氨水处理
氨水处置方案
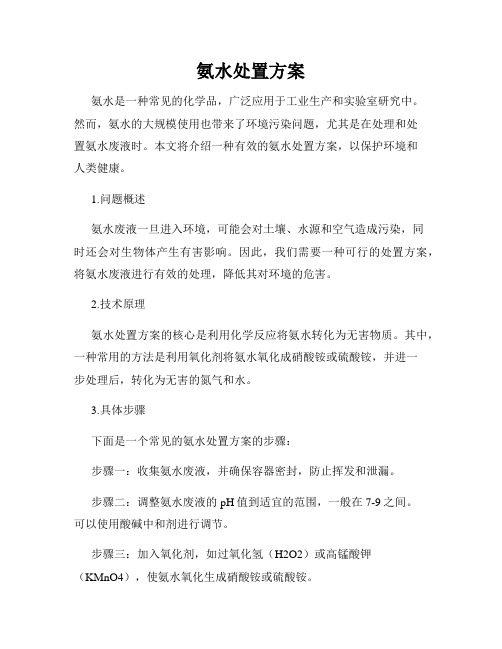
氨水处置方案氨水是一种常见的化学品,广泛应用于工业生产和实验室研究中。
然而,氨水的大规模使用也带来了环境污染问题,尤其是在处理和处置氨水废液时。
本文将介绍一种有效的氨水处置方案,以保护环境和人类健康。
1.问题概述氨水废液一旦进入环境,可能会对土壤、水源和空气造成污染,同时还会对生物体产生有害影响。
因此,我们需要一种可行的处置方案,将氨水废液进行有效的处理,降低其对环境的危害。
2.技术原理氨水处置方案的核心是利用化学反应将氨水转化为无害物质。
其中,一种常用的方法是利用氧化剂将氨水氧化成硝酸铵或硫酸铵,并进一步处理后,转化为无害的氮气和水。
3.具体步骤下面是一个常见的氨水处置方案的步骤:步骤一:收集氨水废液,并确保容器密封,防止挥发和泄漏。
步骤二:调整氨水废液的pH值到适宜的范围,一般在7-9之间。
可以使用酸碱中和剂进行调节。
步骤三:加入氧化剂,如过氧化氢(H2O2)或高锰酸钾(KMnO4),使氨水氧化生成硝酸铵或硫酸铵。
步骤四:对生成的硝酸铵或硫酸铵进行进一步的处理。
可以使用一些方法,如沉淀剂、离子交换剂或高温分解等,将其转化为无害的氮气和水。
步骤五:对处置后的液体进行中和处理,以确保其酸碱度在可接受范围内。
4.注意事项在进行氨水处置时,还需要注意以下几点:- 操作人员必须具备相关的化学知识和实验技能,遵循安全操作规程,佩戴个人防护装备。
- 废液处理过程中产生的废物应按照有关法规进行妥善处置,以减少二次污染的可能性。
- 处理后的水可能仍然含有微量的氨水或其他有机物,因此应进行监测和分析,确保处理效果达到要求。
5.结论通过上述氨水处置方案,可以将氨水废液有效地转化为无害物质,减少对环境的污染。
然而,在实际操作中,考虑到不同情况和需求,可能需要针对具体情况进行适当的调整和优化。
因此,在选择氨水处置方案时,有必要进行充分的研究和实验验证,确保方案的可行性和可靠性。
通过采取适当的氨水处置方案,我们可以更好地保护环境,实现可持续发展。
线路板中氨水的使用用途
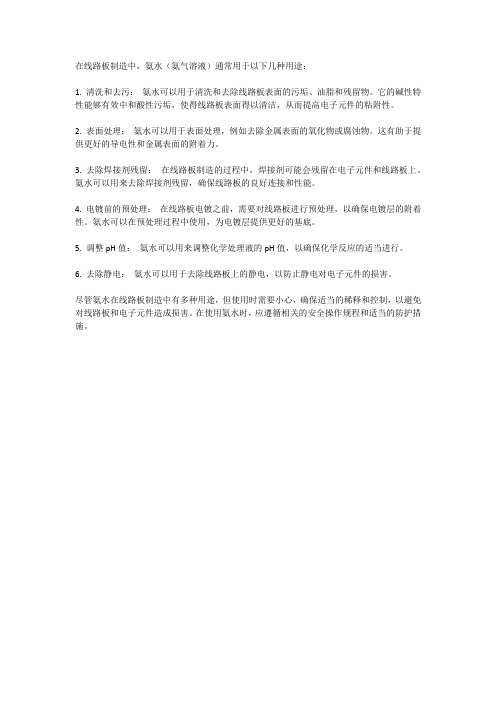
在线路板制造中,氨水(氨气溶液)通常用于以下几种用途:
1. 清洗和去污:氨水可以用于清洗和去除线路板表面的污垢、油脂和残留物。
它的碱性特性能够有效中和酸性污垢,使得线路板表面得以清洁,从而提高电子元件的粘附性。
2. 表面处理:氨水可以用于表面处理,例如去除金属表面的氧化物或腐蚀物。
这有助于提供更好的导电性和金属表面的附着力。
3. 去除焊接剂残留:在线路板制造的过程中,焊接剂可能会残留在电子元件和线路板上。
氨水可以用来去除焊接剂残留,确保线路板的良好连接和性能。
4. 电镀前的预处理:在线路板电镀之前,需要对线路板进行预处理,以确保电镀层的附着性。
氨水可以在预处理过程中使用,为电镀层提供更好的基底。
5. 调整pH值:氨水可以用来调整化学处理液的pH值,以确保化学反应的适当进行。
6. 去除静电:氨水可以用于去除线路板上的静电,以防止静电对电子元件的损害。
尽管氨水在线路板制造中有多种用途,但使用时需要小心,确保适当的稀释和控制,以避免对线路板和电子元件造成损害。
在使用氨水时,应遵循相关的安全操作规程和适当的防护措施。
氨水应急预案
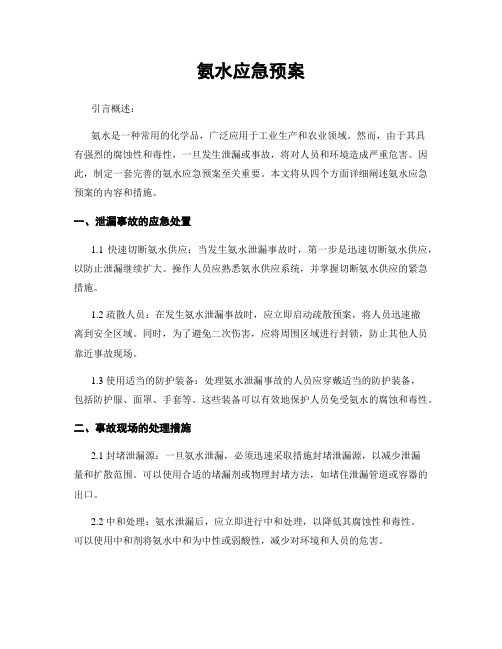
氨水应急预案引言概述:氨水是一种常用的化学品,广泛应用于工业生产和农业领域。
然而,由于其具有强烈的腐蚀性和毒性,一旦发生泄漏或事故,将对人员和环境造成严重危害。
因此,制定一套完善的氨水应急预案至关重要。
本文将从四个方面详细阐述氨水应急预案的内容和措施。
一、泄漏事故的应急处置1.1 快速切断氨水供应:当发生氨水泄漏事故时,第一步是迅速切断氨水供应,以防止泄漏继续扩大。
操作人员应熟悉氨水供应系统,并掌握切断氨水供应的紧急措施。
1.2 疏散人员:在发生氨水泄漏事故时,应立即启动疏散预案,将人员迅速撤离到安全区域。
同时,为了避免二次伤害,应将周围区域进行封锁,防止其他人员靠近事故现场。
1.3 使用适当的防护装备:处理氨水泄漏事故的人员应穿戴适当的防护装备,包括防护服、面罩、手套等。
这些装备可以有效地保护人员免受氨水的腐蚀和毒性。
二、事故现场的处理措施2.1 封堵泄漏源:一旦氨水泄漏,必须迅速采取措施封堵泄漏源,以减少泄漏量和扩散范围。
可以使用合适的堵漏剂或物理封堵方法,如堵住泄漏管道或容器的出口。
2.2 中和处理:氨水泄漏后,应立即进行中和处理,以降低其腐蚀性和毒性。
可以使用中和剂将氨水中和为中性或弱酸性,减少对环境和人员的危害。
2.3 清理和处理废物:在事故现场清理过程中,应注意收集和处理泄漏的氨水和中和剂,以防止二次污染。
废物应按照相关法规和规定进行妥善处理,以确保环境的安全。
三、事故后的善后工作3.1 事故调查和分析:事故发生后,必须进行详细的事故调查和分析,找出事故的原因和责任。
通过分析事故原因,可以采取相应的措施,防止类似事故再次发生。
3.2 事故报告和通知:事故发生后,应及时向相关部门和当地政府报告,并通知相关单位和人员。
报告和通知的内容应包括事故的情况、处理过程和善后措施等,以便及时采取必要的措施。
3.3 事故经验总结和培训:事故发生后,应对事故进行经验总结,并将总结的经验应用于培训和教育中。
氨水应急处置卡

氨水应急处置卡简介本文档提供了氨水应急处置卡的相关信息和指导。
氨水是一种常见的化工品,在使用和储存中可能发生泄漏或事故。
了解正确的应急处置措施对于处理这种情况至关重要。
危险特性- 氨水有刺激性气味,可对眼睛、皮肤和呼吸道造成伤害。
- 氨水有腐蚀性,可能导致化学灼伤。
应急处置步骤1. 保护自身:戴好个人防护装备,包括防护眼镜、防护手套、呼吸器等。
2. 确定泄漏源:查找泄漏来源,并尽可能停止泄露。
3. 隔离区域:立即将周围人员疏散到安全区域,确保不会造成更多的伤害和污染。
4. 通风:打开门窗,增强通风,尽可能减少有害气体浓度。
5. 清除泄漏物:使用吸收剂或稀释剂将氨水泄漏物迅速吸收或稀释。
将液体收集到密封中,将固体收集并包装妥善处置。
6. 处理废物:正确处理氨水泄漏物和清理用具,遵守相关法规和安全操作规程。
7. 报告和记录:向相关管理部门报告事故情况,并详细记录事故经过和处置措施。
注意事项- 氨水泄漏后容易蒸发并形成易燃的氨气,避免明火和高温源。
- 避免与其他化学物品混合使用,以免发生危险反应。
- 接触氨水后,立即用大量清水冲洗受影响的皮肤和眼睛,并寻求医疗帮助。
- 不要遗留泄漏物的残余物,必须妥善处置和处理。
以上是对氨水应急处置的基本指导,具体情况下请参考相关法律法规和专业人员的建议。
---注意: 本文档提供的信息仅供参考。
在应急处置过程中,务必遵循相关法律法规和安全操作规程。
本文档内容是否准确需要根据被处理情况的具体情况进行确认。
氨水泄漏应急处理操作规程

氨水泄漏应急处理操作规程氨水泄漏是一种危险、有毒、易燃的化学物质泄漏事故,对人体和环境都具有潜在的危害。
为了及时有效的处理氨水泄漏事故,保护人员的生命安全和减少环境污染,必须制定一套科学合理的应急处理操作规程。
以下是一个关于氨水泄漏应急处理操作规程的示例,供参考。
一、事故发生后应急响应1.发现氨水泄漏事故时,立即将人员远离危险区域,避免接触有毒气体。
2.将有关人员通知到场,包括安全人员、环保人员、医疗救援人员等。
3.向有关部门和当地政府报告事故情况,请求协助和指导。
4.在确保安全的前提下,尽可能迅速进行现场评估,判断泄漏规模和可能的影响范围。
5.根据事故规模和影响范围,及时做出相应的应急决策,制定详细的应急处理方案。
二、危险区域控制1.在事故发生区域周围建立合理的警戒线或封锁区域,杜绝非相关人员进入。
2.在泄漏源周围设置喷淋装置或雾化装置,以减少氨气扩散。
3.制定有效的通风方案,确保有足够的新鲜空气进入泄漏区域。
4.配备相应的个人防护装备,包括呼吸器、防护手套、防护服等,并要求事故处理人员佩戴。
三、停止泄漏源1.在保证安全的情况下,尝试关闭漏气设备的阀门或切断电源。
2.使用合适的材料或方法将漏气设备进行封堵,阻止氨水继续泄漏。
四、泄漏处置1.根据泄漏规模和影响范围,制定详细的泄漏处置方案,确保处理过程安全有效。
2.使用合适的泄漏清除剂或吸附剂对泄漏液体进行吸收和清除,防止进一步扩散。
3.将清除后的泄漏物进行正确的处置,切勿随意倾倒或排放到环境中。
4.对可能被氨水熏蒸的设备、管道和场地进行清洗和消毒,确保无二次污染。
五、事后处理和监测1.对事故现场进行彻底的清理和整理,恢复正常的生产和作业秩序。
2.进行事故原因的调查和分析,找出事故的根本原因,采取相应的措施进行改进。
3.对泄漏现场和周边环境进行监测,确保没有残留氨水或其他污染物。
4.对参与应急处置的人员进行医学观察和健康监测,预防可能的后续健康问题。
氨水泄露应急处理预案

氨水泄露应急处理预案一、背景:氨水(NH3)是一种常见的化学品,在工业生产和化学实验中经常使用。
然而,氨水泄露事故可能会对人员健康和环境造成严重影响,因此建立一套完善的应急处理预案至关重要。
二、氨水泄露应急处理预案:2.1 报警与通知•在发生氨水泄露事故时,首先立即启动报警系统并通知安全责任人员。
•安全责任人员应立即按照预定程序通知相关部门和人员,包括消防部门、环保部门和紧急救援人员。
2.2 人员安全•当发生氨水泄露事故时,应立即疏散泄露区域的人员。
•所有人员应遵循疏散路线和疏散指示,迅速撤离到安全地点。
•使用个人防护装备(如呼吸器、防护服等)的人员应检查装备是否齐全并正确佩戴。
2.3 封锁泄露源•安全责任人员应尽快到达泄露源附近,并确保自身安全的情况下,封锁泄露源。
•封锁泄露源的方法包括关闭泄露阀门或阀门、堵塞泄漏管道等。
2.4 化学品清理•使用专门的化学品吸收剂或惰性物质(如沙土、干净的土壤)吸收泄露的氨水。
•将吸收的废料和泄露物品转移到专用容器中,并妥善处理。
2.5 通风与除污•对泄露区域进行通风,以促进氨水的挥发。
•使用适当的除臭剂或消毒剂,对泄露区域进行消毒和除污处理。
2.6 事故调查与报告•氨水泄露事故处理完成后,应立即进行事故调查,查明事故原因。
•详细记录事故的经过、应急处理过程以及可能存在的问题和教训。
•根据事故调查结果,及时向相关部门和人员进行事故报告,并提出改进措施和建议。
三、应急演练与培训•针对氨水泄露事故,定期组织应急演练,确保所有相关人员熟悉应急处理预案和操作流程。
•提供必要的培训和技能提高,使相关人员能够正确、迅速地应对氨水泄露事故。
四、相关法律法规与标准•在制定氨水泄露应急处理预案时,必须遵守相关的法律法规和标准,确保预案的合规性和可操作性。
•包括但不限于《中华人民共和国安全生产法》、《化学品安全管理条例》等。
五、预案评估与改进•定期对氨水泄露应急处理预案进行评估,检查预案的可行性和有效性。
最新氨水的危害及相关应急处理措施
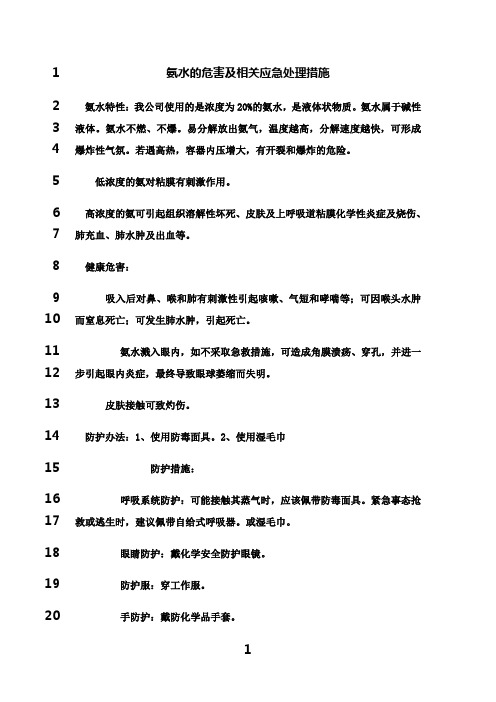
1氨水的危害及相关应急处理措施2氨水特性:我公司使用的是浓度为20%的氨水,是液体状物质。
氨水属于碱性3液体。
氨水不燃、不爆。
易分解放出氨气,温度越高,分解速度越快,可形成4爆炸性气氛。
若遇高热,容器内压增大,有开裂和爆炸的危险。
5低浓度的氨对粘膜有刺激作用。
6高浓度的氨可引起组织溶解性坏死、皮肤及上呼吸道粘膜化学性炎症及烧伤、7肺充血、肺水肿及出血等。
8健康危害:9吸入后对鼻、喉和肺有刺激性引起咳嗽、气短和哮喘等;可因喉头水肿10而窒息死亡;可发生肺水肿,引起死亡。
11氨水溅入眼内,如不采取急救措施,可造成角膜溃疡、穿孔,并进一12步引起眼内炎症,最终导致眼球萎缩而失明。
13皮肤接触可致灼伤。
14防护办法:1、使用防毒面具。
2、使用湿毛巾15防护措施:16呼吸系统防护:可能接触其蒸气时,应该佩带防毒面具。
紧急事态抢17救或逃生时,建议佩带自给式呼吸器。
或湿毛巾。
18眼睛防护:戴化学安全防护眼镜。
19防护服:穿工作服。
20手防护:戴防化学品手套。
21其它:工作现场禁止吸烟、进食和饮水。
工作后,淋浴更衣。
保持良22好的卫生习惯。
23急救措施:24皮肤接触:一旦氨水沾污皮肤,先用清水或2%的食醋液冲洗。
立即用25水冲洗至少15分钟。
若有灼伤,就医治疗。
若皮肤局部出现红肿、水泡,可用262%的食醋液冲洗。
27眼睛接触:立即提起眼睑,用流动清水或生理盐水冲洗至少15分钟。
28或用3%硼酸溶液冲洗。
立即就医。
29吸入:迅速脱离现场至空气新鲜处。
保持呼吸道通畅。
呼吸困难时给30输氧。
呼吸停止时,立即进行人工呼吸。
就医。
31食入:误服者立即漱口,口服稀释的醋或柠檬汁,就医。
32灭火方法:雾状水、二氧化碳、砂土。
33当发现有氨水吸入中毒者(出现呼吸道、眼、鼻、皮肤粘膜的严重刺34激感,并伴随咳嗽、流涕、发痒、气促、紫绀、烦躁等症状),应让他迅速离开35现场,并脱去被氨水污染的衣、裤,尽快去医院,以免发生意外。
36可能发生的情况:371、在氨水装卸过程中,管道破裂泄漏。
氨水应急预案

氨水应急预案一、泄漏应急处理疏散泄漏污染区人员至安全区,禁止无关人员进入污染区,建议应急处理人员戴自给式呼吸器,穿化学防护服。
不要直接接触泄漏物,在确保安全情况下堵漏。
用大量水冲洗,经稀释的洗水放入废水系统。
用沙土、蛭石或其它惰性材料吸收,然后以少量加入大量水中,调节至中性,再放入废水系统。
如大量泄漏,利用围堤收容,然后收集、转移、回收或无害处理后废弃。
二、健康危害1、侵入途径:吸入、食入。
2、健康危害:吸入后对鼻、喉和肺有刺激性引起咳嗽、气短和哮喘等;可因喉头水肿而窒息死亡;可发生肺水肿,引起死亡。
氨水溅入眼内,如不采取急救措施,可造成角膜溃疡、穿孔,并进一步引起眼内炎症,最终导致眼球萎缩而失明。
皮肤接触可致灼伤。
3、慢性影响:反复低浓度接触,可引起支气管炎。
皮肤反复接触,可致皮炎,表现为皮肤干燥、痒、发红。
三、防护措施1、呼吸系统防护:可能接触其蒸气时,应该佩带防毒面具。
紧急事态抢救或逃生时,建议佩带自给式呼吸器。
2、眼睛防护:戴化学安全防护眼镜。
3、防护服:穿工作服。
4、手防护:戴防化学品手套。
5、其它:工作现场禁止吸烟、进食和饮水。
工作后,淋浴更衣。
保持良好的卫生习惯。
四、急救措施1、皮肤接触:一旦氨水沾污皮肤,先用清水或2%的食醋液冲洗。
立即用水冲洗至少15分钟。
若有灼伤,就医治疗。
若皮肤局部出现红肿、水泡,可用2%的食醋液冲洗。
2、眼睛接触:立即提起眼睑,用流动清水或生理盐水冲洗至少15分钟。
或用3%硼酸溶液冲洗。
立即就医。
3吸入:迅速脱离现场至空气新鲜处。
保持呼吸道通畅。
呼吸困难时给输氧。
呼吸停止时,立即进行人工呼吸。
就医。
若鼻粘膜受到强烈的刺激,可滴入1%的麻黄素溶液,重者应吸入糜蛋白酶。
4、食入:误服者立即漱口,口服稀释的醋或柠檬汁,就医。
五、灭火方法:雾状水、二氧化碳、砂土。
发现氨水吸入中毒者(出现呼吸道、眼、鼻、皮肤粘膜的严重刺激感,并伴随咳嗽、流涕、发痒、气促、紫绀、烦躁等症状),应让他迅速离开现场,并脱去被氨水污染的衣、裤;口服食醋50-100毫升,同时服用维生素c50毫克,每日3次;并应请医生急诊治疗,以免发生意外。
- 1、下载文档前请自行甄别文档内容的完整性,平台不提供额外的编辑、内容补充、找答案等附加服务。
- 2、"仅部分预览"的文档,不可在线预览部分如存在完整性等问题,可反馈申请退款(可完整预览的文档不适用该条件!)。
- 3、如文档侵犯您的权益,请联系客服反馈,我们会尽快为您处理(人工客服工作时间:9:00-18:30)。
Nano Res (2010) 3: 126–137 126Microwave Synthesis of Large Few-Layer Graphene Sheets in Aqueous Solution of AmmoniaIzabela Janowska1 ( ), Kambiz Chizari1, Ovidiu Ersen2, Spyridon Zafeiratos1, Driss Soubane1, Victor Da Costa2, Virginie Speisser2, Christine Boeglin2, Matthieu Houllé1, Dominique Bégin1, Dominique Plee3, Marc-Jacques Ledoux1, and Cuong Pham-Huu11 Laboratoire des Matériaux, Surfaces et Procédés pour la Catalyse (LMSPC), UMR7515 CNRS-Université de Strasbourg 25, rue Becquerel, 67087 Strasbourg Cedex 08, France2Institut de Physique et Chimie des Matériaux de Strasbourg (IPCMS), UMR7504 CNRS-Université de Strasbourg 23, rue du Loess, 67037 Strasbourg Cedex 02, France3 Arkema, Groupement de Recherche de Lacq (GRL), BP 34, 64170 LACQ, FranceReceived: 9 November 2009 / Revised: 10 December 2009 / Accepted: 12 December 2009© The Author(s) 2010. This article is published with open access at ABSTRACTFew-layer graphene (FLG) sheets with sizes exceeding several micrometers have been synthesized by exfoliation of expanded graphite in aqueous solution of ammonia under microwave irradiation, with an overall yield approaching 8 wt.%. Transmission electron microscopy (in bright-field and dark-field modes) together with electron diffraction patterns and atomic force microscopy confirmed that this graphene material consisted mostly of mono-, bi- or few-layer graphene (less than ten layers). The high degree of surface reduction was confirmed by X-ray photoelectron and infrared spectroscopies. In addition, the high stability of the FLG in the liquid medium facilitates the deposition of the graphene material onto several substrates via low-cost solution-phase processing techniques, opening the way to subsequent applications of the material. KEYWORDSGraphene, transmission electron microscopy (TEM), expanded graphite exfoliation, microwavesIntroductionGraphene has been attracting increasing scientific attention owing to its outstanding physical properties [1]. Since the first attempt to isolate an individual graphene sheet, which is a monolayer of sp2 bonded carbon [2], numerous studies have been devoted to its synthesis with the aim of improving the overall yield and reproducibility, in order to be able to exploit its various possible applications [3–5]. Graphene sheets are mostly prepared by physical methods such as micro-mechanical cleavage of graphite [2], chemical reduction of exfoliated graphite oxide [6], growth of graphene sheets on metal substrates [7], or vacuum annealing of SiC single crystals [8].In order to improve the yield of the resulting graphene material, several different approaches have recently been proposed. Dato et al.[9] synthesized graphene sheets in a gas-phase medium using ethanol as carbon source and a microwave argon plasma reactor at atmospheric pressure. In the study of Dresselhaus and co-workers [10], large (micrometerNano Res (2010) 3: 126–137DOI 10.1007/s12274-010-1017-1 Research ArticleAddress correspondence to janowskai@unistra.frsize) graphene sheets were synthesized by chemical vapor deposition (CVD) on a nickel film. Very recently, four new methods have been reported for unzipping a carbon nanotube lengthways [3, 11–14]. One method is based on the use of strong oxidizing reagents, e.g., H2SO4/KMnO4, whilst a second one uses the parallel insertion of metal atoms, e.g., Li, in the presence of liquid ammonia followed by a thermal treatment. Regarding these chemical unzipping routes, problems associated with the use of hazardous chemical reagents, and thus the waste disposal, need to be addressed. A third method employs plasma etching to cut nanotubes lengthways after embedding them into a polymer film. The last method reports the synthesis of graphene by catalytic unzipping of carbon nanotubes under microwave irradiation. The as-synthesized graphene materials can be further self-assembled in a liquid medium after partial reduction leading to the formation of millimeter size superstructures similar to the ones reported by Biswas and Drzal [15].Liquid phase exfoliation of graphite or graphite oxide (GO) by chemical solvents has also been reported by several groups. Hernandez et al.[16] reported the synthesis of graphene sheets by liquid phase exfoliation of graphite—which is the most readily available and least expensive precursor of graphene—in various solvents with yields ranging between 1 wt.% and 12 wt.%. The resulting graphene sheets consisted mostly of mono- and/or few-layer graphene sheets with sizes of a few hundred nanometers. Microwave synthesis of exfoliated graphite nanoplatelets has also been reported [17]. However, the average lateral size of the graphite nanoplatelets was somewhat smaller than that obtained in the present work (lateral sizes of several micrometers).1. Methods1.1MaterialsThe expanded graphite used in the present work was purchased from Carbone Lorraine. Ultrapure Milli-Q®water was used for all experiments and the ammonia solution was supplied by Carlo Erba (99.9%) and used as received. 1.2Graphene synthesisThe expanded graphite (EG) with different concent- rations (0.01–1.0 mg/mL) was dispersed in the liquid phase, i.e. distilled water and aqueous solution of ammonia (33 wt.% and 16 wt.%). The dispersion was homogenized by sonication in a low-power sonic bath for 30 min. The sediment was separated by filtration and dried before further processing.The microwave experiments were carried out on a Mars (CEM Corp.) microwave oven with the following characteristics: adjustable power between 300 and 1200 W and maximum temperature of 250 °C. The microwave irradiation was set at 300 W, keeping the temperature between 120 and 200 °C for 60–120 min. The FLG sheets were formed as a suspension in the aqueous phase above the solid residual EG. In order to extract as much as possible of the FLG from the starting EG, the mixture was sonicated for 30 min followed by a decantation step. In the case of pure water as a solvent, the colourless suspension of the graphene sheets was separated from the starting EG by decantation or extraction with a toluene–ammonia (aq.) system, due to the low concentration of the FLG material in the solution.1.3CharacterisationThe morphologies of the EG and the FLG recovered after the microwave synthesis were analyzed on a JEOL 6700 scanning electron microscope (SEM). The microstructure of the as-synthesized samples was investigated by transmission electron microscopy (TEM) on a JEOL 2100 field-emission gun (FEG) microscope operated under an acceleration voltage of 200 kV. TEM measurements were made by drop casting of the FLG dispersion onto holey carbon grids. The XPS measurements were performed on a Thermo VG spectrometer, using Al Kα radiation (hν= 1486.6 eV). The base chamber pressure was 2 ×10–10 mbar. Survey and high-resolution spectra were recorded in constant pass energy mode (100 and 20 eV, respectively). The binding energy scale of SiO2-supported graphene layers was corrected for electrostatic charging using the C 1s peak at 284.5 eV as an internal reference. A Shirley background was subtracted for all spectra. Attenuated total reflectance–Fourier transform infrared (ATR–FTIR) spectra were recorded on a Shimadzu Spectrum 100system. The AFM measurements were performed with a Digital Instruments Nanoscope. A diluted FLG dispersion in toluene (0.1 mg/mL) was spin coated (with a speed of 800 r/min) on a SiO2/Si wafer and examined by AFM in a tapping mode. Scanning tunneling microscopy (STM) was performed in order to ascertain whether the as-synthesized FLG sheets were conductive and also to obtain more insight into the material roughness and regularity. For the thermal treatments, the sample was transferred into a separate chamber and the sample holder was connected to a tungsten filament which played the role of a heating source and allowed thermal treatments up to 600 °C. The thermal treatment was carried out under a dynamic vacuum of 10–9 mbar, which provides a rapid desorption of adsorbed impurities on the FLG surface.2. Results and discussionIn this work, we report the synthesis of large few-layer graphene (FLG) sheets with sizes of a few tenths to a hundred micrometers and their detailed characteri- zation. We show that graphene material with relatively high quality, i.e., low oxygen decoration and large size, can be prepared in high yields by microwave treatment of expanded graphite in aqueous solution of ammonia at low temperatures (below 200 °C). In a previous paper, we have reported that FLG sheets could be produced by catalytic unzipping of carbon nanotubes in water under microwave irradiation [12], although the resulting FLG possessed a relatively high amount of oxygenated functional groups on its surface. In the present work, water is replaced by ammonia which displays a higher reducibility and hence may prevent the incorporation of oxygenated groups into the synthesized FLG. Moreover, the decomposition products of ammonia are also less harmful than other chemical products used to date to synthesize graphene in liquid media. The synthesis of FLG in ammonia could also open a new field of research dealing with the production of nitrogen-doped graphene. As far as the synthesis of graphene-like materials via chemical routes is concerned, this is the first time that FLG sheets with such large sizes have been reported. Our results show that the ammonia concentration can drastically influence the exfoliation of the expanded graphite as well as the dimensions of the final FLG sheets. In addition, the FLG formed by this versatile and easily scalable method is in the form of a stable suspension in the reaction medium that can be further processed or deposited on a variety of substrates for downstream applications.2.1Influence of the ammonia concentrationThe microstructure of the sample formed after micro- wave irradiation was investigated by transmission electron microscopy (TEM). Typical TEM images of the FLG sheets at different magnifications are pre- sented in Fig. 1. A low-magnification TEM micrograph (Fig. 1(a)) shows part of a micrometer size FLG material that is made up of smaller individual graphene sheets. The FLG sheets constituting the assembly exhibit a relatively sharp border (Fig. 1(a)) and statistical TEM analysis indicates that their average size is about 10 µm (see Section S-4 in the Electronic Supplementary Material (ESM)). General TEM views of the graphene sheet assembly show the crumpled structure of the FLG sheet (Figs. 1(b) and 1(c)). Such crumpled structure allows the sheet to accommodate the high aspect ratio of the material without scrolling [18, 19]. The high- resolution TEM micrograph taken at the border of the FLG sheet (Fig. 1(d)) clearly shows the number of graphene layers of the FLG, i.e., five layers. A quantitative analysis is possible in this case due to the particular morphology of the graphene sheets, whereas they are usually scrolled and partially folded at their edges [20]. By statistical analysis of a large number of graphene flakes, we can conclude that the graphene sheets formed by exfoliation of expanded graphite in a ammonia solution (33 wt.%) are made up of no more than ten layers.Furthermore, the size of the as-synthesized FLG sheets is also influenced by the ammonia concen- tration in the solution (see Fig. S-2 in the ESM). At high ammonia concentrations, extremely large graphene sheets with a lateral size exceeding a hundred micro- meters were observed, whereas at lower ammonia concentrations, the average size of the FLG was centered around 10 µm. It seems that the FLG sheets retain their planar morphologies on the TEM grid after the evaporation of the solution. This suggests that the large graphene sheets can be directly deposited onplanar substrates for relevant applications. Again, typical TEM images (Fig. 2(a)) show that the edges of the sheets are generally scrolled and partially folded due to the high surface tension needed for the material to maintain its planarity over a large distance. Indeed, perfect 2-D atomic crystals cannot exist as such without scrolling, unless they are of limited size or contain many crystal defects [21]. The crystallographic structure of the sheet was determined using the selected area electron diffraction (SAED) technique which probes the whole reciprocal lattice of the sample. The SAED pattern of an assembly of three superposed sheets (Fig. 2(b)) is presented in Fig. 2(c) and corresponds to the superposition of three hexagonal lattices, one principal one with strong reflections and two others rotated slightly in-plane with respect to the first one. The typical sixfold symmetry of the pattern comes from the crystallographic structure of the graphene — composed by carbon atoms arranged in a strictly 2-D honeycomb —in real space. To label the diffraction peaks, we use the Miller–Bravais indices {hkil } of graphite, putting the last index l = 0. The two main distances determined by frequency analysis of the spots in the innermost and the next hexagon are 2.13 Å (corresponding to the {1100} spots) and 1.23 Å ({1120} spots), respectively. Such a diffraction pattern suggests the presence of several layers in the graphene sheet assembly (see Section S-4 in the ESM). High-resolution TEM images next to the edge confirm that this FLG is made of two double layer graphene sheets, visualized as two sets of dark lines running in a parallel direction (Fig. 2(d)). Such FLG sheets could be formed by van der Waals forces during the stabilization of the material in solution. It is thought that these sheet assemblies were formed by π-stacking of the graphene material formed during the synthesis or during the cooling step. In fact, these aggregates can be easily re-dispersed by mild sonication.In order to evaluate the typical number of graphenelayers in the dispersed sheets, SAED was utilized toFigure 1 (a) General view of the as-synthesized graphene sheet (using an aqueous solution with 33 wt .% of ammonia) with a width of several micrometers. (b) Closer TEM view of the FLG sheets showing that they are made up of several individual sheets with crumpled morphologies due to their high aspect ratio. (c) Border view of the graphene sheet showing the curled structure of the sheet. (d) High-magnification TEM view of the curled border showing the number of graphene layers forming the graphene sheet. In this micrograph,there are five layers spaced with an interplanar distance of ca. 0.34 nmanalyze several FLG sheets from different samples. This technique allows confident identification of single graphene layers by comparing the peak intensities from the innermost hexagon of the diffraction pattern with those of the next one [16]. In particular, if the multi-layers retain the Bernal (AB) stacking of the material source, which is generally the case for few-layer sheets prepared from graphite, the {2110} spots appear to be more intense than the {1100} spots, whereas for single graphene layers this intensity ratio is reversed. Such an analysis was performed on typical graphene flakes, focusing on their edges. The TEM images suggest the presence of two individual sheets superposed at the edge of the flake (Fig. 3(a)). This observation is confirmed by the analysis of the diffraction pattern that shows the presence of two parallel hexagonal lattices slightly rotated around the perpendicular axis of the hexagon (Fig. 3(a) insert). By comparing the intensity of the {2110} and {1100} spots belonging to each hexagonal lattice, we can conclude that one of the sheets is a single-layer while the other is few-layer. Moreover, the separation in reciprocal space of the spots belonging to the two lattices allows one to visualize each graphene sheet individually, by selecting one of the two equivalent spots with the objective aperture and thus obtaining the corresponding dark field image. As a result it is possible to visualize either or both graphene sheets (by selecting both spots, Fig. 3(b)), or only one of them(Figs. 3(c) and 3(d)).Figure 2 (a) Border view of the FLG sheets showing that each individual sheet is partly folded onto itself. (b) TEM image of an assembly of three superimposed and relatively flat graphene flakes with slight in-plane disorientations between them. (c) Selected area electron diffraction (SAED) pattern of the three graphene sheets depicted in (b). The pattern is indexed using the Miller–Bravais indices for graphite with the Bragg reflections of the innermost hexagon of (0-110) type (2.13 Å spacing) and those of the next hexagon of (-1-120) type (1.23 Å spacing). (d) High-resolution TEM micrograph of the curled border revealing the superposition of two double graphene sheets. The spacing measured between the two contrasted lines is close to 0.34 nmGraphene sheets formed by reaction in water are thicker with smoother borders those synthesized in aqueous solution of ammonia, allowing high-resolution micrographs to be obtained without damaging the sheets with the electron beam (see Fig. S-5 in the ESM). According to the observed results one can state that the nature of the liquid medium has a substantial influence on both the morphology and the microstructure of the graphene layers. TEM analysis carried out on several samples synthesized in aqueous solution of ammonia indicated that the resulting FLG sheets were relatively homogeneous in thickness, with a maximum of ten layers. The results suggest that expanded graphite has been extensively exfoliated to give only few-layer graphene sheets with a yield of around 8 wt.%.The electrical conductivity of the FLG, recovered after 1 h of settling, and spin coated (with a speed of 800 r/min) on a glass substrate with patterned gold was also measured. The thickness of the FLG film deposited onto a SiO 2/Si wafer was ca. 400 nm. The electrical conductivity of the sample deposited at room temperature was 2.5 S/m, which is comparable to that reported in other work, and steadily increased after reduction of the sample in flowing H 2 at 200 °C for 2 h, eventually reaching 250 S/m[22]. Such resultsFigure 3 (a) Representative TEM image of an area where only two superposed and relatively flat graphene sheets are present. The SAED pattern taken with an aperture of 250 nm on the area marked by the white circle is shown in the insert. The Bragg reflections are indexed using the Bravais–Miller indices for graphite. The diffraction pattern is composed of two individual reciprocal lattices corresponding to the two superposed sheets. (b) Dark field image obtained by selecting the two (-1010) diffraction peaks: both graphene sheets are visible. (c, d) Dark fields images obtained by selecting each of the (-1010) diffraction peak separately which allows individual imaging of the two superposed sheets. These images correspond to the multilayer and the monolayer graphene sheets, respectivelycan be attributed to the removal of the oxygenated functional groups decorating the FLG edges, as suggested in the Ref. [13]. The conductivity of the as-synthesized FLG is relatively high compared to that of activated charcoal (1×10–7 S/m) [23] but is still low compared to that of graphite (3×104 S/m) [24]. However, the conductivity of the FLG obtained in the present work is still high in comparison to that of the graphene obtained by solvothermal synthesis wherea conductivity of only 0.067 S/m was obtained [22].2.2Proposed mechanism for the exfoliationTang et al.[25] have reported a new method to synthesize graphene by rapid quenching of pristine highly oriented pyrolytic graphite (HOPG) in an aqueous solution of NH4HCO3. The exfoliation pheno- menon was attributed to the formation of cracks on the HOPG surface during the rapid quenching followed by infiltration of NH4HCO3 into the material. Sub- sequent decomposition of NH4HCO3 (see Eq. (1)) leads to the formation of steam and carbon dioxide which help the exfoliation process.NH4HCO3(aq.) ⎯⎯→ NH3(g) + CO2(g) + H2O(g) (1)Based on the results of Tang et al., a mechanism can be proposed to explain the influence of the ammonia on the exfoliation of the graphite. It is expected that the high wetting of the graphite surface by the ammonia solution enhances the infiltration of the liquid between the graphene planes and thus, during the microwave irradiation, leads to an exfoliation process which produces isolated graphene sheets with different thicknesses. Indeed, the fast evaporation of water and/or the decomposition of ammonia during the microwave irradiation and the subsequent infiltration of the gaseous steam and NH3 (see Eq. (2)) within the expanded graphite matrix could give rise to an exfoliation process when the gaseous pressure over- comes the van der Waals forces between the graphene layers (5.9 kJ/mol). Furthermore, this decomposition is thought to be almost spontaneous due to the high microwave absorption properties of the graphite, which could give rise to a fast temperature increase inside the solid matrix.NH4OH(aq.) ⎯⎯→ NH3(g) + H2O(g) (2)It is expected that at high ammonia concentrations, the liquid wetting is better and thus leads to a deeper infiltration of the ammonia solution between the graphene planes of the expanded graphite, causing the exfoliation of graphene sheets of larger sizes. Again, liquid infiltration in the interlayer galleries of the graphene planes inside the expanded graphite can be put forward to explain the observed results (see Section S-1 in the ESM).2.3Surface characteristics of the few-layer graphene sheetsThe electronic structure of the graphene is strongly influenced by basal-plane or edge functionalization by oxygenated groups. In order to detect the presence of any oxygenated groups, X-ray photoelectron spectros- copy (XPS) and attenuated total reflectance–Fourier transform infrared (ATR–FTIR) spectroscopy were performed. Characteristic C 1s and N 1s core level spectra are presented in Fig. 4. The C 1s spectrum of the graphite/graphene sample shows a narrow peak at 284.5 eV indicating the presence of sp2 hybridized C–C bonds, typically assigned to graphite (Fig. 4(c)) [26]. On samples synthesized in ammonia, a low concentration of nitrogen species is detected (atomic fraction of nitrogen ~ 1%–2%) as indicated by the N 1s spectra (inset of Fig. 4(d)). The binding energy of the N 1s peak at 400.2 eV corresponds to nitrogen atoms bonded to sp2 carbon, and can be attributed to nitrogen atoms substituting for carbon in the graphene sheets [27]. It should be noted that the expected contribution of carbon-bonded nitrogen species in the C 1s spectra is not more than 2%, which is far below the uncertainty of the fitting procedure (estimated around 10%). As expected, on samples synthesized in non-ammonia containing solutions, nitrogen is not detected in the N 1s spectra.An important factor determining the quality of graphene is the degree of oxidation, which affects the electrical properties of the material [28]. Graphene oxide involves bonding of carbon with various oxygen functional groups like hydroxyl (–OH), keto (C=O), carboxyl (–COOH) or epoxy groups. These species have a clear fingerprint in the C 1s region, since theirFigure 4XPS C 1s spectra of the graphene sheets synthesized in (a) pure water and (b) 33 wt.% aqueous solution of ammonia.(c) Direct comparison between the two spectra ((a) and (b)) highlights the presence of a high amount of oxygenated functional groups on the FLG surface (a) synthesized without ammonia. (d) The C 1s spectrum of an unsupported graphene+graphite mixture is presented at the bottom as a reference spectrum. The FLG samples were deposited as a thin film on a SiO2/Si substrate (1 cm ×1 cm) and subsequently dried at 10–7 mbar at room temperature. (d, left) Inset spectrum: the N 1s peaks for samples prepared in ammonia solution and pure waterbinding energies are shifted between 1.5 and 4 eV from the main graphene carbon peak. The C 1s spectra of graphene layers supported on SiO2, prepared in pure water (Fig. 4(a)) and in a 33 wt.% aqueous solution of ammonia solution (Fig. 4(b)) are presented in Fig. 4. For the sake of clarity, a direct comparison between the two XPS spectra, obtained from the FLG synthe- sized in water and in aqueous solution of ammonia is also presented in Fig. 4(c). The comparison confirms the higher concentration of the oxygenated functional groups on the FLG surface synthesized in water than on that synthesized in aqueous solution of ammonia. The increased width of the peaks of the SiO2 supported graphene sheets (Fig. 4(a)) compared to those of the graphene/graphite sample (Fig. 4(d)) (1.5 eV instead of 1 eV), is probably related to the poor electrical conductivity of the SiO2 support, resulting in an electrostatic charging of around 2 eV. As in the case of the “bulk” sample, the C 1s peak is dominated by C–C species at 284.5 eV. For the ammonia-treated samples, only one additional minor component at 289.0 eV is present. The binding energy of this com- ponent can be attributed to nitrogen-bonded carbon species. This is also supported by quantitative calcula- tions which showed that the atomic fraction of the C 1s peak at 289 eV and the N 1s peak is close to unity [29]. For the water-treated sample, two additional com- ponents at 286.6 and 288.6 eV are necessary to fit the overall spectrum. These species are typically assigned to keto and carboxylic carbon species, without exclu- ding the presence of hydroxyl groups. The important information obtained by comparing the C 1s peaks of the samples prepared in aqueous solution of ammonia and pure water is that graphene synthesized in ammonia solution exhibits a very low content of oxygenated species and is mostly composed of graphitic carbon. Again, this information highlights the more reduced state of the graphene sheets prepared in aqueous solution of ammonia.This high degree of reducibility was also confirmed by attenuated total reflection infrared measurements (see Fig. S-6 in the ESM) [6, 29–31]. According to these results, an almost complete lack of peaks in the COOH/C–OH stretching region (3000–3700 cm–1) is found for the sample synthesized in aqueous solution of ammonia, in marked contrast to the spectrum for the sample synthesized in water.2.4Atomic force microscopy analysisThe morphology and thickness of the as-synthesized FLG were examined by atomic force microscopy (AFM). The FLG with quite small lateral size, i.e., 0.2–0.4 µm was well dispersed on a SiO2/Si wafer surface (Fig. 5(a)) and lay flat on the SiO2/Si wafer substrate. The thickness of the FLG in Fig. 5(a) was measured by line profile and a value of around 4.4 nmwas obtained. According to Ref. [32], which indicates that the thickness of a single graphene layer is around 1 nm, the FLG obtained in the present work contain between two and five graphene layers. FLG with larger lateral sizes, i.e., 0.6 µm, was also observed, as highlighted in Fig. 5(b). Statistical analysis revealed that the FLG has an average thickness ranging between3 and 5 nm, which corresponds to FLG containing three to five layers of graphene. It is worth mentioning that FLG with even larger lateral sizes (> 1 µm), as observed by TEM, was not found by AFM. This difference can be explained by the instability of such large lateral sizes of FLG on the hydrophilic SiO2/Si wafer surface. FLG with large lateral sizes have a tendency to scroll during the drying step and thus the analysis of these structures by AFM was not successful.It is expected that FLG with such large lateral sizes is easier to observe by TEM due to the presence of the underlying carbon membrane on the TEM grid which prevents them scrolling during the drying step. This hypothesis is confirmed by using a membrane-free TEM grid (see Figs. S-3(a) and S-3(b) in the ESM) in which case the large FLG readily scrolled, due to its high difficulty in maintaining a high aspect ratio 2-D structure. We are currently investigating the Langmuir– Blodgett method as a way to prepare samples with better stability on the SiO2/Si wafer surface for subsequent AFM analysis.2.5Scanning tunneling microscopy analysisThe topology roughness and the electrical conductivityof the FLG sheets synthesized in aqueous solution of ammonia were measured by scanning tunneling microscopy (STM). The graphene sample was annealedin vacuum at 150 °C for 1 h before analysis. Topographic STM images (Fig. 5(c)) show the relatively high roughness of the sheet with a height variation of up to 5 nm. After further annealing at a higher temperature, 400 °C, the roughness was significantly decreased from 5 to around 2 nm (Fig. 5(d)). Such a decrease can be attributed to the removal of adsorbed species. The morphology of graphene films is dominated by elongated strips with periodic stacking which are characterized by 2 nm high protuberances. Meyer et al. [20] have reported that graphene sheets are stabilized by an out-of-plane deformation which can reach 1 nm in height, similar to the STM results in the present work. Such a corrugation becomes smaller for bilayer graphene and disappears for thicker graphene sheets.In order to further explore the conductivity of these graphene sheets, localized current vs. bias potential curves were acquired (Fig. 5(e)). The curve acquired from –3 V to +3 V clearly exhibits an ohmic behavior over the whole potential range of conductivity (–2 V to +1.8 V). The conductivity is observed at positive and negative bias, clearly indicating the ambipolarity of graphene, where carriers can be tuned between holes and electrons by supplying the requisite bias. Moreover, the signal acquired during the measurement was quite stable (low noise level) indicating that the surface probed by the tip was rather clean and lacking significant amounts of adsorbed impurities. Outside these limits, the conductivity reached saturation levels, demonstrating that all the electronic states of the FLG sheets have been probed [33, 34]. Figure 5(f) highlights the positive effect of the annealing on the conductivity: a ten-fold increase of the conductivity slope (d I/d V) was observed when the sample was heated from 150 °C to 400 °C. These results are in line with the observations already made by Kosynkin et al. [13], who also reported an increase in the conductivity of graphene nanoribbons annealed at 300 °C under H2/Ar, and is also consistent with previously reported data from Hernandez et al.[16], where the authors also found a large increase in conductivity after thermal annealing of the sample. This shows that most of the conducti- vity comes only from the intrinsic properties of the graphene sheets and not from adsorbed impurities. Even if it is very difficult to make assumptions concerning the tip shape and size, one can estimate a tunneling effect area of about 1 nm² over the sample. Considering this, it is possible to make a simple calculation, assuming an ohmic conductivity along one dimension:σ⎛⎞=⎜⎟⎝⎠setpointbiasi tE Awhere σ is the conductivity, i setpoint is the probe current, E bias is the applied bias potential, A is the tunneling。