翻边整形模模具设计规范
翻边模具
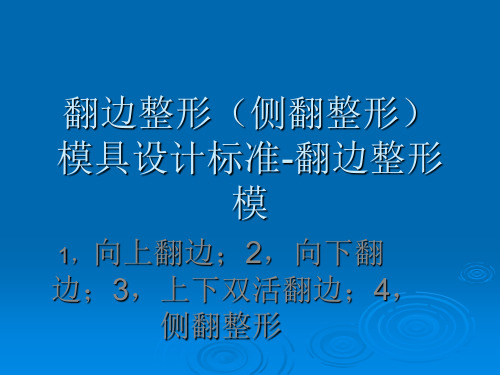
1,向上翻边;2,向下翻
边;3,上下双活翻边;4, 侧翻整形
1,向上翻边:
下模+托料芯
上模
常规上翻:示例:AC274,V102 标准上翻机构:示例:AB455 非标上翻机构:示例:AB455
2,向下翻边:
下模
上模+压料芯
事例:AC251,V338
3,上下双活翻边:
事例6:AA734:滑车为直推形式。 (兼两侧平推三功能)
下模+托料芯
上模+压料芯
事例:AC861,V342
4,侧翻整形:
事例1:V013:滑车为侧推平推形 式,侧翻边为吊翻,侧翻
事例2:AC22229:滑车为滚轴形 式
事例4:AB818: 滑车为拉车形式 (侧翻驱动器为固定在下模和在滑 车上两种形式)
事例5:T748: 滑车为拉车形式,带 侧压料芯。
翻边整形模
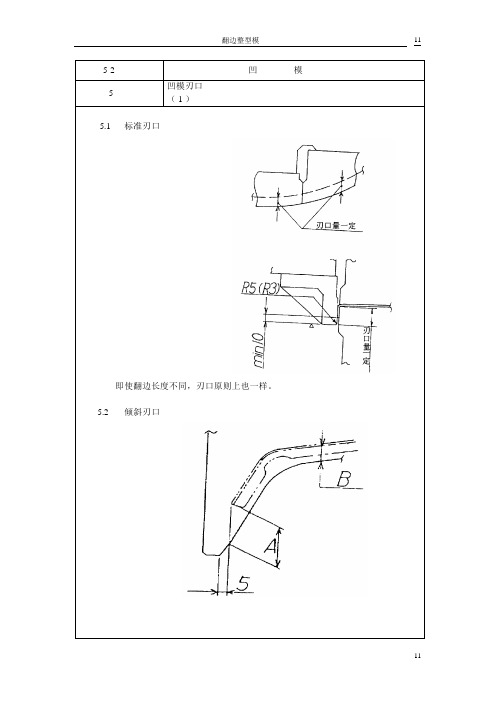
5-3 fv5 顶出器的强度
顶
出
器
18
翻边整型模
19
5.1
标准厚度 顶出器的厚度以右图为基准。(铸件的情况下) 特别是在中央部,顶出器的 断面面积明显变小时,应注意 其强度。
5.2
注意事项 强度变小的地方,或用钢材增加强度,或将材质改为铸钢或球铁。 (考虑使用铸钢时,进行优化计算)
钢材镶块 用钢或球铁一体 压弯翻边时,断面面积小的部位的底面必须接触到底板;断面强度弱的部分, 底面必须与底板接触。
翻边整型模
11
5-2 5 凹模刃口 (1) 标准刃口
凹
模
5.1
即使翻边长度不同,刃口原则上也一样。 5.2 倾斜刃口
11
翻边整型模
12
5-2 5 凹模刃口 (2)
凹
模
5.3
宽度小的冲压件两侧有翻边的情况。
冲压件的宽度小,形状平滑时。
5.4
对凹模的强度有影响时。
凹模的强度弱 时,凹模 A 的刃口如 图所示。
5-3
顶
出
器
19
翻边整型模
20
6
顶出器与凹模的间隙 (1)
顶出器相对与凹模的间隙, 为 0.5 。(平面上不表示出) 模具图上不表示出尺寸。
20
翻边整型模
21
5-3 2
翻 翻边退料板的使用条件 (1)
边
退
料
板
1.1
使用条件 翻边不易退件的部位,必须设置翻边退料板。 例子 ☆ 对称翻边 门、发罩、行李箱板
27
翻边整型模
28
6
内缘翻边的翻边退料板 (1)
5-3
模
具
结
构
04第三章 翻边整形模数控加工规范

20 第三章 翻边整形模数控加工规范第一节 翻整凸模底板一. 作底面加工的基准面1.检测毛坯高度基准线,也称等高线(百位线),调整要求基准线对角高度一致.大型模板(长3.5m 以上)为底面加工作基准时应考虑正面加工各重要位置的加工余量,找正试切余量,可重设定中心,以避免反向加工完后 ,正面各位置尺寸无法按底面基准坐标加工出来。
2.铣基准面:力求做到基准面等高,若无法一致,应取整数差加工(标准垫块作为高度补差)。
二.底面加工A 按铸件中心基准线找正定中心,工件装夹B 底面粗铣:ф63盘型刀具加工,依百位线去除余量。
C快速定位键槽加工,用ф25钻铣粗铣留余量单边0.5mm 。
ф20或ф16立铣精加工,用检棒检测,槽宽公差28+0.03+0.01 。
D压板槽加工,用ф25钻铣开槽.E压板面加工:正面直头加工无干涉的待正面加工时用D63R8刀具加工,有干涉而直头无法加工的转侧铣头加工。
F松开工件压力点螺母,检查支撑点受力情况,作调整,用ф200精盘刀精加工底面,切深在0.2mm以内,要求平面精度在0.02mm以内。
小工件可适当施加压板压力和应用侧顶装置,避免工件移动。
注意事项:1.工件底面加沙,硬度不均等异常切削条件对刀具的影响。
局部问题可采用小刀具,如ф30钻铣消除异常面,可略低于实际加工面0.1mm。
2.底面精加工时支撑物必须均衡受力。
3.一次底面精加工若不能达到其精度,应考虑采用:①. 量表测出表面高度差数值,反向切深为前次高度差值加0.05mm加工。
②. 若出现局部偏差,可针对局部去除高度差值部分。
二.正面结构面加工工件装夹: 按底面定位键槽定中心,用快速定位键定位装夹工件.检查:检验XY平面上的重要加工部位的加工余量,可允许最大偏差5mm以内,如出现严重超差应考虑局部加垫,底面加工位置(快速定位键.压板槽等)重做等异常现象。
ABCDE.结构平面粗加工:选用φ63盘刀开粗。
留0.1-0.5mm余量待精加工。
翻边孔工艺与设计规范标准
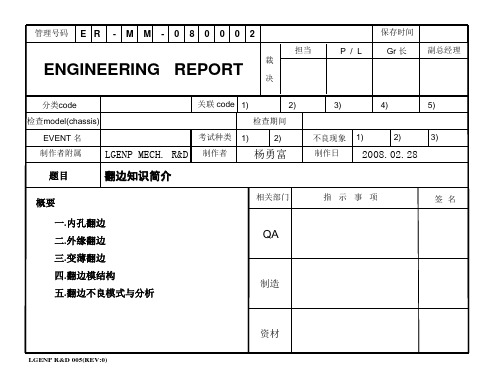
非圆孔翻边坯料的预孔形状和尺寸,可以按圆孔翻边、弯曲和拉深各区分别展开,然后用作图法把 各展开线交接处光滑连接起来。
图1.3.1 非圆孔翻孔
7/13
二.外缘翻边
1.伸长类翻边
伸长类外缘翻边时,其变形类似于内孔翻边,但由于是沿不封闭曲线翻边,坯料变形区内切向的拉应力和 切向的伸长变形沿翻边线的分布是不均匀的,在中部最大,而两端为零。假如采用宽度b一致的坯料形状,则 翻边后零件的高度就不是平齐的,而是两端高度大,中间高度小的竖边。另外,竖边的端线也不垂直,而是向 成一定的角度。为了得到平齐一致的翻边高度,应在坯料的两端对坯料的轮廓线做必要的修正,内倾斜采用如 图2.1.1a中虚边所示的形状,其修正值根据变形程度和 的大小而不同。如果翻边的高度不大,而且翻边沿线的 的曲率半径很大时,则可以不做修正。
K=d/D
1/13
一.内孔翻边
图1.1.1圆孔翻边时的应力与变形情况
K称为翻边系数,K值愈小,则变形程度愈大。翻边时孔边不破裂所能达到的最小K值,称为极限翻边 系数。表1.1.2所列的是低碳钢圆孔翻边的极限翻边系数。对于其它材料,按其塑性情况,可参考表列数值 适当增减。从表中的数值可以看出,影响极限翻边系数的因素很多,除材料塑性外,还有翻边凸模的形式 孔的加工方法及预制的孔径与板料厚度的比值(体现工序件相对厚度的影响)。
2.圆孔翻边
1)圆孔翻边的变形特点与变形程度 将画有距离相等的坐标网格(图1.1.1a)的坯料,放入翻边模内进行翻边(图1.1.1c)。翻边后从图
1.1.1b所示的冲件坐标网格的变化可以看出:坐标网格由扇形变为矩形,说明金属沿切向伸长,愈靠近 口伸长越大。同心圆之间的距离变化不明显,即金属在径向变形很小。竖边的壁厚有所减薄,尤其在孔 口处减薄较为明显。由此不难分析,翻孔时坯料的变形区是d和D1之间的环形部分。变形区受两向拉应 力—切向拉应力σ 1和σ 3的作用( 图1.1.1c );其中切向拉应力是最大主应力。在坯料孔口处,切向拉应 力达到最大值。因此,圆孔翻边的成型障碍在于孔口边缘被拉裂。破裂的条件取决于变形程度的大小。 变形程度以翻边前径d与翻边后孔径D的比值K来表示,即:
第4部分翻边整形模
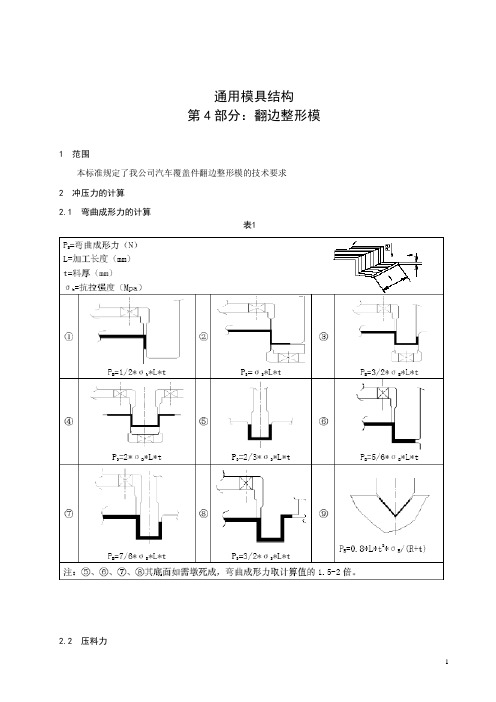
通用模具结构第4部分:翻边整形模1 范围本标准规定了我公司汽车覆盖件翻边整形模的技术要求2 冲压力的计算2.1 弯曲成形力的计算表12.2 压料力1压料力一般为压弯力的15%-30%2.2.1 P为冲压开始点的压料力外板:P=0.3P Z(N)内板:P=(0.15-0.2)P Z(N)2.2.2 弹簧等压力源尽量设在成形部位附近图12.2.3 视压料板形状确定是否兼负平衡作用,如存在平衡力的因素,压料力应大于计算压力。
2.2.4 上弹簧压料和下气垫压料同时使用时,主要考虑向下翻边时的上压料力。
2.2.5 内板件在成形时,如有向外拉料的可能时(如图2),应加大压料力,计算方法与外板相同。
图22.3 弯曲整形力的计算弯曲整形力P=F*qF:为整形部分的投影面积(mm )q:为整形所需的单位压力(MPa),见数据表2:表2材料材料厚度材料材料厚度<3 3-10 <3 3-1008-20号钢80-100 100-120 8TiL 120-150 150-180 20-35号钢100-120 120-150 10TiL 150-180 180-2103 工作行程23.1 ※※※※※※※※※※※※※※※※翻边行程※※※※※※※※※※※※※※※※※※※※※3.1.1 平面及断面形状为直线时,制件末端距凹模圆角R 切点3mm,如图33.1.2 翻边线为折曲线时,在冲压方向上保证翻边行程L不变。
图43.1.3 翻边凸缘宽度不等时,按照翻边宽度最宽处考虑,压入深度沿冲压方向同时开始翻边。
图53.1.4 折弯线和翻边在同一条线上时——折弯部比翻边高度深时,L>l1 压入深度取L值。
34图6 ——翻边高度超出折弯线时,压入深度渐渐变化。
图7——凹模端部弧度大的情况下,如图所示加出余量:图8——翻边线变化大,一个冲压方向不能成形,要分成两序完成,两序相接处最少要重合40mm。
图93.2 压件器工作行程计算图105翻边顶出器工作行程的设定原则上为确保压件器脱开冲压件后才允许翻边顶出器工作。
4.翻边 翻边整形 翻孔设计规范
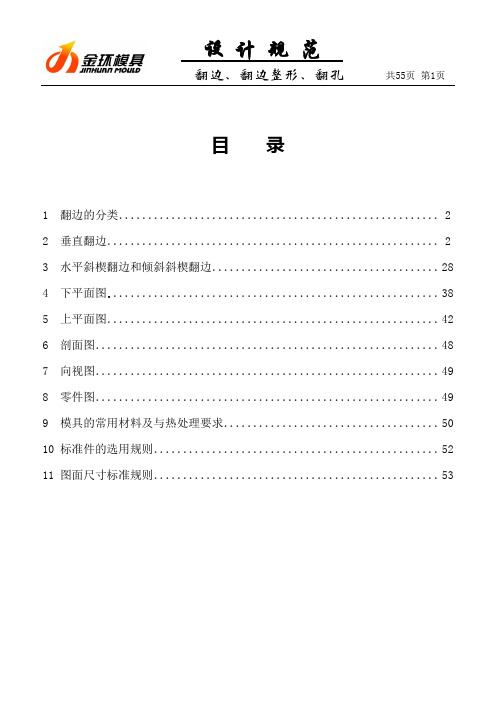
目录1 翻边的分类.......................................................22 垂直翻边.........................................................23 水平斜楔翻边和倾斜斜楔翻边.......................................284 下平面图.........................................................385 上平面图.........................................................426 剖面图...........................................................487 向视图...........................................................498 零件图...........................................................499 模具的常用材料及与热处理要求.....................................5010 标准件的选用规则.................................................5211 图面尺寸标准规则.................................................531 翻边的分类翻边按冲压方向分可分为垂直翻边、水平斜楔、翻边和倾斜翻边。
2 垂直翻边垂直翻边分为平板类翻边和拉延成形类翻边。
2.1 平板类翻边(压弯)平板类翻边(压弯)分为平板直线压弯,曲线翻边和翻孔。
2.1.1平板直线压弯平板直线压弯的展开计算: L=e1+e2+e3+en+R1e+R2e+Rne 式中:L :展开长度;e1、en :各段走线段长度;R1e :压弯圆角的中性层展开长度。
冲压模具毕业设计翻边模设计

刃口尺寸的调整方法:根据冲压件的尺寸和形状,以及冲压机的压力和速度,进行适当的调整
刃口尺寸的确定注意事项:刃口尺寸的确定要符合冲压件的尺寸和形状,以及冲压机的压力和速度,以保证冲压件的质量和生产效率。
刃口尺寸的确定原则:根据冲压件的尺寸和形状,以及冲压机的压力和速度来确定
刃口尺寸的计算方法:根据冲压件的尺寸和形状,以及冲压机的压力和速度,利用公式进行计算
材料处理:对材料进行热处理、表面处理等,提高材料的耐磨性、耐腐蚀性和抗疲劳性
翻边模的工艺参数设计
PART FIVE
冲压工艺方案的确定
确定冲压工艺方案的目的:提高生产效率,降低成本,保证产品质量
冲压工艺方案的选择:根据产品形状、尺寸、材料等因素选择合适的冲压工艺方案
冲压工艺方案的设计:包括模具设计、冲压设备选择、冲压工艺参数设定等
退火:将模具材料加热到一定温度后保温一定时间,消除应力,提高塑性和韧性
调质:将模具材料加热到一定温度后保温一定时间,然后冷却,提高硬度和韧性
渗碳:将模具材料加热到一定温度后渗入碳元素,提高表面硬度和耐磨性
模具材料的选用原则
材料强度:应满足模具的使用寿命要求
材料硬度:应与冲压件的硬度相匹配
材料耐磨性:应具有良好的耐磨性,减少磨损
冲压工艺方案的优化:根据生产实际情况,对冲压工艺方案进行优化和改进,以提高生产效率和产品质量。
冲裁间隙的确定
冲裁间隙的定义:冲裁过程中,冲头和被冲材料之间的最小距离
冲裁间隙的确定方法:经验公式法、试验法、计算机模拟法等
冲裁间隙的确定原则:保证冲裁质量、提高生产效率、降低成本等
冲裁间隙的影响因素:材料性质、冲头形状、冲压速度等
寿命预测的重要性:合理预测模具寿命,有助于优化生产工艺,降低生产成本,提高产品质量。
4.翻边翻边整形翻孔设计要求规范
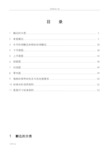
目录1 翻边的分类.......................................................22 垂直翻边.........................................................23 水平斜楔翻边和倾斜斜楔翻边.......................................284 下平面图.........................................................385 上平面图.........................................................426 剖面图...........................................................487 向视图...........................................................498 零件图...........................................................499 模具的常用材料及与热处理要求.....................................5010 标准件的选用规则.................................................5211 图面尺寸标准规则.................................................53 1 翻边的分类翻边按冲压方向分可分为垂直翻边、水平斜楔、翻边和倾斜翻边。
2 垂直翻边垂直翻边分为平板类翻边和拉延成形类翻边。
2.1 平板类翻边(压弯)平板类翻边(压弯)分为平板直线压弯,曲线翻边和翻孔。
2.1.1平板直线压弯平板直线压弯的展开计算: L=e1+e2+e3+en+R1e+R2e+Rne 式中:L :展开长度;e1、en :各段走线段长度;R1e :压弯圆角的中性层展开长度。
- 1、下载文档前请自行甄别文档内容的完整性,平台不提供额外的编辑、内容补充、找答案等附加服务。
- 2、"仅部分预览"的文档,不可在线预览部分如存在完整性等问题,可反馈申请退款(可完整预览的文档不适用该条件!)。
- 3、如文档侵犯您的权益,请联系客服反馈,我们会尽快为您处理(人工客服工作时间:9:00-18:30)。
目录序号内容页次1 冲压力的计算 22 工作行程 43 凸模托料面的设计94 压件器的强度设计115 压件器与凹模分界的设定136 翻边模刃口的种类及使用157 翻边顶出器的安装标准258 退料块及定位块的形状289 翻边变形对策3010 铸件壁厚设计3211 铸造减轻孔设计331.冲压力的计算1.1.弯曲成形力的计算PB=弯曲成形力(N)L=加工长度(mm)t=料厚(mm)σb=抗拉强度(Mpa)①PB =1/2*σb*L*t②PB=σB*L*t③PB=3/2*σB*L*t④PB =2*σB*L*t⑤PB=2/3*σB*L*t⑥PB=5/6*σB*L*t⑦PB =7/6*σB*L*t⑧PB=3/2*σB*L*t⑨PB=0.8*L*t2*σB/(R+t)注:⑤、⑥、⑦、⑧其底面如需墩死成,弯曲成形力取计算值的1.5-2倍。
1.2.压料力压料力一般为压弯力的15%-30%。
➢P为冲压开始点的压料力外板P=0.3 PB(N)内板P=(0.15-0.2)PB(N)➢弹簧等压力源尽量设在成形部位附近制定部门制定日期制定审定批准版次发行部门➢视压料板形状确定是否兼负平衡作用,如存在平衡力的因素,压料力应大于计算压力。
➢上弹簧压料和下气垫压料同时使用时,主要考虑向下翻边时的上压料力。
➢内板件在成形时,如有向外拉料的可能时(如下图示),应加大压料力,计算方法与外板相同。
1.3.弯曲整形力的计算弯曲整形力P=F*qF:为整形部分的投影面积(mm2)q:为整形所需的单位压力(MPa),见数据下表:2.工作行程2.1.翻边行程2.1.1.平面及断面形状为直线时,制件末端距凹模圆角R切点3mm,如下图2.1.2.翻边线为折曲线时,在冲压方向上保证翻边行程L不变。
2.1.3.翻边凸缘宽度不等时,按照翻边宽度最宽处考虑,压入深度沿冲压方向同时开始翻边。
制定部门制定日期制定审定批准版次发行部门2.1.4.折弯线和翻边在同一条线上时➢折弯部比翻边高度深时,L>l1压入深度取L值。
➢翻边高度超出折弯线时,压入深度渐渐变化。
➢立斜面上的翻边,由于凹模运动方向与翻边方向有较大的相对滑动(其中凹模突出点与制件相对滑动的距离A最大,较缓斜面处的距离B最小),故凹模突出点至较缓斜面点之间的凹模口压入深度应设计成渐变。
制定部门制定日期制定审定批准版次发行部门➢凹模端部弧度大的情况下,如图所示加出余量:➢翻边线变化大,一个冲压方向不能成形,要分成两序完成,两序相接处最少要重合40mm。
制定部门制定日期制定审定批准版次发行部门2.2.压件器工作行程计算C=A+α+βC:压件器工作行程A:翻边行程α:10mm(空行程)β:凹模镶块与冲压件接触时的干涉量制定部门制定日期制定审定批准版次发行部门2.3.翻边顶出器的行程决定翻边顶出器工作行程的设定原则上为确保压件器脱开冲压件后才允许翻边顶出器工作。
2.3.1.采用刚性限位(见左图)S=L+B+CS:翻边顶出器的行程L:制件翻边高度B:5-10mm(余量)C:压件器工作行程2.3.2.采用弹性限位(见右图)➢适用于翻边顶出器的行程较大的场合。
➢弹簧B弹力需大于弹簧A的弹力。
➢弹簧A和弹簧B的行程应一致。
S=12(B+C)+LS:翻边顶出器的行程L:制件翻边高度B:5-10mm(余量)C:压件器工作行程制定部门制定日期制定审定批准版次发行部门制定部门 制定日期 制定 审定 批准 版次 发行部门 3. 凸模托料面的设计 3.1. 托料面的结构尺寸形状翻边部 整形部曲率变化平坦 外板 ≥60 ≥70 内板 ≥40 ≥50 变化小外板 ≥70 ≥80 内板 ≥50 ≥60 变化大外板 ≥90 ≥120 内板≥70≥90➢ 托料面设计时,应注意方便制件的取放。
➢ 不会引起制件变形的部分,可沿形空开10mm (见下图左)。
➢ 压料面的符型区应与托料面对应,可比凸模托料面小5-10mm (见上图右)。
➢ 在产生回弹的部位,压件器不要让开。
3.2.凸模托料面不能挖空的情况➢整形或二次拉深时,凸模不要挖空,如下图:➢狭窄的件和狭窄的部位不要挖空。
➢制件回弹大与模面不符型时不要挖空。
3.3.应预测翻边整形时的压料效果,必要时,应加大相应的托料面和压料面。
4.压件器的强度设计4.1.压件器的材料一般为HT250,需用压件器成形时材料为HT300或合金铸铁。
4.2.有推力作用于压件器上时,要注意刚性,图为厚度最薄尺寸(铸铁件时)4.3.强度弱时采用铸钢或增设钢质镶块。
4.4.压件器需墩死时,其与上模的接触面应加大,断面面积小的部位的底面必须接触到底板;断面强度弱的部分,底面必须与底板接触。
制定部门制定日期制定审定批准版次发行部门4.5.压件器的导向➢大量生产时,顶出力大时使用导板➢顶出力小,少量生产时(但是,为方便制造时的调整,有时单侧必须用导板,推荐少采用)。
制定部门制定日期制定审定批准版次发行部门5.压件器与凹模分界的设定5.1.翻边圆角R≤1时:5.2.翻边圆角R>1时:5.3.倾斜的场合制定部门制定日期制定审定批准版次发行部门制定部门 制定日期 制定 审定 批准 版次 发行部门 5.4. 垂直翻边时(在制件外折角线分界):5.5. 整形翻边时不要在倾斜面上分块。
R >5时距切点2mm 分界;预想有回弹时,即使R ≤5,作为回弹对策,也可如上设计。
翻边圆角R ≤5,自折角线分界。
翻边圆角R>5,自切点以外分界。
6.翻边整形模刃口的种类及使用6.1.刃口的种类及淬火方法➢钢材类型:火焰淬火——7CrSiMnMoV;整体淬火——T10A、Cr12MoV➢分块类型:铸钢——铸CH-1;铸铁——HT250、HT300、球墨铸铁、钼铬合金铸铁➢整体类型:铸铁——HT300、球墨铸铁、钼铬合金铸铁6.2.采用规定6.3.翻边凹模设计6.4.翻边凹模标准形式6.4.1.铸造镶块形式➢B≥1.5*A➢A>60mm时设加强筋,凹模圆角需标注于模具图上。
6.4.2.钢材镶块形式➢一般B≥1.5*A。
➢A不小于40mm。
➢C及凹模R一定要在图纸中指出。
6.4.3.铸块+镶块形式➢B≥1.5*A。
➢凹模R一定要在图纸中指出。
制定部门制定日期制定审定批准版次发行部门➢螺孔不应透出有效型面。
6.4.4.凹模刃口➢标准刃口(即使翻边高度不同,刃口原则上也一样)制定部门制定日期制定审定批准版次发行部门➢倾斜刃口 A>B6.4.5.镶块及铸造镶块凹模的大小尺寸➢为了易于搬运及研合,单个镶块质量应小于30kg。
➢铸造镶块长度L≤450mm,锻造镶块L≤300mm。
6.4.6.凹模反侧➢反侧的设置标准:在压弯翻边中,受到很大的力时加反侧。
➢翻边(压弯)凹模除螺钉销钉固定外,还要设键。
制定部门制定日期制定审定批准版次发行部门➢翻边(压弯)凹模除螺钉销钉固定外,采用挡墙结构。
➢翻边(压弯)凹模除螺钉销钉固定外,采用直接反侧块。
6.5.凹模的分块6.5.1.凹模的分块分别取决于凹模形状、重量、长度及钳工配间隙工艺,具体如下述:制定部门制定日期制定审定批准版次发行部门➢为了制造容易,在平面上的直线部分块,在θº及R小时在R之切点以外的附近分块。
(以使钳工修角容易)➢翻边绫线为曲线时,原则上要在法线方向分块,但亦允许与切线成min70º,max110º的夹角分块。
➢凹模端头为尖角时,沿产品终止点加出a尺寸,改成图式形状。
A值(钢min15mm;铸铁min25mm)制定部门制定日期制定审定批准版次发行部门制定部门 制定日期 制定 审定 批准 版次 发行部门 ➢ 在断面形状上的镶块分块应避免出现特别的大的锐角。
A) 翻边线倾斜30º以下时:B) 翻边线倾斜30º以上时:➢ 凹模镶块必须有挡墙或止退键。
➢卸压件器需先卸凹模时,应在凹模上涂红漆,并在图上加以指示。
此种结构尽量不选用。
6.6.角部翻边凹模角部翻边,凹模磨损较严重,应注意以下事项:6.6.1.收缩翻边(收缩率15%以上),凹模角部镶钢口。
钢口镶块收缩率=(l-L)/l*100%根据型面起伏决定钢口镶块的结构形式:制定部门制定日期制定审定批准版次发行部门下图结构,翻边高不足10mm时,可以不要镶块钢口。
6.6.2.伸长翻边(伸长率15%以上),凹模工作表面需硬化处理。
伸长率=(L-l)/l*100%制定部门制定日期制定审定批准版次发行部门7.翻边顶出器的安装标准7.1.翻边顶出器的使用条件:配置翻边退料板时要考虑以下因素:➢制件转弯部位。
➢取得退料平衡的位置。
➢刚性好的部位。
➢封闭翻边时(封闭翻边长度在3mm以下,不是变薄翻边时,不设顶出器)。
➢翻边有夹件(包凸模)倾向时使用。
➢收缩翻边时使用。
➢伸长翻边时使用。
➢形状变化大时使用。
➢孔翻边(内圆翻边)时使用。
7.2.翻边顶出器的类型➢套筒式制定部门制定日期制定审定批准版次发行部门➢一体式➢气缸式(翻边不垂直时,使用这种形式)7.3.翻边顶出器的布置与方向翻边顶出器的布置由顶出器的使用条件及制件形状决定,应考虑如下事项:制定部门制定日期制定审定批准版次发行部门➢尽量在角部安装(角部夹件可能性较大);➢在平衡处安装(翻边顶出器的间隔max600mm);➢考虑在投入取出时没有干涉(考虑定位块);➢在制件刚性强的地方多设置;前挡泥板后挡泥板发动机罩外板后盖门外板前门外板后门外板行李箱外板制定部门制定日期制定审定批准版次发行部门8.退料块及定位块的形状8.1.退料块为确保翻边退件器同步退件,退料块形状与翻边形状线需吻合。
8.2.定位块➢A式➢B式能够采用凸模形状定位的,一般不使用定位块定位。
为防止定位块影响上件,在侧面一般设置B式定位块。
制定部门制定日期制定审定批准版次发行部门8.3.内缘翻边的翻边退料板制定部门制定日期制定审定批准版次发行部门9.翻边变形对策9.1.翻边分类。
➢直线翻边➢伸长翻边➢收缩翻边9.2.翻边变形分析➢直线翻边,翻的边部没有变形。
➢伸长翻边和收缩翻边其边部分有变形,由模具取出时,其形状会发生变化,这种变化不单是角度的变化,包括其棱线在内,形状整体部将起变化。
9.3.棱线变化防止对策➢在翻边处增设加强筋,增加其刚性。
➢不管是伸长翻边,还是收缩翻边,设法减少残留内应力。
9.4.具体翻边对策➢伸长翻边➢增加储料点,以补伸长量➢收缩翻边尽量向下多拉伸成形制定部门制定日期制定审定批准版次发行部门10.铸件壁厚设计类别 A B C D E F G H J K L M N S T①40 40 40 40 40 30 35 30 50 40 30 40 30 40 40②30 30 30 30 30 30 30 30 45 30 30 40 30 40 30 其它注:上表适用板料厚度t≤1.2mm的模具,料厚超出此范围的模具铸件壁厚酌情增加。