汽车板簧 (2)
汽车板簧 标准
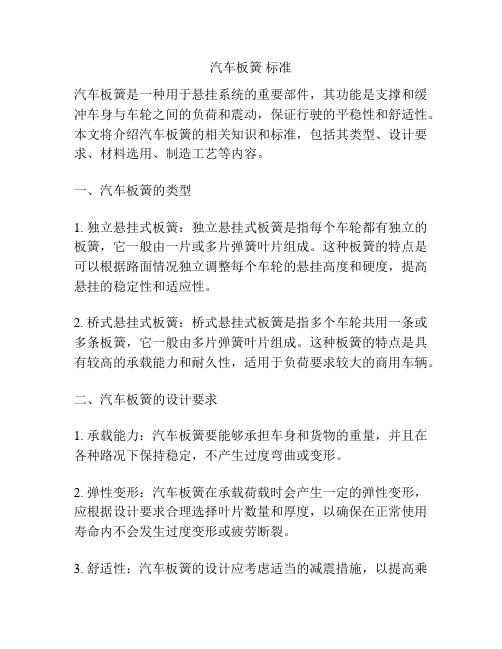
汽车板簧标准汽车板簧是一种用于悬挂系统的重要部件,其功能是支撑和缓冲车身与车轮之间的负荷和震动,保证行驶的平稳性和舒适性。
本文将介绍汽车板簧的相关知识和标准,包括其类型、设计要求、材料选用、制造工艺等内容。
一、汽车板簧的类型1. 独立悬挂式板簧:独立悬挂式板簧是指每个车轮都有独立的板簧,它一般由一片或多片弹簧叶片组成。
这种板簧的特点是可以根据路面情况独立调整每个车轮的悬挂高度和硬度,提高悬挂的稳定性和适应性。
2. 桥式悬挂式板簧:桥式悬挂式板簧是指多个车轮共用一条或多条板簧,它一般由多片弹簧叶片组成。
这种板簧的特点是具有较高的承载能力和耐久性,适用于负荷要求较大的商用车辆。
二、汽车板簧的设计要求1. 承载能力:汽车板簧要能够承担车身和货物的重量,并且在各种路况下保持稳定,不产生过度弯曲或变形。
2. 弹性变形:汽车板簧在承载荷载时会产生一定的弹性变形,应根据设计要求合理选择叶片数量和厚度,以确保在正常使用寿命内不会发生过度变形或疲劳断裂。
3. 舒适性:汽车板簧的设计应考虑适当的减震措施,以提高乘坐的舒适性,减少对乘员的影响。
4. 防腐性:汽车板簧常常在恶劣的环境条件下使用,应进行防腐处理,以延长使用寿命。
三、汽车板簧的材料选用汽车板簧通常由炭素钢或合金钢制成,具有优良的强度和弹性,能够满足不同车辆的要求。
常见的材料包括50CrVA、60Si2Mn、55SiCrV、60CrMNBA等。
四、汽车板簧的制造工艺1. 材料选材:根据设计要求和使用环境选择适当的板簧材料。
2. 板材切割:将选定的板材按照设计要求切割成合适尺寸的形状。
3. 弯曲成型:通过加工设备将切割好的板簧进行弯曲成型,一般采用热成形工艺。
4. 热处理:对成型后的板簧进行热处理,提高其强度和弹性。
5. 表面处理:对板簧进行喷涂或镀锌等表面处理,提高其防腐性能。
典型的汽车板簧标准包括GB/T 1345-2005《汽车板簧》和GBT 5796-2015《汽车板簧》等。
汽车板簧材质的介绍(二)
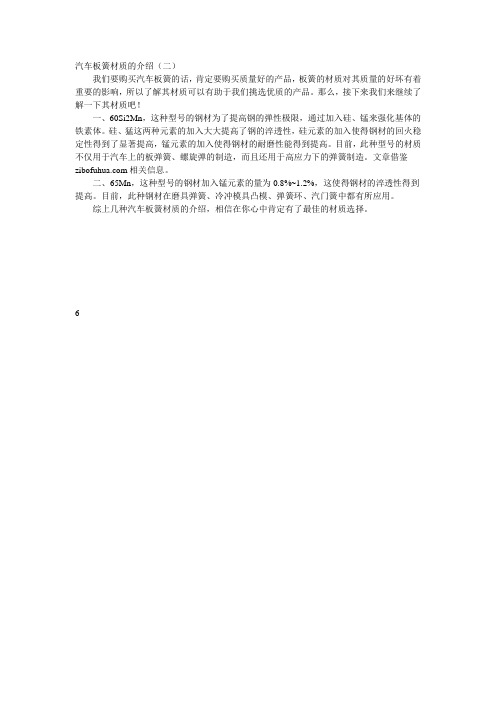
汽车板簧材质的介绍(二)
我们要购买汽车板簧的话,肯定要购买质量好的产品,板簧的材质对其质量的好坏有着重要的影响,所以了解其材质可以有助于我们挑选优质的产品。
那么,接下来我们来继续了解一下其材质吧!
一、60Si2Mn,这种型号的钢材为了提高钢的弹性极限,通过加入硅、锰来强化基体的铁素体。
硅、猛这两种元素的加入大大提高了钢的淬透性,硅元素的加入使得钢材的回火稳定性得到了显著提高,锰元素的加入使得钢材的耐磨性能得到提高。
目前,此种型号的材质不仅用于汽车上的板弹簧、螺旋弹的制造,而且还用于高应力下的弹簧制造。
文章借鉴相关信息。
二、65Mn,这种型号的钢材加入锰元素的量为0.8%~1.2%,这使得钢材的淬透性得到提高。
目前,此种钢材在磨具弹簧、冷冲模具凸模、弹簧环、汽门簧中都有所应用。
综上几种汽车板簧材质的介绍,相信在你心中肯定有了最佳的材质选择。
6。
60Si2Mn汽车板簧热处理工艺设计

1序论1.1 热处理工艺课程设计的意义热处理工艺课程设计是高等工业学校金属材料工程专业一次专业课设计练习,是热处理原理与工艺课程的最后一个教学环节。
其目的是:1. 培养学生综合运用所学的热处理课程的知识去解决工程问题的能力,并使其所学知识得到巩固和发展。
2. 学习热处理工艺设计的一般方法、热处理设备选用和装夹具设计等。
3. 进行热处理设计的基本技能训练,如计算、工艺图绘制和学习使用设计资料、手册、标准和规范。
1.2 热处理课程设计的任务进行零件的加工路线中有关热处理工序和热处理辅助工序的设计。
根据零件的技术要求,选定能实现技术要求的热处理方法,制定工艺参数,画出热处理工艺曲线图,选择热处理设备,设计或选定装夹具,作出热处理工艺卡。
写出设计说明书。
①汽车热处理工艺设计。
②制定热处理工序的工艺参数③分析各热处理工序中材料的组织和性能。
④选择热处理设备。
⑤选择与设计热处理工艺所需的挂具、装具或夹具。
⑥填写热处理工艺卡片。
2 汽车板簧的工作要求、技术要求及选材2.1工作要求和技术要求汽车钢板弹簧式一种弹性元件,其作用式承受车厢以及载物(静载物)的作用,可传递垂直载荷,缓和及抑制不平路面所引起的冲击,限制车身和车轮的振动。
作为弹性元件它既有缓冲、减振、贮能的功能,又负担传递力和导向的作用,在工作过程中,钢板弹簧承受高因道路不平所引起的冲击载荷,并由此或单向循环弯曲应力和振动的作用,同时也要受到泥水和泥沙等侵蚀。
由此其结构简单、使用可靠、维修方便、因而被一般载重汽车广泛使用。
汽车钢板弹簧采用合金钢制造,硬度在380~460HBW,板簧达到最大的强度特性,即高的弹性极限,经过抛丸后处于表面压应力状态,然后进入初步机加工阶段。
有资料介绍重型汽车的“概率-应力曲线”表明,钢板弹簧的所受应力在882~980Pa。
汽车钢板弹簧的主要失效形式有腐蚀疲劳断裂、应力腐蚀断裂、脆性断裂、磨损和应力松弛以及永久性塑性变形等,其危害有停车待修、钢板弹簧损耗量大、降低行车舒适性等,因此应认真对待,减少出现失效的概率,在弹簧制造和热处理等各个环节确保产品质量合格。
板簧设计教材(200802)

板簧设计教材(200802)汽车钢板弹簧设计第一节悬架的定义、功能及其组成悬架是现代汽车上的主要总成之一,它能够把车架(车身)与车轴(车轮)弹性的连接起来,其主要任务是传递作用在与车架和车轮之间的一切力和力矩,并且缓和由于路面不平而传给车身的冲击载荷,衰减由于冲击载荷引起的承载系统的振动,保证汽车的正常行驶。
悬架通常由弹性元件、导向机构及减振装置组成。
弹性元件主要有:钢板弹簧,螺旋弹簧,橡胶弹簧,空气弹簧及油气弹簧等。
在长期的发展过程中,由于钢板弹簧具有结构简单,制造成本较低,占用空间小,维修方便等一系列特点,因此目前在世界各国仍都在大量的采用钢板弹簧。
第二节.钢板弹簧的种类一、按力学性能特点分:分为等刚度、两极刚度复式钢板弹簧、渐变刚度钢板弹簧。
二、按截面形状分:分为等截面板簧和变截面板簧第三节.钢板弹簧的截面形状目前国内钢板弹簧的截面形状有:a矩形截面b单面双槽截面c带凸肋的截面弹簧在设计成不对称形状,目的是把断面的中性轴移近受拉表面,减少弹簧的拉应力。
此种材料也存在缺点(1)槽内容易储存泥沙加剧表面腐蚀。
(2)轧制后在沟槽的对应拉面上,表面质量较差,双槽的比单槽的更严重。
这种表面缺陷成为疲劳起源点。
注:在钢板弹簧的设计过程中应优先选择GB1222-84《弹簧钢》所规定的规格。
第四节.钢板弹簧的主要元件结构一、第一片卷耳形式钢板弹簧的卷耳形式一般有3种结构,上卷耳、下卷耳和平卷耳(柏林耳)。
上卷耳使用的比较多,采用下卷耳主要是为了协调钢板弹簧与转向系的运动,下卷耳在载荷作用下容易张开。
平卷耳可以减少卷耳的应力,因为纵向力作用方向和弹簧主片断面的中心线重合,对于不能增加主片厚度但又要保证主片卷耳强度的弹簧多采用平卷耳。
但是平卷耳制造上比上述两种卷耳复杂,一般轿车多采用平卷耳或下卷耳。
二、第二片包耳汽车在使用条件恶劣的情况下,需要采用加强卷耳的措施。
常见的是将第二片作成包耳形式以保护主片。
轻型车与箱式客车多采用1/4包耳,而大型载货汽车和大型客车多采用3/4包耳或装配式包耳。
60Si_(2)CrV高应力板簧表面脱碳行为研究

现代冶金Modern Metallurgy第49卷第1期2021年2月Vol. 49 No. 1Feb. 202160Si 2CrV高应力板簧表面脱碳行为研究陈一凡#,陈露瑶27陈诗怡27李俊岳23!.张家港海锅新能源装备股份有限公司,江苏张家港215628; 2.南京工程学院材料工程学院,江苏南京211167;3.江苏省先进结构材料与应用技术重点实验室,江苏南京211167)摘要:采用金相法分析了加热温度和保温时间对60S ;2CrV 高应力汽车板簧表面脱碳行为的影响°结果表明:试验材料的脱碳层深度和保温时间的关系符合菲克第二定律°为尽量减轻脱碳对高应力板簧疲劳寿命的影响,建议在生产时在奥氏体单相区较低温度加热并缩短保温时间°关键词:高应力板簧;60S ;2CrV ;脱碳行为;加热制度中图分类号:TG142. 1引言板簧作为卡车和货车悬架系统中重要的传力及弹性元件一般安装在汽车悬架中,通常对汽车的运 行稳定性和平顺性有较大的影响% 60Si z CrV 钢近 年来逐渐用以生产高应力汽车板簧,高应力板簧可以减少板簧叠片的数量、降低汽车自重,对节能减 排、提高商用车装载效率具有重要意义%随着工作应力的提高,高应力板簧逐渐暴露出疲劳寿命低、散差大的问题,成为限制其推广的重要原因'1( %大尺寸夹杂物、表面缺陷和表面脱碳是造成板簧疲劳寿命低的主要因素%在板簧原材生产、变截面轧制和淬火回火过程中都很有可能造成板簧出现明显的脱碳%较深的脱碳层,尤其是完全脱碳层的出现会显著降低板簧表面强度,造成服役时表面过表1早出现疲劳裂纹,最终导致疲劳寿命显著下降%因此,分析60Si z CrV 的表面脱碳行为、研究其脱碳规律对优化高应力板簧热加工和热处理工艺具有重要意义%1实验材料与方案本文实验材料为60Si z CrV 高应力板簧,其典型化学成分如表1所示%试样经过切割后,将表面用 150! ,240! ,400! ,800!砂纸分别进行打磨后进行热处理%为模拟实际生产时钢板暴露于空气中的环 境,使用SY-1000-06箱式电阻炉进行热处理;炉中 气氛为空气%热处理结束后将试样从中间剖开,镶嵌,磨平拋光后使用4%硝酸酒精溶液浸蚀,使用奥 林巴斯GX-51型光学显微镜观察预磨平面的纵剖边一侧的金相形貌%典型60Si%CrV 高应力板簧的化学成分/%w (C)w (Si)w (Mn)w (P )w (S )w (Cr)!(V)!(Ni)!(Fe )0. 63 1. 580. 580. 010. 01 1. 010. 160. 05Bal.通过J-mat pro 软件计算可知60Si z CrV 的A a和A cs 温度分别为780 K 和820 K %因此选取未相变区、两相区和奥氏体单相区加热30 min 后缓冷, 研究加热温度对表面脱碳行为的影响;试验加热温 度分别为 750,800,900,1000,1100,1200 K % 选取900 K 分别保温15,30,60,120 min 后缓冷,研究保温时间对表面脱碳行为的影响%2实验结果与讨论2. 1加热温度的影响2.1.1 未相变区和两相区加热图1为未相变区750 K 加热样品和两相区800收稿日期=2020-12-16第1期陈一凡,等:60Si2CrV高应力板簧表面脱碳行为研究13加热样品的表面形貌%750°C加热样品由于尚未发生相变,仅发生轻微的不完全脱碳,脱碳层深度约20"m,原本的片状珠光体发生了比较明显的球化%两相区800C加热时,样品表面出现了明显的完全脱碳层,脱碳层深度约为35"m%完全脱碳层为全铁素体组织,无论是否经过淬火、回火工艺,都不会转变成马氏体类型组织,因此表面强度较基体显著下降%通常情况下,钢铁材料的疲劳极限约为抗拉强度的0.40.5倍「2(。
汽车钢板弹簧设计计算

1.1单个钢板弹簧的载荷已知汽车满载静止时汽车前轴荷G1=3000kg,非簧载质量Gu1=285kg,则据此可计算出单个钢板弹簧的载荷:Fw1=(G1-Gu1)/2=1357.5 kg (1)进而得到:Pw1=Fw1×9.8=13303.5 N (2)1.2钢板弹簧的静挠度钢板弹簧的静挠度即静载荷下钢板弹簧的变形。
前后弹簧的静挠度都直接影响到汽车的行驶性能[1]。
为了防止汽车在行驶过程中产生剧烈的颠簸(纵向角振动),应力求使前后弹簧的静挠度比值接近于1。
此外,适当地增大静挠度也可减低汽车的振动频率,以提高汽车的舒适性。
但静挠度不能无限地增加(一般不超过240 mm),因为挠度过大,即频率过低,也同样会使人感到不舒适,产生晕车的感觉。
此外,在前轮为非独立悬挂的情况下,挠度过大还会使汽车的操纵性变坏。
一般汽车弹簧的静挠度值通常如表1[2]所列范围内。
本方案中选取fc1=80 mm。
1.3钢板弹簧的满载弧高满载弧高指钢板弹簧装到车轴上,汽车满载时钢板弹簧主片上表面与两端(不包括卷耳孔半径)连线间的最大高度差[3]。
当H0=0时,钢板弹簧在对称位置上工作。
考虑到使用期间钢板弹簧塑性变形的影响和为了在车架高度已限定时能得到足够的动挠度值,常取H0∈10-20mm。
本方案中H01初步定为18mm。
1.4钢板弹簧的断面形状板弹簧断面通常采用矩形断面,宜于加工,成本低。
但矩形断面也存在一些不足。
矩形断面钢板弹簧的中性轴,在钢板断面的对称位置上。
工作时,一面受拉应力,一面受压应力作用,而且上、下表面的名义拉应力和压应力的绝对值相等。
因材料的抗拉性能低于抗压性能,所以在受拉应力作用的一面首先产生疲劳断裂。
除矩形断面以外的其它断面形状的叶片,其中性轴均上移,使受拉应力的一面的拉应力绝对值减小,而受压应力作用的一面的压应力绝对值增大,从而改善了应力在断面上的分布情况,提高了钢板弹簧的疲劳强度并节约了近10%的材料。
汽车钢板弹簧的应用及其发展趋势
1 车用钢板弹簧概述车用钢板弹簧又称为叶片弹簧,它是汽车悬架中应用广泛的一种弹性元件。
它由若干片长度不等、曲率半径不同、厚度相等或不等的弹簧钢片叠合在一起,组成一根近似等强度的弹性梁。
钢板弹簧的断面形状除采用对称断面外,还有采用上下对称的特殊断面。
这样可改善弹簧的受力状况,不仅提高了其疲劳强度,还节约了金属材料。
钢板弹簧在载荷作用下变形,各片之间因相对滑动而产生摩擦,可使车架的振动衰减。
各片之间处于干摩擦,同时还要将车轮所受冲击力传递给车架,因此增大了各片的磨损。
所以在装合时,各片之间要涂上较稠的石墨润滑脂进行润滑,并应定期维护。
钢板弹簧本身还起导向装置的作用,可不必单设导向装置,使结构简化。
有些高级轿车的后悬架也采用钢板弹簧作弹性元件。
目前一些汽车上采用变厚度的单片或2~3片的钢板弹簧,可以减小片与片之间的干摩擦,同时减轻了重量。
2 钢板弹簧的功能结构在采用传统弹簧的吸震式悬架设计上,弹簧起支持车身以及吸收不平路面和其他施力对轮胎所造成的冲击的作用,而这里所谓的其他施力包含加速、减速、制动、转弯等对弹簧造成的施力。
更重要的是在消除振动的过程中要保持轮胎与路面的持续接触,维持车辆的循迹性。
如果弹簧很软,则很容易出现“坐底”的情况,即将悬架的行程用尽。
假如在转弯时发生坐底情况,则可视为弹簧的弹力系数变成无限大(已无压缩的空间),车身会立即产生质量转移,使循迹性丧失。
如果这辆车有着很长的避振行程,那么或许可以避免“坐底”,但相对的车身也会变得很高,而很高的车身意味着很高的车身重心,车身重心的高低对操控表现有决定性的影响,所以,太软的弹簧会导致操控上的障碍。
如果路面的崎岖度较大,那就需要比较软的弹簧才能确保轮胎与路面接触,同时弹簧的行程也必须增加。
弹簧的硬度选择要由路面的崎岖程度来决定,越崎岖要越软的弹簧,但要多软则是个关键的问题,通常这需要经验的累积。
一般来说,软的弹簧可以提供较佳的舒适性以及行经较崎岖的路面时可保持比较好的循迹性;但是,在行经一般路面时,却会造成悬架系统较大的上下摆动,影响操控。
汽车钢板弹簧设计计算
1.1单个钢板弹簧的载荷已知汽车满载静止时汽车前轴荷G1=3000kg,非簧载质量Gu1=285kg,则据此可计算出单个钢板弹簧的载荷:Fw1=(G1-Gu1)/2=1357.5 kg (1)进而得到:Pw1=Fw1×9.8=13303.5 N (2)1.2钢板弹簧的静挠度钢板弹簧的静挠度即静载荷下钢板弹簧的变形。
前后弹簧的静挠度都直接影响到汽车的行驶性能[1]。
为了防止汽车在行驶过程中产生剧烈的颠簸(纵向角振动),应力求使前后弹簧的静挠度比值接近于1。
此外,适当地增大静挠度也可减低汽车的振动频率,以提高汽车的舒适性。
但静挠度不能无限地增加(一般不超过240 mm),因为挠度过大,即频率过低,也同样会使人感到不舒适,产生晕车的感觉。
此外,在前轮为非独立悬挂的情况下,挠度过大还会使汽车的操纵性变坏。
一般汽车弹簧的静挠度值通常如表1[2]所列范围内。
本方案中选取fc1=80 mm。
1.3钢板弹簧的满载弧高满载弧高指钢板弹簧装到车轴上,汽车满载时钢板弹簧主片上表面与两端(不包括卷耳孔半径)连线间的最大高度差[3]。
当H0=0时,钢板弹簧在对称位置上工作。
考虑到使用期间钢板弹簧塑性变形的影响和为了在车架高度已限定时能得到足够的动挠度值,常取H0∈10-20mm。
本方案中H01初步定为18mm。
1.4钢板弹簧的断面形状板弹簧断面通常采用矩形断面,宜于加工,成本低。
但矩形断面也存在一些不足。
矩形断面钢板弹簧的中性轴,在钢板断面的对称位置上。
工作时,一面受拉应力,一面受压应力作用,而且上、下表面的名义拉应力和压应力的绝对值相等。
因材料的抗拉性能低于抗压性能,所以在受拉应力作用的一面首先产生疲劳断裂。
除矩形断面以外的其它断面形状的叶片,其中性轴均上移,使受拉应力的一面的拉应力绝对值减小,而受压应力作用的一面的压应力绝对值增大,从而改善了应力在断面上的分布情况,提高了钢板弹簧的疲劳强度并节约了近10%的材料。
毕业设计(论文)-汽车悬架钢板弹簧的设计
目录第1章绪论 (2)第2章悬架系统的结构与分析 (4)2.1悬架的功能和组成 (4)2.2汽车悬架的分类 (4)2.3悬架的设计要求 (4)2.4悬架主要参数 (5)2.4.1悬架的静挠度cf及刚度c (5)2.4.2悬架的动挠度df (6)2.4.3悬架侧倾角刚度及其在前、后轴的分配 (6)2.4.4钢板弹簧结构............................................................................. . (7)第3章前后悬架系统的设计 (8)3.1前悬架系统设计 (8)3.1.1钢板弹簧的设计 (8)3.1.2.钢板弹簧的验算 (10)3.2后悬架系统设计 (13)3.2.1钢板弹簧的设计 (13)3.2.2钢板弹簧的验算 (15)第4章减振器设计 (19)4.1减振器分类 (19)4.2前后悬架减振器计算 (19)4.2.1相对阻尼系数和阻尼系数 (19)4.2.2最大卸荷力 (20)4.2.3工作缸直径 (21)第5章结论 (23)5.1钢板弹簧参数 (23)5.1.1前悬架参数 (23)5.1.2后悬架参数 (23)5.2双筒式减振器参数 (24)5.2.1前减震器参数 (24)5.2.2后减震器参数 (24)参考文献 (25)第1章绪论悬架是汽车的车架与车桥之间的一切传力连接装置的总称。
它的作用是弹性地连接车桥和车架,缓和行驶中车辆受到的冲击力。
保证货物完好和人员舒适,使汽车在行驶中保持稳定的姿势,改善操纵稳定性;同时悬架系统承担着传递垂直反力,纵向反力和侧向反力以及这些力所造成的力矩,以保证汽车行驶平顺;并且当车轮相对车架跳动时,特别在转向时,车轮运动轨迹要符合一定的要求,因此悬架还起使车轮按一定轨迹相对车身跳动的导向作用。
悬架是汽车中的一个重要组成部分,它把车架与车轮弹性地连接起来,关系到汽车的多种使用性能。
悬架是一个较难达到完美要求的汽车总成,这是因为悬架既要满足汽车的舒适性要求,又要满足其操纵稳定性的要求,而这两方面又是互相对立的。
汽车板簧 标准
汽车板簧标准
汽车板簧是一种用于承载和缓冲汽车重量和震动的弹簧元件。
标准的汽车板簧通常符合以下规范和要求:
1. 材料:汽车板簧通常由高强度合金钢制成,以确保足够的强度和耐久性。
2. 尺寸和几何形状:汽车板簧的尺寸和几何形状必须符合国家或行业标准,以确保与汽车底盘和悬挂系统的匹配。
3. 荷载能力:汽车板簧的荷载能力必须满足车辆的设计要求,以确保在各种工况下都能提供足够的支撑力。
荷载能力通常通过弹簧常数来表示。
4. 弹性性能:汽车板簧必须具有合适的弹性性能,以在负载下产生适当的挠度并能够缓冲和吸收道路震动。
5. 表面处理:为了防止腐蚀和提高耐久性,汽车板簧通常进行表面处理,如镀锌或喷涂防腐涂层。
6. 质量控制:生产和检测汽车板簧需要符合严格的质量控制标准,以确保产品的一致性和可靠性。
这些是标准汽车板簧的一般要求,不同的汽车类型和应用可能会有特定的要求和标准。
为了确保安全和可靠性,建议购买适合特定车型和应用的认证和合规的汽车板簧。
- 1、下载文档前请自行甄别文档内容的完整性,平台不提供额外的编辑、内容补充、找答案等附加服务。
- 2、"仅部分预览"的文档,不可在线预览部分如存在完整性等问题,可反馈申请退款(可完整预览的文档不适用该条件!)。
- 3、如文档侵犯您的权益,请联系客服反馈,我们会尽快为您处理(人工客服工作时间:9:00-18:30)。
汽车板簧失效分析
1.汽车板簧的材质选择
板簧是汽车悬架系统中的重要部件,工作环境恶劣,是汽车的易损部件,所以对其力学性能具有严格的要求。
汽车在行驶过程中,汽车板簧除了要承受车厢及载物的重量,即静载荷外,还要承受因路面不平等原因引起的冲击载荷,并因此造成单向循环弯曲应力。
板簧的主要失效方式是疲劳断裂和永久性塑性变形。
因此,板簧的材料应具有高的强度和硬度,高的弹性极限,弹性减退抗力要好,有较高的屈强比,为防止在交变应力下发生疲劳和断裂,板簧还要具有较高的疲劳的强度和耐蚀性能。
低碳钢为碳含量低于0.25%的碳素钢,因其强度低、硬度低而软,又称软钢。
它包括大部分普通碳素结构钢和一部分优质碳素结构钢,大多不经热处理用于工程结构件,有的经渗碳和其他热处理用于要求耐磨的机械零件。
低碳钢退火组织为铁素体和少量珠光体,其强度和硬度较低,塑性和韧性较好。
综上所述,低碳钢不符合板簧材料高强度和高硬度的要求。
铝合金种类较多,通过加入合金元素以及对热处理工艺的控制,可以得到具有优良性能的铝合金。
铝合金有很多种类,1000系列铝合金含铝量高,往往适用于对强度和硬度要求不高的场合;2000系列铝合金的特点为硬度高,但此系列属于航空铝材,在常规工业中并不常用;3000系列铝合金的主要特点为防锈功能较好;4000系铝合金属于建筑材料,机械零件锻造用材,焊接材料;5000系列铝合金又称镁铝合金,性能优良,缺点是不能做热处理强化;6000系列铝合金适用于对抗腐蚀性,抗氧化性要求较高的场合;7000系铝合金为航空铝材。
综上所述,铝合金不适用于制造汽车板簧。
65Mn弹簧钢,含有0.90%—1.2%的Mn元素,提高了材料的淬透性,φ12mm的钢材油中可以淬透,表面脱碳倾向比硅钢小,经热处理后的综合力学性能优于碳钢,但有过热敏感性和回火脆性。
常用作小尺寸各种扁、圆弹簧、座垫弹簧、弹簧发条,也可制作弹簧环、气门簧、离合器簧片、刹车弹簧及冷拔钢丝冷卷螺旋弹簧。
虽然锰钢淬透性好,但易产生淬火裂纹,并有回火脆性。
因此,汽车板簧常用的材料为60Si2Mn弹簧钢,具有高强度、弹性和淬透性,适于铁道车辆、汽车拖拉机工业上制作承受较大负荷的扁形弹簧或线径在30mm以下的螺旋弹簧、板簧,也适于制作工作温度在250 ℃以下非腐蚀介质中的耐热弹簧以及承受交变负荷及在高应力下工作的大型重要卷制弹簧。
2.汽车板簧服役环境的要素有哪些?
(1)汽车板簧需承受来自汽车车厢以及载物的重量,各弹簧片受力变形,产生弯曲变形;
(2)汽车在行驶过程中,当路面不平时,汽车发生较大幅度和频繁的颠簸,则汽车板簧需承受冲击载荷,并因此造成单向循环弯曲应力;(3)当汽车行驶速度过高时,也会加大汽车板簧的变形幅度,导致板簧加速疲劳而损坏;
(4)紧急刹车会瞬间加大汽车板簧的受力,长期频繁的紧急刹车会对汽车板簧造成严重的损坏;
(5)汽车在转弯时,若转弯速度较大,则会产生过大的离心力,加大外侧板簧的负荷;
3.汽车板簧有可能发生的断裂类型?
(1)塑性变形:当汽车超载时,载荷的重量超过板簧的承载能力,此时板簧往往发生永久性塑性变形
(2)疲劳断裂:由于汽车板簧长期在交变载荷下工作,则容易发生疲劳断裂;
4.如何设计实验确定失效类型?
通过对汽车板簧的化学成分分析,对断口处的显微组织分析等试验方法,分析疲劳断裂件中疲劳裂纹的萌生,疲劳裂纹的扩展,以及最后断裂。
(1)失效的汽车板簧用60Si2Mn弹簧钢制备而成,在失效板簧本体上取样做化学成分分析,观察测试结果是否符合国家规定的60Si2Mn弹簧钢标准。
(2)观察板簧的断口形貌,寻找疲劳源区,疲劳裂纹扩展区,以及瞬时断裂区。
板簧叶片表面(主要是受拉面)有裂痕,缺口,凹坑等,使叶片在受负荷时产生应力集中,引起早期疲劳破坏,所以板簧的疲劳断裂源往往在板簧的表面处。
在疲劳断口处还有清晰可见的贝纹线,此处为疲劳裂纹的扩展区,外观较为光滑,主要特征是围绕疲劳源存在一系列平行的同心弧线,即为疲劳线。
瞬间断裂区外观较为粗糙,与静载断口形貌相似。
(3)疲劳裂纹的萌生
从宏观断口的特征可以看出疲劳断裂的过程为:局部塑性变形—疲劳裂纹的形成—疲劳裂纹的扩展—瞬间断裂。
疲劳裂纹的萌生和扩展过程是疲劳破坏的起始和重要的损伤阶段。
金属所受的交变应力的最大值低于材料的屈服强度,在较低的应力下,材料的变形是局部的,非均匀的,变形严重的地方抗腐蚀能力低,颜色发暗。
微裂纹多在表面形成,主要原因为:一是因为板簧所受到的载荷使其发生弯曲变形,弯曲疲劳时表面变形最大;二是由于表面脱碳强度降低所导致。
60Si2Mn弹簧钢中的Si元素可促进渗碳体的分解,增加脱碳倾向当加热温度较高,保温时间较长时,很容易造成表面脱碳,位错与碳化物或夹杂物相互作用,使相界开裂,与基体剥离,形成微孔,微孔合并后形成裂纹源。
(4)疲劳裂纹的扩展
疲劳裂纹的扩展途径不是唯一的,可以沿晶扩展,也可以穿晶扩展。
在交变应力的作用下,由于位错沿着滑移面往复运动而造成围观裂纹的萌生和扩展。
断口是不均匀的,有许多相互连接而与主裂纹相交的小裂纹,在主裂纹的侧面还有与主裂纹近似平行的小裂纹。
在交变应力的作用下变形是不均匀的,也不是同时的,有先有后,在形成的裂纹扩展的同时又有新的裂纹萌生及扩展,先扩展的裂纹为主裂纹,周围新萌生的微裂纹可称为次生裂纹。
综上所述,提高汽车板簧的疲劳寿命可从以下几方面考虑:
1.选择优良的原材料,材料中的夹杂物以及杂质越少越好
2.加热时应在保护气氛或在真空进行,避免表面脱碳
3.进行表面研磨,提高表面光洁度
4.进行表面强化硬化处理。