高炉冶炼工艺炉渣碱度
高炉炼铁技术简介
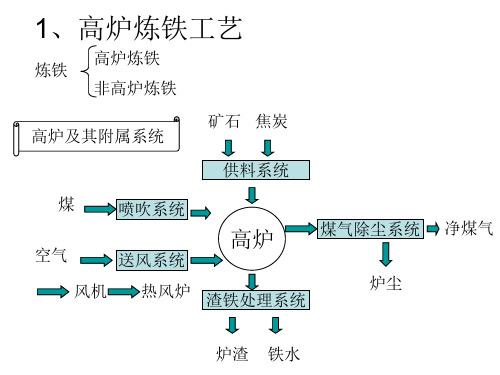
烧结 工艺 流程
精矿、粉矿 (0~10mm)
石灰石、白云石 (80~0mm)
碎焦、无烟煤 (25~0mm)
破碎
>3mm
• 炉渣中氧化物的种类:碱性氧化物、酸性氧化物 和中性氧化物。以碱性氧化物为主的炉渣称碱性 炉渣;以酸性氧化物为主的炉渣称酸性炉渣。
• 炉渣的碱度(R):炉渣中碱性氧化物和酸性氧化 物的质量百分数之比表示炉渣碱度:
• 高炉炉渣碱度一般表示式:R=w(CaO)/w (SiO2)
• 炉渣的碱度根据高炉原料和冶炼产品的不同,一 般在1.0~1.25之间。
消耗的(干)焦炭量(焦比一定的情况 下)
高炉每天消耗的焦炭量 I=
高炉的有效容积
• 生铁合格率:生铁化学成分符合国家标准的总量 占生铁总量的指标。
• 休风率:高炉休风时间(不包括计划大、中、小 修)占日历工作时间的百分数。
规定的日历作业时间=日历时间-计划大中修及
封炉时间
休风率=
高炉休风时间 规定的日历作业时间 ×100%
高炉炉渣与脱硫
• 高炉炉渣是铁矿石中的脉石和焦炭(燃料)中 的灰分等与熔剂相互作用生成低熔点的化 合物,形成非金属的液相。
– 高炉炉渣的成分 – 高炉炉渣作用 – 成渣过程 – 生铁去硫
• 高炉炉渣的来源:矿石中的脉石、焦炭(燃料)中 的灰分、熔剂中的氧化物、被侵蚀的炉衬等。
• 高炉炉渣的成分:氧化物为主,且含量最多的是 SiO2、CaO、Al2O3、MgO。
② 物理性能 包括机械强度和粒度组成等。高炉要求烧结矿机械 强度高,粉末少,粒度均匀。 烧结矿粒度小于5mm的称之为粉末。粉末含量对高 炉料柱透气性影响很大。粉末含量高,高炉透气性差, 导致炉况不顺,可能引起崩料或悬料。 反应机械强度的指标为:转鼓指数、抗磨指数、筛 分指数。 目前武钢烧结矿的转鼓强度大约在79%~80%左右。
高炉生产工艺流程

接下来是炉气处理阶段,高炉冶炼过程中产生的炉气中含有一氧化碳、二氧化碳、氮气等物质。这些气体需要被净化和处理,以达到排放标准。常用的方法包括干法除尘、湿法除尘、除硫和除氮等。
最后是余热回收阶段,高炉生产过程中产生了大量的余热,包括炉渣的冷却余热和炉气的余热。这些余热可以通过余热回收系统进行收集和利用,从而提高能源利用效率。
接下来是炉内反应阶段,当炉缸中的炉料逐渐下降时,炉缸内的温度会迅速上升。炉料在高温下被还原成铁,同时产生大量的炉渣。在这个过程中,还会产生大量的一氧化碳和水蒸气。
然后是铁水出炉阶段,当足够的铁被还原出来时,可以通过倾炉孔将铁水从高炉中排出。铁水会流入铁罐中,并冷却凝固成铁块。
之后是炉渣处理阶段,高炉炉渣是由炉料ห้องสมุดไป่ตู้的铁氧化物、石灰石和其他杂质组成的。处理炉渣主要有两个目的:一是回收其中的铁,二是确保炉渣中的有害物质被安全处理。一般会通过氧枪在炉渣中吹氧气,使其中的铁氧化物氧化成铁,并进一步回收。
高炉生产工艺流程
高炉是一种用于冶炼铁的设备,它能够将铁矿石中的铁氧化物还原成纯铁。高炉生产工艺流程包括六个主要步骤:入炉、炉内反应、铁水出炉、炉渣处理、炉气处理和余热回收。
首先是入炉阶段,这个阶段主要是将铁矿石和焦炭按一定比例装入高炉的上料斗中,然后通过料斗控制系统将料物顺次送入炉缸内。在这个过程中,还会加入一定量的石灰石和焦粉,以调节炉料的碱度和流动性。
锰铁的冶炼方法

书山有路勤为径,学海无涯苦作舟锰铁的冶炼方法高炉冶炼一般采用1000 米3 以下的高炉,设备和生产工艺大体与炼铁高炉相同。
锰矿石在由炉顶下降的过程中,高价的氧化锰(MnO2,Mn2O3,Mn3O4)随温度升高,被CO 逐步还原到MnO。
但MnO 只能在高温下通过碳直接还原成金属,所以冶炼锰铁需要较高的炉缸温度,为此炼锰铁的高炉采用较高的焦比(1600 公斤/吨左右)和风温(1000℃以上)。
为降低锰损耗,炉渣应保持较高的碱度(CaO/SiO2 大于1.3)。
由于焦比高和间接还原率低,炼锰铁高炉的煤气产率和含CO 量比炼铁高炉为高,炉顶温度也较高(350℃以上)。
富氧鼓风可提高炉缸温度,降低焦比,增加产量,且因煤气量减少可降低炉顶温度,对锰铁的冶炼有显著的改进作用。
电炉冶炼锰铁的还原冶炼有熔剂法(又称低锰渣法)和无熔剂法(高锰渣法)两种。
熔剂法原理与高炉冶炼相同,只是以电能代替加热用的焦炭。
通过配加石灰形成高碱度炉渣(CaO/SiO2 为1.3~1.6)以减少锰的损失。
无熔剂法冶炼不加石灰,形成碱度较低(CaO/SiO2 小于 1.0)、含锰较高的低铁低磷富锰渣。
此法渣量少,可降低电耗,且因渣温较低可减轻锰的蒸发损失,同时副产品富锰渣(含锰25~40 %)可作冶炼锰硅合金的原料,取得较高的锰的综合回收率(90%以上)。
现代工业生产大多采用无熔剂法冶炼碳素锰铁,并与锰硅合金和中、低碳锰铁的冶炼组成联合生产流程见图。
现代大型锰铁还原电炉容量达40000~75000 千伏安,一般为固定封闭式。
熔剂法的冶炼电耗一般为2500~3500 千瓦时/吨,无熔剂法的电耗为2000~3000 千瓦时/吨。
锰硅合金用封闭或半封闭还原电炉冶炼。
一般采用含二氧化硅高、含磷低的锰矿或另外配加硅石为原料。
富锰渣含磷低、含二氧化硅高是冶炼锰硅合金的好原料。
冶炼电耗一般约3500~5000 千瓦时/吨。
入炉原料先作预处理,包括整粒、预热、预还原。
高炉冶炼物料平衡计算

高炉冶炼综合计算概述组建炼铁车间(厂)或新建高炉,都必须依据产量以及原料和燃料条件作为高炉冶炼综合计算包括配料计算、物料平衡计算和热平衡计算。
从计算中得到原料、燃料消耗量及鼓风消耗量等,得到冶炼主要产品(除生铁以外)煤气及炉渣产生量等基本参数。
以这些参数为基础作炼铁车间(厂)或高炉设计。
计算之前,首先必须确定主要工艺技术参数。
对于一种新的工业生产装置,应通过实验室研究、半工业性试验、以致于工业性试验等一系列研究来确定基本工艺技术参数。
高炉炼铁工艺已有200余年的历史,技术基本成熟,计算用基本工艺技术参数的确定,除特殊矿源应作冶炼基础研究外,一般情况下都是结合地区条件、地区高炉冶炼情况予以分析确定。
例如冶炼强度、焦比、有效容积利用系数等。
计算用的各种原料、燃料以及辅助材料等必须作工业全分析,而且将各种成分之总和换算成100%,元素含量和化合物含量要相吻合。
将依据确定的工艺技术参数、原燃料成分计算出单位产品的原料、燃料以及辅助材料的消耗量,以及主、副产品成分和产量等,供车间设计使用。
配料计算也是物料平衡和热平衡计算的基础。
依据质量守恒定律,投入高炉物料的质量总和应等于高炉排出物料的质量总和。
物料平衡计算可以验证配料计算是否准确无误,也是热平衡计算的基础。
物料平衡计算结果的相对误差不应大于%。
常用的热平衡计算方法有两种。
第一种是根据热化学的盖斯定律,即按入炉物料的初态和出炉物料的终态计算,而不考虑炉内实际反应过程。
此法又称总热平衡法。
它的不足是没有反应出高炉冶炼过程中放热反应和吸热反应所发生的具体空间位置,这种方法比较简便,计算结果可以判断高炉冶炼热工效果,检查配料计算各工艺技术参数选取是否合理,它是经常采用的一种计算方法。
第二种是区域热平衡法。
这种方法以高炉局部区域为研究对象,常将高炉下部直接还原区域进行热平衡计算,计算其中热量的产生和消耗项目,这比较准确地反应高炉下部实际情况,可判断炉内下部热量利用情况,以便采取相应的技术措施。
高炉炼铁技术主要工艺参数计算公式
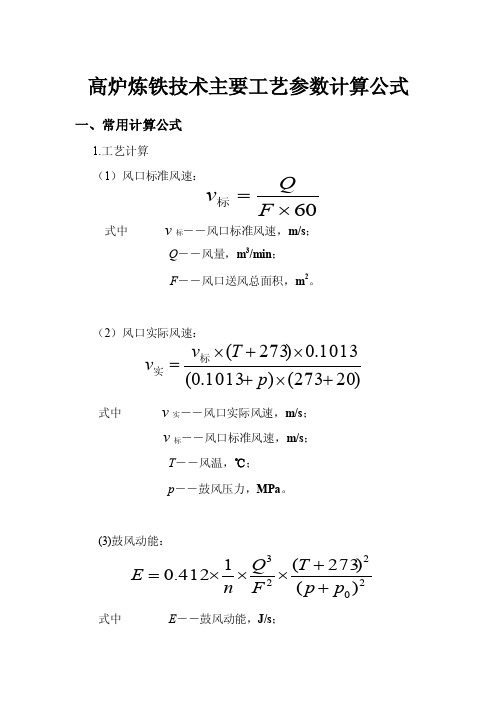
高炉炼铁技术主要工艺参数计算公式一、常用计算公式1.工艺计算(1)风口标准风速:式中v 标--风口标准风速,m/s ;Q ――风量,m 3/min ; F ――风口送风总面积,m 2。
(2)风口实际风速:式中 v 实--风口实际风速,m/s ;v 标--风口标准风速,m/s ;T --风温,℃; p --鼓风压力,MPa 。
(3)鼓风动能:式中 E --鼓风动能,J/s ;60⨯=F Q v 标)20273()1013.0(1013.0)273(+⨯+⨯+⨯=p T v v 标实20223)()273(1412.0p p T F Q n E ++⨯⨯⨯=Q --风量,m 3/min ;n --风口数目,个;F --风口总截面积,m 3; T --热风温度,℃;P --热风压力,Pa ;P 0--标准大气压,等于101325Pa 。
(4)富氧率:1)氧气兑入口在冷风管道孔板前面,即富氧量流经流量孔板,考虑鼓风湿度时富氧率公式为:不考虑鼓风湿度时富氧率公式为:2)氧气兑入口在冷风管道孔板后面,即富氧量未流经流量孔板,考虑鼓风湿度时富氧率公式为:不考虑鼓风湿度时富氧率公式为:()()%10021.029.021.0⨯⎥⎦⎤⎢⎣⎡-++⨯-=风氧氧风Q b Q f Q Q B ()%10021.0⨯-=风氧Q Q b B ()%10021.029.021.0⨯⎥⎥⎦⎤⎢⎢⎣⎡-+++⨯=氧风氧风Q Q b Q f Q B ()%10021.0⨯+⨯-=氧风氧Q Q Q b B式中 B --富氧率,%;Q 风--风量(冷风流量孔板显示值),m 3/min ;Q 氧--富氧量,m 3/min ;0.21--鼓风中含氧率;b --氧气中含氧率,%; f --鼓风湿度,%。
(5)冶炼周期: 式中t --冶炼周期,h ;V ′--由料线到风口中心线的容积,m 3; n --每天料批数,批;V --每批料体积,m 3/批;c --炉料在高炉内压缩率,一般为12~15%。
炼钢与连铸若干新技术

炼钢与连铸若干新技术炼钢与连铸作为钢铁生产的重要环节,关系着钢铁质量、生产效率以及能源消耗。
近年来,随着科学技术的不断发展,炼钢与连铸领域出现了许多新技术,这些新技术在提高产品质量、降低生产成本等方面发挥着重要作用。
本文将介绍一些关于炼钢与连铸的若干新技术。
一、炼钢新技术1. 超高炉渣碱度炼钢技术传统炼钢过程中,高炉渣的碱度一般在1.5以上,导致了炼钢中的碱度冶炼难度大。
超高炉渣碱度炼钢技术通过增加炉渣碱度,提高炼钢过程中的碱度,使得钢水中的夹杂物得以吸附和浮渣,从而有效提高了钢水的质量,降低了夹杂物含量。
2. 高炉富氧燃烧技术传统的高炉燃烧采用煤气、焦炭等作为还原剂,而高炉富氧燃烧技术则采用富氧燃烧,使得炉顶煤气中氧分压大大提高,煤气焚烧效率显著提高,从而有效减少了炼钢过程中的二氧化碳排放,降低了生产成本。
3. 高效矿石还原技术传统的炼钢制程中,矿石还原效率低,而高效矿石还原技术采用高效还原剂和改良还原工艺,可以明显提高还原效率,减少资源的浪费,降低生产成本。
二、连铸新技术1. 动态软浇铸技术动态软浇铸技术是指在连铸过程中,通过实时数据分析,调整结晶器冷却水的流速和温度,实现钢坯凝固过程中的动态调控,确保钢坯结晶组织的均匀性和合格率。
2. 连铸直齿轮技术传统连铸转辊采用辊凹槽结构,而连铸直齿轮技术则采用直齿轮结构,使得连铸转辊的传动机构更加紧凑、稳定、可靠,最大限度地减小了设备的占地面积,提高了生产效率。
3. 连铸在线水平矫直技术传统的连铸坯的矫直需要通过离线操作进行,而连铸在线水平矫直技术则采用在线连铸坯的自动矫直设备,实现了连铸坯的在线矫直,提高了生产效率,降低了生产成本。
以上所提到的炼钢与连铸的新技术只是其中的一部分,随着科学技术的不断进步,相关新技术也在不断涌现。
这些新技术的应用,将进一步推动炼钢与连铸领域的发展,为钢铁行业的持续发展注入新的活力。
高炉配料计算
高炉配料计算冶炼1t 生铁,需要一定数量的矿石、熔刑和燃料(焦炭及喷吹燃料)。
对于炼铁设计的工艺计算,燃料的用量是预先确定的,是已知的量,配料计算的主要任务,就是求出在满足炉渣碱度要求条件下,冶炼规定成分生铁所需要的矿石、熔剂数量。
对于生产高炉的工艺计算,各种原料的用量都是已知的,从整体上说不存在配料计算的问题,但有时需通过配料计算求解矿石的理论出铁量、理论渣量等,有时因冶炼条件变化需要作变料计算。
一、配料计算的目的配料计算的目的,在于根据已知的原料条件和冶炼要求来决定矿石和熔剂的用量,以配制合适的炉渣成分和获得合格的生铁。
二、配料计算时需要确定的已知条件(1)原始资料的收集整理生产中原始资料分析常常不完全,或元素分析和化合物分析不相吻合,加之分析方法不同存在分析误差,以致各种化学组成之和不等于100%。
因此,应该先确定元素在原料存在的形态,然后进行核算,使总和为100%。
换算为100%方法,可以均衡地扩大或缩小各成分的百分比,调整为100%,或者按照分析误差允许的范围,人为的调整为100%。
调整幅度不大时,以调整Al 2O 3或MgO 为宜。
在各种原料中化合物存在的形态和有关换算,按照下述方法处理。
烧结矿分析的S ,P ,Mn 分别以FeS, P 2O 5,MnO 形态存在。
它们的换算为:S──FeS ω(FeS)=ω(S )×3288% P──P 2O 5 ω(P 2O 5) =ω(P )×62142%Mn ──MnO ω(MnO)=ω(Mn )×5571%式中的S ,P ,Mn 等元素皆为分析值(百分含量),当要计算Fe 2O 3时,需要从生铁(TFe )中扣除FeO 和FeS 中的Fe ,再进行换算。
ω(Fe 2O 3)= (112162ω(Fe )-ω(FeO )×7256-ω(FeS )×8856)% 式中的Fe ,FeO 为分析所得烧结矿的全铁和氧化亚铁的百分含量,FeS 为换算所得的硫化亚铁量。
高炉炼铁的原料和产品
高炉炼铁的原料和产品图5-2为高炉炼铁原料和产品的流向图。
高炉使用的原料包括铁矿石(烧结矿、球团矿和块矿)、焦炭、煤粉、鼓风和少量熔剂;产品包括铁水、高炉煤气和高炉渣。
1 原料(1)铁矿石:烧结矿、球团矿和块矿的典型化学成分见表5-1。
在大型高炉炉料结构中,高碱度烧结矿一般占70% -80%,酸性的球团矿和块矿占20% ~30%。
熔剂通常为石灰石, 用来调节炉渣碱度。
高炉渣的碱度(ff = Ca0/Si02)在1.0-1.25之间,当碱性炉料(高碱度烧结矿)与酸性炉料(球团矿和块矿)比例合适时,高炉中可不加或只加少量石灰石。
根据人炉综合品位,冶炼U生铁需要消耗铁矿石1.5~1. 7t。
(2)燃料:焦炭在高炉风口区域燃烧产生大量热量和煤气(CO+ N2)。
煤气中的CO将铁矿石中的氧化铁还原成金W铁,燃烧产生的热量将渣铁熔化成铁水和液态炉渣。
焦炭在高炉内始终呈固态,它能够将整个高炉的料柱支撑起来,保持高炉内部具有良好的透气性。
煤粉从高炉风口喷入炉内,在风口区域燃烧产生热量和还原煤气,可代替部分焦炭。
但煤粉无法代替焦炭的另一个重要作用——支撑料柱。
目前,冶炼It生铁大约需要消耗焦炭250 - 350 kg,消耗煤粉150 ~ 250kg。
(3)鼓风:空气通过高炉鼓风机加压后成为高压空气(鼓风),经过热风炉换热,将温度提高到1100 ~1300"1:,再从高炉风口进人炉缸,与焦炭和煤粉燃烧产生热量和煤气。
鼓风带人高炉的物理热占高炉热量总收人的20%左右。
在鼓风中加人氧气可提高鼓风中的氧含量(称为富氧鼓风)。
采用富氧鼓风可提高风口燃烧温度,有利于高炉提高喷煤量和高炉利用系数。
冶炼It生铁大约需要鼓风1400 ~ 1700m3。
2 产品(1)铁水:铁水的主要化学成分为Fe、C、Si、Mn, P、S等,温度1450 ~ lSSOt。
按照Si含量的不同,将高炉铁水分为炼钢生铁(《>[Si] < 1.25%)和铸造生铁(切[Si]这1.25%)。
钢铁冶金部分课后作业题及答案
1—1高炉炼铁工艺由哪几部分组成?答案(1):在高炉炼铁生产在中,高炉是工艺流程的主体,从其上部装入的铁矿石燃料和溶剂向下运动,下部鼓入空气燃烧燃料,产生大量的还原性气体向上运动。
炉料经过加热、还原、熔化、造渣、渗碳、脱硫等一系列物理化学过程,最后生成液态炉渣和生铁。
组成除高炉本体外,还有上料系统、装料系统、送风系统、冷却系统、液压系统、回收煤气与除尘系统、喷吹系统、动力系统1—2 高炉炼铁有哪些技术经济指标?答案:综合入炉品位(%)炼铁金属收得率(%)生铁合格率(%)铁水含硅(%)铁水含硫(%)风温(℃)顶压(KPa)熟料比(%)球矿比(%)高炉利用系数(t/m3.d)综合焦比(Kg/t)入炉焦比(Kg/t)焦丁比(Kg/t)喷煤比(Kg/t)1—3 高炉生产有哪些特点?答案:一是长期连续生产。
高炉从开炉到大修停炉一直不停地连续运转,仅在设备检修或发生事故时才暂停生产(休风)。
高炉运行时,炉料不断地装入高炉,下部不断地鼓风,煤气不断地从炉顶排出并回收利用,生铁、炉渣不断地聚集在炉缸定时排出。
二是规模越来越大型化。
现在已有5000m3以上容积的高炉,日产生铁万吨以上,日消耗矿石近2万t,焦炭等燃料5kt。
三是机械化、自动化程度越来越高。
为了准确连续地完成每日成千上万吨原料及产品的装入和排放。
为了改善劳动条件、保证安全、提高劳动生产率,要求有较高的机械化和自动化水平。
四是生产的联合性。
从高炉炼铁本身来说,从上料到排放渣铁,从送风到煤气回收,各系统必须有机地协调联合工作。
从钢铁联合企业中炼铁的地位来说,炼铁也是非常重要的一环,高炉体风或减产会给整个联合企业的生产带来严重影响。
因此,高炉工作者要努力防止各种事故,保证联合生产的顺利进行。
1—5 高炉生产有哪些产品和副产品,各有何用途?答案:高炉冶炼主要产品是生铁,炉渣和高炉煤气是副产品。
(1)生铁。
按其成分和用途可分为三类:炼钢铁,铸造铁,铁合金。
(2)炉渣。
高炉冶炼的炉渣与铁水
汇报人:可编辑 2024-01-06
目录
CONTENTS
• 高炉冶炼的基本概念 • 炉渣的形成与作用 • 铁水的形成与成分 • 炉渣与铁水的关系 • 高炉冶炼的环保问题
01 高炉冶炼的基本概念
高炉冶炼的定义
定义
高炉冶炼是一种将铁矿石还原成 液态生铁的冶金过程,通过在高 温下与碳反应,将铁矿石中的铁 氧化物还原成铁。
铁水中还含有碳、硅 、锰、磷、硫等元素 ,这些元素来自铁矿 石和焦炭。
铁水的质量
铁水的质量主要取决于其成分, 特别是碳、磷、硫的含量。
碳含量过高会导致生铁脆性增加 ,磷含量过高会导致生铁冷脆性 增加,硫含量过高会导致生铁热
脆性增加。
因此,控制铁水中各元素的含量 对于生产高质量的生铁和钢材至
关重要。
高炉冶炼的过程
过程
高炉冶炼过程包括矿石的破碎、筛分、混合与运输,焦炭的准备与运输,以及 高炉的装料、送风、熔化、渣铁分离与生铁排出等步骤。
说明
该过程涉及多个环节和复杂的工艺控制,以确保最终生铁的质量和产量。
02 炉渣的形成与作用
炉渣的形成
炉渣的形成是由于矿石、溶剂 和燃料在高温下熔化后与熔融 的铁水相互作用而产生的。
在高炉冶炼过程中,矿石中的 脉石和焦炭中的灰分在高温下 熔化,与铁水中的杂质结合形 成炉渣。
炉渣的形成是一个复杂的物理 化学过程,涉及到多种化学反 应和相变。
炉渣的成分
炉渣的主要成分是硅酸盐矿物, 如硅酸钙和硅酸亚铁,以及铝酸
盐矿物。
此外,炉渣中还含有一定量的铁 、锰、钙、镁等元素,以及少量
的磷、硫等杂质元素。
04 炉渣与铁水的关系
炉渣对铁水的影响
- 1、下载文档前请自行甄别文档内容的完整性,平台不提供额外的编辑、内容补充、找答案等附加服务。
- 2、"仅部分预览"的文档,不可在线预览部分如存在完整性等问题,可反馈申请退款(可完整预览的文档不适用该条件!)。
- 3、如文档侵犯您的权益,请联系客服反馈,我们会尽快为您处理(人工客服工作时间:9:00-18:30)。
高炉冶炼工艺炉渣碱度是表征和决定炉渣物理化学性能的最重要的特性指数。
碱度用等碱性氧化物与酸性氧化物的重量百分比的比值来表示。
为简便起见通常均用,当Al2O3和MgO的含量高、波动大时,采用后两种表示方法。
渣中(CaO+MgO)<(SiO2+Al2O3)的渣叫酸性渣。
这种渣粘度大,凝固慢,通称长渣。
(CaO+MgO)>(SiO2+Al2O3)的渣叫碱性渣。
高碱渣凝固温度高,冷凝快,熔融时流动性好;但温度偏低时,析出固相,就变得粘稠。
这种渣也叫短渣。
(CaO+MgO):(SiO2+Al2O3)≈1.0的炉渣,凝固温度较低,流动性也较好。
在高炉中,为了保证炉况顺行和某些反应的顺利进行,炉渣在炉缸温度范围内的粘度最好不大于5泊,最高不宜超过25泊。
同时,粘度也不宜过低,过低时容易侵蚀炉衬,缩短高炉寿命。
高炉冶炼工艺 - 正文━━━━━━━━━━━━━━━━━━━━━━━━冶炼过程高炉中铁的还原高炉中其他元素的还原铁水中的碳高炉炉渣及渣铁反应炉料和煤气的运动高炉中的能量利用能量的来源和消耗高炉操作线图高炉炼铁车间的二次能源利用高炉冶炼的强化及节焦措施高炉强化高炉喷吹燃料高炉操作开炉;停炉大修;高炉休风;封炉;炉况顺行炉况失常和故障炉前操作━━━━━━━━━━━━━━━━━━━━━━━━冶炼过程高炉冶炼是把铁矿石还原成生铁的连续生产过程。
铁矿石、焦炭和熔剂等固体原料按规定配料比由炉顶装料装置分批送入高炉,并使炉喉料面保持一定的高度。
焦炭和矿石在炉内形成交替分层结构。
矿石料在下降过程中逐步被还原、熔化成铁和渣,聚集在炉缸中,定期从铁口、渣口放出。
鼓风机送出的冷空气在热风炉加热到800~1350℃以后,经风口连续而稳定地进入炉缸,热风使风口前的焦炭燃烧,产生2000℃以上的炽热还原性煤气。
上升的高温煤气流加热铁矿石和熔剂,使成为液态;并使铁矿石完成一系列物理化学变化,煤气流则逐渐冷却。
下降料柱与上升煤气流之间进行剧烈的传热、传质和传动量的过程。
下降炉料中的毛细水分当受热到100~200℃即蒸发,褐铁矿和某些脉石中的结晶水要到500~800℃才分解蒸发。
主要的熔剂石灰石和白云石,以及其他碳酸盐和硫酸盐,也在炉中受热分解。
石灰石中CaCO3和白云石中MgCO3的分解温度分别为900~1000℃和740~900℃。
铁矿石在高炉中于 400℃或稍低温度下开始还原。
部分氧化铁是在下部高温区先熔于炉渣,然后再从渣中还原出铁。
焦炭在高炉中不熔化,只是到风口前才燃烧气化,少部分焦炭在还原氧化物时气化成CO。
而矿石在部分还原并升温到1000~1100℃时就开始软化;到1350~1400℃时完全熔化;超过1400℃就滴落。
焦炭和矿石在下降过程中,一直保持交替分层的结构。
由于高炉中的逆流热交换,形成了温度分布不同的几个区域。
在图1中,①区是矿石与焦炭分层的干区,称块状带,没有液体;②区为由软熔层和焦炭夹层组成的软熔带,矿石开始软化到完全熔化;③区是液态渣、铁的滴落带,带内只有焦炭仍是固体;④风口前有一个袋形的焦炭回旋区,在这里,焦炭强烈地回旋和燃烧,是炉内热量和气体还原剂的主要产生地。
高炉冶炼工艺液态渣铁积聚于炉缸底部,由于比重不同,渣液浮于铁液之上,定时从炉缸放出。
铁水出炉温度一般为1400~1550℃,渣温比铁温一般高30~70℃。
煤气流沿高炉断面合理均匀地分布上升,能改善煤气与炉料之间的传热和传质过程,顺利地完成加热、还原铁矿石和熔化渣、铁等过程,达到高产、低耗、优质的要求。
高炉中铁的还原高炉中主要被还原的是铁的氧化物:Fe2O3(赤铁矿),Fe3O4(磁铁矿)和Fe1-y O(浮氏体,y从0.04到0.125)等。
每得到1000公斤金属铁,通过还原被除去的氧量为:赤铁矿429公斤,磁铁矿382公斤,浮氏体(按FeO计算)286公斤。
主要还原剂焦炭中的碳和鼓风中的氧燃烧生成的CO气体,以及鼓风和燃料在炉内反应生成的H2是高炉中的主要还原剂。
约从400℃开始,氧化铁逐步从高价铁还原成低价铁,一直到金属铁。
间接还原氧化铁由CO还原生成CO2或由H2还原生成H2O的过程。
还原顺序为: Fe2O3─→Fe3O4─→FeO─→Fe(低于570℃时,FeO不稳定,还原顺序为:Fe2O3─→Fe3O4─→Fe)。
从图2可看到各级氧化铁与气相的平衡关系。
高炉冶炼工艺氧化铁还原的主要还原反应为:3Fe2O3+CO─→2Fe3O4+CO2 +8870千卡Fe3O4+CO─→3FeO+CO2 -4990千卡FeO+CO─→Fe+CO2 +3250千卡以及 3Fe2O3+H2─→2Fe3O4+H2O -1000千卡Fe3O4+H2─→3FeO+H2O -14860千卡FeO+H2─→Fe+H2O -6620千卡H2和CO同时作为还原剂存在时,受水煤气反应的制约:H2+CO2─→H2O+CO -9870千卡注:式内反应热从工程习惯按公斤分子计。
直接还原在高温区(约 850℃开始)因有大量焦炭存在,生成的CO2和H2O立即与焦炭反应,转化成CO和H2:CO2+C─→2CO -39600千卡H2O+C─→H2+CO -29730千卡所以从全过程看,可认为是由碳素直接还原氧化铁生成CO和铁:FeO+C─→Fe+CO -36350千卡这种高温还原叫做直接还原。
因为直接还原比间接还原耗热大得多,所以在高炉内应尽可能提高中温区的间接还原率,以降低焦比和燃料比。
影响还原速度的因素气体还原铁矿石的速度受到许多因素的影响:矿石的性质(例如粒度,气孔度,气孔表面积),是难还原的磁铁矿还是易还原的褐铁矿,煤气的成分和流速以及还原温度等。
气-固还原过程包括以下基本环节:①还原气体通过矿粒表面的气膜向矿石表面扩散;②还原气体通过已还原金属层向矿石内部扩散;③金属铁-浮氏体两相界面上的化学反应;④还原气体产物通过已还原金属层向外扩散;⑤还原气体通过附面气膜向外扩散。
还原模式有两种:当矿石结构致密,还原金属层是自外表逐步向矿粒中心扩展,中心未反应的核心部分逐步缩小,可称为“未反应核”还原模式;如果矿石多孔疏松,内扩散十分容易,且粒径不大,则还原过程将同时在整个矿石内部环绕每一个氧化铁微晶进行氧化铁的气固还原反应,这是另一种模式。
整个反应速度决定于化学反应速度和扩散速度。
如果化学反应慢,称为反应处于“化学控制”;如果扩散慢,则称反应处于“扩散控制”。
温度提高,化学反应速度加快,气体的扩散速度也会增加,但增加的幅度较小。
一般说,温度低,矿石粒度小或气孔度大,气流速度高,还原趋向于化学控制范围;相反,温度高,矿石粒度大或者气孔度小,则趋向于扩散控制范围。
如果能出现扩散与化学反应的速度彼此较接近的情况,称还原处于“混合控制”。
还有一种情况,矿石的软熔温度低,当温度升高到使矿石软熔后,矿石的气孔度减小,还原速度反而可能减慢。
因为H2的扩散速度比CO高,H2的还原速度也高于CO。
当煤气中存在CO2或H2O分子时,CO和H2的有效浓度降低,将减慢CO和H2的还原速度。
从铁矿石的还原条件来看,应在矿石不软化的条件下,尽量保持高一些的还原温度,以加快还原速度。
对矿石则要求气孔度大,使还原过程不受扩散的限制;致密的铁矿石应适当减小粒度,这样不仅能使内扩散距离缩短,而且会使气-固相接触总面积增大,有利于还原过程(见冶金过程动力学)。
高炉中其他元素的还原进入高炉的矿石的脉石和焦炭灰分还含有其他一些氧化物(SiO2、Al2O3、CaO、MgO等)、硫化物(FeS2)和磷酸盐【Ca3(PO4)2】。
一些共生铁矿还含有锰、钛、铬、钒、铜、钴、镍、铌、砷、钾、钠等的含氧化合物和少量硫化物。
各种氧化物因化学稳定性不同,有的在高炉内全部还原,有的部分还原,有的完全不能还原,不还原的氧化物就进入炉渣。
硅的还原硅比铁难还原,要到高温区才能被碳还原出来,熔于铁水:(SiO2)+2【C】→【Si】+2CO -151696千卡耗热比铁的直接还原大得多。
式中圆括弧表示炉渣中的氧化物;方括弧表示铁水中的有关元素。
大部分生铁中的硅是焦炭灰分或渣中的SiO2,通过风口附近高温区(1700℃以上)时,先被还原生成气态SiO,SiO在上升过程中再被还原成硅并熔于铁水。
冶炼高硅生铁时,有一部分 SiO随煤气逸出炉外。
含硅愈高,挥发愈多;SiO冷却后又被氧化成极细的SiO2粉末,除增加能耗外,还会恶化炉料透气性和堵塞煤气管道。
为了炼得含硅较高的生铁或合金,宜配用碱度较低的炉渣,以利于酸性SiO2的还原。
由于反应热耗大,必须维持较高的炉温,生铁含硅愈多,燃料消耗(焦比)和成本也愈大。
锰的还原锰矿中的化合物MnO2、Mn3O4、Mn2O3、MnCO3等都很容易被CO还原成MnO,但MnO只能从炉渣中被碳直接还原并熔于铁水:(MnO)+【C】→【Mn】+CO -68640千卡其单位耗热低于硅,但高于铁的直接还原。
MnO是弱碱性,冶炼含锰高的铁,宜采用碱性较高的炉渣,以提高渣中MnO活度,加快还原。
由于需维持较高的炉温,反应热耗又多,生产高锰生铁的燃料消耗和成本也比较高。
其他元素的还原以3CaO·P2O5或3FeO·P2O5形态进入高炉的磷,以及以氧化物或硫化物形态存在的铜、镍、钴、砷、铅等全部被还原。
钒、铌、铬等的氧化物一般可被还原75~80%。
二氧化钛在高炉内只有少量被还原。
钾、钠、锌等金属的沸点低,其化合物在高炉下部高温区被还原成金属后立即挥发,一部分随煤气逸出炉外,一部分又被氧化后沉积在上部炉料表面,随炉料再下降到高温区。
再还原,再挥发,再沉积,循环积累,造成以下严重危害:破坏矿石和焦炭的强度和炉料的透气性;沉积在炉衬中破坏耐火材料,引起结瘤。
因此,对高炉原料中这些元素的含量要有一定的限制,必要时,可以定期降低炉渣碱度,使K2O和Na2O更多地进入炉渣,排出炉外,减轻危害。
包头铁矿石含K2O、Na2O和CaF2较多,影响炉况顺行,现已找到解决途径。
钒、铜、镍、钴、铌等是宝贵的合金元素,它们在铁矿石中如达到一定含量,应考虑回收利用。
中国攀枝花的钒钛磁铁矿和包头的含铌铁矿石,在炼铁过程中得到含钒和含铌的生铁,在进一步处理和回收钒、铌上,取得良好的成果。
铁水中的碳因为在高炉内还会出现还原和渗碳到Fe3C的反应:3Fe+2CO→Fe3C+CO2FeO(MnO,SiO2)+C→Fe(Mn,Si)+CO3Fe+C→Fe3C所以高炉生铁含碳高,其含量主要决定于铁水的成分。
凡能生成碳化物并溶于铁水的元素如锰、钒、铬、铌等能使铁水含碳增加;凡能促使铁水中碳化物分解的元素如硅、磷、硫等会阻碍铁水渗碳。
普通生铁含碳4%左右。
铁水溶解某些碳化物达到饱和后,剩余的碳化物便留在炉渣中,例如炼高硅生铁时的SiC,在炉料含TiO2较多时形成的TiC等。