DFMEA作业指导书(中英文)
最新DFMEA作业指导书.pdf

DFMEA作业指导书1目的在产品设计阶段,预先发现、评价产品可能潜在的失效与后果,及早找出能够避免或减少这些潜在失效发生的措施,并将此过程文件化,为以后的设计提供经验与参考。
2范围适用于公司车辆产品设计FMEA 的开发。
3术语3.1潜在的失效模式及后果分析(FMEA):是失效模式及后果分析的英文FAILURE MODE AND EFFECTSANAL YSIS的缩写,是在产品设计阶段和过程设计阶段,对构成产品的子系统、零部件,对构成过程的各个工序逐一进行分析,找出所有潜在的失效模式,并分析其可能出现的不良后果,从而预先采取必要的措施,以提高产品的质量和可靠性的一种系统化的活动。
3.2设计FMEA(DFMEA):简称DFMEA,是由负责设计的工程师或工程师小组在产品设计阶段采用的一种分析技术,用以最大限度地保证各种潜在的失效模式及相关的起因、机理在产品设计时得到充分的考虑和说明。
3.3 顾客:在FMEA中所指的客户是通常意义的车主。
但广义的讲也指后道工序(产品设计、生产、售后服务)的工程师和操作人员。
4相关流程4.1工作流程4.1.1 项目选定专业所/项目小组在新项目的初期(设计开始前)制定DFMEA分析的项目清单和计划,经部所长/项目经理批准后,报开发管理部备案。
4.1.2 成立小组专业所/项目小组在DFMEA分析时应成立小组,由小组成员共同进行DFMEA表单的填写。
4.1.3 实施DFMEA小组根据“第5条(附录)”的规定,进行DFMEA的表单(附录1)的填写,并一直跟踪到产品批量生产时为止;由供应商/协作设计单位负责的DFMEA项目,专业所/项目小组负责调度。
4.1.4 管理开发管理部负责确认DFMEA编号是否重复、表单填写是否符合编制规则、是否按照计划完成编制任务,同时建立DFMEA数据库;“建议措施”中需进行设计更改的部分由DFMEA小组负责实施;“建议措施”中需进行验证的部分由DFMEA小组按照《设计验证管理办法》的规定提出验证需求,由开发管理部下发设计验证计划。
DFMEA作业指导书 模板

(11)潛在性失效後果對於顧客的定義,可以是下一個制程、後續的作業或地點、經銷商和或汽車車主。
當評估失效潛在效應後果時,每一個物件均應考慮到:①對於最終使用者而言,其後果以產品或系統性能的感受;②對於下一個制程或後續的作業/地點,其後果以制程/操作性能的感受;③對於本部門的制程與作業,其後果以制程/可操作性為原則,考慮產品是否報廢或返工等; (12)嚴重度①嚴重度是針對失效模式中最嚴重的效應等級;②嚴重度等級指數可對系統、子系統或零部件的設計變更或制程之重新設計來降低;③失效模式後果的嚴重度為1分者,則不需要作進一步分析。
(13)類別填寫特殊特性符號。
(14)潛在失效起因/機理失效發生的原因,應從產品設計的方向來分析,如材料的選擇、產品結構設計等。
(15)現行設計預防是指針對對應的失效原因的設計預防方案,如選用好的材料、改變結構優化、實驗設計和模擬分析等。
(16)頻度頻度是指特定原因/機制可能發生的機率。
頻度的評價等級分數是相對值,而非絕對值。
頻度評價等級分數為DFMEA制定時的相對評分,並不一定是反映實際可能的發生。
(17)現行設計探測是針對產品的失效原因或失效模式,提供可採用的實驗分析或者物理測量方法進行識別。
(18)探測度探測度的探測方法能探測出失效模式或失效原因的能力程度,評分辦法見下表:(19)風險順序(R.P.N)如下表示對風險順序是否需要實施改善·對策的判斷基準,對於需要改善的風險,按順序數由高到低的順序,計劃性的實施改善。
風險順序時產品嚴重度、頻度和探測度的乘積。
風險順序=嚴重度×頻度×探測度①如嚴重度為9-10時,探測度或頻度應等於1,如兩項都不為1時應採取措施確保O或D降為1;②如嚴重度S≤8、RPN>100,必須進行採取新的措施使RPN降至100以下;③對RPN的大小進行排序,至少應針對RPN較大的前三項進一步採取措施;④當S≥5時,O≥5或D≥5時應考慮採取措施使之降至5以下;(20)建議措施所建議的各措施的目的是在於依次降低嚴重度、頻度、探測度的級別,必須進行改善。
DFMEA作业指导书

是指失效模式可能帶來的對完成規定功能的影響。
一直帶來顧客的不滿,和不符合安全和政府法規。
失效後果可以從以下方面考慮:①對完成規定功能的影響:②對上一級系統完成功能的影響③對系統內其他零部件的影響④對顧客滿意的影響;⑤對安全和政府法規符合性的影響;⑥對整車系統的影響。
(12)严重度①嚴重度是針對失效模式中最嚴重的效應等級;②嚴重度等級指數可對系統、子系統或零部件的設計變更或製程之重新設計來降低;③失效模式後果的嚴重度為1分者,則不需要作進一步分析。
(13)級別填寫特殊特性符號,如客戶有提供符號要求,則按客戶要求標識。
(14)潛在失效起因/機理機理是至導致失效模式的物理的、化學的、電子的、熱學的或其他失誤傳播過程。
起因是指在設計過程如何允許失效發生的指示,根據可糾正或可控製的事物用簡明的語言描述(如端子強度不足,導致歪斜),不可使用模糊詞語,也可能是設計缺陷的指示。
潛在失效起因的結果就是失效模式;(15)現行設計控製:是指設計過程中被實施的活動部分,這個設計過程已經被完全或得到認可且保證該設計對於所考慮的設計功能要求何可靠性要求來說是充分的;現行設計控製可分為預防、探測兩種:(15-1)現行預防設計控製是指消除(預防)失效原因的發生或減少它們頻度的設計方案,如遵循標準研究及設計、引用標準或優質原料、改變或優化產品結構、防呆/防錯設計和模擬研究(將概念研究轉化實物設計)、類似最佳設計方案及其經驗記錄等。
(15-2)現行探測設計控製針對產品的失效原因或失效模式,通過分析或者物理測量方法進行識別。
如設計評審、樣品測試、功能測試、試驗的設計(包括可靠性測試)、製作模型分析等(16)頻度頻度是指特定原因/機製可能發生的機率。
頻度的評價等級分數是相對值,而非絕對值。
頻度評價等級分數為DFMEA製定時的相對評分,並不一定是反映實際可能的發生。
注:當頻度評價等級=1時,代表失效模式已通過預防設計控製消除,不會再發生;(17)探測度探測度的探測方法能探測出失效模式或失效原因的能力程度,評分辦法見下表:(18)風險序數(R.P.N)如下表示對風險序數是否需要實施改善·對策的判斷基準,對於需要改善的風險,按順序數由高到低的順序,計劃性的實施改善。
FMEA和控制计划编制作业指导书1
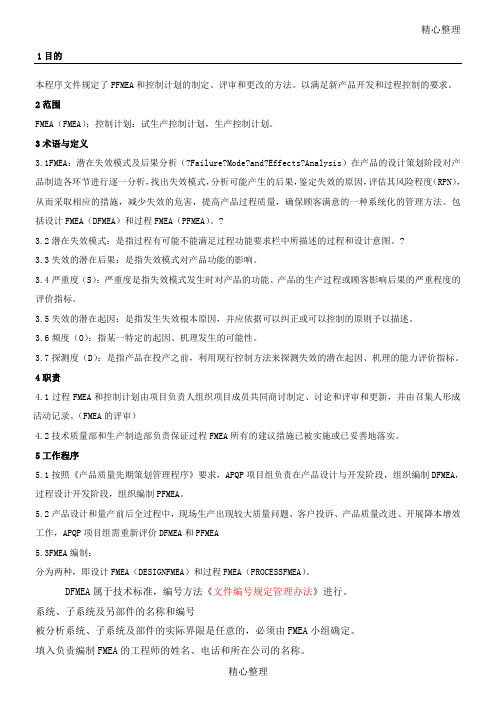
精心整理1目的本程序文件规定了PFMEA和控制计划的制定、评审和更改的方法。
以满足新产品开发和过程控制的要求。
2范围FMEA(FMEA);控制计划:试生产控制计划,生产控制计划。
3术语与定义3.1FMEA:潜在失效模式及后果分析(?Failure?Mode?and?Effects?Analysis)在产品的设计策划阶段对产品制造各环节进行逐一分析,找出失效模式,分析可能产生的后果,鉴定失效的原因,评估其风险程度(RPN),括设计3.23.33.43.53.63.74职责4.1过程4.255.1DFMEA,5.2产品设计和量产前后全过程中,现场生产出现较大质量问题、客户投诉、产品质量改进、开展降本增效工作,APQP项目组需重新评价DFMEA和PFMEA5.3FMEA编制:分为两种,即设计FMEA(DESIGNFMEA)和过程FMEA(PROCESSFMEA)。
DFMEA属于技术标准,编号方法《文件编号规定管理办法》进行。
系统、子系统及另部件的名称和编号被分析系统、子系统及部件的实际界限是任意的,必须由FMEA小组确定。
填入负责编制FMEA的工程师的姓名、电话和所在公司的名称。
填入所分析的设计将要应用和/或影响的车型年/项目(如已知的话)。
填入初次DFMEA应完成的日期,不超过计划的产品批量生产设计发布日期。
填入初稿(第一稿)完成的日期,和最新修订日期。
列出所有确定和/或执行任务的责任部门的名称和个人姓名。
填入被分析项目的名称和其它相关信息。
用尽可能简明的文字说明被分析项目满足设计意图的功能,包括该系统运行环境相关的信息。
指部件、子系统或系统有可能会未达到或不能实现项目/功能栏中所描述的预期功能的情况(如预期项目功能失效)指某一特定的起因/机理在设计寿命内出现的可能性,见表二。
表二:频度(O)的评价准则列出已经完成或承诺要完成的预防措施、设计确认/验证或其它活动,并且这些活动将确保设计对于所考虑的失效模式和/或起因/机理是足够的。
DFMEA作业指导书

文件修正一览表规范/表单权责维护主导单位:研发部变更前:1. 目的1.1. 确保产品在设计中减少错误,使新开发产品能优化设计。
1.2. 藉由DFMEA分析,了解产品于某设计环节上之风险领先指数PRN值>=80时,可参考列入关键工序加以关注管控。
2. 范围针对本公司项目产品开发(客户特别指定要求者)适用之。
3. 参考记录《DFMEA Report》(设计失效模式和影响分析报告)4. 名词定义FMEA : 失效模式分析DFMEA :Design Failure Mode Effects Analysis 设计失效模式分析DFMEA是指设计时间的潜在失效模式分析,是从设计时间把握产品质量预防的一种手段,是如何在设计研发阶段保证产品在正式生产过程~交付客户过程中,如何满足产品质量的一种控制工具。
因为同类型产品的相似性特点,所以DFMEA阶段经常借鉴以前量产过或正在生产中的产品其相关设计上的优缺点,评估后再针对新产品进行的改进与改善。
最终的目的都是追求产品质量的稳定及良品最大化,同时也为大量生产提供可行性的保证。
5. 维护单位研发部6. 权责6.1研发:负责对DFMEA制作与更新。
制作过程,必要时可招集其他部门脑力激荡汇整意见。
6.2品保:依DFMEA相关决议对质量关键点进行管控。
7. 作业程序说明针对特定项目(客户特别指定要求者)之《产品开发申请单》经总经理(含)以上主管审核后,由研发部主导设计DFMEA7.1编制产品/设计需求列表7.1.1 编制清单:列出该产品应有之功能,及不应有之功能,编列时应将已知之产品需求全部纳入。
7.1.2 填入被分析项目(零件)的名称序号(型号),使用术语,并如工程图所指明的一样表明设计级别,在最初公布前,应使用实验号码。
7.2研订产品/设计需求之潜在不良模式7.2.1 不良模式是指某一零件或装配件,可能出现何种缺点,而使产品无法符合其原设计之目的或性能。
7.2.2 潜在的失效模式被定义为一种方式、一个零组件,次系统或系统可能潜在的不会满足设计意图。
DFMEA作业指导书
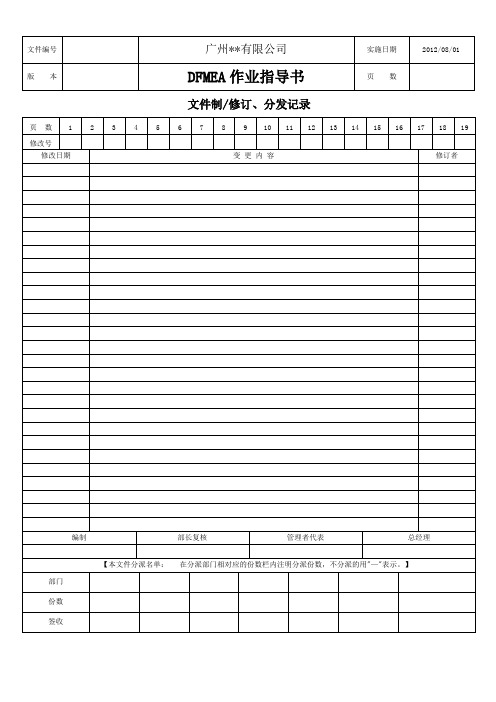
文件制/修订、分发记录1、目的为DFMEA作业提供依据2、适用范围适用于DFMEA的制作与修改3、作业步骤一、准备:由研发部准备以下资料:过往缺陷一览、方案设计、类似品的DFMEA、产品设计目标二、DFMEA的制定,由研发部召集包括生产、品管、采购、业务、技术人员通过会议的方式完成DFMEA表格,完成内容如下所列:(1)、FMEA编号填入FMEA文件的编号,以便查询(2)、部品名及图号注明正在进行过程分析的产品的部品名和图纸号(3)、过程责任部门填入项目工程师姓名及联系电话。
(4)、编制者信息填入负责编制FMEA的工程师的姓名、电话。
(5)、关键日期填入P-FMEA的讨论日期。
(6)、FMEA完成日/修订日填入编制FMEA完成的日期及最新修订的日期。
(7)、核心小组列出有权确定和或执行任务的部门的名称和个人的姓名及职位。
(8)、功能填入产品设计需要达到的要求,包括功能、性能、可靠性、寿命、可装配性及外观项目(9)、要求填入功能功能、性能、可靠性、寿命、可装配性及外观项目的要求;(10)、潜在性失效模式①、在准备DFMEA作业中,假定原材料/过程均为合理,除非依据历来的数据显示进料的品质有缺点,则可纳入分析。
②、可预测到的不良:如材质不良、短料、变形、尺寸超差、碰伤、拉伤、测量的不安全、摆放的不安全等。
(11)、潜在性失效后果①、对于顾客的定义,可以是下一个制程,后续的作业或地点,经销商和或汽车车主。
当评估失效潜在效应后果时,每一个对象均应考虑到:a、对于最终使用者而言,其后果以产品或系统性能的感受,如下表所示:b、对于下一个制程或后续的作业/地点,其后果以制程/操作性能的感受,如下表所示:c、对于本部门的制程与作业,其后果以制程/可操作性为原则,考虑产品是否报废或返工等,如下表所表示:(12)、严重度①、严重度是针对失效模式中最严重的效应等级。
②、严重度等级指数可对系统、子系统或零部件的设计变更或制程之重新设计来降低。
DFMEA编制作业指导书 新版

等等。
2)H型失效模式,指的是产生了有害的非期望功能。典型的这类失效模式有:
噪声、振动、电磁干扰、有害排放、等等。当出现这类失效时,要返回功能描述部分,看是否已有限制要求,如果没有,是否应加以补充。
5.4.3 潜在失效后果(影响):
5.3.2系统、子系统或零部件的名称及编号:注明適當的分析級別並填入被分析的系統、子系統或部件的名稱及編號。
5.3.3设计责任:填入整车厂、部门和小组。如适用, 还包括供方的名称。或者组织内部责任部门。
5.3.4编制者:填入整车厂、部门和小组。 如适用, 还包括供方的名称。
5.3.5车型年/项目:填入所分析的设计将要应用和 / 或影响的车型年 / 项目(如果已知)。
不推荐修改确定为9和10的严重度数值。严重度数值定级为1的失效模式不应进行进一步的分析。
推荐的评分准则见表1,严重度应以表1为导则进行估算:
表1 — 严重度(S)评分准则
影响
标准:对产品影响的严重度(对顾客的影响)
等级
不符合安全性或法规要求
潜在失效模式影响了汽车的安全行驶;或涉及不符合政府法规的情形,失效发生时无预警;
找出失效起因(机理过程缺陷)的可能性和评价指标。
风险顺序数:英文为Risk Priority Number(简写为RPN),是严重度、频率度和探测度三者的乘积,是用于
帮助决定优先措施的一种方法。
顾客:在FMEA中所指的客户通常是指“最终使用者”,也指更高一层的产品设计工程师、制造或装配生产
工程人员。
在编制DFMEA时,项目小组各成员应将原有类似产品的PFMEA的反馈意见传达给产品研发部,作为产品研发制作DFMEA的输入和修改的依据。
DFMEA作业指导书

DFMEA作业指导书DFMEA(Design Failure Mode and Effects Analysis)是一种用于分析产品设计中潜在失效模式及其影响的方法。
本文将为大家提供一份DFMEA的作业指导书,帮助大家了解和运用这一方法。
第一部分:简介DFMEA是一种应用广泛的风险分析工具,它通过对产品设计中可能存在的失效模式进行评估和分析,以便在设计阶段就能够识别和解决问题,从而降低产品的风险和成本。
第二部分:DFMEA的目的和意义1. 识别潜在的失效模式:通过分析和评估设计中可能出现的失效模式,可以及早发现可能导致产品失效或不达标的问题。
2. 评估失效的严重性:通过评估失效对产品的影响程度和严重性,可以确定哪些失效模式对产品的影响最大,进而有针对性地采取措施进行改进。
3. 确定失效的原因:通过分析失效的根本原因,可以找到解决问题的关键环节,为产品改进提供方向和依据。
4. 制定风险管理计划:通过对失效模式的分析,可以确定开展风险管理活动的重点,并制定相应的风险管理计划。
第三部分:DFMEA的应用步骤1. 确定分析范围:明确分析的对象和目标,确定需要进行DFMEA的产品或系统,明确分析的阶段和范围。
2. 建立分析团队:组建由各个相关领域专家组成的分析团队,确保能够全面、准确地评估失效模式和效应。
3. 列出设计特性:根据产品设计和规范,列出所有相关的设计特性,包括功能性和非功能性特性。
4. 识别失效模式:对每个设计特性进行评估,识别可能出现的失效模式。
确定失效的表现形式和潜在原因。
5. 评估失效严重性:对每个失效模式进行评估,确定失效严重性的指标,包括影响程度、发生频率和控制能力等。
6. 确定风险优先级:根据失效严重性评估结果,确定风险的优先级,确定需要重点解决的失效模式。
7. 制定改进措施:针对高风险的失效模式,制定相应的改进措施,确保产品的可靠性和性能达到要求。
8. 跟踪和控制:跟踪实施改进措施的效果,并建立相应的控制措施,确保产品在整个生命周期中的可靠性和稳定性。
- 1、下载文档前请自行甄别文档内容的完整性,平台不提供额外的编辑、内容补充、找答案等附加服务。
- 2、"仅部分预览"的文档,不可在线预览部分如存在完整性等问题,可反馈申请退款(可完整预览的文档不适用该条件!)。
- 3、如文档侵犯您的权益,请联系客服反馈,我们会尽快为您处理(人工客服工作时间:9:00-18:30)。
Design Failure Mode and Effects Analysis (DFMEA) Instructions
设计失效模式影响及后果分析(DFMEA)指导书
NOTE: Design FMEAs must be prepared for all programs (components, subassemblies and assemblies) where has full program design responsibility. In cases where the OEM Customer has design responsibility, every effort must be made to document OEM special characteristics, including safety, for inclusion in the Design FMEA and Control Plan. (Refer to the AIAG FMEA Manual, VDA, etc, and AIAG APQP and Control Plan manual).
备注:所有具有完全设计责任的项目(零件、分总成和总成)都必须准备设计失效模式影响及后果分析。
如果是OEM客户承担设计责任的项目,那么必须将OEM 特殊特性包括安全性体现在设计失效模式影响及后果分析和控制计划中(参考 AIAG 失效模式分析手册,VDA等,以及AIAD APQP和控制计划手册)
DFMEA templates have been developed to support many products. Refer to these templates to aid in the development of new DFMEAs.
已经开发了许多DFMEA模板来支持很多产品。
开发新的DFMEA时参考这些模版。
DFMEA Templates DFMEA 模板
1.
2.
3.
4.
5.
6.
7.
8.
9.
AE-PLUS-FR-13-CH / Rev 16 (01-October-2009)
Johnson Controls, Inc.
Confidential and Proprietary Page 1 of 1。