Mastercam_铣削详细教程
Mastercam X7数控加工立体化教程第6章 二维铣削加工
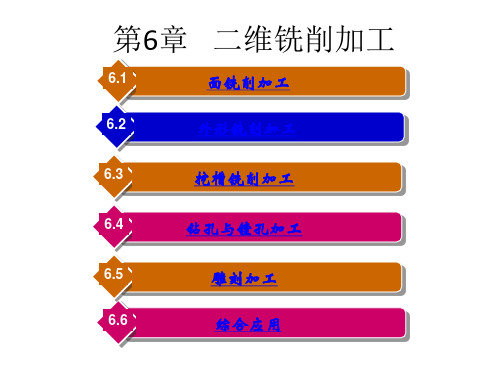
5. 6. 7. 8.
绘制圆弧。 创建图形旋转特征。 绘制矩形。 绘制点。
9. 10. 11. 12.
绘制矩形。 设置毛坯。 设置刀具。 创建面铣削加工特征。
13. 创建外形铣削加工特征。 14. 创建挖槽加工特征。 15. 创建钻孔加工特征。
6.6.2 综合应用2──加工古典砚台
古典砚台是现代家居中一件装饰品,其加工方法综合了挖槽加工、 创建文字以及雕刻文字等,可以通过此案例的练习提高对二维铣削加工 方法的综合应用能力。
第6章 二维铣削加工
6.1 6.2
面铣削加工 外形铣削加工 挖槽铣削加工 钻孔与镗孔加工 雕刻加工 综合应用
6.3
6.4
6.5 6.6
6.1 面铣削加工
6.1.1 重点知识讲解
一、切削方式 在进行平面铣削加工时,可以根据需要选取不同的铣削方式。 在【2D刀具路径-平面铣削】对话框中的【类型】下拉列表中选择不 同的铣削方式。
1. 2. 3.
选择加工机床。 设置刀具库。 设置毛坯。
4. 创建面铣削刀具路径。
5.创建挖槽铣削刀具路径。
6.仿真模拟。
6.4 钻孔与镗孔加工
6.4.1 重点知识讲解
一、操作步骤 创建钻孔数控程序的操作步骤,主要包括绘制轮廓图形、定义机床 类型、设置加工环境以及定义刀具参数等。
二、钻孔点的选取 在钻孔时选取定位点作为孔的圆心,可以是绘图区中的已有点,也 可以构建一定排列方式的点
6.5.2 实战演练──加工艺术品
大树轮廓是艺术家通过手绘而形成线条,然后通过创建各种雕刻加 工刀具路径,从而雕刻出此艺术品,在市场中广受欢迎,价格也较为昂 贵。
1. 2. 3.
选择加工机床。 设置刀具库。 设置毛坯。
MasterCAM外形铣削主要参数的设置方法

MasterCAM外形铣削主要参数的设置方法前言MasterCAM是一款常用的CAM软件,具有强大的功能及灵活的操作性,被广泛应用于机械制造行业。
在进行外形铣削时,合理设置参数是非常重要的,这样可以提高加工效率,保证加工质量。
本文将介绍MasterCAM外形铣削的主要参数设置方法及其影响。
外形铣削的基本概念外形铣削是制造业中常见的一种加工方式。
其基本原理是通过旋转的铣刀在工件表面上进行铣削,移除必要的材料来得到所需的形状。
在MasterCAM中,外形铣削是通过面铣削操作完成的。
在进行外形铣削时,需要考虑铣削方向、铣削深度、刀具直径以及进给速度等参数的设置,以确保加工效果。
外形铣削参数的设置方法铣削方向铣削方向是外形铣削的一个重要参数。
在MasterCAM中,铣削方向分为水平铣削、垂直铣削和多轴旋转三种方式。
选择不同的铣削方向对加工效果有很大的影响。
•水平铣削:水平铣削适用于平整的工件表面,切削刃与工件平面垂直。
这种方式可以使刀具的切入力最小,因此切削效果好,同时也可以提高加工精度和表面平整度。
•垂直铣削:垂直铣削适用于工件边缘或轮廓,铣刀切削方向垂直于工件表面。
这种方式可以保证切削力的均匀分布,同时也有利于加工较深的凸起形状。
•多轴旋转:在MasterCAM中,可以使用多轴旋转的方式进行铣削。
该方式可以实现任意角度的铣削,适用于加工形状较为复杂的工件。
铣削深度铣削深度表示铣刀在一次铣削过程中所能切削的最大深度。
通常情况下,铣削深度应该尽可能大,以提高加工效率。
但是,在考虑铣削深度时也需要考虑切削力和表面质量的影响。
如果铣削深度过大,可能会导致刀具过度磨损、加工精度下降和表面效果下降等问题。
刀具直径刀具直径是外形铣削的一个重要参数,通常情况下,刀具直径越大,铣削效率越高,加工精度越高。
但是,在选择刀具直径时也需要考虑工件的几何形状以及加工深度和切削质量等因素。
进给速度进给速度是铣削过程中切削刃移动的速度,是外形铣削的另一重要参数。
Mastercam铣削粗加工
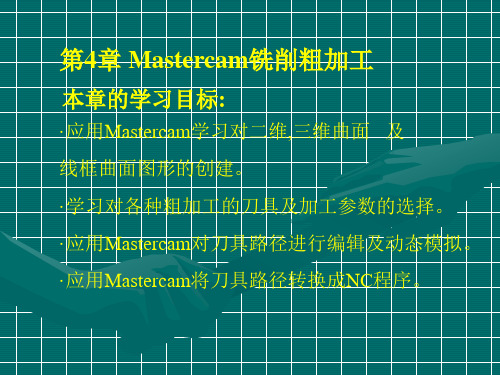
图4.47平行铣削粗加工参数
在图4.47中单击间隙设定,出现间隙设置 对话框如图4.48,设置参数:检查刀具在间 隙过切情形
检查提刀时之过切情形, 参数设置后按图 4.48的O确定按钮,出现铣削路径如图4.50 所示。
图4.48间隙设置对话框
6)加工模拟 单击主功能表的N公用管理/B路径模拟, 弹出如图4.49所示菜单。
图4.38层别对话框
(2)将点移到第10层: 在主功能表中 单击S莹幕/V改变层别,弹出对话框如图 4.39所示,选移动,按O确定。在左边菜单 选/A所有的/P点/D执行,所有的点移到第 十层。
图4.39改变层别对话框
(3)换回第1层:单击主功能表中的层 别:10,出现层别对话框如图4.38所示, 在层别输入1,用鼠标点击取消第10层的 √,如图4.40所示,按O确定,图形上就 不出现点。
11) 在主功能表中设置构图面: S
视角:I ,Z:-100.00。在主功能表中单击 C绘图/S曲线/M手动输入,捕捉10)输入 的四个点,在左侧面生成第三条曲线。如 图4.37所示。
图4.37生成第三条曲线
12)消除点:
(1)在主功能表中单击层别:1,出现层别 对话框如图4.38所示,在层别输入10,选 已使用,按O确定,换成第10层为当前层。
(3)换回第1层:单击主功能表中的层别10, 出现层别对话框如图4.40所示,在层别输入1, 用鼠标点击取消第10层的√,如图4.40所示, 按O确定, 结果如图4.43所示。
图4.43隐藏线段及点
(16) 保存文件: 在主功能表中单击F档 案/S存档,输入文件名:Parallel-R.MC8。
5)构建点:
为了在侧面及中心面上绘制曲线,必须 先设置一些点,通过点生成曲线。
Mastercam课件——第9章 三维铣削加工

• (6) 从刀具库中选择直径8mm的球头铣刀, 并设置刀具参数。
Mastercam
19
设置加工刀具
Mastercam
20
• (7) 单击“曲面粗加工-平行加工”对话框的“曲面
• 单击“切削深度”按钮,打开 “切削 深度”对话框,在该对话框中设置粗加 工的切削深度,可以选择“绝对坐标” 或“增量坐标”方式来设置切削深度。
Mastercam
13
7. 刀间距
• 单击“刀间距”按钮,打开用来设置刀具在不同间距 时的运动方式的对话框。“允许的间隙”选项组用来 设置允许间距;“位移小于允许间隙时,不提刀”选 项组用于设置当移动量小于设置的允许间距时刀具的 移动方式;“位移大于允许间隙时,提刀至安全高度” 选项组用于设置当移动量大于设置的允许间距时刀具 的移动方式;“切弧的半径”输入框用于输入在边界 处刀具路径延伸切弧的半径;“切弧的扫掠角度”输 入框用于输入在边界处刀具路径延伸切弧的角度。
按钮,关闭“工作设定”对话框。
Mastercam
16
曲面模型
Mastercam
17
工件外形设置
Mastercam
18
• (3) 在主菜单中顺序选择“刀具路径” 子菜单中的“曲面加工→粗加工→平行 加工→凸” 选项。
• (4) 在打开的选取曲面子菜单中顺序选择 “全部→曲面→执行” 选项,选取所有曲面。
Mastercam
3
3.多轴加工路径 • 5轴曲线加工: Curve5ax • 5轴钻孔: Drills5ax • 5轴侧刃铣削: Swarf5ax • 5轴流线加工: Flow5ax • 4轴旋转加工: Rotary4ax • 4.线架加工路径 • 直纹加工: Ruled • 旋转加工:Revolution • 扫掠加工: Swept 2D • 3D扫掠加工: Swept 3D • 昆氏加工: Coons • 举升加工: Loft
基于MasterCAM的复杂零件铣削加工

基于MasterCAM的复杂零件铣削加工1. 简介铣削加工是制造业中常用的加工方法之一,它利用刀具通过转动来切削工件,以达到加工目的。
在现代生产中,铣削加工已成为一种广泛应用的机械加工方法,新式工艺不断涌现,其中之一就是MasterCAM软件。
MasterCAM软件是一款常用的计算机辅助制造(CAM)软件,它可以帮助加工人员快速设计复杂的机器零件,相关的加工路径和工艺,并使其能够自动化运行加工过程。
在本文中,我们将会详细介绍如何运用MasterCAM软件进行复杂零件铣削加工。
2. MasterCAM软件的功能介绍MasterCAM软件是一款多功能的CAD/CAM软件,功能强大,操作简易。
其核心功能如下:2.1 CAD功能MasterCAM软件可以提供CAD设计功能,帮助操作人员快速进行机器零件的三维设计,包括底部功能和缩略图预览功能等,为加工提供直观的参考和便利。
2.2 CAM功能MasterCAM软件的CAM功能则非常强大,它能够帮助操作人员生成铣削加工程序。
MasterCAM可以在多个坐标系中生成加工路径,并支持多轴加工,对于复杂的工件进行加工时,MasterCAM无疑是首选之一。
3. 铣削加工流程在进行复杂的零件铣削加工时,我们需要做好以下几个步骤:3.1 建立工件模型首先,我们需要建立一个精确的工件模型来设计铣削加工路径。
MasterCAM提供了多种建模方式,包括实体建模和面建模。
我们可以根据需要使用不同的建模方式,以便于生成更加真实的工件模型。
在进行零件建模时,我们需要考虑加工后零件的形状和尺寸,以及可能存在的加工难度和风险等因素,这些因素都将影响我们对加工路径的设定。
3.2 设计刀具路径接下来,我们需要使用MasterCAM软件生成铣削加工路径。
MasterCAM软件可以选择多种操作方式,如拉入、绕过、切入/切出和掠过等,可以根据实际情况选择合适的操作方式。
在生成铣削加工路径时,需要确定好加工深度、切削速度、进给速度、刀具直径等参数,以保证工件的质量和加工效率。
MasterCAM铣削编程综合实例
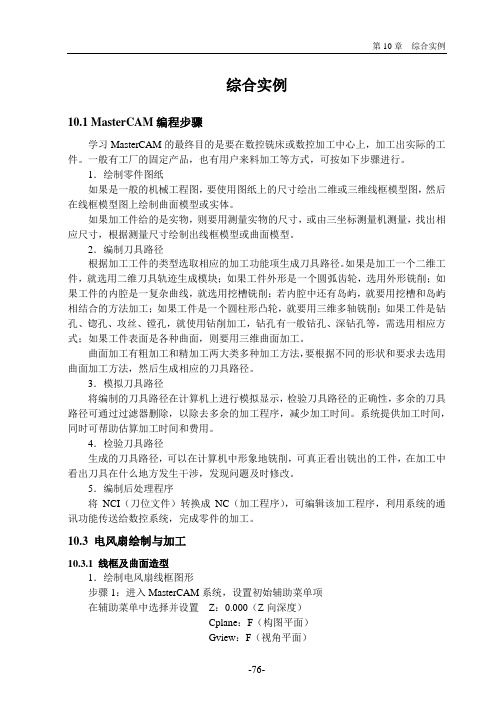
综合实例10.1 MasterCAM编程步骤学习MasterCAM的最终目的是要在数控铣床或数控加工中心上,加工出实际的工件。
一般有工厂的固定产品,也有用户来料加工等方式,可按如下步骤进行。
1.绘制零件图纸如果是一般的机械工程图,要使用图纸上的尺寸绘出二维或三维线框模型图,然后在线框模型图上绘制曲面模型或实体。
如果加工件给的是实物,则要用测量实物的尺寸,或由三坐标测量机测量,找出相应尺寸,根据测量尺寸绘制出线框模型或曲面模型。
2.编制刀具路径根据加工工件的类型选取相应的加工功能项生成刀具路径。
如果是加工一个二维工件,就选用二维刀具轨迹生成模块;如果工件外形是一个圆弧齿轮,选用外形铣削;如果工件的内腔是一复杂曲线,就选用挖槽铣削;若内腔中还有岛屿,就要用挖槽和岛屿相结合的方法加工;如果工件是一个圆柱形凸轮,就要用三维多轴铣削;如果工件是钻孔、锪孔、攻丝、镗孔,就使用钻削加工,钻孔有一般钻孔、深钻孔等,需选用相应方式;如果工件表面是各种曲面,则要用三维曲面加工。
曲面加工有粗加工和精加工两大类多种加工方法,要根据不同的形状和要求去选用曲面加工方法,然后生成相应的刀具路径。
3.模拟刀具路径将编制的刀具路径在计算机上进行模拟显示,检验刀具路径的正确性,多余的刀具路径可通过过滤器删除,以除去多余的加工程序,减少加工时间。
系统提供加工时间,同时可帮助估算加工时间和费用。
4.检验刀具路径生成的刀具路径,可以在计算机中形象地铣削,可真正看出铣出的工件,在加工中看出刀具在什么地方发生干涉,发现问题及时修改。
5.编制后处理程序将NCI(刀位文件)转换成NC(加工程序),可编辑该加工程序,利用系统的通讯功能传送给数控系统,完成零件的加工。
10.3 电风扇绘制与加工10.3.1 线框及曲面造型1.绘制电风扇线框图形步骤1:进入MasterCAM系统,设置初始辅助菜单项在辅助菜单中选择并设置Z:0.000(Z向深度)Cplane:F(构图平面)Gview:F(视角平面)步骤2:绘制直线⑴选择Main Menu/Create/Line/Multi在提示区输入Specify endpoint 1:0,10 ↙Specify endpoint 2:6.25,10 ↙Specify endpoint 3:6.25,0 ↙Specify endpoint 4:6.25,0 ↙按ESC键,结束画线操作。
第8讲 MasterCAM_X5_外形铣削和平面铣削

一、 切削方式 在进行面铣削加工时,可以根据需要选取不同的铣削方式。在【平面加工参 数】选项卡的【切削方式】下拉列表中选择不同的铣削方式,如图8-2所示。 • 【双向】:刀具在加工中可以往复走刀,来回均切削,如图8-2(a)所示。
•
• •
【单向-顺铣】:刀具仅沿一个方向走刀,进时切削,回时空走,如图8-2(b )所示。顺铣是指铣刀与工件接触部分的旋转方向与工件进给方向相同。 【单向-逆铣】:刀具仅沿一个方向走刀,进时切削,回时空走,如图8-2(c )所示。逆铣是指铣刀与工件接触部分的旋转方向与工件进给方向相反。 【一刀式】:仅进行一次铣削,刀具路径的位置为工件的中心位置。采用这 种铣削方式时刀具的直径必须大于工件表面的宽度,如图8-2(d)所示。
8 外形铣削和平面铣削
本章学习目标
掌握平面铣削的基本设置和应用
掌握外形铣削的基本设置和应用
本章大纲
8.1 平面铣削 8.2 外形铣削 8.3 课后练习
8.1
平面铣削
平面铣削加工模组的加工方式为平面加工,主要用于加工平面, 提高工件的平面度、平行度以及降低工件表面粗糙度。
8.1.1
知识点讲解
执行命令【刀具路径】/【面 铣】,弹出【串连选项】对话框, 采用串连方式对绘图区中的几何模 型进行串连操作,确认后系统弹出 【面铣刀】对话框,进入面铣削环 境,如图8-1所示。 在设置面铣削参数时,除了要 设置一组刀具、材料等共同参数外, 还要设置一组其特有的加工参数。
(5)
图8-12 选择刀具类型
图8-13 设置刀具尺寸
4. (1)
(2)
设置加工参数。 返回【面铣刀】对话框进入【平面加工参数】选项卡,设置平面加工 参数,如图8-14所示。 单击 按钮,设置深度分层切削参数,如图8-15所示,然后单 击 按钮。
MasterCAM车、铣加工步骤

**大学答题纸(2009—2010学年第二学期)课号:093E03A02 课程名称:数控技术与编程改卷教师:学号:姓名:得分:铣削加工连杆零件图为:一、图形绘制1、选择菜单栏中的File/New命令新建文件。
2、单击顶部工具栏中的俯视构图面按钮,Set planes to TOP relative to your WCS。
3、单击顶部工具栏中的俯视图按钮。
4、选择菜单栏中的【Create】/【Arc】/【Create Arc Polar】极坐标圆弧命令。
5、按照零件图上尺寸确定各圆弧,得到图1:图16、选择菜单栏中的【Create】/【Line】/【Create Line Endpoint】两点绘线命令,并按照零件图上尺寸确定各直线,得到图2:图27、选择菜单栏中的【Edit】/【Trim/Break】/【Trim/Break】命令,对多余线进行打断。
8、选择菜单栏中的【Create】/【Fillet】/【Fillet Entities】倒圆角命令,按照零件尺寸设置各倒圆角半径,得到图3:图39、选择菜单栏中的【Xform】/【Xform Mirror】镜像命令,得到图4:图4二、规划挖槽加工刀具路径1、单击顶部工具栏中的俯视构图面按钮,Set planes to TOP relative to your WCS。
2、选择菜单栏中的【Toolpaths】/【Pocket Toolpath】挖槽加工命令。
3、系统提示选择串连外形,点击如图5所示箭头处,箭头产生,点击确定按钮,结束串连外形选择。
图54、刀具选择:从刀具库中选择φ10平铣刀,并设置如图6所示的刀具参数。
图65、选择如图7所示挖槽参数选项卡【Pocketing parameters】设置相关参数。
图76、单击深度分层按钮,设置如图8所示深度分层参数,单击确定按钮。
图87、选择如图9所示粗加工/精加工参数选项卡【Roughing/Finishing parameters】,设置相关参数。
- 1、下载文档前请自行甄别文档内容的完整性,平台不提供额外的编辑、内容补充、找答案等附加服务。
- 2、"仅部分预览"的文档,不可在线预览部分如存在完整性等问题,可反馈申请退款(可完整预览的文档不适用该条件!)。
- 3、如文档侵犯您的权益,请联系客服反馈,我们会尽快为您处理(人工客服工作时间:9:00-18:30)。
二维刀具路径4.1加工简介CAM则主要是根据工件的几何外形设置相关的切削加工数据并生成刀具路径,刀具路径实际上就是工艺数据文件(NCI),它包含了一系列刀具运动轨迹以及加工信息,如进刀量、主轴转速、冷却液控制指令等。
再由后处理器将NCI文件转换为CNC控制器可以解读NC码,通过介质传送到加工机械就可以加工出所需的零件。
4.1.1任务1 加工如图4-1所示的实体,介绍数控加工的一般步骤图 4-1 凹模零件步骤1新建文件新建如图4-1所示的凹模零件。
步骤2进入加工模块在主菜单上单击“刀具路径”,如图4-2所示,弹出刀具路径菜单,如图4-3所示。
图 4-2 主菜单 图4-3 “刀具路径”菜单 步骤3设置毛坯单击如图4-3所示的“刀具路径”菜单中的“工作设定”,弹出“工作设定”对话框,如图4-4所示,单击“B使用边界盒”,弹出“边界盒”对话框,如图4-5所示,单击“确定”按钮,返回“工作设定”对话框,将“工件原点”Z设为21,将工件高度Z设置为21,如图4-6所示,单击“确定”返回主菜单,绘图区的工件上出现红色的虚线框,如图4-7所示。
图 4-4 “工作设定”对话框图 4-5 “边界盒”对话框图 4-6 “毛坯参数”设置图 4-7 毛坯设置 图 4-8 “面铣选择”菜单 步骤4选择加工类型单击如图4-3所示的“刀具路径”菜单中的“面铣”,弹出“面铣选择”菜单,如图4-8所示,单击“执行”,弹出面铣对话框,如图4-9所示。
图 4-9 面铣对话框步骤5 设置刀具将鼠标放在“面铣”对话框的空白处,单击鼠标右键,弹出刀具快捷菜单,如图4-10所示,选择快捷菜单中的“从刀具库中选取刀具”,弹出“刀具管理员”对话框,选择直径为10的平刀,如图4-11所示,单击“确定”,“面铣”对话框中出现了第一把刀,主轴转速,进给率设置,如图4-12所示。
图 4-10 “刀具”快捷菜单提示:直接单击“执行”,则加工整个零件的上表面,如果选择某个串连图形,则加工选择的图形上表面。
图 4-11 “刀具管理员”菜单图 4-12 选择直径10的平刀步骤6面铣参数设置单击“面铣”“对话框中的“面铣加工参数”,弹出“面铣加工参数”对话框, “要加工的表面”设为毛坏的高度21,“深度”设为工件表面的高度20,各参数设置如图4-13所示。
:安全高度是指刀具于每一个刀具路径开始进入和退出终了时的高度。
通常,刀具会停留在安全高度,而在此高度之上刀具可以在任何位置平移。
步骤7生成刀轨单击“面铣”对话框中的“确定”,完成面铣刀具路径的设置,如图4-14所示。
图 4-14 面铣刀具路径步骤8仿真加工单击主菜单中的“操作管理”,弹出“操作管理”对话框,如图4-15所示。
单击“实体验证”弹出实体验证窗口,如图4-16所示,单击“持续执行”按钮,播放实体仿真加工加工,加工效果如图4-17所示。
图 4-15 “操作管理”对话框图 4-16 实体验证窗口图 4--17 实体验证结果4.2.2 任务二完成图4-18 所示的零件加工。
图4-18 零件图步骤1新建文件新建如图4-18所示的凹模零件。
步骤2进入加工模块在主菜单上单击“刀具路径”,如图4-19所示,弹出刀具路径菜单,如图4-20所示。
图 4-19 主菜单 图4-20“刀具路径”菜单 步骤3设置毛坯单击如图4-18所示的“刀具路径”菜单中的“工作设定”,弹出“工作设定”对话框,如图4-21所示,单击“B使用边界盒”,弹出“边界盒”对话框,如图4-22所示,单击“确定”按钮,返回“工作设定”对话框,将“工件原点”Z设为11,将工件高度Z设置为11,如图4-23所示,单击“确定”返回主菜单,绘图区的工件上出现红色的虚线框,如图4-24所示。
图 4-21 工作设定”对话框 图 4-22“边界盒”对话框图 4-23 “毛坯参数”设置 图 4-24 毛坯设置 步骤4选择加工类型单击如图4-20所示的“刀具路径”菜单中的“面铣”,弹出“面铣选择”菜单,如图4-25所示,单击“执行”,弹出面铣对话框,如图4-26所示。
图 4-25 “面铣选择”菜单图 4-26 面铣对话框步骤5设置面铣刀具将鼠标放在“面铣”对话框的空白处,单击鼠标右键,弹出刀具快捷菜单,如图4-27所示,选择快捷菜单中的“从刀具库中选取刀具”,弹出“刀具管理员”对话框,选择直径为10的平刀,如图4-28所示,单击“确定”,“面铣”对话框中出现了第一把刀,主轴转速,进给率设置,如图4-29所示。
图4-27“刀具”快捷菜单图 4--28 “刀具管理员”菜单图 4--29 选择直径10的平刀步骤6面铣参数设置单击“面铣”“对话框中的“面铣加工参数”,弹出“面铣加工参数”对话框, “要加工的表面”设为毛坏的高度11,“深度”设为工件表面的高度10,各参数设置如图4-30所示。
图4-30 面铣加工参数对话框步骤7生成刀轨单击“面铣”对话框中的“确定”,完成面铣刀具路径的设置,如图4-31所示。
图 4--31 面铣刀具路径步骤8面铣仿真加工单击主菜单中的“操作管理”,弹出“操作管理”对话框,单击“实体验证”弹出实体验证窗口,单击“持续执行”按钮,播放实体仿真加工加工,加工效果如图4-32所示。
图 4--32 实体验证结果步骤9选择加工类型单击如图4-20所示的“刀具路径”菜单中的“外形铣削”,弹出“外形铣削”选择菜单,如图4-33所示,单击“实体”,弹出“实体选择”菜单,将实体边界设为“Y”,其它设为“N”,如图4-34所示,按顺序选择五棱柱上表面的五边形,如图3-35所示。
图 4-33 “面铣选择”菜单 图 4-34 “实体选择”菜单图 4-35 选择五边形五边形选择完成后,连续单击两次“执行”弹出“外形铣削”对话框,如图4-36所示,从刀具库中选取直径为16的平刀,主轴转速,进给率设置,如图4-37所示。
图4-36“刀具”快捷菜单图 4--37 选择直径16的平刀单击“外形铣削”“对话框中的“外形铣削参数”,弹出“外形加工参数”对话框, “要加工的表面”设为零件的高度10,“深度”设为五棱柱的底面高度5,高度参数设置如图4-38所示。
图 4-38 外形铣削高度参数设置在“XY 分次铣削”前面的小框中打“”,然后单击“XY 分次铣削”,弹出“XY 平面分次铣削设定”对话框,将次数设为“4”,间距设为“8.0”,其它设置如图4-39所示。
图4-39 外形铣削高度参数设置在“Z 轴分层铣削”前面的小框中打“”,然后单击“Z轴分层铣削”,弹出“Z轴分层铣深设定”对话框,将“最大粗切削量”设置为2.0,其它设置如图4-40所示,单击“确定”,返回“外形铣削”对话框,在“进/退刀向量”前面的小框中打“”,如图4-41所示。
图4-40 Z轴分层铣深参数设置图 4-41 外形铣削参数设置步骤12 生成刀轨单击“外形铣削”对话框的“确定”,完成外形铣削刀具路径的设置,如图4-42所示。
图 4--42 外形铣削刀具路径步骤13外形铣削仿真加工单击主菜单中的“操作管理”,弹出“操作管理”对话框,如图4-43所示,单击“实体验证”弹出实体验证窗口,单击“持续执行”按钮,播放实体仿真加工加工,加工效果如图4-44所示。
4-43 操作管理对话框4-44 零件仿真加工步骤14选择加工类型单击如图4-20所示的“刀具路径”菜单中的“挖槽”,弹出“挖槽”选择菜单,如图4-33所示,单击“实体”,弹出“实体选择”菜单,将实体边界设为“Y”,其它设为“N”,如图4-34所示,按选择圆柱孔上表面的圆形,如图4-45所示。
图 4-45 选择圆形步骤15设置挖槽刀具五边形选择完成后,连续单击两次“执行”弹出“挖槽”对话框,从刀具库中选择直径为20的圆鼻刀,其它参数设置,如图4-46所示。
图4-46 选择直径10的圆鼻刀对着圆鼻刀单击鼠标右键,弹出“定义刀具”对话框,将“刀角半径”设为2,其它参数不变,如图4-47所示。
单击“确定”退出“定义刀具”对话框。
图4-47 刀角半径的设置步骤16 挖槽参数设置单击“挖槽”“对话框中的“挖槽参数”,弹出“挖槽参数”对话框, “要加工的表面”设为零件的高度10,“深度”设为圆柱孔底面高度5,在“Z轴分层铣削”前面的小框中打“”,然后单击“Z轴分层铣削”,弹出“Z轴分层铣深设定”对话框,将“最大粗切削量”设置为2.0,其它设置如图4-48所示,单击“确定”,返回“挖槽”对话框,单击“挖槽”对话框的的选项卡“粗铣/精铣参数”选项卡,弹出“粗铣/精铣对数”对话框,“切削方式”选择螺旋切削,勾中“螺旋式下刀”,其它参数不变,如图4-49所示。
图4-48 Z轴分层铣深参数设置图4-49 粗铣/精铣参数对话框步骤17生成刀轨单击“挖槽”对话框的“确定”,完成挖槽铣削刀具路径的设置,如图4-50所示。
图 4--50 挖槽刀具路径单击主菜单中的“操作管理”,弹出“操作管理”对话框,如图4-51所示,单击“实体验证”弹出实体验证窗口,单击“持续执行”按钮,播放实体仿真加工加工,加工效果如图4-52所示。
4-51 操作管理对话框4-51 挖槽实体验证单击如图4-20所示的“刀具路径”菜单中的“钻孔”,弹出“钻孔”选择菜单,如图4-52所示,单击“手动”,弹出“抓点方式”菜单,如图4-53所示,单击“圆心点”,在图形区选择圆柱孔上表面的圆形,即捕捉到圆孔中心,如图4-45所示。
4-52 钻孔选择菜单4-53 抓点方式菜单图 4-54 捕捉到圆孔中心步骤20设置钻孔刀具孔中心选择完成后,连续单击两次“执行”弹出“钻孔”对话框,从刀具库中选择直径为12的钻头,其它参数设置如图4-55所示。
图4-55 选择直径12的钻头步骤21钻孔参数设置单击“钻孔”“对话框中的“Simple drill-no peck”,弹出“Simple drill-no peck”对话框, “要加工的表面”设为零件的高度5,“深度”设为0,在“刀尖补偿”前面的小框中打“”,其它参数使用默认,如图4-56所示。
图4-56 Simple drill-no peck设置步骤22生成刀轨单击“钻孔”对话框的“确定”,完成外钻孔刀具路径的设置,如图4-57所示。
图 4--57 钻孔刀具路径步骤23钻孔仿真加工单击主菜单中的“操作管理”,弹出“操作管理”对话框,如图4-58所示,单击“实体验证”弹出实体验证窗口,单击“持续执行”按钮,播放实体仿真加工加工,加工效果如图4-59所示。
4-58 操作管理对话框4-59 钻孔实体验证4.5.1 任务三加工如图4-85所示的零件。
图4--60 零件步骤1新建文件新建如图4-60所示的凹模零件。
步骤2进入加工模块在主菜单上单击“刀具路径”,如图4-19所示,弹出刀具路径菜单,如图4-20所示。