高炉炉渣碱度计算
高炉炼铁技术简介
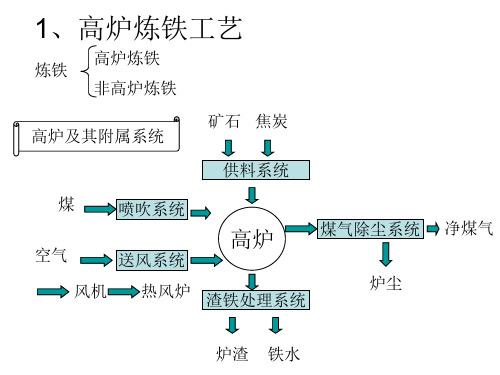
烧结 工艺 流程
精矿、粉矿 (0~10mm)
石灰石、白云石 (80~0mm)
碎焦、无烟煤 (25~0mm)
破碎
>3mm
• 炉渣中氧化物的种类:碱性氧化物、酸性氧化物 和中性氧化物。以碱性氧化物为主的炉渣称碱性 炉渣;以酸性氧化物为主的炉渣称酸性炉渣。
• 炉渣的碱度(R):炉渣中碱性氧化物和酸性氧化 物的质量百分数之比表示炉渣碱度:
• 高炉炉渣碱度一般表示式:R=w(CaO)/w (SiO2)
• 炉渣的碱度根据高炉原料和冶炼产品的不同,一 般在1.0~1.25之间。
消耗的(干)焦炭量(焦比一定的情况 下)
高炉每天消耗的焦炭量 I=
高炉的有效容积
• 生铁合格率:生铁化学成分符合国家标准的总量 占生铁总量的指标。
• 休风率:高炉休风时间(不包括计划大、中、小 修)占日历工作时间的百分数。
规定的日历作业时间=日历时间-计划大中修及
封炉时间
休风率=
高炉休风时间 规定的日历作业时间 ×100%
高炉炉渣与脱硫
• 高炉炉渣是铁矿石中的脉石和焦炭(燃料)中 的灰分等与熔剂相互作用生成低熔点的化 合物,形成非金属的液相。
– 高炉炉渣的成分 – 高炉炉渣作用 – 成渣过程 – 生铁去硫
• 高炉炉渣的来源:矿石中的脉石、焦炭(燃料)中 的灰分、熔剂中的氧化物、被侵蚀的炉衬等。
• 高炉炉渣的成分:氧化物为主,且含量最多的是 SiO2、CaO、Al2O3、MgO。
② 物理性能 包括机械强度和粒度组成等。高炉要求烧结矿机械 强度高,粉末少,粒度均匀。 烧结矿粒度小于5mm的称之为粉末。粉末含量对高 炉料柱透气性影响很大。粉末含量高,高炉透气性差, 导致炉况不顺,可能引起崩料或悬料。 反应机械强度的指标为:转鼓指数、抗磨指数、筛 分指数。 目前武钢烧结矿的转鼓强度大约在79%~80%左右。
高炉工长常用公式
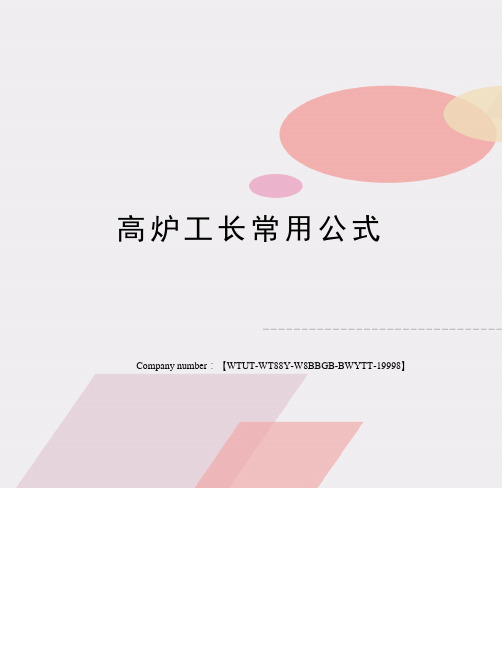
高炉工长常用公式Company number:【WTUT-WT88Y-W8BBGB-BWYTT-19998】工长公式1.透气性指数透气性指数=风量/(风压-顶压)2.压差压差=风压-顶压3.综负综负=矿石批重/(焦批干基+焦丁干基+煤粉×1000/小时料批)++4.理燃理燃(迁钢)=1500+×风温-×煤粉×1000/(小时料批×批铁量)-×鼓风湿度+40×(×氧量+×(风量-×氧量)/(风量-)理燃(1,3炉)=1530+×风温+[4970×氧量/×60×风量)-3770×煤量/×60×风量)]5.炉腹煤气炉腹煤气=×风量+氧量/30+鼓风湿度/1000×18×(风量+氧量/60)+煤粉×1000/60×100×26.标准风速标准风速=风量/(风口面积×60)7.实际风速实际风速=((标准风速×(风温+273)×/(+风压)×(273+20))8.鼓风动能鼓风动能=×风量3/风口面积2×(风温+273)2/(风压×101325+101325)2×10-5×103/ 9.二元碱度二元碱度=CaO / (SiO2-矿批×含铁量×Si系数×10.三元碱度三元碱度=(CaO+MgO)/ (SiO2-矿批×含铁量×Si系数×11.渣铁比渣铁比=CaO×96000/Fe×CaO系数12.硫负荷硫负荷=S/Fe×96013.批铁量批铁量=Fe×14.炉渣碱度R2=CaO/SiO2R3=(CaO+MgO)/SiO2R4=(CaO+MgO)/(SiO2+Al2O3)15.冶炼周期冶炼周期=风口中心线至料线炉容/(每批料体积×(1-)16. 出铁流速出铁流速=估重/出铁时间。
高炉铁合金冶炼主要技术经济指标计算方法

高炉铁合金冶炼主要技术经济指标计算方法一、锰铁合格率锰铁合格率是指报告期内锰铁检验合格量与锰铁检验总量的百分比。
其计算公式为:锰铁合格率(%) = 锰铁检验合格量(吨)×100%锰铁送检总量(吨)计算说明:高炉开工后,不论任何原因产生的出格锰铁,均应参加锰铁合格率的计算;式中子、母项单位为标准吨。
二、低硅锰铁率低硅锰铁率是指低硅锰铁量占合格锰铁总量的百分比。
其计算公式为:低硅锰铁率(%)= 低硅锰铁总量(吨)×100%合格锰铁总量(吨)计算说明:低硅锰铁是指符合现行国标一组硅要求的锰铁;式中子、母项单位为标准吨。
三、燃料比燃料比是指每炼1吨合格锰铁(标准吨)所消耗的入炉燃料的数量。
它反映燃料的节约或浪费以及高炉操作水平的高低。
燃料全部以扣除水分的干基计算,其计算公式为:燃料比(千克/吨) = 入炉焦炭耗用量(千克)+入炉喷吹燃料耗用量(千克)合格锰铁生产量(吨)入炉焦比(千克/吨) = 入炉焦炭耗用量(千克)合格锰铁生产量(吨)煤粉消耗(千克/吨)= 喷入高炉内的煤粉数量(千克)合格锰铁生产量(吨)计算说明:式中母项单位为标准吨。
高炉铁合金工序单位能耗参照高炉炼铁工序单位能耗计算公式计算。
四、入炉锰矿消耗入炉锰矿消耗是指每炼一吨合格锰铁(标准吨)所消耗的入炉锰矿石的数量,包括天然矿石和人造块矿。
天然矿石按扣除水分的干基计算。
其计算公式为:锰矿石消耗(千克/吨)=入炉天然矿石消耗量(千克)+入炉人造块矿消耗是(千克)合格锰铁生产量(吨)计算说明:式中母项单位为标准吨。
五、入炉熔剂消耗入炉熔剂消耗是指每炼一吨合格锰铁(标准吨)所消耗的入炉熔剂数量,它包括石灰石、白云石、生石灰,萤石等用于造渣的碱性化合物。
这一指标综合反映炉料质量好坏及造渣操作的合理性。
其计算公式为:熔剂消耗(千克/吨)=入炉熔剂消耗总量(千克)合格锰铁生产量(吨)其中:熟料消耗(千克/吨)=入炉熟料消耗量(千克)合格锰铁生产量(吨)计算说明;(1)各种熔剂入炉消耗都不扣水分;(2)熟料包括生石灰及焙烧后的白云石;(3)式中母项单位为标准吨。
高炉冶炼物料平衡计算
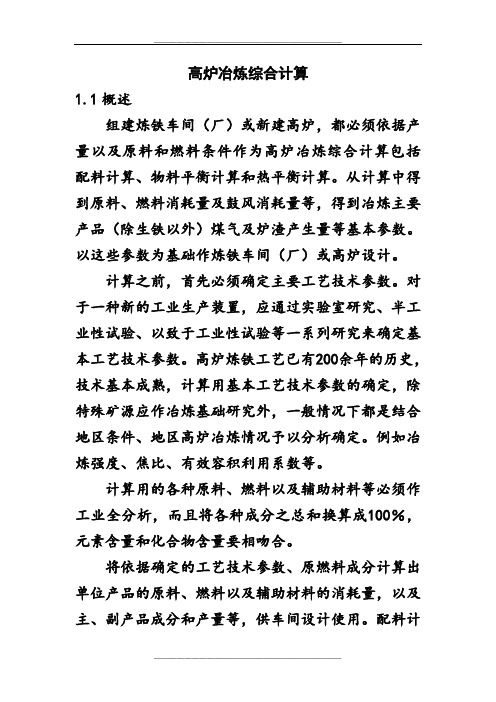
高炉冶炼综合计算1.1概述组建炼铁车间(厂)或新建高炉,都必须依据产量以及原料和燃料条件作为高炉冶炼综合计算包括配料计算、物料平衡计算和热平衡计算。
从计算中得到原料、燃料消耗量及鼓风消耗量等,得到冶炼主要产品(除生铁以外)煤气及炉渣产生量等基本参数。
以这些参数为基础作炼铁车间(厂)或高炉设计。
计算之前,首先必须确定主要工艺技术参数。
对于一种新的工业生产装置,应通过实验室研究、半工业性试验、以致于工业性试验等一系列研究来确定基本工艺技术参数。
高炉炼铁工艺已有200余年的历史,技术基本成熟,计算用基本工艺技术参数的确定,除特殊矿源应作冶炼基础研究外,一般情况下都是结合地区条件、地区高炉冶炼情况予以分析确定。
例如冶炼强度、焦比、有效容积利用系数等。
计算用的各种原料、燃料以及辅助材料等必须作工业全分析,而且将各种成分之总和换算成100%,元素含量和化合物含量要相吻合。
将依据确定的工艺技术参数、原燃料成分计算出单位产品的原料、燃料以及辅助材料的消耗量,以及主、副产品成分和产量等,供车间设计使用。
配料计算也是物料平衡和热平衡计算的基础。
依据质量守恒定律,投入高炉物料的质量总和应等于高炉排出物料的质量总和。
物料平衡计算可以验证配料计算是否准确无误,也是热平衡计算的基础。
物料平衡计算结果的相对误差不应大于0.25%。
常用的热平衡计算方法有两种。
第一种是根据热化学的盖斯定律,即按入炉物料的初态和出炉物料的终态计算,而不考虑炉内实际反应过程。
此法又称总热平衡法。
它的不足是没有反应出高炉冶炼过程中放热反应和吸热反应所发生的具体空间位置,这种方法比较简便,计算结果可以判断高炉冶炼热工效果,检查配料计算各工艺技术参数选取是否合理,它是经常采用的一种计算方法。
第二种是区域热平衡法。
这种方法以高炉局部区域为研究对象,常将高炉下部直接还原区域进行热平衡计算,计算其中热量的产生和消耗项目,这比较准确地反应高炉下部实际情况,可判断炉内下部热量利用情况,以便采取相应的技术措施。
高炉炼铁技术简易计算1

高炉炼铁技术简易计算题1.有效容积1260m 3高炉,矿批重30t,焦批重8t,压缩率为15%。
求:从料面到风口水平面的料批数(冶炼周期),(r 矿取1.8t/ m 3,r 焦取0.5 t/ m 3,工作容积取有效容积的85%) 答案:有效系数有效容积工作容积⨯=85.01260⨯=﹦1071 m 3压缩率焦炭堆比重焦炭批重矿石堆比重矿批重量每批料的炉内体积⨯⎪⎭⎫ ⎝⎛+=()%1515.00.88.10.30-⨯⎪⎭⎫ ⎝⎛+=﹦27.77m 3 每批料在炉内体积工作容积到达风口平面的料批数=77.271071=≈39 经过39批料到达风口平面。
2.620m 3高炉焦批3850kg ,焦丁批重200kg ,矿批15000kg 每小时喷煤8000kg ,每小时跑6批料,求焦炭综合负荷。
答:条件中没有给出焦炭含水分百分数,既将焦炭按干焦进行计算,如果有水分百分数还要扣除水分折合为干焦量后进行计算()批料焦丁量批料煤量批干焦炭重量批料矿量焦炭综合负荷++=2.060.885.300.15++=﹦2.793.烧结矿碱度从1.25降到1.15,已知烧结矿含SiO 2为13.00%,矿批为20t/批,如全部使用烧结矿,如何调整石灰石用量?(石灰石有效CaO 为50%)答案:此为自溶性烧结或者是低碱度烧结时的现场计算,目前已经非常少见()石灰石有效率现碱度原碱度烧结矿石批重每批料需要加减石灰石-⨯⨯⨯=10002SiO也可以分步计算石灰石用量:50.0/15.125.11000%00.13)(石量一吨烧结矿需要加石灰-⨯⨯=﹦26 kg当矿石批重为20t 时,全部使用烧结矿时,每批加石灰时26×20=520kg/批 每批加石灰石520 kg 。
4.544m 3高炉正常的日产量1300t 生铁,风量1150m 3/min 。
某天因上料系统出现故障减风至800m 3/min ,两小时后恢复正常,问减风影响生铁产量多少? 答案:⎪⎭⎫⎝⎛-⨯⨯=正常时风量水平减风时风量水平正常风量水平减风累计时间日产量减风影响生铁产量24 ()115080011502241300-⨯⨯=﹦33 t 减风影响生铁产量33t 。
高炉开炉配料计算
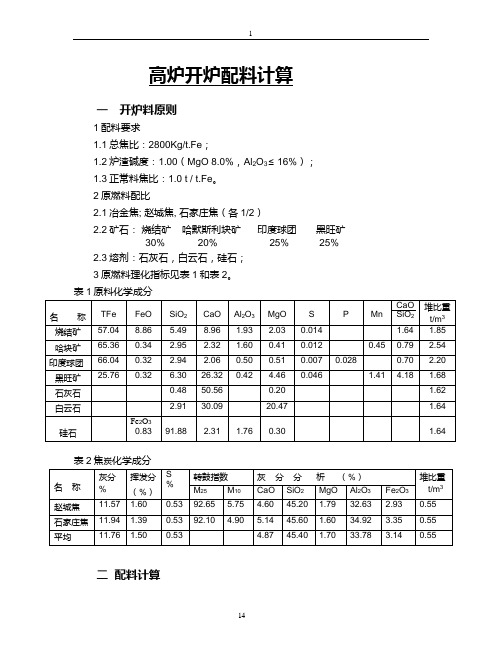
高炉开炉配料计算一开炉料原则1配料要求1.1总焦比:2800Kg/t.Fe;1.2炉渣碱度:1.00(MgO 8.0%,Al2O3≤16%);1.3正常料焦比:1.0 t / t.Fe。
2原燃料配比2.1冶金焦; 赵城焦, 石家庄焦(各1/2)2.2矿石:烧结矿哈默斯利块矿印度球团黑旺矿30% 20% 25% 25%2.3熔剂:石灰石,白云石,硅石;3原燃料理化指标见表1和表2。
二配料计算1、预计生铁成分元素Fe C Si Mn S含量(%) 92.47 4.0 3.0 0.5 0.032 、Fe、Mn回收率Fe回收率: 99.0%;Mn回收率 60.0%; S 分配率:85%进入炉渣,5%进入生铁。
3、以100 Kg混合矿计算:3.1 100 Kg混合矿平均含Fe:30×57.04%+20×65.36%+25×66.04+25×25.76% = 53.134,100 Kg混合矿出铁:100×53.13%×0.99 / 0.9247 = 56.886 Kg。
3.2炉渣成分核算:(1)生铁中Si消耗SiO256.886×3.0%×60 / 28 = 3.657(2)炉渣中FeO量53.134×1.0%×72 / 56 = 0.683(3)入炉料的S负荷30×0.014%+20×0.012%+25×0.007%+25×0.046%+56.886×0.53%=0.321(4)炉渣中的CaS0.321×85%×72 / 32=0.614(5)脱硫消耗CaO0.614×56/72=0.478(6)原燃料成分中进入炉渣的数量(7)炉渣成分调整为使炉渣成分达到要求标准,加白云石和硅石进行调整。
硅石加入量为:x白云石加入量为:y3.927+91.88% x +2.91% y =10.096+2.31% x+30.09% y2.045+0.30% x +20.47% y= 8.0%20.652+96.25% x+53.47% y解方程:x = 7.422 Kg。
高炉开炉配料计算

设X——空焦
Y——正常料
列方程为:
7.506 X
+
13.17 Y
= 311
4.5
×
16
+
4.5
× (X+Y)
÷(
6.429
× Y)
=2
整理方程得:
13.173 Y
+
7.51 X
= 311
8.357143 Y
-
4.5 X
= 72
解方程:
110.0858 Y
+ 62.73222 X
= 2599.071
110.0858 Y
+
7.506
×
13
炉渣成分校对
全炉渣成分校对表
品种 数量
烧结矿 105.6
球团 70.4
锰矿 3.84
石灰石
0
硅石 13.584
萤石
4.8
白云石 15.026
焦炭 202.5
铁量 102.86
合计
成分 100%
100
96%
96
kg/t
焦炭 130.500
合计
成分 100%
100.000
96%
96
kg/t
=
正常料炉渣成分校对见表4
正常料组成及成分校对表
表4
品种 数量
SiO2
CaO
焦炭
4.5
0.256
0.028
烧结矿 6.6
0.390
0.890
球团矿 4.4
0.300
0.020
锰矿 0.240 0.010
0.000
石灰石
0
0.000
高炉冶炼物料平衡计算

高炉冶炼综合计算概述组建炼铁车间(厂)或新建高炉,都必须依据产量以及原料和燃料条件作为高炉冶炼综合计算包括配料计算、物料平衡计算和热平衡计算。
从计算中得到原料、燃料消耗量及鼓风消耗量等,得到冶炼主要产品(除生铁以外)煤气及炉渣产生量等基本参数。
以这些参数为基础作炼铁车间(厂)或高炉设计。
计算之前,首先必须确定主要工艺技术参数。
对于一种新的工业生产装置,应通过实验室研究、半工业性试验、以致于工业性试验等一系列研究来确定基本工艺技术参数。
高炉炼铁工艺已有200余年的历史,技术基本成熟,计算用基本工艺技术参数的确定,除特殊矿源应作冶炼基础研究外,一般情况下都是结合地区条件、地区高炉冶炼情况予以分析确定。
例如冶炼强度、焦比、有效容积利用系数等。
计算用的各种原料、燃料以及辅助材料等必须作工业全分析,而且将各种成分之总和换算成100%,元素含量和化合物含量要相吻合。
将依据确定的工艺技术参数、原燃料成分计算出单位产品的原料、燃料以及辅助材料的消耗量,以及主、副产品成分和产量等,供车间设计使用。
配料计算也是物料平衡和热平衡计算的基础。
依据质量守恒定律,投入高炉物料的质量总和应等于高炉排出物料的质量总和。
物料平衡计算可以验证配料计算是否准确无误,也是热平衡计算的基础。
物料平衡计算结果的相对误差不应大于%。
常用的热平衡计算方法有两种。
第一种是根据热化学的盖斯定律,即按入炉物料的初态和出炉物料的终态计算,而不考虑炉内实际反应过程。
此法又称总热平衡法。
它的不足是没有反应出高炉冶炼过程中放热反应和吸热反应所发生的具体空间位置,这种方法比较简便,计算结果可以判断高炉冶炼热工效果,检查配料计算各工艺技术参数选取是否合理,它是经常采用的一种计算方法。
第二种是区域热平衡法。
这种方法以高炉局部区域为研究对象,常将高炉下部直接还原区域进行热平衡计算,计算其中热量的产生和消耗项目,这比较准确地反应高炉下部实际情况,可判断炉内下部热量利用情况,以便采取相应的技术措施。
- 1、下载文档前请自行甄别文档内容的完整性,平台不提供额外的编辑、内容补充、找答案等附加服务。
- 2、"仅部分预览"的文档,不可在线预览部分如存在完整性等问题,可反馈申请退款(可完整预览的文档不适用该条件!)。
- 3、如文档侵犯您的权益,请联系客服反馈,我们会尽快为您处理(人工客服工作时间:9:00-18:30)。
浅谈炉渣碱度计算
摘要:通过计算机办公软件Microsoft Excel 编辑公式计算和分析炉渣碱度,并对现在玉钢炼铁作业区高炉工长核料计算提出改进意见。
关键词:碱度Excel 核料
The basicity on slag calculation
Kang yun
Abstract:through the computer software for office use Microsoft Excel edit formula calculation and analysis the basicity slag, and now working in the blast furnace ironmaking jade steel foreman nuclear material calculation improvements.
Keywords: alkalinity Excel nuclear material
一、概论
玉钢炼铁作业区于2005年2月28日开炉投产,现有450m3高炉两座,1080m3高炉一座。
开炉后高炉操作沿用昆钢老厂的核料计算,采用每批料需加石灰石量来作为碱度调整的依据,进行核料计算。
由于现在炉料结构的变化,碱度调剂采用改变烧结矿和酸性炉料之间配比的方法,取代石灰石调整碱度。
原来的核料计算已经不适应现在的生产需求,因此,探索和寻找新的核料方法具有重要的意义。
二、炉渣配料计算
1、Microsoft Excel 简介
Microsoft Excel是微软公司的办公软件Microsoft Office 的组件之一,是微软公司为Windows操作系统编写的一款表格处理软件,它可以进行各种数据的处理,统计分析和辅助决策操作,广泛地应用于管理、统计、金融等众多领域。
本文才用Excel的公式编辑计算炉渣碱度和炉料结构中烧结矿和球团矿的理论配比。
解决原料大幅度变化时的配料计算。
2、核料计算
计算方法为:每批料所需的石灰石量=[(入炉点的SiO2量-还原生铁中的
Si所需SiO2)×R2-入炉总的CaO量]÷石灰石的有效溶剂。
缺点:只能计算出所需石灰石用量,对工长调整炉渣碱度时指导意义不大。
新的计算方法根据原料成分直接计算炉渣碱度,计算公式为:
R2=入炉总的CaO量÷(入炉点的SiO2量-还原生铁中的Si所需SiO2)具体的计算方法如下:
图一
T理=(B8*E8+B9*E9+B10*E10+B14*E14)*0.97/0.95
炉渣碱度:
=(D8*E8+D9*E9+D10*E10)/(C8*E8+C9*E9+C10*E10+C11*E11+C12*E12+C13* E13-B16*2.14*0.005)
烧结矿溶剂系数=D8*1000-1.08*(C8*1000-B8*1000*2.14*0.005)
球团矿溶剂系数=D9*1000-1.08*(C9*1000-B9*1000*2.14*0.005)
块矿溶剂系数=D10*1000-1.08*(C10*1000-B10*1000*2.14*0.005)
焦炭溶剂系数=D11*1000-1.08*(C11*1000-B11*1000*2.14*0.005)
煤粉溶剂系数=D12*1000-1.08*(C12*1000-B12*1000*2.14*0.005)
小焦溶剂系数=D13*1000-1.08*(C13*1000-B13*1000*2.14*0.005)
烧结矿理论配比计算为
=((15000*(-F9)+E10*F9-E10*F10-E11*F11-E12*F12-E13*F13)/(F8-F9))/150 球团矿理论配比计算为
=((15000*(-F8)+E10*F8-E10*F10-E11*F11-E12*F12-E13*F13)/(F9-F8))/150 3、运用实例
3.1已知原料成分、用量计算炉渣碱度
原料成分为:
表一
计算碱度为1.08
3.2计算炉温对碱度的影响
原料成分和炉料结构如表一,炉温对碱度的影响如表二所示
表二
由以上计算可知炉温对碱度的影响很大。
3.3溶剂系数计算
矿石和焦炭的溶剂系数是指在满足自身造渣条件下,所剩余或需要补加的石灰石量,计算公式如下:
k=
有效
cao cao si TFe sio w w R w w w --0][)(2*]28
60
]
[
式中
k 矿石和焦炭的溶剂系数kg/t 2sio w 矿石或焦炭的sio2含量,kg/t )(TFe w 矿石或焦炭的全铁量,kg/t ][si w 生铁含si 量,%
cao w 矿石或焦炭的cao 含量kg/t 0R 炉渣碱度
有效cao w 石灰石中有效cao 含量
有效cao w =熔熔)(0)(R sio cao w w -,熔熔,)()(sio cao w w 石灰石中cao 及sio2的含量,%
由于碱度计算中不考虑石灰石量,所以在以下的溶剂系数计算中采用
k=cao si TFe sio w R w w w --0][)(2*]28
60
]
[ 其实际意义为:矿石和焦炭的溶剂系数是指在满足自身造渣条件下,所贡献的cao 量,kg/t
如表一所示原料成分的溶剂系数为
3.4当炉料结构大幅度变化时烧结矿和球团矿的配比计算
已知条件:原料成分、矿批、块矿用量(可以为0)和设定炉温,求达到规定碱度的烧结矿和球团矿配比。
3.4.1当块矿为0时的理论配比计算如图一所示。
3.4.2当块矿用量为2000kg/批时,计算如下:
碱度验算
三、总结
通过Excel可以使繁琐的计算变为很简单的过程,大大的节约变料计算时间。
特别是在原料大幅度变化时,对高炉变料有很好的指导作用。
不足之处,由于计算是纯理论计算,所以对原料分析的准确性有较高的要求。
同时由于原料的粉末情况不同,炉尘灰的吹出量无法计算出来,所以碱度计算值在炉尘灰的吹出量多,影响到碱度时会造成计算值与实际炉渣碱度存在误差。
由于本人的工作经验和理论水平有限,请评审老师对不对之处或欠妥的地方不吝赐教为感。
参考文献:
1. 周传典《高炉炼铁生产技术手册》冶金工业出版社2003年版
2. 宋建成《高炉炼铁理论与操作》冶金工业出版社2005年版
3. 张家驹《铁冶金学》东北工学院出版社1987年版
4. 王国正《Excel 2003使用技巧》冶金工业出版社1997年版
5. 王莜留《高炉生产知识问答》冶金工业出版社2004年版。