CPK抽样方法
Ppk,Cpk,Cmk 三者的区别及计算

Cmk是德国汽车行业常采用的参数,称为临界机器能力指数,它仅考虑设备本身的影响,同时考虑分布的平均值与规范中心值的偏移;由于仅考虑设备本身的影响,因此在采样时对其他因素要严加控制,尽量避免其他因素的干扰,计算公式与Ppk相同,只是取样不同CP(或Cpk)工序能力指数,是指工序在一定时间里,处于控制状态(稳定状态)下的实际加工能力。
它是工序固有的能力,或者说它是工序保证质量的能力。
这里所指的工序,是指操作者、机器、原材料、工艺方法和生产环境等五个基本质量因素综合作用的过程,也就是产品质量的生产过程。
产品质量就是工序中的各个质量因素所起作用的综合表现CPK:强调的是过程固有变差和实际固有的能力;CMK:考虑短期离散,强调设备本身因素对质量的影响;CPK:分析前提是数据服从正态分布,且过程受控;(基于该前提,CPK一定>0)CMK:用于新机验收时、新产品试制时、设备大修后等情况;CPK:至少1.33CMK:至少1.67CMK一般在机器生产稳定后约一小时内抽样10组50样本CPK在过程稳定受控情况下适当频率抽25组至少100个样本一旦上限(USL, upper specification limit)与下限(LSL, lowe r specification limit)已经定义,cmk可用来计算贴装精度。
由于极限值一般是对称的,我们可以用简化的规格极限SL=US L=-LSL进行计算,如图一所示。
cmk= 规格极限-贴装偏移3x标准偏差= 3SL-&micr o; 3σ以下的cmk结果是针对图一所提出的条件和客户所定义的50& micro;m规格极限。
cmk= SL-µ 3σ= (50-6)µm 24µ m =1.83Cmk (machine capability index)机器能力指数机器能力指数,是最适合评估机器对于一个特殊要求的可适用性。
CPK抽样方法

计算Cpk收集数据:子组容量n:最好就是在4~5,子组个数k:20~25,子组抽样间隔一般瞧产品得产量考虑,1hr少于10件8hr 1组1hr10~19pics4hr 1组1hr20~49pics 2hr 1组1hr大于50pics 1hr 1组抽样一般都就是在尽量短得时间完成ﻭ取样条件:必须就是连续加工零件组成,且为单一批量设备必须先进行预热至正常/最佳状态,预热时间视不同设备而具体规定;设备附件:设备之工装、夹具必须为正常/最佳状态(新工装、夹具需使用至寿命5-10%为正常),且在加工过程中不允许改变与损坏,否则需重新开始;生产过程:设备在生产过程内要保持其性能稳定性,(如避免受机械故障;停电;损耗;腐蚀等),否则需重新开始;ﻭ操作员:只允许指定一名操作人员(为熟练者);检验员:只允许指定一名检验人员(为熟练者);量具:只允许使用一个量具(为合格者);检验过程:保持同一检验方法与检验环境条件不变(如温度、湿度、场地等);零件测量规定在具体确定位置,并保持每次测量均相同。
、在什么情况下要对机器能力进行测试?回答就是,在很多情况下都要进行机器能力系数测试,但就是,最重要得情况有两种:(1)在最终认可以前,证明新设备就是合格得;或者(2)确定工序中新发现得造成工序异常波动得原因。
前提条件:1、在机器能力测试中使用得零件毛坯应从同一供货厂商处购买,并要求其材料相同,由同一浇铸模铸成或由同一套模具配套件制成。
2、前一道工序(前一台机床)所加工出得零件应符合设计与加工要求,其尺寸须符合公差要求。
3、对于所选取得零件数目有如下规定:连续地测量每个产品规格中得50个零件以某种特定得方式记录下来。
(如连续得序数)4、如果一台机床可以加工两种以上得零件,或者就是零件编号不同得同种零件,则对其加工得每一种规格得零件都要求做机器能力得测试。
5、在机器能力测试前,如果刀具就是未曾使用过得刀具,则要求先用去刀具总寿命得5~10%(因为新得刀具磨损剧烈,故而加工出得产品尺寸极不稳定,当用去刀具总寿命得5~10%以后刀具磨损程度平缓,零件得加工尺寸稳定)。
一模多穴ppk取样
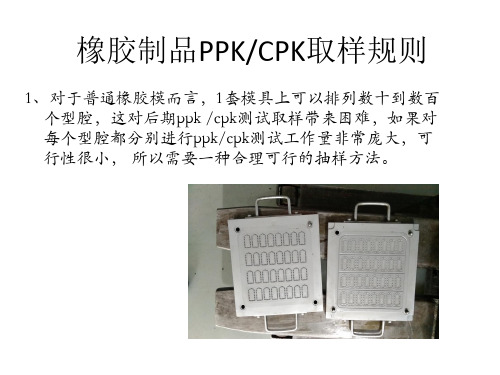
1、对于普通橡胶模而言,1套模具上可以排列数十到数百 个型腔,这对后期ppk /cpk测试取样带来困难,如果对 每个型腔都分别进行ppk/cpk测试工作量非常庞大,可 行性很小, 所以需要一种合理可行的抽样方法。
2、普通橡胶制品一般采取压 制成型工艺,当模具尺寸固定 后可能对产品尺寸产生影响的 主要因素为成型条件,包括以下 三点: ①成型压力 ②成型温度 ③成型时间
3、以上三因素中,成型时间对于某一产品来说设置值是固定 不变的;温度和压力虽然在设置上都有固定值,但实际上 受加热系统和施压系统的制约导致它们在磨具上有不同的 分布: ①温度分度:模具中心 最高,四角温度最低; ②压力分布:中心压力 最大,四角压力最小。 以上两因素会导致产品 尺寸在模具分布上出现 极大和极小值(前提模 具尺寸OK)。
四角处 中心处
4、在了解每模n穴之间的差异后,选取最大和最小pk取样时一般遵守“四角一中” 原则,即每次取样时模具的四角和中心对应型腔各取 1pcs,一次取5pcs,在生产过程中相隔适当时间取6次。
CPK抽样方法范文
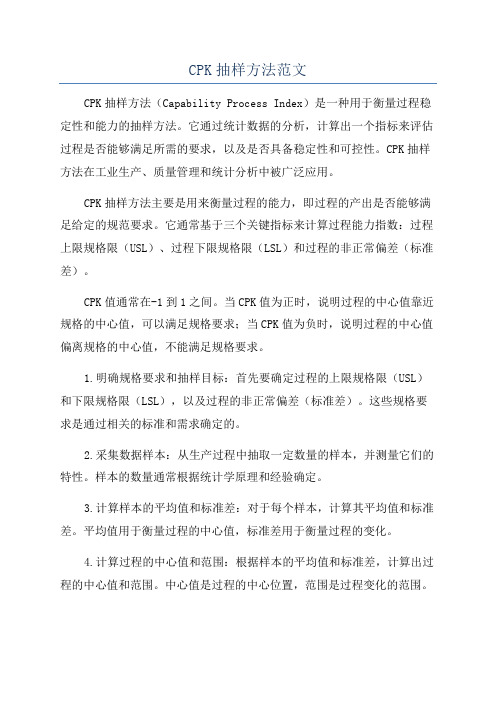
CPK抽样方法范文CPK抽样方法(Capability Process Index)是一种用于衡量过程稳定性和能力的抽样方法。
它通过统计数据的分析,计算出一个指标来评估过程是否能够满足所需的要求,以及是否具备稳定性和可控性。
CPK抽样方法在工业生产、质量管理和统计分析中被广泛应用。
CPK抽样方法主要是用来衡量过程的能力,即过程的产出是否能够满足给定的规范要求。
它通常基于三个关键指标来计算过程能力指数:过程上限规格限(USL)、过程下限规格限(LSL)和过程的非正常偏差(标准差)。
CPK值通常在-1到1之间。
当CPK值为正时,说明过程的中心值靠近规格的中心值,可以满足规格要求;当CPK值为负时,说明过程的中心值偏离规格的中心值,不能满足规格要求。
1.明确规格要求和抽样目标:首先要确定过程的上限规格限(USL)和下限规格限(LSL),以及过程的非正常偏差(标准差)。
这些规格要求是通过相关的标准和需求确定的。
2.采集数据样本:从生产过程中抽取一定数量的样本,并测量它们的特性。
样本的数量通常根据统计学原理和经验确定。
3.计算样本的平均值和标准差:对于每个样本,计算其平均值和标准差。
平均值用于衡量过程的中心值,标准差用于衡量过程的变化。
4.计算过程的中心值和范围:根据样本的平均值和标准差,计算出过程的中心值和范围。
中心值是过程的中心位置,范围是过程变化的范围。
5.计算过程能力指数:根据过程的中心值、范围和规格要求,使用统计学方法计算出过程的能力指数。
常用的计算公式是CPK = min[(USL-中心值)/(3*标准差), (中心值-LSL)/(3*标准差)]。
6.分析结果和改进措施:根据计算得出的CPK值来评估过程的能力。
如果CPK值大于1,说明过程具备稳定性和可控性,可以满足规格要求。
如果CPK值小于1,说明过程存在问题,需要采取改进措施来提高过程的能力。
总之,CPK抽样方法是一种常用的过程能力评估方法,通过统计数据的分析,计算出过程的能力指数,帮助企业了解和提高过程的稳定性和可控性。
CPK抽样方法
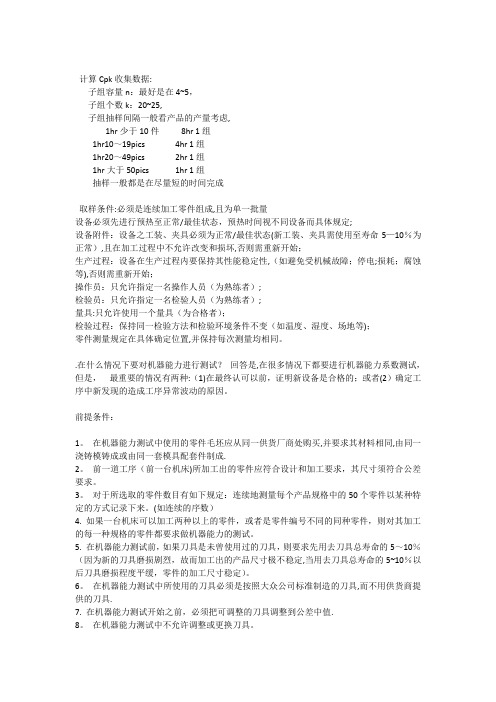
计算Cpk收集数据:子组容量n:最好是在4~5,子组个数k:20~25,子组抽样间隔一般看产品的产量考虑,1hr少于10件8hr 1组1hr10~19pics 4hr 1组1hr20~49pics 2hr 1组1hr大于50pics 1hr 1组抽样一般都是在尽量短的时间完成取样条件:必须是连续加工零件组成,且为单一批量设备必须先进行预热至正常/最佳状态,预热时间视不同设备而具体规定;设备附件:设备之工装、夹具必须为正常/最佳状态(新工装、夹具需使用至寿命5—10%为正常),且在加工过程中不允许改变和损坏,否则需重新开始;生产过程:设备在生产过程内要保持其性能稳定性,(如避免受机械故障;停电;损耗;腐蚀等),否则需重新开始;操作员:只允许指定一名操作人员(为熟练者);检验员:只允许指定一名检验人员(为熟练者);量具:只允许使用一个量具(为合格者);检验过程:保持同一检验方法和检验环境条件不变(如温度、湿度、场地等);零件测量规定在具体确定位置,并保持每次测量均相同。
.在什么情况下要对机器能力进行测试?回答是,在很多情况下都要进行机器能力系数测试,但是,最重要的情况有两种:(1)在最终认可以前,证明新设备是合格的;或者(2)确定工序中新发现的造成工序异常波动的原因。
前提条件:1。
在机器能力测试中使用的零件毛坯应从同一供货厂商处购买,并要求其材料相同,由同一浇铸模铸成或由同一套模具配套件制成.2。
前一道工序(前一台机床)所加工出的零件应符合设计和加工要求,其尺寸须符合公差要求。
3。
对于所选取的零件数目有如下规定:连续地测量每个产品规格中的50个零件以某种特定的方式记录下来。
(如连续的序数)4. 如果一台机床可以加工两种以上的零件,或者是零件编号不同的同种零件,则对其加工的每一种规格的零件都要求做机器能力的测试。
5. 在机器能力测试前,如果刀具是未曾使用过的刀具,则要求先用去刀具总寿命的5~10%(因为新的刀具磨损剧烈,故而加工出的产品尺寸极不稳定,当用去刀具总寿命的5~10%以后刀具磨损程度平缓,零件的加工尺寸稳定)。
CPK
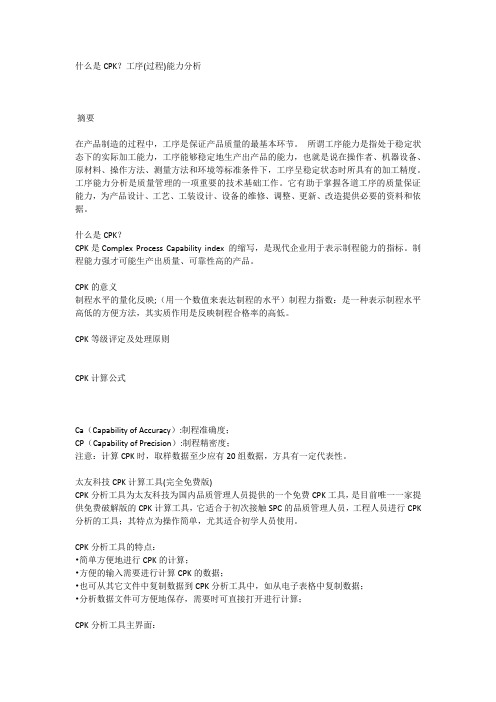
什么是CPK?工序(过程)能力分析摘要在产品制造的过程中,工序是保证产品质量的最基本环节。
所谓工序能力是指处于稳定状态下的实际加工能力,工序能够稳定地生产出产品的能力,也就是说在操作者、机器设备、原材料、操作方法、测量方法和环境等标准条件下,工序呈稳定状态时所具有的加工精度。
工序能力分析是质量管理的一项重要的技术基础工作。
它有助于掌握各道工序的质量保证能力,为产品设计、工艺、工装设计、设备的维修、调整、更新、改造提供必要的资料和依据。
什么是CPK?CPK是Complex Process Capability index 的缩写,是现代企业用于表示制程能力的指标。
制程能力强才可能生产出质量、可靠性高的产品。
CPK的意义制程水平的量化反映;(用一个数值来表达制程的水平)制程力指数:是一种表示制程水平高低的方便方法,其实质作用是反映制程合格率的高低。
CPK等级评定及处理原则CPK计算公式Ca(Capability of Accuracy):制程准确度;CP(Capability of Precision):制程精密度;注意:计算CPK时,取样数据至少应有20组数据,方具有一定代表性。
太友科技CPK计算工具(完全免费版)CPK分析工具为太友科技为国内品质管理人员提供的一个免费CPK工具,是目前唯一一家提供免费破解版的CPK计算工具,它适合于初次接触SPC的品质管理人员,工程人员进行CPK 分析的工具;其特点为操作简单,尤其适合初学人员使用。
CPK分析工具的特点:•简单方便地进行CPK的计算;•方便的输入需要进行计算CPK的数据;•也可从其它文件中复制数据到CPK分析工具中,如从电子表格中复制数据;•分析数据文件可方便地保存,需要时可直接打开进行计算;CPK分析工具主界面:CPK分析工具操作方法:1、清空数据2、输入数据3、进入“分析选项”设置参数4、设置分析规格数据5、设置数据输入及分析区域6、设置计算CPK值的子组大小7、直方图区间分组选择项8、标准差选择方法9、计算CPK值10、文件处理功能说明CPK= Min[ (USL- Mu)/3s, (Mu - LSL)/3s] Cpk应用讲议 1. Cpk的中文定义为:制程能力指数,是某个工程或制程水准的量化反应,也是工程评估的一类指标。
CPK PPK CMK的区别与联系
Ppk、Cpk,还有Cmk三者的区别及计算CPK ppkCPK是过程能力指数。
PPK是性能指数。
CMK是设备能力指数。
CPK和PPK是根据安排好的间隔进行抽样的,每次抽样要连续抽取(其实只要求算PPK时,在最后的所有产品里随即抽样也是可以的,当然顾客死拧就别跟他争这个了)。
CPK与PPK计算公式一样,只是sigma的计算不一样而已,这也就是他们的区别,CPK使用Rbar/d2计算组内变差,PPK用传统的那个公式计算总变差。
CMK是连续抽样的。
总结:CPK与PPK区别在sigma的计算;CMK与PPK区别在于抽样方法。
CPK是间隔取样,但PPK不一定要求间隔取样。
CPK是研究组内变差,而PPK是研究组间变差,CPK是能力指数而PPK是性能指数。
CMK是设备能力Ppk、Cpk,还有Cmk三者的区别及计算1、首先我们先说明Pp、Cp两者的定义及公式Cp(Capability Indies of Process):稳定过程的能力指数,定义为容差宽度除以过程能力,不考虑过程有无偏移。
Pp(Performance Indies of Process):过程性能指数,定义为不考虑过程有无偏移时,容差范围除以过程性能。
(该指数仅用来与Cp及Cpk对比,或/和Cp、Cpk一起去度量和确认一段时间内改进的优先次序)CPU:稳定过程的上限能力指数,定义为容差范围上限除以实际过程分布宽度上限。
CPL:稳定过程的下限能力指数,定义为容差范围下限除以实际过程分布宽度下限。
2、现在我们来阐述Cpk、Ppk的含义Cpk:这是考虑到过程中心的能力(修正)指数,定义为CPU与CPL的最小值。
它等于过程均值与最近的规范界限之间的差除以过程总分布宽度的一半。
即:Ppk:这是考虑到过程中心的性能(修正)指数,定义为:或的最小值。
即:其实公式中的K是定义分布中心μ与公差中心M的偏离度,μ与M的偏离为ε=| M-μ|3、公式中标准差的不同含义①在Cp、Cpk中,计算的是稳定过程的能力,稳定过程中过程变差仅由普通原因引起,公式中的标准差可以通过控制图中的样本平均极差估计得出:因此,Cp、Cpk一般与控制图一起使用,首先利用控制图判断过程是否受控,如果过程不受控,要采取措施改善过程,使过程处于受控状态。
CPK 测算过程与方法
CPK测算过程与方法
1、定义:
计数型:不能通过直接测量得出,例如:固定罩壳.不能直接测量出此工序的相关值,只能计算出固定的数量,数出其中不良品数量.
计量型: 计量型:可以直接通过工具或是仪器测量出所需数值或数据的工序.例如:封箱就可以通过测量封箱胶带的长度.此工序就为计量型.
2、此次只对讲量型工位进行CPK测算,计数型工位此次不需要制作.
3、CPK测算的六个步骤:
第一步:确定质量特性:质量特性为为工艺要求的质量控制范围
第二步:确定抽样方法:确定样本的抽取方式
第三步:确定测量方法:确定测量工具及测量方法
第四步:计算实测CPK值:通过转换软件或卡利特软件进行测计算工序CPK值
第五步:CPK定义分极:根据CPK 测算等级进行分极,确定是否需要改进
第六步: CPK分析改进: 通过5M1E对不合格工序进行分析改进
(选取一个需要测算的计量型工位,然后根据其质量特性记录测量数值,例如:注气.记录下每次注入氟得昂的质量.将记录的数值输入到MINTAB中,规定出上下限值后.就可以得出CPK值.根据CPK 测算等级进行分极,确定是否需要改进;通过5M1E对不合格工序进行分析改进)
(CPK测算等级表)。
《计算CPK的数据取样原则探讨》
计算CPK的数据取样原则探讨计算Cpk收集数据:子组容量n:最好是在4~5,子组个数k:20~25,子组抽样间隔一般看产品的产量考虑,1hr少于10件8hr 1组1hr10~19pics 4hr 1 组1hr20~49pics 2hr 1 组1hr 大于50pics 1hr 1 组抽样一般都是在尽量短的时间完成计算CmK数据取样原则探讨取样条件:必须是连续加工零件组成,且为单一批量设备必须先进行预热至正常 /最佳状态,预热时间视不同设备而具体规定;设备附件:设备之工装、夹具必须为正常/最佳状态(新工装、夹具需使用至寿命5-10%为正常),且在加工过程中不允许改变和损坏,否则需重新开始;生产过程:设备在生产过程内要保持其性能稳定性,(如避免受机械故障;停电;损耗;腐蚀等),否则需重新开始;操作员:只允许指定一名操作人员(为熟练者);检验员:只允许指定一名检验人员(为熟练者);量具:只允许使用一个量具(为合格者);检验过程:保持同一检验方法和检验环境条件不变(如温度、湿度、场地等);零件测量规定在具体确定位置,并保持每次测量均相同。
.在什么情况下要对机器能力进行测试回答是,在很多情况下都要进行机器能力系数测试,但是,最重要的情况有两种:(1)在最终认可以前,证明新设备是合格的;或者(2)确定工序中新发现的造成工序异常波动的原因。
前提条件:1. 在机器能力测试中使用的零件毛坯应从同一供货厂商处购买, 同,并要求其材料相由同一浇铸模铸成或由同一套模具配套件制成。
2. 前一道工序(前一台机床)所加工出的零件应符合设计和加工要求,其尺寸须符合公差要求。
3. 对于所选取的零件数目有如下规定:连续地测量每个产品规格中的50个零件以某种特定的方式记录下来。
(如连续的序数)4. 如果一台机床可以加工两种以上的零件,或者是零件编号不同的同种零件,则对其加工的每一种规格的零件都要求做机器能力的测试。
5. 在机器能力测试前,如果刀具是未曾使用过的刀具,则要求先用去刀具总寿命的5~10 %(因为新的刀具磨损剧烈,故而加工出的产品尺寸极不稳定,当用去刀具总寿命的5-10%以后刀具磨损程度平缓,零件的加工尺寸稳定)。
计算CPK的数据取样原则探讨
计算CPK的数据取样原则探讨计算Cpk收集数据:子组容量n:最好是在4~5,子组个数k:20~25,子组抽样间隔一般看产品的产量考虑,1hr少于10件8hr 1组1hr10~19pics 4hr 1组1hr20~49pics 2hr 1组1hr大于50pics 1hr 1组抽样一般都是在尽量短的时间完成计算CmK 数据取样原则探讨取样条件:必须是连续加工零件组成,且为单一批量设备必须先进行预热至正常/最佳状态,预热时间视不同设备而具体规定;设备附件:设备之工装、夹具必须为正常/最佳状态(新工装、夹具需使用至寿命5-10%为正常),且在加工过程中不允许改变和损坏,否则需重新开始;生产过程:设备在生产过程内要保持其性能稳定性,(如避免受机械故障;停电;损耗;腐蚀等),否则需重新开始;操作员:只允许指定一名操作人员(为熟练者);检验员:只允许指定一名检验人员(为熟练者);量具:只允许使用一个量具(为合格者);检验过程:保持同一检验方法和检验环境条件不变(如温度、湿度、场地等);零件测量规定在具体确定位置,并保持每次测量均相同。
.在什么情况下要对机器能力进行测试?回答是,在很多情况下都要进行机器能力系数测试,但是,最重要的情况有两种:(1)在最终认可以前,证明新设备是合格的;或者(2)确定工序中新发现的造成工序异常波动的原因。
前提条件:1.在机器能力测试中使用的零件毛坯应从同一供货厂商处购买,并要求其材料相同,由同一浇铸模铸成或由同一套模具配套件制成。
2.前一道工序(前一台机床)所加工出的零件应符合设计和加工要求,其尺寸须符合公差要求。
3.对于所选取的零件数目有如下规定:连续地测量每个产品规格中的50个零件以某种特定的方式记录下来。
(如连续的序数)4.如果一台机床可以加工两种以上的零件,或者是零件编号不同的同种零件,则对其加工的每一种规格的零件都要求做机器能力的测试。
5.在机器能力测试前,如果刀具是未曾使用过的刀具,则要求先用去刀具总寿命的5~10%(因为新的刀具磨损剧烈,故而加工出的产品尺寸极不稳定,当用去刀具总寿命的5~10%以后刀具磨损程度平缓,零件的加工尺寸稳定)。
- 1、下载文档前请自行甄别文档内容的完整性,平台不提供额外的编辑、内容补充、找答案等附加服务。
- 2、"仅部分预览"的文档,不可在线预览部分如存在完整性等问题,可反馈申请退款(可完整预览的文档不适用该条件!)。
- 3、如文档侵犯您的权益,请联系客服反馈,我们会尽快为您处理(人工客服工作时间:9:00-18:30)。
计算Cpk收集数据:
子组容量n:最好是在4~5,
子组个数k:20~25,
子组抽样间隔一般看产品的产量考虑,
1hr少于10件8hr 1组
1hr10~19pics 4hr 1组
1hr20~49pics 2hr 1组
1hr大于50pics 1hr 1组
抽样一般都是在尽量短的时间完成
取样条件:必须是连续加工零件组成,且为单一批量
设备必须先进行预热至正常/最佳状态,预热时间视不同设备而具体规定;
设备附件:设备之工装、夹具必须为正常/最佳状态(新工装、夹具需使用至寿命5-10%为正常),且在加工过程中不允许改变和损坏,否则需重新开始;
生产过程:设备在生产过程内要保持其性能稳定性,(如避免受机械故障;停电;损耗;腐蚀等),否则需重新开始;
操作员:只允许指定一名操作人员(为熟练者);
检验员:只允许指定一名检验人员(为熟练者);
量具:只允许使用一个量具(为合格者);
检验过程:保持同一检验方法和检验环境条件不变(如温度、湿度、场地等);
零件测量规定在具体确定位置,并保持每次测量均相同。
.在什么情况下要对机器能力进行测试?回答是,在很多情况下都要进行机器能力系数测试,但是,最重要的情况有两种:(1)在最终认可以前,证明新设备是合格的;或者(2)确定工序中新发现的造成工序异常波动的原因。
前提条件:
1. 在机器能力测试中使用的零件毛坯应从同一供货厂商处购买,并要求其材料相同,由同一浇铸模铸成或由同一套模具配套件制成。
2. 前一道工序(前一台机床)所加工出的零件应符合设计和加工要求,其尺寸须符合公差要求。
3. 对于所选取的零件数目有如下规定:连续地测量每个产品规格中的50个零件以某种特定的方式记录下来。
(如连续的序数)
4. 如果一台机床可以加工两种以上的零件,或者是零件编号不同的同种零件,则对其加工的每一种规格的零件都要求做机器能力的测试。
5. 在机器能力测试前,如果刀具是未曾使用过的刀具,则要求先用去刀具总寿命的5~10%(因为新的刀具磨损剧烈,故而加工出的产品尺寸极不稳定,当用去刀具总寿命的5~10%以后刀具磨损程度平缓,零件的加工尺寸稳定)。
6. 在机器能力测试中所使用的刀具必须是按照大众公司标准制造的刀具,而不用供货商提供的刀具。
7. 在机器能力测试开始之前,必须把可调整的刀具调整到公差中值。
8. 在机器能力测试中不允许调整或更换刀具。
9. 在机器能力测试中如果出现机械故障,如测试中刀具损坏。
停电、则必须重新
开始测试。
10. 机器能力测试只允许在已经预热0.5~1小时的机器上进行,对不同的机器来说预热的情况是不同的。
11. 在机器能力测试中,对零件的测量必须按照规定在某个规定的位置上测量。
12. 在统计卡上用连续的对应于加工顺序的数字把测量值记录下来。
13. 确定统计学的特征数据。
14. 计算出Cm和Cmk的值
CPK/PPK/Cmk三者的区别及计算
三者的区别及计算三者的区别及计算
16. CPK是过程能力指数。
PPK是性能指数。
CMK是设备能力指数。
CPK和PPK是根据安排好的间隔进行抽样的,每次抽样要连续抽取(其实要只要求算PPK在最后的所有产品里随即抽样也是可以的,当然顾客死拧就别根他争这个了)。
CPK与PPK计算公式一样,只是sigma的计算不一样而已,这也就是他们的区别,
CPK使用Rbar/d2计算组内变差,PPK用传统的那个公式计算总变差。
CMK是连续抽样的,既然没分组当然计算sigma时就不会用到CPK的公式了,是的
也用哪个传统公式计算sigma。
总结:CPK与PPK区别在sigma的计算;CMK与PPK区别在于抽样方法。
CPK是间隔取样但PPK不一定要求间隔取样CPK是研究组内变差而PPK是研究组间变差CPK 是能力指数而PPK是性能指数.
CMK是设备能力
Ppk、Cpk,还有Cmk三者的区别及计算
1、首先我们先说明Pp、Cp两者的定义及公式
Cp(Capability Indies of Process):稳定过程的能力指数,定义为容差宽度除以过程能力,不考虑过程有无偏移,一般表达式为:
Pp(Performance Indies of Process):过程性能指数,定义为不考虑过程有无偏移时,容差范围除以过程性能,一般表达式为:
(该指数仅用来与Cp及Cpk对比,或/和Cp、Cpk一起去度量和确认一段时间内改进的优先次序)
CPU:稳定过程的上限能力指数,定义为容差范围上限除以实际过程分布宽度上限,
一般表达式为:
CPL:稳定过程的下限能力指数,定义为容差范围下限除以实际过程分布宽度下限,
一般表达式为:
2、现在我们来阐述Cpk、Ppk的含义
Cpk:这是考虑到过程中心的能力(修正)指数,定义为CPU与CPL的最小值。
它等
于过程均值与最近的规范界限之间的差除以过程总分布宽度的一半。
即:
Ppk:这是考虑到过程中心的性能(修正)指数,定义为:或的最小值。
即:
其实,公式中的K是定义分布中心μ与公差中心M的偏离度,μ与M的偏离为ε=| M-μ| ,则:
于是,,
3、公式中标准差的不同含义
①在Cp、Cpk中,计算的是稳定过程的能力,稳定过程中过程变差仅由普通原因引
起,公式中的标准差可以通过控制图中的样本平均极差估计得出:
因此,Cp、Cpk一般与控制图一起使用,首先利用控制图判断过程是否受控,如果
过程不受控,要采取措施改善过程,使过程处于受控状态。
确保过程受控后,再计
算Cp、Cpk。
②由于普通和特殊两种原因所造成的变差,可以用样本标准差S来估计,过程性能指数的计算使用该标准差。
即:
4、几个指数的比较与说明
①无偏离的Cp表示过程加工的均匀性(稳定性),即“质量能力”,Cp越大,这质量特性的分布越“苗条”,质量能力越强;而有偏离的Cpk表示过程中心μ与公差中心M的偏离情况,Cpk越大,二者的偏离越小,也即过程中心对公差中心越“瞄准”。
使过程的“质量能力”与“管理能力”二者综合的结果。
Cp与Cpk的着重点不同,需要同时加以考虑。
②Pp和Ppk的关系参照上面。
③关于Cpk与Ppk的关系,这里引用QS9000中PPAP手册中的一句话:“当可能得
到历史的数据或有足够的初始数据来绘制控制图时(至少100个个体样本),可以
在过程稳定时计算Cpk。
对于输出满足规格要求且呈可预测图形的长期不稳定过程,
应该使用Ppk。
”
④另外,我曾经看到一位网友的帖子,在这里也一起提供给大家(没有征得原作者本人同意,在这里向原作者表示歉意和感谢),上面是这样写的:
“所谓PPK,是进入大批量生产前,对小批生产的能力评价,一般要求≥1.67;而CPK,是进入大批量生产后,为保证批量生产下的产品的品质状况不至于下降,且为保证与小批生产具有同样的控制能力,所进行的生产能力的评价,一般要求≥1.33;
一般来说,CPK需要借助PPK的控制界限来作控制。
…
Cpk Ppk Cmk的用法:Cpk: 大批量生产的长期的过程能力控制,要求>1.33;
Ppk: 小批量生产或订单量不大,不连续,要求>1.67;
Cmk: 新设备、检修后的设备或新产品试产,对设备能力的评估,至少50件样品,要求>2.0;
PPK 人机料法环测不变最好是一个批次的全部取样或部分抽样测出的值按照PPK的计算方法计算出来的值由于是在一个批次内取样变差较小看的是组内差异一般用于试做阶段所以汽车行业要求PPK>1.67一般所计算出来的控制线也作为以后量产时的控制线
CPK则是在人机料法环测有变化的情况每班或每天抽样计算的是组间差异由于组间差异毕竟是大于组内差异的所以要求CPK>1.33
CMK算的是机器能力指数。