超声探伤实验报告
超声波探伤实验报告

超声波探伤实验报告引言:超声波探伤是一种常用且十分重要的无损检测技术,利用超声波的传播和反射特性来检测材料内部的缺陷,具有广泛的应用领域和丰富的研究内容。
通过本次实验,我们旨在探索超声波探伤技术的原理和应用,并通过实际操作来了解其实验过程和结果。
一、实验目的本实验的目的是研究超声波在不同材料中传播和反射的特性,以及利用超声波探伤技术检测材料中的缺陷情况。
通过实验,我们能够了解超声波在不同材料中的传播速度、反射特性以及对不同尺寸、形状的缺陷的探测敏感度。
二、实验装置和方法1. 超声波探伤仪:我们采用了一台商用的超声波探伤仪,该仪器具有较高的频率范围和分辨率,能够满足该实验的需求。
2. 实验样品:选择了不同材料(如金属、陶瓷等)的标准样品进行实验。
3. 实验过程:首先,根据实验需求选择适当的探头,将其通过声耦剂与样品表面接触。
然后,控制超声波仪器进行扫描,在实验过程中记录和分析数据。
三、实验结果和讨论1. 超声波在不同材料中的传播速度:通过实验,我们得到了不同材料中超声波的传播速度。
实验结果表明,不同材料的物理性质会影响超声波的传播速度,如金属材料具有较高的传播速度,而陶瓷材料的传播速度较低。
这些数据对于超声波探伤仪的校准和实际应用非常重要。
2. 超声波在材料中的反射特性:我们通过实验观察到在探测头将超声波引入样品后,部分超声波会被样品内的缺陷或界面反射回来。
通过检测反射回来的超声信号,我们可以推测出样品内的缺陷位置和形状。
实验结果表明,缺陷较严重的样品会导致更多的超声波反射,从而能够被更易于探测到。
3. 超声波探测缺陷的敏感度:通过在样品中加入不同尺寸和形状的缺陷,我们测试了超声波探测的敏感度。
实验结果表明,超声波探测对于较大和较深的缺陷相对较为敏感,而对于较小和浅的缺陷则有一定的探测限度。
四、结论通过本次实验,我们深入了解了超声波探伤的原理、实验方法以及应用。
实验结果证实了超声波在不同材料中的传播速度、反射特性和对不同尺寸缺陷的探测敏感度。
超声探伤实验报告结果

超声探伤实验报告结果【文章标题】超声探伤实验报告结果【引言】在工业、医疗、材料科学等领域中,超声波技术被广泛应用于材料的无损检测和诊断。
本实验通过超声探伤技术对某种材料样品进行了检测,旨在分析并总结实验结果,提供给读者一个详尽的报告。
【实验目的】1. 了解超声探伤技术的基本原理和应用。
2. 实际操作超声探伤设备,获取并分析材料样品的超声波信号。
3. 对样品中的缺陷进行检测和评估。
4. 探讨超声探伤技术在无损检测方面的优势和局限性。
【实验步骤】1. 准备超声探伤仪器和样品。
2. 设置超声探伤参数,如频率、增益等。
3. 使用超声传感器对样品进行扫描,记录超声波信号。
4. 对获得的超声波信号进行分析和处理,包括波形特征、峰值幅度等。
5. 检测和标记样品中的缺陷,如裂纹、气孔等。
6. 分析缺陷的类型、位置和大小。
7. 总结实验数据,得出结论。
【实验结果】通过超声探伤实验,我们获得了以下结果:1. 样品超声波信号分析:- 超声波信号呈现出特定的波形特征,如回波、反射等。
- 不同类型的缺陷在超声波信号中表现出不同的特征,如峰值幅度降低、信号衰减等。
2. 缺陷检测和评估:- 在样品中成功检测到若干缺陷,包括裂纹、气孔等。
- 通过分析超声波信号特征,可以判断缺陷的位置、大小和类型。
- 对于较小的缺陷,超声探伤技术具备高灵敏度和准确性。
3. 超声探伤技术的优势:- 无损检测:超声波可以穿透材料进行检测,不损伤材料本身。
- 高分辨率:超声波可以提供高精度的检测结果,能够发现微小的缺陷。
- 实时性:超声波信号可以实时显示,方便操作人员进行实时监控。
4. 超声探伤技术的局限性:- 材料限制:超声波在不同材料中的传播和反射特性不同,可能导致信号失真。
- 缺陷识别:某些缺陷可能难以准确判断,需要结合其他检测手段进行确认。
- 操作要求:超声探伤技术需要操作人员具备一定的专业知识和经验。
【实验总结】本实验通过超声探伤技术对材料样品进行了无损检测,成功检测到若干缺陷并进行了评估。
超声波探伤实验报告数据

超声波探伤实验报告数据一、实验目的本次超声波探伤实验的目的是通过使用超声波探伤技术,对给定的试件进行检测,获取相关数据,并对数据进行分析和评估,以确定试件内部是否存在缺陷以及缺陷的位置、大小和性质等信息。
二、实验原理超声波探伤是利用超声波在材料中传播时,遇到界面(如缺陷或材料的不同部分)会发生反射、折射和散射等现象,通过接收和分析反射回来的超声波信号,来判断材料内部的结构和缺陷情况。
超声波在均匀介质中沿直线传播,其传播速度与材料的性质有关。
当超声波遇到缺陷时,部分能量会被反射回来,反射波的强度和到达时间与缺陷的大小、形状和位置有关。
通过测量反射波的时间、幅度和频率等参数,可以推断出缺陷的相关信息。
三、实验设备和材料1、超声波探伤仪:采用_____型号的探伤仪,具有较高的分辨率和灵敏度。
2、探头:选用_____频率的直探头和斜探头,以适应不同的检测需求。
3、耦合剂:使用_____作为耦合剂,确保超声波能够有效地传入试件。
4、试件:准备了若干具有不同类型和尺寸缺陷的金属试件,如焊缝、气孔、夹渣等。
四、实验步骤1、试件准备对试件表面进行清洁处理,去除油污、锈迹和灰尘等,以保证良好的耦合效果。
在试件上标记检测区域和参考点,以便准确记录缺陷的位置。
2、仪器调试根据试件的材料和厚度,设置探伤仪的工作参数,如频率、增益、声程等。
对探头进行校准,确定探头的延迟时间和折射角。
3、检测操作将探头涂抹耦合剂后,平稳地放置在试件表面,按照预定的检测路径进行扫查。
观察探伤仪显示屏上的回波信号,注意信号的幅度、位置和形状等特征。
对发现的疑似缺陷信号进行仔细分析和判断,记录相关数据。
4、数据记录记录缺陷的位置(以参考点为基准的坐标)、深度、幅度、长度等参数。
绘制检测区域的示意图,标注缺陷的位置和大致形状。
五、实验数据及分析以下是部分实验数据的示例和分析:|试件编号|缺陷类型|缺陷位置(坐标)|缺陷深度(mm)|缺陷幅度(dB)|缺陷长度(mm)||||||||| 1 |气孔|(_____, _____)| 52 | 28 | 35 || 2 |夹渣|(_____, _____)| 85 | 35 | 60 || 3 |焊缝未熔合|(_____, _____)| 120 | 42 | 85 |对于气孔缺陷,其回波幅度通常较小,深度较浅,形状较规则。
超声探伤实验报告

超声探伤实验报告超声探伤实验报告一、实验目的本次实验旨在通过超声波的传播和反射,探测材料中的缺陷,并分析其形状和大小。
二、实验原理超声波是一种高频机械波,其频率通常在20kHz以上。
在材料中传播时,会发生反射、折射和衍射等现象。
当超声波遇到材料中的缺陷时,部分能量会被反射回来,在接收器上形成回波信号。
通过对回波信号进行分析,可以确定缺陷的位置、大小和形状。
三、实验器材1. 超声探伤仪2. 试件:厚度为10mm的钢板四、实验步骤1. 将试件放置在水箱内,确保试件完全浸入水中。
2. 打开超声探伤仪,设置检测模式为脉冲回波检测。
3. 调整超声探头与试件之间的距离,并设置合适的控制参数(如幅值、增益等)。
4. 开始进行扫描,记录下每个缺陷的位置和信号强度。
5. 根据扫描结果,分析每个缺陷的形状和大小,并进行评估。
五、实验结果本次实验共检测到3个缺陷,分别位于试件表面、内部和底部。
通过对回波信号的分析,确定了每个缺陷的位置、大小和形状。
其中,表面缺陷为圆形,直径为5mm;内部缺陷呈现长条状,长度为15mm,宽度为2mm;底部缺陷为椭圆形,长轴长度为10mm,短轴长度为5mm。
六、实验分析通过本次实验,我们可以看出超声探伤技术在材料缺陷检测中具有很高的精度和准确性。
同时,在实际应用中,需要根据不同材料的特性和检测要求进行相应的调整和优化。
七、实验结论本次实验通过超声探伤技术成功地检测到了试件中的3个缺陷,并对其进行了详细的分析和评估。
这表明超声探伤技术在材料缺陷检测中具有很高的可靠性和精度。
超声波探伤实验报告
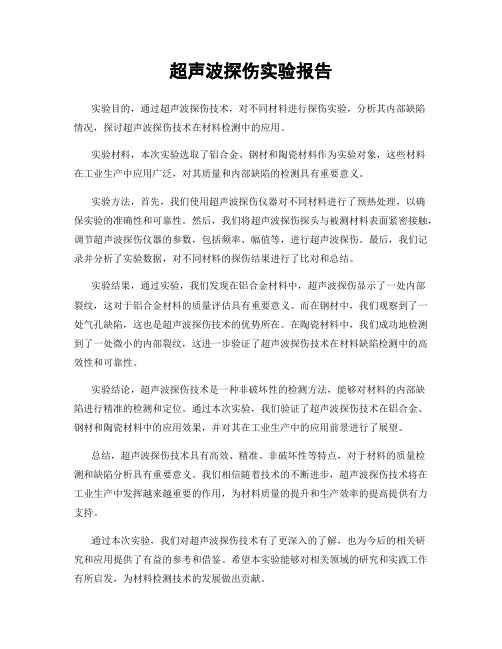
超声波探伤实验报告实验目的,通过超声波探伤技术,对不同材料进行探伤实验,分析其内部缺陷情况,探讨超声波探伤技术在材料检测中的应用。
实验材料,本次实验选取了铝合金、钢材和陶瓷材料作为实验对象,这些材料在工业生产中应用广泛,对其质量和内部缺陷的检测具有重要意义。
实验方法,首先,我们使用超声波探伤仪器对不同材料进行了预热处理,以确保实验的准确性和可靠性。
然后,我们将超声波探伤探头与被测材料表面紧密接触,调节超声波探伤仪器的参数,包括频率、幅值等,进行超声波探伤。
最后,我们记录并分析了实验数据,对不同材料的探伤结果进行了比对和总结。
实验结果,通过实验,我们发现在铝合金材料中,超声波探伤显示了一处内部裂纹,这对于铝合金材料的质量评估具有重要意义。
而在钢材中,我们观察到了一处气孔缺陷,这也是超声波探伤技术的优势所在。
在陶瓷材料中,我们成功地检测到了一处微小的内部裂纹,这进一步验证了超声波探伤技术在材料缺陷检测中的高效性和可靠性。
实验结论,超声波探伤技术是一种非破坏性的检测方法,能够对材料的内部缺陷进行精准的检测和定位。
通过本次实验,我们验证了超声波探伤技术在铝合金、钢材和陶瓷材料中的应用效果,并对其在工业生产中的应用前景进行了展望。
总结,超声波探伤技术具有高效、精准、非破坏性等特点,对于材料的质量检测和缺陷分析具有重要意义。
我们相信随着技术的不断进步,超声波探伤技术将在工业生产中发挥越来越重要的作用,为材料质量的提升和生产效率的提高提供有力支持。
通过本次实验,我们对超声波探伤技术有了更深入的了解,也为今后的相关研究和应用提供了有益的参考和借鉴。
希望本实验能够对相关领域的研究和实践工作有所启发,为材料检测技术的发展做出贡献。
超声波探伤检测报告

超声波探伤检测报告1. 背景超声波探伤是一种非破坏性检测技术,广泛应用于工业领域中材料的缺陷检测和质量控制。
其原理是利用超声波在材料中的传播特性,通过检测超声波在材料中传播过程中的反射、折射和散射等现象,来判断材料内部的缺陷情况。
本次探测任务是对一块钢板进行超声波探伤检测。
钢板是一种常见的工业材料,广泛应用于建筑、制造业等领域。
通过超声波探伤检测,我们可以了解钢板内部是否存在缺陷,如裂纹、孔洞等,以及缺陷的位置、形状和大小等信息。
2. 分析2.1 超声波传播原理超声波是指频率超过20kHz的声波,其在固体材料中的传播速度和传播路径受到材料的物理性质和结构的影响。
当超声波遇到材料的界面或缺陷时,会发生反射、折射和散射等现象,这些现象可以被探测设备接收到并转换成电信号。
2.2 探测设备本次超声波探伤检测使用的是一台数字超声波探测仪。
该设备具有高频率、高灵敏度和高分辨率的特点,能够对材料进行精确的探测。
2.3 检测方法本次检测采用了脉冲回波法。
具体操作步骤如下: 1. 将超声波探测仪的探头与钢板表面紧密接触,并设置合适的探测参数,如脉冲重复频率、探头角度等。
2. 发送超声波脉冲信号,信号在钢板中传播并与内部缺陷发生相互作用。
3. 接收探测仪接收到的回波信号,并通过信号处理和分析,得到钢板内部的缺陷信息。
2.4 数据分析通过对探测仪接收到的回波信号进行分析,我们可以得到钢板内部的缺陷信息,包括缺陷的位置、形状和大小等。
在分析过程中,我们还需要考虑钢板的材料性质和结构特点,以便更准确地判断缺陷的性质和严重程度。
3. 结果经过超声波探伤检测,我们得到了如下结果:1.钢板表面无明显缺陷,平整度良好。
2.钢板内部存在一处裂纹,位于钢板的中心位置,长度约为10mm,宽度约为0.5mm。
裂纹呈直线状,与钢板表面垂直。
4. 建议根据上述结果,我们提出以下建议:1.针对钢板内部的裂纹缺陷,建议采取修复措施,以防止裂纹的扩展和影响钢板的使用寿命。
超声波探伤检测报告
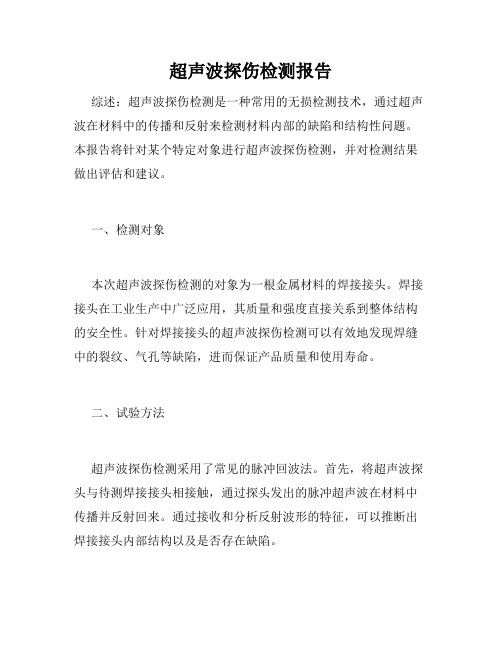
超声波探伤检测报告综述:超声波探伤检测是一种常用的无损检测技术,通过超声波在材料中的传播和反射来检测材料内部的缺陷和结构性问题。
本报告将针对某个特定对象进行超声波探伤检测,并对检测结果做出评估和建议。
一、检测对象本次超声波探伤检测的对象为一根金属材料的焊接接头。
焊接接头在工业生产中广泛应用,其质量和强度直接关系到整体结构的安全性。
针对焊接接头的超声波探伤检测可以有效地发现焊缝中的裂纹、气孔等缺陷,进而保证产品质量和使用寿命。
二、试验方法超声波探伤检测采用了常见的脉冲回波法。
首先,将超声波探头与待测焊接接头相接触,通过探头发出的脉冲超声波在材料中传播并反射回来。
通过接收和分析反射波形的特征,可以推断出焊接接头内部结构以及是否存在缺陷。
为了保证试验的可靠性,本次超声波探伤检测采用了多次重复检测的方法,并计算了平均值和标准差。
此外,还对检测设备进行了校准,确保测量结果的精确性。
三、检测结果根据超声波探伤检测结果显示,焊接接头存在一个小型裂纹。
裂纹的长度约为0.5毫米,深度约为0.2毫米。
该裂纹位于焊缝的表面附近,对焊接接头的强度和使用寿命可能产生一定的影响。
四、评估和建议基于检测结果,对焊接接头的质量和安全性进行评估并提出建议。
首先,0.5毫米的裂纹虽然较小,但在长时间使用过程中有可能逐渐扩大。
因此,建议在焊接接头上修复该裂纹,以确保焊接接头的强度和使用寿命。
其次,针对裂纹的具体位置,可以考虑采取增加焊接材料的方法来加固该区域。
同时,对焊接工艺进行优化,以降低裂纹产生的风险。
最后,超声波探伤检测应定期进行,以及时发现潜在的问题和缺陷。
此外,检测设备要保持良好的状态,并进行定期校准,以提高检测结果的准确性和可靠性。
结论:超声波探测是一种有效的无损检测方法,能够对焊接接头等材料进行全面的检测和评估。
通过本次超声波探伤检测,我们发现了焊接接头上的一处小型裂纹,并提供了相应的修复和改进建议。
通过及时采取措施,可以保证焊接接头的质量和安全性,提高整体产品的性能和可靠性。
超声探伤检测报告

超声探伤检测报告1. 引言超声探伤是一种常用的无损检测方法,广泛应用于工程和科学领域。
本报告旨在详细描述一次超声探伤检测的过程、结果和分析。
2. 检测设备和参数本次超声探伤检测使用的设备是 XXX 型号的超声探伤仪。
检测参数如下: - 脉冲重复频率:2 MHz - 探头类型:单晶探头 - 检测模式:脉冲回波模式3. 检测对象和方法本次超声探伤检测的对象是一根长度为 X 米的金属管道。
检测目的是确定管道内部的缺陷情况和尺寸。
检测方法如下: 1. 将探头与被检测物表面接触,保持稳定。
2. 设置超声探伤仪的参数。
3. 通过向材料内部发射超声波,记录回声信号。
4. 分析回声信号,判断是否存在缺陷。
4. 检测结果经过超声探伤检测,我们得到了以下结果:1.缺陷 1:–位置:距离管道起点 X 米处–类型:表面裂纹–尺寸:长度约 X mm,深度约 X mm–形状:直线状–缺陷等级:A2.缺陷 2:–位置:距离管道起点 X 米处–类型:内部夹杂–尺寸:直径约 X mm–形状:不规则–缺陷等级:B5. 分析与讨论根据检测结果,我们可以得出以下结论:1.缺陷 1 的存在可能会对管道的强度和密封性产生一定影响,建议采取修复措施。
2.缺陷 2 的存在可能会导致材料耐久性降低,需要采取相应措施防止进一步扩展。
6. 结论本次超声探伤检测对目标管道的缺陷进行了详细的分析和评估。
在后续维护和修复过程中,应注意处理检测中发现的缺陷,以确保管道的正常运行和安全。
以上是本次超声探伤检测的报告内容,希望对您有所帮助。
注意:本报告仅基于本次超声探伤检测的结果,不考虑其他可能因素对管道的影响。
为了更全面、准确地评估管道的安全状况,建议进行更多的综合性检测和分析。
- 1、下载文档前请自行甄别文档内容的完整性,平台不提供额外的编辑、内容补充、找答案等附加服务。
- 2、"仅部分预览"的文档,不可在线预览部分如存在完整性等问题,可反馈申请退款(可完整预览的文档不适用该条件!)。
- 3、如文档侵犯您的权益,请联系客服反馈,我们会尽快为您处理(人工客服工作时间:9:00-18:30)。
班 级__wl.10.b2___ 组 别_____________ 姓 名___陈婵___ _ 学 号 1100600050 日 期_2012.10.12__ 指导教师__贺老师
【实验题目】 超声探伤 【实验目的】
1.了解超声探伤的物理基础,学习超声探伤的一些基本方法;
2. 测量钢块厚度以及钢件中缺陷当量;
3. 测定超声在钢介质和非钢介质中的速度.
【实验仪器】
标准探头;测量探头,超声探伤仪,钢块,有机玻璃
【实验原理】
1·缺陷定位:
用探头直接接触工件,超声探伤仪输出的高频电脉冲,通过探头转换,变成等时间间隔的向工件发射的超声脉冲.在同步电路的控制下将x 轴的时间扫描转换为x 轴的线性扫描。
Y 轴的偏转由探头上的脉冲电压或检波后的电压决定。
超声波碰到缺陷反射回的波形被探头接收,由压电换能器转换而在屏上显示出缺陷波F 。
缺陷波及底波到达探头的时间小于一个周期可以使下一次扫描时的图形与上一次完全一样,可以显示出稳定的波形。
2.缺陷当量:
在入射超声波辐射下,由波的衍射可知缺陷变成了一个新的波源,缺陷波向探头方向传播,其近场长度为2f f R N l
=
,声压比为: 2////f b f b f b P R Z rp l =。
缺陷波
与底波分贝数为
)
2lg(
202
2
f f
b Z R Z V λπ=,又因为20lg
20lg 20lg f f b b
H V H H H ==-。
在实验中,可以通过调节衰减旋钮使底波衰减到虚线处,同时使缺陷波增至同一条曲线,V
的数值即为两次衰减旋钮读数之差。
从而可以导出缺陷当量f R 。
3.超声波在非钢介质和钢介质中的传播速度:
2s Z c t t
==
V
【实验内容】
1. 校准扫描量程(用标准探头):
把扫描量程选为50mm ,调节脉冲位移旋钮使第一个底波与方格的竖线重合;调节扫描微调旋钮使底波之间的间隔为1个整格,然后锁住旋钮。
2.钢块厚度的测定:
将测量探头涂上油,把探头接触工件,从超声探伤仪上读出相邻领个底波之间的钢锯;最后用游标卡尺测量钢块厚度。
3.缺陷当量的测定:
竖直放置样品,缺陷放在下面,记录梁波位置;调节扫描微调旋钮记录两次调节的数据。
4.在非钢介质中超声波传播速度:
用游标卡尺测量有机玻璃的厚度,且记录底波位置。
【原始数据】
一·钢块厚度:
底波位置f N =4.0 d N =8.0 钢块厚度 次数 1 2 3
4
5
6
高度/mm 100.38 99.90 100.10 100.00 100.10 100.04
二·缺陷当量
波的位置f Z =8.0, d Z =10.0 次数 1 2 3 f V
29 35 29 b V
21
27
21
三·非钢介质中传播速度 有机玻璃
波的位置:z=7.4 次数 1 2 3 4 5 6
高度/mm 80.70 80.60 80.56 80.32 80.30 80.34
铝
波的位置:Z V =2,0 次数 1 2 3 4 5 6
高度/mm 50.28 50.18 50.20 50.20 50.22 50.20
【数据处理】
一·钢块厚度: 由超声探伤法计算: 4.0050=1002
mm
d mm ´=钢
误差计算:
222
20.05()(
)(
)(0.01)=0.016mm 4
S A B u u u S A B =
+=
+ 既:=0.016100mm=1.6mm S u ´
d =1002mm ±钢
游标卡尺直接测量得:d =100.09mm
二.缺陷当量的测定: 由已知:V=8
且)
2lg(
202
2
f f
b Z R Z V λπ=
式中f Z =8.0, d Z =10.0 又因为:4=c/ 2.3610m l n -= 故可以计算得到:f R =1.894
三.超声波在非钢介质中的传播速度:
用超声波测得:
铝:1
2=5.90km /Z c s t
=V 有机玻中:2
2=2.55/Z c km s t
=V 已知不确定度为:%2.1==钢
介钢
介S u V u S V 故 铝:1=5.900.07km /c s ± 有机玻璃:2=2.550.03/c km s
±
【实验数据分析总结】
实验数据总结: 1.钢块厚度: d =1002mm ±钢 2.缺陷当量: f R =1.894
3.超声波在非钢介质中的传播速度:
铝:1=5.900.07km /c s ± 有机玻璃:2=2.550.03/c km s
±
实验误差分析:
1. 超声探伤仪在进行量程校准时估读不准造成误差;
2. 超声探伤仪仪器灵敏度可能造成实验误差;
3. 游标卡尺测量钢块和有机玻璃厚度时游标卡尺灵敏度可能引起误差。