均衡化平准化生产案例
均衡化平准化生产案例

案例
改善1: 将顺序反过来,月初生产需求量少的产品
改善效果:第12天就可以开始发货。
案例
改善2: 为了更快、更灵活的响应市场,必须要分批次
我们选择周为时间跨度。在下表,月需求量在 B 列,周平均需求量 在 C 列。我们只能离散制造完成的数量在 D 列(需要被四舍五入)。 四舍五入后,会产生多余的时间,这就需要我们选择如何使用,例如 什么产品可以“过剩”。E 列就是我们每周的生产计划。
F 列是按计划的月生产量(E x 4),在 G 列我们检查和 B 列的差异, 并在最后一周进行调整。
案例
改善2: 每周按 E 列模式重复生产,在最后一周进行调整。计划模拟的 结果:
改善效果:
每个产品可以在第2天就可以发货。比最初的情况(20天后 发货)时间利用率提高了90%!
差
别
案例
一个生产车间天, 每小时生产一个产品,可以生产以下六个不同颜色的产品。 市场平均每月需求量分摊如下:
案例
方法1:传统的计划 规模经济,批次生产,最大限度的减少换模时间 月初安排生产所需最长时间的产品,月底生产所需时间最少的产品
如果客户在本月第一天订购了每种产品(6种),必须等到 月底(20 个工作日)所有产品才可以开始发货。
生产线平衡分析改善案例

生产线平衡分析改善案例引言生产线平衡是指在生产过程中,通过合理分配各个工序的工作量,使得各个工序的产能能够实现平衡,从而提高生产效率、降低成本,并确保产品质量。
本文将以一个实际案例为例,介绍生产线平衡分析和改善的具体过程。
案例背景某电子产品制造公司拥有一条生产线,生产一种电子产品,该产品的组装工序分为A、B、C、D四个子工序。
在目前的生产线上,工序A的生产能力远超其他三个工序,导致A工序成为瓶颈工序,无法满足后续工序的需求,从而影响了整个生产线的效率和产量。
因此,公司决定进行生产线平衡分析,并制定改善方案,以提高生产线的平衡度。
生产线平衡分析1. 数据收集首先,需要收集工序A、B、C、D的工作时间数据,包括每个工序的加工时间、准备时间和等待时间。
这些数据将作为分析的基础。
2. 流程图绘制根据数据收集到的各个工序的时间,并结合实际生产情况,可以绘制出生产线的流程图。
流程图可以清晰地展示每个工序的工作时间和流程顺序,有助于进一步分析。
3. 生产线平衡计算根据流程图,可以计算出每个工序的工作时间总和。
然后,根据目标产量,计算出每个工序的标准工作时间,即每个工序应该占用的时间比例。
通过比较实际工作时间和标准工作时间,可以评估生产线的平衡度。
4. 分析结果根据生产线平衡计算的结果,可以看出工序A的工作时间远超其他工序,导致生产线的不平衡。
这也解释了为什么A工序成为瓶颈工序。
改善方案1. 调整工序A的产能由于工序A是瓶颈工序,可以考虑通过增加设备或优化工艺,提高工序A的产能,以满足后续工序的需求。
这可以通过增加工序A的设备数量、提高工段效率或优化工艺流程等手段实现。
2. 优化其他工序除了调整工序A的产能外,还可以进一步优化其他工序的流程,减少每个工序的工作时间。
例如,可以通过流程改进、工艺优化、培训员工等方式,提高其他工序的效率,从而平衡整个生产线。
3. 调整生产计划根据生产线平衡分析的结果,可以对生产计划进行合理调整。
均衡化生产改善案例
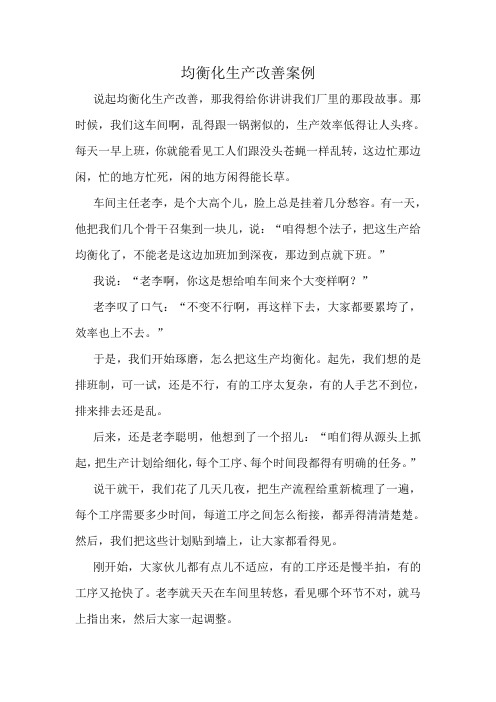
均衡化生产改善案例说起均衡化生产改善,那我得给你讲讲我们厂里的那段故事。
那时候,我们这车间啊,乱得跟一锅粥似的,生产效率低得让人头疼。
每天一早上班,你就能看见工人们跟没头苍蝇一样乱转,这边忙那边闲,忙的地方忙死,闲的地方闲得能长草。
车间主任老李,是个大高个儿,脸上总是挂着几分愁容。
有一天,他把我们几个骨干召集到一块儿,说:“咱得想个法子,把这生产给均衡化了,不能老是这边加班加到深夜,那边到点就下班。
”我说:“老李啊,你这是想给咱车间来个大变样啊?”老李叹了口气:“不变不行啊,再这样下去,大家都要累垮了,效率也上不去。
”于是,我们开始琢磨,怎么把这生产均衡化。
起先,我们想的是排班制,可一试,还是不行,有的工序太复杂,有的人手艺不到位,排来排去还是乱。
后来,还是老李聪明,他想到了一个招儿:“咱们得从源头上抓起,把生产计划给细化,每个工序、每个时间段都得有明确的任务。
”说干就干,我们花了几天几夜,把生产流程给重新梳理了一遍,每个工序需要多少时间,每道工序之间怎么衔接,都弄得清清楚楚。
然后,我们把这些计划贴到墙上,让大家都看得见。
刚开始,大家伙儿都有点儿不适应,有的工序还是慢半拍,有的工序又抢快了。
老李就天天在车间里转悠,看见哪个环节不对,就马上指出来,然后大家一起调整。
有一天,我正好碰到老李在跟一个年轻工人小张说:“小张啊,你这道工序得慢点儿,你得跟上那边的节奏,不能老是提前完成,不然后面的工序就乱了。
”小张挠挠头:“可是,我干得快,不是说明我效率高嘛?”老李笑了:“效率高是好,但得整体协调,你一个人快了,其他人就得跟着你跑,这不就乱套了?”小张点了点头,从那以后,他就开始注意自己的节奏,尽量跟其他人保持一致。
就这样,经过一段时间的努力,我们车间的生产终于慢慢均衡了起来。
每天上班,你再也看不到那种忙乱的现象了,每个工序都在有条不紊地进行着。
工人们脸上的笑容也多了,大家伙儿都觉得轻松了不少。
老李看着这一切,终于露出了久违的笑容:“看来,这均衡化生产还真是个好东西,咱们以后得继续坚持。
生产线平衡分析改善案例(PPT53张)

工位间和工位内的多余的WIP为零。
B值=1
一 物 流
物流
顺畅流动 没有停滞
物留
中间停滞 隐藏问题
“一个流”的益处
1. 内建品质管理; 2. 创造真正的灵活弹性; 3. 创造更高的生产力; 4. 腾出更多厂房空间; 5. 改善安全性; 6. 改善员工士气; 7. 降低存货成本。
生产线平衡定义
对生产的全部工序进行均衡,调整作业 负荷和工作方式,消除工序不平衡和工 时浪费,实现“一个流”。
入料
出料
平衡生产线的意义
通过平衡生产线可以综合应用到程序分析、动作分析 、layout分析,搬动分析、时间分析等全部IE手法,提 高全员综合素质 在平衡的生产线基础上实现单元生产,提高生产应变 能力,对应市场变化实现柔性生产系统 减少单件产品的工时消耗,降低成本(等同于提高人 均产量) 减少工序的在制品,真正实现“一个流” 提高作业及设备工装的工作效率
5、生产线平衡的计算
各工程净时间总计 生产线平衡率(%)= 时间最长工程*人员数 *100% 如上图表中,生产线平衡率= 1505 90*19 不平衡率(%)= 100% —平衡率(%) *100% = 88%
对生产线来说,不平衡率越小越好,一般控 制5%-13%之间,至少要控制在15%以下。
案例:工时测定和线平衡计算
降低线体速度,减少生产产量
减少人手(2) 工 作 時 間
因生产需求量降低而 可降低线体速度
将工序3﹑4的工作时 间分配至工序 1﹑2﹑5里﹐从而工 序3﹑4工作岗位的人 手可调配至其它生产 线去。
工序 1
精益生产之均衡化生产

绿色生产的融合
环保理念:注重环境保护减少 污染排放
绿色技术:采用环保技术和工 艺提高生产效率
循环经济:实现资源的循环利 用降低资源消耗
绿色供应链:建立绿色供应链 实现上下游企业的协同发展
定制化生产的趋势
个性化需求:消费者对个性化产品的需求日益增长 技术进步:3D打印、智能制造等技术的发展为定制化生产提供了可能 供应链管理:供应链管理技术的提升使得定制化生产更加高效和灵活
意义:均衡化生产可以 提高生产效率降低生产 成本提高产品质量增强 企业的竞争力。同时也 可以减少生产过程中的 浪费和环境污染符合可 持续发展的理念。
实现方式
采用先进的生产技术提高生产 效率
合理安排生产计划避免生产瓶 颈
加强供应链管理确保原材料供 应稳定
提高员工技能水平减少生产过 程中的浪费
适用范围
利实施
调整生产流程
确定生产瓶颈:分析生产过程中 的瓶颈环节找出影响生产效率的 因素
引入自动化设备:引入自动化设 备减少人工操作提高生产效率
添加标题
添加标题
添加标题
添加标题
优化生产流程:对瓶颈环节进行 优化提高生产效率
培训员工:对员工进行培训提高 他们的技能和素质提高生产效率
优化资源配置
确定生产目 标:明确生 产任务和生 产目标
环保意识:消费者对环保产品的需求增加定制化生产可以减少浪费降低环境影响
全球化生产的挑战与机遇
挑战:全球市场竞争激烈需要不断提高产品质量和降低成本 机遇:全球市场广阔可以扩大销售范围提高利润 挑战:全球供应链管理复杂需要加强供应链管理能力 机遇:全球供应链管理可以降低库存成本提高生产效率
THEME TEMPLATE
感谢观看
现场改善的着眼点——均衡化生产

现场改善的着眼点——均衡化生产均衡化生产①为了完成后工序拉动式生产,均衡化生产是必不可少的,例如:后工序今天需要100个产品,明天只需要5个,这样一来前工序就会有大量的库存,滞留多余的设备和人员。
均衡化就是要求生产平稳地、均衡地进行。
均衡化不仅要达到产量的均衡,而且还要保证品种、工时和生产负荷的均衡。
②实施均衡化生产时,循环表能够在某一条生产线上具体体现出生产比例。
当需要生产物品A50%、物品B30%、物品C20%时,我们就可以按照A●B●A●C●A●B●A●C●A●B的顺序决定批量,进行生产。
大批量生产与小批量生产大批量:把同一种产品在同一时间内集中起来进行生产,例如:50*1这种生产方式。
要生产50个产品时,把50个产品集中起来,一次性完成生产。
一般都认为批量越大生产效率越高,但事实情况往往并不是这样。
小批量:大批量生产不适用于均衡化生产,而且也不能及时对应客户需求,要尽可能地把批量减少,小批量生产的最高境界是一个流。
当要生产同一种产品50个时。
采用1*50的生产模式,一个一个地分成50次生产,每次只生产1个。
稼动率与可动率稼动率:设备实际运作时间占一天既定工作时间的比率。
例如,A 设备在一天8小时可以加工100个零部件,当某天需要加工70个零部件时,机器A的稼动率就是70%。
稼动率并非越高越好,而是取决于市场需求量。
可动率:想让机器运转的时候机器就能及时正常运转的比率,按下按钮就能马上进入工作状态。
在生产现场,想要及时准确地进行生产,可动率达100%是最理想的状态。
因此需要设备的及时点检和维护,排除故障。
提高可动率。
整体效率与局部效率整体效率:在精益生产理念指导下,不仅追求局部效率的提高,更注重的是全公司、整条生产线、所有设备效率的提高。
这样才能够达到事半功倍的效果。
局部效率:每个工序中、每条生产线和每台设备各自进行孤岛作业,不与前后工序保持一致,只是一味地想提高单个工序效率,结果却是徒劳无功。
均衡化生产2-平准化生产培训资料PPT课件
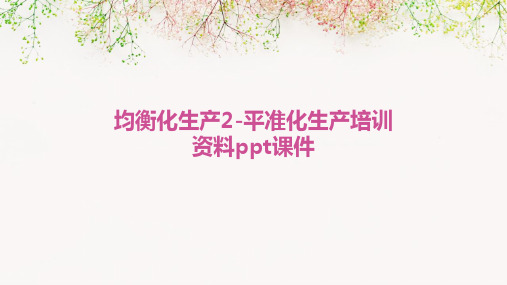
平准化生产的适用范围
02
平准化生产的原理和方法
生产计划的平准化是平准化生产的核心,它通过将生产计划分解为若干个较小的计划,使生产过程更加稳定和可控。
生产计划的平准化可以减少生产过程中的波动,提高生产效率和产品质量,降低库存和生产成本。
生产计划的平准化需要综合考虑市场需求、产品特点和生产能力等因素,制定合理的生产计划和调度方案。
均衡化生产2-平准化生产培训资料ppt课件
目 录
CONTENCT
平准化生产概述 平准化生产的原理和方法 平准化生产的实施步骤 平准化生产的优势和挑战 平准化生产的应用案例
01
平准化生产概述
平准化生产是指在生产过程中,通过调整生产计划和控制生产进度,实现均衡、稳定的生产,以满足市场需求和降低生产成本为目标的一种生产方式。
04
平准化生产的优势和挑战
优化资源配置
平准化生产能够根据市场需求合理配置人力、物力和财力资源,提高了资源利用效率。
提升生产线的协同效应
平准化生产要求生产线上的各个环节协同工作,提高了整个生产过程的协同效应,从而提高了生产效率。
减少生产过程中的浪费
平准化生产通过合理安排生产计划,避免了生产过剩或不足的问题,减少了生产过程中的浪费。
设备维护和管理难度大
02
平准化生产需要设备维护和管理方面的技术支持,以确保设备的稳定运行。解决方案是建立完善的设备维护和管理体系,加强技术人员的培训和交流。
人员素质和管理难度大
03
平准化生产需要高素质的员工和管理人员来实施。解决方案是加强员工培训和管理能力的提升,建立完善的员工培训和管理体系。
面临的挑战和解决方案
平准化生产强调在生产过程中保持稳定的生产节奏,避免生产波动和浪费,以提高生产效率和产品质量。
平准化生产

配套企业(乙)
这样的企业以后 可不能和他们合
作了。
配套企业(丙)
均衡化(平准化)生产
前月18日左右 下单
补充
销售店
库存
(销售库存)
库存
(只库存 销量好的)
均衡化
计划
生产管理部
工厂工务部
毎日的生产计划 (车辆整体)
次月确定 生产计划
确定每天的 毎日的零件 生产计划 使用量计划
每月、每天
(计划条件)
N+1 N+2
季・月・周・日
根据条件进行均等 的生产
每日按车序循环生产
第一类:总量均衡
均衡化(平准化)生产
为什么需要总量的均衡 化????
使大的幅度变为小的幅度!
如果现场的能力 发挥到最大值,
会导致设备 ・物・人的浪费
工
?
作
必 要
量
工
作
能
力
力? 必 要 工 作 能
时间
均衡化(平准化)生产
每天
按车型排均衡化 按零件排均衡化
收到没有库存 的车辆订单
15% 日变动 日计划变更(工厂生产的3天前)
补充库存的生产 -1
新订单
+1
85% 月度确定
如何实现平准化生产
100%均衡化
均衡化(平准化)生产
如何实现平准化生产①
・利用TT来做平准化生产
均衡化(平准化)生产
如何实现平准化生产②
(例):总装工序
5分 4分
(3)按照最高人员配置 (4)换车型时,更换所有零部件
(6)导致配套企业的抱怨,影响长期合作
3分
第二类:品种均衡
均衡化(平准化)生产
- 1、下载文档前请自行甄别文档内容的完整性,平台不提供额外的编辑、内容补充、找答案等附加服务。
- 2、"仅部分预览"的文档,不可在线预览部分如存在完整性等问题,可反馈申请退款(可完整预览的文档不适用该条件!)。
- 3、如文档侵犯您的权益,请联系客服反馈,我们会尽快为您处理(人工客服工作时间:9:00-18:30)。
别
案例
一个生产车间每天工作 7 小时、每周工作 5 天、每月工作 20 天, 每小时生产一个产品,可以生产以下六个不同颜色的产品。 市场平均每月需求量分摊如下:
案例
方法1:传统的计划 规模经济,批次生产,最大限度的减少换模时间 月初安排生产所需最长时间的产品,月底生产所需时间最少的产品
如果客户在本月第一天订购了每种产品(6种),必须等到 月底(20 个工作日)所有产品才可以开始发货。
F 列是按计划的月生产量(E x 4),在 G 列我们检查和 B 列的差异, 并在最后一周进行调整。
案例
改善2: 每周按 E 列模式重复生产,在最后一周进行调整。计划模拟的 结果:
改善效果:
每个产品可以在第2天就可以发货。比最初的情况(20天后 发货)时间利用率提高了90%!
案例
改善1: 将顺序反过来,月初生产需求量少的产品
改善效果:第12天就可以开始发货。
Hale Waihona Puke 案例改善2: 为了更快、更灵活的响应市场,必须要分批次
我们选择周为时间跨度。在下表,月需求量在 B 列,周平均需求量 在 C 列。我们只能离散制造完成的数量在 D 列(需要被四舍五入)。 四舍五入后,会产生多余的时间,这就需要我们选择如何使用,例如 什么产品可以“过剩”。E 列就是我们每周的生产计划。