轧钢用水平连铸圆坯标准
连铸圆坯标准

连铸圆坯标准
连铸圆坯是指通过钢铁连铸技术,在连铸机上连续铸造出的圆形钢坯。
目前,国家标准中对连铸圆坯的技术要求主要包括以下两个标准:
GB/T 17426-2019《连铸钢坯尺寸、形状、重量和允许偏差》:该标准规定了连铸钢坯尺寸、形状、重量和允许偏差的技术要求,包括圆径、圆周、偏差、重量等方面的要求。
GB/T 6394-2017《钢铁产品取样方法》:该标准规定了钢铁产品取样的方法和规范,包括取样位置、数量、样品标识和保存等要求。
除了以上两个标准,还有许多与连铸圆坯生产相关的标准和规范,如废钢管理、铸坯表面质量要求等。
这些标准和规范对于保障连铸圆坯的生产质量和安全性具有重要意义。
1。
连铸圆坯质量控制

连铸圆坯质量控制连铸坯质量检验及控制一、连铸坯的内部结构(凝固组织)的一般特征及检验。
连铸坯的检验方法连铸坯的内部结构:经过酸浸(酸洗)或硫印的方法在连铸坯横断面或纵断面上用肉眼或低倍放大镜看到内部组织结果。
硫印硫印是用感光相纸显示试样上硫偏析(合金中各组成元素在结晶时分布不均匀的现象称为偏析)的方法,主要用于钢铁行业铸坯质量的检验。
从铸坯上取纵向或横向试样,试验面加工的光洁度不应低于6。
使用反差大的溴化银表面相纸,把与试样大小相同的相纸放入稀硫酸中浸泡1-2分钟后取出,将相纸对准检查面轻轻覆盖好,将试样与相纸间气泡赶净,待接触2-5分钟后取下,将相纸在流水中冲洗,然后定影烘干,即完成一张硫印。
印基本原理:硫酸与试样上的硫化物(FeS、MnS)发生反应,生成硫化氢气体,硫化氢气体再与感光相纸上的溴化银作用,生成硫化银沉淀在相纸相应的位置上,形成黑色或褐色斑点。
用硫印试验,可显示钢锭、连铸坯中心裂纹、偏析线、低倍结构和夹杂分布等。
酸洗用酸液洗去基体表面锈蚀物和轧皮的过程。
用酸浸或硫印法所显示的组织结构属于宏观结构,是连铸坯和金属材料检验中最为常见的检验技术。
连铸坯的内部结构连铸坯自表面至中心都是由边缘等轴晶区(激冷区)、柱状晶区和中心等轴晶,区三部分组成。
温度梯度较大时,固液两相区(图1)小,有利于柱状晶的生长,而凝固速度较快,则易于生成枝晶间距小的铸造组织,所以连铸坯具有较发达的柱状晶组织,并具有较小的枝晶间距。
(图1)枝晶间距是指相邻同次枝晶间的垂直距离,它是树枝晶组织细化程度的表征。
枝晶间距越小,组织就越细密,分布于其间的元素偏析范围也就越小,故越容易通过热处理而均匀化。
通常采用的有一次枝晶(柱状晶主干)间距d1,和二次分枝间距d2两种。
连铸坯宏观组织的好坏可以用等轴晶所占的比例多少来衡量,轴晶结构致密,加工性能能好。
柱状晶具有明显的方向性,加工性能差,容易导致中心偏析,中心疏松和中心裂纹等缺陷。
连铸坯、钢板检验规定
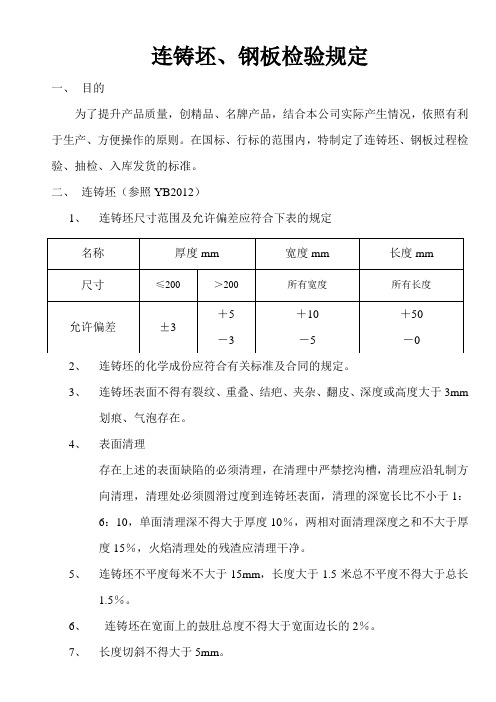
连铸坯、钢板检验规定一、目的为了提升产品质量,创精品、名牌产品,结合本公司实际产生情况,依照有利于生产、方便操作的原则。
在国标、行标的范围内,特制定了连铸坯、钢板过程检验、抽检、入库发货的标准。
二、连铸坯(参照YB2012)1、连铸坯尺寸范围及允许偏差应符合下表的规定2、连铸坯的化学成份应符合有关标准及合同的规定。
3、连铸坯表面不得有裂纹、重叠、结疤、夹杂、翻皮、深度或高度大于3mm划痕、气泡存在。
4、表面清理存在上述的表面缺陷的必须清理,在清理中严禁挖沟槽,清理应沿轧制方向清理,清理处必须圆滑过度到连铸坯表面,清理的深宽长比不小于1:6:10,单面清理深不得大于厚度10%,两相对面清理深度之和不大于厚度15%,火焰清理处的残渣应清理干净。
5、连铸坯不平度每米不大于15mm,长度大于1.5米总不平度不得大于总长1.5%。
6、连铸坯在宽面上的鼓肚总度不得大于宽面边长的2%。
7、长度切斜不得大于5mm。
8、测量位置厚度---以距侧边及端面部位约100-200mm处卡量。
宽度---在长度方向中部测量为准长度---连铸坯长度的最短距离处测量为准三、钢板(参照GB709)1、钢板尺寸范围及允许偏差应符合下表的规定宽度公差钢板的长度允许偏差注:厚度公差见附后表A四切边钢板:对角线按5-15mm验收,单边长度按0-8mm验收。
四毛边钢板:在宽度方向上单边距板边40mm不保性能,小缺陷不于修磨,长度距板头150mm内不保性能及不于修磨表面缺陷。
两头切钢板:单边长度按0-8mm验收,两端头凸凹小于150mm不于切头,大于150mm需切头。
2、表面不得有裂纹、重叠、结疤、夹杂、气泡、拉裂、氧化铁皮压入等缺陷存在。
3、钢板的化学成份应符合有关标准及合同的规定。
4、表面清理存在上述的表面缺陷应进行修磨,在清理中严禁挖沟槽,修磨应光滑过渡到钢板表面,清理深宽长比不小于1:6:10。
5、对于锅炉、压力容器、船体结构用的钢板和合同中规定的特殊用途的钢板,缺陷下面钢板的厚度应不小于相应钢板产品标准中规定的最小允许厚度。
圆管坯检验质量标准
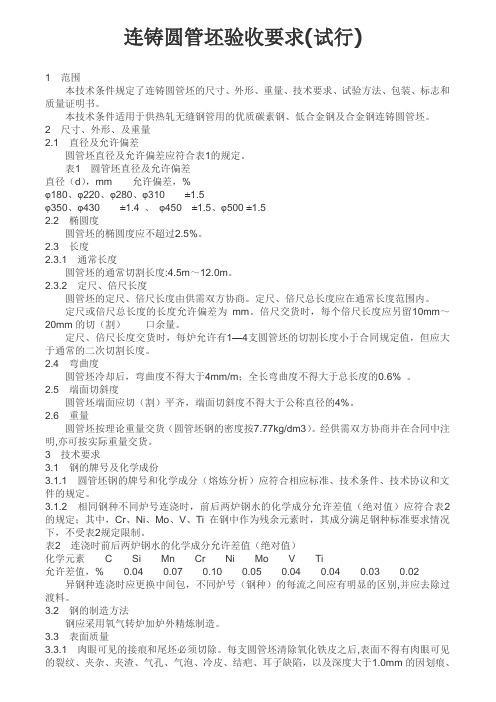
连铸圆管坯验收要求(试行)1 范围本技术条件规定了连铸圆管坯的尺寸、外形、重量、技术要求、试验方法、包装、标志和质量证明书。
本技术条件适用于供热轧无缝钢管用的优质碳素钢、低合金钢及合金钢连铸圆管坯。
2 尺寸、外形、及重量2.1 直径及允许偏差圆管坯直径及允许偏差应符合表1的规定。
表1 圆管坯直径及允许偏差直径(d),mm 允许偏差,%φ180、φ220、φ280、φ310 ±1.5φ350、φ430 ±1.4 、φ450 ±1.5、φ500 ±1.52.2 椭圆度圆管坯的椭圆度应不超过2.5%。
2.3 长度2.3.1 通常长度圆管坯的通常切割长度:4.5m~12.0m。
2.3.2 定尺、倍尺长度圆管坯的定尺、倍尺长度由供需双方协商。
定尺、倍尺总长度应在通常长度范围内。
定尺或倍尺总长度的长度允许偏差为mm。
倍尺交货时,每个倍尺长度应另留10mm~20mm的切(割)口余量。
定尺、倍尺长度交货时,每炉允许有1—4支圆管坯的切割长度小于合同规定值,但应大于通常的二次切割长度。
2.4 弯曲度圆管坯冷却后,弯曲度不得大于4mm/m;全长弯曲度不得大于总长度的0.6% 。
2.5 端面切斜度圆管坯端面应切(割)平齐,端面切斜度不得大于公称直径的4%。
2.6 重量圆管坯按理论重量交货(圆管坯钢的密度按7.77kg/dm3)。
经供需双方协商并在合同中注明,亦可按实际重量交货。
3 技术要求3.1 钢的牌号及化学成份3.1.1 圆管坯钢的牌号和化学成分(熔炼分析)应符合相应标准、技术条件、技术协议和文件的规定。
3.1.2 相同钢种不同炉号连浇时,前后两炉钢水的化学成分允许差值(绝对值)应符合表2的规定;其中,Cr、Ni、Mo、V、Ti在钢中作为残余元素时,其成分满足钢种标准要求情况下,不受表2规定限制。
表2 连浇时前后两炉钢水的化学成分允许差值(绝对值)化学元素 C Si Mn Cr Ni Mo V Ti允许差值,% 0.04 0.07 0.10 0.05 0.04 0.04 0.03 0.02 异钢种连浇时应更换中间包,不同炉号(钢种)的每流之间应有明显的区别,并应去除过渡料。
连铸圆坯工艺规程

大方圆坯连铸技术工艺规程1 连铸钢水要求连铸钢水必须经炉外精炼,保证脱氧充分,成分、温度均匀,符合连铸要求。
1.1 液相线温度的确定钢水液相线温度按照下式计算:TL=1536℃-[78×C%+7.6×Si%+4.9×Mn%+34×(P+S)%+5×Al%+1.5%×Cr%+2.0×Mo%+2.0×V%+18.0×Ti%+4.0×Ca%+5.0×Cu%]其中:C%——为钢种中碳的百分含量Si%——为钢种中硅的百分含量Mn%——为钢种中锰的百分含量(P+S)%——为钢种中的硫和磷的百分含量Al%——为钢种中铝的百分含量1536℃——为纯铁的液相线温度,TL——为钢种液相线温度1.2 连铸钢水温度要求钢包钢水温度必须控制在连铸要求的范围内,即:a.低碳钢:TL+(70~80)℃(第一炉)b.中碳钢:TL+(65~75)℃(第一炉)c.高碳钢:TL+(55~65)℃(第一炉)d.三流浇注、零次罐+5:℃e.浇注小断面:+5℃第二炉及以后各炉均比第一炉低10~20℃2 中间包准备2.1 中间包修砌2.1.1 绝热层砌砖A.砖与座砖模子应留出120mm的间距。
B.不得使用有裂纹、受潮变质及严重残缺的砖。
C.砖缝≯2mm,并保证砌缝灰浆饱满。
D.砌筑用高温火泥搅拌均匀、稠度合适。
2.1.2 中间包永久层浇注A.投入搅拌机的搅拌量不应超过搅拌机定量的50%。
B.干料加入搅拌机内,应干混1-2分钟,按重量比加入8-10%的水,继续搅拌2-3分钟,混匀即可出料。
C.搅拌好的料应尽快使用,以在15分钟内用完为宜。
D.浇注时应用边加料边振动的连续施工法,一次加料不宜超过300mm高。
E.包底浇注高度距包底钢板180mm。
F.振动以泥料充分泛浆无大的气泡冒出为宜,从料中取出振动棒时,不宜过快,防止造成空洞。
G.浇注完中间包底养生2小时后方可支模板,模板与绝热层间距为123mm。
钢锭连铸坯验收标准

钢锭连铸坯验收标准
1、连铸坯的化学成份应符合有关标准的规定;
2、尺寸允许偏差;
尺寸130×130、200×200、φ130、φ200边长允许偏差(mm)±4.0±6.0 对角线长度之差(mm)≤6.0≤9.0 允许偏差(mm)±3.0±4.0椭圆度(mm)不大于直径公差的0.75倍;
3、外形:
3.1、方坯弯曲度每米不大于20 mm,总弯曲度不大于总长度的1.5%;
3.2、圆坯弯曲度每米不大于15 mm,总弯曲度不大于总长度的1.0%;
3.3不得有明显的扭转,端部切斜不得大于10 mm;
4、表面质量□不得有肉眼可见的裂纹、重叠、结疤、夹渣、夹杂、气孔、深度(高度)大于3mm的滑痕、划伤、皱纹、凸块。
如有上述缺陷存在则必须清除,清除深、宽、长比不得小于1:6:8;
5、保证连铸坯的质量,头坯、尾坯的切除量规定如下:
头坯:不得少于700mm;
尾坯:不得少于1000 mm 如头坯切除量达不到上述要求,则判第一条坯为利用品;
尾坯切除量达不到上述要求,则判最后一条坯为利用品;
6、班组质量员对连铸坯进行逐支检查,写上炉号和钢号,注明利用品,按炉做好原始记录;
7、质检部质检员每天对表面质量进行检查,合格品盖上“检”字章,做好抽查记录。
铸坯质量相关问题

铸坯质量相关问题铸坯质量标准如下:1、边长允许偏差±5.0 mm。
2、对角线之差±14.0 mm。
3、连铸坯的弯曲度每米不得大于20 mm,总弯曲度不得大于总长度的2%。
4、连铸坯允许鼓肚,但高度不得超过连铸坯边长的允许正偏差(5 mm)。
5、连铸坯端部切斜不得大于20 mm。
6、连铸坯不得有明显的扭转。
7、连铸坯表面不得有肉眼可见的裂纹、重接、翻皮、结疤、夹杂、深度或高度大于3 mm的划痕、压痕、擦伤、气孔,皱纹、冷溅、耳子、凹坑和深度大于2 mm的发纹。
连铸坯横截面不得有缩孔、皮下气泡。
铸坯质量分析:(一)、脱方1、缺陷特征:横截面上两个对角线超标,常伴随有角部横裂和内部裂纹的产生。
2、影响:在加热炉内造成堆钢,在轧制时产生折叠或扭转;铸坯因脱方而伴随角部内裂,易在轧制时产生裂边缺陷。
3、产生原因:(1)一冷、二冷冷却不均匀;(2)结晶器铜管尺寸不合适,铜管变形,磨损严重;(3)连铸机对弧不准;(4)结晶器振动不平稳。
4、预防及消除办法(1)保证结晶器水缝均匀;(2)保证一冷水水质,防止结垢;(3)保证结晶器铜管尺寸,及时更换结晶器铜管;(4)保证二冷段喷嘴对中,切喷嘴无堵塞;(5)对弧精度符合工艺要求;(6)调整好振动参数,使结晶器振动平稳,无偏振现象。
(二)、中心线裂纹1、缺陷特征:铸坯中心线有裂纹,类似方坯的中心疏松,中心线周围有严重的疏松、偏析和夹杂物。
2、影响及危害:在轧制无法焊合,在钢材上成为缩孔残余或分层。
3、产生原因:钢液在冷却和结晶过程中体积收缩时填充不足所致。
具体原因如下:(1)铸坯在冷却的过程中冷却强度不够;(2)拉速过快;(3)浇注温度过高;(4)扇形段辊间距不合适。
4、预防和消除办法:(1)增大比水量,延长冷却段;(2)控制拉速;(3)降低钢水过热度;(4)合理的配水制度;(5)调整合适的辊间距,避免鼓肚。
(三)、切割断面不齐1、缺陷特征:切割断面粗糙,凹凸不平。
连铸板坯BQB131-2003

-
SS540
G
≤6
0.12~0.21 ≤0.25 0.90~1.40 ≤0.035 ≤0.035
-
一 St33 般 St37-2 结 St37-2 构 St37-2 钢 St37-2
St37-3 St37-3 St37-3 St37-3 St37-3 St44-2 St44-2 St50-2
A
≤13 0.03~0.12 ≤0.08 0.15~0.65 ≤0.035 ≤0.035 Alt≥0.01
-
St52-3 St52-3 St52-3
G
<7
0.13~0.22 0.20~0.55 1.20~1.70 ≤0.035 ≤0.035 Alt≥0.01
G
7~<18 0.13~0.22 0.20~0.55 1.10~1.60 ≤0.035 ≤0.035 Alt≥0.01
G 18~25.4 0.13~0.22 0.20~0.55 1.10~1.60 ≤0.030 ≤0.030 Nb≤0.04
SM520B
G
1.4~9 0.12~0.21 ≤0.25 0.90~1.40 ≤0.035 ≤0.035 Nb≤0.04
SM520B
G
>9~12 0.06~0.15 0.20~0.60 1.10~1.60 ≤0.035 ≤0.035 Nb≤0.04
SM520C
G
1.6~6 0.12~0.21 ≤0.25 0.85~1.35 ≤0.035 ≤0.035 Nb≤0.04
A >6~12.7 0.06~0.15 ≤0.05 0.45~0.95 ≤0.035 ≤0.035 Alt≥0.008
G
≤6
0.12~0.21 0.04~0.30 0.20~0.70 ≤0.035 ≤0.035
- 1、下载文档前请自行甄别文档内容的完整性,平台不提供额外的编辑、内容补充、找答案等附加服务。
- 2、"仅部分预览"的文档,不可在线预览部分如存在完整性等问题,可反馈申请退款(可完整预览的文档不适用该条件!)。
- 3、如文档侵犯您的权益,请联系客服反馈,我们会尽快为您处理(人工客服工作时间:9:00-18:30)。
轧钢用水平连铸圆坯标准
QJ/HYXC03.01—2002
1 范围
本标准规定了轧钢用水平连铸圆坯(以下简称圆棒)的尺寸、外形、重量及允许偏差、技术要求、试验方法、检验规则、包装、标志及质量证明书。
本标准是我公司购水平连铸圆坯签订合同和对圆坯检查、验收、使用的依据。
2 引用标准
下列标准所包含的条文,通过在本标准中引用而构成本标准的条文。
GB700 普通碳素钢;
GB1591 低合金结构钢;
GB1222 弹簧钢;
GB222 钢的化学分析用试验取样法及成品化学成分允许偏差;
GB223 钢铁及合金化学分析法;
GB2101 型钢验收、包装标专及质量证明书的一般规定。
3 术语
热点裂纹:由于铸坯热收缩,集中发生在凝固壳最薄弱的热点处而引起的与冷隔平行的一种横裂纹。
4 尺寸、外形、重量及允许偏差
4.1 直径及允许偏差和外形
圆棒的直径及允许偏差和外形应符合附表1规定
4.2 长度及允许偏差
圆棒通常定尺长度为6m±mm,非定尺长度应是1.5m的倍数,即3.0m、4.5m,但总量不超过10%。
4.3 重量
圆棒按实际重量交货。
5 技术要求
5.1 牌号及化学成分
5.1.1 牌号及化学成分应符合附表2规定。
5.1.2 圆棒的化学成分允许偏差应符合GB222的标准。
5.2 冶炼方法
电弧炉冶炼。
5.3 交货状态
圆棒以铸态交货。
5.4 表面质量
5.4.1 圆棒表面不应有肉眼可见的结疤、纵裂纹、夹渣及深度超过3mm的气孔等缺陷。
圆棒端面不应有肉眼可见的缩孔。
允许有从实际尺寸算起不超过2mm的划痕、压痕及折皱存在,允许有深度不大于1mm的热点裂纹及冷隔存在。
5.4.2 圆棒表面缺陷应清除,清除深度从实际尺寸算起不应大于直径的5%,清理处应圆滑无棱角,清理宽度不应小于深度的6倍,在同一截面最大清理深度只准有一处。
6 试验方法
圆棒的试验方法、取样部位及数量应符合附表3的规定。
7 检验规则
7.1 检查和验收
圆棒的化学成分由供方提供。
圆棒的尺寸和表面质量由技术质量部负责检查验收。
7.2 炉号划分
圆棒的上下相邻炉号划分方法:以盛钢桶钢水注入中间包时起,即做为下一炉的开始。
7.3 组坯规则
圆棒应按批进行检查和验收,每批由同一牌号、同一炉号的圆棒组成。
8 包装、标志及质量证明书
8.1 包装
每批圆棒可分为若干捆包装,通常每捆10—15支(重量不应超过10吨),用盘条或铁丝均匀捆扎结实。
8.2 标志
每捆圆棒应附有标志,写明牌号、炉号、规格、数量及重量。
8.3 质量证明书
圆棒的质量证明书应符合GB2101的规定。
9 本标准由魏克冲起草,。
10 本标准自2002年10月1日起生效。