流化床一步制粒法的工艺优化
一步制粒机工作性能的要求有哪些
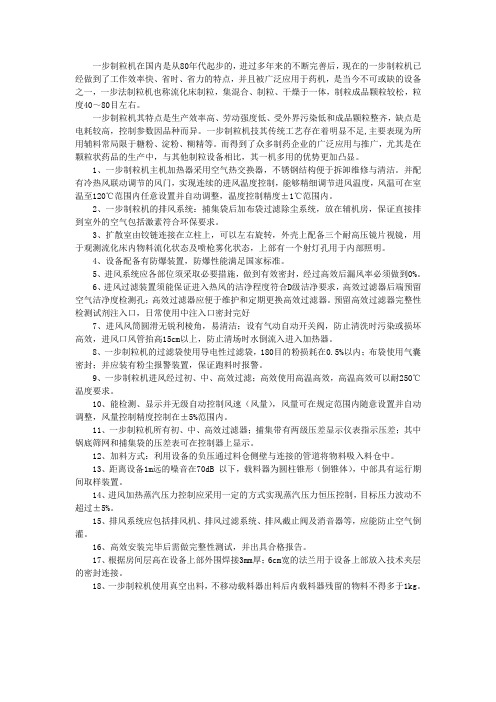
一步制粒机在国内是从80年代起步的,进过多年来的不断完善后,现在的一步制粒机已经做到了工作效率快、省时、省力的特点,并且被广泛应用于药机,是当今不可或缺的设备之一,一步法制粒机也称流化床制粒,集混合、制粒、干燥于一体,制粒成品颗粒较松,粒度40~80目左右。
一步制粒机其特点是生产效率高、劳动强度低、受外界污染低和成品颗粒整齐,缺点是电耗较高,控制参数因品种而异。
一步制粒机技其传统工艺存在着明显不足,主要表现为所用辅料常局限于糖粉、淀粉、糊精等。
而得到了众多制药企业的广泛应用与推广,尤其是在颗粒状药品的生产中,与其他制粒设备相比,其一机多用的优势更加凸显。
1、一步制粒机主机加热器采用空气热交换器,不锈钢结构便于拆卸维修与清洁。
并配有冷热风联动调节的风门,实现连续的进风温度控制,能够精细调节进风温度,风温可在室温至120℃范围内任意设置并自动调整,温度控制精度±1℃范围内。
2、一步制粒机的排风系统:捕集袋后加布袋过滤除尘系统,放在辅机房,保证直接排到室外的空气包括激素符合环保要求。
3、扩散室由铰链连接在立柱上,可以左右旋转,外壳上配备三个耐高压镜片视镜,用于观测流化床内物料流化状态及喷枪雾化状态,上部有一个射灯孔用于内部照明。
4、设备配备有防爆装置,防爆性能满足国家标准。
5、进风系统应各部位须采取必要措施,做到有效密封,经过高效后漏风率必须做到0%。
6、进风过滤装置须能保证进入热风的洁净程度符合D级洁净要求,高效过滤器后端预留空气洁净度检测孔;高效过滤器应便于维护和定期更换高效过滤器。
预留高效过滤器完整性检测试剂注入口,日常使用中注入口密封完好7、进风风筒圆滑无锐利棱角,易清洁;设有气动自动开关阀,防止清洗时污染或损坏高效,进风口风管抬高15cm以上,防止清场时水倒流入进入加热器。
8、一步制粒机的过滤袋使用导电性过滤袋,180目的粉损耗在0.5%以内;布袋使用气囊密封;并应装有粉尘报警装置,保证跑料时报警。
一步制粒工艺的关键参数
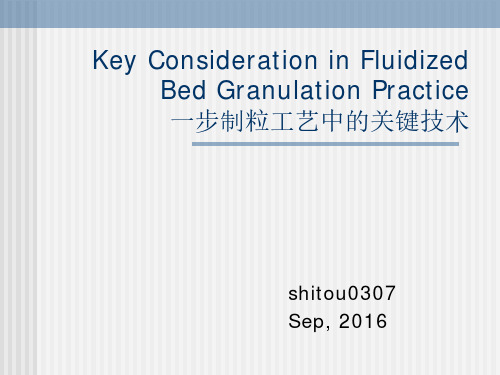
常见问题FAQ 讨论与持续学习 Discussion& Keep learning
Fluidized Bed Granulation
制粒的本质目的:改善物料粉体学特性; 常见制粒方法:湿法制粒,干法(辊压),一步制粒, 喷雾干燥,熔融挤出等; 一步制粒在制药工 艺中的地位? 为何会选择一步制 粒?
Introduction
Process
FAQ
Discussion
常见问题FAQ
Q8.湿法制粒和流化床制粒工艺互换?
单从工艺角度讲,这种转化一般是能实现的,但是需要特别注意用流化床和湿法 制粒机制备的粉体学性质会有差异(5th Slide),比如堆密度,一般会相差 0.2g/ml,还有就是湿法制粒的处方转化为流化床制粒后,处方可能需要适当调 整,如粘合剂。 一般不推荐采用等量递加混合均匀后再转入流化床中制粒,可以直接将药物溶解 或混悬于粘合剂中,采用雾化喷入,保证含量均匀。必要时要润洗容器,否则容 易导致含量偏低; 如果流化床制粒采用淀粉浆作为粘合剂,注意不要将热不稳定的药物直接加入到 热的淀粉浆中去; 这种案例其实是不建议用流化床制粒,但是如果一定需要采用该法,可以先在流 化床外混合均匀后转入流化床,运行后开始阶段采用较大的喷液速率和较小的风 量进行制粒。 Process FAQ Discussion
shitou0307 Sep, 2016
Topic Outlines
介绍 Introduction 工艺概况 Process Overview
设备,环境 Equipment, Environment 物料&处方 Material and formulation consideration 工艺控制与放大 Process Control and Scale up
流化床制粒技术介绍
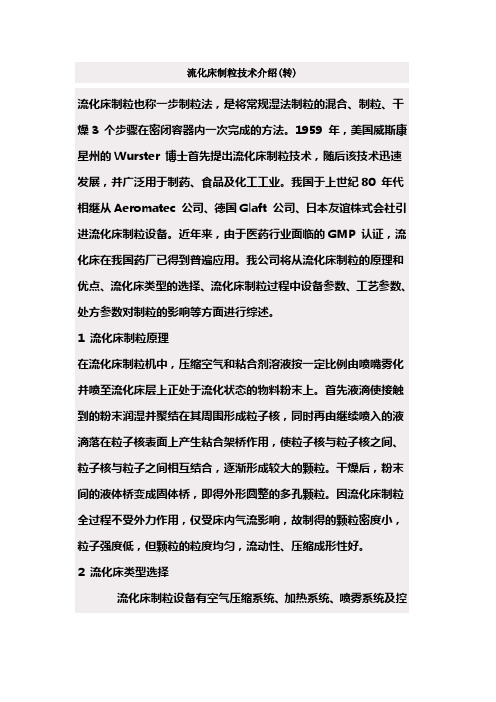
流化床制粒技术介绍(转)流化床制粒也称一步制粒法,是将常规湿法制粒的混合、制粒、干燥3 个步骤在密闭容器内一次完成的方法。
1959 年,美国威斯康星州的Wurster 博士首先提出流化床制粒技术,随后该技术迅速发展,并广泛用于制药、食品及化工工业。
我国于上世纪80 年代相继从Aeromatec 公司、德国Glaft 公司、日本友谊株式会社引进流化床制粒设备。
近年来,由于医药行业面临的GMP 认证,流化床在我国药厂已得到普遍应用。
我公司将从流化床制粒的原理和优点、流化床类型的选择、流化床制粒过程中设备参数、工艺参数、处方参数对制粒的影响等方面进行综述。
1 流化床制粒原理在流化床制粒机中,压缩空气和粘合剂溶液按一定比例由喷嘴雾化并喷至流化床层上正处于流化状态的物料粉末上。
首先液滴使接触到的粉末润湿并聚结在其周围形成粒子核,同时再由继续喷入的液滴落在粒子核表面上产生粘合架桥作用,使粒子核与粒子核之间、粒子核与粒子之间相互结合,逐渐形成较大的颗粒。
干燥后,粉末间的液体桥变成固体桥,即得外形圆整的多孔颗粒。
因流化床制粒全过程不受外力作用,仅受床内气流影响,故制得的颗粒密度小,粒子强度低,但颗粒的粒度均匀,流动性、压缩成形性好。
2 流化床类型选择流化床制粒设备有空气压缩系统、加热系统、喷雾系统及控制系统等组成。
主要结构由容器、空气分流板、喷嘴、过滤袋、空气进出口、物料排出口等组成。
按其喷液方式的不同分为3 类:顶喷流化床、转动切喷流化床、底喷流化床。
流化床制粒一般选择顶喷流化床。
近年来,为了发挥流化床制粒的优势,亦出现了一系列以流化床为母体的多功能复合型制粒设备。
如我公司新推出的多功能流化床、搅拌流化制粒机、转动流化制粒机、搅拌转动流化制粒机等。
现我们仅就流化床制粒进行探讨。
3 流化床制粒的优点尽管流化床制粒受到诸多因素影响,但与其他制粒方式相比,该技术仍具有很多优点。
a .物料的干混、湿混、搅拌、颗粒成型、干燥都在同一台流化床设备内完成,减少了大量的操作环节,节约了生产时间。
流化床制粒经验分享之工艺篇

流化床制粒经验分享之工艺篇流化床制粒也被称做沸腾制粒或一步制粒,是将物料一次投入到密闭的容器内,在容器内将物料进行均匀的混合、再通过设备将粘合剂均速喷入,让粘合剂与物料充分混合,在容器内进行流动,形成小颗粒,通过底端送入热风,收集成品干颗粒的技术。
流化床整个制粒过程主要分为四个步骤:物料预热、喷液、干燥和冷却。
业内根据流化床制粒经验,现将分享的制粒经验工艺篇如下:物料预热业内表示,其实在物料预热之前还有空机预热其的主要目的有两个:一是流化床开机初始的进风风量一般都不稳定,通过空机预热让设备运行一定时间后可以保证该参数趋于稳定,避免参数不稳定对后面物料预热造成不利影响;二是通过机器预热,可以大大减少物料预热时间,提率。
物料预热阶段的参数设置建议:由于开始物料细粉率极高、静电也比较大,建议在保证物料流化状态下采用较低的进风风量,流化床的抖袋频率尽可能高一点;以物料温度作为程序的跳转点,跳转点的物料温度因产品性质和生产批量的不同略有不同,一般是在45-50度。
喷液业内建议,在每次进行流化床制粒之前,特别是使用一种粘合剂时,先进行喷液测试,记录喷液曲线,即蠕动泵上的标示数对应的喷液速率;观察在设定的雾化压力下粘合剂的雾化状态,判断标准:雾化喷液时,手掌与喷液方向垂直快速穿过整个喷液面,以手掌上没有明显湿润感为宜。
喷液阶段的参数设置建议:喷液开始阶段,物料的粒径逐渐由小变大,为了保证流化状态,可以对进风风量进行相应调整(风量由小到大);过滤袋的抖袋频率开始喷液时可以设置相对较高,等物料逐渐成颗粒时可以降低抖袋频率和时间。
喷液阶段一般是以时间为跳转点。
如果是处于工艺摸索阶段,建议定时从流化床取样口取样,观察颗粒状态,特别是要防止颗粒过湿。
另外,为了保证颗粒质量同时提高生产效率,建议将整个喷液过程分为若干个(一般为2-3个)喷液速率进行梯度制粒。
定时记录系统相关参数(包括了进风风量、进风温度、排风温度、物料温度、喷液速率、雾化压力、物料压差、过滤袋压差、过滤袋抖袋频率和时间等),一个好的流化床工艺在每个喷液速率梯度下均会有平台期,即上述所有的参数均保持稳定。
流化床制粒工艺开发及优化探讨

流化床制粒工艺开发及优化探讨摘要:流化床制粒作为改善粉体不良性质的主要制粒方法,由于其工艺环节少,颗粒均匀、可压性好等特点,近年来在制药工业中备受关注。
本文就流化床技术的特点、基本理论和工艺优化等方面进行了较为详细的阐述。
关键词:流化床制粒;基本理论;工艺优化;前言流化床制粒也叫一步制粒,主要是将常规湿法制粒的混合、制粒、干燥三个步骤在密闭容器内一次完成的方法。
我国于上世纪80年代引进流化床制粒设备,近年来在我国已得到普遍应用[1]。
根据喷液方向与物料运动方向的不同,可将流化床分为三类:顶喷流化床、底喷流化床、切线喷流化床。
三种流化床构造的不同使它们具有不同的工艺用途。
其中顶喷流化床制粒广泛用于粉体的制粒工艺,本文将对其基本原理、变量控制和优化等方面进行介绍。
1 流化制粒基本理论流化床制粒首先通过吹入热空气将物料在流化状态下混合,对其再喷入制粒所用的粘合剂溶液,直到达到符合要求的润湿量或颗粒大小,然后对湿颗粒进行干燥到预定的温度或干燥失重。
下面将详细介绍粒子在流化床内流化、聚集成长的过程和理论。
1.1 粒子流化理论流化床操作过程是由热空气向上通过装载固体物料的床体。
空气影响流化状态的机理已经被很多研究者讨论过[2]。
在低气体流速下,粒子床是一个固体床,压力差与表观速度成正比。
随着气体流速的增加,达到粒子床从固定粒子到流化粒子转变的临界点。
当气体流速增大,通过床的压力差也增大,直到在特定流速时粒子的摩擦力等于床体的有效重量。
当气体流速逐渐增加,粒子床开始膨胀,高度逐渐增加,而压力差只有轻微的增大。
在一定的流化速度下,粒子被气体携带,这种现象称为“夹带”。
当进风速度足够大时,粒子床上表面界限逐渐模糊,夹带更为显著,粒子被气流带离流化床。
影响流化状态的因素包括:①进风速度;②空气分配板孔径和直径;③粒子的大小和密度;④物料含湿量;⑤流化床直径/高度比。
其中,进风速度是影响流化状态的最主要因素。
1.2 粒子聚集理论聚集是粒子长大的过程。
流化床制粒理论与实践

流化床制粒理论与实践流化床制粒理论流化床制粒混合工艺特别适合粒径范围在50-200μm的物料。
颗粒的流化行为是各种颗粒之间作用力和相互作用力的总和。
当经过料床的气流足够大时,颗粒克服重力得以流化。
在低的进风速度下,颗粒的运动速度与流化床内压降成正比。
随着进风速度的增加,流化床内颗粒由静止变为悬浮,此时对应的气流速度为最小流化速度(Umf)。
最小流化速度在一步制粒工艺中是一个初级下限,随着制粒工艺的进行,最小流化速度应该是变化且逐渐增大的。
制粒工艺的流化速度应大于最小流化速度,这样才不会使粗细颗粒分离。
当流化速度高于最小流化速度时,流化床内物料运动很像剧烈沸腾的液体,料床底部有气泡(在接近流化床床底的地方形成,靠近气流分布板),并在风机的作用下迅速上升至表面破裂。
也由此可知气流分布板的设计对流化床的特性有重大影响。
随着流化速度的增加,粉体体积膨胀,床体内单位体积内的颗粒密度降低。
当流化速度达到某一速度时便会将颗粒吹走,此时的速度被称为夹带速度。
流化床制粒混合程度与粒径和气流通过物料的运动方式有关。
气流运动方式影响气体与颗粒之间传热。
标准进风速度通常为1.0~2.0m/s。
对于聚团的物料,所需的空气流速为最小流化速度的五到六倍。
干燥需要低速,如0.8-1.4m/s。
由于流化床内存在湿物料,因此在干燥的早期阶段需要较高的速度,但通常会在产品失去水分时降低风速,目的是保证颗粒良好的运动且防止物料进入过滤器。
在流化床制粒工艺中,颗粒运动和快速干燥很重要。
颗粒在流化床观察孔自由向下流动是比较好的制粒状态,也可以通过出风温度监测不好的流化状态。
每个产品都有恒定的干燥速率,其中流化床内温度在相当长的一段时间内保持相对恒定。
如果出风温度上升速率比预期的快,则表明流化状态不好,可能必须停止制粒,并且需要手动或机械干预来辅助流化。
颗粒聚集与生长机理聚集是以细颗粒为起始物料增大粒度的过程,颗粒生长主要有三种机制:1.由于颗粒表面存在不流动的液体而形成粘结液桥,可以促进细颗粒的粘结;2.存在界面力和毛细管压力使得颗粒变得紧实;3.由于干燥过程中溶解物质的结晶而形成固体桥。
制粒技术详述
· 粘合剂的雾化多采用有气喷雾,雾化的程度是喷嘴内空 气和液体混合的比例来决定的,雾化空气压力增大,则 空气比例增加,易使粘合剂形成细雾,降低对粉末 的 湿润能力,所得颗粒粒径小、脆性大,而松密度和 流 动性则不受影响。但雾化压力过高会改变流化状态,使 气流紊乱,粉粒在局部结块;
· 2. 捕集袋安装完毕后,应检查带筒是否完全竖直向下,不得有倾斜和扭转, 否则物料易于聚集在捕集袋筒内;
· 3. 捕集袋整体安装到位后,方可打开“上密封”充气,否则会使其密封圈 充气膨胀爆裂,或密封不严密,生产过程中漏粉;
· 4. “上密封”打开后,切记将绞车反转两圈,否则生产过程中捕集袋振摇时 ,钢丝绳被拉断,此外,也不可将钢丝绳松得过多,否则钢丝绳易扭曲缠绕 ;
制粒技术
主要内容
· 一、制粒技术概念 · 二、制粒方法 · 三、流化床制粒(一步制粒)
一、制粒技术概念
· 制粒(granulation)技术:是把粉末、熔融液、 水溶液等状态的物料加工制成一定形状与大小的 粒状物的技术。
· 制粒的目的:①改善流动性,便于分装、压片; ②防止各成分因粒度密度差异出现离析现象;③ 防止粉尘飞扬及器壁上的粘附;④调整堆密度, 改善溶解性能;⑤改善片剂生产中压力传递的均 匀性;⑥便于服用,方便携带,提高商品价值。
· 温度过低,则湿颗粒不能及时干燥,相互聚结成大 的、潮湿的团块,也会造成塌床。
三、流化床制粒(一步制粒)
· 4. 湿度
· 在颗粒形成过程中,进风湿度大,则湿颗粒不能及时 干燥,易粘结粉料。当以易吸湿的中药浸膏粉为底料 时,若进风湿度大,往往可能在物料预热时就产生大 量结块,造成塌床。因此,应控制环境湿度,降低进 风空气的湿度。
· 3. 流化床制粒又称沸腾制粒,是固体物料呈沸腾 状态与雾滴接触聚集成粒。因此,必须注意观察物 料是否保持沸腾状态,并要防止结块。当物料或物 料中较大的团块出现不沸腾现象时,应停止喷雾, 进行干燥;必要时出料,取出结块物料,用快速整 粒机将团块适当粉碎或干燥后再将团块粉碎,再与 原物料混合后重新制粒;
一步制粒过程
一步制粒过程一步制粒是指在一个工艺过程中完成物料的制粒和干燥。
这种制粒方法相对于传统的两步制粒过程更加高效和节约能源。
一步制粒过程主要包括原料准备、混合、制粒和干燥四个步骤。
下面将详细介绍每个步骤的工艺过程。
1. 原料准备在一步制粒过程中,首先需要准备好需要制粒的原料。
原料的选择应根据产品的要求,包括颗粒大小、形状、密度等。
原料通常是粉末或颗粒状的,可以是单一成分或多种成分的混合物。
2. 混合将原料加入混合机中进行充分混合。
混合的目的是使原料成分均匀分布,确保最终产品的质量稳定。
混合机通常采用搅拌器或滚筒式混合机,通过旋转或翻转将原料进行混合。
3. 制粒混合后的原料进入制粒机进行制粒。
制粒机通常采用挤压制粒机或湿法制粒机。
挤压制粒机通过挤压原料使其成型,并通过切割装置将成型的颗粒切割成所需的大小。
湿法制粒机则通过加入适量的液体使原料粘结成球状颗粒。
4. 干燥制粒后的颗粒进入干燥机进行干燥。
干燥的目的是去除颗粒中的水分,提高颗粒的稳定性和质量。
干燥机通常采用流化床干燥机或旋转干燥机。
流化床干燥机通过高速气流使颗粒悬浮并干燥,旋转干燥机则通过旋转将颗粒暴露在热空气中进行干燥。
一步制粒过程的优点是能够在一个工艺过程中完成制粒和干燥,减少了设备和能源的消耗。
同时,一步制粒过程中的混合、制粒和干燥步骤能够更好地控制产品的质量,提高产品的一致性和稳定性。
然而,一步制粒过程也存在一些挑战。
首先,原料的选择和混合的过程对最终产品的质量有很大影响,需要进行仔细的选择和控制。
其次,制粒和干燥的过程需要控制好温度、湿度和气流等参数,以避免颗粒的破碎或结块。
一步制粒过程是一种高效和节能的制粒方法,通过原料准备、混合、制粒和干燥四个步骤完成制粒过程。
它能够提高产品的一致性和稳定性,并且节约设备和能源的消耗。
然而,一步制粒过程也需要仔细控制原料选择、混合、制粒和干燥的参数,以确保最终产品的质量。
流化制粒法
流化制粒法
流化制粒法是一种常用的制粒工艺,主要适用于颗粒状固体物料的制备。
该方法利用气流将固体颗粒悬浮并流化,然后在悬浮状态下通过喷雾涂覆、干燥、粘结等工艺使颗粒逐渐增大和固结,最终形成所需的颗粒产品。
流化制粒法的主要步骤包括:
1. 准备原料:将需要制备的物料粉末准备好,按照一定的配方和比例混合。
2. 流化床干燥:将混合物料放入流化床设备中,通过控制床层气流速度和温度使物料在床层中悬浮并得到充分干燥。
3. 喷雾涂覆:在干燥的物料表面喷洒溶液或悬浮液,使其逐渐沉积在物料表面形成薄膜层。
4. 干燥固结:将喷雾后的颗粒继续加热,使液体薄膜迅速挥发或凝固形成固态薄膜,并粘结物料颗粒。
5. 筛分和干燥:对所制备的颗粒进行筛分,将不符合要求的颗粒重新回收再制备,符合要求的颗粒进行进一步干燥以去除残余的水分。
6. 包装和储存:对制得的颗粒产品进行包装和储存,以便后续使用或销售。
流化制粒法具有操作简单、生产效率高、颗粒形状可调控等优点,广泛应用于制药、食品、化工等行业中的颗粒制备过程。
湿法制粒——流化床制粒
常见制粒方法的特点及问题❈❈ 序 ❈❈在医药生产中,几乎所有的固体制剂的制备过程都离不开制粒过程。
当前药企广泛应用的制粒方法有:湿法制粒、干法制粒、喷雾制粒,熔融制粒、离心造粒等,其中湿法制粒(流化床制粒、高速剪切制粒)和干法制粒为最为常用的制粒方法。
本文就这两种方法特点和常见的问题进行简单的介绍:(本文暂不考虑设备本身结构或设计问题造成的制粒问题)湿法制粒——流化床制粒流化床制粒过程中微粒长大的机理分为:包衣长大和团聚长大,包衣长大是指粘合剂以雾滴形式铺展在颗粒表面,层层包裹,使颗粒长大;团聚长大是指两个或两个以上的颗粒由粘合剂形成的液体桥或固体桥而团聚在一起,使颗粒长大。
在制粒过程中,经常遇到的问题有:1、 制粒结束后颗粒粒径分布较宽,且细粉太多a.风机频率太高或喷枪位置较高,增加了粘合剂的溶剂挥发,造成物料不能完全润湿,颗粒间不能形成稳定的固体桥,呈现喷雾干燥现象,阻断颗粒团聚长大;b.粘合剂的用量较少,增加粘合剂的用量,使较多的颗粒间形成固体桥,促进颗粒长大;c.粘合剂的种类或浓度不合适,颗粒间不能形成稳定的固体桥,建议更换粘度较大的粘合剂,但同时需注意粘合剂粘度太大造成堵枪;d.喷枪的喷雾范围小于物料床的面积,造成中间物料因接触较多粘合剂而形成较大颗粒,而外围物料因接触粘合剂较少而形成的颗粒较小。
此时应调节喷枪的喷雾范围使其与物料床面积相同(若粘合剂喷雾范围过大,则造成湿物料贴壁)。
此外也可调整物料的流化状态,若物料的流化状态好,也能使物料颗粒的粒径分布较窄;e.若粘合剂的用量加大后仍出现细粉太多现象,则有可能是由于粘合剂。
2、 制得的颗粒中有较大颗粒,甚至塌床颗粒较大的原因是粘合剂与颗粒接触后不能及时干燥,粘合剂在大量粉末颗粒间形成液体桥使物料团聚成较大颗粒。
防止形成较大颗粒或塌床的方法有:文竹昨天药事纵横a. 增加雾化压力或降低供液速度,使雾滴减小,粘合剂与颗粒接触后及时干燥,防止粘合剂与大量物料团聚;b. 增加风机频率 ,改善物料流化状态,防止物料粘连结块;c. 升高进风温度,使雾滴与颗粒接触后能及时干燥,防止物料继续长大。
- 1、下载文档前请自行甄别文档内容的完整性,平台不提供额外的编辑、内容补充、找答案等附加服务。
- 2、"仅部分预览"的文档,不可在线预览部分如存在完整性等问题,可反馈申请退款(可完整预览的文档不适用该条件!)。
- 3、如文档侵犯您的权益,请联系客服反馈,我们会尽快为您处理(人工客服工作时间:9:00-18:30)。
颗粒成型率 /%
休止角 /(°)
50
79.58
28.4
60
95.98
29.7
70
79.91
35.4
由图 1可知 , 随着进风温度的提高 , 形成的细颗 粒越 多 , 粒径 也 明显 减 小 , 当温 度 处 于 50 ℃时 , 小于 24目的颗粒过多 。出现这种现象的原因可能 是 , 进风温度增高 而其它条件不变 时 , 喷入 的黏合 剂 、溶剂蒸发速度也随之变快 , 降低了对物料的润湿 和渗透程度 , 形成的液体桥和内聚力降低 , 影响了粒 子聚集能力 , 形成的颗粒粒径变小 [ 2] 。而温度过低 时 , 粉末过度湿润 , 湿颗粒来不及干燥而相互聚结成 大的团块 , 此时很难维持好的流化状态 , 更容易造成 踏床 [ 3] 。本实验选用的是水和乙醇的混合溶剂 , 温 度处于 60 ℃时 , 制备出的颗粒粒径最为合适 , 合格 率最高 。 2.2.3 喷雾压力的影响 喷雾是通过气流将液体 高度分散为液滴的过程 , 目的在于增加黏合剂与粉 体的接触面积 。喷雾压力是制粒中另一个重要工艺 因素 , 实验中选用 23 ~ 35 Hz的进风风速 、进风温度 为 60 ℃以及喷雾速率为 10 mL/min的工艺条件 , 喷 雾压力对造粒的影响见图 2、表 3。
考察法 , 考察进风风速 、进风温度 、喷雾速率和喷雾 压力等因素对颗粒粒径分布和流动性的影响 。
1 实验部分
1.1 材料与仪器 乳 糖 Tabletose100, 200 目 ;微晶 纤维素 VTVAPUR101;聚维酮 K30(分子量 38000);95%乙醇 , 化 学纯 ;去离子水 , 自制 。
图 1 温度对粒径分布的影响 Fig.1 Theeffectoftemperatureonparticlesizedistribution
1 78
应用化工
第 40卷
表 2 温度对颗粒参数的影响 Table2 Influenceoftemperatureonparticleparameters
温度 /℃
第 40卷第 1期 2011年 1月
应 用 化 工 AppliedChemicalIndustry
Vol.40 No.1 Jan.2 011
应用技术
流化床一步制粒法的工艺优化
高丹丹 , 刘哲鹏 , 陈岚 , 乔培 , 瞿良 , 沈泉健
(上海理工大学 医疗器械与食品学院 , 上海 200093)
图 2 喷雾压力对粒径分布的影 响 Fig.2 Theeffectofpressureofsprayonparticle
sizedistribution
表 3 喷雾压力对颗粒参数的影 响
Table3 Influenceofpressureofsprayon particleparameters
喷雾压力 /MPa
收稿日期 :2010-09-29 修改稿日期 :2010-10-30 作者简介 :高丹丹 (1987 -), 女 , 河 北保定人 , 上海理工大学硕士生在读 , 师从刘哲鹏高 级工程师 , 主要从 事药物新剂 型与
新设备的研究 。 电话 :13482740163, E-mail:gaodandan@ 通讯作者 :刘哲鹏 , 高级工程师 , 硕导 。 E-mail:zhepengliu@
流化床制粒是操作工艺性较强的制粒方法 , 是 由物料特性 、喷雾 、流态化工艺和设备操作条件之间 相互影响的结果 , 而且成型颗粒的性质对其后续工 艺例如压片 、灌注胶囊等操作起着重要的影响 。
目前 , 关于流化床工艺参数对颗粒粒径影响的 研究很多 , 但是很少文献能详细提供颗粒粒径分布 。 本文制备乳糖与微晶纤维素压片颗粒 , 采用单因素
粒度分布 。 如果黏合力和撞击力的大小关系失调 , 就会造成颗粒的过大或过小 。 2.2 工艺参数对造粒的影响 在片剂压缩成型过程中 , 颗粒性质会影响片剂 成型好坏 , 所以重点考察颗粒粒径以及流动性 。本 文对流化床制粒工艺中主要的 4个重要参数进风风 速 、进风温度 、喷雾压力以及喷射速率进行了单因素 实验优化 , 结果分析如下 。 2.2.1 进风风速的选取 在流化床造粒技术中 , 进 风风速的选取要以保证流化床层颗粒始终处于良好 的流化状态为原则 [ 2] 。若风速过大 , 就不能避免物 料冲到捕尘袋上 , 而单位时间通过的热空气气量过 多 , 使得黏合剂水分蒸发过快 , 颗粒变小 , 细粉过多 。 而且随着风速的增大 , 颗粒收到的撞击力也变大 , 使 得颗粒磨损加大 , 粒径变小 。过小的风速不能使物 料有效混合 , 物料沸腾状态差 , 黏合剂的水分不能及 时蒸发 , 造成湿颗粒来不及干燥 , 容易造成踏床 。
流化床制粒法也称一步制粒技术 , 是将传统的 混合 、制软材 、制粒 、干燥等单元操作于一体 。 与湿 法制粒相比无需整粒 , 制成的颗粒可以进行直接成 品 、灌注胶囊或压片 , 具有操作时间短 、物料损失少 以及生产 效率高的优点 , 其得到的产品粒度分布均 匀 、流动性 、压缩成形性好 , 且更适用于热敏性物料 的制粒 , 在食品 、医药以及材料领域应用广泛 [ 1] 。
摘 要 :采用流化床一步制粒法制备工业 压片颗粒 , 讨论了流化床设备工艺参数 (进风风量 、进风温度 , 喷雾速 率和 喷雾压力 )对颗粒形成的 (粒径分布 和休 止角 )影 响 。 结果 表明 , 最佳 实验 条件为 风机 频率 23 ~ 35 Hz, 进风温 度 60 ℃ , 喷雾速率 10 mL/min, 喷雾压力 1.5 MPa时 , 所得颗粒粒径分布最优 , 流动性最好 。 关键词 :流化床 ;制粒 ;工艺参数 ;粒径分布 中图分类号 :TQ 460.5 文献标识码 :B 文章编号 :1671 -3206(2011)01 -0176 -03
2 结果与讨论
2.1 颗粒生长机理 颗粒的长大方式取决 于黏合剂的水分 蒸发速 度 , 当黏合剂被雾化成微小的液滴喷到粉末上时 , 如 果颗粒表面以及热气流中的热量可以使黏合剂中的 水分快速蒸发 , 形成的固体物质则依靠范德华力 、分 子引力等存留在颗粒表面 , 经过多次喷涂 , 使得颗粒 不断长大 , 此种方式被称为涂层式生长 。 如果热量 不足以使粉体表面的黏合剂水分蒸发 , 湿润的粒子 之间则形成液体桥和内聚力桥 , 在其作用下形成的 粒子核的大小取决于喷雾的雾滴大小 , 当粒子核不 断增多 , 液体桥的毛细血管力将松散的粒子核聚集 并结合成颗粒 , 经过流化干燥 , 水分蒸发 , 液体桥变 成固体桥 , 得到疏松而多孔的颗粒 , 称为团聚造粒方 式。
Theoptimizationoffluidizedbedone-step pelletizationtechnology
GAODan-dan, LIUZhe-peng, CHENLan, QIAOPei, QULiang, SHENQuan-jian
(SchoolofMedicalInstrumentandFoodEngineering, UniversityofShanghai forScienceandTechnology, Shanghai200093, China)
第 1期
高丹丹等 :流化床一步 制粒法的工艺优化
17 7
数进行制粒 , 当定量的黏合剂喷雾完毕后 , 再通人热 空气流化干燥一段时间后取料 。
表 1 处方设计表 Table1 Prescriptionform design
处方
用量 /g
微晶纤维素
250
乳糖
250
PVPK30 溶液
600 mL
1.2.2 颗粒合格率考察 压片颗粒的最优粒径分 布需处于 24 ~ 100 目之间 , 并 呈正态分布 , 无需整 粒 。 要求细粉含量一定 , 过多会影响颗粒流动性 ;过 少则片重差异较大 。颗粒成型率 =[ 24 ~ 100目之 间的颗粒 /全部颗粒 ] ×100%。 1.2.3 粒径分布 将所需的一系列筛网按孔径大 小置于实验台上 , 取定量 100 g的待测颗粒 , 以 5 Hz 固定频率振动 5 min。 测定不同目筛网上滞留物料 的重量 , 计算累计筛下重量百分比 。同一工艺参数 , 重复测量 3次 , 取平均值 。 1.2.4 流动性休止角测量 取一定量的待测颗粒 , 并固定于水平放置的坐标纸上方 5 cm处 , 取定量的 待测颗粒沿漏斗壁倒入漏斗中 , 当所有颗粒从漏斗 中漏出 , 在坐标纸上形成圆锥体 , 由坐标纸测量圆锥 体斜面与平面的夹角即为休止角 , 重复 5次 , 取平均 值。
LBL-1型流化床包衣制粒机 。 1.2 实验方法 1.2.1 颗粒制备方法 实验设备选用的是流化床 包衣制粒 机的顶 喷装置 , 称 量处 方量 的乳糖 和微 晶纤维 素 , 过 100 目 筛 , 粘 合 剂 选 用 浓 度 为 8% (g/100 mL)的聚维酮 K30溶液 , 溶剂为体积比 1 ∶1 的乙醇和水的混合溶剂 。 调节好制粒所需的工艺参
成型率 /%
休止角 /(°)
0.5
59.72
27.6
Hale Waihona Puke 1.595.9830.7
2.5
87.78
32.5
3.5
81.53
37.7
由图 2可知 , 随着喷雾压力的不断变大 , 颗粒的 粒径分布也随之减小 。 当喷雾压力过低 , 压力处于
0.5 MPa时 , 0 ~ 24目的颗粒数量明显增加 , 而且有 非常大的颗粒产生 。 由于喷雾压力的改变直接影响 喷出的雾滴大小 , 压力越大 , 液滴越小 , 反之液滴越 大 。黏合剂液滴越小 , 液体表面积也就越大 , 被热空 气蒸发水分的速率也越高 , 使得颗粒的粒径变小 , 细 粉增多 。而当黏合剂液滴过大时 , 雾化液滴喷雾的 锥角减小 , 润湿粉体能力降低 , 过大的液滴更容易产 生大的结块颗粒 。当雾化压力为 1.5 MPa时 , 雾化 液滴大小合适 , 颗粒合格率最高 。 2.2.4 喷雾速率的影响 实验中选用 25 ~ 30 Hz 的进风风 速 、进 风温 度为 60 ℃以及 喷雾 压 力为 1.5 MPa的工艺条件 , 喷雾速率对造粒的影响见图 3、表 4。