德国JRT太阳能电池全自动丝网印刷设备
太阳能电池制造中的丝网印刷技术概述

太阳能电池制造中的丝网印刷技术概述摘要太阳能电池连接技术的最重要的部分就在硅衬底金属化制造。
这个方法是一项先进的印刷工艺,这个技术能够在很大程度上决定太阳能电池的能量转换效率。
这项工艺被大规模用于太阳能电池的批量化生产,是第三代太阳能电池制造过程中最重要的环节。
关键词丝网印刷;晶体硅;电极;质量控制太阳能电池是利用光电效应将光能转化成电能的装置。
它是太阳能发电的基础和核心。
目前,光伏电池生产有二个主要难题。
第一,怎么增加太阳能电池的转换效率,以加大电池板组件一平方米范围内的发电量。
第二,在加大投入成本之前,怎样通过现有技术使太阳能电池的制造力得到加强。
丝网印刷技术在制造太阳能电池片背电场和正电极的生产中越来越成熟运用,逐渐变成了现在光伏电池生产的最为流行的技术。
1 太阳能电池丝网印刷1.1 丝网印刷在光伏电池制造过程中的位置制造晶体硅光伏电池的过程有印刷背电极、铝背场和正电极。
电极印刷的好坏很大程度上决定了电池片性能的好坏。
所以它是光伏电池制造过程的一个主要环节。
利用丝网印刷技术,在硅片上印刷一种化学活性很高的金屬浆料,通过烘干将金属浆料固化,然后在高温状态下快速烧结。
在具有化学活性的金属浆料作用下,金属和硅晶体生成了一个合金层,从而形成良好的接触以及铝背场。
1.2 丝网印刷技术丝网印刷是采用压印的方式将预定的图形印刷在基板上,该设备由电池背面银铝浆印刷、电池背面铝浆印刷和电池正面银浆印刷三部分组成。
其工作原理为:利用丝网图形部分网孔透过浆料,用刮刀在丝网的浆料部位施加一定压力,同时朝丝网另一端移动。
浆料在移动中被刮刀从图形部分的网孔中挤压到基片上。
由于浆料的黏性作用使印迹固着在一定范围内,印刷中刮板始终与丝网印版和基片呈线性接触,接触线随刮刀移动而移动,从而完成印刷行程,得到印制的丝网图形。
丝网印刷技术,是把包含金属的混合导电浆料通过网状孔压入,压在晶体硅片上生成新的电路和电极,并由光伏电池衍生出光电子。
太阳能电池片丝网印刷

烘干和烧结
烘干和烧结的目的
烘干和烧结是为了使印刷在硅片表面的油墨或涂料干燥并 固定在适当的位置,同时使油墨或涂料发生必要的物理和 化学变化。
烘干和烧结工艺
烘干和烧结工艺应根据油墨或涂料的特性和太阳能电池片 的材料特性进行合理控制,包括温度、时间和气氛等参数。
烘干和烧结设备
烘干和烧结设备可以采用隧道式烘干机或烘箱,设备应具 备温度控制和时间控制功能,以确保烘干和烧结效果的一 致性和稳定性。
丝网质量
01
丝网的材质、目数、开口尺寸等参数直接影响印刷质量,选用
高质量的丝网是保证印刷精度的前提。
印刷参数
02
印刷压力、速度、刮刀角度和硬度等参数的设置对印刷线条的
宽度、高度和均匀性有触变性、干燥速度等性能参数对印刷效果和固化
过程有直接影响。
质量检测方法
目视检测
检测与修复
检测目的
检测与修复是为了确保太阳能电池片丝网印刷的质量和可靠性,及 时发现并处理存在的缺陷和问题。
检测方法
检测方法包括目视检测、自动光学检测和X射线检测等,应根据印 刷品的特性和质量要求选择适当的检测方法。
修复工艺
对于发现的缺陷和问题,可以采用适当的修复工艺进行处理,如局部 热处理、激光修复等,以确保太阳能电池片的质量和性能符合要求。
03 太阳能电池片丝网印刷工 艺流程
涂布感光胶
涂布感光胶
在丝网印刷前,需要在硅片表面涂布 一层感光胶,以增强丝网印刷的附着 力。
涂布方式
涂布厚度
感光胶的厚度应均匀,且需根据丝网 印刷的精度要求来控制,一般而言, 较薄的涂布厚度可以提高印刷线条的 精度。
感光胶可以采用喷涂、刷涂或浸涂的 方式进行涂布,具体涂布方式应根据 感光胶的特性和生产工艺要求而定。
得可太阳能推出新一代太阳电池丝网印刷设备
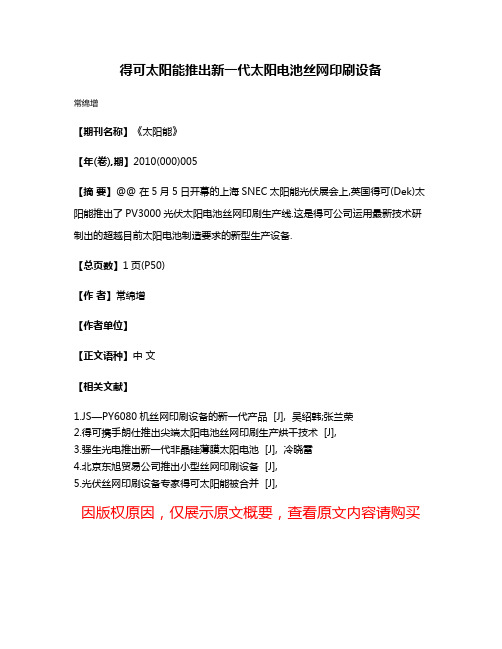
得可太阳能推出新一代太阳电池丝网印刷设备
常绵增
【期刊名称】《太阳能》
【年(卷),期】2010(000)005
【摘要】@@ 在5月5日开幕的上海SNEC太阳能光伏展会上,英国得可(Dek)太阳能推出了PV3000光伏太阳电池丝网印刷生产线.这是得可公司运用最新技术研制出的超越目前太阳电池制造要求的新型生产设备.
【总页数】1页(P50)
【作者】常绵增
【作者单位】
【正文语种】中文
【相关文献】
1.JS—PY6080机丝网印刷设备的新一代产品 [J], 吴绍韩;张兰荣
2.得可携手朗仕推出尖端太阳电池丝网印刷生产烘干技术 [J],
3.强生光电推出新一代非晶硅薄膜太阳电池 [J], 冷晓雷
4.北京东旭贸易公司推出小型丝网印刷设备 [J],
5.光伏丝网印刷设备专家得可太阳能被合并 [J],
因版权原因,仅展示原文概要,查看原文内容请购买。
太阳能电池丝网印刷简介

12. 分选机(SSD01) 分选机共有32个电池片目标仓,根据上道工序的检测结果,真 空吸头可将电池片放至预先确定的目标仓中。当一个目标仓到 达了设定的最大值,信号灯将会被激活,此时可以打开抽屉取 出电池片。
太阳能电池丝网印刷简介
1.3 ASYS 印刷机主界面
太阳能电池丝网印刷简介
太阳能电池丝网印刷简介
硅片经过三次印刷工序后的效果图
背银印刷
背铝印刷
正银印刷
太阳能电池丝网印刷简介
IV区生产流程
▪ 上料→边缘碎片检测→背电极印刷→人 工检测→烘干→缓冲存储器→背面铝印 刷→人工检测→烘干→缓冲存储器→翻 转电池片→正银栅线印刷→自动检测→ 烧结→缓冲存储器→冷却→测试→分类 →包装
太阳能电池丝网印刷简介
1丝网印刷、烧结和测试设备简介
1.1ASYS工艺流程
▪ SES(上料)→XS(背电极印刷)→烘干→SMP (缓冲传送器)→XS(背电场印刷) →烘干 →SMP(缓冲传送器)→SFS(翻转电池片) →XS(正电极印刷)→SIS(自动检测)→烧 结→SBB(缓冲装置)→冷却→SDA(测试分检) →包装
• 区域上部表明刮刀目前是否举起(UP)或者是否降低(DWN)。 • 区域下部提供了刮刀头的信息。如果只有上部水平条亮,那么刮刀
当前在后部。只有底部的水平条亮,那么刮刀当前在前部。另外, 字母BP出现在条的附近,表明刮刀头在基准位置。在印刷工艺中, 两个箭头中的一个会亮起来,表明当前刮刀的运行方向,并且字母 P或者F会出现表明刮刀当前印刷还是回料。
太阳能电池丝网印刷简介
10. 电池片冷却单元(SCU01)
电池片离开烧结炉后的温度较高不适合电气测试,因此要进行冷却降 温,电池片通过两个旋转轮通过,设备上部有两组风扇对其冷却至环 境温度。
太阳能电池-丝网印刷烧结、测试工艺作业指导书
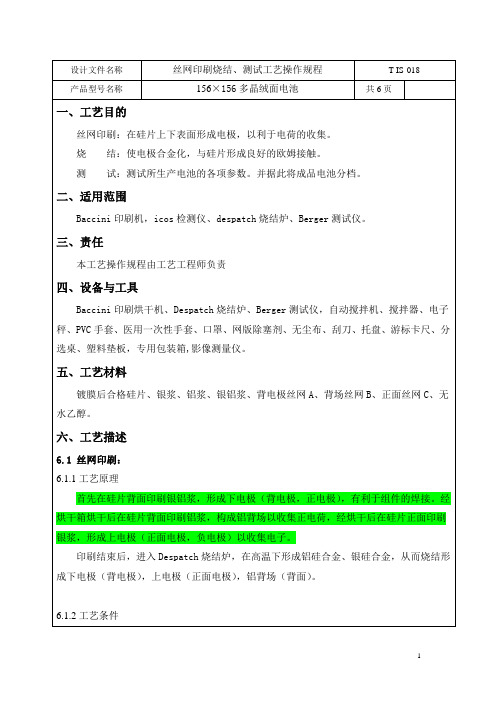
设计文件名称丝网印刷烧结、测试工艺操作规程T-IS-018产品型号名称156×156多晶绒面电池共6页一、工艺目的丝网印刷:在硅片上下表面形成电极,以利于电荷的收集。
烧结:使电极合金化,与硅片形成良好的欧姆接触。
测试:测试所生产电池的各项参数。
并据此将成品电池分档。
二、适用范围Baccini印刷机,icos检测仪、despatch烧结炉、Berger测试仪。
三、责任本工艺操作规程由工艺工程师负责四、设备与工具Baccini印刷烘干机、Despatch烧结炉、Berger测试仪,自动搅拌机、搅拌器、电子秤、PVC手套、医用一次性手套、口罩、网版除塞剂、无尘布、刮刀、托盘、游标卡尺、分选桌、塑料垫板,专用包装箱,影像测量仪。
五、工艺材料镀膜后合格硅片、银浆、铝浆、银铝浆、背电极丝网A、背场丝网B、正面丝网C、无水乙醇。
六、工艺描述6.1 丝网印刷:6.1.1工艺原理首先在硅片背面印刷银铝浆,形成下电极(背电极,正电极),有利于组件的焊接。
经烘干箱烘干后在硅片背面印刷铝浆,构成铝背场以收集正电荷,经烘干后在硅片正面印刷银浆,形成上电极(正面电极,负电极)以收集电子。
印刷结束后,进入Despatch烧结炉,在高温下形成铝硅合金、银硅合金,从而烧结形成下电极(背电极),上电极(正面电极),铝背场(背面)。
6.1.2工艺条件印刷线烘干抽气功率印一为:30%-50%,印二为 60%-80%烧结冷却水:PH值 7.2-7.6 入水16-20℃,压力150PSI,流量10GPM压缩空气:流量2700SCFH,压力60-70PSI6.1.3.注意事项:在印刷过程中应该调整适当的印刷压力、丝网和电池片之间的间隙和印刷速度。
C丝网更换周期为16小时(即隔班更换)。
印刷各项参数必须在规定范围内进行调整,如超出范围,需经技术人员同意,并做好相关记录,不得随意更改。
B丝网更换周期为24小时。
使用期间,根据铝浆印刷量调整参数,通常是调整丝网间隙、压力和印刷速度。
JRT丝网印刷机操作手册

JRT Operating Instructions SPL DSP2Typ:DSP2 Machine no.:DSP2 Year of construe:2008JRT Photovoltaics GmbH & Co. KGRobert-Bosch-Str. 1 D-79331 Teningen Tel.: +49(0)7641 / 583-0 Fax: +49(0)7641 / 583-110www.jrt-pv.deGermany Operating InstructionsSolarprinter SPLJRT Operating Instructions SPL DSP2Basic instructionsBasic instructionsThese Operating Instructions describes the JRT Solar Printer Line DSP2.This is intended as a provisional document. A detailed and thoroughversion of the technical documents will be provided on delivery of thecomplete system.These SOP are a constituent part of the system. They must always bekept in the proximity of the system. Strict observation of the SOP is aprerequisite for the correct use and handling of the system and for thesafety of the operators which depends on this.All of the supplied technical information, care and maintenanceinstructions or separate instruction manuals for parts, components oraccessories must also be observed.Flawless functioning, safety during operation, and the least possiblenumber of disturbances are ensured only when used in combination withcomponents tested and approved by JRT.Use only accessories that were tested and approved by JRT together withthis machine. If third party accessories are used JRT cannot assume anyguarantee for the safe operation or reliable function of the system.There can be no guarantee claims in the event of damages caused by theuse of third party accessories.JRT only regards itself as responsible for the system in terms of safety,reliability and function if:installation, extensions, resetting, modifications and repairs arecarried out by a party expressly authorised by JRT or by JRT itself.the system is used in compliance with these SOP.All documents correspond to the version of the system and the state of thesafety standards on which it is based on going to print. All protective rightsare reserved for the devices, switches, processes, software programs,and names mentioned in the documentation.Duplication - even of extracts - is only permitted with the writtenpermission of JRT GmbH & Co. KG.The Basic safety instructions are marked in this manual as on page 4:Version history of the operating instructionsThe changes to the operating instructions and the change date arerecorded in this section in table form. The latest changes are always at thestart of the table.Date Changes02/15/2008Key word index (page 38) and version history (page 3) extended.Table of contents updated.02/14/2008Machine name changed. All headers and footers regenerated.Basic safety instructionsThese SOP contain safety instructions which must be observed to ensurepersonal safety and to avoid damage to property.The instructions for personal safety are emphasised by several additionalwarning and hazard symbols.Instructions regarding exclusively material damage or other importantinformation are not marked by warning symbols.Depending on the degree of risk, these are treated as follows:HAZARD Means that death, serious injury or substantial material damage willoccur if the corresponding precautionary measures are not taken.WARNING Means that death, serious injury or substantial material damage mayoccur if the corresponding precautionary measures are not taken.CAUTION Means that minor injury may occur if the correspondingprecautionary measures are not taken.NOTE Without a warning triangle means that material damage can occur if thecorresponding precautionary measures are not taken. This may be animportant or an informative instruction.NOTE The information “maximum workplace concentration” can be found in:Deutsche Forschungsgesellschaft, Kennedyallee 40, D-53175 Bonn.During normal operation, the noise level is 65 dB (A).The machine and accessories must be disposed of in accordance with thelocal regulations at the end of their service life. Besides the battery in theoperating panel and the lubricants (oils and greases), the machine doesnot contain any hazardous materials.In case of doubts, questions or service requirements, please contact:JRT GmbH & Co. KG Tel.: +49 (0) 7641 / 583-0Robert-Bosch-Str. 1Fax: +49 (0) 7641 / 583-110D-79331 Teningen www.jrt-pv.deGermany1 Use and functional setup1.1 Proper useBasic principles The system is built in accordance with the state of the art and therecognised safety standards. Nonetheless, its use can result in risks to thelife and health of the users or third parties, damage to the system itself orother material damage.Only use the system in technically perfect condition and for the intendedpurpose in a safety and risk-conscious manner and in accordance with theoperating instructions. In particular, any faults which could impair safetymust be rectified immediately!The JRT solar printer SPL-ALBATROS is used exclusively for the printingof solar cells (wafers). Only materials such as pastes, lacquers andcleaning agents with a flashpoint over 40 °C may be used. The pastesand cleaning agents may not be mechanically atomised even if theirflashpoint is above 40 °C.Adequate room ventilation must be provided.The machine is intended for commercial use only.Any other or more extensive usage is improper.Correct usage also includes:Strict observation of these short operating procedures / SOP.Personnel selection.and Work on the system may only be carried out by reliable, trained or qualification instructed personnel.Clear allocation of responsibilities. Obligation to supervise personnel intraining.Work on the electrical equipment of the system may only be carried out bya qualified electrician or by instructed personnel under the direction andsupervision of a qualified electrician in accordance with the electricalengineering regulations.Work on pneumatic equipment may only be carried out by personnelqualified for this purposeNOTE The JRT screen printing machines have diverse applications. They can beused to apply the widest possible range of pastes to the widest possiblerange of print materials. As we always draw up the performance featuresindividually for our customers, please note that the use of print materials orpastes other than those used in the projection phase can alter theperformance features cited in our offers.1.2 Functional setupThe cited item nos.:-1-to-8-are in fig.1.2.2on page 9.Rotary indexing table -1-On the rotary indexing table there are four print tables – so-called printnests-2-;-3-;-4-. The table turns by 90 °on every cycle, so that it movesto 4 positions in one rotation.Inlet station -5-In the inlet station the wafers are placed on the print table.A paper is spanned over the print table onto which the wafers are placed.The paper, which is rolled off a roll-6-behind the print tables and rolledonto a roll underneath the print table, has two tasks: on the one hand itconveys the wafers after printing onto the transport belt to thedownstream dryer, and on the other hand it ensures that the cells arealways placed on a clean underlay which is free of ink or other residues.After they are placed on the print table, the wafers are fixed by a vacuum. Print station -4-Here the wafers are printed using the screen printing process. The printstation consists mainly of the print head-9-with squeegee carriage-10-and the screen rails-11-.The print head can be raised for cleaning the underside of the screen.Two vertical positions are available: an upper and a middle position. Inboth positions the print head is mechanically locked for safety reasons toprevent unintended lowering.The squeegee pressure can be adjusted separately for the right and theleft cylinder. The pre-squeegee pressure cannot be changed. Thesqueegee bar is swivelled and can be passed over a drip channel-12-.1.2 Functional setup Item no.Fig. 1.2.1Designation -9-Printing head -10-squeegee carriage -11-Screen rail -12-Drip channel -13-Squeegee pressure cylinder Printing cycle Lowering the print headPrinting the material by advancing the squeegeeRaising the print headFlooding the screen by returning the flood bar.Register setting (screen alignment) is automatic.Outlet station Item3 on the rotaryindexing table The camera over the output station (optional) checks the print quality and the condition of the wafer. Only predefined print errors are recognised by the camera. Damaged wafers are removed.To output the wafers the paper is rolled off the upper roll until the solar cells have reached the connecting transport belt.The machine is controlled via an operating panel with monitor.As required by the applicable directives, all moving or rotating parts are secured with technical protective measures.Fig. 1.2.2on page 9 shows the main components of the JRT solar printer SPL-ALBATROS.1.2 Functional setupItem no.Fig. 1.2.2Designation -1-Rotary indexing table -2-Inlet station -3-Paper control station -4-Print station -5-Paper roll -6-Outlet station with camera (optional)-7-Jockey roller on the paper transport system Fig. 1.2.2 Solarprinter Aufbau3 The operating panelThe machine is equipped with a SIMATIC control system and is operatedby mouse and keyboard. Operation is menu aided, i.e. related settings aregrouped respectively in a menu window on the screen.In all of the menu windows the lower section always shows the standardoperating keys(see page 18) with which you can execute the mostfrequent operating steps.You actuate the buttons by clicking on them with the mouse.To enter values, click on the entry field. A keyboard is displayed withwhich you can make all of the necessary entries. Use the enter key toconfirm the entry and remove the keyboard from the screen.The operating panel also contains the key to switch on the control systemand an emergency stop switch.4 The menusBasic principles This chapter briefly introduces the individual menus.Reminder:The control system is menu aided, i.e. related settings are groupedrespectively in a menu window on the screen.In the following section Machine setup(see page 20) you can read howthe machine is started up and which settings have to be made in themenusNOTE The individual menus are called up by clicking on the corresponding button;the buttons shown in the menus are actuated in the same way.To enter values or text, click on the entry field. A keyboard is displayedwith which you can make all of the necessary entries. Use the enter keyto confirm the entry and close the keyboard.In all of the menus the standard operating keys are shown on the lowersoftkey bar on the screen (see page 18), e.g.Automatic ON/OFF,Automatic START/STOP or Starting position.JRT Operating Instructions SPL DSP2Once the system is booted up, the system start window appears. Click on The control system is booted up and theappears.the function of the individual stations pending error messages and warnings The other menus for printer, dryer etc. can be called up with the buttonsbelow the header.On page 15 you will find a detailed description of the individual functionsin correspondence to the numbers on this page (14).JRT Operating InstructionsSPL DSP21In the system overview window you can call up the other individual menus on the menu bar at the top. These are: printer, dryer, statistics, miscellaneous and fault reports2List with fault reports. Fault reports cause a shutdown of the machine.3List with warning reports.4To select the machine setting.5To load the corresponding machine settings in the machine control system.6Diagram of rotary indexing table (middle) and the four stations: print station, inlet station, paper control station, outlet station; the red panel symbolises the switched-on camera lighting. Numbers displayedrepresent the individual print nests. When the rotary indexing table turns, the print nest numbers turn with it.7Diagram of the trapdoor (to remove rejected parts).8Diagram of the synchronising belt.9Extreme left: result for the last wafer, then the result for the second last etc.10List of pending reports (fault or warning reports).11To confirm reports.12Control lamps dryer, cooling zone green: temperature OKyellow: heating/cooling red: fault13Control lamps dryer, heating zone. green: temperature OKyellow: heating/cooling red: fault14Control lamps dryer belt. green: speed OKred: fault15To switch the dryer belt on and off.16Standard operating keys.17Function control inlet, print and outlet station as well as paper control and rotary indexing table. yellow: station working green: station has workedred: fault18To start automatically (e.g. after a change of screen) the machine moves to the basic position, automatic mode is switched on and the machine starts up.19To call up the camera image (screen centering) on the separate monitor. 20To initiate a change of screen. Automatic operation stops. Squeegee carriage is raised and passes over the drip channel. The screen frame clamp opens.21To start the automatic screen alignment process.22Last fault occurringDisplay of the information You can display detailed information for the individual stations.windowA window appears in each case with two lines:The first line shows the current action.The second line shows the conditions for the next action.The control lamps below indicate the function of the step chain.To display the information window, click on the symbol of the station andselect Open / close information. Use the same procedure to close theinformation window.Fig. 4.2 SYSTEM OVERVIEW Open /close informationSwitch step mode on / off You can switch on step mode to make settings at the individual stations.The buttons Reset and Step forwards are displayed.To switch step mode on, click on the icon for the station and select Stepmode on /off. You can switch the step mode off in the same wayFig. 4.3 Menu SYSTEM OVERVIEW Switch step mode on / off Attention!If step mode is activated you have to continue through the individual stepson the step chain by individual clicks on the corresponding button.The machine comes to a standstill after every step.Standard operating keys. The lower standard operating keys bar is the same in all menu windows1 Automatic ON/OFF.To switch from manual to automatic mode.You can only switch to automatic mode if the machine is in the startingposition. In automatic mode, pressing Automatic START/STOP triggersthe print cycles automatically until the machine is stopped by pressingAutomatic START/STOP2 Automatic START/STOP For starting and stopping the machine in automatic mode.3 Squeegee forwards / back To move the squeegee in manual operation (Automatic START/STOP is not pressed). The squeegee carriage moves forwards to the end position and then back again.4 Screen cleaning.To activate the screen cleaning (before the print head can be raised withFrame UP / DOWN,Clean screen must be pressed). To lower the printhead you must press either the button Starting position or Frame UP /DOWN.The function ”Clean screen” is automatically deactivated5 Swivel squeegee Use this to swivel the squeegee bar upwards and pass it over the dripchannels.When you press key5:the squeegee carriage moves to the centre of the print headthe squeegee bar swivels upwardsthe squeegee carriage waits for the drip-off timethe squeegee carriage passes over the drip channelWhen you press the key again:the squeegee carriage moves to the centre of the print headthe squeegee bar swivels downward6 Starting positionBrings the machine to the starting position. While approaching the startingposition, the key flashes green. As soon as starting position is reached,the key is permanently lit in green.7 Dryer ON/OFF To switch the dryer on and off.8 Screen clamp To open and close the screen frame clamp.9 Squeegee forward Causes the squeegee carriage to remain in the position “print end” afterevery print (screen open).10 Frame UP / DOWN To raise or lower the print head in setup mode or to raise and lower theprint head for cleaning the screen or changing the paper roll.5 Adjusting the machine5.1 Referencing, bringing the machine to the starting positionWARNING Risk of injury due to moving machine parts.Serious physical injury to head and hands by crushing or severingof body parts.Before switching on (start-up) the machine (system), make surethat nobody is working on or in the machine.Close the protective doors.Apply safety and protection covers.After actuating the main switch, the drives for print head, squeegeecarriage and screen lift have to execute a reference motion.Only then can the machine be brought to the starting position.Switch on compressed air supply.Actuate main switch.First the start information window appears.The system is booting up! Please wait.After booting up, the start window appears on the screen.The system overview window is opened by mouse click on the softkeySystem loaded!Fig. 5.1.1 System loaded5.1 Referencing, bringing the machine to the starting positionFig. 5.1.2 SYSTEM OVERVIEW Switch on the control system at the control panel. The illuminated button must be lit up.Click on the Starting position key.The machine now carries out a reference motion with the print head, i.e. the print head is raised to the end position where it remains. During the reference motion the button Starting positionflashes. Click on Starting position once more.The print head. is lowered and remains in the position “raised”.Click on Starting position once more.Now the squeegee carriage and the screen lift carry out a reference motion.Click on Starting position once more.The squeegee carriage moves forward to the position “print end”. The machine has reached its starting position and the button Starting position is lit permanently in green5.2 Inserting screenClick on the button Printer in the system overview window. The windowPRINTER – print parameters appears. Click on the button Setup in theupper standard operating key bar and the window PRINTER – setupappears(Fig. 5.2.1).Fig. 5.2.1 PRINTER - setupOpen the screen clamp.Insert screen.Close the screen clamp again. The screen frame is alignedautomatically.5.3 Inserting the squeegee Press the softkey Squeegee forwards / back on the lower standard operating key bar to move the squeegee carriage to a favourable position for inserting the squeegee.Select a squeegee of the appropriate length.The squeegee should extend beyond both sides of the printed image by approximately 20 mm.The maximum length of the squeegee depends on the size of the screen frame.. Maintain a distance of at least 100 mm between the end of the squeegee and the screen frame. Make sure that the two swivel plates are set at the same squeegeeangle. If not, this can be corrected using the clamp lever.Insert the flood bar (front) and the printing squeegee (rear) into theclamping receivers and tighten the clamping levers (6).Make sure that the squeegee is under symmetrical tension and does not protrude to the right and left more than 25% of the total lengthBefore switching on (start-up) the machine (system), make sure that nobody is working on the squeegee cylinders.If the controller fails, the cylinders may raise or lowerunpredictably. For this reason, switch off the main switch before performing adjustment work that requires a longer amount of time.If the cylinders were moved manually while the power wasswitched off (like when the main switch is switched off), they will return to the previously selected position when the power is turned back on.WARNING Risk of injury due to moving machine parts.Serious physical injury to head and hands by crushing or severing of body parts.5.4 Setting the print parametersEntering the print and Click on the softkey Print parameters in the upper softkey bar to flood speed.open the PRINTER - print parameters windowClick on the entry panel-1- print speed and used the keyboarddisplayed to enter the starting value 100 mm/s (input range 100 (400)mm/s).Press the enter key J+to confirm the entry. This also closes thekeyboard.Proceed in the same way for-2- flood speed.Fig. 5.4.1 PRINTER – print parameters Print speed / Flood speed5.4 Setting the print parametersAdjusting the SqueegeeYou can set the squeegee path in two ways:Stroke . 1. By driving the squeegee carriage to the front and back end positionand then storing the respective position by pressing a key.2. By entering the front (print start) and rear (print end) end position as anumerical value in the squeegee menu NOTERisk of the squeegee arm colliding with the screen frame.Damage to the squeegee and the screen frame. Whenever possible, always set the squeegee path by moving the squeegee carriage.1. Moving the squeegeecarriage and storingthe end position (Fig. 5.4.1) Move the squeegee carriage with -3- Squeegee forwards /back to the print start and press-4- Teach In Start.Then move the squeegee carriage to the print end and press -5-Teach In End .Fig. 5.4.1 PRINTER – print parameters Teach In Start / End HAZARD Insufficient minimum distance at the end positions betweensqueegee and screen frame.Increased risk of crushing injury to hands.The distance between the squeegee and the screen framemust not be less than 25 mm.5.4 Setting the print parameters2. Entering end positions Click on the entry panel-6- Position print start end enter the value (theas numerical values value is entered in mm and measured from the rear end stop of the (Fig. 5.4.2)squeegee carriagePress the enter key J+to confirm the entry.Proceed in the same way for-7- Position print endFig. 5.4.2 PRINTER – print parameters Position print start / print end5.5 Changing the paper rollTo change the paper roll, the corresponding print nest must be in the printstation.When the system demands a change of paper, click on the softkey-1-Request paper change in the menu PRINTER – print parameters (Fig.5.5.1).The machine continues running until the corresponding print nest is in theprint station. The machine stops and the print head moves upwards intothe cleaning position.-1-Fig. 5.5.1 PRINTER – print parameters Request paper change5.5 Changing the paper rollOpen the holder for the take-up roll. To do this lift the locking lever and slide itto the right (Fig 5.5.1). Remove the roll to be changed.Fig. 5.5.1 Locking lever to open the holderPlace the new roll on the lower tray (Fig. 5.5.2).Fig. 5.5.2 Inserting the new roll5.5 Changing the paper rollStick the end of the paper (Fig. 5.5.3) to the end of the take-up roll withadhesive tape and wind on some paper with a few turns.Insert the take-up roller. and close the holderFig. 5.5.3 Sticking the end of the paper to the take-up roll.Wind on paper with a few turns.Now grip the new roll and lead the paper under the jockey roller and overthe print head (Fig. 5.5.4).Place the new roll into the holder after the print head and close the lockinglever.Fig. 5.5.4 Thread paper under the jockey roller Fasten the roll on the rear holder.5.5 Changing the paper rollSwitch to the submenu Manual control.Use the symbol key at-1- Take-up roll in the paper transport window to windon paper until the jockey roller has reached the upper position (Fig. 5.5.5).Fig. 5.5.5. PRINTER – Manual control Take-up roll5.6 Working on the underside of the screen To carry out work on the underside of the screen, the whole print head can be raised.There are two positions to choose from: one at the top and one around the middle. You can select the position in the submenu print parameters.Make sure that the print head reaches this position and stops automatically. Only in these positions is the print head mechanically locked and is thus secured against unintentional lowering. Click onStarting position. Click on Clean screen . Click on Frame UP / DOWN .The print head is raised into the cleaning position. Wait until the print head reaches its end position and all movement has stopped. Move the print head to the end position. Then the print head is mechanically locked and thus prevented from unintentional lowering.Now you can open the door and begin work.After work is completed you must close the door and either press Starting position or Frame UP / DOWN . The Clean screen function is automatically deactivated.If you would like to clean the screen during automatic mode you only have to click on Clean screen : the machine stops. the squeegee carriage stops in the forwards position (screen notflooded). The print head is raised into the cleaning position.When work is completed, press: Basic position Automatic ON/OFF Automatic START/STOP HAZARDPrint head not in end position.Increased crushing risk for head, neck and hands.5.7 Storing and loading machine settingsIn the menu PRINTER – print parameters you can store machine settingsunder a data set name or reload them using this data set name.In the window Recipe administration Printer you can enter thecorresponding data.Storing settings Make all of the machine settings.Click on key-1-(see Fig. 5.7.2on page 33).Load the data from the machine control system with the key-4-.Enter a data set name in the entry panel-6-.Store the data with one of the keys-2-.Load settings Enter the data set name under which the settings are stored in theentry panel-6-or select it with-7-.Use key-5-to load the data in the machine control system.The loaded settings appear in the table column Value(see item no.-8-onpage 32).Delete stored machine settingsEnter the data set name under which the settings are stored in the entry panel-6-or select it with-7-.Use the key-3-to delete the settings.Fig. 5.7.1 PRINTER – print parameters Recipe administration Printer5.7 Storing and loading machine settingsFig. 5.7.2 Recipe administration Printer5.8 Selecting a languageThe language of the display texts can be selected in the Miscellaneous menuby clicking on key-1- Select language(Fig. 5.8.1).Fig.5.-1-8.1MISCELLANEOUFig. 5.8.1.MISCELLANEOUS Select language6 Automatic mode 6.1PrintingSet up the machine (see Chapter 5, page 20). Add paste.Click on the softkey -1- Start position .Select automatic mode with -2- Automatic ON/OFF . Start automatic mode with -3- Automatic START/STOP .You can also start the machine by simply clicking on-4- Machine START . With this key the starting process is executed automatically:The machine moves to the starting position. Automatic mode is selected. The machine starts running.-Fig. 6.1.1 SYSTEM OVERVIEW Print-4--3--2--1-。
太阳能硅电池片丝网印刷装置及印刷方法[发明专利]
2019运动会通讯稿100字【十篇】运动场上有你飒爽的英姿;运动场上有你拼搏的身影。
面对着漫漫征途,你没有畏惧和退缩。
任汗水大湿脊背;任疲惫爬满全身;你依然奋力追赶,只有一个目标;只有一个信念为了班级的荣誉,拼搏吧!快去击败困难、快去夺取胜利!千百双眼睛在注视着你们,希望就在前面,加油啊,运动健儿们,胜利就在前面。
一根细细的杆子横放在半空中,它细,然而却像你生命中的坎,不可怕,不要怕,只要你有决心,只要你有信心,这又算得了什么?没有经历过坎坷就不会有成功的喜悦,一次次的战胜,一次次的超越自己,加油吧,努力跳过这挡在你前面的坎去燃烧你的青春!篇三热情地释放光芒的红日,被阵阵此起彼伏的加油声震撼,慌张地投入到乌云的怀抱那群北飞的候鸟却因为热火朝天的场面而盘旋在运动场上,留恋着这里与寂静的天空截然不同的热闹围绕在运动场边的树木,在秋风的频繁光顾下奏鸣出悦耳的树叶的交响曲,仿佛是为了配合场上的拉拉队,为奋斗的运动员们加油鼓劲篇三短暂的一瞬间,显示出你惊人的速度,铿锵有力的一声吼叫,把你全身的力量都凝聚在这一刻上努力吧!加油啊!时间短暂并不代表你激情短暂,距离不长却表示你成功不远,相信自己,冲啊!胜利就在眼前,失去不会再现!篇四一条跑道,要四个人去打造一个信念,要四个人去拼搏!每次交接都是信任的传递!每次交接都是永恒的支持!前世的五百次回眸,才能够换来今天的相遇,冲吧!向着终点,向着个四个人的共同目标,前进!篇五漫漫长路,你愿一人独撑,忍受着孤独与寂寞,承受着体力与精神的压迫,任汗水溶于泪水,可脚步却从不停歇。
好样的,纵然得不了桂冠,可坚持的你,定会赢得最后的掌声篇六深深的呼吸,等待你的是艰难的5000米。
相信胜利会属于你们。
但在这征途上,需要你用勇敢的心去面对。
我们在为你加油,你是否听到了我们发自心中的呐喊? 困难和胜利都在向你招手,去呀,快去呀,不要犹豫。
快去击败困难、快去夺取胜利!相信你会送给我们一个汗水浸湿的微笑!篇七磨炼的是非凡的毅力,较量的是超常的体力,拼搏的是出类拔萃的耐力。
太阳能电池片丝网印刷_烧结工艺(完整版)
丝网印刷的定义
利用丝网图形部分网孔透浆料,非图文部分网孔不透浆料的 基本原理进行印刷。印刷时在丝网一端倒入浆料,用刮刀在 丝网的浆料部位施加一定压力,同时朝丝网另一端移动。浆 料在移动中被刮板从图形部分的网孔中挤压到基片上。印刷 过程中刮板始终与丝网印版和承印物呈线接触,接触线随刮 刀移动而移动,而丝网其它部分与承印物为脱离状态,保证 了印刷尺寸精度和避免蹭脏承印物。当刮板刮过整个印刷区 域后抬起,同时丝网也脱离基片,并通过回墨刀将浆料轻刮 回初始位置,工作台返回到上料位置,至此为完整 的一个
印刷行程。
丝网印刷的五个要素
丝网印刷由五大要素构成,即丝网、刮刀、浆料、工 作台以及基片。
刮刀
刮刀的作用是将浆料以一定的速度和角度将浆料压入 丝网的漏孔中,刮刀在印刷时对丝网保持一定的压力, 刃口压强在10~15N/cm之间,刮板压力过大容易使 丝网发生变形,印刷后的图形与丝网的图形不一致, 也加剧刮刀和丝网的磨损,刮板压力过小会在印刷后 的丝网上存在残留浆料。
Park 刮刀的停止位置,印刷和回墨完成后,印刷头的停止位置。 Pressure 刮刀压力,印刷时括刀下降到Down-stop位置,这个位置的参数必须
设置得比电池稍低(0.3-0.4mm应该足够了),这样实际的压力(左边显示的数 值)才能达到设置值。单位是牛顿,在压力模式下,印刷压力越大,瞬时刮刀 下降的位置就会越低,很可能会远超过0.3-0.4mm,对网版和印刷质量造成比较 大的损害,所以在日常设定印刷压力时需以小为宜。实际参数设定时,压力越 大,承印量越小,压力越小,承印量越大,,压力的变化实际是刮刀位置的变 化。
印刷参数
PRINTING Alternate squeegee 单程印刷:刮刀向前运动印刷一片片 子,向后返回印刷下一片;Double squeegee 两次印刷:对每一块 片子向前印刷一次,再向后印刷一次;Squeegee and Flood 印刷后回 料(常用);Flood and squeegee 回料后印刷;
太阳能电池工艺丝网印刷简介
故障处理
● 第一道: 第一道: 1.上料台Feed C/V2经常会有承载盒不到位引起的报警,可以分为两种:一种是Magazine 1.上料台Feed C/V2经常会有承载盒不到位引起的报警,可以分为两种:一种是Magazine 上料台 经常会有承载盒不到位引起的报警 处在Down的位置,只要把盒子推到位就可以了;另一种是Magazine 处在Up 的位置, Down的位置 处在Down的位置,只要把盒子推到位就可以了;另一种是Magazine 处在Up 的位置, 那时你推盒子是推不动的,因为被卡死了,只要让Magazine 处在Down 那时你推盒子是推不动的,因为被卡死了,只要让Magazine 处在Down 位置再把盒子 推到位就行了。 推到位就行了。 经常会吸住承载盒内的拖盘而报警,原因是盒子上端开口比较大, 2.Wafer transfer 经常会吸住承载盒内的拖盘而报警,原因是盒子上端开口比较大,拖 盘挡住了感应器而造成,只要将拖盘放正,把Wafer transfer移到另一个位置就行了, 盘挡住了感应器而造成, 只要将拖盘放正, transfer移到另一个位置就行了, 移到另一个位置就行了 把盒子整一下。 把盒子整一下。 有吸两片的现象,方法有a .调节风刀的大小和风刀吹风的位置 调节风刀的大小和风刀吹风的位置; 3.Wafer transfer 有吸两片的现象,方法有a .调节风刀的大小和风刀吹风的位置; .调节四个吸嘴的高低 .调慢气缸的上升速度 ,风刀吹风的时间 调节四个吸嘴的高低;c 调慢气缸的上升速度;d 风刀吹风的时间。 b .调节四个吸嘴的高低;c .调慢气缸的上升速度;d ,风刀吹风的时间。 因为硅片碎掉,摄想头定位出现报警而造成的机械手不动作,方法有a .放 4.Alignment 因为硅片碎掉,摄想头定位出现报警而造成的机械手不动作,方法有a .放 好片子上重新照点定位就可以;b .如果 不行,只有甩源关掉,用手将Alignment 如果a 好片子上重新照点定位就可以;b .如果a 不行,只有甩源关掉,用手将Alignment 推 P1的位置 然后重新启动电源, 的位置, 有一个复位的过程旧可以了。 离Standby P1的位置,然后重新启动电源,让Alignment 有一个复位的过程旧可以了。 5.印刷台面有压板的现象 原因有:网板下面胶带粘的太多太厚, 印刷台面有压板的现象, 5.印刷台面有压板的现象,原因有:网板下面胶带粘的太多太厚,员工在装片时没有注意 硅片与硅片之间是否有小碎片或灰尘,印刷台面没有调平或是刚带打毛, 硅片与硅片之间是否有小碎片或灰尘,印刷台面没有调平或是刚带打毛,硅片本身有 受过伤或裂痕。 受过伤或裂痕。
德国原装高科技丝网印刷系统登陆Print China 2011
时展 出。本刊记 者有幸在展会现场采访 了S 德 国 S P 董事会主席兼销售总监A e K S x ] a e 先生以及 R S 1 r K
量优 良 ,使 用寿命 长 第 二 应 用范 围广泛 第 三 速度快 ;第 四 ,精度高 ,质量稳定 ,印刷效果
2 1 . 今 日印刷 0 15
5 5
印速及 油墨等 因素影 响悄悄改变而使其稳定 性无法
控 制 S S P 独有 的P H I E  ̄ 胶系统配 合德 国R S J K 碳纤维 刮板却 轻松解决 了其他 系统 无法处理 的难题 .使印
能以满足业界要求 在设定 、检测 、流程控制等操 作方面更加方便简易 ,大大降低 了各 项成本 。
( 广东 )国际 印刷技 术展 览会 ( 1 C n P n 1 r t h 8 2 1 )于2 l 年4 0 1 0 1 月9 3 ~1 日在广东现代国际展览 中心 隆重举行 。本届展会 4 号馆特 别展出丝 网印刷 及数字 印刷 。S S R S 及 K 亚洲总代 理—— 卧龙 岗国 P
德 国原 装高科技 丝 网Et 系统登 陆 ru ] s
Pr t h a 2 1 n 01 i C i n
完美 。A e K 1 e 先生介绍 : x ] a S r 目前的印刷方式 里 ,胶 印 占了5 名 ,此外 的大多数效果都是通过 丝 0
网 印 刷 来 实 现 的 。丝 网 印刷 凭 借 承 印物 广 泛 ,包 括
题 ,既可 以及 时为客户提供服 务更可 以直 接与 S S P 在 德 国 的工 程师 通过 联线 检 测 对其远 程 诊 断与 监 控 ,以便维修 。 A e K 1 e 先生认 为卧龙 岗国际有 限公司是 x ] a sr
- 1、下载文档前请自行甄别文档内容的完整性,平台不提供额外的编辑、内容补充、找答案等附加服务。
- 2、"仅部分预览"的文档,不可在线预览部分如存在完整性等问题,可反馈申请退款(可完整预览的文档不适用该条件!)。
- 3、如文档侵犯您的权益,请联系客服反馈,我们会尽快为您处理(人工客服工作时间:9:00-18:30)。
Standard Standard for front and rear side controls. As an option, customer systems can be integrated Standard Optional (integrated in the printer) Optional, can be integrated before and after printing Optional Optional Optional Optional Optional
Output data depend on the process parameters. The technical information is subject to change.
PRINT LINE
GREATER EFFICIENCY AND THROUGHPUT
AT LOWER COST PER WP
PRINT LINE
TEST LINE
METALLIZATION LINE
TWO COMPANIES BUNDLE THEIR ENERGY,
DEFINING A NEW FORMULA ENSURING THE HIGHEST DEGREE OF EFFICIENCY: JRT.
JRT–our mission
#02 Print station
The printing station is characterised by the smooth screen printing ensuring low wafer mechanical stress. The screen can be moved in cleaning position, so that the printing mechanism is easily accessible. Changing the screen and squeegee is rendered extremely simple and easy. The automatic screen positioning by means of a camera system ensures high precision and accuracy of printing. High throughput performance is attained through „authentic“ double usage. The printing station is suitable for future cell designs.
Technical data
Wafer size [mm] Wafer thickness [µm] Throughput/hour (gross)
125 x 125, 156 x 156, String Ribbon-Sizes 100 – 400 2400 (optional 2800)
Features
JRT–backed by two technological leaders
The independent JRT Photovoltaics combines the know-how and market experience of two strong partners: Jonas & Redmann and Thieme. The result is an optimal service spectrum in the sector of metallization and handling technologies for the partial coating of crystalline solar cells. Here, the highest quality standards, innovative technologies and the synergy of long-year experience come together in the respective core competencies.
#01 Control
The clear text indicator provides an optimum overview. Large displays, savable parameters including formulation management as well as the usage of the most modern SPC technology contribute to user friendliness. The system is equipped with a MES interface for the monitoring of quality-relevant parameters and a single wafer pursuit. A visualisation of the image processing as well as the system technology with condition analysis is integrated in the system concept.
leading technologies
METALLIZATION LINE
LOADER
PRINTER
DRYER
LOADER
PRINTER
DRYER
LOADER
PRINTER
FAST FIRING FURNACE
UNLOADER
TION KNOWS A LOT OF GOOD SOLUTIONS
JRT–the customer‘s objectives are our objectives
Our declared objective is to make our industrial partners more competitive through more efficient installations and services. The successive reduction in wafer thickness reduces the use of silicon, our processing and coating procedures increase throughput while cutting breakage rates, ensuring a high efficiency at low cost. Furthermore, we understand „leading technologies“ as a daily challenge to implement the requirements of our customers with passion and ambition. With many innovative new features and characteristics, reliability and quality, we are shaping the future for strong partnerships and successful customer relations.
Breakage control / breakage discharge Print control Buffer storage Automatic paste feed Weighing station Patented paper control Firing sunny-side-up MWT (Metal Wrap Through) Selektive Emitter Laser edge insulation
#03 Print nest
When depositing the wafers in the print nest, they are precisely placed. The wafer is affixed with the help of a vacuum on the interruption-free print nest, so that a precise printing is assured. The print nest is equipped with a paper support which ensures a consistent clean print nest surface. It is possible to optionally interconnect a paper check, which inspects the paper for contamination. After a screen changeover, the roll-to-roll paper support can be used as a test print substrate to avoid the usage of wafers for set-up. The paper feed/ transport guarantees a smooth wafer transport to the following stations.