180°折弯的模具结构设计
弯曲模具的结构设计
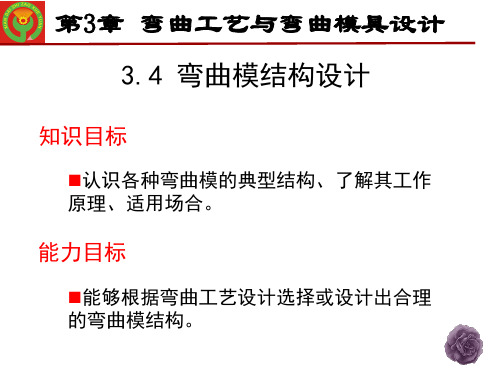
1—斜楔;2—活动凹模;3—凸模;4—弹性元件 动画15/16
第3章 弯曲工艺与弯曲模具设计
3.4 弯曲模结构设计
知识小结:
无压料装置 V形件弯曲模 有压料装置 1.单角弯曲模:L形件弯曲模 折板式弯曲模
一般U形件弯曲模 2.U形件弯曲模: 夹角小于90°的U形件弯曲模
斜楔结构的U形件弯曲模 3.Z形件弯曲模
思考: 定位板能否克服偏移现象?
结构特点: 结构简单、制造容易、成本低; 坯料容易偏移,精度较低。
2-定位板
第3章 弯曲工艺与弯曲模具设计
3.4 弯曲模结构设计
3.4.2 V形件 弯曲模(续) (2)有压料装置 的V形件弯曲模
思考: 坯料如何定位? 压料装置由哪些零件组成? 压料装置起什么作用?
结构特点: 结构简单、 工件平面度高、回弹量小。
3.4.7 C形弯曲模
1—模柄;2—凸模;3—导正销;4—定位销;5—顶件器;6—摆动式凹模;
第3章 弯曲工艺与弯曲模具设计 3.4 弯曲模结构设计
3.4.7 C形弯曲模(续)
(a) 弯曲初始状态 (b) U形中间弯曲状态 (c) C形最终弯曲状态
第3章 弯曲工艺与弯曲模具设计 3.4 弯曲模结构设计
弯曲时模具圆角半径与凹模深度1凸模圆角半径2凹模圆角半径查表3133凹模深度查表31335弯曲模主要部件和零件的设计351弯曲模工作部分尺寸的设计续例35弯曲凸凹模工作部分尺寸
第3章 弯曲工艺与弯曲模具设计 3.4 弯曲模结构设计
知识目标
认识各种弯曲模的典型结构、了解其工作 原理、适用场合。
能力目标
1—凸模;2—凹模;3—定位板
第3章 弯曲工艺与弯曲模具设计
180 度管道模设计

上世纪80年代初期,全世界管道、管接头行业相继掀起了一股以塑代钢的风潮,我们国内的塑料管接头企业也如火如荼地发展起来。
我当时创办了国内第一家私营的模具设计公司,(常州精艺模具设计社)承接了很多个系列的管接头模具的设计任务。
当时请我们设计管节头模具的厂家有20多家。
记得国家标准的号码是GB5836。
其中有一个弯管接头如下图:(经过简化的管接头的名称为:180度弯头。
从注塑模具的机构的层面来讲,这是非常困难的。
当时国外仅瑞士有一家搞出来,国内绝无仅有。
外国人只卖塑件不卖模具,就怕你们学了去。
明知山有虎,偏向虎山行。
不过这只大老虎也太厉害了。
我整整一个月,废寝忘食,也想不出个办法,从逻辑上来讲圆弧抽芯这一头抽出来,那一头和它的固定机构又进去了,假如分成二半,各旋转90度,但是各自的固定机构也要打架。
直想得我神魂颠倒,伊人憔悴。
我几次想过要放弃,也多次去北京有关部门商量,能否修改标准,但是谈何容易啊,“国标”能够随便该的吗?但事实是,模具做不出来,“国标”也是空的。
其实所有的有关厂家都在动脑筋,谁拔得头筹,就可以一统天下,垄断全国的生意。
后来有的企业想出了偷懒的方法,做成倆半,然后用胶水粘起来。
但是强度不够。
没有实用价值。
没有其他的办法,我只能继续硬着头皮向前冲,各种各样的方法都试过了,应该是已经到了“山穷水尽”的地步了,好听一点是“江郎才尽”吧。
我是个顽固派,死不服输的牛脾气,眼看着几个月过去了,人也一天天廋下去。
我几个学生看我太专注了,不要想坏了头脑,硬拖着我出去散散心。
来到一家舞厅玩,我根本不会跳舞,傻傻地坐在那里看别人跳,看着打蜡的象玻璃一样光滑的地板和地板上转来转去的人影,我迷糊了,昏昏沉沉快要睡着了一样。
突然间我脑中灵光一现,为什么跳舞的人在转,地板上人的影子也在转,都在转,人和影子为什么不打架呢?假如这地板是模具的分型面,上面转的人是前模的旋转机构,人的影子是后模的旋转机构,那不是毫不相干,不会打架了吗?我大叫一声:“我想到了,我想到了”,手舞足蹈地冲出了舞厅。
弯曲模结构设计
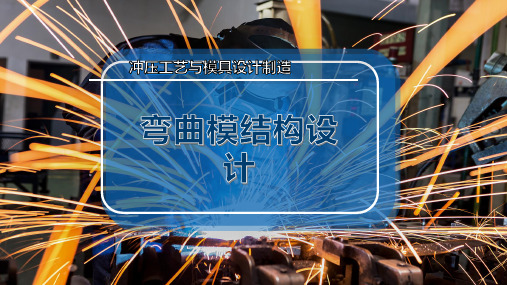
弯曲工艺与弯曲模设计
弯曲模结构设计
二、弯曲模工作部分尺寸的设计
4.凸、凹模间隙 V形弯曲模的凸、凹模间隙是靠调整压机的闭合高度来控
制的,设计时可以不考虑。
U形件弯曲模的凸、凹模单边间隙一般可按下式计算:
Z / 2 tmax Ct t Ct
式中 C——间隙系数,可查表3.9.4。
当工件精度要求较高时,其间隙应适当缩小,取Z/2=t。
(1)尺寸标注在外形上
(2)尺寸标注在外形上
凹模尺寸 LA
Lmax 0.75
A 0
凸模尺寸
LT
(LAZ)源自0 T凸模尺寸 凹模尺寸
LT
(Lmin
0.75)
0 T
LA
(LT
Z)A 0
式中
T A——凸、凹模的制造公差,可采用IT7~IT9级精度, 一般取凸模的精度比凹模精度高一级。
弯曲工艺与弯曲模设计
1.凸模圆角半径 当工件的相对弯曲半径r/t较小时,凸模圆角半径 rT
取等于工件的弯曲半径r,但不应小于表3.2.2所列的最小弯 曲半径值rmin。
当r/t>10时,则应考虑回弹,将凸模圆角半径rT 加以修正。
弯曲工艺与弯曲模设计
弯曲模结构设计
二、弯曲模工作部分尺寸的设计
2.凹模圆角半径
凹模两边的圆角半径应一致,否则在弯曲时坯料会发生偏移。
弯曲工艺与弯曲模设计
弯曲模结构设计
二、弯曲模工作部分尺寸的设计
5.U形件弯曲凸、凹模横向尺寸及公差
决定原则:
工件标注外形尺寸时,应以凹模为基准件,间隙取在凸 模上。
工件标注内形尺寸时,应以凸模为基准件,间隙取在凹 模上。
弯曲工艺与弯曲模设计
弯曲模具设计(带全套cad图)

模具课程设计说明书——弯曲模课程设计学校:学院:专业:姓名:学号:指导教师:目录第一章工艺分析及工艺方案的拟订1.1、零件工艺性分析 (1)1.2、工艺方案的确定 (1)第二章工艺设计2.1、确定排样方案 (2)2.2、计算各工序的压力 (3)2.3、压力机的选取 (4)第三章模具类型及结构形式的选择 (5)第四章模具工作零件刃口尺寸及公差的计算4.1、凸、凹模刃口尺寸计算原则 (5)4.2、刃口尺寸计算 (5)第五章模具零件的选用,设计及必要的计算5.1、凹模结构尺寸的确定 (6)5.2、卸料树脂的选用 (7)5.3、其他标准件零件的选用 (7)第六章凸凹模加工工艺方案6.1、凹模、凸模加工工艺路线 (7)6.2、模具装配 (9)第一章工艺分析及工艺方案的拟订1.1零件工艺性分析一、零件图二、零件的工艺性分析(1)冲裁件的结构工艺性此制件的形状较简单,需要圆角过渡,可以加上R0.5,便于模具的加工和减少冲压时在尖角处开裂的现象,同时也可以防止尖角部位刃口的过快磨损。
(2)冲裁件的尺寸精度冲裁件的精度主要以其尺寸精度、冲裁断面粗糙度、毛刺高度三个方面的指标来衡量,根据零件图上的尺寸标注及公差,可以判断属于尺寸精度为IT12—IT14的经济级普通冲裁。
1.2、工艺方案的确定一、冲压工序的选择在满足冲裁件质量与生产率的要求下,选择单工序冲裁方式,其模具寿命较长,生产率高,操作较方便和工作安全性高。
二、冲压顺序的安排落料,弯曲共两道工序,本设计中只需要设计落料模。
第二章工艺设计2.1、确定排样方案一、搭边与料宽搭边搭边值的大小与材料的力学性能、厚度、零件的形状与尺寸、排样的形式、送料及挡料方式、卸料方式等因素有关。
搭边值一般由经验确定,根据所给材料厚度δ=1.2mm,确定搭边工作间a1为2.0mm, a为2.0mm。
具体可见排样图,如下:(2)条料宽度条料宽度的确定原则:最小条料宽度要保证冲裁时零件周边有足够的搭边值,最大条料宽度要能在冲裁时顺利地在导料板之间送进,并与导料板之间有一定的间隙。
薄壁大圆弧零件的折弯模具设计方法
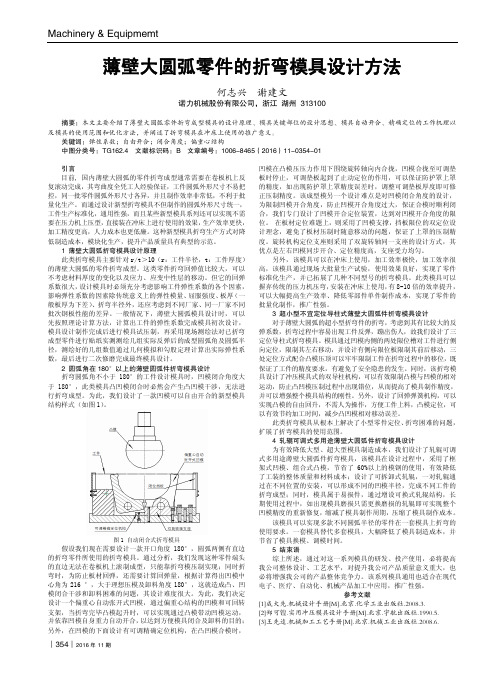
Machinery & Equipmemt︱354︱2016年11期薄壁大圆弧零件的折弯模具设计方法何志兴 谢建文诺力机械股份有限公司,浙江 湖州 313100摘要:本文主要介绍了薄壁大圆弧零件折弯成型模具的设计原理、模具关键部位的设计思想、模具自动开合、精确定位的工作机理以及模具的使用范围和优化方法,并阐述了折弯模具在冲床上使用的推广意义。
关键词:弹性系数;自由开合;闭合角度;偏重心结构中图分类号:TG162.4 文献标识码:B 文章编号:1006-8465(2016)11-0354-01引言 目前, 国内薄壁大圆弧的零件折弯成型通常需要在卷板机上反复滚动完成,其弯曲度全凭工人经验保证,工件圆弧外形尺寸不易把控,同一批零件圆弧外形尺寸各异,并且制作效率非常低,不利于批量化生产。
而通过设计新型折弯模具不但制作的圆弧外形尺寸统一,工件生产标准化,通用性强,而且某些新型模具系列还可以实现不需要在压力机上压型,直接装在冲床上进行使用的效果,生产效率更快,加工精度更高,人力成本也更低廉。
这种新型模具折弯生产方式对降低制造成本,模块化生产,提升产品质量具有典型的示范。
1 薄壁大圆弧折弯模具设计原理 此类折弯模具主要针对r/t>10(r:工件半径,t:工件厚度)的薄壁大圆弧的零件折弯成型。
这类零件折弯回弹值比较大,可以不考虑材料厚度的变化以及应力、应变中性层的移动。
但它的回弹系数很大,设计模具时必须充分考虑影响工件弹性系数的各个因素,影响弹性系数的因素除传统意义上的弹性模量、屈服强度、板厚(一般板厚为下差)、折弯半径外,还应考虑到不同厂家、同一厂家不同批次钢板性能的差异。
一般情况下,薄壁大圆弧模具设计时,可以先按照理论计算方法,计算出工件的弹性系数完成模具初次设计,模具设计制作完成后进行模具试压制,再采用现场测绘法对已折弯成型零件进行贴纸实测测绘几组实际反弹后的成型圆弧角及圆弧半径,测绘好的几组数值通过几何模拟和勾股定理计算出实际弹性系数,最后进行二次修磨完成最终模具设计。
折弯模结构设计_图文_图文

• 3.3 上下脱料板应有内导柱导正,内导柱长度在闭合状态 下不可伸出脱料板;
• 3.4 下模做导正块,使向下折弯冲头在折弯前先被导正, 导正镶块应在自由状态时比下脱板高3~5MM为佳;
• 3.5 定位方式在一般情况下采用外定位,特殊情况采用内 孔定位。
上下成型模结构
实例
4.向下成型
•料厚T •0.6 以下 •0.6 ~1.0 •1.2~1.5 •1.6~2.0 •2.0以上
•V沟深度 •3.0 H
•俩边R值 •4.5 •请示上
级
•2.0 •2.5~3.0 •3.0~3.5 •请示上
级
• 2.3.2 当折边高度较矮时,作V曲模时一定要先 在侧视图上模拟,初始阶段料带边缘一定要过俩 边R1。0mm左右,如图B所示,相差不多时可通 过适当减少V沟深度H和俩边R值来满足此要求。 相差太多时要请示上级来确认是否按V曲模设计 ,还是按其它折弯方式。有几种方式要分别考虑 ,图C,产品中间有一小部分初始阶段料带边缘没 有过俩边R1。0mm,还是可以考虑V曲的,图D 是产品中间有很长部分初始阶段料带边缘没有过 俩边R1。0mm,图E是产品端部有一部分,此俩
•折弯模结构设计_图文_图文.ppt
一、分类
V形折弯
向下成型
折弯模的 结构分类
Z形折弯
向上成型
二、工艺分析
1.Z形折弯
• 1.1 当C<5T时,一次成形,计算参见展开系数 设计标准(如图1)为减少材料的流动性,上模 板成形部分应做压筋,宽度0.5MM≤W≤1.5MM ,深05MM≤H≤0.3MM; 为减轻材料的刮伤以及 有利于材料的成形,应在下模折弯块成形部分倒 角R≥0.3MM; 由于Z曲在折弯过程中流动性很大 ,在保证压缩量足够的情况下,弹簧压力应越大 越好。
无擦伤折弯模具结构的设计

无擦伤折弯模具的结构设计摘要: 越来越多的机箱(机柜)面板或上盖等板金制品中,对其外观表面要求很严格.在这些制折弯成形时,用一般的折弯模具很难达到此种表面质量要求,对此,提出一种新的折弯模具结构的设计.关键词: 翻转块折弯块, 滑动摩擦, 静摩擦. 转动轴点. 翻倒.一,一般折弯模具结构分析最常见的板金制品折弯模具结构如图一所示,此种模具结构折弯时,因制品与折弯块是相对滑动摩擦,故在制品的折弯外侧面会有擦伤(R 越小则擦伤越严重).为解决此问题,也可在此基础上改进,把折弯块的R 部改为滚轴结构,如图二,在折弯时滚轴在制品的带动下转动,因此制品外侧与滚轴是发生滚动摩擦,成形后擦伤痕迹明显减少,但不能完全避免!1.折弯块,2.下脱料板 1,滚轴 2.折弯块,3.下脱料板 图一 一般折弯模具二,无擦伤折弯模具的结构设计如右图三所示为一”U”形制品折弯模具结构图, 1,折弯上冲头 2,翻动折弯块(板) 3,翻动块定位 4,下浮动脱料板5,翻动板托块(支撑块) 6,翻动板靠块 7,下固定板制品示意图三,翻动板折弯成形过程分析及设计要点:1. 模具在折弯初始状态时,翻动折弯块水平置于下脱料板与翻动板定位块之间,脱料板比翻动折弯块高出1~2mm.如图四所示,设计时要确保b=a+0.05,方便翻动块能立起,并且要使翻板左下部修成大R角, 同时使转动半径c=d-0.1,防止翻动板绕转动轴点翻转时与定位块干涉.2,在折弯开始时,下脱料板向下运动,材料带动翻动板绕靠块的尖角点作转动,并且翻动板会在靠块尖角处作相对滑动.此时,要确保翻动板外侧有在R,以免下侧定位块干涉,而翻不起来,在靠块尖角处不可以倒角,否则翻动板可能会滑出.3,当翻动板绕转动点转到直立插入下脱料板与靠块之间,此时脱料板继续向下,动,翻动板与靠块发生滑动,当翻动板下到与靠块下面6~8mm时成形完成,要点是确保脱料板与靠块的间隙要稳定,磨,以便减小滑动摩擦力,对于下脱料板的行程取30mm较可靠.(因行程较大,用气垫顶料)4,脱模时,下脱料板被顶起,翻动板在反撑块的作用下向上推出,完全脱出后,翻动板在自身重力的作用下绕着支撑块的支撑点向外翻动与材料脱离,翻倒后在侧定位块的大圆角作用下自找正,回复到原始状态.此过程的要点是一定要把支撑块的上面以及翻动板下支撑部分做成斜坡(支撑点越小越好),以便于靠自重力翻转.(注意:斜坡只能是局部而不是整条,否则折弯开始时翻动块可能会滑出.)四,翻动板折弯模具的应用:翻动板折弯模成形过程中,材料面与翻动板的滑动极小,所以成形后制品表面无损伤,擦痕.常用于机壳,面板等外观有严格要求的制品.也可应用于诸如:折弯时避位多,折起直边太长,或折边根部有凸起等不能用一般折弯模具的制品(如图八:);还可用于成形在R角或小于90度的制品,(如图九:)五,结束语此种无擦伤折弯模具的运动是滑动与转动相结合在以转动为主要运动,与制品表面的相对滑动几乎没有,所以能达到很好的外观要求.一般人们可能会认为此种结构很复杂,其实它就是人们熟知的摆块结构在理论上的发展与实践应用的变异.参考文献:1,<<泠压冲模设计>>,第四机械工业部标准化研究所,1979.北京.2,<<冲模设计手册>>,冲模设计手册编写组,1999,机械工业出版社。
弯曲及弯曲模设计
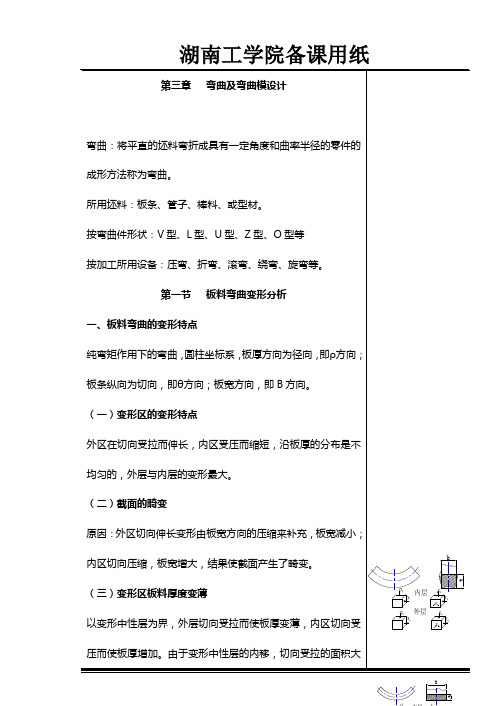
第三章弯曲及弯曲模设计弯曲:将平直的坯料弯折成具有一定角度和曲率半径的零件的成形方法称为弯曲。
所用坯料:板条、管子、棒料、或型材。
按弯曲件形状:V型、L型、U型、Z型、O型等按加工所用设备:压弯、折弯、滚弯、绕弯、旋弯等。
第一节板料弯曲变形分析一、板料弯曲的变形特点纯弯矩作用下的弯曲,圆柱坐标系,板厚方向为径向,即ρ方向;板条纵向为切向,即θ方向;板宽方向,即B方向。
(一)变形区的变形特点外区在切向受拉而伸长,内区受压而缩短,沿板厚的分布是不均匀的,外层与内层的变形最大。
(二)截面的畸变原因:外区切向伸长变形由板宽方向的压缩来补充,板宽减小;内区切向压缩,板宽增大,结果使截面产生了畸变。
(三)变形区板料厚度变薄以变形中性层为界,外层切向受拉而使板厚变薄,内区切向受压而使板厚增加。
由于变形中性层的内移,切向受拉的面积大于受压面积。
(四)弯曲后板料长度增加一般弯曲件均属于宽板弯曲,因此弯曲前后板料宽度基本不变,对于r/t的较小弯曲件,由于板厚有明显的变薄现象,按体积不变,必然造成板料长度的增加。
二、弯曲变形区的应力应变状态:宽板和窄板的径向和切向应力应变相同,而宽度方向则不同。
1、窄板弯曲(b/t≤3):窄板弯曲时,根据塑性力学中最小阻力定律,材料沿宽度方向的流动几乎不受限制,故有σb≈0。
根据体积不变条件εθ+εb+εt=0可知,窄板弯曲时的应力应变分布如图示。
2、宽板弯曲(b/t>3):材料沿宽度方向的流动阻力大,εb≈0。
其应力应变分布如图示。
外层内层bσρσσθσρσbθσεθερbεθερt外层内层ρσσθσρθσεθεbερεθεεbρtb三、弯曲变形的阶段性 (一)弹性弯曲阶段如右图a)示,在弯曲的初期,外弯曲力矩M 的数值较小,在变形区内、外层表层产生的切向应力的数值远小于材料的屈服应力,沿板厚的全部材料层只产生弹性变形。
去掉弯矩,变形将消失。
(二)弹-塑性弯曲阶段如上图b)示,当外弯矩M 增大到一定数值时,内、外表层的切向应力首先达到材料的屈服应力,而进入塑性状态。
- 1、下载文档前请自行甄别文档内容的完整性,平台不提供额外的编辑、内容补充、找答案等附加服务。
- 2、"仅部分预览"的文档,不可在线预览部分如存在完整性等问题,可反馈申请退款(可完整预览的文档不适用该条件!)。
- 3、如文档侵犯您的权益,请联系客服反馈,我们会尽快为您处理(人工客服工作时间:9:00-18:30)。
標題:《180°折彎的模具結構設計》作者: 羅峻
工號: KD553
部門: DT1五金開發
關鍵詞: 180°折彎,送料,脫料,雙滑塊機構,定深折彎,整形,兩次折彎,合模,分模,帶料,變形,剝料板行程,成形。
摘要:在模具設計中,如果產品有180º折彎結構,排樣時盡可能把產品180°的折彎方向設計成與送料一致,這樣便於送料和脫料。
如果根據產品結構要求,必須設計成
180°折彎方向與送料反向,則可採用雙滑塊機構,為了避免刮傷材料,滑塊應採用斜面配合。
正文:180°折彎的模具結構設計在五金模具設計中,我們經常會遇到一些SHELL類的產品有180°折彎的結構形式
如圖(A)﹑(B)所示。
設計此類模具應注意:排樣時盡可能把產品180°的折彎方向設計
個步驟完成:
a:向下定深折彎 b:向上打翹起
c:向下折90° d:180°折彎根據第四步(d )的1801.用滑塊和擺塊來進行 180°折彎
A B C
如圖(D)所示,當彈片被向下折90°以後,可用擺塊調整來使其達到大於90°。
用滑塊和擺塊來調整180°成形,這種模具結構設計比較復雜,有時調整效果不是很理想,並且在大量生產中調整狀況亦不是很穩定,所以這種結構在180°折彎中盡量少用,隻適合用於大於90°而小於180°的折彎。
D
2.採用兩次折彎機構:
如圖(E)所示,由於兩次折彎的折彎線不在同一位置上,故能達到180°折彎之效果。
兩次折彎線的距離L等於C∕4,C的大小如圖F所示。
E F
這種設計方法的特點是:模具結構簡單,折彎效果好,並且在生產中比較穩定。
方案2.
二.180
如圖(G
其具體運動情況如圖:滑塊2在固定塊3上左右滑動,滑塊4在固定塊5垂直紙面滑動。
沖子1調整2,剝料板入子6調整4。
合模狀態:當上模下行時,剝料板入子 6先接觸到滑塊4,推動滑塊4垂直紙面向裡運動,先達到工作狀態的位置。
隨著上模的繼續下行,1推動2後達到工作狀態,完成成形工作。
分模狀態:隨著模具上行,上模板帶動沖子1向上運動,則 2退後恢復到初始位置,使其完全與工件脫離開。
緊接著剝料板開始向上運動。
6 向上運動,則 4沿著5垂直紙面向
合模過程:隨著模具下行,L6大於L1,則6首先推動4運動達到工作狀態,緊接著1推動2後達到工作狀態,完成成形動作。
J
分模過程:隨著上模座的上行,由於剝料板行程較大,直至1和6完全從下模板脫出,即2和4完全恢復到初始位置,剝料板才開始上行,此時滑塊4 與工件完全脫開,不會帶料。
這樣便於送料。
同時4與5 是斜面配合,這樣設計才不會刮傷材料割面。
由上述分析可知:這種設計方法結構雖然很復雜,但解決了帶料問題,而且可以進行大量生產。
這種設計方法的關鍵是:合模時,滑塊4要比滑塊2先到位,分模時,剝料板在滑塊2和4恢復到初始位置才開始運動。
滑塊4與5要斜面配合,但斜度不能太大,一般取6--7º。
用方式2的結構設計的模具投之於生產,得到了生產課同仁的認可,模具可以滿足大量生產之要求。
以上是我對180º折彎的模具結構的一些見解,也是我在模具設計中的一些心得,上敘所有的模具結構均在試模過程驗証過。
由於本人模具設計經驗不足,如本文有不妥之處,敬請賜教。
參考文獻: 《沖模設計應用實例》, 機械工業出版社,ISBN 7-111-07055-0 《沖模設計資料》,重慶大學王孝培主編,機械工業出版社
《模具材料與使用壽命》,武漢汽車工業大學出版社。