塑胶产品常见缺陷及改善办法(1).
塑胶件常见缺陷不良分析及对策讲解
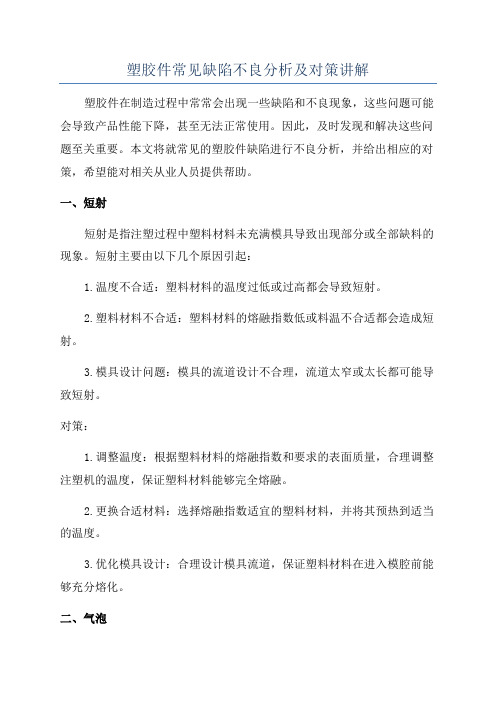
塑胶件常见缺陷不良分析及对策讲解塑胶件在制造过程中常常会出现一些缺陷和不良现象,这些问题可能会导致产品性能下降,甚至无法正常使用。
因此,及时发现和解决这些问题至关重要。
本文将就常见的塑胶件缺陷进行不良分析,并给出相应的对策,希望能对相关从业人员提供帮助。
一、短射短射是指注塑过程中塑料材料未充满模具导致出现部分或全部缺料的现象。
短射主要由以下几个原因引起:1.温度不合适:塑料材料的温度过低或过高都会导致短射。
2.塑料材料不合适:塑料材料的熔融指数低或料温不合适都会造成短射。
3.模具设计问题:模具的流道设计不合理,流道太窄或太长都可能导致短射。
对策:1.调整温度:根据塑料材料的熔融指数和要求的表面质量,合理调整注塑机的温度,保证塑料材料能够完全熔融。
2.更换合适材料:选择熔融指数适宜的塑料材料,并将其预热到适当的温度。
3.优化模具设计:合理设计模具流道,保证塑料材料在进入模腔前能够充分熔化。
二、气泡气泡是指塑胶件表面或内部出现的小气孔或气泡。
气泡可能导致产品外观不良或性能下降。
气泡的产生主要有以下几个原因:1.塑料材料中含有挥发性成分:一些塑料材料中含有挥发性成分,如果注塑温度过高,这些挥发性成分就会挥发出来形成气泡。
2.模具表面不洁净:如果模具表面不干净或有油污等杂质,气泡就会在塑料注入过程中被吸附在塑料中形成。
3.注塑机压力过高:注塑机压力过高会导致空气被压进模具中,形成气泡。
对策:1.调整注塑温度:根据塑料材料的特性,合理调整注塑温度。
温度过高易导致气泡产生,温度过低则容易短射。
2.模具清洁:保持模具表面干净,定期对模具进行清洗,去除杂质和油污。
3.控制注塑机压力:根据塑料材料的特性和模具的要求,合理控制注塑机的压力,避免空气进入模具。
三、热处理不当塑胶件经过热处理后,如果处理不当,可能导致产品性能下降或出现变形等问题。
常见的热处理问题有:1.温度不合适:热处理时,温度不合适会导致产品硬度不均匀或过硬。
塑胶产品的常见缺陷及分析

塑胶产品的常见缺陷及分析塑料制品是现代生活中不可或缺的一部分。
然而,塑料制品仍然存在一些常见的缺陷,这些缺陷可能导致产品质量下降,甚至无法使用。
下面是一些常见的塑料制品缺陷及其分析。
1.气泡和气孔:塑料制品中的气泡和气孔是由于在制造过程中塑料内部的空气没有完全排除或者在冷却期间塑料表面形成的。
这些气泡和气孔会导致产品表面不光滑,并在应力作用下引起断裂。
减少气泡和气孔的方法包括将塑料完全熔化,并控制良好的冷却过程。
2.毛边和厚度不均:由于模具设计和制造不当,塑料制品的边缘可能会有毛边。
毛边的存在会影响产品的外观和使用寿命。
此外,塑料制品的厚度分布不均匀可能导致产品一些部分容易破裂。
为了解决这些问题,需要优化模具设计,并确保模具制造过程的准确性。
3.烧伤和变色:在注塑过程中,如果温度控制不当,塑料可能会被过热,导致烧伤和变色。
这些问题会影响产品的外观和性能。
要解决这些问题,需要正确控制注塑机的温度和压力,并使用合适的冷却设备。
4.变形和翘曲:塑料制品可能在使用过程中变形或翘曲,这主要是由于应力超过材料的强度限制引起的。
为了避免变形和翘曲,可以通过增加产品的结构设计,加固材料强度或者改变制造过程来提高产品的稳定性。
5.色差:塑料制品可能存在色差,这是由于原料、配方和加工条件的变化引起的。
色差会影响产品的外观一致性。
要解决这个问题,需要优化原料和配方的选择,严格控制加工过程的温度和压力,以确保产品色差的控制在可接受的范围内。
综上所述,塑料制品的常见缺陷包括气泡和气孔、毛边和厚度不均、烧伤和变色、变形和翘曲以及色差。
这些缺陷可能导致产品质量下降,影响外观和性能。
为了解决这些问题,需要优化模具设计、加强原料和配方的控制,严格控制加工过程中的温度和压力。
只有通过严格的质量控制,才能生产出高质量的塑料制品。
塑料件缺陷及改进措施

塑料件缺陷及改进措施塑料件在实际应用中存在一些常见的缺陷,这些缺陷可能会对产品的质量和性能产生负面的影响。
下面将介绍一些常见的塑料件缺陷,并提出相应的改进措施。
1.熔接线痕:在注塑过程中,由于熔融塑料的流动不均匀,容易形成熔接线痕。
这些痕迹可能会导致产品强度降低、疲劳性能差等问题。
改进措施:调整注塑工艺参数,如制定适当的注射速度、保持压力等,以促进塑料的均匀流动,减少熔接线痕的产生。
2.气泡:注塑过程中,由于塑料内含有的气体随着高温熔融逸出,易形成气泡。
气泡会导致产品的密封性能下降、外观质量差等问题。
改进措施:提高注塑设备的真空度,减少气体残留。
此外,在塑料原料中加入消泡剂,能够降低气泡的产生。
3.龟裂:塑料零件在冷却过程中,由于不均匀的收缩率和内应力,易出现龟裂缺陷。
这种缺陷会导致产品的强度下降、易开裂等问题。
改进措施:采用合适的冷却方法,如适当提高冷却介质的温度、均匀冷却等,以减少塑料件的收缩和内应力的产生。
4.比色差:一些塑料件在生产过程中,由于塑料原料的不均匀混合或加工温度控制不当,易形成色差。
这会导致产品的外观质量差,影响产品的整体美观度。
改进措施:严格控制塑料原料的配比,确保原料的均匀混合。
同时,加强对注塑设备的温度控制,保持适当的加工温度,有助于减少温度对产品颜色的影响。
5.纹理不良:在塑料件表面会产生一些不良的纹理,如模具印痕、晶化痕迹等。
这些缺陷会降低产品的表面质量、减少产品的美观度。
改进措施:优化模具的设计和制造工艺,减少模具表面的磨损和粗糙度。
同时,在注塑过程中控制好注塑温度和注塑压力,以减小纹理缺陷的产生。
总而言之,塑料件的缺陷主要体现在熔接线痕、气泡、龟裂、比色差和纹理不良等方面。
为了改善塑料件的质量和性能,应从加工工艺、原料控制、模具改进等方面入手,提高生产工艺的稳定性和可控性。
同时,加强质量检测和监控,及时发现和解决问题,以确保塑料件的质量满足产品要求。
塑胶件常见的缺陷产生原因及解决办法

塑胶件常见的缺陷产生原因及解决办法一、设计方面的缺陷:1.不合理的尺寸设计:塑胶件的尺寸设计不合理可能导致尺寸偏差过大、尺寸不一致等问题。
解决方法是根据塑胶件的具体用途和要求进行合理的尺寸设计,并进行合适的工艺分析和模流分析。
2.没有考虑到材料的特性:不同塑料材料具有不同的热胀冷缩系数、熔融温度等特性,设计时没有考虑到这些特性可能导致尺寸偏差、变形等问题。
解决方法是根据塑料材料的特性进行合适的设计和模具制造选型。
3.模具设计问题:模具设计不合理或者制造质量不过关可能导致塑胶件的缺陷问题。
解决方法是进行合理的模具设计,并选择专业的模具制造厂家。
4.不合理的壁厚设计:塑胶件的壁厚设计不合理可能导致塑胶件变形、收缩不均匀等问题。
解决方法是根据塑胶件的材料特性和实际使用要求进行合理的壁厚设计。
二、材料方面的缺陷:1.材料质量问题:不合格的原料质量可能导致塑胶件出现异味、颜色不均匀等问题。
解决方法是选择合格的塑料原料供应商,并进行原料的严格检验。
2.材料混合不均匀:塑料材料在加工过程中没有充分混合均匀可能导致塑胶件的颜色不均匀等问题。
解决方法是进行充分的原料预处理和混炼,确保塑料材料的均匀性。
3.熔体温度不均匀:塑料材料在注塑过程中温度不均匀可能导致塑胶件尺寸偏差、表面气泡等问题。
解决方法是调整注塑机的温度控制系统,确保熔体温度均匀稳定。
三、工艺方面的缺陷:1.注塑工艺参数设置不当:注塑过程中,如射胶压力、射胶速度、冷却时间等工艺参数设置不当可能导致塑胶件出现尺寸偏差、气泡、表面缺陷等问题。
解决方法是根据塑料的特性和产品要求进行合理的工艺参数设置。
2.模具温控不均匀:模具温度不均匀可能导致塑胶件出现收缩不一致、尺寸偏差等问题。
解决方法是进行模具温度分析和温控系统的优化。
可以采用热流道模具、快速温度控制系统等技术手段解决问题。
3.模具保养不当:模具的使用寿命长,如果没有进行定期的保养和维修可能导致塑胶件出现模纹、模具磨损等问题。
塑件缺陷原因及改善方法

塑件缺陷原因及改善方法塑件是一种常见的工程材料,广泛应用于汽车、家电、电子、医疗设备等领域。
然而,在塑件生产过程中,常常会出现一些缺陷,如气泡、毛刺、热缩、变形等问题,这些缺陷会影响塑件的质量和性能。
因此,了解塑件缺陷的原因,并采取相应的改善方法,对于提高塑件质量和性能具有重要意义。
首先,塑件缺陷的原因有多种,下面是一些常见的原因及相应的改善方法:1.气泡:气泡是塑件生产过程中常见的缺陷,通常是由于原料中含有挥发性成分,或者模具中有气体积聚引起的。
改善方法包括:使用质量稳定的原料,避免使用含有挥发性成分的原料;在塑件生产过程中提高注塑压力,减少气泡的生成;对模具进行定期维护,清除模具中的积聚气体。
2.毛刺:毛刺是塑件表面出现的细小突起,通常是由于模具不平整或模具开合不良引起的。
改善方法包括:对模具进行定期检修和研磨,保持模具的平整度;调整模具开合速度和压力,使开合动作更加平稳;在设计模具时考虑减少毛刺的生成。
3.热缩:塑件在冷却后会发生热缩现象,导致尺寸变小。
这是由于塑料在冷却过程中会收缩引起的。
改善方法包括:在设计模具时考虑塑件的热缩率,合理设置模具尺寸,使得塑件在冷却后能得到正确的尺寸;控制注塑过程中的冷却时间和温度,避免过快或过慢的冷却导致过大的热缩。
4.变形:塑件在注塑过程中可能会发生变形,导致尺寸不准确或形状失真。
这是由于塑料在注塑过程中由于内应力不平衡引起的。
改善方法包括:优化模具设计,使模具在注塑过程中能够充分填充塑料,并保持良好的冷却效果;控制注塑过程的温度、压力和速度,减少内应力的释放。
此外,还有一些其他常见的塑件缺陷,如熔流线、白斑、开裂等。
这些缺陷的原因和改善方法也各不相同,需要具体问题具体分析。
总的来说,塑件缺陷的原因多种多样,通过针对不同的原因采取相应的改善方法,能够有效地提高塑件的质量和性能。
对于塑件生产企业来说,建立完善的质量控制体系,加强原材料的筛选和控制,定期维护和检修模具,改进注塑工艺,都是改善塑件质量和性能的重要措施。
塑胶件常见的缺陷产生原因及解决办法

17.射嘴漏胶
产生原因
解决方法
熔胶筒温度过高
降低熔胶筒温度尤其射嘴段
背压调整不当
适当降低背压及螺杆转速
松退行程不够
增加松退时间,更改射嘴头设计
感谢此文编者的辛勤付出!
浇口不合理
调整模具入口大小或位置
射嘴堵塞
拆除射嘴并进行清理
原料温度过高
降低熔胶筒温度
模具温度不当
重调模具温度
冷却时间不够
增加冷却时间
排气不良
缩水处设排气孔
制品本身或其筋、柱过厚
检讨制品
熔胶筒过大
换较小熔胶筒
螺杆止道环(过胶圈)磨损
拆除螺杆止道环(过胶圈)检查、更换
3.制品粘胶
产生原因
解决方法
填料过饱
脱模油太多
少量或尽量不用
浇道及溢口过大或过小
调整模具入口尺寸或改变其位置
模内空气排除不及
增开排气孔或检查原排气孔是否堵塞
8.流纹
产生原因
解决方法
原料熔融不佳
提高料温、背压,加快螺杆转速
模具温度太低
提高模具温度
注射速度太慢或太快
适当调整注射速度
注射压力太高或太低
适当调整注射压力
原料不洁或渗有他料
检查原料
浇道或浇口太小
加大浇道或浇口
原料内润滑剂不够
增加原料内润滑剂
螺杆止道环(过胶圈)磨损
拆除螺杆止道环(过胶圈)检查、更换
机器能量不够
更换为较大的机器
2.缩水
产生原因
解决方法
模具进胶不足
熔胶量不足
增大熔胶行程
注射压力低
提高注射压力
保压不够
塑胶常见缺陷的原因分析及改善措施
五、易弯曲变形产品的品质要求(三)
产品取出后迅速用 专用治具定型加工, 纠正变形,以达到
品质要求。 注意:按先后顺 序循环进行定型和 加工,要确保每个 产品的定型时间达 到2分钟以上!!
六、注塑缺陷原因分析及改善方法(一)
1、料花/汽花 注塑过程中若原料烘料温度偏低、烘料时间不足、注塑工艺(料温、 背压、残量、注射速度及螺杆转速等)变化都会导致产品出现料花。
下表即为料花产生的原因分析及改善方法:
注塑料花/汽花产生缺陷原因分析及改善方法
材料
原因分析
1、材料没有按烘料条件干燥,烘料温度 或烘料时间不足导致材料干燥不充分
改善对策
1.严格按标准烘料条件烘 料
2.射嘴温度太高
2.降低射嘴温度
3.背压过大或螺杆转速过快 工艺参数
4.料筒内残留料过多(过热分解)
3.降低背压或螺杆转速 4.减少残留量
二、公司注塑制品不良缺陷和作业要求
1.公司注塑制品不良缺陷主要有哪些? 缺胶、披锋、粘模、缩水、顶白、料花/汽花、烧焦、气泡、气纹、夹水 纹、流纹、裂纹、黑点/混色、色差、尺寸NG、赌孔、断柱等 2.作业要求 1)操作工开机前必须向管理人员或品检人员问清楚有关产品开机要求、
品质要求、加工要求、包装要求及留意事项,严禁在不熟悉产品标准 的情况下操作。
背压(5)充分干燥材料
2.金属异常损耗 检查螺杆、炮筒的损伤、腐蚀
3.模具排气不足
(1)降低模具锁模力 (2)模具增加排气
烧焦不良 孔堵不良
七、安全作业要求
1.机器的安全装置主要用来保护人员的安全。 2.开机前首先应检查 。 1)前、后安全门和安全杠的挡板是否有效控制。 2)检查机器是否有漏油、漏水情况. 3)检查模具是否有粘模、压坏模和漏水情况。 3.因炮筒温度高,机器炮筒的下面一律不准放脱模剂、顶针油、防
塑胶件常见缺陷产生的原因及解决方法
塑胶件常见缺陷产生的原因及解决方法1.原材料质量问题:塑胶件常见的原材料问题包括原材料中含有杂质、原料失效、原料配比不正确等。
这些问题会导致塑胶件的质量下降和性能降低。
解决方法是对原材料进行严格的检验和筛选,确保原材料的纯度和质量。
2.模具设计问题:模具设计不合理可能导致塑胶件的缺陷,例如模具壁厚不均匀、模腔表面粗糙等。
解决方法是对模具进行合理设计,确保模具的结构和尺寸满足产品要求,并提高模具的制造工艺和加工精度。
3.注塑工艺问题:注塑过程中的工艺参数设置不当会导致塑胶件出现缺陷,例如温度不稳定、压力不均匀、注射速度过快等。
解决方法是优化注塑工艺参数,确保温度、压力、速度等参数的稳定和均匀。
4.模具磨损和损坏:长时间使用会导致模具磨损和损坏,影响塑胶件的质量和外观。
解决方法是加强模具的保养和维护,定期进行模具清洁和润滑,并进行必要的修复和更换。
5.后道工艺问题:塑胶件的后道加工也可能引发缺陷,例如焊接不牢固、喷涂不均匀等。
解决方法是加强后道工艺的控制,提高工艺的稳定性和一致性。
综上所述,要解决塑胶件常见缺陷的问题,需要从原材料选择、模具设计、注塑工艺、模具维护和后道工艺等方面入手,通过优化和控制各个环节,提高产品的质量和性能。
同时,还需要建立健全的质量管理体系,对生产过程进行全面监控和检测,及时发现和解决问题。
最后,还应该加强员工的培训和技能提升,提高操作技术和质量意识,提高产品的一致性和稳定性。
只有通过不断改进和严格控制,才能有效降低塑胶件的缺陷率,提高产品的质量和市场竞争力。
塑胶件常见缺陷产生的原因及解决方法
塑胶件常见缺陷产生的原因及解决方法一、材料问题1.材料选择不当:选择不适合的塑胶材料或材料质量不达标,容易导致塑胶件的缺陷。
解决方法是根据具体要求选择合适的塑胶材料,并进行必要的材料测试和质量控制。
2.材料批次差异:不同批次的塑胶材料可能存在差异,如流动性、收缩率等,导致成型件的缺陷。
解决方法是进行材料测试和合理的材料配方设计,确保不同批次的材料性能稳定一致。
二、工艺问题1.注塑工艺参数不合理:注塑工艺参数(如注射速度、保压时间等)不合理会导致成型件的缺陷,如短流、气泡等。
解决方法是通过优化注塑工艺参数,使之更加合理和稳定。
2.注塑模具设计和制造问题:模具结构不合理、尺寸精度不达标等问题会导致成型件的缺陷,如模具表面瑕疵、尺寸偏差等。
解决方法是进行合理的模具设计和制造,并进行必要的模具修整和维护。
3.注塑材料温度控制不当:材料温度过高或过低都会导致成型件的缺陷,如熔接线、气泡等。
解决方法是通过调整料筒温度、模具温度等进行合理的温度控制。
4.模具开合不良:模具开合不良或夹模力不足会导致成型件的缺陷,如模具压痕、塌陷等。
解决方法是保持模具开合顺畅,并确保夹模力适当。
三、设计问题1.设计尺寸不合理:设计尺寸过大或过小、壁厚不均匀等问题会导致成型件的缺陷,如尺寸偏差、变形等。
解决方法是根据塑胶件的使用要求和成型工艺特点进行合理的尺寸设计,并进行必要的尺寸优化。
2.设计结构不合理:设计结构复杂、壁薄部位过多等问题容易导致成型件的缺陷,如留痕、焊痕等。
解决方法是简化设计结构、增加加强筋等措施,提高塑胶件的强度和表面质量。
3.装配接口设计不当:塑胶件的装配接口设计不当会导致装配困难、配套件脱落等问题,影响整体使用效果。
解决方法是合理设计装配接口,确保装配紧固可靠。
以上是塑胶件常见缺陷产生的原因及解决方法的概述。
在实际生产中,还需要根据具体情况进行详细分析和解决。
为了确保塑胶件的质量,需要在材料选择、工艺控制和设计优化等方面进行全面的控制和改进。
塑胶件常见的缺陷产生原因及解决办法
塑胶件常见的缺陷产生原因及解决办法塑胶件是广泛应用于各个领域的一种重要工程材料,但由于其加工过程的特殊性,常常会出现各种缺陷。
这些缺陷可能会影响塑胶件的外观、性能甚至是功能,因此怎样解决塑胶件的缺陷成为了一个非常重要的问题。
本文将探讨塑胶件常见的缺陷产生原因及解决办法。
1.短射:短射是指塑胶件注射模具中未填满的部分。
造成短射的原因主要有以下几点:(1)注射速度过快,导致塑料未来得及填满模具空腔;(2)熔融温度过低,导致塑料的流动性差;(3)模腔设计不合理,导致塑料流动受阻。
解决办法:(1)调整注射速度,控制在合适范围内;(2)调整熔融温度,确保塑料具有良好的流动性;(3)优化模腔设计,提高塑料的填充性能。
2.热流痕:热流痕是指在填充过程中,由于塑料的流动速度不一致或受到障碍物干扰而造成的痕迹。
产生原因:(1)注射速度过快导致塑料流动速度不均匀;(2)模具设计不合理,导致流道阻力较大;(3)模具表面存在污物或磨损,阻碍流动。
(1)调整注射速度,确保塑料流动速度均匀;(2)优化模具设计,减小流道阻力;(3)定期保养模具,确保模具表面光洁无污物。
3.翘曲:翘曲是指塑胶件在冷却过程中由于收缩不均匀而造成的扭曲变形。
产生原因:(1)注射过程中温度分布不均匀,导致冷却速度不均匀;(2)部分材料的收缩率较大,造成不均匀收缩;(3)模具设计不合理,导致冷却不均匀。
解决办法:(1)控制注射过程中的温度分布,确保全面均匀冷却;(2)使用收缩率较小的材料;(3)优化模具设计,确保冷却均匀。
4.气泡:气泡是塑胶件内部或表面存在的气体囊状物。
产生原因:(1)注射过程中,塑料因挤压和高温导致内部气体产生;(2)注射过程中,未充分排除空气导致气泡残留;(3)塑料材料含有挥发性成分,造成气泡。
(1)调整注射过程中的温度和压力,减少气体产生;(2)注射过程中加入真空排气步骤,充分排除空气;(3)选择不含挥发性成分的塑料材料。
5.纹痕:纹痕是塑胶件表面存在的细微沟纹。
- 1、下载文档前请自行甄别文档内容的完整性,平台不提供额外的编辑、内容补充、找答案等附加服务。
- 2、"仅部分预览"的文档,不可在线预览部分如存在完整性等问题,可反馈申请退款(可完整预览的文档不适用该条件!)。
- 3、如文档侵犯您的权益,请联系客服反馈,我们会尽快为您处理(人工客服工作时间:9:00-18:30)。
• 模具:
• 1.改善模具排气 • 2.防止包气(entrapped air)
缺陷:走胶
Defect:incompletely filled parts
缺胶
走胶改善对策
• 工艺: • 1.提高注射速度及注射压力 • 2.提高保压压力及保压时间 • 3.提高料筒温度
• 4.提高背压
• 模具: • 1.增大浇口及流道截面积 • 2.提高模腔表面温度 • 3.改善模具排气
缺陷:披锋
Defect: flash 披锋
披锋改善对策
• 工艺:
1.降低注射速度及注射压力 2.降低保压压力及保压时间 3.降低背压 4.降低料筒温度 5.增加锁模力
• 模具
1.降低浇口及流道截面积 2.降低模腔表面温度 3.减少排气槽截面积
缺陷: 变形
Defect: deformation
变形
白线
白线改善对策
• 工艺:
• 1.增加锁模力
• 2.降低保压压力及减少保压时间 • 4.降低注射速度及注射压力 • 4.提高料筒温度 • 模具: • 1.提高模腔表面温度
缺陷: 拖白
Defect:Dragging-whitening
拖白
拖白改善对策
• 工艺: • 1.降低保压压力及保压时间 • 2.降低注射速度及注射压力 • 模具:
注塑产品常见缺陷认知
培训对象:注塑作业员 培训讲师:品质张强 培训地点:公司会议室
培训日期:2016年4月5日
缺陷: 夹水纹 lines 夹水纹
Defect: weld
夹水纹改善对策
• 工艺: • 1.提高注射速度 • 2.增加炮筒温度 • 3.增加保压压力 • 模具:
• 1. 提高模温
• 2. 增大浇口及流道截面积 • 3. 改善模具的排气
缩水改善对策
• 工艺:
• 1. 提高注射速度及注射压力 2.提高保压压力及保压时间 3.提高料筒温度 4.提高背压 5.延长冷却时间
• 模具:
• 1.增大浇口及流道截面积 2.降低模腔表面温度 3.改善模具排气
缺陷: 顶白
Defect: visible ejector marks
顶白
顶白改善对策
变形改善对策
• 工艺:
• 1.降低保压压力及保压时间
• 2.降低背压 • 3.延长冷却时间 • 模具: • 1.增加浇口截面积
• 2.均匀模腔表面温度
缺陷: 蛇纹
Defect: Jetting
蛇纹
gate
蛇纹的改善对策
• 工艺: • 1.降低注射速度 • 2.提高炮筒温度 • 模具:
• 压压力及保压时间 • 2.降低顶针压力及顶出速度
• 3.延长冷却时间
• 模具: • 1.降低模腔表面温度 • 2.检查修复模具的倒扣(undercut) • 3.加大顶针的截面积及改善顶针布置
缺陷: 烧焦
Defect: Diesel effect
烧焦
烧焦改善对策
• 工艺: • 1.降低注射速度及注射压力 • 2.降低料筒温度 • 3.降低锁模力
• 1.优化模腔蚀纹
• 2.加大出模斜度
缺陷: 拉白 拉白
Defect:Pulling-whitening
拉白改善对策
• 工艺: • 1.降低保压压力及保压时间 • 2.降低注射速度及注射压力 • 3.延长冷却时间
• 4.降低顶出速度及顶出压力
• 模具: • 1.加出模斜度 • 2.省顺骨位
缺陷: 起皮 Defect: Flaking of surface layer
•
5 . 减少松退行程
• 模具: • 1. 增大浇口及流道的截面积 • 2. 提高模腔表面温度
缺陷: 皱纹
Defect: record grooves effect
皱纹
皱纹改善对策
• 工艺
• 1.提高注射速度
• 2.提高注射压力及保压压力 • 3.提高料筒温度 • 模具 • 1.增大浇口及流道截面积
起皮
起皮改善对策
• 工艺: • 1.降低注射速度 • 2.充分干燥原料 • 3.降低料筒温度 • 原料:
• 1.检查原料是否混有杂料
• 模具: • 1.提高模腔表面温度
缺陷: 黑点
Defect: Dark spots
黑点
黑点改善对策
• 工艺:
• 1.降低料筒温度
• 2.降低背压 • 3.降低螺杆转速 • 4.减少残量 • 原料:
缺陷: 气纹
Defect: air lines
气纹
气纹的改善对策
• 工艺: • 1. 降低注射速度
•
2.
增加料筒温度
• 模具: • 1. 增大浇口截面积 • 2. 提高模腔表面温度 • 3. 加深冷料井
缺陷: 气花
气花
Defect: air streaks
气花的改善对策
• 工艺: • • • • 1. 3. 4. 降低注射速度 增加料筒温度 提高背压 2 . 充分干燥原料
• 检查原料是否混有杂料
缺陷:光泽不一
Defect:Gloss differences
光泽不一
光泽不一改善对策
• 工艺:
• 1.提高注射速度及注射压力
• 2.提高保压压力及保压时间 • 3.提高料筒温度 • 模具: • 1.均匀模腔表面温度
缺陷: 表面斑点
Defect:Spots on surface
• 2.提高模腔表面温度
缺陷: 混色
Defect: color streaks
混色
混色的改善对策
• 工艺 • 1.提高背压 • 2.降低螺杆转速,以增加混炼时间 • 3.提高料筒温度 • 4.增加残量
• 机器
• 1.选用混炼型喷嘴(探针载流/滑动载流) • 2.选用BM螺杆
缺陷: 缩水 缩水
Defect: sink mark
表面斑点
表面斑点改善对策
• 工艺: • 1.提高注射速度及注射压力 • 2.增加螺杆转速 • 3.增加背压 • 4.提高料筒温度
• 模具:
• 1.提高模腔表面温度
THANK YOU
谢谢大家
品质部
• 2.移动浇口位置。
缺陷: 真空泡
Defect:Vacuum vesicle
真空泡
真空泡的改善对策
• 工艺: • 1.降低注射速度 • 2.增加保压压力及保压时间 • 3.增加背压
• 4.降低料筒温度
• 模具: • 1.增加浇口截面积 • 2.提高模腔表面温度
缺陷: 白线
Defect: White lines