工位操作区域:起始和结束位置
工位开始和结束位置
工位70%位置
2. 工位器具
工位器具5S要求
• 工位器具上无灰尘、油污、垃圾等
工位器具5S要求
• 工位器具上存放的 零件与工位器具需 吻合 • 现场有工位器具损 坏需及时报修(或 负责修理部门需及 时给予修理) • 工位器具上存放的 零件数与工位器具 设计存放零件数符 合
工位器具5S要求
• 工位器具上存 放的零件按存 放要求存放 • 工位器具摆放 整齐
入口编号
仓库位置 人行通道标识 警示
开启方向
人员通行许可
定置定位
地面和墙 上均标明 存放物料 相关信息
各类工装备件分类标识,说明具体用 途,附图片以避免备件防错位置
温度计
压力表
现物上如有标志,即不必每次对照标准书,任谁都可以 知道正常与否。
18. 人员素养
每班班前会重申5S、设备TPM、劳保用品穿戴、工艺纪律等要求
通过简单易懂的图片,将5S要求、员工自ຫໍສະໝຸດ 提出的5S改进内容张 贴在工厂门口
目视墙上将所有正在改进的5S项目公布于众,跟踪进度
员工5S宣言书,张贴在人人都能看到的通道旁,宣言书中有此员 工负责的5S具体项目和完成时间,小组成员等
管理人员定期对5S的推行效果进行评估
5S 图例集
红色使用区域
• 灭火机箱 • 50mm 红色胶带 实心线
红色使用区域
• 消火拴 • 50mm红色胶带 实心线 • 开门处1M内无障碍物,25cm为 一格分成四格
红色使用区域
• 禁止通行 • 50mm红色胶带 实心线
红色使用区域
• 工位操作区域:起始和结束位置
工位开始和结束位置
工位70%位置
2. 工位器具
工位器具5S要求
• 工位器具上无灰尘、油污、垃圾等
工位器具5S要求
• 工位器具上存放的 零件与工位器具需 吻合 • 现场有工位器具损 坏需及时报修(或 负责修理部门需及 时给予修理) • 工位器具上存放的 零件数与工位器具 设计存放零件数符 合
工位器具5S要求
• 工位器具上存 放的零件按存 放要求存放 • 工位器具摆放 整齐
入口编号
仓库位置 人行通道标识 警示
开启方向
人员通行许可
定置定位
地面和墙 上均标明 存放物料 相关信息
- 1、下载文档前请自行甄别文档内容的完整性,平台不提供额外的编辑、内容补充、找答案等附加服务。
- 2、"仅部分预览"的文档,不可在线预览部分如存在完整性等问题,可反馈申请退款(可完整预览的文档不适用该条件!)。
- 3、如文档侵犯您的权益,请联系客服反馈,我们会尽快为您处理(人工客服工作时间:9:00-18:30)。
5S现场改善图片案例
5S现场改善图片案例S现场改善图片案例
5S现场改善图片案例
5S现场改善图片案例
5S现场改善图片案例
5S现场改善图片案例
5S现场改善图片案例
5S现场改善图片案例
5S现场改善图片案例
5S现场改善图片案例
5S现场改善图片案例
5S现场改善图片案例
5S现场改善图片案例
5S现场改善图片案例
5S现场改善图片案例
5S现场改善图片案例
5S现场改善图片案例
5S现场改善图片案例
5S现场改善图片案例
5S现场改善图片案例
5S现场改善图片案例
5S现场改善图片案例
5S现场改善图片案例
5S现场改善图片案例
5S现场改善图片案例
5S现场改善图片案例
5S现场改善图片案例
5S现场改善图片案例
5S现场改善图片案例
5S现场改善图片案例
5S现场改善图片案例
5S现场改善图片案例
5S现场改善图片案例
5S现场改善图片案例
5S现场改善图片案例
5S现场改善图片案例
5S现场改善图片案例
5S现场改善图片案例
5S现场改善图片案例
5S现场改善图片案例
5S现场改善图片案例
5S现场改善图片案例
5S现场改善图片案例
5S现场改善图片案例
5S现场改善图片案例
5S现场改善图片案例
5S现场改善图片案例
5S现场改善图片案例
5S现场改善图片案例
5S现场改善图片案例
5S现场改善图片案例
5S现场改善图片案例
5S现场改善图片案例