第6章 离子镀膜
离子镀膜PPT课件

离子镀膜技术——离子镀膜的类型
(3)在多阴极方式中,即使气压保持不变,只改变作为热电子发射源的灯丝电流,放 电电流就会发生很大的变化,因此可通过改变辅助阴极(多阴极)的灯丝电流来控制放电状态。
(4)由于主阴极(基板)上所加维持辉光放电的电压不高,而且多阴极灯丝处于基板四 周,扩大了阴极区、改善了绕射性,减少了高能离子对工件的轰击作用,避免了直流二极型 离子镀溅射严重、成膜粗糙、温升高而难以控制的弱点。
但在工艺实现比较困难,因为不易产生足够数量 的固态物质离子,并能将它们引出和聚焦成束。
2. 分子束外延制膜法(MBE) 外延工艺:合适的条件下,在适当的衬底上生成
一层晶格结构完整的新单晶层外延层的制膜工艺。
同质外延:外延层与衬底材料在结构和性质上 相同,但纯度可控等。
异质外延:外延层与衬底材料在结构和性质不同。
离子镀膜技术
Ion Plating
§4.4 离子镀膜技术
★ 离子镀膜的原理 ★ 离子镀膜的特点 ★ 离子轰击的作用 ★ 离子镀膜的类型
离子镀是在真空条件下,利用气体放电使气体 或被蒸发物质部分离化,在气体离子或被蒸发物质 离子轰击作用的同时把蒸发物或其反应物沉积在基 片上。
离子镀把气体的辉光放电、等离子体技术与真 空蒸发镀膜技术结合在一起,不仅明显地提高了镀 层的各种性能,而且大大地扩充了镀膜技术的应用 范围。
离子镀膜技术——离子镀膜的类型 ★ 离子镀膜的类型
按薄膜材料气化方式分类:
电阻加热、电子束加热、高频感应加热、阴极弧光放电加热等。
按原子或分子电离和激活方式分类:
辉光放电型、电子束型、热电子型、电弧放电型、以及各种离子源。
一般情况下,离于镀膜设备要由真空室、蒸发源(或气源、溅射源等)、高压电源、离化 装置、放置基片的阴极等部分组成。
离子镀膜及CVD
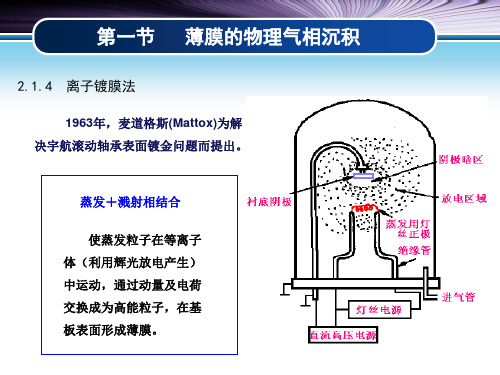
1 、温度 影响淀积速率、薄膜的结晶状态。
不同的沉积温度,可得到单晶或多晶薄膜。一般希望低温沉积
Vapor phase epitaxy (VPE)
特征:必须有化学反应发生;但PVD 中也可能有化学反应发生,主要过程是
蒸镀、溅射这样的物理搬运过程。
第二节 薄膜的化学气相沉积
二、CVD的分类 1 .按沉积温度分:低温(200 -500 ℃ ) 中温(500 -1000 ℃ ) 高温(1000 -1300 ℃ )
2.1.4 离子镀膜法 离子镀的特点(与蒸发和溅射相比)
(1) 膜层附着性能好: A、阴极溅射的清洗作用,B、伪扩散层 (2) 膜层的密度高(通常与大块材料密度相同):高能离子的作用 (3) 绕射性能好:离化后的正离子沿电力线方向运动 (4) 可镀材质范围广泛:金属、非金属、合成材料、敏感材料 (5) 有利于化合物膜层的形成:电能→反应的活化能 (6) 淀积速率高,成膜速度快,可镀较厚的膜:Ti膜:0.23mm/h
不需要高真空;可沉积 各种金属,半导体,无机物, 有机物薄膜材料;可控制材料 的化学计量比;批量生产,半 连续流程。
利用热、等离子体、紫外线、激光、微波等各种能源,使气态物质经化 学反应形成固态薄膜。它的反应物是气体,生成物之一是固体。
Chemical Vapor Deposition (CVD),
在膜/基间形成一定厚度的缓变过渡层,
可能形成新相
第一节 薄膜的物理气相沉积
缓变层的作用
提高膜层的附着性 提高膜层的硬度 提高膜层的抗磨损能力 提高膜层的抗氧化能力 提高膜层的抗腐蚀能力
表面改性 可形成梯度薄膜层, 组成简便改性层
第一节 薄膜的物理气相沉积
影响4:气体渗入膜层中
第6章离子镀膜ppt课件

3.离子能量
• 离子的溅射、沉积均与离子能量有关 ; • Vc为衬底阴极所加的负偏压,离子的平均
能量为eVc/10。当Vc为1~5kV时,离子的 平均能量为100~500 eV 。 • 这有沉积和溅射作用同时存在。 • D.G.Teer测出金属的离化率只有0.1~1%。
4.中性原子
• 受到碰撞的中性金属粒子的数量大约为金属离子数的20倍; • 但是,并非所有的高能中性原子都能到达基板。通常,约
Ei eUi ,其中Ui 是淀积离子的平均加速电压。
3.薄膜表面的能量活性系数
薄膜表面的能量活性系数 可由下式近似给出
(Wi Wv )/Wv (niEi nvEv )/ nvEv (4
当 nvEv niEi 时,可得
niEi eUi ( ni ) C Ui ( ni )
nvEv 3kTv / 2 nv Tv nv
•则
n 9.76 1016 / cm。2 s
• ②溅射剥离效应
• 设离子电流密度为j,则单位时间内轰击到基片表面的 离子数,溅射率为η,则单位时间内溅射的原子数nj,
nj
nj
103 j
1.6 1019
0.631016
j / cm2
s
• 式中,是一价正离子电荷量(只考虑一价正离子),j
是入射离子形成的电流密度。
• 与溅射镀膜,离子轰击靶(阴极)溅射出原子成膜。而离子镀中,离 子或中性原子直接在负高压(阴极)成膜。
6.2 离子镀的特点
(1)膜层附着性能好。 因为在离子镀过程中,利用辉光放电所产生的大量高能粒子对
基片表面产生阴极溅射效应,对基片表面吸附的气体和污物进行 溅射清洗,使基片表面净化,而且伴随镀膜过程这种净化清洗随 时进行,直至整个镀膜过程完成,这是离子镀获得良好附着力的 主要原因之一。
第6章-电子束和离子束加工

离子注入—演示
用高能量粒子直接击入工件,令工件表面层改性。
(3)离子束加工的特点
1)离子束流密度及离子能量可以精确控制。离子束加工是所 有特种加工方法中最精密、最精细的加工方法,是当代毫微 米(纳米)加工技术的基础。 2)离子加工在高真空中进行,所以污染少,适于对易氧化金 属、合金材料和高纯度半导体材料的加工。 3)离子束加工是靠离子轰击材料表面的原子来实现的。宏观 压力很小,加工应力、热变形等极小,加工质量高。 4)利用机械碰撞能量加工,故加工范围广,适合于对各种材 料和低刚度零件的加工。 5)加工过程容易控制,易实现自动化。 6)离子束加工设备费用高、成本高,加工效率低。
电子束加工分类
通过控制电子束能量密度的大小和能量注入时 间,就可以达到不同的加工目的。 电子束打孔、切割等加工:高电子束能能量密度, 使材料融化和气化,就可以进行; 电子束焊接:使材料局部融化就可以进行; 电子束热处理:只使材料局部加热就可以进行; 电子束光刻加工:利用较低能量密度的电子束轰击 高分子材料时产生化学变化的原理,即可进行。
解加工,最后焊接成整件 。
焊接加工样件
焊接加工样件
卫星姿态发动机气瓶直径约300mm,由不锈钢板冲压成半球。 要求用电子束焊接将两半球焊在一起,同时要求将焊口对侧内 壁毛刺熔融。
(4)表面改性/热处理
加热冷却速度快,获得超细晶粒和很高的表面硬度。 热转化效率高,可达90%,而激光的转换效率只有7%-10%。 可实现合金化
刻蚀
功率密度对加工模式的影响
a) 低密度
b) 中低密度
c) 高密度
表面改性
电子束焊接
电子束打孔、切槽
电子束加工的应用范围
(1)高速打孔
特点
特种加工技术---第六章:电子束和离子束加工

h
17
2 离子束加工在高真空环境下进行,所以污染少,特别适用于对易 氧化的金属、合金材料和高纯度半导体进行加工。
3 离子束加工是靠离子轰击材料表面的原子来实现的,是一种微观 作用,宏观压力很小,所以加工应力、热变形极小,加工质量高, 适合于加工各种材料和低刚度薄壁零件。
4 与电子束加工类似,离子束加工设备费用贵、成本高,应用范围 受到一定的限制。
h
4
三 电子束加工装置 一般说来,一套典型的电子束加工装置主要包括以下几个 主要组成部分
➢ 电子枪 ➢ 真空系统 ➢ 控制系统 ➢ 电源
h
5
1 电子枪 作用:发射电子束 组成:发射阴极,控制栅极、加速阳极
h
6
2 真空系统 真空系统的主要作用是保证电子束加工时维持1.33×10-21.33×10-4Pa的真空度,因为只有在真空中,电子才能高 速运动。此外,加工时产生的金属蒸汽会影响电子的发射 和运动,因此也需要不断地把加工中产生的金属蒸汽不断 抽走。
第六章 电子束和离子束加工
电子束加工-----Electron Beam Machining
离子束加工-----Ion Beam Machining
电子束加工主要用于打孔、焊接、切割、刻蚀、热处理和光刻 加工等方面。 离子束加工主要用于离子刻蚀、离子镀膜加工以及离子注入 加工等方面。
h
1
第一节 电子束加工
3 控制系统和电源
电子束加工设备控制系统主要包括:束流聚焦控制、束流位置 控制和束流强度控制。
束流的位置控制是为了改变电子束的方向,常用电磁偏转来控制
电子束焦点的位置。
电子束加工设备对电源电压的稳压性要求较高,因为电压波动
会影响电子束聚焦的稳定性。 h
离子镀膜法

离子镀膜技术——离子镀膜的类型 ★ 离子镀膜的类型
按薄膜材料气化方式分类:
电阻加热、电子束加热、高频感应加热、阴极弧 光放电加热等。
按原子或分子电离和激活方式分类:
辉光放电型、电子束型、热电子型、电弧放电型、 以及各种离子源。 一般情况下,离于镀膜设备要由真空室、蒸发源 ( 或 气源、溅射源等 ) 、高压电源、离化装置、放置基片的阴 极等部分组成。
离子镀膜技术——离子轰击的作用
溅射清洗
薄膜淀积前对基片的离子轰击。将产生如下 结果:
溅射清洗作用 吸附气体、各种污染物、氧化物
产生缺陷和位错网
入射粒子传递给靶材原子的能量超过靶原子发生离位的 最低能量时,晶格原子将会离位并迁移到晶格的间隙位置上 去,从而形成空位、间隙原子和热激励。轰击粒子将大部分 能量传递给基片使其发热,增加淀积原子在基片表面的扩散 能力,某些缺陷也可以发生迁移、聚集成为位错网。
离子镀膜技术——离子轰击的作用
破坏表面晶格 离子轰击产生的缺陷很稳定的话,表面的晶体结构 就会被破坏而成为非晶态 气体掺入 不溶性气体的掺入能力决定于迁移率、捕获位置、 基片温度及淀积粒子的能量大小 非晶材料捕集气体的能力比晶体材料强。
表面成分改变 溅射率不同 表面形貌变化 表面粗糙度增大,溅射率改变 温度升高
由于高能粒子轰击,基片温度较高,有时不得不 对基片进行冷却。
薄膜中含有气体量较高。
离子镀膜技术——离子轰击的作用 ★ 离子轰击的作用
离子镀膜的整个过程中都存在着离子轰击。 离化率:是指被电离的原子数占全部蒸发原子的百分数。
中性粒子的能量 W n E
3kTv Ev 2
离子镀膜技术——离子镀膜的类型
直流二极型离子镀
离子镀膜法简述-10082953-李煊
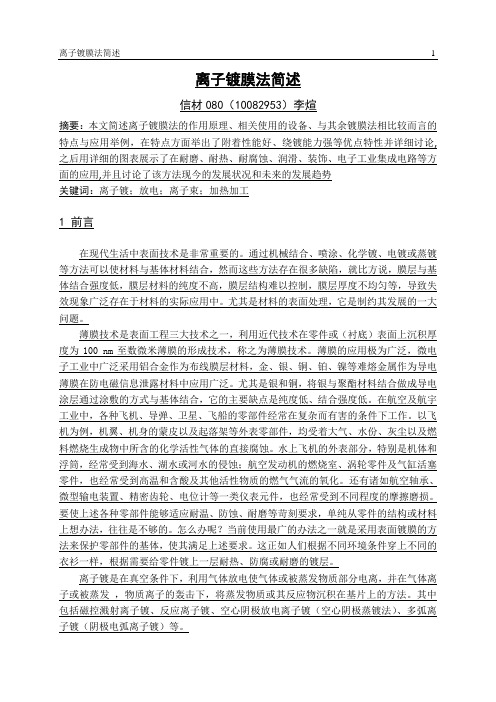
离子镀膜法简述信材080(10082953)李煊摘要:本文简述离子镀膜法的作用原理、相关使用的设备、与其余镀膜法相比较而言的特点与应用举例,在特点方面举出了附着性能好、绕镀能力强等优点特性并详细讨论,之后用详细的图表展示了在耐磨、耐热、耐腐蚀、润滑、装饰、电子工业集成电路等方面的应用,并且讨论了该方法现今的发展状况和未来的发展趋势关键词:离子镀;放电;离子束;加热加工1 前言在现代生活中表面技术是非常重要的。
通过机械结合、喷涂、化学镀、电镀或蒸镀等方法可以使材料与基体材料结合,然而这些方法存在很多缺陷,就比方说,膜层与基体结合强度低,膜层材料的纯度不高,膜层结构难以控制,膜层厚度不均匀等,导致失效现象广泛存在于材料的实际应用中。
尤其是材料的表面处理,它是制约其发展的一大问题。
薄膜技术是表面工程三大技术之一,利用近代技术在零件或(衬底)表面上沉积厚度为100 nm至数微米薄膜的形成技术,称之为薄膜技术。
薄膜的应用极为广泛,微电子工业中广泛采用铝合金作为布线膜层材料,金、银、铜、铂、镍等难熔金属作为导电薄膜在防电磁信息泄露材料中应用广泛。
尤其是银和铜,将银与聚酯材料结合做成导电涂层通过涂敷的方式与基体结合,它的主要缺点是纯度低、结合强度低。
在航空及航宇工业中,各种飞机、导弹、卫星、飞船的零部件经常在复杂而有害的条件下工作。
以飞机为例,机翼、机身的蒙皮以及起落架等外表零部件,均受着大气、水份、灰尘以及燃料燃烧生成物中所含的化学活性气体的直接腐蚀。
水上飞机的外表部分,特别是机体和浮筒,经常受到海水、湖水或河水的侵蚀;航空发动机的燃烧室、涡轮零件及气缸活塞零件,也经常受到高温和含酸及其他活性物质的燃气气流的氧化。
还有诸如航空轴承、微型输电装置、精密齿轮、电位计等一类仪表元件,也经常受到不同程度的摩擦磨损。
要使上述各种零部件能够适应耐温、防蚀、耐磨等苛刻要求,单纯从零件的结构或材料上想办法,往往是不够的。
怎么办呢?当前使用最广的办法之一就是采用表面镀膜的方法来保护零部件的基体,使其满足上述要求。
ch6 溶液镀膜法--化学溶液沉积
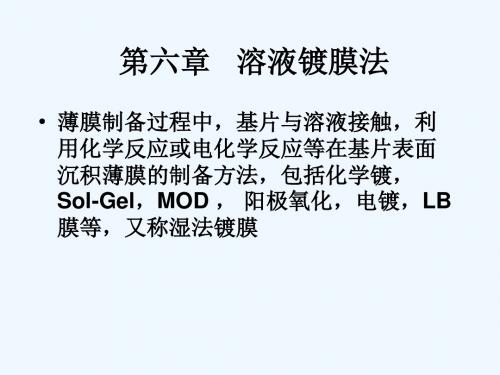
• 机理:膜局部溶解→多孔形膜 不发生溶解→屏蔽形膜。 • 用途: 多孔形膜,防金属腐蚀,磨损,装饰。 屏蔽形膜,电解电容器。
§6-3 电镀法
• 电镀:在含有被镀金属离子得水溶液中通 过直流电,使得正离子在阴极上放电,得 到金属薄膜。 • 化学镀:不从外部供电,利用氧化还原反 应或者置换反应,使得金属盐水溶液中得 金属离子在基片表面析出的方法。Fe片插 入Cu2+ 。置换反应价值不大,更多的是氧 化还原反应。
§6-2 阳极氧化法
• 在电解液中,使铝、镁等金属或者合金 作阳极,并加上一定的直流电压,利用 电化学反应在阳极金属表面形成氧化物 薄膜的方法。 • 存在两个过程,一个是金属氧化物的形 成,一个是金属溶解。
– 金属的氧化反应:
M + nH2O → MOn + 2nH+ + 2ne
– 金属的溶解反应:
• 生长方法: A.倾斜法 缺点:溶液和生长晶体表面分离不完全, 有部分溶液粘附在生长层表面,并且生 长层厚度和均匀性难以控制 B.浸渍法 与倾斜法相似,设备简单,外延层厚度 不易均匀 C.滑动舟法(主要使用方法) 可进行多层液相外延源片GaAs的作用是 使溶液达到饱和。
附着一层膜的,可连续附着另一层膜的, 称Y型膜η up≈ η down ≈1 疏水基板:只能在插入过程中附着一 层膜,称X型膜(不稳定)η up≈ 0 • 亲水基板:只能在提出过程中附着一层膜, 称Z型膜 (不稳定) η down ≈0 • 水平附着法 表面平滑,水平的基板从上向下缓慢下降, 可制得理想的X型膜。
应用有限 • 并非所有金属都具有催化活性 Fe、Cr、Ni、Cu、Ag、Au、Co…
• 还原剂电极电位稍低于沉积金属 次磷酸盐、甲醛、硼氢化物、阱
- 1、下载文档前请自行甄别文档内容的完整性,平台不提供额外的编辑、内容补充、找答案等附加服务。
- 2、"仅部分预览"的文档,不可在线预览部分如存在完整性等问题,可反馈申请退款(可完整预览的文档不适用该条件!)。
- 3、如文档侵犯您的权益,请联系客服反馈,我们会尽快为您处理(人工客服工作时间:9:00-18:30)。
6.3 离子轰击的作用 1.离化率
• 离化率是指被电离的原子数占全部蒸发原子数的百分比 例。是衡量离子镀特性的一个重要指标。 • 特别在反应离子镀中更为重要。因为它是衡量活化程度 的主要参量。被蒸发原子和反应气体的离化程度对薄膜 的各种性质都能产生直接影响。
1、 中性粒子的能量 中性粒子所具有的能量 Wv 主要取决于蒸发温度的高低,其值为
4.中性原子
• 受到碰撞的中性金属粒子的数量大约为金属离子数的20倍; • 但是,并非所有的高能中性原子都能到达基板。通常,约 有70%左右可到达基板,其余30%则到达器壁、夹具等处。 • 这些高能中性原子的平均能量为eVc/22,当Vc为1~5kV 时,其平均能量为45~225eV。考虑到粒子间碰撞几率不 相同,离子和高能中性原子的能量将在零至数千伏范围内 变化,个别粒子的能量也能达到1~5keV。 • D.G.Teer测出金属的离化率只有0.1~1%。中性能量的原 子为其的20倍。 • 所以,由于产生了大量高能中性原子,故提高了蒸发粒子 的总能量。因此,使得离子镀具有许多优点。
5.离子入射到固体表面的三种现象
• 金属离子照射到固体表面上,根据入射的离子能量E值的 大小的不同,一般来说可以产生下述三种现象: E 5 0 eV • (1)沉积现象( ) E 5 0 eV ) • (2)溅射现象( • (3)离子注入现象( E 1 K eV )。 • 沉积现象是指照射的金属离子附着在固体表面上的现 象,这一现象与离子的动能有关,一般来说,动能小,附 着几率越大,获得的沉积速率也高。 • 随着入射离子能量的增加,因离子轰击作用,基片原子即 会被溅射出并进入到真空室中,这就是溅射作用。这时已 经附着在表面上的部分金属原子当受到后续入射的同种离 子的溅射作用后还会重新返回到真空室中。 • 而且,如果入射离子能量再进一步增大时,离子还会注入 到表面的原子层中,即产生离子注入现象。
• 离子能量在300eV以下时,沉 积现象占优势,Ge沉积量大; • 但是随着入射离子能量的增加, 溅射现象逐渐占优势从而使 Ge的沉积量呈减少趋势。从 测量Ge厚度来看,当离子能 量超过500eV时,Ge膜没有 发现沉积。这一能量值,正好 与Ge的自溅射产额等于1时的 能量相对应。 • 当能量超过900eV时,Ge附 着量又呈现增加的趋势,即出 现了离子注入现象。表5-15是 相应于几种金属成膜时所需的 最大临界能量范围。
• 与溅射镀膜,离子轰击靶(阴极)溅射出原子成膜。而离子镀中,离 子或中性原子直接在负高压(阴极)成膜。
6.2 离子镀的特点
(1)膜层附着性能好。 因为在离子镀过程中,利用辉光放电所产生的大量高能粒子对 基片表面产生阴极溅射效应,对基片表面吸附的气体和污物进行 溅射清洗,使基片表面净化,而且伴随镀膜过程这种净化清洗随 时进行,直至整个镀膜过程完成,这是离子镀获得良好附着力的 主要原因之一。 另一方面,离子镀过程中溅射与淀积两种现象并存,在镀膜初期, 可在膜基界面形成组分过渡层或膜材与基材的成分混合层, Mattox 称之为“伪扩散层“,能有效改善膜层的附着性能。 (2)膜层的密度高(通常与大块材料密度相同)。 离子镀过程中,膜材离子和高能中性原子带有较高的能量到达基 片,可以在基片上扩散、迁移。而且膜材原子在空间飞行过程中 即使形成了蒸气团,到达基片时也能被离子轰击碎化,形成细小 的核心,生长为细密的等轴结晶。 在此过程中,高能氩离子对改善膜层的结构,并使之形成接近块 材的密度值,发挥了重要作用。 也可以说,镀层质量高,主要是由于淀积膜层不断受到正离子轰击, 从而引起冷凝物发生溅射,使膜层致密,针孔和空气孔大大减少 的缘故。
• (3)绕射性能好。 • 离子镀过程中,部分膜材离子被离化成正离子后,它们将 沿着电场的电力线方向运动,凡是电力线分布之处,膜材 离子都能到达。在离子镀中由于工件为阴极,且带负高压, 因此,工件的各个表面(包括孔、槽、面向蒸发源或背向 蒸发源的表面)都处于电场之中。这样,膜材的离子就能 到达工件的所有表面。 • 另外,由于膜材在压强较高的情况下(>1Pa)被电离, 气体分子的平均自由程λ比源基之间的距离h小,所以蒸 气的离子或分子在它到达基片的路程中将与惰性气体分子、 电子及其它蒸气原子之间发生多次碰撞,产生非定向的气 体散射效应,使膜材粒子散射在整个工件周围。 • 由于上述原因,离子镀可以在基片的所有表面上淀积薄膜。 这是真空蒸发所无法比拟的。
10
10
2
3 104来自50V 5000V 50V 5000V
500V 5000V
10 10 10 10 10 10
1 1
1
3
2
2
500V 5000V
•由表可见,在离子镀中可以通过改变Ui和ni/ne,使ε值提高2~3个数量级。
• 图4-2 能量活性系数与离化率、离子平均加速电压的关系(1800K) • 如离子的平均加速电压较低时,例如Ui=500V,离化率为3*10-3时,离 子镀的能量活性系数则与溅射时相同。因此,在离子镀过程中离化率 的高低非常重要。 • 图4-2是在典型的蒸发温度时,能量活性系数与离化率和的关系。从 该图可看出,能量活性系数与加速电压的关系,在很大程度上受离化 率的限制。为了提高离子镀活性系数,通常可通过提高离子镀装置的 离化率来实现。几种离子镀装置的离化率值见表4-3所示。
1.工作原理
2.成膜机理
• 1)蒸发原子与等离子区中的正离子和被激活的 惰性气体原子及电子发生碰撞,成为离子,或 获得能量的原子沉积在基片表面上成膜; 2)成膜前Ar离子的溅射清洗基片。由于基片处 于负高压,Ar+轰击表面溅射清洗表面。 3)基片在成膜过程中受到Ar+和被电离的蒸发 原子对基片的溅射。 必须淀积效应优于溅射剥离效应,沉积的离子 原子数n大于被溅射的原子nj,即成膜条件
6.1 离子镀原理
• 结构:热蒸发源,直流负高压,进气管路,。。
• 当真空度抽至10-4Pa的髙真空 后,通入惰性气体(Ar),使 真空度达到1~10-1Pa。 • 接通高压电源,则在蒸发源与 基片之间建立了一个低气压气 体的等离子体区。 • 使镀材气化蒸发,蒸发粒子进 入Plasma区,与等离子区中 的正离子和被激活的惰性气体 原子及电子发生碰撞,其中一 部分蒸发粒子被电离成正离子, 正离子在负高压电场加速的作 用下,到达并沉积在表面成膜; 其中一部分获得了能量的原子, 也到达表面并沉积成膜。
W v nv E v
(4-4)
式中, n v ——单位时间在单位面积上所淀积的粒子数; E v ——蒸发粒子的动 能; E v 3 kT v / 2 ,其中,k 为波尔兹曼常数, T v 为蒸发物质的温度。 2、 离子能量
离子的能量 W i 主要由阴极加速电压决定,其值为
W i ni E i
• (4) 可镀材质范围广泛。可在金属或非金属表面上镀金属 或非金属材料。如塑料、石英、陶瓷和橡胶等材料,以及 各种金属、合金和某些合成材料、敏感材料、高熔点材料 等。 • (5) 有利于化合物膜层的形成。 • 在离子镀技术中,在蒸发金属的同时,向真空室通入某些 反应性气体,则可反应生成化合物。由于辉光放电低温等 离子体中高能电子的作用,将电能变成了金属粒子的反应 活化能,所以可在较低温度下形成在高温下靠热激发才能 形成的化合物。 • (6) 淀积速率高,成膜速度快,可镀较厚的膜。通常, 离子镀淀积几十微米厚的膜层时,其速度较其他镀膜方法 快。试验表明:离子镀钛每小时约为0.23㎜,镀不锈钢约 为0.3㎜。
3
n j n j
10
3
j
19
1 .6 1 0
0 .6 3 1 0
16
j / cm s
2
•
式中,是一价正离子电荷量(只考虑一价正离子),j 是入射离子形成的电流密度。
3.离子能量
• 离子的溅射、沉积均与离子能量有关 ; • Vc为衬底阴极所加的负偏压,离子的平均 能量为eVc/10。当Vc为1~5kV时,离子的 平均能量为100~500 eV 。 • 这有沉积和溅射作用同时存在。 • D.G.Teer测出金属的离化率只有0.1~1%。
当 n v E v n i E i 时,可得
(4
U i ni ( )C ( ) n v E v 3 kT v / 2 n v Tv n v
式中,
ni nv
ni E i
eU i
ni
(4-7
——离子镀过程中的离化率;C——可调节参数。
• 在离子镀中轰击离子的能量取决于基片加速 电压,加速电压典型能量值为50~5000eV。 离子的平均能量为eVc/10.离子的平均能量为 5~500 eV. • 溅射所产生的中性原子也有一定的能量分布, 其平均能量约为几个电子伏。 • 在普通的电子束蒸发中,若蒸发温度为2000K, 则蒸发原子的平均能量为0.2eV。 • 各种镀膜方法所达到的能量活性系数ε值见表 4-2。
表 4-2 不同镀膜工艺的表面能量活性系数
镀膜工 艺艺 真空蒸发 溅射 能量活 性系数 1 5~10 参数
蒸发粒子所具有的能量 E v 0.2 eV 溅射粒子所具有的能量 E s 1 10 eV 离化率 n i / n v 平均加速电压U i
离子镀
1.2 3.5 25 250 2500
(4-5)
式中, n i ——单位时间对单位面积轰击的离子数; E i ——离子的平均能量,
E i eU i ,其中 U i 是淀积离子的平均加速电压。
3.薄膜表面的能量活性系数 薄膜表面的能量活性系数 可由下式近似给出
(W i W v ) / W v ( n i E i n v E v ) / n v E v
• 考虑薄膜沉积过程中基片表面的清洁状态时,由于物理吸附气体分子 的能量约为0.1~0.5eV,化学吸附气体的能量约为1~8eV。因此,只 要恰当地选择离子的照射能量,入射的离子就可以把这两种分子从基 片表面上轰击掉,从而达到表面清洁的目的。 • 而且如采用较高能量的离子对固体表面进行照射,不仅会引起基片原 子的溅射,而且还能使基片近表面的原子发生离位,产生缺陷等。这 些原子的离位和缺陷,对于晶体膜的生长,可作为晶体生长所必需的 晶核。同时,随着离子的轰击还会促进表面原子的扩散。 • 因此,束流沉积法与传统的薄膜沉积法相比较,在相同的基片温度下 产生晶体生长的条件是容易实现的。特别是在团簇离子束沉积中,沉 积粒子更易于在基片表面上移动,这种效果可以认为是表面迁移效果 所产生的。 • 离子镀的成膜的粒子与蒸发镀的粒子能量主要区别,蒸发原子直接到 达表面,0.1~1eV; 离子镀为蒸发离子或高能原子,能量在几百~几千 eV。