PCB常见缺陷原因与措施
PCB常见缺陷及可接受实用标准

PCB常见缺陷及可接受实用标准PCB(Printed Circuit Board,印刷电路板)是现代电子产品中最常见的一种组件,它通过电路的印刷、组装和焊接,将电子元件连接在一起,实现电子设备的功能。
然而,在PCB的制造过程中,常会出现一些缺陷,这些缺陷可能影响电子设备的性能和可靠性。
因此,制造PCB时必须要遵循一些可接受的实用标准,以确保PCB的质量。
1.焊接质量不良:焊接是将电子元件连接到PCB上的重要步骤。
当焊接质量不良时,会导致焊点不牢固,甚至存在焊接虚焊的情况。
这些问题会导致电子元件的连接不可靠,对PCB的性能和可靠性产生负面影响。
2.电路导通不畅:PCB上的导线和线路是电子元件之间传递信号的重要媒介。
如果导线和线路不通畅,就会导致信号传输受阻,影响电子设备的正常工作。
常见的导通不畅问题包括导线断开、导线短路和导线粘连等。
3.隔离不良:在PCB上,不同的电路往往需要隔离开来,以防止相互干扰。
当隔离不良时,就会出现电路互相干扰的情况,影响电子设备的信号稳定性和抗干扰能力。
隔离不良的表现包括隔离距离不足、隔离层不牢固和隔离层污染等。
4.电器仿真效果不佳:在PCB设计阶段,常常需要进行电气仿真,以验证电路设计的正确性和性能。
如果电气仿真效果不佳,就会导致电路设计存在缺陷,无法满足性能要求。
电器仿真效果不佳的原因可以是元件模型不准确、电路参数设置错误和仿真软件问题等。
为了确保PCB的质量,制造业界制定了一些可接受的实用标准,使制造商和消费者能够统一对PCB的质量进行评估。
其中最重要的标准之一是IPC-A-600,它是IPC(Institute of Printed Circuits,印制电路协会)颁布的标准,用来评估PCB的外观和可接受的缺陷等级。
IPC-A-600将PCB的缺陷分为多个等级,从IPC-A-600A到IPC-A-610F,每个等级都对缺陷的种类、数量和位置进行详细的规定,以便制造商和消费者能够根据需求选择合适的等级。
pcb阻焊常见缺陷原因与措施
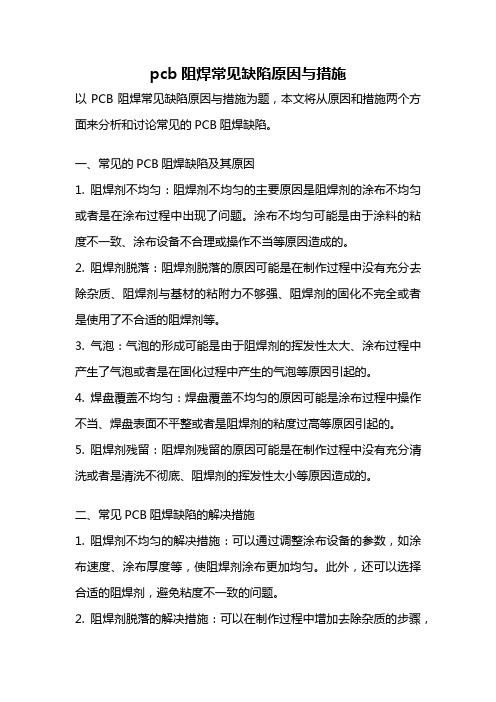
pcb阻焊常见缺陷原因与措施以PCB阻焊常见缺陷原因与措施为题,本文将从原因和措施两个方面来分析和讨论常见的PCB阻焊缺陷。
一、常见的PCB阻焊缺陷及其原因1. 阻焊剂不均匀:阻焊剂不均匀的主要原因是阻焊剂的涂布不均匀或者是在涂布过程中出现了问题。
涂布不均匀可能是由于涂料的粘度不一致、涂布设备不合理或操作不当等原因造成的。
2. 阻焊剂脱落:阻焊剂脱落的原因可能是在制作过程中没有充分去除杂质、阻焊剂与基材的粘附力不够强、阻焊剂的固化不完全或者是使用了不合适的阻焊剂等。
3. 气泡:气泡的形成可能是由于阻焊剂的挥发性太大、涂布过程中产生了气泡或者是在固化过程中产生的气泡等原因引起的。
4. 焊盘覆盖不均匀:焊盘覆盖不均匀的原因可能是涂布过程中操作不当、焊盘表面不平整或者是阻焊剂的粘度过高等原因引起的。
5. 阻焊剂残留:阻焊剂残留的原因可能是在制作过程中没有充分清洗或者是清洗不彻底、阻焊剂的挥发性太小等原因造成的。
二、常见PCB阻焊缺陷的解决措施1. 阻焊剂不均匀的解决措施:可以通过调整涂布设备的参数,如涂布速度、涂布厚度等,使阻焊剂涂布更加均匀。
此外,还可以选择合适的阻焊剂,避免粘度不一致的问题。
2. 阻焊剂脱落的解决措施:可以在制作过程中增加去除杂质的步骤,确保基材的表面干净;同时,选择具有较强粘附力的阻焊剂,并确保其固化完全。
3. 气泡的解决措施:可以选择挥发性较小的阻焊剂,减少气泡的产生;在涂布过程中要注意操作,避免气泡的形成;在固化过程中要控制好温度和时间,确保气泡能够顺利排出。
4. 焊盘覆盖不均匀的解决措施:可以通过调整阻焊剂的粘度,使其更易于涂布;此外,还可以选择合适的涂布工艺和设备,确保阻焊剂能够均匀地覆盖在焊盘表面。
5. 阻焊剂残留的解决措施:在制作过程中要充分清洗阻焊剂,确保其完全去除;可以选择具有较大挥发性的阻焊剂,加快其挥发速度,减少残留。
PCB阻焊常见缺陷的原因有阻焊剂不均匀、阻焊剂脱落、气泡、焊盘覆盖不均匀和阻焊剂残留等。
pcb常见缺陷原因与措施

加强操作人员的安全意识教育, 确保生产过程中的安全和稳定。
04
PCB常见缺陷的检测方法与技 巧
目视检测法
直接观察PCB表面
通过肉眼或放大镜观察PCB表面是否存在裂纹、变形、气泡、污 渍等缺陷。
检查焊接质量
目视检测法可以用于检查焊接质量,如焊点大小、形状、光泽度等 是否符合要求。
识别元器件
目视检测法可以用于识别元器件的型号、规格、极性等是否正确。
焊盘腐蚀
使用合适的清洗剂清洗腐蚀的焊盘,然后用烘干机烘干。
阻焊层缺陷修复方法与技巧
阻焊层脱落
使用合适的涂料重新涂刷脱落的阻焊层,然后用烘干机烘 干。
阻焊层变色
使用合适的清洗剂清洗变色的阻焊层,然后用烘干机烘干 。
阻焊层起泡
检查阻焊层起泡原因,如果是由于涂层过厚导致,可以使 用砂纸打磨起泡区域,然后重新涂刷阻焊层,最后用烘干 机烘干。
生产设备问题
总结词
设备故障或误差
详细描述
PCB生产过程中使用的设备,如钻孔机、曝光机、蚀刻机等,如果出现故障或误 差,可能导致PCB出现孔径不准确、线路不清晰、蚀刻过度等缺陷。
生产工艺问题
总结词
工艺参数不当
详细描述
PCB生产过程中的各项工艺参数,如温度、压力、时间等,如果设置不当,可能导致PCB出现翘曲、起泡、氧化 等缺陷。
优化生产工艺和流程
对生产工艺和流程进行持续改 进,提高生产效率和产品质量 。
引入先进的生产技术和设备, 提高生产自动化程度。
优化生产布局和物流管理,减 少生产过程中的浪费和损失。
提高操作人员技能和素质
加强操作人员技能培训,提高操 作人员的技能水平和操作规范意
识。
建立激励机制,鼓励操作人员积 极参与技术革新和改进活动。
PCB常见缺陷原因与措施.pptx
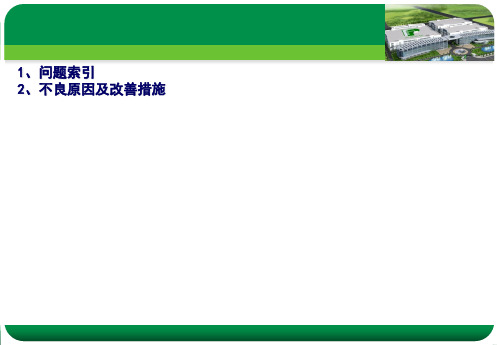
• •
T H E E N D 8、For man is man and master of his fate.----Tennyson人就是人,是自己命运的主人11:0311:03:108.5.2020Wednesday, August 5, 2020
9、When success comes in the door, it seems, love often goes out the window.-----Joyce Brothers成功来到门前时,爱情往往就走出了窗外。 11:038.5.202011:038.5.202011:0311:03:108.5.202011:038.5.2020
• 5、You have to believe in yourself. That's the secret of success. ----Charles Chaplin人必须相信自己,这是成功的秘诀。-Wednesday, August 5, 2020August 20Wednesday, August 5, 20208/5/2020
50、桥连
结束
谢谢!
• 1、Genius only means hard-working all one's life. (Mendeleyer, Russian Chemist) 天才只意味着终身不懈的努力。20.8.58.5.202011:0311:03:10Aug-2011:03
• 2、Our destiny offers not only the cup of despair, but the chalice of opportunity. (Richard Nixon, American President )命运给予我们的不是失望之酒,而是机会之杯。二〇二〇年八月五日2020年8月5 日星期三
Pcb常见问题缺陷类型及原因
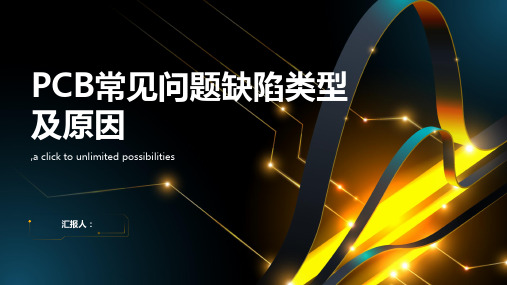
解决方法:a) 加强制造过程中的质量检查,确保线路连接良好;b) 定期检查 和维修,发现断裂及时修复或更换;c) 提高PCB材料的耐久性和稳定性
绝缘不良
类型:绝缘不良
原因:绝缘材料 老化或受潮
影响:导致电路 短路或断路
解决方法:更换 绝缘材料或进行 烘干处理
原因:设计错误、 制造过程中控制 不严格
影响:电气性能 不稳定、产品可 靠性降低
解决方案:重新 设计导体间距、 加强制造过程中 的质量控制
焊盘偏移
定义:焊盘偏移是指焊盘位置与电路设计不一致,导致焊接时出现偏差
原因:a. 电路板生产过程中,焊盘位置精度不足;b. 电路板受热变形; c. 焊接过程中,热压不均匀导致焊盘位移
导体宽度不足
定义:导体宽度小于设计要求,可能导致电流容量不足或电气性能下降。 原因:制造过程中,线宽控制不准确或材料问题导致导体宽度不足。 影响:可能导致电路性能不稳定或产品失效。 解决方案:在制造过程中加强线宽控制,选择合适的材料和工艺。
导体间距不足
定义:导体间距 小于规定的最小 间距,可能导致 电气短路或断路
人为操作失误
操作人员技能不足
操作不规范
责任心不强
疲劳作业
THANKS
汇报人:
环境因素影响
温度:过高或过低的温度可能导致PCB性能下降或出现缺陷 湿度:湿度过高可能导致PCB受潮,引起短路或断路等问题 污染物:空气中的尘埃、化学物质等污染物可能附着在PCB表面,导致缺陷产生 光照:长时间暴露在紫外线下可能导致PCB老化,产生缺陷
设备故障
设备老化或维护不当导致性能下降 设备精度不足或配置不正确 设备操作人员技能水平不足或操作不当 设备供应商的技术支持和服务不到位
pcb常见缺陷原因与措施

焊点氧化
长时间存储可能导致焊点氧化,引起接触不良 或开路。
结构变化
长时间存储可能导致PCB结构变化,如弯曲或变形。
04
检测与修复过程中的常见缺陷 原因
检测设备故障或精度不足
设备老化
设备长时间使用可能导致 部件磨损,影响检测精度 。
设备维护不当
定期维护和保养不到位, 可能导致设备故障。
设备校准问题
制定操作规范
制定详细的操作规范和作业指导书,确保员工严格按照规范进行操 作。
建立激励机制
建立员工激励机制,鼓励员工积极学习和提高自己的技能水平。
加强运输和存储环节的管理和监控
确保运输安全
选择具有良好信誉和稳定运输能力的物流公司,确保 产品在运输过程中不受损坏或丢失。
加强存储管理
制定存储管理规定和操作规范,确保产品存储环境良 好,避免产品在存储过程中受损或变质。
进行定期检查
对存储和运输环节进行定期检查,及时发现和处理可 能出现的问题。
06
针对不同类型缺陷的具体应对 措施建议
针对原材料问题的应对措施建议
严格控制原材料质量
对供应商进行评估和选择,确保原材料的质 量稳定可靠。
加强原材料检验
对进料进行严格检验,确保符合设计要求和 相关标准。
建立原材料追溯体系
对原材料进行标识和追溯,以便及时发现和 解决问题。
设备校准不准确,导致检 测结果偏差。
修复技术不当或材料问题
修复方法选择不当
针对不同缺陷应采用不同的修复方法 ,选择不当可能导致修复效果不佳。
材料质量问题
修复工艺问题
修复过程中工艺控制不当,如温度、 压力、时间等参数控制不准确,可能 导致修复失败。
Pcb常见问题缺陷类型及原因
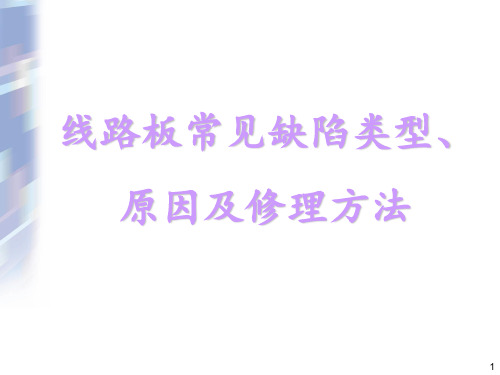
板污 板面有污渍
杂物、药水等污染
锡面不良/锡 薄
1>锡面高低不够 2>锡过薄过厚 3>锡面粗糙
喷锡机速度过快或前处理不好
工序
钻孔工序 干菲林工序
绿油工序
修理方法
不能修理
图例
蚀刻工序的 退锡段
不能修理
菲林制作
白字印上去的可翻 印,蚀刻上去的不能
修理
内层AOI工 序
不能修理
喷锡工序 FQC修理
不可修理
各工序都可 能
包金手指的红胶纸渍没有清洁干净
镀金工序 镀金
内层压板 外层镀金前
工序
轻微: 点金 严重: 不能修理
镀金工序
有布沾菲林水顺着金 手指方向往外擦
图例
16
F)板外围缺点
17
缺陷名称
状况
原因分析
漏斜边
该斜边的地方没 有斜边(金手指位 人为操作错误 置)
漏锣坑位
该锣坑位的地方 没有锣坑位
1>资料出错 2>人为操作错误
状况
原因分析
工序
修理方法
孔内有绿油/ 镀通孔内及锡面应喷 1>绿油冲板时没有冲干净 绿油上锡面 上锡,但被绿油覆盖 2>绿油曝光不良,导致冲不干净
甩绿油
绿油的附着力不够,用 胶纸撕拉时脱落
1>印绿油之前磨板不佳 2>绿油搅拌不均匀 3>印完绿油后锔板时间不够
绿油印歪
对位不正,导致绿油有 规则地上锡圈/锡面
现象
工序
修理方法
图例
蚀刻后各工 轻微可拖锡,严重不
序
可修理
锡面露铜
该上锡的地方没有 锡,而且露出铜面
1>绿油残留于铜面 2>喷锡前处理不佳
pcb常见缺陷原因与措施

pcb常见缺陷原因与措施汇报人:日期:•孔洞和针孔•短路和断路•线路设计不良•基材不良目•环境因素影响•材料和工艺问题录孔洞和针孔孔洞孔的电镀质量不良,导致孔壁有颗粒或凸起。
孔壁上有异物,如金属屑、纤维或灰尘。
电镀过程中,液体内有气泡产生并滞留在孔壁上。
孔洞对孔进行清洁,去除异物和灰尘。
采用高质量的电镀液和电镀设备,提高电镀质量。
对孔径和孔深进行精确控制,确保电镀时能够完全覆盖。
预防措施孔洞在制作PCB时,对孔进行清洁和干燥,避免异物和灰尘的残留。
短路和断路原因分析解决方法预防措施线路设计不良布局不合理走线不规范未遵循最佳实践030201原因分析优化布局修正走线遵循最佳实践解决方法加强设计培训建立PCB设计的审核机制,确保设计的质量和可靠性。
强化审核机制增加技术投入预防措施基材不良基材质量不好基材储存不当原因分析使用高质量的基材储存环境控制解决方法对基材进行严格的质量控制在生产前对基材进行严格的质量检查,包括外观、物理性能和电气性能等指标。
储存环境监控定期对基材储存环境进行检查和维护,确保环境条件符合要求。
预防措施环境因素影响污染物空气中的微粒和有害气体可能污染PCB的表面和内部,导致缺陷。
温度和湿度过高或过低的温度和湿度可能影响PCB的制造过程和性能,导致缺陷的产生。
静电制造过程中的静电可能导致PCB上的微粒移动,产生缺陷。
原因分析控制温度和湿度空气净化静电防护解决方法定期检测空气质量培训员工定期检查和维护环境设备预防措施材料和工艺问题03压合工艺问题01板材选择不当02制造工艺问题原因分析1 2 3选用高质量板材优化制造工艺压合工艺优化解决方法严格控制材料质量对板材、胶片、铜箔等材料进行严格的质量控制,确保其符合制造要求。
加强工艺技术研究不断加强制造工艺技术的研究和开发,提高制造水平。
定期维护设备对制造设备进行定期维护和保养,确保其正常运行,提高制造效率。
预防措施感谢观看。
- 1、下载文档前请自行甄别文档内容的完整性,平台不提供额外的编辑、内容补充、找答案等附加服务。
- 2、"仅部分预览"的文档,不可在线预览部分如存在完整性等问题,可反馈申请退款(可完整预览的文档不适用该条件!)。
- 3、如文档侵犯您的权益,请联系客服反馈,我们会尽快为您处理(人工客服工作时间:9:00-18:30)。
菲林保存不当,使得菲林有变形现象,导致对位偏移。
1、要求资料室及阻焊工序严格控要求控制菲林存放温湿度,并定时检查温 湿度计的值,并进行记录,防止菲林变形。2、阻焊对位人员在进行对位时, 首先确认菲林,与板子进行对位检查,用放大镜查看菲林与板是否能够重 合,发现菲林有变形情况,立即将菲林作报废处理48、焊盘缺陷 49、 Mark点缺陷 50、桥连
不良原因及改善措施
1、阻焊偏位上焊盘
一般性的主要原因(含生产和检验两个方面的原因) 针对原因的控制措施(含执行层面和技能层面)
作业员在对位时,菲林与板对位不准,产生偏移,导致阻焊偏 要求作业员对位后,首先检查对位孔的对准度,再用放大镜检查板内BGA或 位上焊盘。 焊盘的对准度,控制在1.5-2mil之间。保证对位精度。
1、显影前,首先由领班确认显影参数,并作好记录;2、显影时,首先进 显影时,显影速度参数不当,导致阻焊未切底显影掉,残留于 行首板确认,首板确认OK后再进行生产,如果首板不合格,由工艺进行参 焊盘,使之阻焊上焊盘。 数调整,直至首板确认OK,后续板依此参数进行生产;2、显影过程中不允 许任何员工私自调整参数,QA工程师进行在线稽查。
显影时,显影参数设置不当及药液浓度偏高,导致阻焊桥脱落。 检验员在检验时,未知客户不接收阻焊桥脱落这一缺陷,故在检验时, 将顾客的要求列入库存特殊要求数据库,对检验工序员工进行培训宣导,让员工熟知 依照公司检验标准,允许5%的阻焊桥脱进行管控,导致缺陷板流至客户。 香客户的接收标准,便于检验时作好出货控制。
终检领班对派单给各检验员检验外观时,必须对每个型号查询ERP指示,将 终检在检验时,领班没有复核阻焊颜色要求,导致流程卡上无阻 ERP上顾客的特殊要求及阻焊颜色等备注在流程卡上,检验员在检验时,首先 焊颜色要求指示,检验员在检验时,未对阻焊颜色作管控。 将生产实板与领班备注的内容进行核对,当发现有不符项时,及时反馈。
板子在烤箱内放置不规范,导致板子局部受热不均,出现色差
印刷完阻焊的板子,在烘烤时,烘烤时间过长,导致阻焊受热烘 在烘板时,每一型号必须记录烘板时间和出板时间,当烘板时间达到后必须 烤过度,出现颜色变异。 立即将板取出冷却。流程QA进行在线稽查。
绿色油墨及黄色油墨的板,在喷锡后,部分板子有返工,进行返 规定喷锡返工只允许返喷锡一次,喷锡完后必须与原板子进行阻焊颜色对比, 喷锡,由于阻焊经高温的冲击会产生颜色变异,故导致返喷锡板 如果阻焊颜色产生明显差异,即作报废处理。 阻焊颜色与正常板阻焊颜色产生色差。 到终检的板有部分因修理补油,终检再次烘板时间过长,导致板子 规定终检修理补油板再次烘板时必须进行烘烤时间记录,避免长时间烘板而 阻焊与正常生产板阻焊颜色产生色差。 导致阻焊颜色出现变异,产生阻焊色差。 客户对阻焊颜色没有提出特别要求,由于绿色及黄色阻焊本身的 1、若客户对阻焊颜色有特别要求,建议客户在制作说明中进行备注。2、由 特性,在制程中控制较大很大,易出现色差,故终检在检验时, 于绿色及黄色油墨本身的特性,在制程中控制难度大,建议客户提供阻焊颜 未作管控,按正常板出货。 色差异接收标准,终检在出货时依标准进行出货管控。
要求工序在显影前,首先确认显影机各参数(包括:显影温度、显影压力、 显影时,显影参数设置不当及药液浓度偏低,导致孔内阻焊没有 显影速度)及当天化学实验室对显影液的浓度分析,确保参数及显影液浓度 冲洗干净。 在受控范围后再进行显影生产。
1、由终检主管对检验员进行检验方法的培训,针对孔的检验方法,在检验时, 1、检验员在检验时,因检验方法不当,导致阻焊入孔的板未被 将两块或三块板叠合在一起,对着灯光呈50度角进行查看,确认孔内是否有 检验出来,流至客户端;2、检验人员对阻焊入过孔的标准不清 阻焊;2、由终检主管对员工定期进行产品接收标准的培训,并进行考试,确 楚导致问题板漏到客户手中。 保员工明确各缺陷的接收标准。
顾客有要求阻焊颜色预审漏看按常规颜色制作。
阻焊工序生产时,没有查看ERP指示,按照常规颜色制作,导致 生产前,统一由领班对各型号查询ERP指示,将要求之阻焊颜色备注于流程卡 错误。 阻焊工序一栏,员工依流程卡上的指示进行油墨选定。
员工在查询ERP指示时,同时打开有多个ERP,导致在查看时,因 生产前,统一由领班查询ERP指示,当任务栏上打开有多个ERP时,将其进行 不仔细,看错对应型号,将其它型号之ERP上指示的阻焊颜色备 关闭,重新打开一个ERP进行查询,避免混淆,导致查询错误。 注到了实际需查询的型号之流程卡上。
1、问题索引 2、不良原因及改善措施
问题索引
1、阻焊偏位上焊盘 2、盘中孔曝油 3、阻焊脱落 4、阻焊色差 5、阻焊颜色做错 6、阻焊桥脱落 7、阻焊入孔 8、漏阻焊塞孔 9、过孔假性露铜 10、测试孔(焊盘)漏开窗 11、焊盘余胶(显影不净) 12、阻焊杂物 13、板面划伤 14、字符上焊盘 15、字符重影
不良原因及改善措施
4、阻焊色差
批量板中部分板在生产过程中,有进行套印,套印后的板因阻焊 规定:板子若需返工阻焊,要求工序必须将原阻焊退洗掉,然后再按正常板 厚度有其差异,导致与正常印刷的板产生颜色差异,出现颜色深、 生产流程重新进行阻焊印刷,不允许直接在印有阻焊的板上进行阻焊套印。 浅现象。 要求员工在放板时,必须严格按照工艺规定的烘板放置要求进行放置,使板 子受热均匀,避免出现局部色差。
16、字符模糊 17、字符印错层 18、漏印字符 19、板面沾字符油 20、字符变色 21、板厚不符 22、叠层错误 23、白斑 24、板翘 25、分层起泡 26、多孔 27、少孔 28、孔偏 29、PTH孔径超公差 30、NPTH孔径超公差
问题索引
31、NPTH孔晕圈 32、阶梯孔做反 33、孔铜不足 34、孔电阻超标 35、锡堵孔 36、孔内毛刺 37、喷锡板可焊性不良 38、沉金板可焊性不良 39、水金板可焊性不良 40、表面工艺做错 41、过孔不通 42、开路 43、 V-CUT缺陷 44、外形缺陷 45、标记缺陷
不良原因及改善措施
6、阻焊桥脱落
客户文件中设计之阻焊桥宽度不超过我司生产制作阻焊桥的能力,工程 与顾客沟通针对超公司生产能力的处理规则,加入到该顾客的特殊要求中 处理时没有与顾客进行确认,直接按照公司《工程常规问题处理办法》 去掉阻焊桥,做成开通窗。 顾客设计的阻焊桥宽度满足做生产做阻焊桥要求,但CAM人员在处理 对制作完成的文件进行检查时,使用矩形图查看Pad to Pad spacing信息,检查阻焊制 时,误将其做成阻焊开通窗。 作是否与顾客要求一致。 要求工序在印刷阻焊时,必须依据ERP指示要求之阻焊厚度来对印刷之刮刀角度及力 阻焊印刷时,板面油墨印得太厚,曝光时底层的油墨光聚合反应未完全, 度等进行调节,印刷时进行首板制作,并且油墨厚度规进行厚度测量,符合ERP指示 显影时底层油墨受Na2CO3或K2CO3溶液的浸蚀,造成阻焊桥脱落。 厚度要求后再进行其它厚的印刷。 预烘前,首先由员工依照不同阻焊颜色对其预烘时间及温度之要求对烘箱参数时行设 印完阻焊后进行预烘板时,预烘时间太短、温度太低,使得底层油墨预 定,并每周由设备部和阻焊工序对预烘箱的温度均匀性及温差进行测量,检查其温度 固化程度不够,显影时造成阻焊桥白化,undercut过大,造成脱落。 差异是否在控制范围。 曝光能量太低,造成油墨光聚合反应不完全,显影时底层油墨受Na2CO3 要求工序在曝光前,依照各种油墨特性对其参数之要求,首先需用曝光尺测量曝光能 或K2CO3溶液的攻击,造成阻焊桥脱落。 量,当曝光能量符合要求后再进行阻焊曝光。 阻焊曝光后停留时间过短,导致油墨的聚合交联反应尚未完全,使得油 要求工序对阻焊板曝完光后,必须停留15分钟以上才能进行阻焊显影,确保油墨的聚 墨与基材的附着力差,显影时将阻焊桥冲洗掉。 合交联反应完全,使阻焊桥与基材结合牢固。
1、定期将客诉问题板及不良图片给检验员进行现场培训,提高员工对缺陷 检验员在检验过程中,因检验不仔细或检验技能不够,导致检 的识别能力;2、定期对员工的技能进行培训和检出能力考核,保持员工的 验漏检。 整体操作和检验技能水平。
不良原因及改善措施
2、盘中孔曝油
1、阻焊工序塞完孔后,对板子的烘烤方式不当,未执行分段 1、要求工序针对盘中孔塞孔的板必须实行分段固化,依照要求控制分段固 固化的时间及温度,采用同一温度进行烘板,这样孔内水气受 化的时间及温度,使阻焊逐淅固化。避免曝油。 热澎胀,阻焊曝裂。
不良原因及改善措施
5、阻焊颜色做错
预审错误,由于顾客信息提供了两种阻焊颜色,未与顾客确认; 当顾客提供不同信息冲突时在预审表中记录与顾客确认; NOPE更改时,顾客要求更改阻焊,CAM制作人员忘记更改ERP 制作更改单时,制作人员按《产品资料更改作业标准步骤》进行更改,防止 指示信息。 单凭记忆制作遗漏,由专人稽查执行情况。 CAM人员审核客户信息与预审信息不一致又没有确认信息时需与预审人员确 认
要求工序在显影前,首先确认显影机各参数(包括:显影温度、显影压力、显影速度) 及当天化学实验室对显影液的浓度分析,确保参数及显影液浓度在受控范围后再进行 显影生产。 后固化前,首先由员工依照不同阻焊颜色对其后固化时间及温度之要求对烘箱参数时 阻焊后固化烘烤时间及温度不足,使得阻焊与基材的结合力降低,经3M 行设定,并每周由设备部和阻焊工序对预烘箱的温度均匀性及温差进行测量,检查其 胶带试验后产生阻焊桥脱落。 温度差异是否在控制范围。 后固化前,首先由员工依照不同阻焊颜色对其后固化时间及温度之要求对烘箱参数时 针对沉金板,由于后固化时间过长或固化温度过高,导致阻焊油墨变脆, 行设定,并每周由设备部和阻焊工序对预烘箱的温度均匀性及温差进行测量,检查其 由于沉金药液对其阻焊具有攻击性,导致阻焊桥掉油、脱落。 温度差异是否在控制范围。
3、阻焊脱落
阻焊印刷后,烘板时间及温度不够,导致阻焊未完全固化,经 要求阻焊工序在烘板前,首先确认烘板设定温度及时间,参数OK后再进行烘 过客户端过炉高温冲击后,阻焊分层起泡。 板,并由领班负责将其参数进行完整性记录,QA进行稽查。 阻焊油墨过薄,沉金后,由于沉金药液对阻焊有攻击性,导致 要求阻焊工序在进地阻焊印刷时,必须将首板采用阻焊测厚仪进行阻焊厚度 阻焊脱落。 的测量,依其厚度来调整机台,阻焊厚度达到ERP指示要求后再进行生产。 阻焊前处理对板子处理效果不好,铜面有单点氧化,导致阻焊 1、板子在过前处理时,要求阻焊工序首先确认前处理生产参数(速度、烘 与板面结合力差,经烘烤后出现阻焊起泡(板子烘干度不够, 干段温度),是否与工艺要求一致,参数调整OK后再进行生产;2、定期对 使得过孔孔内有水气,导致孔口边缘铜面氧化,使得阻焊与铜 前处理机进行保养,并检查前处理磨刷滚轮及吸水海棉是否有磨损。 面的结合力不好,经烘后或过炉时使之产生阻焊起泡)。 规范阻焊工序过前处理的板,必须在2小时内完成阻焊印刷,超过2小时未印 阻焊过前处理后,在阻焊房内停留时间过长,使之铜面出现单 刷的板,必须重新过前处理后再进行印刷。(过前处理的板由阻焊工序进行 点氧化,导致阻焊与板面结合力差,经烘烤后出现阻焊起泡。 时间记录)。 搅拌阻焊时,开油水舔加过多,喷锡或过炉时,过孔之间的油 要求生产工序员工在搅拌阻焊时,必须依照工艺规范要求规定的比例进地开 墨挥发膨胀,导致阻焊脱落起泡。 油水的添加,由领班进行审核监督。