自动化太阳能发电系统英文文献翻译
光伏发电中英对照文献

外文参考文献译文及原文目录外文文献译文 (1)1.中国光伏发电的战略地位 (1)2.世界光伏产业现状和发展预测 (2)3.中国光伏发电市场和产业现状 (3)4.中国光复发电的市场预测和规划建议 (5)5.结论 (6)外文文献原文 (7)1.China's strategic position PV (7)2.The world's current situation and development of photovoltaic industryforecast (9)3.The Chinese PV market and industry statu s (10)4.China's PV market forecasting and planning proposals (13)5.Conclusions (15)外文文献译文1、中国光伏发电的战略地位1.1 中国的能源资源和可再生能源现状和预测;无论从世界还是从中国来看,常规能源都是很有限的,中国的一次能源储量远远低于世界的平均水平,大约只有世界总储量的10%。
从长远来看,可再生能源将是未来人类的主要能源来源,因此世界上多数发达国家和部分发展中国家都十分重视可再生能源对未来能源供应的重要作用。
在新的可再生能源中,光伏发电和风力发电是发展最快的,世界各国都把太阳能光伏发电的商业化开发和利用作为重要的发展方向。
根据欧洲JRC 的预测,到2030年太阳能发电将在世界电力的供应中显现其重要作用,达到10%以上,可再生能源在总能源结构中占到30%;2050 年太阳能发电将占总能耗的20%,可再生能源占到50%以上,到本世纪末太阳能发电将在能源结构中起到主导作用。
我国政府重视可再生能源技术的发展,主要有水能、风能、生物质能、太阳能、地热能和海洋能等。
我国目前可再生能源的发展现状如下:水能:我国经济可开发的水能资源量为3.9 亿千瓦,年发电量1.7 万亿千瓦时,其中5 万千瓦及以下的小水电资源量为1.25 亿千瓦。
自动化专业英语 unit3 新能源 全文翻译
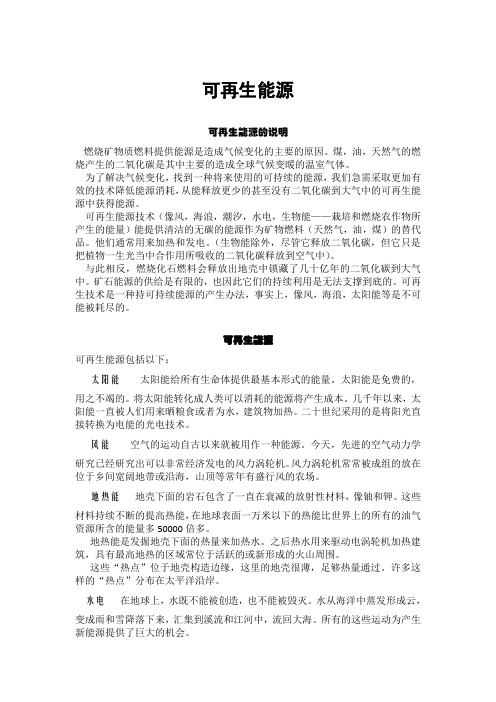
可再生能源可再生能源的说明燃烧矿物质燃料提供能源是造成气候变化的主要的原因。
煤,油,天然气的燃烧产生的二氧化碳是其中主要的造成全球气候变暖的温室气体。
为了解决气候变化,找到一种将来使用的可持续的能源,我们急需采取更加有效的技术降低能源消耗,从能释放更少的甚至没有二氧化碳到大气中的可再生能源中获得能源。
可再生能源技术(像风,海浪,潮汐,水电,生物能——栽培和燃烧农作物所产生的能量)能提供清洁的无碳的能源作为矿物燃料(天然气,油,煤)的替代品。
他们通常用来加热和发电。
(生物能除外,尽管它释放二氧化碳,但它只是把植物一生光当中合作用所吸收的二氧化碳释放到空气中)。
与此相反,燃烧化石燃料会释放出地壳中锁藏了几十亿年的二氧化碳到大气中。
矿石能源的供给是有限的,也因此它们的持续利用是无法支撑到底的。
可再生技术是一种持可持续能源的产生办法,事实上,像风,海浪,太阳能等是不可能被耗尽的。
可再生能源可再生能源包括以下:太阳能太阳能给所有生命体提供最基本形式的能量。
太阳能是免费的,用之不竭的。
将太阳能转化成人类可以消耗的能源将产生成本。
几千年以来,太阳能一直被人们用来晒粮食或者为水,建筑物加热。
二十世纪采用的是将阳光直接转换为电能的光电技术。
风能空气的运动自古以来就被用作一种能源。
今天,先进的空气动力学研究已经研究出可以非常经济发电的风力涡轮机。
风力涡轮机常常被成组的放在位于乡间宽阔地带或沿海,山顶等常年有盛行风的农场。
地热能地壳下面的岩石包含了一直在衰减的放射性材料,像铀和钾。
这些材料持续不断的提高热能,在地球表面一万米以下的热能比世界上的所有的油气资源所含的能量多50000倍多。
地热能是发掘地壳下面的热量来加热水。
之后热水用来驱动电涡轮机加热建筑,具有最高地热的区域常位于活跃的或新形成的火山周围。
这些“热点”位于地壳构造边缘,这里的地壳很薄,足够热量通过。
许多这样的“热点”分布在太平洋沿岸。
水电在地球上,水既不能被创造,也不能被毁灭。
太阳能发电外文翻译文献

太阳能发电外文翻译文献(文档含中英文对照即英文原文和中文翻译)Design of a Lead-Acid Battery Charging and Protecting IC in Photovoltaic SystemZENG De-you,LING Chao-dong,LI Guo-gang1.IntroductionSolar energy as an inexhaustible, inexhaustible source of energy more and more attention. Solar power has become popular in many countries and regions, solar lighting has also been put into use in many cities in China. As a key part of the solar lighting, battery charging and protection is particularly important. Sealed maintenance-free lead-acid battery has a sealed, leak-free, pollution-free, maintenance-free, low-cost, reliable power supply during the entire life of the battery voltage is stable and no maintenance, the need for uninterrupted for the various typesof has wide application in power electronic equipment, and portable instrumentation. Appropriate float voltage, in normal use (to prevent over-discharge, overcharge, over-current), maintenance-free lead-acid battery float life of up to 12 ~ 16 years float voltage deviation of 5% shorten the life of 1/2. Thus, the charge has a major impact on this type of battery life. Photovoltaic, battery does not need regular maintenance, the correct charge and reasonable protection, can effectively extend battery life. Charging and protection IC is the separation of the occupied area and the peripheral circuit complexity. Currently, the market has not yet real, charged with the protection function is integrated on a single chip. For this problem, design a set of battery charging and protection functions in one IC is very necessary.2.System design and considerationsThe system mainly includes two parts: the battery charger module and the protection module. Of great significance for the battery as standby power use of the occasion, It can ensure that the external power supply to the battery-powered, but also in the battery overcharge, over-current and an external power supply is disconnected the battery is to put the state to provide protection, the charge and protection rolled into one to make the circuit to simplify and reduce valuable product waste of resources. Figure 1 is a specific application of this Ic in the photovoltaic power generation system, but also the source of this design.Figure1 Photovoltaic circuit system block diagramMaintenance-free lead-acid battery life is usually the cycle life and float life factors affecting the life of the battery charge rate, discharge rate, and float voltage. Some manufacturers said that if the overcharge protection circuit, the charging rate can be achieved even more than 2C (C is the rated capacity of the battery), battery manufacturers recommend charging rate of C/20 ~ C/3. Battery voltage and temperature, the temperature is increased by 1 °C, single cell battery voltage drops 4 mV , negative temperature coefficient of -4 mV / ° C means that the battery float voltage. Ordinary charger for the best working condition at 25 °C; charge less than the ambient temperature of 0 °C; at 45 °C may shorten the battery life due to severe overcharge. To make the battery to extend the working life, have a certain solar battery array Charge controllercontroller Dischargecontroller DC load accumulatorunderstanding and analysis of the working status of the battery, in order to achieve the purpose of protection of the battery. Battery, there are four states: normal state, over-current state over the state of charge, over discharge state. However, due to the impact of the different discharge current over-capacity and lifetime of the battery is not the same, so the battery over discharge current detection should be treated separately. When the battery is charging the state a long time, would severely reduce the capacity of the battery and shorten battery life. When the battery is the time of discharge status exceeds the allotted time, the battery, the battery voltage is too low may not be able to recharge, making the battery life is lower. Based on the above, the charge on the life of maintenance-free lead-acid batteries have a significant impact, while the battery is always in good working condition, battery protection circuit must be able to detect the normal working condition of the battery and make the action the battery can never normal working state back to normal operation, in order to achieve the protection of the battery.3.Units modular design3.1The charging moduleChip, charging module block diagram shown in Figure 2. The circuitry includes current limiting, current sensing comparator, reference voltage source, under-voltage detection circuit, voltage sampling circuit and logic control circuit.Figure2 Charging module block diagramdriverV oltage amplifierV oltage sampling comparatorStart amplifierState level control Charging indicator Logicalmodule Undervoltage detection circuitR- powerCurrent sampling comparator Limitingamplifier Power indicatorThe module contains a stand-alone limiting amplifier and voltage control circuit, it can control off-chip drive, 20 ~30 mA, provided by the drive output current can directly drive an external series of adjustment tube, so as to adjust the charger output voltage and current . V oltage and current detection comparator detects the battery charge status, and control the state of the input signal of the logic circuit. When the battery voltage or current is too low, the charge to start the comparator control the charging. Appliances into the trickle charge state when the cut-off of the drive, the comparator can output about 20 mA into the trickle charge current. Thus, when the battery short-circuit or reverse, the charger can only charge a small current, to avoid damage to the battery charging current is too large. This module constitutes a charging circuit charging process is divided into two charging status: high-current constant-current charge state, high-voltage charge status and low-voltage constant voltage floating state. The charging process from the constant current charging status, the constant charging current of the charger output in this state. And the charger continuously monitors the voltage across the battery pack, the battery power has been restored to 70% to 90% of the released capacity when the battery voltage reaches the switching voltage to charge conversion voltage Vsam charger moves to the state of charge. In this state, the charger output voltage is increased to overcharge pressure V oc is due to the charger output voltage remains constant, so the charging current is a continuous decline. Current down to charge and suspend the current Ioct, the battery capacity has reached 100% of rated capacity, the charger output voltage drops to a lower float voltage VF.3.2 Protection ModuleChip block diagram of the internal protection circuit shown in Figure 3. The circuit includes control logic circuit, sampling circuit, overcharge detection circuit, over-discharge detection comparator, overcurrent detection comparator, load short-circuit detection circuit, level-shifting circuit and reference circuit (BGR).Figure3 Block diagram of battery protectionThis module constitutes a protection circuit shown in Figure 4. Under the chip supply voltage within the normal scope of work, and the VM pin voltage at the overcurrent detection voltage, the battery is in normal operation, the charge and discharge control of the chip high power end of the CO and DO are level, when the chip is in normal working mode. Larger when the battery discharge current will cause voltage rise of the VM pin at the VM pin voltage at above the current detection voltage Viov, then the battery is the current status, if this state to maintain the tiov overcurrent delay time, the chip ban on battery discharge, then the charge to control the end of CO is high, the discharge control side DO is low, the chip is in the current mode, general in order to play on the battery safer and more reasonable protection, the chip will battery over-discharge current to take over the discharge current delay time protection. The general rule is that the over-discharge current is larger, over the shorter the discharge current delay time. Above Overcharge detection voltage, the chip supply voltage (Vdd> Vcu), the battery is in overcharge state, this state is to maintain the corresponding overcharge delay time tcu chip will be prohibited from charging the battery, then discharge control end DO is high, and charging control terminal CO is low, the chip is in charging mode. When the supply voltage of the chip under the overdischarge detection voltage (Vdd <Vdl,), then the battery is discharged state, this state remains the overdischarge delay time tdl chip will be prohibited to discharge the battery at this time The charge control side CO is high, while the discharge control terminal DO is low, the chip is in discharge mode. Sampling circuitOver discharge detection comparatorControl logic circuit Level conversion circuit Overcharge detection comparator Over-current detection comparator2 Over-current detection comparator1Over-current detection circuitLoad short detection circuitFigure4 Protection circuit application schematic diagram4.Circuit DesignTwo charge protection module structure diagram, the circuit can be divided into four parts: the power detection circuit (under-voltage detection circuit), part of the bias circuit (sampling circuit, the reference circuit and bias circuit), the comparator (including the overcharge detection /overdischarge detection comparator, over-current detection and load short-circuit detection circuit) and the logic control part.This paper describes the under-voltage detection circuit (Figure 5), and gives the bandgap reference circuit (Figure 6).Figure5 Under-voltage detection circuitProtectionmoduleBiasing circuit Reference circuit Bleeder circuit difference amplifier Output circuitAmplifierAmplifierFigure6 A reference power supply circuit diagramBattery charging, voltage stability is particularly important, undervoltage, overvoltage protection is essential, therefore integrated overvoltage, undervoltage protection circuit inside the chip, to improve power supply reliability and security. And protection circuit design should be simple, practical, here designed a CMOS process, the undervoltage protection circuit, this simple circuit structure, process and easy to implement and can be used as high-voltage power integrated circuits and other power protection circuit.Undervoltage protection circuit schematic shown in Figure 5, a total of five components: the bias circuit, reference voltage, the voltage divider circuit, differential amplifier, the output circuit. The circuit supply voltage is 10V; the M0, M1, M2, R0 is the offset portion of the circuit to provide bias to the post-stage circuit, the resistance, Ro, determine the circuit's operating point, the M0, M1, M2 form a current mirror; R1 M14 is the feedback loop of the undervoltage signal; the rest of the M3, M4 and M5, M6, M7, M8, M9, M10, M11, M12, M13, M14, composed of four amplification comparator; M15, DO, a reference voltage, the comparator input with the inverting input is fixed (V+), partial pressure of the resistance R1, R2, R3, the input to the inverting input of the comparator, when the normal working of the power supply voltage, the inverting terminal of the voltage detection is lost to the inverting terminal voltage of the comparator is greater than V+. Comparator output is low, M14 cutoff, feedback circuit does not work; undervoltage occurs, the voltage divider of R1, R2, R3, reaction is more sensitive, lost to the inverting input voltage is less than V when the resistor divider, the comparator the output voltage is high, this signal will be M14 open, the voltage across R into M at both ends of the saturation voltage close to 0V, thereby further driving down the R1> R2, the partial pressure of the output voltage, the formation of the undervoltage positive feedback. Output, undervoltage lockout, and plays a protective role.5. Simulation results and analysisThe design of the circuit in CSMC 0.6 μm in digital CMOS process simulation and analysis of the circuit. In the overall simulation of the circuit, the main observation is that the protection module on the battery charge and discharge process by monitoring Vdd potential and Vm potential leaving chip CO side and DO-side changes accordingly. The simulation waveform diagram shown in Figure 7, the overall protection module with the battery voltage changes from the usual mode conversion into overcharge mode, and then return to normal working mode, and then into the discharge mode, and finally back to normal working mode. As the design in the early stages of the various parameters to be optimized, but to provide a preliminary simulation results.Figure7 Overvoltage and under-voltage protection circuit simulation waveform6.ConclusionDesigned a set of battery charging and protection functions in one IC. This design not only can reduce the product, they can reduce the peripheral circuit components. The circuit uses the low-power design. This project is underway to design optimization stage, a complete simulation can not meet the requirements, but also need to optimize the design of each module circuit.光伏系统中蓄电池的充电保护IC电路设计曾德友,凌朝东,李国刚1.引言太阳能作为一种取之不尽、用之不竭的能源越来越受到重视。
自动化太阳能发电系统英文文献翻译

在混合光伏阵列中采用滑模技术的电源控制发电系统
摘要
变结构控制器来调节输出功率的一个独立的混合发电系统。 该系统包括光伏 发电和风力发电, 存储电池组和一个变量的单相负载。控制律承认两种操作模式 。 第一条用在当日晒度足够满足对电力的需求的情况下。第二运作模式应用在 日晒度不足的时候。后者致使系统在最大功率操作点(MPOP)操作下存储尽可能 多的能量。根据IncCond算法开发的一种新方法。滑模控制用于技术设计的控制 律。这些技术提供了一个简单的控制律设计框架,并有助于它们自带的鲁棒性。 最后,指导方针根据考虑为实际系统的设计。
1引言
可再生能源, 如风力和太阳能被认为是非常前途的能源。它们拥有可以满足 不断增加的世界能源需求的特点。另一方面,他们是基于无公害转换流程,它们 需要的主要资源是取之不尽,用之不竭,并且免费的。对于远程、远离电网的地 方,它往往是比用输电线路[1] 提供一个独立的电力来源拥有可行性。在这些电 网中, 在混合动力系统结合模块的基础上, 可再生能源发电以柴油为动力的备用 发电机已考虑ERED等效为一个可行的选择[2, 3]。然而,柴油发电机在孤立的燃 料供应和其运作领域是相当麻烦,相比较可再生能源,显得不划算[4]。为了取 代柴油备用发电机,独立的混合动力系统经常采用结合可再生能源来源的TARY 型材,如风力和光伏发电,合适的存储设备,如电池。自存储成本仍然是一个重 大的经济约束,通常光伏/风能/电池系统是用“适当”的大小以减少资本成本。 本文提出了一种控制策略,以规范的混合动力系统,包括光伏发电和风力 发电,蓄电池组和可变负载的输出功率作为研究。控制可调整的光伏发电、风力 发电, 以满足负载和电池充电的电源要求。系统以在独立控制下的最大发电的主 要目标。该控制器的设计开发,在之前的文献[5]中提过。因此,根据不同的大 气条件,不同的光伏阵列控制律使用的范围不同。第一条用在暴晒的地方,运作 模式足以提供的总功率需求,和风力发电一起适用。另一条控制律是在曝晒度不 足情况下跟踪最大功率操作点(MPOP),使系统保持尽可能多的储存的能量。 跟踪MPOP的方法是一个新的扩展版本下的IncCond算法[6]。 对于这两种操作模式设计控制律均使用滑模方法。这种技术很有吸引力,它 简化了设计任务,并使控制器具有鲁棒性。此外,根据第二次的运作模式,这种 技术提供的MPOP收敛速度最快。
光伏发电介绍英文作文
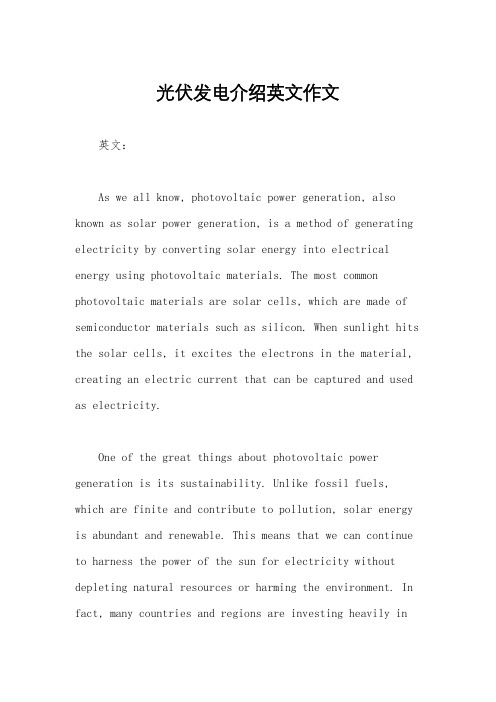
光伏发电介绍英文作文英文:As we all know, photovoltaic power generation, also known as solar power generation, is a method of generating electricity by converting solar energy into electrical energy using photovoltaic materials. The most common photovoltaic materials are solar cells, which are made of semiconductor materials such as silicon. When sunlight hits the solar cells, it excites the electrons in the material, creating an electric current that can be captured and used as electricity.One of the great things about photovoltaic power generation is its sustainability. Unlike fossil fuels, which are finite and contribute to pollution, solar energy is abundant and renewable. This means that we can continue to harness the power of the sun for electricity without depleting natural resources or harming the environment. In fact, many countries and regions are investing heavily insolar power as a clean and sustainable energy source.Another benefit of photovoltaic power generation is its versatility. Solar panels can be installed on a wide rangeof surfaces, from rooftops to open fields, making it a flexible option for generating electricity. In addition, solar panels can be used in both grid-connected and off-grid systems, providing power to remote areas that may not have access to traditional electricity sources.In my own experience, I have seen the impact of photovoltaic power generation firsthand. In my hometown, many households have installed solar panels on their roofsto generate electricity for their own use. This has notonly reduced their reliance on traditional power sources, but also saved them money on electricity bills. Furthermore, I have visited solar farms where vast fields of solarpanels are used to generate large amounts of electricityfor the local community. It's amazing to see how the powerof the sun can be harnessed to provide clean andsustainable energy for so many people.Overall, photovoltaic power generation is a promising and environmentally friendly method of generating electricity. With ongoing advancements in technology and increasing awareness of the importance of renewable energy, I believe that solar power will play an increasingly significant role in meeting our energy needs in the future.中文:众所周知,光伏发电,也被称为太阳能发电,是一种利用光伏材料将太阳能转换为电能的发电方法。
太阳能热光伏发电系统研究与仿真外文翻译

Introduction1.1 Photovoltaic Energy Conversion1.2 solar Cells and Solar Energy Conversion1.3 solar Cell ApplicationsReferences1.1PHOTOVOLTAIC ENERGY CONVERSIONPhotovoltaic energy conversion is the direct production of electrical energy in the form of current and voltage from electromagnetic (i.e., light,including infrared, visible. and ultraviolet) energy. The basic four steps needed for photovoltaic energy conversion are:1. a light absorption process which causes a transition in a material(the absorber) from ground state to an excited state,2.the conversion of the excited state into (at least) a free negativeand free positive-charge carriers pair, and3. discriminating transport mechanism, which causes the resultingfree negative-charge carriers to move in one direction (to a con-tact that we will call the cathode) and the resulting free positive-charge carriers to move in another direction (to a contact that wewill call the anode).The energetic photogenerated negative-charge carriers arriving, at the cathode result in electrons which travel through an external path (an electric circuit). While traveling this path, they lose their energy doing something useful at an electrical "load," and finally they return to the anode of the cell. At the anode, every one of the returning electrons completes the fourth step of photovoltaic energy conversion, which is closing the circle by4. combining with an arriving positive-charge carrier, thereby returning theabsorber to the ground state.In some materials, the excited state may be a photogenerated free electron-free hole pair. In such a situation, step 1 and step 2 coalesce. In some materials, the excited state may be an exciton, In which case steps 1 and 2 are distinct.A study of the various man-made photovoltaic devices that carry out these four steps is the subject of this text. Our main interest is photovoltaic devices that can efficiently convert the energy in sunlight into usable electrical energy. Such devices are termed solar cells or solar photovoltaic devices. Photovoltaic devices can be designed to be effective for electromagnetic spectra other than sunlight. For example, devices can be designed to convert radiated heat (infrared light) into usable electrical energy. These are termed thermal photovoltaic devices. There are also devices which directly convert light into chemical energy. In these, the photogenerated excited state is used to drive chemical reactions rather than to drive electrons through an electric circuit. One example is the class of devices used for photolysis. While our emphasis is on solar cells for producing electrical energy, photolysis is briefly discussed later in the book .1.2 SOLAR CELLS AND SOLAR ENERGY CONVERSIONThe energy supply for a solar cell is photons coming from the sun .This input is distributed ,in ways that depend on variables like latitude, time of day, and atmospheric conditions ,over different wavelengths .the various distributions that are possible called solar spectra. The product of this light energy input, in the case of a solar cell, is usable electrical energy in the form of current and voltage. Some common "standard" energy supplies from the sun, which are available at or on the earth, are plot- ted against wavelength (λ) in W/㎡/nm spectra in Figure 1.l A. An alternative photons/㎡-s/nm spectrum is seen in Figure 1.1B.The spectra in Figure 1.1A give the power impinging per area(㎡)in a band of wavelengths 1 nm wide (the bandwitdth ∆λ)centered on each wavelength λ. In this figure, the AM0 spectrum is based on ASTM standard E 490FIGURE 1.1 Solar energy spectra.(a): Data expressed in watts per ㎡per nm bandwidth for AMO (from Ref .1 with permission) and for AM l.5G, and AW1.5D spectra(from Ref.2, with permission).(b): The AM l.5G data expressed in terms of impinging photons per second per cm²per 20 nm bandwidth.()d hc λλλλΦ⎰oand is used for satellite applications. The AM1.5G spectrum, based on ASTM standard G173, is for terrestrial applications and includes direct and diffuse light .It integrates to 1000 W/㎡.the AM1.5D spectrum,also based on G173 ,is for terrestrial applications but includes direct light only. It integrates to 888 W/㎡. The spectrum in Figure 1.l B has been obtained from the AM1.5G spectrum of Figure 1.l A by converting power to photons per second per cm2 and by using a bandwidth of 20nm. Photon spectra Φ(λ), exemplified by that in Figure 1.l B, are more convenient for solar cell assessments, because optimally one photon translates into one free electron-free hole pair via steps 1 and 2 of the four steps needed for photovoltaic energy conversion.Standard spectra are needed in solar cell research, development, and marketing because the actual spectrum impinging on a cell in operation can vary due to weather, season, time of day, and location. Having standard spectra allows the experimental solar cell performance of one device to be compared to that of other devices and to be judged fairly, since the cens can be exposed to the same agreed-upon spectrum. The comparisons can be done even in the laboratory since standard distributions can be duplicated using solar simulators.The total power Pin per area impinging on a cell for a given photon spectrum Φ。
太阳能发电-中英文翻译Solarelectricalenergygeneration文献翻译
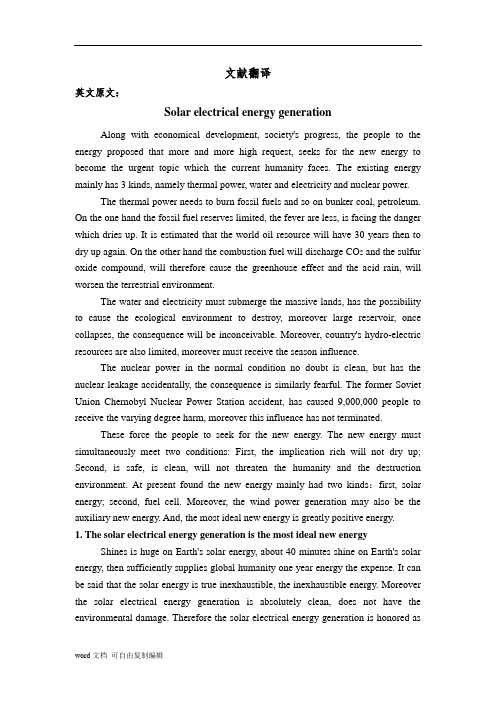
文献翻译英文原文:Solar electrical energy generationAlong with economical development, society's progress, the people to the energy proposed that more and more high request, seeks for the new energy to become the urgent topic which the current humanity faces. The existing energy mainly has 3 kinds, namely thermal power, water and electricity and nuclear power.The thermal power needs to burn fossil fuels and so on bunker coal, petroleum. On the one hand the fossil fuel reserves limited, the fever are less, is facing the danger which dries up. It is estimated that the world oil resource will have 30 years then to dry up again. On the other hand the combustion fuel will discharge CO2 and the sulfur oxide compound, will therefore cause the greenhouse effect and the acid rain, will worsen the terrestrial environment.The water and electricity must submerge the massive lands, has the possibility to cause the ecological environment to destroy, moreover large reservoir, once collapses, the consequence will be inconceivable. Moreover, country's hydro-electric resources are also limited, moreover must receive the season influence.The nuclear power in the normal condition no doubt is clean, but has the nuclear leakage accidentally, the consequence is similarly fearful. The former Soviet Union Chernobyl Nuclear Power Station accident, has caused 9,000,000 people to receive the varying degree harm, moreover this influence has not terminated.These force the people to seek for the new energy. The new energy must simultaneously meet two conditions: First, the implication rich will not dry up; Second, is safe, is clean, will not threaten the humanity and the destruction environment. At present found the new energy mainly had two kinds:first, solar energy; second, fuel cell. Moreover, the wind power generation may also be the auxiliary new energy. And, the most ideal new energy is greatly positive energy.1. The solar electrical energy generation is the most ideal new energyShines is huge on Earth's solar energy, about 40 minutes shine on Earth's solar energy, then sufficiently supplies global humanity one year energy the expense. It can be said that the solar energy is true inexhaustible, the inexhaustible energy. Moreover the solar electrical energy generation is absolutely clean, does not have the environmental damage. Therefore the solar electrical energy generation is honored asis the ideal energy.Obtains the electric power from the solar energy, must carry on the electro-optical transformation through the greatly positive battery to realize. It completely was formerly different with other power source electricity generation principle, has the following characteristic: ①Non-depletion danger; ②Clean (does not have environmental damage) absolutely; ③It is not distributed the resources the region the limit; ④But is using electricity place nearby generates electricity; ⑤The energy quality is high; ⑥The user easy to accept from the sentiment; ⑦The gain energy expenditure's time is short. The deficiency is:①The illumination energy distribution density is small, namely must take the huge area; ②Obtains the energy with four seasons, the day and nights and cloudy clear and so on meteorological conditions concerns. But generally speaking, the flaw does not cover the fine jade, takes the new energy, the solar energy has the enormous merit, therefore receives various countries the value.Must enable the solar electrical energy generation to achieve the practical level truly; first, must raise the solar energy electro-optic conversion efficiency and reduce its cost; second, must realize the solar electrical energy generation with present's electrical network networking.At present, solar panels mainly has the mono-crystalline silicon, the polycrystalline silicon, the amorphous state silicon three kinds. The mono-crystalline silicon solar cell conversion efficiency is highest, has reached above 20%, but the price is also the most expensive. The amorphous state silicon solar cell conversion efficiency is lowest, but the price is the cheapest, from now on most will be hopeful uses in generally generating electricity will be this kind of battery. Once its big area module electro-optic conversion efficiency achieves 10%, each watt generating set price falls to 1-2 US dollars, then sufficiently compete with present's electricity generation way. It is estimated that at the end of this century it may achieve this level.Certainly, in the special use and the laboratory uses the solar cell efficiency must be much higher, if the US Boeing develops by the gallium arsenic semiconductor with the positive electricity place which too the stibium gallium semiconductor overlaps becomes, the electro-optic conversion efficiency may reach 36%, has caught up with the coal-burning electricity generation efficiency quickly. But because it is too expensive, at present can only be restricted on the satellite uses.2. Solar electrical energy generation applicationAlthough solar electrical energy generation day and nights, clear and rain, season influence, but may carry on scattered, therefore it is suitable for various each household minute to carry on the electricity generation severally, moreover must join in the power supply network, causes each family when the electric power is wealthy may sold it to the Electricity company, when the insufficiency be possible from the Electricity company to buy up. Realizes this point’s technology not to be difficult to solve, the key lies in must have the corresponding legal safeguard. Now the US, Japan and so on developed country has made the corresponding law, guaranteed that carries on the solar electrical energy generation the family benefit, encourages the family to carry on the solar electrical energy generation.Japan has realized the solar electrical energy generation system the same electricity company electrical network's networking in April, 1992, had some families to start to install the solar electrical energy generation equipment. The Japanese Ministry of International Trade and Industry started from 1994 take individual housing as an object, implemented to purchases the solar electrical energy generation equipment's expense to subsidize 2/3 systems. Requests the first year had 1000 households families, when 2000 to have 70,000 households families to install the solar electrical energy generation equipment.According to the Japanese Department concerned estimates in the Japanese 21,000,000 households individual housing, if has 80% to install the solar electrical energy generation equipment, then may satisfy 14% which the national total power needs, if units and so on factory and office building also carry on the solar electrical energy generation with the room, then the solar electrical energy generation will occupy the national electric power 30%-40%. The current hindrance solar electrical energy generation popular most primary factor is the expense is expensive In order to satisfy the general family power requirement 3 kilowatt generating system, needs 6,000,000 to 7,000,000 Japanese Yen, has not included the installment wages. The concerned expert believed that when must fall at least to 1,000,000 to 2,000,000 Japanese Yen, the solar electrical energy generation only then can popularize truly. The key to reduce the expense lie in the solar cell to raise the conversion efficiency and to reduce the cost.Some time ago, the US Texas Instruments Company and SCE Corporation announced that they develop one kind of new solar cell, each unit is the diameter less than 1 millimeter bead, they distribute regularly densely and numerously on the softaluminum foil, looks like many silkworm eggs to cling on the paper is the same. Then distributes in about 50 square centimeters area has 1,700 such units. This kind of new battery's characteristic is, although the conversion efficiency has 8%-10%, but the price is cheap. Moreover aluminum foil bottom bush soft solid, may look like the cloth to fold equally at will, and durable, hangs in toward the sun place then may generate electricity, is convenient. It is said that uses this kind of new solar cell, so long as each watt power capacity equipment 1.5 to 2 US dollars, moreover each round of once electricity's expense might also fall to 14 cents about, definitely may compete with the ordinary power plant. Each family hangs this kind of battery on the roof, the wall toward the sun, every year may obtain 1,000-2,000 degrees electric powers.3. Solar electrical energy generation prospectThe solar electrical energy generation has a more exciting plan. First, Japan proposes creates the century plan. Prepares the desert and the sea area carries on the electricity generation using the ground, and through superconducting cable whole world solar power station connection unification electrical network in order to global. According to reckoning, to 2000, in 2050, in 2100, even if all uses the solar electrical energy generation supplies the whole world energy, the occupying land area is also 651,100 square kilometer, 1,867,900 square kilometer, 8,291,900 square kilometers. 8,291,900 square kilometers only occupy the complete sea area 2.3% or the complete desert area 51.4%, even is the Sahara area 91.5%. Therefore this plan has the possibility to realize.Another one is the space electricity generation plan. As early as in 1980 the NASA and Department of Energy proposed that in the spatial construction solar power station tentative plan, prepares on the synchronous orbit to put one long 10 kilometers, to extend 5 kilometer big plates, above covers entirely the solar cell, like this then may provide 5,000,000 kilowatts electric powers. But this needs to solve to the ground wireless electric transmission question. Already proposed with the micro wave beam, the laser beam and so on each kind of plan. At present although has realized the short distance, the short time, the low power microwave wireless electric transmission with the mockup, but to true practical also has the long distance.Along with our country technology's development, in 2006, China had three enterprises to enter global first ten, symbolizes that China will become one of global new energy science and technology central, in the world the solar energy light bends down widespread application, what caused present to be deficient was raw materialsupply and the price rise, we needed dissemination of technology at the same time, to use the new technology, with the aim of reducing the cost large scale, was this new energy long-term development provides the driving force!The solar energy use mainly divides into several aspects: The family with the small solar energy power plant, the large-scale incorporation power plant, the building integration light bends down the glass curtain wall, the solar energy street light, the scenery supplementary street light, the scenery supplementary power supply system and so on, now main application way for construction integration and scenery supplementary system.The world present had the nearly 200 companies to produce the solar cell, but produces the plants mainly hand in the Japanese business.Recent years the South Korean Tri-star, LG expressed the positive participation's desire, China two sides across the Taiwan Strait are similarly very warm-hearted. It is reported that our country Taiwan in 2008 crystallizes the silicon solar cell productivity to reach 2.2GW, later will expand by every year 1GW productivity in the past and started to produce the thin film solar cell, this year will strengthen vigorously, Taiwan anticipated that “the solar cell great nation” emulated to Europe. in 2010 various countries and the area have above 1GW the productive plan solar cell manufacturer to have Japanese Sharp, German Q-Cells, Scho~Solar, turns 5 prestige RWE Solar, Chinese Suntech Power and so on 5 companies, above other 7 500MW productivity company.Recent years the world solar cell market advanced triumphantly, an excellence, but the rare financial storm brought the economic crisis, was similarly presses in solar cell market on dark clouds, the Major enterprise like Germany Q-Cells achievement declined accordingly, because pre-year the world too positive electricity market also the demand will be this year worn out, the petroleum price dropped, but the competitive power counter-promotion and so on disadvantage factor lowered But at the same time, the people also see the US. After the Obama comes on stage, soon applies the Green New Deal policy, may have 150,000,000,000 US dollar subsidy funds including the among them green energy program, Japan will also carry out the subsidy system to continue to popularize solar cell's application4. Solar cell electricity generation principle:The solar cell is pair of light has the response and can transform the energy of light the electric power the component. Many kinds of materials can produce the lightto bend down the effect, for example: Mono-crystalline silicon, polycrystalline silicon, amorphous silicon, gallium arsenic, selenium indium copper and so on. Their electricity generation principle basic same, presently take crystal as example description light electricity generation process. The P crystalline silicon may result in the N silicon after the doping phosphorus, forms the P-N knot.When light illumination solar cell surface, part of photons by silicon material absorption; The photon energy transfer has given the silicon atom, caused the electron to occur more moved, becomes the free electron to tie the both sides in P-N to gather has formed the potential difference, when exterior key-on, under this voltage's function, will have the electric current to wind through the exterior electric circuit to have certain output. This process's essence is: The photon energy transforms the electrical energy the process.5. Crystalline silicon solar cell's manufacture process:The silicon is on our star preserves one of most abundant quantity materials. Had discovered after the 19th century scientists crystalline silicon semiconductor characteristic, it changed all nearly, even humanity's thought. 20 century's ends, in our life everywhere obviously “silicon” the f orm and the function, the crystalline silicon solar cell is in the recent 15 years forms the industrial production to be quickest. The production process may divide into five steps approximately: a、depuration process.b、pulls good process.c、slice process.d、system battery process.e、and the seal process.6. Solar cell's application:In the 1960s, the scientists already applied the solar cells in the spatial technology-communication satellite power supply, on the century's end, in the human self-introspection's process, bends down unceasingly regarding the light generates electricity this kind so clean and the direct energy form already even more kind, not only in the spatial application, but also gives full play in the numerous domains.For example: The solar energy garden lamp, the solar electrical energy generation household with the system, the stockaded village power supply's independent system, the light bends down the water pump (potable water or irrigation), the correspondence power source, the petroleum oil pipeline cathodic protection, the fiber optic cable communications pumping station power source, in the seawater desalination system, the cities the guidepost, the highway guidepost and so on. Europe and America and so on advanced countries bend down the electricitygeneration the light to merge the city to use electricity the system and the remote border district nature village power supply system integrate the development direction. The solar cell and the building system's union already formed the industrial production tendency.参考译文:太阳能发电随着经济的发展、社会的进步,人们对能源提出越来越高的要求,寻找新能源成为当前人类面临的迫切课题。
太阳能相关英文文献翻译

Solar Tracker for Solar Water HeaterAbstractThe Solar Tracker team was formed in the fall of 2005 from five students in an ME design team, and a Smart House liaison. We continued the work of a previous solar tracker group. The task was to design a prototype tracking device to align solar panels optimally to the sun as it moves over the course of the day. The implementation of such a system dramatically increases the efficiency of solar panels used to power the Smart House. This report examines the process of designing and constructing the prototype, the experiences and problems encountered, and suggestions for continuing the project.1.IntroductionSolar tracking is the process of varying the angle of solar panels and collectors to take advantage o f the full amount of the sun’s energy. This is done by rotating panels to be perpendicular to the sun’s angle of incidence. Initial tests in industry suggest that this process can increase the efficiency of a solar power system by up to 50%. Given those gains, it is an attractive way to enhance an existing solar power system. The goal is to build a rig that will accomplish the solar tracking and realize the maximum increase in efficiency. The ultimate goal is that the project will be cost effective – that is, the gains received by increased efficiency will more than offset the one time cost of developing the rig over time. In addition to the functional goals, the Smart House set forth the other following goals for our project: it must not draw external power (self-sustaining), it must be aesthetically pleasing, and it must be weatherproof.The design of our solar tracker consists of three components: the frame, the sensor, and the drive system. Each was carefully reviewed and tested, instituting changes and improvements along the design process. The frame for the tracker is an aluminum prismatic frame supplied by the previous solar tracking group. It utilizes an ‘A-frame’ design with the rotating axle in the middle. Attached to the bottom of this square channel axle is the platform which will house the main solarcollecting panels. The frame itself is at an angle to direct the panels toward the sun (along with the inclination of the roof). Its rotation tracks the sun from east to west during the day.The sensor design for the system uses two small solar panels that lie on the same plane as the collecting panels. These sensor panels have mirrors vertically attached between them so that, unless the mirror faces do not receive any sun, they are shading one of the panels, while the other is receiving full sunlight. Our sensor relies on this difference in light, which results in a large impedance difference across the panels, to drive the motor in the proper direction until again, the mirrors are not seeing any sunlight, at which point both solar panels on the sensor receive equal sunlight and no power difference is seen.After evaluation of the previous direct drive system for the tracker, we designed a belt system that would be easier to maintain in the case of a failure. On one end of the frame is a motor that has the drive pulley attached to its output shaft. The motor rotates the drive belt which then rotates the pulley on the axle. This system is simple and easily disassembled. It is easy to interchange motors as needed for further testing and also allows for optimization of the final gear ratio for response of the tracker.As with any design process there were several setbacks to our progress. The first and foremost was inclement weather which denied us of valuable testing time. Despite the setbacks, we believe this design and prototype to be a very valuable proof-of-principle. During our testing we have eliminated many of the repetitive problems with the motor and wiring so that future work on the project will go more smoothly. We also have achieved our goal of tracking the sun in a ‘hands-off’ demo. We were able to have the tracker rotate under its own power to the angle of the sun and stop without any assistance. This was the main goal set forth to us by the Smart House so we believe our sensed motion prototype for solar tracking will be the foundation as they move forward in the future development and implementation of this technology to the house.2. Defining the ProblemThe project was to complete the “REV 2” design phase of the solar tracker to be used on the Smart House. While the team was comprised of members from the ME160 senior design course, the customer for this project was to be the Smart House organization. Jeff Schwane, a representative from the Smart House, was our liaison and communicated to our group the direction Smart House leadership wished us to proceed.At our first meeting with Jeff and Tom Rose, the following needs were identified:1.Track the sun during the daye no external power source3.Weather proof4.Cost effective power gain5.Must look good6.Solar panel versatile i.e. can fit different types of panelsWith these needs in hand, we constructed a Quality Function Deployment chart. This chart can be found in Appendix A. The QFD showed the major areas of concern might have been: number of panels/size of panels, internal power requirements, motor torque required.At our first meeting we were also able to set up our goals for the semester. Having a working prototype capable of tracking the sun was to be the main goal for the end of the semester, but we soon found that in order to accomplish this, we would be forced to omit portions of the design criteria in hopes they would be worked out later. This would result in the optimization of platform space on the roof to be irrelevant, with our goal being to have one platform track. It also led to the assumption that our base would not need to be tested for stability or required to be fastened to the roof. With an idea of where we were to begin, from scratch with the possibility of using the frame from the “REV 1” design, and an idea of where we were to finish, with a moving prototype, we constructed the Gantt chart that can be found in Appendix B. Our group planned to meet with Jeff once a week to make sure we were on track with the needs of the Smart House. Jeff would also meet with Tom Rose, the director of Smart House, at least once a week in order to keep everyone on the same page. With our goals in mind weembarked on the process of idea generation.3. Concepts and Research3.1 Tracking TypeOur group used a brainstorming approach to concept generation. We thought of ideas for different solar tracking devices, which proved difficult at times due to the existing frame and concept presented to us by Smart House. Other concepts were generated through research of pre-existing solar tracking devices. Originally our concept generation was geared towards creating a completely new solar tracker outside of the constraints of the previous structure given to us by Smart House. This initial brainstorming generated many concepts. The first one was a uni-axial tracking system that would track the sun east to west across the sky during the course of a day and return at the end of the day. This concept presented the advantage of simplicity and presented us with the option to use materials from the previous structure (which was also intended to be a uni-axial tracker) in construction. Another more complex concept was to track the sun bi-axially which would involve tracking the sun both east to west and throughout the seasons. The advantage of this concept was a more efficient harvesting of solar energy. The third concept was to only track throughout the seasons. This would provide small efficiency gains but nowhere near the gain provided by tracking east to west.The different structures we came up with to accomplish tracking motion included a rotating center axle with attached panels, hydraulic or motorized lifts which would move the main panel in the direction of the sun, and a robotic arm which would turn to face the sun. The clear efficiency gains coupled with the simplicity of design of the uni-axial tracking system and the existence of usable parts (i.e. motor and axle) for the rotating center axle structure, led us to the choice of the East to West tracking, rotating center axle concept.3.2 StructureOnce the method of motion was chosen, it was necessary to generate concepts for the structural support of the axle. Support could be provided by the triangular prismatic structure which was attempted by the previousSmart House solar tracker group or through the use of columns which would support the axis on either side. While the prismatic structure presented the advantage of mobility and an existing frame, the columns would have provided us with ease of construction, simple geometric considerations, and ease of prospective mounting on the roof. Due to the heightened intensity of time considerations, the previous financial commitment to the prismatic structure by Smart House, and our limited budget, the presence of the pre-existing frame proved to be the most important factor in deciding on a structure. Due to these factors we decided to work within the frame which was provided to us from the previous Solar Tracker group.3.2 Tracking MotionOnce the structural support was finalized we needed to decide on a means to actualize this motion. We decided between sensed motion, which would sense the sun’s position and move to follow it, and continuous clock type motion, which would track the sun based on its pre-determined position in the sky. We chose the concept of continuous motion based on its perceived accuracy and the existence of known timing technology. During the evaluation stage, however, we realized that continuous motion would prove difficult. One reason was the inability to draw constant voltage and current from the solar panels necessary to sustain consistent motion, resulting in the necessity for sensing the rotation position to compensate. Continuous motion also required nearly constant power throughout the day, which would require a mechanism to store power. Aside from these considerations, the implementation of a timing circuit and location sensing device seemed daunting. After consulting Dr. Rhett George, we decided on a device using two panels and shading for sensed motion.4. Analysis and Embodiment4.1 Structure GeometryThe geometry of the frame was created in order to allow the solar panels to absorb light efficiently. This was done by allowing rotation in the east-west direction for tracking the sun daily and a 36°inclination (Durham’s latitude) towards the south. Because this frame was designedto be placed on a roof with a slope of 25°, the actual incline of the frame was made to be 11°.The geometry of the existing platform structure was modified. This was done in order to incorporate the results from the Clear Day Model supplied to us by Dr. Knight. This model led to the conclusion that the platform should track to up to 60° in both directions of horizontal. Thus, the angle range of the frame had to be increased. The sides of the frame were brought in to increase the allowable angle of rotation, and they were brought in proportionally to maintain the inclination angle of 11°. Also, crosspieces were moved to the inside of the frame to allow greater rotation of the platform before it came into contact with the support structure.The panels used for sensing and powering rotation were placed on the plane of the platform. Mirrors were placed perpendicular to and in between the panels to shade one and amplify the other in order to produce a difference to power the motor. The sensing panels were placed outside the platform area to maintain the largest area possible for collecting panels. A third sensing panel was mounted nearly vertical and facing east to aid rotation back towards the sun in the morning. This panel was attached to the frame under the platform, so that during most of the day, it’s shaded with minimal effec ts on sensed rotation.Minimizing the torques on the motor was a main concern in order to minimize the motor power needed. The platform designed for the placement of the collecting solar panels was placed under the rotational shaft so that the panels would be aligned with it the rotational axis. Since the main panels comprise the majority of the weight putting these in the plane of the rotational axis reduces torque on the shaft. The sensing panels were placed symmetrically about the axis of rotation in order to prevent additional torque on the motor. The third panel was attached to the frame instead of the platform or rotational shaft so as to also avoid any torque.4.2 MaterialsMaterials selection for most of the frame was simple because it had already been constructed. The mirrors used for the amplification andshading of the sensing panels were also already purchased and available for use. Additional parts for attachment of the panels and mirrors to the frame were taken from the scrap pieces available in the machine shop. In our selection of sensing panels, size and power needed to be balanced effectively. The panels were to be as small as possible in order to add minimal stress and weight to the frame but also needed to be powerful enough to power the rotation of the platform. Therefore, the most powerful of the intermediate sized panels available were selected. The panels purchased also appeared to be the most reliable of our options. 4.3 Drive MechanismAfter designing a prototype and testing it, the motor purchased and used by the previous solar tracker group was slipping. It was removed, and the installation of a gear system with another simple motor was suggested and attempted. Professor Knight supplied some gears as well as some belts and pulleys. One end of the shaft was lathed so that one of the pulleys could be set on it, and spacers were bought so that a 6V motor we had available could power another pulley. These pulleys were to be connected by a belt. This motor demonstrated insufficient strength to turn the rotational shaft. The original motor, once detached, was taken apart and examined. Itappeared to be working again so a new pulley was purchased to fit it and was attached in the place of the 6V motor.5. Detailed Design5.1 FrameThe frame was designed from one inch square aluminum tubing, and a five foot long, two inch square tube for the axle. It is constructed with a rigid base and triangular prismatic frame with side supporting bars that provide stability. The end of the axle is attached to a system of pulleys which are driven by the motor. It is easily transported by removing the sides of the base and folding the structure.5.2 SensorOur sensing panels are bolted to the bottom of the main solar panel frame and braced underneath with half inch L-brackets. The mirrors are attached to the inside of the sensing panels and braced by L-brackets as well. The whole structure attaches easily to the main panel frame which isattached to the main axle using four 2-inch U-bolts. A third panel is bolted to the structure to return the main panels direction towards the horizon of sunrise.5.3 How the Sensor WorksOur sensor creates movement of the motor by shading one of the panels and amplifying the other when the system is not directly facing the sun. The two sensing panels are mounted parallel to the main panels symmetrically about the center axle with two mirrors in between them. The shading on one of the panels creates high impedance, while the amplified panel powers the motor. This happens until the panels receive the same amount of sunlight and balance each other out (i.e. when the sensing panels and main panels are facing the sun.). We initially attempted using a series configuration to take advantage of the voltage difference when one of the panels was shaded (Appendix C). This difference, however, was not large enough to drive the motor. We subsequently attempted a parallel configuration which would take advantage of the impedance of the shaded panel (Appendix C) and provide the current needed to drive the motor. Once the sensing mechanism has rotated from sunrise to sunset, the third panel, which is usually shaded, uses sunlight from the sunrise of the next day to power the motor to return the panels towards the direction of the sun.6. Prototype TestingInitial testing was done using just the sensing component and a 6V motor. The panels were tilted by hand to create shading and amplification.A series configuration of the sensing panels was initially tested and proved ineffective. Data acquisition showed a maximum of a 2V difference across the motor, which was insufficient to power it. Upon testing the panels individually, it was discovered that the open voltage across each individual panel would only vary between 21.5V and 19.5V when fully amplified and fully shaded, respectively. The current running through each panel, however, was seen to fluctuate between nearly 0 amps when shaded, up to 0.65 amps when fully amplified. Therefore, in order to take advantage of the increase in impedance of the solar panels due to shading, we chose to put our sensing panels in parallel with eachother and the motor. Tests with this configuration turned the motor in one direction, stopped when the sensing panels were nearly perpendicular to the sun, and reversed direction as the panels rotated past perpendicular. We found the angle range necessary to stop the motor to be very small. It was also observed that the panels rotated to slightly past perpendicular when they ceased motion. This error may be due to a difference in the innate resistance in each individual sensing panel. When tested it was found that one panel had a resistance of 52 kΩ, and the other panel resistance was 53 kΩ. Other testing found the voltage and current provided by the sensing solar panels to the motor to be consistent at all points, excluding when the solar panels are directly facing the sun. Through testing it was concluded that resistance may need to be added to one of the panels to compensate for the differences in the internal resistances of the individual panels, and a voltage regulator needs to be added to decrease the voltage seen across the motor. The original motor was prone to failure as its slippage caused the breakdown of our initial prototype after testing. This led to the institution of the pulley and belt driven system which would allow for easier maintenance given motor failure or slippage. The success of our initial testing and prototype proved to us the efficacy of our solar tracker design.7. ConclusionThroughout this project we enlisted the support of multiple resources (i.e. ME and EE professors, previous Smart House teams). We learned early on that a clear problem definition was essential to efficient design and progress. We struggled initially as we tried to design a tracking device that was diffe rent from the previous solar tracker group’s attempt, without fully weighing the size of their investment and the advantages of using the existing frame for our purposes. As we worked with the fixed frame construction from the previous group we learned that variability of design is key, especially when in the initial phases of prototyping. After many setbacks in testing of the solar panels, we learned that when working with solar panels, much time needs to be set aside for testing due to the unpredictability of the weather.The actual implementation of using the prototype in its intendedlocation on the Smart House roof requires weather-proofing to protect the wiring and electrical connections from the elements, housing for the motor, a bracing system to attach the structure to the roof, and possible redesign to eliminate excess height and simplify overall geometry. The efficiency of the sensor system could be improved by widening the mirrors or by placing blinders along the sides of the panels to decrease the effects of reflected and refracted light incident on the shaded sensing panel.适用于太阳能热水器的太阳能跟踪器摘要太阳能跟踪器设计团队成立于2005年秋季,设计团队由五名队员组成,我们还负责与智能家居的联络工作。
- 1、下载文档前请自行甄别文档内容的完整性,平台不提供额外的编辑、内容补充、找答案等附加服务。
- 2、"仅部分预览"的文档,不可在线预览部分如存在完整性等问题,可反馈申请退款(可完整预览的文档不适用该条件!)。
- 3、如文档侵犯您的权益,请联系客服反馈,我们会尽快为您处理(人工客服工作时间:9:00-18:30)。
1引言
可再生能源, 如风力和太阳能被认为是非常前途的能源。它们拥有可以满足 不断增加的世界能源需求的特点。另一方面,他们是基于无公害转换流程,它们 需要的主要资源是取之不尽,用之不竭,并且免费的。对于远程、远离电网的地 方,它往往是比用输电线路[1] 提供一个独立的电力来源拥有可行性。在这些电 网中, 在混合动力系统结合模块的基础上, 可再生能源发电以柴油为动力的备用 发电机已考虑ERED等效为一个可行的选择[2, 3]。然而,柴油发电机在孤立的燃 料供应和其运作领域是相当麻烦,相比较可再生能源,显得不划算[4]。为了取 代柴油备用发电机,独立的混合动力系统经常采用结合可再生能源来源的TARY 型材,如风力和光伏发电,合适的存储设备,如电池。自存储成本仍然是一个重 大的经济约束,通常光伏/风能/电池系统是用“适当”的大小以减少资本成本。 本文提出了一种控制策略,以规范的混合动力系统,包括光伏发电和风力 发电,蓄电池组和可变负载的输出功率作为研究。控制可调整的光伏发电、风力 发电, 以满足负载和电池充电的电源要求。系统以在独立控制下的最大发电的主 要目标。该控制器的设计开发,在之前的文献[5]中提过。因此,根据不同的大 气条件,不同的光伏阵列控制律使用的范围不同。第一条用在暴晒的地方,运作 模式足以提供的总功率需求,和风力发电一起适用。另一条控制律是在曝晒度不 足情况下跟踪最大功率操作点(MPOP),使系统保持尽可能多的储存的能量。 跟踪MPOP的方法是一个新的扩展版本下的IncCond算法[6]。 对于这两种操作模式设计控制律均使用滑模方法。这种技术很有吸引力,它 简化了设计任务,并使控制器具有鲁棒性。此外,根据第二次的运作模式,这种 技术提供的MPOP收敛速度最快。
2光伏电池的电气特性
光伏电池产生的瞬时电能取决于几个电池参数和变量的环境条件, 如日照和 温度。其电动行为可以用简单的非线性电流源串联与内在电池串联电阻(R s )为基 础。在这种模式下的电流源,可以通过下面表达式表示[6-8]: ipv = Iph − Irs eq v pv +i pv R s AKT − 1 ① 其中Iph 是一个给定的曝晒下的电流,Irs 是电池反向饱和电流,ipv 和 v pv 分 别是输出电流和太阳能电池的电压,q是电子电荷,K为波尔兹曼常数,T为电池 的温度。因子A看成理想的p-n结特性的电池偏差,值在的1到5之间[6]。此外,反 向饱和电流(Irs )和光照下(Iph )取决于日照和温度: T Irs = Ior ( )3 eqE go 1 T r −1 T KT ② Tr
4.2第二种运作模式:发电条件不足 不足发电条件下必须改变操作单元阵列最大功率点的控制目标。 MPOP依赖大气 条件所以它必须跟踪。 已有文献报道用不同的技术来实现这一目标。其中有些是 基于测量大气条件[8],其他方法有用改变阵列配置[11],以及其他基于算法不断 调整光伏阵列的有效载荷[6,7,12]。所有这些方法当中,相比最成功的为MPOP 跟踪的,因为它们不受特定的大气条件或实际负载影响[6]。这些算法,通常被 称为扰动与观察(P&O)算法,通过工作点的离散转变生产和检测结果的光伏 输出功率变化。如果输出功率的增加,转变将在同一方向,反之则反。自适应可 以包含在这些算法中,一旦MPOP已达到[13]它可以减少收敛时间和扰动过程中 的功率损耗减少。P&O算法的主要缺点是,他们无法应付快速变化的大气条件 ,因为他们无法在扰动的大气条件区分输出功率的变化。为了克服这个问题,在 [6]中提出一种不同的方法,称为IncCond。增量和瞬时电导测量要依据eqn.1源控制发电系统
摘要
变结构控制器来调节输出功率的一个独立的混合发电系统。 该系统包括光伏 发电和风力发电, 存储电池组和一个变量的单相负载。控制律承认两种操作模式 。 第一条用在当日晒度足够满足对电力的需求的情况下。第二运作模式应用在 日晒度不足的时候。后者致使系统在最大功率操作点(MPOP)操作下存储尽可能 多的能量。根据IncCond算法开发的一种新方法。滑模控制用于技术设计的控制 律。这些技术提供了一个简单的控制律设计框架,并有助于它们自带的鲁棒性。 最后,指导方针根据考虑为实际系统的设计。
Iph = (Isc + K1 (T − Tr ))λ 100 ③ 其中Ior 是在参考温度Tr 下的反向饱和,Ego 是在电池中所使用的半导体的带 隙能量,Isc 是在参考温度下日照电流,K1 是短路电流温度系数,λ 为日照系数 其单位是 mW cm2 。这些常量的典型值在附录(第8篇)中。 在图1中, 是一个特定的光伏电池的电气特性。其中提出了把日照作为一个可 变参数,并考虑两个不同日照下的温度值。图2所示,可以观察到的大气条件下 MPOP对系统的影响。 在光伏电池阵列中,产生的电流表达式类似于eqn. 1: ipv = np Iph − np Irs eq v pv +ipv R s AKT − 1 ④ 其中np 代表并行模块的数量,由ns 个串联的电池构成。因此,由eqn.4可得 简单的阵列发电的表达式: ppv = np Iph vpv − np Irs vpv eq v pv +i pv R s AKT − 1 ⑤ 从上述表达式得到,通过改变vpv 值可最大限度地提高发电,它由暴晒和电 池温度而定。
基础上。但是,报告中的算法保持一个固定步实施,最终可能限制对MPOP的收 敛速度。 对于这种操作模式, IncCond方法滑模控制在发电条件不足的下的设计要满 足eqn.10: ∂ipv ipv h2 − + =0 (18) ∂vpv vpv 然后,基于滑动面的考虑,可以看出,横截条件根据MPOP实行: ipv 2io ipv ∂h2 −io ∂ipv Lg h2 = T g x = + ≌ (19) ∂x Cv pv ∂vpv vpv CV 2 PV 因此,要实现滑动的存在条件,切换的控制信号必须是: 0 if h2 ≥ 0 u= (20) 1 if h2 < 0 在这种情况下,相当于控制假设下面的表达式: 0 if h2 ≥ 0 u= (20) 1 if h2 < 0 然后,考虑eqn.18和eqn.7 ,eqn.21,理想的滑模动态将写成: vb vpv ipv io = − + (22a) L L io i vc = Cb (22b) Eqn. 22a清楚地显示了一个稳定的平衡点。注意到根据标志 ib ,eqn.22b表示 稳定或不稳定的动态。在第一种情况,当 ib 的标志是负的,稳定的动力学特征代 表电池组的放电。反之,当其标志是正的,这个公式代表非最小相位相同的(行 为在上一节分析)。唯一不同的是,在这种情况下,电池组充电通过 ib 改变而不 是 Ib ref 。 在整个模式建立中,控制律将开关固定在一个位置(打开或关闭)。这样, MPOP对收敛速度的影响取决于三个因素,即转换器的活性元素,大气条件和负 载的大小。因此,IncCond方法滑模技术提出对MPOP进行最快的速度收敛这一概 念。 一旦系统达到滑动流形切换控制律就可以使系统保持在滑动面上。然而, 考 虑到IGBT的有限开关频率,系统代表了典型的抖振系统。MPOP周围的振荡行为 , 一方面是由于不同的大气条件在不变或缓慢的情况下有功率损耗,但另一方面 ,它有利于增量电导的测量。在4.4节给出了关于此方面的指导方针。 4.3综合控制法 真正的最终控制法包括两种操作模式,可以通过下面的表达式表达: ∂ipv if − v 2 > Pref ∂vpv pv 1 if hl ≥ 0 then 1st mode of operation 0 if hl < 0 (23) ∂ipv 2 if − v ≤ Pref ∂vpv pv 0 if h2 ≥ 0 then 2nd mode of operation 1 if h2 < 0 当大气条件足以满足要求的能量,提出的控制律,分别建立两区的第一和第 二操作模式。要确定每种模式的域,如图6所示,光伏阵列和控制器所产生的电
3系统建模
光伏发电系统通常通过固态转换器连接负载。 这种拓扑结构允许光伏发电系 统调节其发电端电压。此外,为减少电能供应的概率,光伏阵列往往与其它发电 系统(风电,柴油等)或一些储能系统(主要是电池)相结合。通过这种方式, 系统可以应付变化莫测的天气条件,增强系统的可靠性[4]。
混合发电系统拓扑的不同取决于它涉及的模块和系统的主要意图。 根据本文 考虑结构如图 3 。这种拓扑结构由蓄电池组确定直流母线电压。光伏阵列通过 DC/DC降压转换器连接。在另一侧,直流母线通过高压变频器连接到负载。负载 将直流侧电流作为输出电流iL 。最后,电流iw iL 表示风力发电模块,但在一般情 况下,在混合动力系统中它要考虑到许多其他的综合效应来源。 混合动力系统的动态模型可以通过瞬时切换模式的DC / DC降压转换器建立 ,以下是描述方程: ipv io vpv = − u (6a) C C v pv vb io = − L + L u (6b) 其中io 和 vb ,是DC / DC转换器输出端子的电压和电流,u是开关控制信号 ,它只能采取离散值0(开关打开)或1(开关闭合)。 然后,考虑到电池组模型,包括一个理想的电压源(Eb ),电容器(Cb )和电阻 (R b ) [9],整个动态串联系统模型可以写成: ipv io vpv = − u (7a) C C v v pv io = − Lb + L u (7b) vc = C (io + iw − iL )
4.1第一个操作模式:充足的发电条件 这种运作模式下的暴晒条件和电池温度都足以满足Pref .。要实现滑模这一目表要 用到电池组的电流即: hl = iL + Ib ref − iw − io = 0 (12) 为了建立滑模模型要满足[10]中所提条件。因此,滑模需要满足eqn.12中的 条件:
vpv ∂hl g x =− (13) T ∂x L 这始终是消极的。然后,为了实现滑动存在的条件[10],切换的控制信号必 须是: 1 if hl ≥ 0 u= (14) 0 if hl < 0 等效控制 ueql 是连续控制信号用来保持表面的不变性,得到 ∂h ∂h ∂h hl x = T x = T f x + T g x ueql = 0 (15) ∂x ∂x ∂x 即 Lf hl (x) vb ueql x = = (16) Lg hl (x) vpv 然后,把eqn. 16代入 eqn. 7,理想的滑模动态可得: ipv io vb vpv = − (17a) C C vpv Ib vc = ref (17b) Cb Eqn. 17a绘制在图5。 由此可以看出,有两个平衡点的光伏阵列可以提供所需 的电流。 B点是稳定的,显然是所需的操作点。另一方面A点明显不稳定,在这 种操作模式下系统永久运行。 然而,最终的控制策略不会允许一个是一个有效的 操作点(4.3节中给出更多的细节)。 可以指出的是,eqn.17b代表非最小相位行为。这种行为的物理意义是很清楚 的:它代表了电池组能源再利用。 Lg hl =