流化床制粒理论与实践
流化床制粒 沸腾制粒-概述说明以及解释
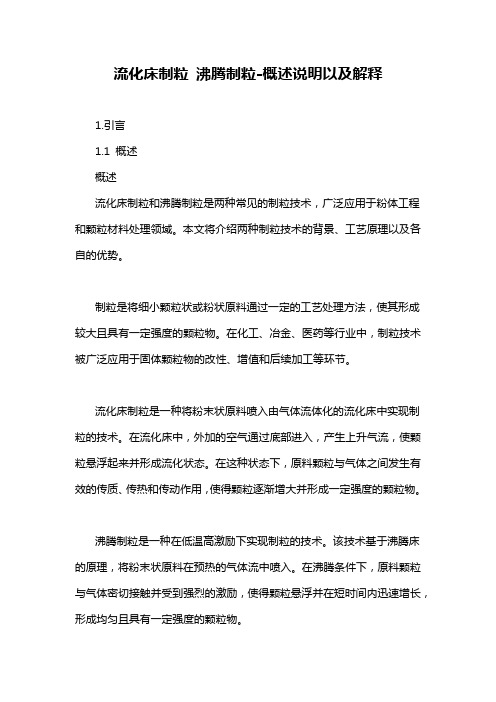
流化床制粒沸腾制粒-概述说明以及解释1.引言1.1 概述概述流化床制粒和沸腾制粒是两种常见的制粒技术,广泛应用于粉体工程和颗粒材料处理领域。
本文将介绍两种制粒技术的背景、工艺原理以及各自的优势。
制粒是将细小颗粒状或粉状原料通过一定的工艺处理方法,使其形成较大且具有一定强度的颗粒物。
在化工、冶金、医药等行业中,制粒技术被广泛应用于固体颗粒物的改性、增值和后续加工等环节。
流化床制粒是一种将粉末状原料喷入由气体流体化的流化床中实现制粒的技术。
在流化床中,外加的空气通过底部进入,产生上升气流,使颗粒悬浮起来并形成流化状态。
在这种状态下,原料颗粒与气体之间发生有效的传质、传热和传动作用,使得颗粒逐渐增大并形成一定强度的颗粒物。
沸腾制粒是一种在低温高激励下实现制粒的技术。
该技术基于沸腾床的原理,将粉末状原料在预热的气体流中喷入。
在沸腾条件下,原料颗粒与气体密切接触并受到强烈的激励,使得颗粒悬浮并在短时间内迅速增长,形成均匀且具有一定强度的颗粒物。
流化床制粒和沸腾制粒不仅具有相似的原理,而且在实际应用中也有很多共同之处。
它们都能够在较短时间内实现颗粒的快速增长和强度的提高,从而满足不同行业对制粒品质的要求。
此外,通过合理地选择原料和控制工艺参数,可以调节颗粒的形状、大小和物理性质,以满足特定的应用需求。
本文将详细介绍流化床制粒和沸腾制粒的工艺原理,并对两种制粒技术的优势进行比较分析。
通过深入了解这两种技术的特点和应用领域,可以为颗粒物的制备及应用提供一定的参考和指导。
1.2 文章结构文章结构部分内容如下:本文主要分为三个部分:引言、正文和结论。
引言部分首先概述了本文的主题——流化床制粒和沸腾制粒,并介绍了文章的结构。
随后,明确了本文的目的,即讨论和比较这两种制粒方法的背景、原理和优势。
正文部分分为两个小节,分别介绍了流化床制粒和沸腾制粒两种方法的背景介绍和工艺原理。
在背景介绍中,将简要介绍流化床制粒和沸腾制粒的发展历程,以及它们在工业领域的应用情况。
流化床制粒法

流化床制粒法
流化床制粒法是一种广泛应用于制药、化工、农药等领域的制粒技术。
它是利用流化床的气体动力学特性,将粉状或颗粒状原料在气流中不断翻滚、碰撞、摩擦,形成颗粒的过程。
流化床制粒法具有以下优点:
一、操作简单,易于控制。
流化床制粒法的操作过程相对简单,只需将原料加入流化床中,调整好气流速度和温度等参数,即可完成制粒过程。
而且,由于流化床内气体的搅拌作用,原料颗粒之间的接触面积大,容易形成均匀的颗粒。
二、颗粒质量好。
流化床制粒法可以控制颗粒大小和形状,从而得到质量稳定、均匀一致的颗粒产品。
此外,由于流化床内气体的搅拌作用,颗粒表面光滑,不易产生毛刺和裂缝等缺陷。
三、适用范围广。
流化床制粒法适用于各种类型的原料,包括粉状、颗粒状和液态原料。
而且,由于流化床内气体的搅拌作用,即使是易于聚集的粘性原料也可以得到良好的制粒效果。
四、生产效率高。
流化床制粒法可以实现连续生产,而且由于气体搅拌作用,原料颗粒之间的接触面积大,制粒速度快,生产效率高。
除了以上优点之外,流化床制粒法还有一些缺点。
例如,由于气体搅拌作用,制粒过程中会产生一定量的细小颗粒和粉尘,需要进行处理。
此外,在处理一些温度敏感或易挥发的原料时,需要控制好流化床内的温度和湿度等参数。
总之,流化床制粒法是一种具有广泛应用前景和发展潜力的制粒技术。
随着科技的不断进步和人们对高质量、高效率生产的需求不断提高,相信这种技术将会得到进一步的发展和应用。
流化床造粒技术浅析
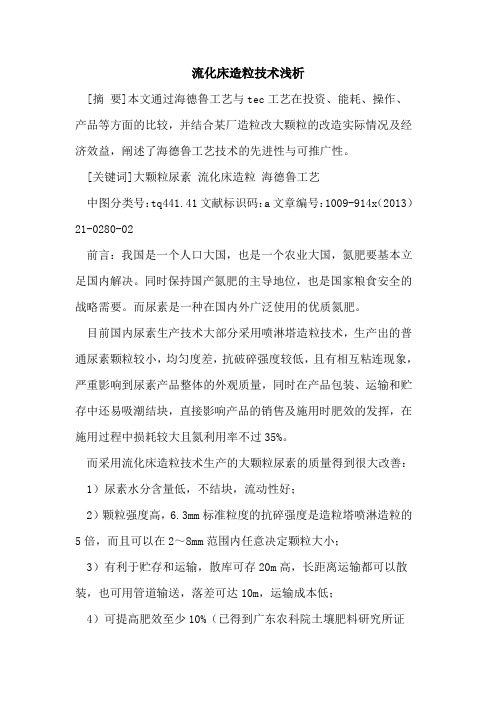
流化床造粒技术浅析[摘要]本文通过海德鲁工艺与tec工艺在投资、能耗、操作、产品等方面的比较,并结合某厂造粒改大颗粒的改造实际情况及经济效益,阐述了海德鲁工艺技术的先进性与可推广性。
[关键词]大颗粒尿素流化床造粒海德鲁工艺中图分类号:tq441.41文献标识码:a文章编号:1009-914x(2013)21-0280-02前言:我国是一个人口大国,也是一个农业大国,氮肥要基本立足国内解决。
同时保持国产氮肥的主导地位,也是国家粮食安全的战略需要。
而尿素是一种在国内外广泛使用的优质氮肥。
目前国内尿素生产技术大部分采用喷淋塔造粒技术,生产出的普通尿素颗粒较小,均匀度差,抗破碎强度较低,且有相互粘连现象,严重影响到尿素产品整体的外观质量,同时在产品包装、运输和贮存中还易吸潮结块,直接影响产品的销售及施用时肥效的发挥,在施用过程中损耗较大且氮利用率不过35%。
而采用流化床造粒技术生产的大颗粒尿素的质量得到很大改善:1)尿素水分含量低,不结块,流动性好;2)颗粒强度高,6.3mm标准粒度的抗碎强度是造粒塔喷淋造粒的5倍,而且可以在2~8mm范围内任意决定颗粒大小;3)有利于贮存和运输,散库可存20m高,长距离运输都可以散装,也可用管道输送,落差可达10m,运输成本低;4)可提高肥效至少10%(已得到广东农科院土壤肥料研究所证实);5)氮的利用率高,对水稻作物,为达到同一收获量,施用大粒尿素可节省用量1/3,氮素吸收率比普通尿素高出20%,肥效高,不挥发;在北美市场,流化床造粒比造粒塔喷淋造粒每吨价格高出5~10美元,成本约增加2~3美元。
在西欧市场高出10~15美元。
国际市场供大于求时,前者价格稳定,但后者价格下跌。
2010年全世界尿素生产能力约1.78亿吨,产量约1.65亿吨,总需求量1.56亿吨,其中大颗粒尿素的产量约7791万吨,已占当年世界尿素总产量的47.2%。
大颗粒尿素已逐渐成为国际市场的一个主流品种,市场份额高达47.2%。
流化床结晶造粒法

流化床结晶造粒法
流化床结晶造粒法是一种利用流化床技术进行颗粒结晶制备的方法。
在流化床结晶造粒过程中,通过将溶解的物质喷洒到固体颗粒床上,溶液或悬浮液中的溶质在固体床内迅速结晶形成颗粒,从而实现了颗粒的结晶造粒。
流化床结晶造粒法的关键是在流化床中同时实现溶液或悬浮液的供应、气固流化和结晶过程的有效耦合。
这种方法的主要优点是操作灵活、形成的颗粒分布均匀、产品质量稳定且可以实现连续生产。
流化床结晶造粒法在制药、化工等领域具有广泛的应用。
流化床结晶造粒法可以用于制备药物微球、饲料颗粒、肥料颗粒等产品。
同时,该方法还可以改善溶液中的反应条件、控制晶体尺寸分布并实现粒度调节,对于一些需要控制晶体尺寸分布和形态的工艺具有重要意义。
流化床技术及国内的应用

流化床技术及国内的应用流化床技术及国内的应用从流化床在国内制药工业应用的情况出发,分析了流化床在干燥、制粒、制丸、包衣方面的各自特点,同时也阐明了流化床技术发展方向。
流化床技术的应用较为广泛,其中最为广泛的应用技术为流化床干燥,流化床干燥又称沸腾干燥,使颗粒等物料呈沸腾状态,并在动态下进行热交换。
流化床技术因气—固两相大面积接触,其快速传热传质、温度梯度小的特性而被广泛运用于工业生产。
然而,制药工业运用流化床技术进行粉(粒)状物料干燥已有数十年的历史,20世纪末,由德国、日本、瑞士引进的流化床一步制粒机为我国固体制剂生产作出了革命性贡献。
近年来,流化床技术已溶入至干燥、制粒、药物包衣等领域。
1.流化床干燥机1.1间隙式流化床随着制药厂GMP改造工作的开展,带搅拌的流化床干燥机得到广泛的运用。
其特点:(1)床内设置搅拌,避免了死角及“沟流”现象;(2)设备结构简单,成本低,得以快速推广。
缺点:间隙式操作,批处理能力低。
同时,对粉尘含量高的干燥操作,过滤器阻力损失大,不能连续操作。
1.2连续式流化床干燥GMP改造促进了间隙式搅拌流化床的运用,但也在相当程度上将连续式流化床带入了误区,将其定位在清洗死角和交叉污染上,而几乎被遗忘。
连续式流化床却具有间隙式流化床无法比拟的优点:(1)连续进出料,适合大规模生产操作,同使用多台间隙式流化床相比,其无需移动料车,布局面积小;(2)动态下进料,避免了加料引起的压实、结块死角。
(3)易于与制粒机、振荡筛、整粒机构成连续生产线,实现封闭操作的物流系统。
随着GMP的深入,连续式设备会得以发展,但需要制药厂、药机工程设计人员向如下方向去深入研究:(1)湿粒加料,现行的压板加料伴随密封不严的现象,而星形加料未解决对粒的挤压、变形甚至粘连的问题。
由此看来,开发密闭性良好的分散加料装置势在必行;(2)清洗死角的问题,传统的过滤角以圆弧过度,舌形多孔板代替直孔板,不积料视窗应得以贯彻;(3)CIP方面,在设备可扩展分离室,流化床进风系统设置CIP清洗,避免交叉污染。
流化床设备的操作实习报告
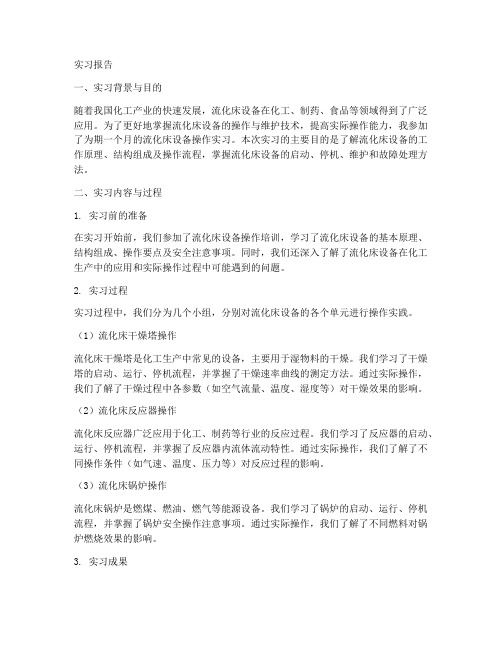
实习报告一、实习背景与目的随着我国化工产业的快速发展,流化床设备在化工、制药、食品等领域得到了广泛应用。
为了更好地掌握流化床设备的操作与维护技术,提高实际操作能力,我参加了为期一个月的流化床设备操作实习。
本次实习的主要目的是了解流化床设备的工作原理、结构组成及操作流程,掌握流化床设备的启动、停机、维护和故障处理方法。
二、实习内容与过程1. 实习前的准备在实习开始前,我们参加了流化床设备操作培训,学习了流化床设备的基本原理、结构组成、操作要点及安全注意事项。
同时,我们还深入了解了流化床设备在化工生产中的应用和实际操作过程中可能遇到的问题。
2. 实习过程实习过程中,我们分为几个小组,分别对流化床设备的各个单元进行操作实践。
(1)流化床干燥塔操作流化床干燥塔是化工生产中常见的设备,主要用于湿物料的干燥。
我们学习了干燥塔的启动、运行、停机流程,并掌握了干燥速率曲线的测定方法。
通过实际操作,我们了解了干燥过程中各参数(如空气流量、温度、湿度等)对干燥效果的影响。
(2)流化床反应器操作流化床反应器广泛应用于化工、制药等行业的反应过程。
我们学习了反应器的启动、运行、停机流程,并掌握了反应器内流体流动特性。
通过实际操作,我们了解了不同操作条件(如气速、温度、压力等)对反应过程的影响。
(3)流化床锅炉操作流化床锅炉是燃煤、燃油、燃气等能源设备。
我们学习了锅炉的启动、运行、停机流程,并掌握了锅炉安全操作注意事项。
通过实际操作,我们了解了不同燃料对锅炉燃烧效果的影响。
3. 实习成果通过实习,我们掌握了流化床设备的基本操作技能,能够独立完成流化床干燥塔、反应器、锅炉等设备的启动、运行、停机及维护工作。
同时,我们了解了流化床设备在实际生产中的应用,为今后的工作打下了坚实基础。
三、实习总结与体会本次实习让我们对流化床设备有了更深入的了解,掌握了实际操作技能。
在实习过程中,我们学会了如何分析并解决操作过程中遇到的问题,提高了自己的动手能力。
流化床及管道系统简介
流化床及管道系统简介近年来,由于医药行业面临的GMP认证,流化床制粒在我国药厂已得到普遍应用。
制粒的过程是将生产用原辅料装在移动式容器中,通过液压提升机或真空上料机送至高剪切混台制粒机里,粘合剂通过喷枪加到里面,制粒完成后通过出料系统流动至安装在湿法制粒机上的湿整粒机进行整粒,物料通过重力和流化床本身的负压抽进流化床进行干燥;干燥完后通过提升翻转或大功率真空出料机转移到干整粒机里整粒,然后物料再流到物料桶或可移动混粉料斗里,而后就可送去混粉、压片或分装等。
流化床制粒原理:在流化床制粒机中,压缩空气和混合剂溶液按一定比例由喷嘴雾化并喷至流化床层上正处于流化状态的物料粉末上。
首先液滴使接触到的粉末润湿并聚结在其周围形成粒子核,同时再由继续喷入的液滴落在粒子核表面上产生黏合架桥作用,使粒子核与粒子核之间、粒子核与粒子之间相互结合,逐渐形成较大的颗粒。
干燥后,粉末间的液体桥变成固体桥,即得外形圆整的多孔颗粒。
因流化床制粒全过程不受外力作用,仅受床内气流影响,故制得的颗粒密度小,粒子强度低,但颗粒的粒度均匀,流动性、压缩成形性好。
流化床工艺流程PID图流化床剖面图(1)流化床剖面图(2)进口流化床用气点比较多,上图为流化床各点位压缩空气控制阀,业主要求阀门设在吊顶以下方便操作的位置(离地1350mm处)。
流化床进风管路上的各测点比较多,具体位置由老外定位,在相应位置我们要加上丝头,调试时将检测仪表安装。
设备排水点及进风进风口均需要可拆卸的法兰接或者是卡盘接软管连接设备硬管固定支架管路中的监测点全为卡盘式快接头反吹扫设备方口与圆管道连接处需加工天圆地方管道与设备接口往往不是国标法兰,需要测量定制流化床配套的真空系统加工的天圆地方及与设备相连的软管流化床排风室管道布置实际生产中应注意的问题:实际生产中,有时会出现起团或塌床的问题,可能是黏合剂的流速和浓度过大,湿颗粒来不及干燥相互粘连在一起所致,也可能是流化床制粒机中相对湿度太大,超过了颗粒本身的临界相对湿度所致,可降低黏合剂流速,在其中加入水或乙醇以降低黏度,同时应该适当加大流化风量并提高进口温度。
中药流化床制粒技术的应用与发展
锅内 滚动吹干, 并用W号树脂PEG 乙 醇溶液进行包
衣, 可很好解决颗粒的吸湿问题U sl0
4 讨论 上述介绍为目 前常见的中药流化床制粒工艺的应
的浓缩浸膏喷雾, 使其在母核上附聚、 干燥成粒。可用 于作母核的辅料常选用 120 目 蔗糖粉、 一 p 环糊精、 磷
酸氢钙粉 、 滑石粉 、 微球硅胶 、 甘露醇、 、 一 乳糖 a 淀粉
而粗, 但CRH值低, 不利于长期保存, 需要好的 包装材
料160 11 对于无糖型颗粒的包装材料需特别强调, 一般的
分, 提高了成品的稳定性, 效果良 好。在花针感冒颗粒 剂的离心浓缩液中加人 巧 %的白糊精, 80℃ 在 将其溶 解, PGL- l0A 型喷雾干燥机即可消除粘壁现象, 用 得
到合格的干燥颗粒。 尽量降低干浸膏粉的粘滞性和引湿性, 严格控制
粘合剂雾化液滴过大, 或喷雾频率过高等;工艺设计
不合理}习 , 。
3.1.2 防止 “ 塌床” 的方法
对于不同的处方、 不同的中 药成分, 在操作中 可以 根 实际情况, 采取措施来预防和解决 “ 塌床” 现
象。
中 药 应 与 测 :0 6年 2期 43 国物 用 监 0 第
中药专题
我们将吸附澄清— 高速离心沉降这两种提取分 离技术结合起来, 用于颗粒剂的煮提制备工艺中, 该
【 作者简介] 张燕平, 副主任药师, 女, 主要从事中药制剂 面研究
上海中 药二厂采用流化喷雾干燥制粒技术改进银 翘片 工艺, 不但减少了 制粒工序, 而且制得的 颗粒疏松,
TEL: ( 010 )66937426
42 中 药 应 与 测 2 0 年 2期 国 物 用 监 0 “第
中药专题
呈多孔状, 压片后硬度高, 崩解快, 提高了片剂质量 0 加人适量的甜蜜素和糊精作为辅料, 运用喷雾干 燥法制备,制得脑心康无糖颗粒剂,经 TLC 定性 、
简述流化床制粒的基本原理
简述流化床制粒的基本原理
流化床制粒是一种常用的固体颗粒制备技术。
其基本原理是将颗粒物料置于流化床中,通过对床层施加适当的气体流速,使颗粒床形成一种类似流体的状态。
在这个状态下,颗粒物料能够均匀地受到气体的搅拌和冲击,从而实现颗粒的制备和调控。
在流化床制粒中,气流起到了重要的作用。
通过调节气流的流速和流量,可以控制颗粒床的压力、温度、湿度等参数,进而影响颗粒的形态和性质。
通常采用的气流有空气、氮气等,可以选择性地调节床内的气氛,以满足不同颗粒制备的要求。
流化床制粒适用于较小的颗粒物料(一般在100微米至5毫米之间),可用于制备颗粒、粉末涂层、催化剂、微胶囊等。
它具有制备效率高、颗粒均匀、操作灵活等优点。
同时,通过调节气流参数,还可以实现颗粒的粒径、密度、形状等的调控。
流化床制粒机工作原理
流化床制粒机工作原理流化床制粒机是一种常见的粉体处理设备,广泛应用于化工、医药、食品等行业。
它是一种以流化床技术为基础的制粒设备,通过将颗粒物料悬浮在气体流中,利用气体的剪切、冲击和颗粒之间的碰撞来实现粒径的增大和颗粒形状的改变。
流化床制粒机的工作原理可以简单概括为以下几个步骤:1. 预处理:将需要制粒的物料进行预处理,如研磨、混合等,以提高物料的流动性和均匀性。
2. 进料和气体注入:物料和气体通过进料装置分别注入到流化床制粒机中。
物料通过进料装置均匀地分布在流化床内,而气体则通过气体注入装置注入到床体底部,形成了气体流动的床层。
3. 流化床形成:随着气体的注入,床层内的物料开始流动并逐渐形成流化床。
在流化床中,物料受到气体流动的作用,呈现出类似于液体的流动性质,即颗粒之间相互悬浮并不断运动。
4. 颗粒增大:在流化床中,物料颗粒之间的碰撞和气体的冲击作用下,颗粒逐渐增大。
当物料颗粒较小时,气体流动的剪切力会使颗粒不断互相碰撞,从而使颗粒逐渐增大。
5. 颗粒形状改变:在流化床中,物料颗粒之间的碰撞和气体的冲击作用下,颗粒的形状也会发生变化。
例如,颗粒可能会变得更加圆滑或均匀,从而改善物料的流动性和可处理性。
6. 收集和分离:经过一定时间的处理,物料颗粒达到所需的粒径和形状后,会被收集和分离出来。
一般情况下,收集和分离设备会根据颗粒的大小和密度进行分类,以便得到符合要求的制粒产品。
流化床制粒机的工作原理基于流化床技术,利用气体流动和颗粒之间的碰撞来实现颗粒的增大和形状的改变。
它具有制粒效率高、操作方便、粒径分布均匀等优点,被广泛应用于颗粒制备过程中。
流化床制粒机通过将物料悬浮在气体流中,利用气体的剪切、冲击和颗粒之间的碰撞来实现颗粒的增大和形状的改变。
它是一种高效的粉体处理设备,广泛应用于化工、医药、食品等行业,对于提高产品质量和生产效率具有重要意义。
- 1、下载文档前请自行甄别文档内容的完整性,平台不提供额外的编辑、内容补充、找答案等附加服务。
- 2、"仅部分预览"的文档,不可在线预览部分如存在完整性等问题,可反馈申请退款(可完整预览的文档不适用该条件!)。
- 3、如文档侵犯您的权益,请联系客服反馈,我们会尽快为您处理(人工客服工作时间:9:00-18:30)。
流化床制粒理论与实践
流化床制粒理论
流化床制粒混合工艺特别适合粒径范围在50-200μm的物料。
颗粒的流化行为是各种颗粒之间作用力和相互作用力的总和。
当经过料床的气流足够大时,颗粒克服重力得以流化。
在低的进风速度下,颗粒的运动速度与流化床内压降成正比。
随着进风速度的增加,流化床内颗粒由静止变为悬浮,此时对应的气流速度为最小流化速度(Umf)。
最小流化速度在一步制粒工艺中是一个初级下限,随着制粒工艺的进行,最小流化速度应该是变化且逐渐增大的。
制粒工艺的流化速度应大于最小流化速度,这样才不会使粗细颗粒分离。
当流化速度高于最小流化速度时,流化床内物料运动很像剧烈沸腾的液体,料床底部有气泡(在接近流化床床底的地方形成,靠近气流分布板),并在风机的作用下迅速上升至表面破裂。
也由此可知气流分布板的设计对流化床的特性有重大影响。
随着流化速度的增加,粉体体积膨胀,床体内单位体积内的颗粒密度降低。
当流化速度达到某一速度时便会将颗粒吹走,此时的速度被称为夹带速度。
流化床制粒混合程度与粒径和气流通过物料的运动方式有关。
气流运动方式影响气体与颗粒之间传热。
标准进风速度通常为1.0~2.0m/s。
对于聚团的物料,所需的空气流速为最小流化速度的五到六倍。
干燥需要低速,如0.8-1.4m/s。
由于流化床内存在湿物料,因此在干燥的早期阶段需要较高的速度,但通常会在产品失去水分时降低风速,目的是保证颗粒良好的运动且防止物料进入过滤器。
在流化床制粒工艺中,颗粒运动和快速干燥很重要。
颗粒在流化床观察孔自由向下流动是比较好的制粒状态,也可以通过出风温度监测不好的流化状态。
每个产品都有恒定的干燥速率,其中流化床内温度在相当长的一段时间内保持相对恒定。
如果出风温度上升速率比预期的快,则表明流化状态不好,可能必须停止制粒,并且需要手动或机械干预来辅助流化。
颗粒聚集与生长机理
聚集是以细颗粒为起始物料增大粒度的过程,颗粒生长主要有三种机制:
1.由于颗粒表面存在不流动的液体而形成粘结液桥,可以促进细颗粒的粘结;
2.存在界面力和毛细管压力使得颗粒变得紧实;
3.由于干燥过程中溶解物质的结晶而形成固体桥。
理想状态下,流化床内的初级颗粒经过喷雾区时与润湿剂雾滴接触,润湿剂在颗粒表面扩散润湿颗粒。
同时颗粒之间相互撞击形成液桥,而后在流化床内部干燥固化形成颗粒。
流化床制粒机理见下图。
影响流化床制粒工艺的因素可分为三大类:处方相关变量、设备相关变量及工艺相关变量。
处方相关变量:一步制粒理想的起始物料应该具有低密度(密度差异小)、粒径小、粒度分布范围窄、接近球形。
物料的内聚力、静
电、粒度分布、结晶或无定形性质以及润湿性等会影响颗粒的性质。
当制剂物料中含有疏水性物料或亲水性物料与疏水性物料的混合物时会出现流化困难。
混合物的疏水性增加,导致颗粒的生长减少。
可以通过添加表面活性剂(如月桂硫酸钠、SDS)改善疏水性物料一步制粒的效果。
粘合剂:不同的粘合剂具有不同的粘结性质,粘合剂的类型、制剂中的粘合剂用量和粘合剂的浓度对颗粒性质具有重大影响。
粘合剂的加入方式也会影响颗粒性质,有研究发现将粘合剂内加用乙醇制粒,颗粒的粒度更大,但当把粘合剂加入溶液中制粒的颗粒不易碎且流动性好。
粘合剂的温度影响溶液的黏度,进而影响液滴的大小。
粘合剂溶液温度升高,溶液的黏度降低,从而减小了液滴的粒径,因此制得的颗粒平均粒径较小。
粘合剂溶液的黏度和浓度会影响粘合剂雾滴的大小。
粘合剂黏度增加,形成的雾滴更大,制得的颗粒粒径更大。
设备相关变量:由于随机流化而发生的聚集和磨损,需要在制粒过程中控制颗粒。
这是一个复杂的过程,因为主要的流化条件和粒度分布在此过程中会发生变化。
当经过调节的空气通过流化床的下部气室引入时,给定体积的空气的流化速度决定了如何实现流化。
气流分布板提供了向产品供应空气的合适方法。
主要通过其开孔面积百分比来识别。
通常可以使用开孔面积为4%到30%的气流分布板。
这些可互换的气流分布板或具有可调节开孔的气流分布板可以提供一定范围的装载能力,从而可以高效、均匀地生产。
为了防止窜动,操作员可以选择具有最佳提升性能的气流分布板。
具有小的开孔面积来产生足够大的压降的气流分布板可以保证产品均匀流化,不会堵塞过滤器。
或者可以使用具有较大开孔面积的气流分布板将具有较高堆密度的产品进行流化处理。
流化床的几何形状是可能影响制粒工艺的因素。
流化速度必须从流化床底部到顶部边缘下降一半以上,以防止较小的较轻的颗粒被吹到过滤器中,从而与流化床中较重的产品分离。
通常圆锥形的容器与膨胀室是优选的,其中气流分布板横截面直径与容器顶部的直径之比为1:2。
工艺相关的变量:流化床制粒工艺是动态过程,其中通过喷枪产生雾滴并将其沉积在随机流化的颗粒上。
粘合剂溶剂蒸发,留下粘合剂。
在所有溶剂蒸发之前,其他无规则颗粒与潮湿颗粒接触粘结。
将该工艺重复多次以产生所需的颗粒。
有许多控制制粒的工艺变量。
最重要的工艺变量有:工艺的进风温度、雾化压力、空气流化速度和体积、喷液速度、喷枪的位置和喷枪的数量、物料温度和出风温度、过滤器的孔隙率和反吹频率、流化床体积。
这些工艺参数是相互依存的,如果可以理解这种相互依存的关系,则可以生产出所需的产品。
进风温度取决于粘合剂载体的选择及所形成的颗粒的热敏感性。
通常水性溶液允许使用进风温度范围60℃-100℃。
有机溶剂需要使用50℃至低于室温的进风温度。
较高的进风温度将粘合剂溶剂迅速蒸发,将形成较小的易碎的颗粒。
重要工艺变量及其对流化床制粒工艺的影响见下表。
流化床制粒工艺是一个稳健的工艺,必须对所有关键工艺参数进行精确的可重复性控制。
需要有效而可靠的工艺控制工具来确保最终产品的质量。