GCr15轴承钢冶炼工艺优化
gcr15轴承钢球的热处理工艺及质量控制

gcr15轴承钢球的热处理工艺及质量控制
GCr15轴承钢球是一种高强度、高硬度、高耐磨性的工业材料,广泛应用于各种机械设备中。
为了保证GCr15轴承钢球的高品质和长寿命,必须采用适当的热处理工艺和严格的质量控制。
GCr15轴承钢球的热处理工艺主要包括:淬火、回火、正火、退火、球磨等。
其中,淬火是最关键的一个步骤,其目的是使钢球表面形成一层硬度高、强度大的贝氏体组织,从而提高其抗磨损性能和耐久性。
回火则是为了消除淬火过程中产生的残余应力和脆性,使钢球具有足够的韧性和塑性,以防止在使用过程中出现断裂等问题。
质量控制方面,需要对GCr15轴承钢球进行严格的化学成分、物理性能、金相组织、尺寸和形状等检测和测试。
特别是球面粗糙度、硬度、圆度和表面质量等指标的控制,直接影响到钢球的使用寿命和性能表现。
总之,GCr15轴承钢球的热处理工艺和质量控制是保证其优良性能和长寿命的重要保障,需要科学、严谨地操作和检测。
- 1 -。
GCr15轴承钢工艺改进及性能研究

ProcessImprovementandPerformanceStudyofGCr15BearingSteel
WangZhi-feng1,2,RenHui-ping1,FangQi1
(1.SchoolofMaterialandMetallurgy,InnerMongoliaUniversityofScienceandTechnology, Baotou014010,InnerMongoliaAutonomousRegion,China;
些问题[2]。为了完善 GCr15生产工艺,提升与稳定 产品质量,对化学成分、钢液洁净度及碳偏析、坯料 的质量及轧制温度、斯太尔摩冷却等主要质量控制 因素进行优化;完善工艺流程、工艺参数、各工序质 量控制点和关键指标控制措施等工艺技术指导文 件,并对技术操作进行规范,最终提高了线材的表面 质量并改善了热轧组织。
钢坯运入→成批称重→入库存放→炉前上料→ 钢坯质量检查→单支称重→加热→粗轧→切头尾→ 中轧→预精轧(轧间水冷)→切头尾→精轧(轧间水 冷)→穿水冷却→吐丝成圈→散卷冷却→集卷→切 头尾→压紧打捆→称重挂牌→卸卷→入库。线材在 轧制过程中要严格控制轧制温度和时间。
2 结果分析与讨论
2.1 冶炼 炼钢 共 组 织 试 生 产 多 个 批 次,118m 定 尺
GCr15是一种高硬度、高耐磨且合金含量较少 的高碳铬轴承钢,经热处理后具有较高的硬度、均匀 的组织、良好的耐磨性、高接触疲劳性,可用作承受 大负荷,要求高耐磨性、高弹性极限、高接触疲劳强 度的机械 零 件 及 各 种 精 密 量 具 冷 冲 模 等[1]。 该 钢 冷加工塑性中等,切削性能一般,焊接性能差,对形 成白点敏感性大,有回火脆性,在应用推广中存在一
收稿日期:2017-12-11 作者简介:王智峰(1987-),男,内蒙古包头市人,在读硕士,工程师,现从事生产管理工作。
CBN刀片硬车削GCr15轴承钢表面粗糙度的切削参数优化
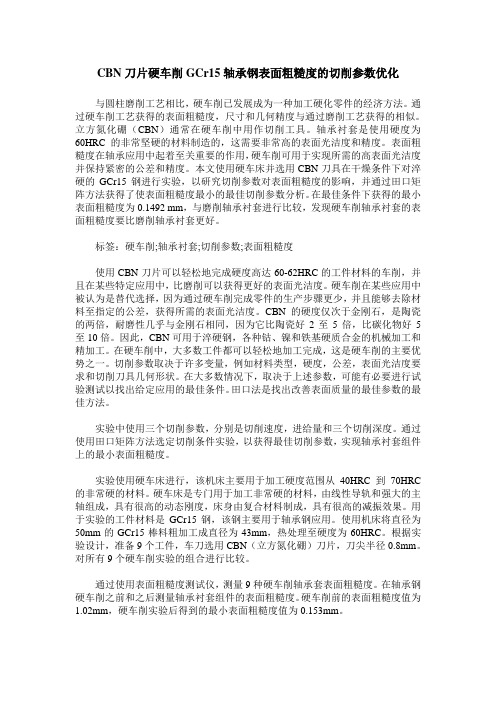
CBN刀片硬车削GCr15轴承钢表面粗糙度的切削参数优化与圆柱磨削工艺相比,硬车削已发展成为一种加工硬化零件的经济方法。
通过硬车削工艺获得的表面粗糙度,尺寸和几何精度与通过磨削工艺获得的相似。
立方氮化硼(CBN)通常在硬车削中用作切削工具。
轴承衬套是使用硬度为60HRC的非常坚硬的材料制造的,这需要非常高的表面光洁度和精度。
表面粗糙度在轴承应用中起着至关重要的作用,硬车削可用于实现所需的高表面光洁度并保持紧密的公差和精度。
本文使用硬车床并选用CBN刀具在干燥条件下对淬硬的GCr15钢进行实验,以研究切削参数对表面粗糙度的影响,并通过田口矩阵方法获得了使表面粗糙度最小的最佳切削参数分析。
在最佳条件下获得的最小表面粗糙度为0.1492 mm,与磨削轴承衬套进行比较,发现硬车削轴承衬套的表面粗糙度要比磨削轴承衬套更好。
标签:硬车削;轴承衬套;切削参数;表面粗糙度使用CBN刀片可以轻松地完成硬度高达60-62HRC的工件材料的车削,并且在某些特定应用中,比磨削可以获得更好的表面光洁度。
硬车削在某些应用中被认为是替代选择,因为通过硬车削完成零件的生产步骤更少,并且能够去除材料至指定的公差,获得所需的表面光洁度。
CBN的硬度仅次于金刚石,是陶瓷的两倍,耐磨性几乎与金刚石相同,因为它比陶瓷好2至5倍,比碳化物好5至10倍。
因此,CBN可用于淬硬钢,各种钴、镍和铁基硬质合金的机械加工和精加工。
在硬车削中,大多数工件都可以轻松地加工完成,这是硬车削的主要优势之一。
切削参数取决于许多变量,例如材料类型,硬度,公差,表面光洁度要求和切削刀具几何形状。
在大多数情况下,取决于上述参数,可能有必要进行试验测试以找出给定应用的最佳条件。
田口法是找出改善表面质量的最佳参数的最佳方法。
实验中使用三个切削参数,分别是切削速度,进给量和三个切削深度。
通过使用田口矩阵方法选定切削条件实验,以获得最佳切削参数,实现轴承衬套组件上的最小表面粗糙度。
GCr15轴承钢235mm×265mm方坯连铸工艺的优化

GCr15轴承钢235mm×265mm方坯连铸工艺的优化
王超;袁守谦;陈列;王德炯;张兵
【期刊名称】《特殊钢》
【年(卷),期】2009(030)002
【摘要】西宁特钢的GCr15轴承钢连铸坯由90 t UHP Consteel EAF-LF(VD)-CC流程生产.通过全程保护浇铸,钢中平均氧含量减少3.15×10-6;控制钢水过热度≤20℃,拉速0.7~0.8 m/min,二次冷却比水量0.40 L/kg,铸坯平均等轴晶率≥60%,且铸坯质量明显提高;在上述优化工艺参数下,采用3.25 Hz/250 A结晶器电磁搅拌和20 Hz/300 A凝固末端电磁搅拌,铸坯中心碳偏析指数为0.99~1.20.
【总页数】2页(P48-49)
【作者】王超;袁守谦;陈列;王德炯;张兵
【作者单位】西安建筑科技大学冶金工程学院,西安,710055;西安建筑科技大学冶金工程学院,西安,710055;西宁特钢股份有限公司,西宁,810000;西宁特钢股份有限公司,西宁,810000;西安建筑科技大学冶金工程学院,西安,710055
【正文语种】中文
【中图分类】TF7
【相关文献】
1.优化GCr15轴承钢连铸工艺参数实践 [J], 张建设;赵瑞华;邢梅峦;刘宪民;张家泉
2.莱钢大方坯合金钢连铸工艺优化 [J], 刘金玲
3.西宁特殊钢厂235mm×265mm大方坯合金钢连铸机 [J], 王小玲;吴耀中
4.简析高锰钢小方坯冶炼连铸工艺优化 [J], 汪敏
5.45#钢方坯连铸工艺优化实践 [J], 程建军;韦耀环;周律敏;袁友多;刘前;韦宝祖因版权原因,仅展示原文概要,查看原文内容请购买。
首钢80tLD-LF-VD-CC生产GCr15轴承钢的工艺实践
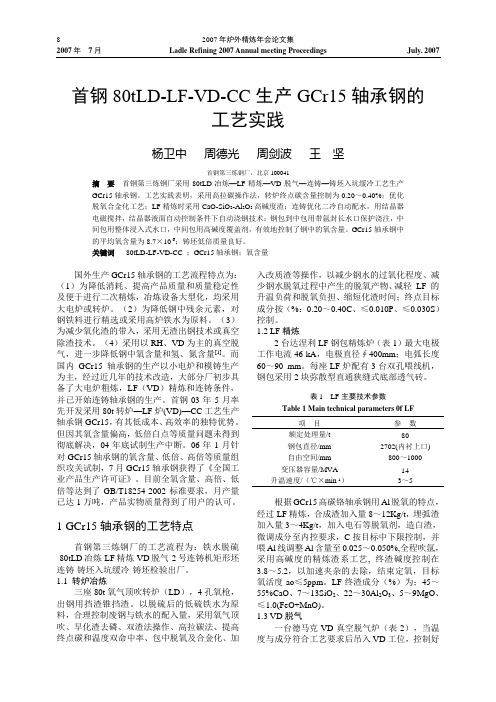
1)首钢第三炼钢厂在国内率先采用80tLD冶炼-LF精炼-VD脱气-CC工艺流程生产GCr15轴承钢,生产顺行,质量稳定,去年7月经国家质量监督检验检疫总局的审查,获得了《全国工业产品生产许可证》。
2)经过对转炉、精炼、连铸工艺的不断优化,钢水的纯净度不断提高,GCr15轴承钢的[O]含量从04年平均为13ppm降至目前平均为8.7ppm的好水平;得到了低倍组织良好、高纯净度、C偏析小的连铸坯,棒材质量完全符合GB/T18254-2002和用户要求,月产量已达1万吨。
0.20~0.30
0.30~0.40
≤0.012
≤0.010
1.45~1.55
≤10
≤2
2连铸坯质量与轧材分析
2.1连铸坯低倍组织
根据连铸坯低倍检验结果,铸坯低倍组织均匀细致,表面质量良好,取200mm×200mm铸坯进行酸浸横向低倍检验(N=165),结果为:中心偏析0级,缩孔0~2.0级,中心疏松0~1.0级,角部裂纹0~0.5级,而非金属夹杂物、皮下裂纹、中心裂纹、中间裂纹均为0级。
铸坯定尺长度/m
8.4~10.8
冶金长度/m
21
出坯温度/℃
700
矫直方式
连续矫直
二冷冷却方式(水、雾)
自动配水,气雾冷却
M-EMS
有
铸流保护
有
连铸机平均作业率/%
80
连铸机连浇炉数
15~28
平均浇铸时间/min
36~55
生产能力/万t·a-1
75
1.5 GCr15轴承钢成分要求
按GB/T18254-2002标准生产GCr15的钢材化学成分范围宽、偏析大、表面有划痕,甚至有裂纹,难以满足轴承钢的高质量要求。为确保钢材高纯净度、表面质量、碳化物偏析、成分偏差
优化GCr15轴承钢连铸工艺参数实践

( . 京 科 技 大 学 冶 金 与 生 态 工 程 学 院 ,北 京 10 8 ;2 1北 00 3 .石 家 庄 钢 铁 公 司 ,河 北 石 家 庄
00 3 ) 5 0 1
摘 要 :通 过 对 GC I 铸 工 艺 参数 的对 比试 验 , 找 到 了 最 佳 的 连 铸 工 艺 参 数 ,明 显 l ta d r l d se l v o l m pr ve n r q lt as g bil n ol te sob i usy i i e e o d.
Ke o d :b ai g se l o t u u a t g p o e s a a ee y W r s e rn te ;c n n o s c s n r c s ;p r i i m tr
表 1 3 连铸 机主 要 工 艺 参 数 #
中心偏 析 是 由于连铸 坯凝 固末 期 ,尚未凝 固富 集 偏 析元 素 的 钢 液 流 动造 成 的 。 钢 液 在 凝 固过 程 中 , 由于溶 质元 素在 固液相 中的再 分配 形成 了铸 坯 化 学成 分 的 不 均 匀 性 ,中 心 部 位 C,S ,P含 量 明 显 高于 其它 部位 ,形成 中心 偏 析 。中心 偏析 往往 与
工 艺 改 进 前 ,连铸 坯 经 常 出 现 缩 孔 、 中心 疏 松 、 中心偏 析 等 缺 陷 ,见 图 1 ( 孔 4级 ) 图 2 缩 、 ( 中心疏 松 3级 ,缩孔 1级 )所 示 。在 二 冷 区 ,铸
坯 内外 温度梯 度 大 ,柱 状 晶 发 达 有 时造 成 穿 晶结
构 。如果 二冷 区冷却 不均 匀 ,就会 导致 柱状 晶的生
参数 ,使 铸坯 质量 得到 了 明显 改 善 。
gcr15钢碳化物细化处理工艺

gcr15钢碳化物细化处理工艺该文档旨在介绍GCR15钢碳化物细化处理工艺的研究背景、目的和主要内容。
研究背景:GCR15钢是一种常用的轴承钢,其碳化物细化处理可以提高材料的硬度和耐磨性,从而增强其使用寿命和性能。
因此,对于GCR15钢的碳化物细化处理工艺进行深入研究具有重要的理论和实践意义。
研究背景:GCR15钢是一种常用的轴承钢,其碳化物细化处理可以提高材料的硬度和耐磨性,从而增强其使用寿命和性能。
因此,对于GCR15钢的碳化物细化处理工艺进行深入研究具有重要的理论和实践意义。
研究目的:本文旨在探索并优化GCR15钢的碳化物细化处理工艺,以提高材料的性能和使用寿命。
通过深入分析不同处理参数和工艺条件对钢材性能的影响,为进一步优化制造工艺提供参考和指导。
研究目的:本文旨在探索并优化GCR15钢的碳化物细化处理工艺,以提高材料的性能和使用寿命。
通过深入分析不同处理参数和工艺条件对钢材性能的影响,为进一步优化制造工艺提供参考和指导。
研究目的:本文旨在探索并优化GCR15钢的碳化物细化处理工艺,以提高材料的性能和使用寿命。
通过深入分析不同处理参数和工艺条件对钢材性能的影响,为进一步优化制造工艺提供参考和指导。
研究目的:本文旨在探索并优化GCR15钢的碳化物细化处理工艺,以提高材料的性能和使用寿命。
通过深入分析不同处理参数和工艺条件对钢材性能的影响,为进一步优化制造工艺提供参考和指导。
主要内容:本文将从以下几个方面展开研究:主要内容:本文将从以下几个方面展开研究:主要内容:本文将从以下几个方面展开研究:主要内容:本文将从以下几个方面展开研究:碳化物细化处理工艺的基本原理碳化物细化处理工艺的基本原理碳化物细化处理工艺的实验设计和方法不同处理参数对GCR15钢材性能的影响工艺参数优化及性能改善方案结论和展望通过对GCR15钢碳化物细化处理工艺的研究,我们期望能够为提高钢材性能和使用寿命提供有效的工艺改进方案,为相关领域的发展和应用做出贡献。
连铸生产GCr15轴承钢工艺的改进

3 - 1
GC r15 钢是 一种 合金 含量较 少、 具有 良好性 能、 应用 最 广泛的高碳铬轴承钢。由于其使用环境 的特殊性 , 用户 对其 质量提出较为严格的要 求。 GCr15 钢 的特点 是两相 区宽 , 柱 状晶发达 , 易产生 中心疏 松和 偏析 , 生产 过程 中对 于连铸 工 艺的精 确控制 要求非 常严格。虽 然 GC r15 低过 热度浇注 有 利 , 可减轻中心疏松和偏析的缺陷 , 但过 热度低 , 可导致 钢水 在水口冻结 , 造 成生 产事故 , 不 利于 连续生 产。本钢 特钢 厂 生产 GC r15 钢时 , 中间包过 热度控 制在 10 ~ 20 , 出现因 中 包过热度低而发生 冻钢 事故造 成断 浇。铸坯 拉速 和负滑 动 时间等因素 , 影响 结晶器 保护 渣的润 滑作 用 , 使铸 坯表面 振 痕较深。经过对连铸工艺过程的改进 , 连铸生 产的 G Cr15 低 倍合格率明显提高 , 带状组 织合格率达 100% 。
弧形半径 /mm 台数 机数 流数
流间距 /mm 断面 /mm mm 中间包工作容量 / t 中间包控流方式 设计年产量 / t
自 2006 年本钢特 钢厂 连铸 生产轴 承钢 以来 , 采 用的 连 铸工艺参数见 表 2。由 于对 连铸 生产 轴承 钢的 生产 经验 不 足 , 工艺参数选取不尽合理 , 出现一些质量问题和生产事故 ,
经过对连铸工艺过程的改进连铸生产的gcr15倍合格率明显提高带状组织合格率达100有必要对连铸工艺参数进行优化调整原有的连铸工艺参数液相线1447102017026430改进后连铸生产gcr15的工艺条件根据生产实际情况和产品检验结果结合查阅相关文献gcr15钢的连铸工艺参数进行优化调整具体参数见表连铸工艺的优化参数原有连铸生产gcr15的工艺条件本钢特钢厂连铸机主要参数见表连铸机的主要参数14472524470弧形半径mm台数间距mm断面mmmm中间包工作容量优化后的过热度和拉速150001515202030303535404065180023526519中间包控流方式设计年产量塞棒自动控流4800002006年本钢特钢厂连铸生产轴承钢以来采用铸工艺参数见表2
- 1、下载文档前请自行甄别文档内容的完整性,平台不提供额外的编辑、内容补充、找答案等附加服务。
- 2、"仅部分预览"的文档,不可在线预览部分如存在完整性等问题,可反馈申请退款(可完整预览的文档不适用该条件!)。
- 3、如文档侵犯您的权益,请联系客服反馈,我们会尽快为您处理(人工客服工作时间:9:00-18:30)。
炼钢生产中,脱氧剂一般为Fe-Si、Fe-Mn、A1 等,但是相应的脱氧产物Si02、MnS、AI:03等很 难从钢中完全去除而成为钢中的夹杂物,对轴承
硼([C])≥o.08%,在此基础上进行脱氧工艺试
验,按照设计的取样方案,对不同脱氧精炼工艺过
程取样分析钢中氧含量,选取有代表性的4炉分
析结果,如表3所示。
试验用Ba—Si合金粒度设计为10~100 rain。 另一种脱氧剂是铝铁,为西钢熔炼的产品,其铝质 量分数在45%"-50%的范围内,表中用“Al”表 示。
2.2脱氧工艺试验
脱氧试验分为预脱氧和终脱氧,脱氧剂设计 方案为Al、Al+Ba—Si合金。作为预脱氧剂Ba-Si 合金在Consteel电炉出钢过程中加入钢包中,而 作为终脱氧剂时,则是在精炼的过程中加入。结 合实际生产工艺,对预脱氧剂和终脱氧剂的配比 及单位用量进行了设计,具体见表2。
the results the smelting and refining processes of the GCrl 5 bearing steel were optimized and the cleanliness of the liquid steel prominently improved. Key words:bearing steel;cleanliness;deoxidizer;process optimization
2.Xining Special Steel Co.,Ltd.,Xining 8 1 0000,China) Abstract:One of the key factors to improve the bloom quality is the cleanliness of steel. Appropriate selection of the steel—making process
万方数据
第4期
王超,等:GCrl5轴承钢)台炼工艺优化 有减少的空间。
・23・
熔化时间增加了1 min,但是钢包的平均寿命提 高了4次。虽然2号精炼渣的平均冶炼时间有所 减少,但还是略显时间长,这主要是由于实验炉 次的原因,操作上不紧凑,因而平均冶炼时间还
3.2.2氧含量和夹杂物的比较
通过两种精炼渣系在精炼中的试验,取样分 析钢中氧含量和夹杂物。如表7、表8所示。
供低磷、温度合适和化学成分控制准确的钢水,减 少精炼炉的负担。在原有的工艺下,Consteel电炉 采用大供氧量操作以及操作上的不协同,造成出钢 终点碳含量偏低,不仅影响金属物料与合金料的收 得率,而且使氧化终点钢水中氧的含量偏高,增加 了炉后脱氧的负担,导致成本上升。对终点碳的准 确控制。可参考图1碳氧平衡曲线所示[4]。
Optimization of steelmaking process for GCrl 5 bearing steel bloom WANG Cha01,YUAN Shou—qianl,CHEN De-j ion8a,ZHANG Bin91
Lid,WANG
(1.Xi'an University of Architecture and Technology,Xi'an,710055,China;
基金项目:陕西省教育厅专项基金(05JK248)
生产过程中存在以下问题:(1)氧含量较高,而且 不稳定,氧质量分数平均在15×10“左右,高于 国内10×10“以下的先进水平;(2)夹杂物细系 夹杂物级别较高,粗系夹杂物也有出现。根据西 钢的设备和工艺(UHP
Consteel
EAF—LF/VD
CC),制定高碳铬轴承钢冶炼工艺优化方案、脱氧 剂和精炼渣组成设计的试验方案,以提高钢液的 纯净度,为连铸提供质量稳定的钢液。
1.2
试验材料
对试验所选用批次的硅钡合金取样分析,对
应的国标成分要求(GB/T15710—1995)和分析的 化学成分如表1所示。
表1硅钡合金的化学成分
电炉冶炼工艺的优化
初炼炉为Consteel电弧炉,主要任务是快速提
类别百—丁1—等1—r了
国标要求≥15.0≥50.0≤3.0≤0.40≤O.30≤O.04≤o.04 取样分析t>17.37/>52.32≤2.6≤o.40≤o.20≤().04≤0.04
3.1
试验方案
对设计的新精炼渣(2号)与原精炼渣(1号)
进行冶金效果对比试验,分别在LF进行5炉次 试验。两种精炼渣化学成分分析如表5所示。
注:表中数据横线上方为范围值,横线下方为平均值。
表5不同精炼渣的化学成分
分析表3和表4中的数据,从中可以得出,采 用铝与硅钡合金共同处理轴承钢,特别是以硅钡 合金进行终脱氧处理钢水,即实验方案2和方案 4,不仅可以进一步降低钢中的氧含量,而且消除 了钢中点状夹杂物,同时,钢中的脆性夹杂有所降 低。这是钡参与脱氧、脱硫反应,其反应速度很 快,初生夹杂物含钡量高,并且在10 s内能够全 部上浮。
as
well
as
the pre-oxidizer,final deoxi—
dizer and refining slag and their compositions will directly affect the the cleanliness of
liquid steel and the quality of the bloom.In view of the deficiency of the smelting and
refining processes
of the GCrl 5
bearing steel previously implemented
an
optimized
as
scheme was put forward and the industrial scale experiment carried out promptly and
现。精炼渣的碱度、氧化性(FeO+MnO)及仙Q对
钢液的脱硫、脱氧及夹杂的去除有很大的影响。 高碱度渣具有较低的氧势和较高的CaO活 度,有利于脱硫,但碱度过大,精炼渣的熔化温度 升高,黏度增加,造成精炼渣流动性恶化,直接影 响精炼脱氧和脱硫效果。特别是对轴承钢来说, 渣中CaO活度增加,会使点状夹杂增加。研究表 从表6可以看出,虽然2号精炼渣的脱硫率 小于1号精炼渣,但对2号精炼渣的精炼效果分 析发现,使用2号精炼渣也能有效控制钢中平均 硫质量分数小于0.025%,符合标准规定的含 量;由于2号渣中CaF2配加量的减少,精炼渣的
3.2试验结果分析
试验主要考查新精炼渣的脱硫能力,以及考 查对钢中的氧含量和夹杂物分布等级的影响。
3.2.1脱硫
1号精炼渣与2号精炼渣经过5炉次对比试 验,经过数据分析认为有好的精炼效果,并将2号 精炼渣投入使用,对数据进行统计整理见表6。
表6新旧渣精炼效果的对比
3精炼渣系的优化
在LF精炼中,精炼渣具有脱氧、脱硫的作用, 而精炼渣泡沫化后,可以进行埋弧操作并且稳定电 弧,保护炉盖等耐火材料,且具有提高热效率、吸附 夹杂等多种功能。这些功能的实现条件是要具有 合理成分结构的精炼渣,通过大量的试验研究发
・20・
2009年8月 第25卷第4期
炼钢
Steelmaking
Aug.2009 V01.25 No.4
GCrl 5轴承钢冶炼工艺优化
王超1,袁守谦1,陈列2,王德炯2,张兵1
(1.西安建筑科技大学冶金工程学院,陕西西安710055;2.西宁特钢股份有限公司,青海西宁810000)
摘要:钢液的纯净度是提高轴承钢连铸坯质量的关键因素之一,而冶炼工艺以及预脱氧剂、终脱氧 剂、精炼渣的合理选择及成分组成.直接影响钢液的纯净度和铸坯的质量。针对GCrl5轴承钢冶炼和 精炼工艺中的不足,提出优化方案,并进行工业性试验,优化了轴承钢的冶炼、精炼工艺,使钢液的纯净 度得到显著的提高。 关键词:轴承钢;纯净度;脱氧剂;工艺优化 中图分类号:TF762.4文献标识码:B文章编号:1002-1043(2009)04-0020-04
表7两种精炼渣生产的轴承钢氧含量和夹杂物评级
由表7可以看出,采用2号精炼渣后,A类夹 杂物减少,D类夹杂物消除了,虽然钢中的训(O)降 低了2.5
X
钢入炉量,严格控制吹氧的工艺参数,从源头保证
钢的洁净度; (2)在轴承钢冶炼中,选用铝与硅钡合金进行 脱氧处理,特别是以硅钡合金进行终脱氧,不仅使 钢中的氧含量进一步降低,而且消除了钢中点状 夹杂物,同时,使钢中的脆性夹杂有所减少, (3)在精炼过程中,低碱度精炼渣和硅钡合金 终脱氧工艺的有机结合,不仅能有效去除钢中的 点状夹杂物,改变夹杂物的形态,而且能有效地控 制硫含量。
王超,等:GCrl5轴承钢>台炼工艺优化
・21
・
钢而言,会使其疲劳寿命降低。近些年的研究表 明IS-6],碱土金属作为脱氧剂,尤其是含钡合金在 脱氧及夹杂物的变性方面有显著作用而得到了广 泛应用。结合西钢的实际情况,选择硅钡合金和 铝为脱氧剂,进行了优化脱氧剂的试验。
2.1
1.1原料制度
低熔点有色金属元素如As、Sn、Te、Bi、Pb元 素的带入,会使轴承表面出现软点、硬度不均等, 国内外的相关标准和技术协议对此都有严格的规 定。因而,为了降低钢水中的杂质含量,应严格控 制入炉废钢的质量,采用精料原则,减少含有色金 属元素的废钢人炉量。具体方案为适当多配S、P 含量低的生铁,每炉配加量为20一-.30 t,同时减少 进口废钢配加量,控制每炉配加量15 t以下,其 余为国产废钢。
1
Consteel电弧炉工艺优化
Consteel电弧炉冶炼环节直接或间接的影响
钢液纯净度,对入炉原料和电弧炉冶炼工艺进行 优化,从源头上有效地控制钢水中有害元素和夹
作者简介:王超(1969一).男.西安建筑科技大学冶金工程学院,讲师,博士生,从事电弧炉、连铸新技术的研究以及连铸的数值模拟。