齿轮噪音改进
齿轮噪音标准
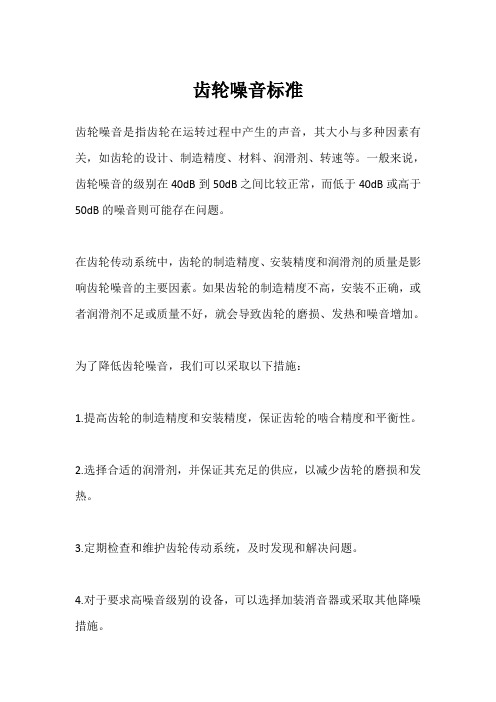
齿轮噪音标准
齿轮噪音是指齿轮在运转过程中产生的声音,其大小与多种因素有关,如齿轮的设计、制造精度、材料、润滑剂、转速等。
一般来说,齿轮噪音的级别在40dB到50dB之间比较正常,而低于40dB或高于50dB的噪音则可能存在问题。
在齿轮传动系统中,齿轮的制造精度、安装精度和润滑剂的质量是影响齿轮噪音的主要因素。
如果齿轮的制造精度不高,安装不正确,或者润滑剂不足或质量不好,就会导致齿轮的磨损、发热和噪音增加。
为了降低齿轮噪音,我们可以采取以下措施:
1.提高齿轮的制造精度和安装精度,保证齿轮的啮合精度和平衡性。
2.选择合适的润滑剂,并保证其充足的供应,以减少齿轮的磨损和发热。
3.定期检查和维护齿轮传动系统,及时发现和解决问题。
4.对于要求高噪音级别的设备,可以选择加装消音器或采取其他降噪措施。
齿轮噪音的正常范围是40dB到50dB之间,如果超过这个范围,就需要检查齿轮传动系统是否存在问题,并采取相应的措施进行解决。
通过提高齿轮的制造和安装精度、选择合适的润滑剂、定期检查和维护等措施,可以有效地降低齿轮噪音,提高设备的使用寿命和效率。
行星齿轮箱出现噪音的分析及处理方法

行星齿轮箱出现噪音的分析及处理方法背景介绍行星齿轮箱是一种用于变速和转速的机械装置,广泛应用于工业生产线和机械制造业等领域。
在行星齿轮箱的运行过程中,有时会出现异常噪音,严重影响了其运转效率和寿命。
因此,分析行星齿轮箱噪音的来源并采取措施进行处理,将对提升机械设备的运行效率和减少维修成本具有重要作用。
声音的来源在行星齿轮箱的运行过程中,声音主要来自于以下几个方面:1. 传动齿轮脱落或磨损行星齿轮箱中的传动齿轮是整个机械结构的核心,如果由于制造不合格、使用时间过长等原因导致齿轮磨损或松动,会产生不正常的噪音。
2. 轴承故障或磨损轴承是行星齿轮箱运行过程中起着支撑和减摩作用的部件,如果轴承故障或磨损,对齿轮箱的运行状态带来极大的影响。
3. 润滑与密封不良润滑和密封不良也是行星齿轮箱噪音的来源之一,如果机械部件缺乏足够的润滑油或密封技术不良,就会导致噪声过大。
噪音的处理方法行星齿轮箱出现噪音时,需要采取一些有效的处理方法,以减少其对机械设备的影响。
以下是一些常见的噪音处理方法:1. 检查齿轮脱落和磨损首先,需要检查行星齿轮箱中的齿轮是否存在脱落或磨损等问题。
如果有问题,需要及时更换或修复相应的机械部件,以恢复良好的运行状态。
2. 更换轴承另外,如果发现行星齿轮箱的轴承存在问题,就需要及时更换可靠的轴承。
同时,需要定期对轴承进行检查和保养,防止轴承出现故障或磨损。
3. 加强润滑和密封对于润滑和密封不良的情况,需要加强相应的措施,使机械设备的润滑和密封性能得到有效保障。
比如,可以针对具体情况加大润滑油的使用量,或优化润滑油的质量,并加强部件的密封性能等。
结论综上所述,行星齿轮箱出现噪音的原因可能来自于齿轮脱落或磨损、轴承故障或磨损,以及润滑和密封不良等方面。
要对这些问题进行有效的处理,保障机械设备的良好运行状态,我们可以采取检查方案和更换零部件、加强润滑和密封等多种措施,来减小行星齿轮箱噪音的发生。
齿轮噪音大的原因和解决方法
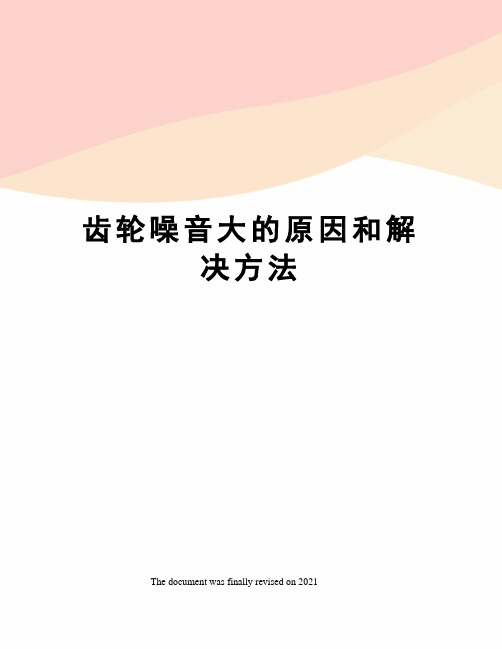
齿轮噪音大的原因和解决方法The document was finally revised on 2021齿轮噪音大的原因和解决方法(一)塑胶齿轮侧间隙取时的噪音最小;齿轮配合一般一硬一软,POM的应配尼龙的,一来不会粘合,也可以补偿误差;对于POM齿轮,噪声大,可以在POM料里加点尼龙,然后在用塑料齿轮脂加在其上,噪声要大大的降低,当然POM的齿轮一定要开模做。
(二)可能是速度太快或配合不好。
赛钢料耐磨,排除结构问题,噪音仍然是它比较突出的缺点,如果改用尼龙料会好些有以下可能:1:齿轮与轴的配合间隙过大,产生窜动;2:齿轮组中心距过大或过小,一般装配后,齿间应有10到15丝的空隙;齿轮噪音与齿轮的渐开线啮合有关(三)对于玩具牙箱,噪音是个大问题:1。
噪音源:噪声与速度成平方比,所以噪声都在高速级,一般只要解决了高速级的噪声,整体的噪声就解决了2。
中心距过小,有磨的声音,电流较大。
中心距过大,有碰的声音。
小模数齿轮中心距的经验值:a=m(z1+z2)/2+3.中心孔:有无孔斜,有无喇叭孔,孔与齿的同心度4。
齿形:齿形有无偏胖5。
润滑油:不但齿上要加润滑油,孔与轴上也要加润滑油6。
设计时注意齿轮箱要全封闭起来,可以大大的降低噪声听声音时可把电压调低,速度变慢来听,可以发现有无周期性的声音(四)总结以下几点降低噪音的方法,供大家参考。
1、蜗轮、蜗杆不能用同一种材料。
2、直接注塑的蜗轮、蜗杆,齿形精度很难控制,造成齿形厚薄不均,可以改成先注塑毛胚,再机加工,以保证精度。
3、保证中心距,不能忽大忽小,一般是上偏差~~,不能走下偏差,否则会卡死,阻力聚增。
4、保证蜗杆不串轴。
5、保证齿形精度。
6、保证轴向跳动不能大。
如何降低齿轮传动噪音
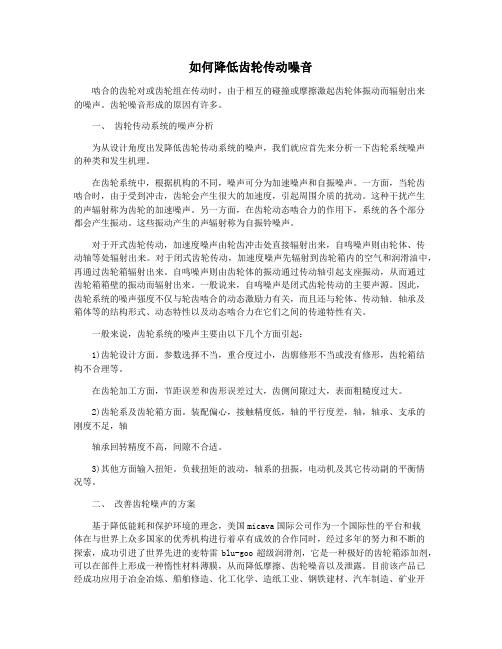
如何降低齿轮传动噪音啮合的齿轮对或齿轮组在传动时,由于相互的碰撞或摩擦激起齿轮体振动而辐射出来的噪声。
齿轮噪音形成的原因有许多。
一、齿轮传动系统的噪声分析为从设计角度出发降低齿轮传动系统的噪声,我们就应首先来分析一下齿轮系统噪声的种类和发生机理。
在齿轮系统中,根据机构的不同,噪声可分为加速噪声和自振噪声。
一方面,当轮齿啮合时,由于受到冲击,齿轮会产生很大的加速度,引起周围介质的扰动。
这种干扰产生的声辐射称为齿轮的加速噪声。
另一方面,在齿轮动态啮合力的作用下,系统的各个部分都会产生振动。
这些振动产生的声辐射称为自振铃噪声。
对于开式齿轮传动,加速度噪声由轮齿冲击处直接辐射出来,自鸣噪声则由轮体、传动轴等处辐射出来。
对于闭式齿轮传动,加速度噪声先辐射到齿轮箱内的空气和润滑油中,再通过齿轮箱辐射出来。
自鸣噪声则由齿轮体的振动通过传动轴引起支座振动,从而通过齿轮箱箱壁的振动而辐射出来。
一般说来,自鸣噪声是闭式齿轮传动的主要声源。
因此,齿轮系统的噪声强度不仅与轮齿啮合的动态激励力有关,而且还与轮体、传动轴.轴承及箱体等的结构形式、动态特性以及动态啮合力在它们之间的传递特性有关。
一般来说,齿轮系统的噪声主要由以下几个方面引起:1)齿轮设计方面。
参数选择不当,重合度过小,齿廓修形不当或没有修形,齿轮箱结构不合理等。
在齿轮加工方面,节距误差和齿形误差过大,齿侧间隙过大,表面粗糙度过大。
2)齿轮系及齿轮箱方面。
装配偏心,接触精度低,轴的平行度差,轴,轴承、支承的刚度不足,轴轴承回转精度不高,间隙不合适。
3)其他方面输入扭矩。
负载扭矩的波动,轴系的扭振,电动机及其它传动副的平衡情况等。
二、改善齿轮噪声的方案基于降低能耗和保护环境的理念,美国micava国际公司作为一个国际性的平台和载体在与世界上众多国家的优秀机构进行着卓有成效的合作同时,经过多年的努力和不断的探索,成功引进了世界先进的麦特雷blu-goo超级润滑剂,它是一种极好的齿轮箱添加剂,可以在部件上形成一种惰性材料薄膜,从而降低摩擦、齿轮噪音以及泄露。
精密齿轮减低噪音的措施

精密齿轮减低噪音的措施1.齿面改善提高齿面加工质量可以有效减少噪音产生。
采用更精密的齿轮加工设备和工艺,比如专用的磨削、研磨和拉削工艺来提高齿面的光洁度,减小齿向的误差和形状偏差,这样可以减少齿轮啮合时的冲击和振动,从而降低噪音。
2.齿形优化齿形的设计和优化可以减少齿轮的噪音。
采用分段齿形和曲线齿形设计可以改变齿轮啮合时的冲击和振动模式,减弱谐振共振现象的发生。
同时,根据应力分布的优化,可以减小齿根应力和表面压力,从而降低噪音产生。
3.增加润滑剂的使用润滑剂在齿轮传动中起到减少摩擦和磨损的作用。
正确选择和使用润滑剂可以降低齿轮噪音。
一般来说,采用高黏度的润滑剂,可以减小齿轮的啮合冲击和振动,从而降低噪音。
另外,添加抗磨剂和消泡剂等特殊添加剂也可以减少齿轮噪音。
4.减小齿轮间隙适当减小齿轮间隙可以减少齿轮传动时的冲击和振动,从而降低噪音产生。
在设计和加工过程中要尽量控制齿轮间隙的误差和变化,提高啮合精度和配合精度。
同时,可以通过优化背隙系数和啮合滚动角来减小齿轮间隙,从而降低噪音。
5.合理选用材料齿轮的材料选择对噪音的影响也很大。
一般来说,硬度较高的材料更容易产生噪音。
对于需要降低噪音的应用,可以选择硬度合适并且强度足够的材料,比如低碳合金钢和渗碳淬火钢等。
此外,要保证齿轮的材料质量和加工质量,避免杂质和缺陷的存在。
6.减震与隔振设计在齿轮传动系统中,可以采用减震和隔振措施来减少噪音。
比如,在传动链条上可以安装减震垫圈、齿轮衬套等零件,来减缓齿轮啮合时的冲击和振动传递。
同时,可以使用减震丝杠和减振座来降低齿轮传递的振动对机械设备的传导,从而减少噪音。
总之,减少精密齿轮噪音是一个涉及多个方面的复杂问题,需要从齿面改善、齿形优化、润滑剂的使用、齿轮间隙控制、材料选用和减震与隔振设计等方面综合考虑和解决。
通过采取合理的技术措施,可以有效地降低精密齿轮的噪音水平,提高机械设备的性能和操作环境。
齿轮传动噪音影响因素和控制措施

齿轮传动噪音影响因素和控制措施浙江省温岭市317503摘要:齿轮传动噪音是机械传动中的一个重要问题,对机械设备的正常运行和工作环境都会产生不良影响。
本文旨在探讨齿轮传动噪音的影响因素和控制措施。
首先介绍了齿轮传动的基本原理和传动噪音的产生机理,然后分析了影响齿轮传动噪音的因素,包括齿轮参数、齿轮磨合、齿轮精度等。
最后提出了控制齿轮传动噪音的措施,包括改善齿轮参数、优化齿轮磨合、提高齿轮精度、减小齿轮间隙、降低齿轮转速、使用隔音材料等。
关键字:齿轮传动;传动噪音;影响因素;控制措施;一、引言齿轮传动是机械传动中广泛应用的一种形式,具有传动效率高、承载能力大、传动精度高等优点。
然而,在齿轮传动中,噪音问题一直是一大难题。
齿轮传动噪音会对机械设备的正常运行产生不良影响,也会对工作环境产生噪声污染。
控制齿轮传动噪音是非常必要的。
本文将探讨齿轮传动噪音的影响因素和控制措施。
因此,研究齿轮传动噪音的影响因素和控制措施,对于提高机械传动的工作效率和可靠性具有重要意义。
二、齿轮传动的基本原理和传动噪音的产生机理1.齿轮传动的基本原理齿轮传动是一种通过齿轮的啮合来实现传动的机械传动方式。
齿轮传动具有传动效率高、承载能力大、传动精度高等优点,因此广泛应用于各种机械设备中。
齿轮传动还具有传动平稳、寿命长、维护方便等优点,因此在工程领域得到广泛应用。
齿轮传动的基本原理是通过齿轮之间的啮合来实现转动的传动。
齿轮之间的啮合方式有直齿轮啮合、斜齿轮啮合、蜗杆齿轮啮合等多种形式。
其中,直齿轮啮合最为常见,也是应用最广泛的一种啮合形式。
在直齿轮啮合中,齿轮的齿形为直线,因此齿轮间的啮合效率较高,能够承受较大的负载,且制造和维护较为简便。
2.传动噪音的产生机理齿轮传动噪音是由齿轮啮合时产生的振动和冲击声引起的。
当齿轮啮合时,由于齿轮齿形的不完美和齿轮间隙的存在,会产生振动和冲击力。
这些振动和冲击力会导致齿轮和机械系统产生噪声。
齿轮噪音的大小取决于多个因素,包括齿轮齿形的准确性、齿轮间隙的大小、齿轮磨合状态、齿轮材料和加工工艺等。
机械设计中的齿轮传动系统优化方法研究
机械设计中的齿轮传动系统优化方法研究齿轮传动是机械工程中常用的一种动力传输方式,广泛应用于各种机械设备中。
通过齿轮的啮合配合,可以实现高效、精确的转动传递,确保机械设备的稳定性和可靠性。
然而,在实际工程设计中,齿轮传动系统常常面临着各种问题,如传动效率低、噪声大、寿命短等。
因此,对齿轮传动系统进行优化是一项十分重要的任务。
齿轮传动系统的优化方法研究可以从多个方面入手,涵盖了传动效率、噪声、寿命等方面的考虑。
下面将介绍几种常见的齿轮传动系统优化方法。
首先,传动效率是齿轮传动系统优化的重要指标之一。
通过改进齿轮的几何形状、齿轮材料选择以及润滑方式等,可以提高传动效率。
对于齿轮的几何形状来说,常见的优化方法包括减小齿轮啮合时的摩擦损失,采用更合理的啮合角等。
此外,合理选择齿轮材料,提高齿轮的硬度和抗磨损性能,也能有效提高传动效率。
另外,在设计润滑系统时,要注重选用适当的润滑方式和合适的润滑剂,以减小摩擦损失,提高传动效率。
其次,减小齿轮传动系统的噪声也是优化的重要目标之一。
齿轮传动系统在运动过程中会产生噪音,影响到机械设备的正常工作和运行环境的安静。
为了减小噪声,可以从减小振动和减小噪音源入手。
在设计齿轮时,采用合理的齿轮模数、齿数和齿轮间距等几何参数,可以有效减小齿轮的振动幅度,减少噪音的产生。
此外,选择低噪音的齿轮材料,使用减震和隔音结构,也可以起到减小噪音的作用。
最后,延长齿轮传动系统的使用寿命也是一项重要的优化目标。
齿轮在传动过程中受到很大的载荷和磨损,容易引起疲劳断裂和啮合面的磨损。
为了延长齿轮传动系统的使用寿命,可以从齿轮材料的选择、齿轮轮廓修形、表面处理等方面入手。
选择高强度、高耐磨的齿轮材料可以提高齿轮的使用寿命。
同时,通过合理的齿轮轮廓修形和表面处理,可以改善齿轮的接触应力分布和摩擦性能,减小齿轮的磨损,延长使用寿命。
除了上述方法外,还可以借助计算机辅助设计软件和仿真工具来进行齿轮传动系统的优化研究。
如何减少齿轮的噪音
如何减少齿轮的噪音减少齿轮噪音的方法:为了避免减速机不能通过出厂测试,原因之一是减速机存在间歇性高噪声;用ND6型精密声级计测试,低噪声减速机为72.3Db(A),达到了出厂要求;而高噪声减速机为82.5dB(A),达不到出厂要求。
经过反复测试、分析和改进试验,得出的结论是必须对生产的各个环节进行综合治理,才能有效降低齿轮传动的噪声。
1、控制齿轮的精度:齿轮精度的基本要求:经实践验证,齿轮精度必须控制在GB10995-887~8级,线速度高于20m/s齿轮,齿距极限偏差、齿圈径向跳动公差、齿向公差一定要稳定达到7级精度。
在达到7级精度齿轮的情况下,齿部要倒梭,要严防齿根凸台。
2、控制原材料的质量:高质量原材料是生产高质量产品的前提条件,我公司用量最大的材料40Cr和45钢制造齿轮。
无论通过何种途径,原材料到厂后都要经过严格的化学成分检验、晶粒度测定、纯洁度评定。
其目的是及时调整热处理变形,提高齿形加工中的质量。
3、防止热处理变形:齿坯在粗加工后成精锻件,进行正火或调质处理,以达到:(1)软化钢件以便进行切削加工;(2)消除残余应力;(3)细化晶粒,改善组织以提高钢的机械性能;(4)为最终能处理作好组织上的准备。
应注意的是,在正火或调质处理中,一定要保持炉膛温度均匀,以及采用工位器具,使工件均匀地加热及冷却,严禁堆放在一起。
需钻孔减轻重量的齿轮,应将钻孔序安排在热处理后进行。
齿轮的最终热处理采用使零件变形较小的齿面高频淬火;高频淬火后得到的齿面具有高的强度、硬度、耐磨性和疲劳极限,而心部仍保持足够的塑性和韧性。
为减少变形。
齿面高频淬火应采用较低的淬火温度和较短的加热时间、均匀加热、缓慢冷却。
4、保证齿坯的精度:齿轮孔的尺寸的精度要求在孔的偏差值的中间差左右分布,定在±0.003~±0.005mm;如果超差而又在孔的设计要求范围内,必须分类,分别转入切齿工序。
齿坯的端面跳动及径向跳动为6级,定在0.01~0.02mm范围内。
新能源汽车齿轮的精密热处理与噪音控制
新能源汽车齿轮的精密热处理与噪音控制随着环境保护意识的增强以及对传统燃油汽车的限制,新能源汽车的市场需求与日俱增。
作为新能源汽车核心的动力传动系统,齿轮在其中起到至关重要的作用。
然而,由于传动系统的高速运转以及重负荷工作环境,齿轮会产生噪音和振动,影响车辆的驾乘舒适性。
为此,精密热处理和噪音控制成为了新能源汽车齿轮制造中的重要环节,本文将深入探讨其相关技术与应用。
一、精密热处理技术精密热处理是指对齿轮材料进行适当的加热与冷却过程,以改善其性能和延长使用寿命的过程。
常见的精密热处理技术包括渗碳、氮化和磨齿焊接等。
1. 渗碳技术渗碳技术是通过将齿轮表面浸入含有碳元素的气体、液体或固体介质中,使碳原子在材料表面渗透,与基体金属发生相互作用,形成其密度较高的复合层。
这一层具有较高的硬度、耐磨性和适度的韧性,能够有效提高齿轮的承载能力和耐磨性能。
2. 氮化技术氮化技术是将齿轮表面浸入含有氮元素的气体中,以高温高压条件下使氮原子与金属基体发生化学反应,形成强硬的氮化物层,提高齿轮的表面硬度和耐磨性能。
与渗碳技术相比,氮化技术具有更高的表面硬度和较低的表面粗糙度,能够有效减少齿轮在工作过程中的磨损和噪音产生。
3. 磨齿焊接技术磨齿焊接技术是将两个或多个齿轮通过磨齿焊接设备连接起来,形成一体化的传动装置。
这种技术能够有效提高齿轮的精度和刚度,减少零部件的数量,降低传动噪音和振动。
同时,磨齿焊接技术还具有生产效率高、成本较低等优点,被广泛应用于新能源汽车齿轮的制造中。
二、噪音控制技术噪音控制是指通过各种措施和技术手段,减少或消除齿轮工作过程中产生的噪音和振动。
常见的噪音控制技术包括减振、减速噪声和噪声隔离等。
1. 减振技术减振技术是通过改变齿轮体系的结构和减少相对振动的方法,来降低齿轮噪音的技术。
例如,采用减振装置、增加齿轮支撑点、增加齿轮的副数等措施,能够有效地减少齿轮在工作过程中产生的振动和噪音。
2. 减速噪声技术减速噪声技术是指通过改变齿轮传动比例和改进齿形设计,减少速度变化和齿轮啮合时产生的冲击噪声。
齿轮噪音原因分析
齿轮噪音原因分析齿轮传动噪声产生原因及控制齿轮传动的噪音是很早以前人们就关注的问题。
但是人们一直未完全解决这一问题,因为齿轮传动中只要有很少的振动能量就能产生声波形成噪音。
噪音不但影响周围环境,而且影响机床设备的加工精度。
由于齿轮的振动直接影响设备的加工精度,满足不了产品生产工艺要求。
因此,如何解决变速箱齿轮传动的噪音尤为重要。
下面谈谈机械设备设计和修理中消除齿轮传动噪音的几种简单方法。
1噪音产生的原因1.1转速的影响齿轮传动若输出功率较低,则齿轮的振动频率升高,啮台冲击更加频密,高频波更高。
据有关资料了解,输出功率在1400转回/分钟时产生的振动频率超过5000h。
产生的声波超过88db构成噪音硬。
通常光学设备变速箱输入轴的输出功率都较低。
高达2000~2800转回/分钟。
因此,光学设备必须化解噪音问题就是须要研究的。
1.2载荷的影响我们将齿轮传动做为一个振动弹簧体系,齿轮本身做为质量的振动系统。
那么该系统由于受变化相同的冲击载荷,产生齿轮圆周方向改变振动,构成圆周方向的振动力。
加之齿轮本身刚性极差就可以产生周期振幅发生噪音。
这种噪音稳定而不尖叫声。
1.3齿形误差的影响齿形误差对齿轮的振动和噪音存有脆弱的影响。
齿轮的齿形曲线偏移标准渐开线形状,它的公法线长度误差也就减小。
同时齿形误差的偏移量并使齿顶上与齿根互相阻碍,发生齿顼棱边压板,从而产生振动和噪音。
1.4共振现象的影响齿轮的共振现象就是产生噪音的关键原因之一。
所谓共振现象就是一个齿轮由于刚性极差齿轮本身的固有振动频率与压板齿轮产生相同的振动频率,这时就可以产生共振现象。
由于共振现象的存有,齿轮的振动频率提升,产生低一级的振动噪音。
必须化解共振现象的噪音问题,只有提升齿轮的刚性。
1.5啮合齿面的表面粗糙度影响齿轮压板面粗糙度可以引起齿轮圆周方向振动,表面粗糙度越差,振动的幅度越大,频率越高,产生的噪音越大。
1.6润滑的影响对压板齿轮齿面杀菌较好可以增加齿轮的振动力,它与杀菌的方法有关。
- 1、下载文档前请自行甄别文档内容的完整性,平台不提供额外的编辑、内容补充、找答案等附加服务。
- 2、"仅部分预览"的文档,不可在线预览部分如存在完整性等问题,可反馈申请退款(可完整预览的文档不适用该条件!)。
- 3、如文档侵犯您的权益,请联系客服反馈,我们会尽快为您处理(人工客服工作时间:9:00-18:30)。
治理齿轮传动噪声| [<<][>>]为了避免减速机不能通过出厂测试,原因之一是减速机存在间歇性高噪声;用N D6型精密声级计测试,低噪声减速机为72.3Db(A),达到了出厂要求;而高噪声减速机为82.5d B(A),达不到出厂要求。
经过反复测试、分析和改进试验,得出的结论是必须对生产的各个环节进行综合治理,才能有效降低齿轮传动的噪声。
1、齿轮精度的基本要求经实践验证,齿轮精度必须控制在G B10995-887~8级,线速度高于20m/s齿轮,齿距极限偏差、齿圈径向跳动公差、齿向公差一定要稳定达到7级精度。
在达到7级精度齿轮的情况下,齿部要倒梭,要严防齿根凸台。
2、控制原材料的质量高质量原材料是生产高质量产品的前提条件,某公司用量最大的材料40Cr和45钢制造齿轮。
无论通过何种途径,原材料到厂后都要经过严格的化学成分检验、晶粒度测定、纯洁度评定。
其目的是及时调整热处理变形,提高齿形加工中的质量。
3、防止热处理变形齿坯在粗加工后成精锻件,进行正火或调质处理,以达到:(1)软化钢件以便进行切削加工;(2)消除残余应力;(3)细化晶粒,改善组织以提高钢的机械性能;(4)为最终能处理作好组织上的准备。
应注意的是,在正火或调质处理中,一定要保持炉膛温度均匀,以及采用工位器具,使工件均匀地加热及冷却,严禁堆放在一起。
需钻孔减轻重量的齿轮,应将钻孔序安排在热处理后进行。
齿轮的最终热处理采用使零件变形较小的齿面高频淬火;高频淬火后得到的齿面具有高的强度、硬度、耐磨性和疲劳极限,而心部仍保持足够的塑性和韧性。
为减少变形。
齿面高频淬火应采用较低的淬火温度和较短的加热时间、均匀加热、缓慢冷却。
4、保证齿坯的精度齿轮孔的尺寸的精度要求在孔的偏差值的中间差左右分布,定在±0.003~±0.005mm;如果超差而又在孔的设计要求范围内,必须分类,分别转入切齿工序。
齿坯的端面跳动及径向跳动为6级,定在0.01~0.02mm范围内。
5、切齿加工措施对外购的齿轮刀具必须进行检验,必须达到AA级要求。
齿轮刀具刃磨后必须对刀具前刃面径向性、容屑槽的相邻周节差、容屑槽周节的最大累积误差、刀齿前面与内孔轴线平行度进行检验。
在不影响齿轮强度的前提下,提高齿顶高系数,增加0.05~0.1m,,改善刀具齿顶高系数,避免齿轮传动齿根干涉。
M=1~2的齿轮采用齿顶修圆滚刀,修圆量R=0.1~0.15m。
消除齿顶毛刺,改善齿轮传动时齿顶干涉。
切齿设备每年要进行一次精度检查,达不到要求的必须进行维修。
操作者亦要经常进行自检,特别是在机床主轴径向间隙控制在0. 01mm以下,刀轴径跳0.005mm以下,刀轴窜动0.008mm以下。
刀具的安装精度:刀具径向跳动控制在0.003mm以下,端面跳动0.004mm以下。
切齿工装精度,心轴外径与工件孔的间隙,保证在0. 001~0.004mm以内。
心轴上的螺纹必须在丙顶类定位下,由螺纹床进行磨削:垂直度≦0.003m m,径跳≦0.005m m。
螺母必须保证内螺纹与基准面一次装夹车成,垫圈的平行度≦0.003mm。
6、文明生产齿轮传动噪声有30%以上的原因来自毛刺、磕碰伤。
有的工厂在齿轮箱装配前,去除毛刺及磕碰伤,是一种被动的做法。
作者比较主张以下做法:(1)齿轮轴类零件,滚齿后齿部立即套上专用的塑料保护套后转入下道工序,并带着专用的塑料保护套入库和发货。
(2)进行珩齿工艺,降低齿面粗糙度,去除毛刺,并防止磕碰伤,能有效地降低齿轮传动噪声。
7、采取基它材料及热处理、表面处理方式(1)可利用粉末冶金成型技术,齿轮成型后齿部高频淬火。
(2)采用墨铸铁,齿轮切削加工后,再进行软氮化处理。
(3)采用40Cr材料,齿轮切削功工后,采用软氮化处理或齿部镀铜处理。
综合所述,要根治齿轮传动噪声,齿轮材料及热处理是要本,齿坯精度是保证,齿轮精度是关键,文明生产是基础。
感谢读者推荐!欢迎您推荐、自荐机械工程学文章和门户网站>>>齿顶、齿向修整轮齿是一个弹性体,工作受力后不可避免地要发生弯曲变形。
虽然啮合结束后恢复原状,但啮合时的变形会发生基节误差那样的影响,使下一对齿的齿顶和齿根发生干涉,能产生很大的冲击而引起啮合噪音。
表面渗碳淬火齿轮的许用K系数约为调质齿轮的4-5倍。
轮齿变形的影响,比调质齿轮大得多。
为了避免啮合冲击,改善齿面润滑状态,降低啮合噪音,需对齿轮的齿顶和齿向进行修整。
起修整量是根据齿轮负荷计算齿轮变形量,齿轮轴的弯曲,扭转变形量后确定的。
对高承载能力的高硬度齿面的渗碳淬火齿轮,齿顶、齿向修整技术是保证产品性能不可缺少的必要条件。
我公司已建立了自己的齿顶、齿向修形计算标准和计算程序,并成功的用NiIES、MAAG、Hoefier及国产磨齿机对我厂生产的各种齿轮,其中包括按西欧、日本和美国设计的图纸生产的齿轮进行了修正。
降低齿轮传动噪声的综合治理我厂是从事齿轮制造的专业厂,为军工和民用等行业服务时,不管是齿轮件、还是减速器,用户都对齿轮传动噪声问题十分敏感,历年来用户反馈的意见大多是与怎样降低齿轮噪声有关。
用户提出的要求也很高,如一种出口欧洲的三级行星齿轮减速器的噪声指标是小于54dB、洗衣机齿轮箱总成的噪声指标是小于40dB,特别是在分贝值达到的情况下,还提出悦耳度问题,就是要没有杂音。
我厂经过多年努力,得出的结论是必须要综合治理:从原材料、热处理、齿坯加工、齿形加工、文明生产等方面采取措施,才能有效地降低齿轮传动噪声,以满足用户的要求。
一、控制原材料的质量我厂使用量最大的材料是20CrMo、40Cr及45号钢。
采用由质量稳定的抚顺钢厂、首都钢厂定点供货,到厂后都要经过严格的化学成分检验、晶粒度测定、纯洁度评定。
其目的是及时调整热处理工艺,控制热处理变形,提高齿形加工中的质量。
二、防止热处理变形1. 齿坯在粗加工后或精锻件,进行正火或调质处理。
2. 正火或调质处理中,一定要保持炉膛温度的均匀性,以及采用工位器具,使工件均匀地加热及冷却(严禁堆放,一般工厂办不到)。
并通过在齿轮端面分度圆周上测定硬度HR±C0.5来控制。
3. 采用氰化处理。
比渗碳淬火温度低、变形小。
4. 部分齿轮高频淬火及氰化处理件中改用软氮化工艺。
我厂采用的稀土催渗软氮化工艺,具有硬度值高、白亮层厚等优点。
经过用户严格试验,应用面正在不断扩大。
我厂出口欧洲的三级行星减速器就是全部采用软氮化工艺,它有效地减少了热处理变形。
5. 用于氰化处理的设备,必须采用滴注式UNIC气体渗碳氮化炉。
我厂使用的设备是盐城丰东热处理有限公司生产的,多年来使用稳定。
三、稳定提高齿坯精度1. 提高齿轮孔的精度齿轮孔的尺寸精度,要求在孔的念头值的中间差左右分布,定在±0.003~±0.005mm,如果超差而又在孔的设计要求范围内,必须分开转入切齿工序,以便采取措施。
孔的直线度必须控制在0.003mm以内。
2. 控制端面跳动及外径跳动1)齿坯的端面跳动是直接影响齿向公差的项目。
我厂在工艺上都采用热处理前提高一级的办法。
首先加工齿轮两端面,保证平行度在0.01mm以内,然后在工装上精镗孔,保证达到孔对端面的跳动公差。
2)齿坯的径向跳动,我厂工艺上也采用热处理前提高一级的办法。
在切齿时100%校圆,主要是作为一道检验工序,确保齿圈跳动公差。
四、切齿加工中的措施1. 齿轮刀具1)对外购的齿轮刀具,全部进行检验,必须达到AA级要求。
达不到要求的齿轮刀具,本厂全部进行精铲磨。
2)齿轮刀具刃磨后必须检测:刀具前刃面径向性、;容屑槽的相邻周节差、容屑槽周节的最大累积误差、刀具前刃面与内孔轴线平行度。
每天抽查20%的加工件。
3)齿轮刀具全部采用镀钛处理,提高刀具耐用度,改善刀具齿顶部分的磨损,防止齿轮根部圆弧过大。
4)m = 0.3~0.8的齿轮采用顶切滚刀。
m = 1~2的齿轮采用齿顶修圆滚刀,修圆量R = 01~0.15mm。
消除齿顶毛刺,改善齿轮传动时齿顶干涉。
5)在不影响齿轮强度的情况下,提高滚刀的齿顶高系数,加高(0.05~0.1)m,改善刀具齿顶耐用度,避免齿轮传动时齿根干涉。
2. 切齿工序1)切齿设备由机动科每年进行一次精度检查,达不到的必须进行维修。
操作者还经常进行自检;特别是机床主轴径向间隙控制在0.01mm以下,刀轴径跳在0.005mm以下。
刀轴窜动在0.008以下。
2)刀具安装精度,刀具径跳控制在0.003mm以下,端跳在0.004以下。
3)切齿工装:心轴外径与工件孔的间隙,保证在0.001~0.004mm以内。
心轴上的螺纹必须在两顶尖定位下,由螺纹磨床进行磨削:垂直度≤0.003mm以下,径跳≤0.005。
螺母必须保证内螺纹与基准面一次装夹车成。
垫圈的平行度≤0.003mm。
4)切齿的质量控制首件必须通过专职检验员检验通过,检验项目为Fw、Fr、Fi″、fi″、Fβ、Ff。
加工中操作者经常检查Fi、Fr、值。
批检:每300件一批,抽检Fw、Fr、Fi″、fi″,抽查量为10%~15%,W值为30%,而ff、Fβ为0.5%~1%。
五、热处理后的加工1. 对于软氮化及齿部高频淬火的齿轮孔,一般采用热处理前放量法、热处理后再进行研孔工艺,以有利于保持精度,降低成本。
2. 对于氰化处理的齿轮孔,全部采用分度圆定位、阿基米德螺旋线锁紧的磨孔工艺。
六、文明生产齿轮传动噪声有30%以上的原因来自毛刺、磕碰伤,也是一个很难根治的问题。
有的工厂在齿轮箱装配前,把啮合的一对齿轮在噪声检查机上对啮,去除毛刺及磕碰伤,这是一种很被动的做法。
我厂采用以下几方面的措施。
1. 切齿后全部采用工位器具转运。
2. 齿轮轴类零件,滚齿后齿部立即套上塑料管后转入下道工序,并带塑料管发货。
3. 氰化件,热处理后经过液体喷砂处理。
4. 氰化齿轮进行珩齿工艺。
目前对齿轮外齿珩齿工艺是否降低齿轮精度有争议,根据我厂的实践,只要采取工艺措施,能够保持齿轮精度改善齿面的粗糙度,可靠地去除毛刺,并防止磕碰伤,有效地降低齿轮传动噪声。
七、采用其它材料及热处理、表面处理方式,以降低齿轮传动噪声。
摩托车发动机初级从动齿轮,线速度超过20m/s,但负载较小,可采用:1. 利用粉末冶金成型技术,齿轮成型后齿部高频淬火。
2. 采用球墨铸铁,齿轮切削加工后,再进行软氮化处理。
3. 采用40Cr材料,齿轮切削加工后,再进行软氮化处理或齿部镀铜处理。
综上所述,要根治齿轮传动噪声,齿轮材料及热处理是根本,齿坯精度是保证,齿轮精度是关键,文明生产是基础。
根据我厂长期实践中的加工模数范围及涉及到的行业,认为齿轮精度必须控制在GB10095---88 7~8级。
当线速度高于20m/s的齿轮,齿距极限偏差、齿圈径向跳动公差、齿向公差一定要稳定达到7级精度。