机床主要参数的确定
机床参数及详解

机床参数无论是哪种型号的CNC系统都有大量的参数,少则儿百个,多则上千个,看起来眼花缭乱。
经过认真讨论,归纳起来又有肯定的共性可言,现供应其分类方式以做参考。
1、按参数的表示形式来划分,数控机床的参数可分为三类。
(1)状态型参数状态型参数是指每项参数的八位二进制数位中,每一位都表示了一种独立的状态或者是某种功能的有无。
例如FANUCO-TD系统的1号参数项中的各位所表示的就是状态型参数。
(2)比率型参数比率型参数是指某项参数设置的某几位所表示的数值都是某种参量的比例系数。
例如FANUCO—TD系统的512、513、514号参数项中每项的八位所表示就是比率型参数。
(3)真实值参数真实值参数是表示某项参数是直接表示系统某个参数的真实值。
这类参数的设定范围一般是规定好的,用户在使用时肯定要留意其所表示的范围,以免千百万设定参数的参数超出范围值。
例如FANUCO—TD系统的522、523、524、525号参数项中每项的八位所表示的就是比率参数。
2、按参数本身的性质可分为两类(1) 一般型参数凡是在CNC制造厂家供应的资料上有具体介绍参数均可视为一般型参数。
这类参数只要按着资料上的说明弄清含义,能正确、敏捷应用即可。
(2)隐秘级参数隐秘级参数是指数控系统的生产厂在各类公开发行的资料所供应的参数说明中,均有一些参数不做介绍,只是在随机床所附带的参数表中有初始的设定值,用户搞不清其具体的含义。
假如这类参数发生转变,用户将不知所措,必需请厂家专业人员进行维护和修理。
西门子840D主要参数意译西门子8 4 0 D的主要参数释义文字一、通道机床数据20000通道名称20050几何轴•通道轴的安排20060通道中的几何轴名称20070通道中机床轴号20220通道中的通道轴名称20220主导主轴的号20222主轴旋转的使能/使能取消20224轴运行的M运行(西门子模式)20225轴运行的M功能(外部模式)20226 T, M刀具地址代号转变20228在MMC上显示轴20220带面对轴功能的几何轴20228大事驱动程序调用的设置20229 Prog-Events 的属性20220 RESET复位时的基本功能设置20222 NC启动的基本功能设置20224方式转变中断了MDI20226带读限制的中断程序关闭20227带信号的中断程序关闭20228几何轴转变自动使能20220复位时刀具生效20221复位的预选刀具20222 RESET复位/启动和TC时刀具生效20223 RESET 时$P_USEKT 的预选值20224刀具夹持装置号20226 RESET复位时刀架生效20228换刀在搜寻中20220 RESET复位时刀沿生效20222有效总偏差复位20220用复位健使转换生效。
5、标准机床参数的设定

标准机床参数的设定1)多次按压MDI键盘上的[SYSTEM]按键,直至屏幕横向功能条出现[参数设定],通过对应横向软键选择,选择后,画面跳转为[参数设定支援]画面。
2)移动光标至[轴设定],通过横向软件选择[操作]---[初始化]---出现[是否设定初始值?]---选择[执行],系统自动将轴设定中的相关参数设定为标准值。
3)设定完成后,将跳转至[报警信息]画面,并增加了[PW0000 必须关断电源]的报警,忽略此报警,再次选择[SYSTEM]按键,进入[参数设定支援]画面,移动光标至[轴设定]处,通过横向软键选择[操作]---[选择],进行以下标准参数设定。
轴设定参数设置列表参数号参数名称参数中文注解设定值1006#3 X DIA 各轴的移动指令为:0: 半径指定。
1: 直径指定。
11320 XZ LIMIT + 各轴的存储行程限位的正方向坐标值调试期间不使用软限位时,此参数设置为-1.机床动作调试完毕后,此参数设置应距离硬件限位5mm。
1321 XZ LIMIT - 各轴的存储行程限位的负方向坐标值调试期间不使用软限位时,此参数设置为1.机床动作调试完毕后,此参数设置应距离硬件限位5mm。
1410 DRY RUN RATE 空运行速度此参数设置为机、电、液协议中轴快速移动速度的一半1420 XZ RAPID FEEDRATE 各轴的快速移动速度此参数设置为机、电、液协议中轴快速移动速度。
1421 XZ RAPID OVR F0 每个轴的快速移动倍率的F0 速度200mm200mm1423 XZ JOG FEEDRA TE 每个轴的JOG 进给速度1000mm1000mm1424 XZ MANUAL RAPID 每个轴的手动快速移动速度此参数设置为机、电、液协议中轴快速移动速度的一半1425 XZ REF RETURN FL 每个轴的手动返回参考点的FL 速度300mm300mm1428 XZ REF FEEDRA TE 每个轴的参考点返回速度3000mm3000mm4)设置参数完毕后,选择横向软键左侧的[回退键],并通过横向软键选择[参数设定],返回至上一级画面,移动光标至[伺服设定]处,通过横向软键选择[操作]---[选择],进入[伺服设定]参数画面,并根据下表设置相应参数 参数名称 中文注解设定值电机代码由于0ID 系统要求使用HRV2功能,所以调试时应根据电机铭牌查询电机代码,并加100为设定值。
如何正确选择数控机床的使用参数

如何正确选择数控机床的使用参数数控机床作为一种重要的现代化加工设备,广泛应用于汽车制造、航空航天、机械制造等领域。
选择正确的使用参数对于保证加工质量、提高生产效率至关重要。
本文将从机床的类型、加工材料、加工工艺等方面来探讨如何正确选择数控机床的使用参数。
首先,在选择数控机床的使用参数之前,我们需要了解加工的具体需求以及机床的类型。
数控机床有多种类型,包括铣床、车床、钻床等,每一种类型的机床在使用参数上也会有所不同。
例如,在选择车床的使用参数时,需要考虑所加工零件的直径、长度、精度等因素。
在选择铣床的使用参数时,则需要考虑工件的尺寸、表面粗糙度要求、加工刀具的类型等因素。
因此,在选择数控机床的使用参数时,必须充分了解所加工零件的具体要求,合理选择机床类型,并根据不同类型的机床进行参数的设置。
其次,在选择数控机床的使用参数时,需考虑所加工材料的类型、性质和硬度。
不同的材料对机床的使用参数有着不同的要求。
例如,对于硬度较高的金属材料,应选择较高的切削速度和进给速度,以确保切削刀具与工件之间的接触时间较短,并减小切削力,提高加工效率。
而对于脆性材料,应选择较小的进给速度和切削速度,以避免过大的切削力造成工件断裂或表面破坏。
在选择数控机床使用参数时,必须根据材料的性质和硬度来调整切削速度、进给速度、进给深度等参数,以实现最佳的加工效果。
此外,在选择数控机床使用参数时,还需要考虑具体的加工工艺。
不同的加工工艺对机床使用参数有着不同的要求。
例如,在进行粗加工时,应选择较大的进给速度和切削速度,以提高加工效率;而在进行精加工时,则需要选择较小的进给速度和切削速度,以提高加工精度。
另外,还需要注意切削液的使用,以降低加工温度、延长刀具寿命,并减少切削过程中产生的摩擦和磨损。
在选择数控机床使用参数时,必须根据具体的加工工艺要求,合理调整各项参数,以实现高效、精确的加工。
最后,在选择数控机床使用参数时,还需要充分考虑机床本身的性能指标和技术参数。
第七章 机床主要参数的确定2
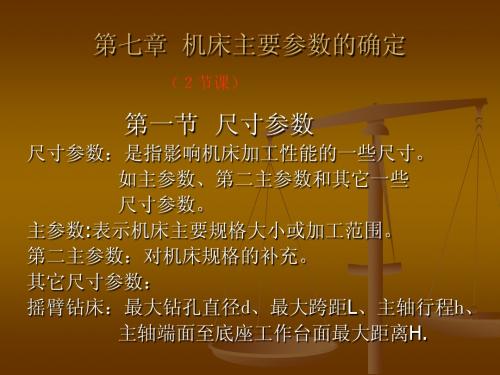
第二节 运动参数
一、运动参数:是指机床主轴、刀架、工作台等 的运动速度。 主运动参数: 回转主运动机床,如车床、铣床等,主运动参数是 主轴转速。 1000 v n ( r / min) d
直线主运动的机床,如插床和刨床。 主运动参数是每分钟往复次数(str/min).
nr
1000 v 2 L
(kw)
如水平运动,克服质量和摩擦力所需的功率:
P2
f mg v
'
60000
k w
根据计算出的空行程功率和电动机的转 速,再计算起动转矩,并据此来选择电动机, 并使选用的电动机的起动转矩大于计算的起动 转矩。 一般普通机床的空行程电动机功率和空行 程的速度列表7-4。
动力参数
一、主运动功率的确定;电动机的功率确定 1、计算法: P P P P
主 切 机 空转
切削功率的计算: (1)车、镗、磨等工序的切削功率:
P切
FZ v 60000
( kw)
(2)钻、扩等工序的切削功率:
P切
MK n 9550
( kw)
空转功率损失计算:
K1 P空 ( 3 5d a ni k 2 d 主 n主)(kw 6 10
PS
FQ V S 60000 S
(KW)
三、空行程功率的确定 参考同类型机床,辅之以计算,最好再经试 验验证。
P空行程 P1 P2
(KW)
P 1
Ta n 9550
'
kw
F v
如升降运动克服质量和摩擦力所需的功率:
P2
m g f
60000
)
机械摩损功率的计算:
第7章机床主参数
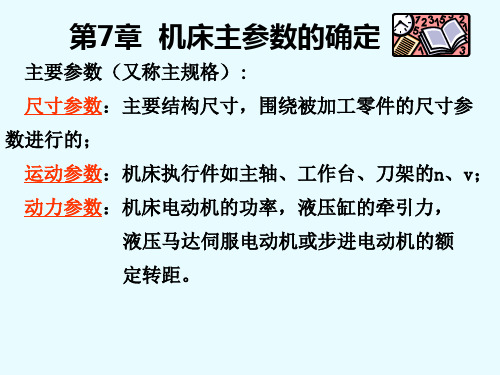
及其它参数。
7.2.4 公比的选用原则
1
● A=1- : 对于通用机床,为使转速损失不大,机床结构又不过于
复杂,一般取 =1.41 or 1.26
●对于大批量生产用的专门化机床,自动化机床,公比应取的小
一些,一般取 =1.12 or 1.26。因为这类机床的生产率高,转速损
失影响较大;另一方面,这类机床不常变速,变速机构可采用变换 齿轮机构,后者能实现小的公比,而结构又比较简单。
●对于大型机床,公比应 取的小一些,一般 = 1.26、
1.12、1.06。因为大型机床切削加工时间长,转速损失的 影响较大。如铣床类。
● 对于非自动化小型机床,公比应取的大一些,一般
取 为1.58、1.78或2,因为在这类机床上,辅助时间
较多,而切削时间所占比重不大,转速损失的影响不大。
7.3 动力参数
如果加工某一工件需要的最有利的切削速度为v,相应
的转速为n:
nj﹤n﹤nj+1
如果采用较高的转速nj+1,必将提高v,刀具耐用度将
降低,以采用较低转速为宜。
这时转速损失为: n- nj 相对转速损失为: A= (n- nj)/n
A= limn n j= n j1 n j = 1- n j
nn j 1
,了解并统计这些机床上常用的主轴转
速如下:
车轴类零件: n=400~900
盘形类:
n=150~300
机修:
n=80~150
车大导程螺距: n=10~40
个别:
nmax=1500 nmin=7
njmax=1273 分析国内外同类 D=400
确定: nmax=1500
nmin=10
第七章机床主要技术参数

10
E1
③为了便于采用双速或三速电动机,公比为2的某次方根
E2
2
机械工程学院 School of Mechanical Engineering
第七章 机床主要技术参数的确定
标准公比
①公比是2的某次方根,其数列每隔若干项增加或缩小2 倍,如 3 2 数列为10、12.5、16、20、25、32、40等, 每隔两级增大2倍。
机械工程学院 School of Mechanical Engineering
第七章 机床主要技术参数的确定 (2)运动参数 ①主运动参数 Ⅰ 主运动最高转速nmax和最低转速nmin Ⅱ 转速级数Z Ⅲ 公比φ Ⅳ 变速范围Rn= nmax/ nmin ②进给运动参数:情况同① (3)动力参数:指主运动、进给运动和其他辅助运动的 动力消耗。
ηS 可以用于主传动功率P主和进给传动功率Ps行粗略估算 车床:Ps=(0.03~0.04) P主(KW)
钻床:Ps=(0.04~0.05) P主(KW)
铣床:Ps=(0.04~0.05) P主(KW)
机械工程学院 School of Mechanical Engineering
第七章 机床主要技术参数的确定 7.3.3 快速运动功率的确定
按照等比数列排列的主轴转速,往往可以通过串联若干滑 移齿轮来实现。所以主轴转速n n=n电•iⅠ•iⅡ•••= n电•i总
因此,主轴转速按照等比数列排列时,充分利用了每一对滑移齿 轮的传动比,用同样数量的齿轮,可得到较多的变速级数。
机械工程学院 School of Mechanical Engineering
第七章 机床主要技术参数的确定 4.公比的选用
设主轴最高转速与最低转速之比值,称为转速范围Rn,则: Rn=nmax /nmin = nZ/n1 =n1φ z-1/n1 =φ z-1 即 z=1+lgRn/lgφ (Z为转速级数) 选用标准公比φ的一般原则: ①用于大批大量生产的自动化与半自动化机床,因为要求较高的 生产率,相对转速损失要小,因此φ要小些,一般取1.12或1.26。 ②大型机床加工大尺寸工件,机动时间长,选择合理的切削速度 对提高生产率作用较大,φ应小些,取1.12或1.26。 ③中型通用机床,万能性较大,因而要求转速级数z要多一些, 但结构又不能过于复杂, φ常取1.26或1.41。 ④小型机床切削加工时间常比辅助时间少,结构要求简单一些, 变速级速也不多,公比φ常取1.58或1.78。
机床主要参数的确定课件
机床主要参数的确定
第二节 运动参数
2、主轴转速的合理排列方式 为了满足各种不同工艺的要求,主轴必须有若
干不同的转速,如采用分级变速方式。 例:有一台车床,主轴转速(r/min)共12级,分别
为31.5、45、63、90、180、250、355、 500、710、1000、1400 。 呈等比数列,公比为φ=1.41
机床主要参数的确定
第三节 动力参数
➢ 进给运动采用单独的普通电动机的机床,需要确定 进给运动所需的功率。
方法:参考同类型机床和计算相结合。
➢ 进给功率PS(kW)
FQ——进给牵引力(N) VS——进给速度 (m/min) ηs——机械效率
机床主要参数的确定
机床主要参数的确定
第二节 运动参数
4、公比的选用 ➢ 对于一般生产率要求较高的普通机床,减少相对转
速损失是主要的,所以公比φ取得较小,如1.26或 1.41等。 ➢ 有些小型机床希望简化构造,公比φ可取得大些, 如1.58、2等。 ➢ 对于自动机床,减少相对转速损失率的要求更高, 常取φ=1.12或1.26。
式中:n——转速(r/min); v——切削速度(m/min); d——工件(或刀具)直径(mm)。
机床主要参数的确定
第二节 运动参数
② 主运动是直线运动的机床,主运动参数是每分钟 的往复次数(次/分)。 例:插床、刨床。
机床主要参数的确定
第二节 运动参数
1、最低nmin和最高nmax转速的确定 ①确定的方法是实际调查和比较同类型机床,并考
例
卧式车床是床身上工件的最大回转直径/10; 齿轮加工机床是最大工件直径/10; 外圆磨床是最大磨削直径/10; 无心磨床是最大磨削直径; 升降台铣床、矩台平面磨床是工作台面宽度/10; 龙门刨床、龙门铣床是工作台工作面宽度/100; 卧式铣镗床是主轴直径/10 ; 立式钻床、摇臂钻床是最大钻孔直径; 牛头刨床、插床是最大刨削和插削长度/10。 (以上单位均为mm,)也有的机床不用尺寸作为主参数,
数控铣削加工参数的确定原则
数控编程时,编程人员必须确定每道工序的切削用量,并以指令的形式写入程序中。
切削用量包括主轴转速、背吃刀量及进给速度等。
对于不同的加工方法,需要选用不同的切削用量。
切削用量的选择原则是:保证零件加工精度和表面粗糙度,充分发挥刀具切削性能,保证合理的刀具耐用度并充分发挥机床的性能,最大限度地提高生产率,降低成本。
(1)主轴转速的确定主轴转速应根据允许的切削速度和工件(或刀具)的直径来选择。
其计算公式为:n=1000v/(πD)计算的主轴转速n最后要根据机床说明书选取机床有的或较接近的转速。
(2)进给速度的确定进给速度F是数控机床切削用量中的重要参数,主要根据零件的加工精度和表面粗糙度要求以及刀具、工件的材料性质选取。
最大进给速度受机床刚度和进给系统的性能限制。
在轮廓加工中,在接近拐角处应适当降低进给量,以克服由于惯性或工艺系统变形在轮廓拐角处造成“超程”或“欠程”现象。
确定进给速度的原则:1)当工件的质量要求能够得到保证时,为提高生产效率,可选择较高的进给速度。
一般在100~200mm/min范围内选取。
2)在切断、加工深孔或用高速钢刀具加工时,宜选择较低的进给速度,一般在20~50mm/min范围内选取。
3)当加工精度,表面粗糙度要求高时,进给速度应选小些,一般在20~50mm/min范围内选取。
4)刀具空行程时,特别是远距离“回零”时,可以选择该机床数控系统给定的最高进给速度。
(3)背吃刀量确定背吃刀量(a p)根据机床、工件和刀具的刚度来决定,在刚度允许的条件下,应尽可能使背吃刀量等于工件的加工余量,这样可以减少走刀次数,提高生产效率。
为了保证加工表面质量,可留0.2~0.5mm精加工余量。
数控铣床及数控车床技术参数
气缸直径
ф30-50mm
3
机械手摆动角度
0-190 °
4
机械手摆动速度
0.2-0.7 s / 90°
5
使用气压
0.1-0.6Mpa
6
手指最大外径夹持力
≧118N
7
手指最大内径夹持力
≧130N
8
手指行程
≧4mm(单边)
9
快移速度
≧50米/分
10
★定位精度最低要求
±0.05mm
11
料仓
循环垛码料盘
12
1-2,机床主要技术参数要求
★床身最大回转直径
mm
≧ф270
托板上最大回转直径
mm
Ф150-250
★最大加工长度
mm
≧320
主轴转速范围
r/mm
50-3000
主轴换挡方式
变频
主电机功率
Kw
≧4
★卡盘形式
液压卡盘
卡盘直径
mm/
≧160(6寸)
主轴通孔直径
mm
Ф30-60
X轴快移速度
m/min
5-11
Z轴快移速度
五、其他要求:
5-1安装、调试要求:主机及附件的免费安装调试并负担所需耗材,直至达到验收指标,提供合格证明书、说明书及质保书等。
5-2培训要求:免费现场培训和售后培训,培训时间不少于2个工作日。
5-3售后服务:自验收之日起,整机提供三包服务一年,终身服务。
m/min
5-15
X轴行程
mm
≧200
Z轴行程
mm
≧200
刀架形式
四工位电动刀塔
刀架转位重复定位精度
机床的主要技术参数有哪些你造吗?
机床的主要技术参数有哪些你造吗?机床的主要技术参数(主参数和基本参数)•主参数:代表机床规格的大小,在机床型号中,用阿拉伯数字给出的是主参数折算值(1/10或/100)。
•基本参数:包括尺寸参数、运动参数和动力参数。
(一)尺寸参数:机床的主要结构尺寸。
(二)运动参数:机床执行中的运动速度,包括主运动的速度范围、速度数列和进给运动的进给量范围、进给量数列以及空行程速度等。
1、主运动参数1)主轴转数:对作回转运动的机床,其主运动参数是主轴转数。
计算公式为:n=1000V/(πd)主运动是直线运动的机床,如:插床,刨床。
其主运动参数是机床工作台或滑枕的每分钟往复次数。
2)主轴最低和最高转数的确定专用机床用于完成特定的工艺,主轴只需一种固定的转速。
通用机床的加工范围较宽,主轴需要变速,需要确定其变速范围,即最低和最高转数。
采用分级变速时,还应确定转速的级数。
n min=1000V min/(πD max) n max=1000V max/(πD min)变速范围为:R n=n max/n min3)有级变速时主轴转速序列无级变速时,n max与n min之间的转速是连续变化的有级变速时,应该在n max和n min确定后,再进行转速分级,确定各中间级转速。
主运动的有级变速的转速数列一般采用等比数列,满足等比数列关系:n j+1=n j? ;n z=n1*?z-14)标准公比?为了便于机床设计和使用,规定了标准公比值:1.06,1.12,1.26,1.41,1.58,1.78,2.00其中,?=1.06是公比?数列的基本公比,其他可以由基本公比派生而来。
2、进给运动参数进给量:a.大部分机床(如车,钻床等):进给量用工件或刀具每转的位移(mm/r)表示;b.直线往复运动机床(如刨,插床):进给量以每以往复的位移量表示;c.铣床和磨床:进给量以每分钟的位移量(mm/min)表示。
(三)动力参数机床的动力参数是指驱动主运动、进给运动和空行程运动的电动机功率。
- 1、下载文档前请自行甄别文档内容的完整性,平台不提供额外的编辑、内容补充、找答案等附加服务。
- 2、"仅部分预览"的文档,不可在线预览部分如存在完整性等问题,可反馈申请退款(可完整预览的文档不适用该条件!)。
- 3、如文档侵犯您的权益,请联系客服反馈,我们会尽快为您处理(人工客服工作时间:9:00-18:30)。
n 1000v d
式中: n ―转速( r/min ); v― 切削速度( m/min ); d― 工件(或刀具)直径(mm)。
2021/2/7
5
主运动是直线运动的机床,如插床或刨床,主 运动参数是每分钟的往复次数。对于不同的机床, 主运动参数有不同的要求。专用机床和组合机床是 为某一特定工序而设计制造的,每根主轴一般只须 有一个转速,根据最有利的切削速度和直径而定, 故没有变速要求。通用机床是为适应多种零件加工 而设计制造的,主轴需要变速。因此需确定它的变 速范围,即最低与最高转速。如果采用分级变速, 则还应确定转速级数。
给机构简单,采用了棘轮机构,进给量由每次往复转过的齿数
而定,则是等差数列。供大量生产用的自动和半自动车床,常
用交换齿轮来调整进给量。这时可以不按一定的规则,而用交
换齿轮选择最有利的进给量。卧式车床因为要车螺纹,进给箱
的分级应根据螺纹标准而定。螺纹标准不是一个等比数列,而
2是021一/2/7个分段的等差数列。
卧式车床是床身上工件的最大回转直径;
齿轮加工机床是最大工件直径;
外圆磨床和无心磨床是最大磨削直径;
龙门刨、铣床,升降台铣床和矩形工作台平面磨床
是工作台工作面宽度;
卧式铣镗床是主轴直径;
立式钻床和摇臂钻床是最大钻孔直径;
牛头刨床和插床是最大刨削和插削长度
也有的机床不用尺寸作为主参数,如拉床的主参
数是额定拉力等。
2021/2/7
3
有的机床,一个主参数还不足以确定机床的规格,
还需第二主参数加以补充:
车床的第二主参数是最大工件长度;
铣床和龙门刨床是工作台工作面长度;
摇臂钻床是最大跨距等。
此外,还要确定其他一些尺寸参数:
车床常常还要确定在刀架上工件的最大回转直径和
主轴孔允许通过的最大棒料直径等;
龙门铣床还应确定横梁的最高和最低位置等;
14
三、标准公比和标准数列 机床转速是从小到大递增的,因此φ> 1 。
为使最大相对转速损失率不超过 50 % ,即
,则,φ≤2 。因此1 <Ф≤2 为方便起见,规定了公比的标准值:
1.06 ,1.12 ,1.26 ,1.41 ,1.58 , 2。
当采用标准公比后,转速数列可从表 7-1 中直
接查出。表中给出了以 1.06 为公比的从 1-10000
2021/2/7
6
1.最低(nmin)和最高(nmax)转速的确定: nmin和nmax的比值是变速范围:
2021/2/7
7
在确定切削速度时应考虑到多种工艺的需要。 切削速度主要与刀具和工件的材料有关。常用的刀 具材料有高速钢、硬质合金和陶瓷等。工件材料可 以是钢、铸铁以及铜铝等有色金属。切削速度可通 过切削试验、查切削用量手册和通过调查得到。
2021/2/7
9
最大的相对转速损失率是当所需的转速 n 趋近于 nj + l时,也就是:
在其他条件(直径、进给、切深)不变的情况下, 转速的损失就反映了生产率的损失。对于普通机床, 如果认为每个转速的使用机会都相等,那么应使 Amax 为一定值,即:
从这里可看出,任意两级转速之间的关系应为:
n j十1 =njφ
在确定了 nmax和 nmin后,如采用分级变速(大 多数普通机床),则应进行转速分级;如采用变速 电动机进行无级变速(大多数数控和重型机床),
有时也需用分级变速机构来扩大其调速范围。
2021/2/7
8
2.分级变速时的主轴转速数列:
如某机床的分级变速机构共有 Z 级,其中 n1 = nmin, nz=nmax , Z 级转速分别为: nl , n2 , n3,…, nj , nj
2021/2/7
10
机床的转速应该按等比数列(几何级数) 分级。其公比为φ,各级转速应为
最大相对转速损失率为:
变速范围为:
2021/2/7
11
例:有一台车床,主轴转速ห้องสมุดไป่ตู้r/min)共12级,分别为: 31.5、45、63、90、125、180、250、355、500、710、 1000、1400,公比为φ=1.41,则最大相对转速损失率:
+ l ,…, nz 如果加工某一工件所需要的最有利的切削速度
为 v ,则相应的转速为n。通常,分级变速机构不能
恰好得到这个转速,而是 n 处于某两级转速 nj , nj + l 之间: nj < n < nj+l如果采用较高的转速nj+l,必将提 高切削速度,刀具的耐用度将要降低。为了不降低
刀具耐用度,以采用较低的转速 nj 为宜。这时转速 的损失为 n-nj ,相对转速损失率为:
摇臂钻床还要确定主轴下端面到底座间的最大和最
小距离,其中包括了摇臂的升降距离和主轴的最大伸
出量等。
当主参数、第二主参数和其他一些尺寸参数确定
后,就基本上确定了该机床所能加工或安装的最大工
件的尺寸。机床的尺寸参数是根据零件尺寸确定的。
2021/2/7
4
第二节 运动参数
一、主运动参数 回转主运动的机床,主运动参数是主轴转速。
常20以21/2每/7 分钟的位移量表示,即单位为r/ min 。
13
在其他条件(切速、切深等)不变的情况下,进给量的损失
也反映了生产率的损失。数控机床和重型机床的进给为无级调
整;普通机床多采用分级调整。如进给链为外联系传动链,为使
相对损失为一定值,则进给量的数列也应取等比数列。有的往
复主运动机床,例如刨床和插床,进给运动是间歇的,为使进
第七章 机床主要参数的确定
第一节 尺寸参数 第二节 运动参数 第三节 动力参数
2021/2/7
1
第一节 尺寸参数
机床尺寸参数的确定,主要是确定影响机床加工 性能的一些尺寸。其中包括机床的主参数、第二主 参数和其他一些尺寸参数。
2021/2/7
2
机床的主参数是代表机床规格大小的一种参数,各
类机床以什么尺寸作为主参数已有统一的规定。
变速范围:
等比数列同样适用子直线往复主运动(刨床、插
床)的往复次数数列、进给数列以及尺寸和功率参数
系列。
2021/2/7
12
二、进给运动参数
大部分机床的进给量用工件或刀具每转的位移表
示,即单位为mm/r,如车床、钻床、镗床及滚齿机等。
直线往复运动的机床,如刨、插床,以每一往复的位
移表示。铣床和磨床;由于使用的是多刃刀具,进给量
的数值。 1.12 = 1.062, 1.26 = 1.064,