工件坐标系的确定
FANUC系统确定工件坐标系方法

FANUC系统确定工件坐标系有三种方法第一种是:通过对刀将刀偏值写入参数从而获得工件坐标系。
这种方法操作简单,可靠性好,他通过刀偏与机械坐标系紧密的联系在一起,只要不断电、不改变刀偏值,工件坐标系就会存在且不会变,即使断电,重启后回参考点,工件坐标系还在原来的位置。
第二种是:用G50设定坐标系,对刀后将刀移动到G50设定的位置才能加工。
对到时先对基准刀,其他刀的刀偏都是相对于基准刀的。
第三种方法是:MDI参数,运用G54~G59可以设定六个坐标系,这种坐标系是相对于参考点不变的,与刀具无关。
这种方法适用于批量生产且工件在卡盘上有固定装夹位置的加工。
航天数控系统的工件坐标系建立是通过G92 Xa zb (类似于FANUC的G50)语句设定刀具当前所在位置的坐标值来确定。
加工前需要先对刀,对到实现对的是基准刀,对刀后将显示坐标清零,对其他刀时将显示的坐标值写入相应刀补参数。
然后测量出对刀直径Фd,将刀移动到坐标显示X=a-d Z=b 的位置,就可以运行程序了(此种方法的编程坐标系原点在工件右端面中心)。
在加工过程中按复位或急停健,可以再回到设定的G92 起点继续加工。
但如果出意外如:X或Z轴无伺服、跟踪出错、断电等情况发生,系统只能重启,重其后设定的工件坐标系将消失,需要重新对刀。
如果是批量生产,加工完一件后回G92起点继续加工下一件,在操作过程中稍有失误,就可能修改工件坐标系,需重新对刀。
鉴于这种情况,我们就想办法将工件坐标系固定在机床上。
我们发现机床的刀补值有16个,可以利用,于是我们试验了几种方法。
第一种方法:在对基准刀时,将显示的参考点偏差值写入9号刀补,将对刀直径的反数写入8号刀补的X值。
系统重启后,将刀具移动到参考点,通过运行一个程序来使刀具回到工件G92起点,程序如下:N001 G92 X0 Z0;N002 G00 T19;N003 G92 X0 Z0;N004 G00 X100 Z100;N005 G00 T18;N006 G92 X100 Z100;N007 M30;程序运行到第四句还正常,运行第五句时,刀具应该向X的负向移动,但却异常的向X、Z 的正向移动,结果失败。
六点法定义工具坐标系的步骤

六点法定义工具坐标系的步骤一、引言在工程领域中,工具坐标系是一种基本的坐标系,用于定义工具或工件在机床上的位置和姿态。
通过建立工具坐标系,可以准确描述机床中工具的位置、方向和姿态,从而实现精确的加工和定位。
本文将介绍以六点法定义工具坐标系的步骤,以帮助读者更好地理解和应用这一方法。
二、确定基准点确定基准点是定义工具坐标系的第一步。
基准点是工具坐标系的原点,通常选择机床上的一个固定点作为基准点。
在选择基准点时,需要考虑其稳定性和易于测量的特点。
三、确定X轴方向确定X轴方向是定义工具坐标系的第二步。
X轴是工具坐标系的一个重要方向,它通常与机床上的一个固定轴线平行。
在确定X轴方向时,可以选择机床上的一个固定轴线,如工作台的移动方向。
四、确定Z轴方向确定Z轴方向是定义工具坐标系的第三步。
Z轴是工具坐标系的另一个重要方向,它垂直于X轴和Y轴。
在确定Z轴方向时,可以选择机床上的一个固定轴线,如主轴的旋转轴线。
五、确定Y轴方向确定Y轴方向是定义工具坐标系的第四步。
Y轴是工具坐标系的剩余方向,它与X轴和Z轴垂直。
在确定Y轴方向时,可以选择机床上的一个固定轴线,如机床的进给方向。
六、确定坐标正负方向确定坐标正负方向是定义工具坐标系的最后一步。
在确定坐标正负方向时,需要考虑工具坐标系与机床坐标系之间的转换关系。
通常情况下,X轴正方向指向机床坐标系的正方向,Y轴正方向与机床坐标系的正方向相同,而Z轴正方向则与机床坐标系的负方向相反。
通过以上六个步骤,就可以完整地定义一个工具坐标系。
在实际应用中,可以通过测量和计算来确定工具坐标系的各个参数,如基准点的坐标和坐标轴的方向。
定义好工具坐标系后,就可以根据需要进行加工和定位,实现精确的工艺要求。
总结通过以上六点法定义工具坐标系的步骤,可以准确地描述工具或工件在机床上的位置和姿态。
这一方法在工程领域中得到广泛应用,对于实现精确的加工和定位非常重要。
在实际应用中,需要仔细选择基准点和确定坐标轴的方向,以确保工具坐标系的准确性和稳定性。
简述abb工业机器人工件坐标系的设定步骤和作用
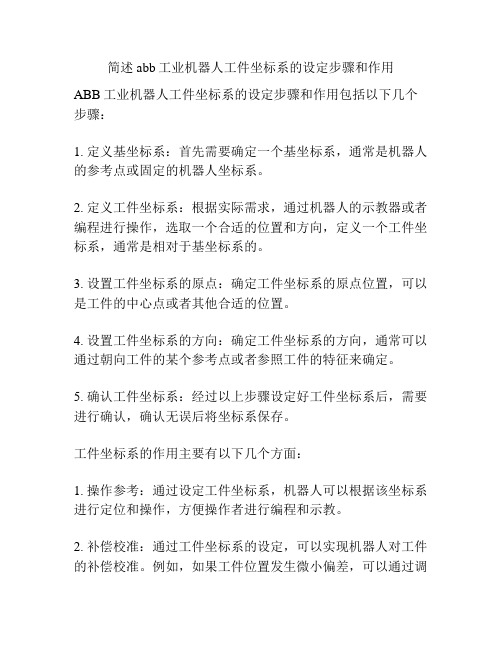
简述abb工业机器人工件坐标系的设定步骤和作用
ABB工业机器人工件坐标系的设定步骤和作用包括以下几个步骤:
1. 定义基坐标系:首先需要确定一个基坐标系,通常是机器人的参考点或固定的机器人坐标系。
2. 定义工件坐标系:根据实际需求,通过机器人的示教器或者编程进行操作,选取一个合适的位置和方向,定义一个工件坐标系,通常是相对于基坐标系的。
3. 设置工件坐标系的原点:确定工件坐标系的原点位置,可以是工件的中心点或者其他合适的位置。
4. 设置工件坐标系的方向:确定工件坐标系的方向,通常可以通过朝向工件的某个参考点或者参照工件的特征来确定。
5. 确认工件坐标系:经过以上步骤设定好工件坐标系后,需要进行确认,确认无误后将坐标系保存。
工件坐标系的作用主要有以下几个方面:
1. 操作参考:通过设定工件坐标系,机器人可以根据该坐标系进行定位和操作,方便操作者进行编程和示教。
2. 补偿校准:通过工件坐标系的设定,可以实现机器人对工件的补偿校准。
例如,如果工件位置发生微小偏差,可以通过调
整工件坐标系来实现对偏差的修正。
3. 工具坐标系的设定:在某些情况下,需要将工具的坐标系与工件坐标系进行关联。
通过设定工件坐标系,可以方便地设定工具的坐标系,以实现更精确的操作。
总的来说,ABB工业机器人工件坐标系的设定步骤和作用可以帮助机器人实现精确的操作和补偿校准,提高工作效率和质量。
建立工件坐标系的步骤

建立工件坐标系的步骤一、确定基准面和基准点:基准面是建立坐标系的参考平面,通常选择工件上便于加工的平面作为基准面。
基准点是基准面上的确定点,用来确定坐标系的位置。
确定基准面和基准点后,可以用辅助工具(如划线底板、平行仪等)将基准点标记在基准面上。
二、确定坐标轴的方向和顺序:坐标轴是建立坐标系的基准线,它决定了工件坐标系的方向。
常用的坐标轴有X轴、Y轴和Z轴。
在确定坐标轴的方向时,需要考虑三个方向上的运动,以便确保机床能够满足加工的要求。
在确定坐标轴的顺序时,一般采用右手定则,即拇指指向X轴的正方向,食指指向Y轴的正方向,中指指向Z轴的正方向。
三、确定坐标轴的起点和单位:坐标轴的起点是确定坐标系原点的位置,通常选择工件上的其中一明显特征点作为坐标轴的起点。
确定起点后,需要确定坐标轴的单位,即每单位长度所代表的数值。
常用的单位有毫米、厘米和英寸等。
四、绘制坐标系图像:在机械加工过程中,必须将工件坐标系的信息传达给机床控制系统,以便于机床按照给定的坐标进行加工。
绘制坐标系图像是传达坐标系信息的一种常用方式。
绘制坐标系图像时,需要将基准面、基准点、坐标轴方向和起点等信息准确地表示出来。
五、校验坐标系的准确性:建立好的工件坐标系需要经过校验,以确保其准确性。
校验的方法有很多种,一般可以通过测量工件上的几何要素(如尺寸、角度、位置等)来验证坐标系的正确性。
如果测量结果与设计要求相符,则可以认为建立的工件坐标系准确无误。
一般来说,建立工件坐标系的步骤可以概括为:确定基准面和基准点,确定坐标轴的方向和顺序,确定坐标轴的起点和单位,绘制坐标系图像,校验坐标系的准确性。
通过按照以上步骤进行操作,可以确保建立的工件坐标系准确无误,以便机床能按照给定的坐标进行准确的加工。
工件坐标系设定
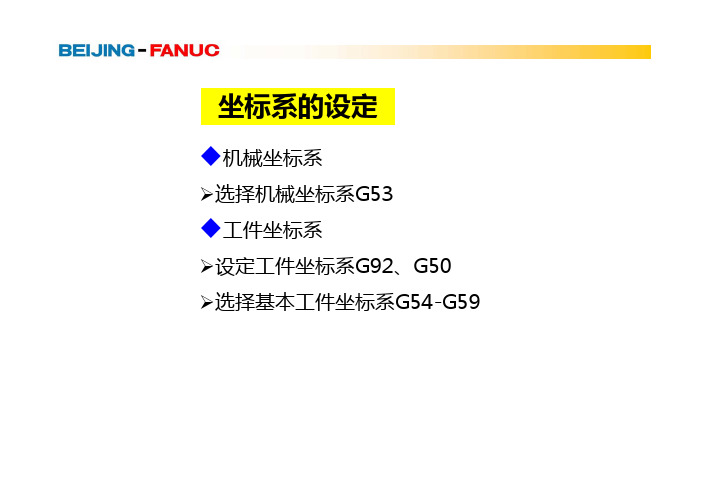
通过改变外部原点偏置量或工件原点偏置量,就可以改变在G54~G59中指定 的6个坐标系位置。 改变外部工件原点偏置量或工件原点偏置量的方法有下列两种: ● 利用MDI 面板的方法 ● 利用程序的方法(使用可编程数据输入G代码或者工件坐标系设定G代码)
G10改变工件坐标系G54~G59
工件坐标系设定的方法(对刀)
偏移量
Z+ 工件原点
常见对刀方法 z试切法 z塞尺、标准棒 z寻边器 z杠杆表
Y+
X+
G54-G59工件坐标系设定界面
外部工
X+
件原点
偏置
MDI 面板分别进行: X0 测量 Y0 测量 Z0 测量
测量工件原 点偏置量
例:O0001;
工件坐标系使用案例
N001 G54; 接通电源时,选择G54 N002 G90G01X0Y0F1000;移动到G54程序原点
N003 G91G00X_Y_;
(加工程序)
N022 G55; 指令G55,刀具不移动 N023 G90G01X0Y0F1000;移动到G55程序原点 N024 G91G00X_Y_;
(加工程序)
N042 G56; 指令G56,刀具不移动 N043 G90G01X0Y0F1000;移动到G56程序原点 N044 G91G00X_Y_;
●把刀具移动到程序原点,把A点设
A
为工件原点时:
G92 X0 Y0 ;
设定工件坐标系(T系列)
设定工件坐标系(T系列)
格式: ห้องสมุดไป่ตู้50 X_ Z_ ;
工件原点设在卡盘的中心:
G50 X128.0 Z375.0(直径指定)
工件原点设定在工件右侧端面上:
工件坐标系的确定

工件坐标系的确定1. 机床坐标系为了保证数控机床的运动、操作及程序编制的一致性,数控标准统一规定了机床坐标系和运动方向,编程时采用统一的标准坐标系。
(1) 坐标系建立的基本原则1) 坐标系采用笛卡儿直角坐标系,右手法则。
如图11-2所示,基本坐标轴为X、Y、Z直角坐标,相应于各坐标轴的旋转坐标分别记为A、B、C。
2) 采用假设工件固定不动,刀具相对工件移动的原则。
由于机床的结构不同,有的是刀具运动,工件固定不动;有的是工件运动,刀具固定不动。
为编程方便,一律规定工件固定,刀具运动。
3) 采用使刀具与工件之间距离增大的方向为该坐标轴的正方向,反之则为负方向。
即取刀具远离工件的方向为正方向。
旋转坐标轴A、B、C的正方向确定如图11-2所示,按右手螺旋法则确定。
(2) 各坐标轴的确定确定机床坐标轴时,一般先确定Z轴,然后确定X轴和Y轴。
Z轴:一般以传递切削力的主轴定为Z坐标轴,如果机床有一系列主轴,则选尽可能垂直于工件装夹面的主要轴为Z轴。
Z轴的正方向为从工件到刀具夹持的方向。
X轴:为水平的、平行于工件装夹平面的轴。
对于刀具旋转的机床,若Z轴为水平时,由刀具主轴的后端向工件看,X轴正方向指向右方;若Z轴为垂直时,由主轴向立柱看,X轴正方向指向右方。
对无主轴的机床(如刨床),X轴正方向平行于切削方向。
Y轴:垂直于X及Z轴,按右手法则确定其正方向。
(3) 机床坐标系的原点机床坐标系的原点也称机械原点、参考点或零点,这个原点是机床上固有的点,机床一经设计和制造出来,机械原点就已经被确定下来。
机床启动时,通常要进行机动或手动回零,就是回到机械原点。
数控机床的机械原点一般在直线坐标或旋转坐标回到正向的极限位置。
2. 工件坐标系(编程坐标系)图11-3 工件坐标系与机床坐标系的位置关系 工件坐标系是由编程人员在编制程序时用来确定刀具和程序的起点,工件坐标系的原点可由编程人员根据具体情况确定,但坐标轴的方向应与机床坐标系一致,并且与之有确定的尺寸关系。
简述工业机器人工件坐标的标定方法以及工件坐标系的作用

简述工业机器人工件坐标的标定方法以及工件坐标系的作用随着工业机器人在生产领域的应用越来越广泛,工件坐标的准确性和标定成为了至关重要的问题。
工件坐标标定是指确定机器人执行任务时所需的工件坐标与实际工件位置之间的准确关系。
下面我们来详细讨论一下工业机器人工件坐标的标定方法以及工件坐标系的作用。
工业机器人工件坐标的标定方法:1. 基础标定法:将工件放置在已知坐标系中,通过测量机器人末端执行器相对于该已知坐标系的坐标来计算工件坐标系的位置和姿态。
2. 视觉标定法:通过机器视觉系统获取工件的图像信息,利用图像处理算法计算工件的位置和姿态。
3. 可编程标定法:通过程序控制机器人执行一系列特定动作,例如移动、旋转等,然后通过测量工具对机器人末端执行器的坐标进行测量,从而计算出工件坐标系的位置和姿态。
4. 双手协作标定法:利用机器人两只手的力和力矩传感器测量工件的力和力矩,通过对力和力矩的分析和计算,得到工件坐标系的位置和姿态。
工件坐标系的作用:1. 精确定位:工件坐标系的确定可以帮助机器人实现对工件的精确定位,从而有效地进行操作和加工。
2. 姿态控制:工件坐标系可以帮助机器人确定工件的姿态,从而实现准确的操作和加工。
3. 任务规划:工件坐标系可以作为规划的参考,帮助机器人确定路径和动作,从而实现高效的任务规划和执行。
4. 误差补偿:通过对工件坐标系的标定,可以计算出机器人在执行任务时可能存在的误差,从而进行误差补偿,提高生产的准确性和一致性。
5. 自动化生产:工件坐标系的准确标定可以使机器人实现自动化生产,提高生产效率和品质。
在工业机器人应用中,工件坐标的标定方法和工件坐标系的作用至关重要。
通过选择适合的标定方法,并正确理解和利用工件坐标系的作用,可以提高工业机器人的生产效率和准确性,促进制造业的发展。
简述工业机器人工件坐标的标定方法以及工件坐标系的作用

简述工业机器人工件坐标的标定方法以及工件坐标系的作用工件坐标的标定方法主要包括直接法和间接法两种。
直接法是通过对每个工件的各个特征点进行测量、计算,建立工件的坐标系,一般适用于复杂的工件;间接法是通过对工具或治具的定位基准面进行测量,而间接确定工件的位置,一般适用于简单的工件。
坐标标定的具体步骤主要包括:第一步,选择三个不在一直线上的点作为基准点;第二步,用基准点建立一个局部坐标系;第三步,测量参考点在局部坐标系中的坐标;第四步,测量参考点在世界坐标系中的坐标;第五步,求解两坐标系之间的变换矩阵;第六步,确认变换矩阵的正确性。
这些步骤中,选择基准点和测量参考点的位置是关键环节。
工件坐标系主要用于确定工件的位置和姿态。
在工件上建立一个坐标系,可以方便地描述工件在空间中的位置和方向,这在许多机械制造过程中是必需的,如数控编程、机器人路径规划等。
工件坐标系一般以工件的特征点、特征线或特征面为基准,建立与工件几何形状、尺寸、位置关系密切的坐标系。
通过坐标系,可以实现工件的精确位置定位,从而提高生产效率和加工精度,对于提高产品质量、降低生产成本具有重要意义。
- 1、下载文档前请自行甄别文档内容的完整性,平台不提供额外的编辑、内容补充、找答案等附加服务。
- 2、"仅部分预览"的文档,不可在线预览部分如存在完整性等问题,可反馈申请退款(可完整预览的文档不适用该条件!)。
- 3、如文档侵犯您的权益,请联系客服反馈,我们会尽快为您处理(人工客服工作时间:9:00-18:30)。
工件坐标系的确定
1. 机床坐标系
为了保证数控机床的运动、操作及程序编制的一致性,数控标准统一规定了机床坐标系和运动方向,编程时采用统一的标准坐标系。
(1) 坐标系建立的基本原则
1) 坐标系采用笛卡儿直角坐标系,右手法则。
如图11-2所示,基本坐标轴为X、Y、Z直角坐标,相应于各坐标轴的旋转坐标分别记为A、B、C。
2) 采用假设工件固定不
动,刀具相对工件移动的原则。
由于机床的结构不同,有的是
刀具运动,工件固定不动;有
的是工件运动,刀具固定不动。
为编程方便,一律规定工件固
定,刀具运动。
3) 采用使刀具与工件之间距离增大的方向为该坐标轴的正方向,反之则为负方向。
即取刀具远离工件的方向为正方向。
旋转坐标轴A、B、C的正方向确定如图11-2所示,按右手螺旋法则确定。
(2) 各坐标轴的确定
确定机床坐标轴时,一般先确定Z轴,然后确定X轴和Y轴。
Z轴:一般以传递切削力的主轴定为Z坐标轴,如果机床有一系列主轴,则选尽可能垂直于工件装夹面的主要轴为Z轴。
Z轴的正方向为从工件到刀具夹持的方向。
X轴:为水平的、平行于工件装夹平面的轴。
对于刀具旋转的机床,若Z轴为水平时,由刀具主轴的后端向工件看,X轴正方向指向右方;若Z轴为垂直时,由主轴向立柱看,X轴正方向指向右方。
对无主轴的机床(如刨床),X轴正方向平行于切削方向。
Y轴:垂直于X及Z轴,按右手法则确定其正方向。
(3) 机床坐标系的原点
机床坐标系的原点也称机械原点、参考点或零点,这个原点是机床上固有的点,机床一经设计和制造出来,机械原点就已经被确定下来。
机床启动时,通常要进行机动或手动回零,就是回到机械原点。
数控机床的机械原点一般在直线坐标或旋转坐标回到正向的极限位置。
2. 工件坐标系(编程坐标系)
图11-3 工件坐标系与机床坐标系的位置关系 工件坐标系是由编程人员
在编制程序时用来确定刀具和
程序的起点,工件坐标系的原点
可由编程人员根据具体情况确
定,但坐标轴的方向应与机床坐标系一致,并且与之有确定的尺寸关系。
机床坐标系与工件坐标
系的关系如图11-3所示。
不同的工件建立的坐标系也可有所不同,有的数控系统允许一个工件可建立多个工件坐标系,或者在一个工件坐标系下再建立一个坐标系,称之为局部坐标系。
局部坐标系原点的坐标值应是相对于工件坐标系,而不是相对于机床坐标系。
通过建立多个坐标系或局部坐标系可大大简化零件的编程工作。