玻璃常见缺陷
玻璃热弯缺陷
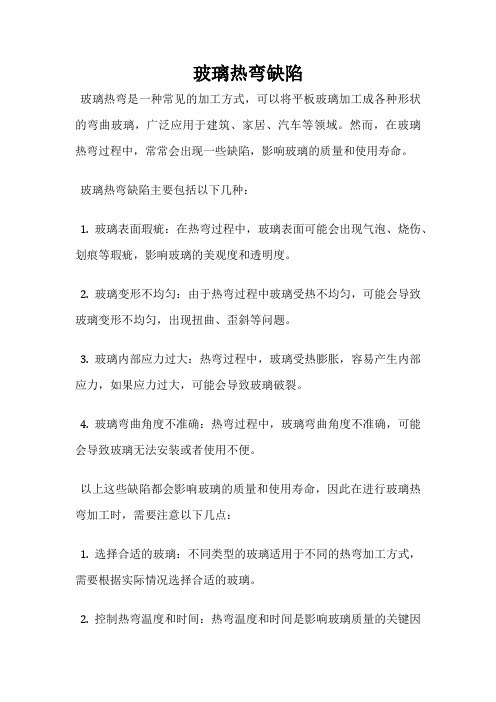
玻璃热弯缺陷
玻璃热弯是一种常见的加工方式,可以将平板玻璃加工成各种形状的弯曲玻璃,广泛应用于建筑、家居、汽车等领域。
然而,在玻璃热弯过程中,常常会出现一些缺陷,影响玻璃的质量和使用寿命。
玻璃热弯缺陷主要包括以下几种:
1. 玻璃表面瑕疵:在热弯过程中,玻璃表面可能会出现气泡、烧伤、划痕等瑕疵,影响玻璃的美观度和透明度。
2. 玻璃变形不均匀:由于热弯过程中玻璃受热不均匀,可能会导致玻璃变形不均匀,出现扭曲、歪斜等问题。
3. 玻璃内部应力过大:热弯过程中,玻璃受热膨胀,容易产生内部应力,如果应力过大,可能会导致玻璃破裂。
4. 玻璃弯曲角度不准确:热弯过程中,玻璃弯曲角度不准确,可能会导致玻璃无法安装或者使用不便。
以上这些缺陷都会影响玻璃的质量和使用寿命,因此在进行玻璃热弯加工时,需要注意以下几点:
1. 选择合适的玻璃:不同类型的玻璃适用于不同的热弯加工方式,需要根据实际情况选择合适的玻璃。
2. 控制热弯温度和时间:热弯温度和时间是影响玻璃质量的关键因
素,需要根据实际情况进行合理控制。
3. 采用先进的热弯设备:先进的热弯设备可以提高热弯加工的精度和效率,减少缺陷的出现。
4. 进行质量检测:热弯加工完成后,需要进行质量检测,及时发现和处理缺陷,确保玻璃的质量和使用寿命。
玻璃热弯缺陷是影响玻璃质量和使用寿命的重要因素,需要在热弯加工过程中注意控制,采取有效的措施减少缺陷的出现。
钢化玻璃常见的缺陷产生原因
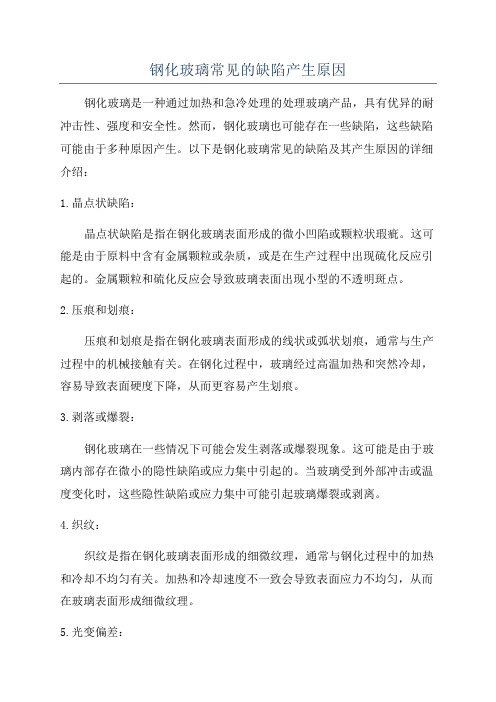
钢化玻璃常见的缺陷产生原因
钢化玻璃是一种通过加热和急冷处理的处理玻璃产品,具有优异的耐冲击性、强度和安全性。
然而,钢化玻璃也可能存在一些缺陷,这些缺陷可能由于多种原因产生。
以下是钢化玻璃常见的缺陷及其产生原因的详细介绍:
1.晶点状缺陷:
晶点状缺陷是指在钢化玻璃表面形成的微小凹陷或颗粒状瑕疵。
这可能是由于原料中含有金属颗粒或杂质,或是在生产过程中出现硫化反应引起的。
金属颗粒和硫化反应会导致玻璃表面出现小型的不透明斑点。
2.压痕和划痕:
压痕和划痕是指在钢化玻璃表面形成的线状或弧状划痕,通常与生产过程中的机械接触有关。
在钢化过程中,玻璃经过高温加热和突然冷却,容易导致表面硬度下降,从而更容易产生划痕。
3.剥落或爆裂:
钢化玻璃在一些情况下可能会发生剥落或爆裂现象。
这可能是由于玻璃内部存在微小的隐性缺陷或应力集中引起的。
当玻璃受到外部冲击或温度变化时,这些隐性缺陷或应力集中可能引起玻璃爆裂或剥离。
4.织纹:
织纹是指在钢化玻璃表面形成的细微纹理,通常与钢化过程中的加热和冷却不均匀有关。
加热和冷却速度不一致会导致表面应力不均匀,从而在玻璃表面形成细微纹理。
5.光变偏差:
光变偏差是指钢化玻璃在一些情况下可能会导致光线透射的颜色和变形。
这可能是由于原料中的金属杂质或生产过程中的一些物质残留导致的。
玻璃缺陷检测

玻璃片缺陷视觉检测1.玻璃缺陷特征玻璃片生产过程中,常见的缺陷有:气泡、划痕、结石、夹杂物,翘曲等。
各类缺陷的主要特点分:(1)气泡,该类缺陷是由于玻璃生产材料含有气体、外界环境气泡、金属铁丝等引起,主要特点为整体轮廓近似于圆形、线形、中空、具有光透射性等。
(2)结石,由于其热胀系数和外界环境热胀系数的差异,该类缺陷严重影响玻璃质量。
主要分为:原材料结石、耐火材料结石以及玻璃析晶结石等。
(3)夹锡,夹锡主要分为粘锡和锡结石,其特点是呈暗黑色、具有光吸收性。
(4)划伤,该缺陷主要是玻璃原板与硬质介质间的相互摩擦产生,外表呈线性。
(5)表面裂纹及线道,其特点表面呈线性。
具体的缺陷图如图1-1所示:(a)无缺陷玻璃图像(b)含气泡玻璃图像(c)含结石玻璃图像(d)含裂纹玻璃图像(e)含夹杂物的玻璃图像(f)划痕的玻璃图像图 1-1 玻璃典型缺陷图像2玻璃缺陷视觉监测系统工作原理2.1 玻璃缺陷视觉检测原理玻璃生产过程大体可分为:原料加工、备制配合料、熔化和澄清、冷却和成型及切裁等。
在各生产过程中,由于制造工艺、人为等因素,在玻璃原板的生产任一过程中都有可能产生缺陷,根据玻璃现行标准中的规定,玻璃常见的缺陷主要包括:气泡、粘锡、划伤、夹杂等。
无缺陷的玻璃其特点是质地均匀、表面光洁且透明。
玻璃质量缺陷检测是采用先进的CCD 成像技术和智能光源。
系统照明采用背光式照明,其原理如图2-1所示,即在玻璃的背面放置光源,光线经待检玻璃,透射进入摄像头[1]。
图 2-1 检测原理图示意图光线垂直入射玻璃后,当玻璃中没有杂质时如图2-2(a)所示,出射的方向不会发生改变,CCD 摄像机的靶面探测到的光也是均匀的;当玻璃中含有杂质时,出射的光线会发生变化,CCD 摄像机的靶面探测到的光也要随之改变。
玻璃中含有的缺陷主要分为两种:一是光吸收型(如沙粒,夹锡等夹杂物)如图2-2(b)所示,光透射玻璃时,该缺陷位置的光会变弱,CCD 摄像机的靶面上探测到的光比周围的光要弱;二是光透射型(如裂纹,气泡等)如图2-2(c)所示,光线在该缺陷位置发生了折射,光的强度比周围的要大,因而CCD 摄像机的靶面上探测到的光也相应增强。
玻璃瓶成形最为常见的八大缺陷

我们总结玻璃瓶成形最为常见的八大缺陷如下:
(1)裂纹
裂纹是玻璃瓶最普遍的缺点。
它可能非常细,有些只有在反射光中才能发现。
经常产生的部位是瓶口、瓶颈和肩部,瓶身和瓶底部也常有裂纹产生。
(2)厚薄不匀
这是指玻璃瓶上的玻璃分布不均匀。
主要是玻璃料滴温度不均匀,温度高的部分黏度小,容易吹薄;温度低的部分阻力大,较厚。
模型温度不均匀,温度高的一边玻璃冷却慢,容易吹薄,温度低的一边,因玻璃冷却快而吹厚。
(3)变形
料滴温度和作用温度过高,由成形模脱出的瓶子尚未完全定形,往往会下塌变形。
有时瓶的底部尚软会印上输送带的纹痕而使瓶底不平。
(4)不饱满
料滴温度过低或模型过冷会使口部、肩部等处吹不饱满,产生缺口、瘪肩和花纹不清晰等缺陷。
(5)冷斑
玻璃表面上不平滑的斑块称为冷斑。
这种缺陷的产生原因主要是模型温度过冷,多在开始生产或停机再生产时发生。
(6)突出物
玻璃瓶合缝线突出或口部边缘向外凸出的缺陷。
这是由于模型部件制造不够正确或安装不够吻合而产生的。
模型损坏、合缝面上有污物、顶芯提起太晚未进入位置前玻璃料已落入初形模中,就会使一部分玻璃从隙缝中压出或吹出。
(7)皱纹
皱纹有各种形状,有的是折痕,有的是成片的很细的皱纹。
皱纹产生的原因主要是由于料滴过冷,料滴过长,料滴未落在初形模中间而粘连在模腔壁上而产生的。
(8)表面缺点
瓶罐的表面发毛、不平,主要是由于模腔表不光滑而造成的。
模型的润滑油不清洁或涂油的刷子过脏,也会使瓶罐表面质量下降。
玻璃缺陷检测

玻璃片缺陷视觉检测1.玻璃缺陷特征玻璃片生产过程中,常见的缺陷有:气泡、划痕、结石、夹杂物,翘曲等。
各类缺陷的主要特点分:(1)气泡,该类缺陷是由于玻璃生产材料含有气体、外界环境气泡、金属铁丝等引起,主要特点为整体轮廓近似于圆形、线形、中空、具有光透射性等。
(2)结石,由于其热胀系数和外界环境热胀系数的差异,该类缺陷严重影响玻璃质量。
主要分为:原材料结石、耐火材料结石以及玻璃析晶结石等。
(3)夹锡,夹锡主要分为粘锡和锡结石,其特点是呈暗黑色、具有光吸收性。
(4)划伤,该缺陷主要是玻璃原板与硬质介质间的相互摩擦产生,外表呈线性。
(5)表面裂纹及线道,其特点表面呈线性。
具体的缺陷图如图1-1所示:(a)无缺陷玻璃图像(b)含气泡玻璃图像(c)含结石玻璃图像(d)含裂纹玻璃图像(e)含夹杂物的玻璃图像(f)划痕的玻璃图像图 1-1 玻璃典型缺陷图像2玻璃缺陷视觉监测系统工作原理2.1 玻璃缺陷视觉检测原理玻璃生产过程大体可分为:原料加工、备制配合料、熔化和澄清、冷却和成型及切裁等。
在各生产过程中,由于制造工艺、人为等因素,在玻璃原板的生产任一过程中都有可能产生缺陷,根据玻璃现行标准中的规定,玻璃常见的缺陷主要包括:气泡、粘锡、划伤、夹杂等。
无缺陷的玻璃其特点是质地均匀、表面光洁且透明。
玻璃质量缺陷检测是采用先进的CCD 成像技术和智能光源。
系统照明采用背光式照明,其原理如图2-1所示,即在玻璃的背面放置光源,光线经待检玻璃,透射进入摄像头[1]。
图 2-1 检测原理图示意图光线垂直入射玻璃后,当玻璃中没有杂质时如图2-2(a)所示,出射的方向不会发生改变,CCD 摄像机的靶面探测到的光也是均匀的;当玻璃中含有杂质时,出射的光线会发生变化,CCD 摄像机的靶面探测到的光也要随之改变。
玻璃中含有的缺陷主要分为两种:一是光吸收型(如沙粒,夹锡等夹杂物)如图2-2(b)所示,光透射玻璃时,该缺陷位置的光会变弱,CCD 摄像机的靶面上探测到的光比周围的光要弱;二是光透射型(如裂纹,气泡等)如图2-2(c)所示,光线在该缺陷位置发生了折射,光的强度比周围的要大,因而CCD 摄像机的靶面上探测到的光也相应增强。
玻璃常见缺陷
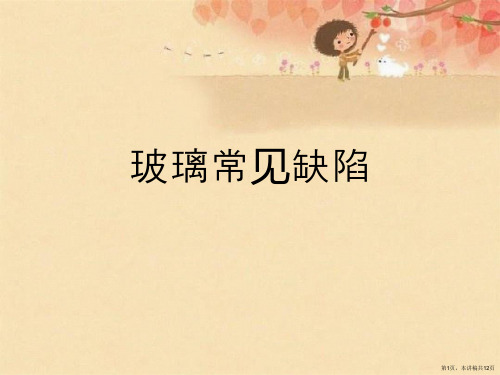
玻璃常见缺陷
第1页,本讲稿共12页
从原料加工、配合料的制备、熔化、玻 璃液的澄清、玻璃液的均化、玻璃液的冷却、 成型及切裁等各生产过程中,工艺制度的破坏 或制作过程的差错,都会在平板玻璃原料上表 现为各种不同的缺陷。平板玻璃的缺陷使玻璃 质量大大降低,甚至严重影响玻璃的进一步成 型和加工,或者造成大量的废品。
第3页,本讲稿共12页
缺陷分类
11 气气泡泡(气体夹杂物) 22 析析晶晶与与结结石(石固(体固夹杂体物夹)杂物) 33 条条纹纹和和节节瘤(瘤玻(璃玻态夹璃杂态物夹)杂物) 44 光光学学变变形形(析(斑锡)斑) 55 划划伤伤((磨磨伤)伤)
第4页,本讲稿共12页
玻璃中的气泡是可见的气体夹杂物,不仅影响玻璃 制品的外观质量,更影响玻璃的透明性和机械强度。
根据气泡产生的原因不同,可以分成:一次气泡 ,二次气泡,外界空气气泡,耐火材料气泡和金属 铁引起的气泡等多种。
解决办法:大气泡逸出,小气泡溶解。
第5页,本讲稿共12页
第6页,本讲稿共12页
结石是出现在玻璃体中的结晶状固体夹杂 物,是玻璃体内最危险的缺陷,是使玻璃出 现开裂损坏的主要因素。
主要产生原因是原料中含硅质大颗 粒或者长石大颗粒未完全熔化造成的。 应严格控制原料粒度范围。还可能是耐 火材料受到侵蚀,产生剥落物造成。
第2页,本讲稿共12页
平板玻璃缺陷种类和它产生的原因是多种多样的 。根据缺陷存在于玻璃的内部和外部,分为内在缺 陷和外观缺陷。不同种类的的缺陷,其研究方法也 不同,当玻璃中出现某种缺陷时往往需要通过很多 方法研究解决,才能做出判断。
液晶玻璃清洗常见缺陷及处理办法

液晶玻璃清洗缺陷及处理办法1.摩擦痕迹(滚轮印)1.1 产生原因:由于与玻璃直接接触“O”型圈造成直线性摩擦痕迹。
对策方法:定期对O型圈等与玻璃接触部件进行检查、维护,湿润洁净布擦拭O 型圈,严重的要及时更换。
1.2 产生原因:由于盘刷对玻璃压力过大或者盘刷安装水平不够,玻璃在盘刷单元非流向型位移造成的摩擦痕迹。
对策方法:每次更换盘刷后调整好盘刷水平,并跑一些调机品检查盘刷清洗效果。
2.破片2.1 产生原因:玻璃在生产线上由于人为操作或者设备问题可能造成玻璃碎裂,破片。
对策方法:立即停机,清理碎屑;否则将会产生一系连缺陷,对生产产生严重影响。
2.2 产生原因:清洗机碎片、玻璃基板断裂:研磨工序产生的掉片或者裂纹在清洗机内部由于压力原因导致玻璃基板破碎和断裂,如图所示。
对策方法:通知上一工序调整生产工艺对策掉片;2.3 产生原因:盘刷和滚刷压入量过大导致破片对策方法:适当减少压入量;2.4产生原因:上下压轮错位,玻璃基板受力不均导致破碎,如图所示对策方法:调整压轮位置,使上下压轮位置一致;3.擦伤、划伤3.1 旋转类:在玻璃基板表面呈圆弧状分布的擦、划伤;产生原因:可能是盘刷或者吸盘造成的;重的要及时更换;3.2 呈直线型或者等距离分布的产生原因:对应位置滚轮或者对应位置的气浮边缘位置擦划到玻璃;对策方法:首先确定是流向型还是非流向型如果是流向型,可能是清洗产生,非流向型则基本确定非清洗产生,然后根据检查工序提供的坐标位置对策;3.3表面大面积出现擦划伤;产生原因:大面积接触玻璃表面造成的对策方法:要尽量避免非传动过程中其他物体接触玻璃;3.4非规律类:产生原因:人为可能性大;对策方法:严禁人员不戴手套搬运玻璃;在搬运过程中严禁碰撞其他物体,轻拿轻放;3.5呈点状分布的:产生原因:碎屑引起的;或者滚刷引起;对策方法:碎片后要及时清理,清理过程中要仔细,不得有碎屑残留;用水枪对转动的滚刷侧面进行冲洗,吃水深度2-3mm;4 水痕产生原因:由于风刀干燥的气压或流量不够,不能将玻璃表面水彻底干燥,或风刀加热器温度低,或者风刀角度不合适;造成残余水珠在玻璃上慢慢蒸发形成水痕。
玻璃常见缺陷

缺陷分类
1 1 2 2
气泡 气泡(气体夹杂物) 析晶与结石(固体夹杂物) 析晶与结石(固体夹杂物) 条纹和节瘤(玻璃态夹杂物) 条纹和节瘤(玻璃态夹杂物) 光学变形(析斑) 光学变形(锡斑) 划伤(磨源自) 划伤(磨伤)3 3 4 4
5 5
玻璃中的气泡是可见的气体夹杂物,不仅影
响玻璃制品的外观质量,更影响玻璃的透明性
辊子擦伤是传动辊子与 玻璃接触时在玻璃表面留下 的由于摩擦引起的表面划伤 缺陷,这种缺陷产生的主要 原因是由于辊子表面有磨伤 或污染等。 解决办法就是及时检修 辊道和清除槽内杂质。
THANK YOU
和机械强度。
根据气泡产生的原因不同,可以分成:一次 气泡,二次气泡,外界空气气泡,耐火材料气 泡和金属铁引起的气泡等多种。 解决办法:大气泡逸出,小气泡溶解。
结石是出现在玻璃体中的结晶状 固体夹杂物,是玻璃体内最危险的缺 陷,是使玻璃出现开裂损坏的主要因 素。 主要产生原因是原料中含硅质大 颗粒或者长石大颗粒未完全熔化造成 的。应严格控制原料粒度范围。还可 能是耐火材料受到侵蚀,产生剥落物 造成。
玻璃体内存在的异类玻璃夹杂物称为玻璃 态夹杂物,属于一种较普遍的玻璃不均匀性方 面的缺陷,在化学组成和物理性质上与玻璃体 不同。 形成原因主要是硅质料、长石料的大颗粒 或超细粉团,在配合料的熔化过程中已熔化但 由于扩散不均而停留在玻璃表面拉引成型后形 成的。主要措施是加强原料的外观检查。
是玻璃表面上的微小凹坑,其形状呈平滑的圆 形,直径0.06-0.1mm,深0.05mm.这种斑点损害了 玻璃光学质量,使观察的的物像发生畸变,称“光 畸变点”。 形成原因主要是有氧化亚锡和硫化亚锡蒸汽 的聚集冷凝。减少光学变形缺陷的办法主要有,减 少氧污染和硫污染。为了防止斑点缺陷的产生,要 经常采用高压保护气体吹扫锡面上的氧化亚锡和硫 化亚锡的冷凝物,以减少光学变形缺陷。
- 1、下载文档前请自行甄别文档内容的完整性,平台不提供额外的编辑、内容补充、找答案等附加服务。
- 2、"仅部分预览"的文档,不可在线预览部分如存在完整性等问题,可反馈申请退款(可完整预览的文档不适用该条件!)。
- 3、如文档侵犯您的权益,请联系客服反馈,我们会尽快为您处理(人工客服工作时间:9:00-18:30)。
第6页/共11页
第7页/共11页
玻璃体内存在的异类玻璃夹杂物称为玻璃 态夹杂物,属于一种较普遍的玻璃不均匀性方 面的缺陷,在化学组成和物理性质上与玻璃体 不同。
第3页/共11页
玻璃中的气泡是可见的气体夹杂物,不仅影 响玻璃制品的外观质量,更影响玻璃的透明性 和机械强度。
根据气泡产生的原因不同,可以分成:一次 气泡,二次气泡,外界空气气泡,耐火材料气 泡和金属铁引起的气泡等多种。
解决办法:大气泡逸出,小气泡溶解。
第4页/共11页
第5页/共11页
结石是出现在玻璃体中的结晶状 固体夹杂物,是玻璃体内最危险的缺 陷,是使玻璃出现开裂损坏的主要因 素。
解决办页
THANK YOU
第11页/共11页
从原料加工、配合料的制备、熔化、玻 璃液的澄清、玻璃液的均化、玻璃液的冷却、 成型及切裁等各生产过程中,工艺制度的破 坏或制作过程的差错,都会在平板玻璃原料 上表现为各种不同的缺陷。平板玻璃的缺陷 使玻璃质量大大降低,甚至严重影响玻璃的 进一步成型和加工,或者造成大量的废品。
第1页/共11页
平板玻璃缺陷种类和它产生的原因是多种 多样的。根据缺陷存在于玻璃的内部和外部, 分为内在缺陷和外观缺陷。不同种类的的缺陷, 其研究方法也不同,当玻璃中出现某种缺陷时 往往需要通过很多方法研究解决,才能做出判 断。
实际上,玻璃的缺陷如同数学误差一样, 是不可能彻底消除和避免的,我们能做的只是 尽量减少操作失误出现的缺陷,以及尽最大努 力将各种缺陷降到最低。
第2页/共11页
缺陷分类
11 气气泡泡(气体夹杂物) 22 析析晶晶与与结结石(石固(体固夹杂体物夹)杂物) 33 条条纹纹和和节节瘤(瘤玻(璃玻态夹璃杂态物夹)杂物) 44 光光学学变变形形(析(斑锡)斑) 55 划划伤伤((磨磨伤)伤)
形成原因主要是硅质料、长石料的大颗粒 或超细粉团,在配合料的熔化过程中已熔化但 由于扩散不均而停留在玻璃表面拉引成型后形 成的。主要措施是加强原料的外观检查。
第8页/共11页
是玻璃表面上的微小凹坑,其形状呈平滑的圆 形,直径0.06-0.1mm,深0.05mm.这种斑点损害了 玻璃光学质量,使观察的的物像发生畸变,称“光 畸变点”。
形成原因主要是有氧化亚锡和硫化亚锡蒸汽 的聚集冷凝。减少光学变形缺陷的办法主要有,减 少氧污染和硫污染。为了防止斑点缺陷的产生,要 经常采用高压保护气体吹扫锡面上的氧化亚锡和硫 化亚锡的冷凝物,以减少光学变形缺陷。
第9页/共11页
辊子擦伤是传动辊子与 玻璃接触时在玻璃表面留下 的由于摩擦引起的表面划伤 缺陷,这种缺陷产生的主要 原因是由于辊子表面有磨伤 或污染等。