固体推进剂成型工艺
固体火箭推进剂-221

火箭技术对固体推进剂的要求
燃烧性能:固体推进剂装药在发动机内的燃烧必须是有规律的,即燃烧稳定、 重现性好。燃烧规律最好不受或少受环境条件(装药初温、燃烧室压强、平行 于燃面的气流速度)的影响,以满足发动机内弹道性能不变,保证火箭射击精度 的要求。 力学性能:要求固体推进剂装药,特别是大型药柱应有足够的抗拉强度和延伸 率,在使用温度范围内不软化、不发脆,不产生裂缝。贴壁浇注的装药不与发 动机绝热层脱粘。 物理、化学安定性:要求固体推进剂有长的使用寿命 安全性能:在贮存、运输、装配过程中不发生燃烧和爆炸事故。在受到机械冲 击力时应有足够的稳定性。还应有高的自燃温度,以防意外着火事故。 经济性能:火箭技术的发展,注意力主要放在新技术应用上,飞行器的高性能 是设j计的准则,较少考虑经济性能。现在和未来经济性能是重要条件之一。经 济性能将成为一项重要指标。 燃烧产物无烟或少烟:易被敌人发现发射基地;某些用激光或红外光等制导的 导弹,烟雾会使光波衰减。 良好的工艺性能和重现性:
它是棉纤维或木纤维大分子与硝酸反应的生成物
[C6 H 7O2 (OH )3 ] y yxHNO3 H 2 SO4 [C6 H 7O2 (OH )3 x (ONO2 ) x ] y yxH 2O
双基推进剂的组分-硝化纤维素NC
y为大分子的基本链节数目,即称聚合度。 x为被-(ONO2)取代的-(OH)数。对于一个链节,x为小于或等于3 的整数,但因反应过程不均匀,每个链节的x不尽相同,其平均值不 一定是整数。 纤维素被酯化的程度习惯上用含氮量N%表示,它代表了硝化纤维素 中氮元素的重量百分含量。控制反应条件可以得到含氮量不同的硝化 纤维度,含氮量由实验测定。
固体推进剂的基本概念
高能固体推进剂技术未来发展展望

图2 Fig. 2
固体推进剂输入激光能产生的激光化学推进技术
Laser chemical propulsion technology caused by the laser energy input on the solid propellant
3
国外高能固体推进剂技术的最新进展
国外固体推进剂技术的发展方向为高能、 钝感、 低
表1 Tab. 1 性能 密度( / g / cm3 ) 生成热( / kJ / mOI) 熔点 / 分解温度 / K HMX l. 9l 84 548 HMX 和新型氧化剂的密度和生成热
( 三氨基硝酸胍) 、 四硝基双吡唑 ( 制得的推进剂理论 比冲可达 2 67lN・S / kg) 、 二硝基双三唑 ( 制得的推进 剂理论比冲可达 2 774N ・ S / kg ) 和硝基双氮-氧化-三 ( 制得的推进剂理论比冲可达 2 833N ・ S / kg ) 唑-四唑 等。 新型高能量物质探索研究还包括化学键激发态 ( H4 、 FN3 、 Li3 H) 、 高能基态 ( !-N2 O2 、 O6 、 CIF5 O ) 、 亚稳 态 ( L in 、 H3+ H - 、 Rg n X - ) 、 超价态 ( FKPOKPF、 NH4- 、 NF4- 、 CH5- ) 、 张力 ( MgC2 、 B2 Be2 、 N2 CO ) 等物质的理论 探索。其中, 可用于固体推进剂的有 FN3 、 Li3 H、 CIF5 O、 MgC2 、 B2 Be2 、 N2 CO、 NF4- 等。理论计算表明, 这些 组分的引入可以大幅度提高固体推进剂的能量特性, 如用 FN3 取代 AP, 可使推进剂能量提高 5 ~ l0S; CIF5 O 可使推进剂能量提高 20S 以上。 HMX 与新型氧化剂 的性能 ( 主要是密度和生成热) 对比见表 l 。
电控固体推进剂技术发展现状及趋势
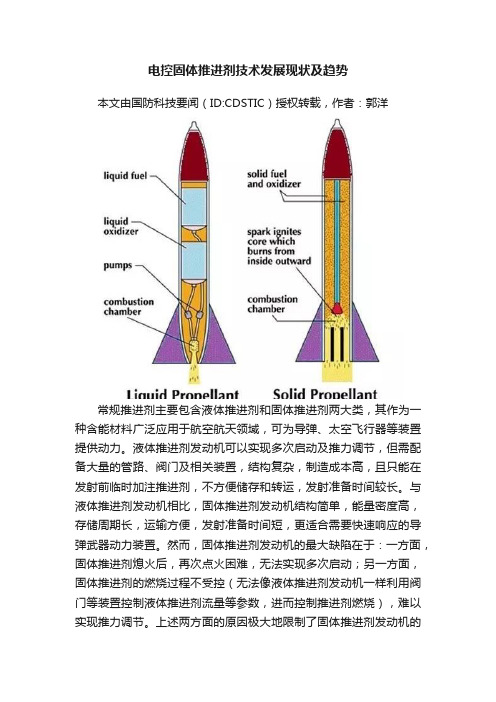
电控固体推进剂技术发展现状及趋势本文由国防科技要闻(ID:CDSTIC)授权转载,作者:郭洋常规推进剂主要包含液体推进剂和固体推进剂两大类,其作为一种含能材料广泛应用于航空航天领域,可为导弹、太空飞行器等装置提供动力。
液体推进剂发动机可以实现多次启动及推力调节,但需配备大量的管路、阀门及相关装置,结构复杂,制造成本高,且只能在发射前临时加注推进剂,不方便储存和转运,发射准备时间较长。
与液体推进剂发动机相比,固体推进剂发动机结构简单,能量密度高,存储周期长,运输方便,发射准备时间短,更适合需要快速响应的导弹武器动力装置。
然而,固体推进剂发动机的最大缺陷在于:一方面,固体推进剂熄火后,再次点火困难,无法实现多次启动;另一方面,固体推进剂的燃烧过程不受控(无法像液体推进剂发动机一样利用阀门等装置控制液体推进剂流量等参数,进而控制推进剂燃烧),难以实现推力调节。
上述两方面的原因极大地限制了固体推进剂发动机的推广应用。
为了充分结合固体推进剂发动机和液体推进剂发动机两者的优点,研究人员尝试从两个方面对固体推进剂发动机进行改进:一是优化固体推进剂发动机设计,例如设置发动机喷喉可调节装置,通过增大或减小喷喉截面积调节发动机推力;二是采取改变固体推进剂药柱形状等措施,例如圆筒形、星形等特殊形状,试图控制固体推进剂的燃烧过程。
但上述两种方式都属于被动适应固体推进剂的燃烧特性,效果有限,依然无法实现多次启动和灵活的推力调节。
为了从根本上突破固体推进剂发动机在应用上的瓶颈,研究人员提出了电控固体推进剂(ESP)概念,这种新型固体推进剂药柱中设置有电极,通电后药柱即被点燃,断电后药柱即熄火,还可通过调节电压来控制固体推进剂的燃速,实现了对固体推进剂燃烧过程的主动控制,从而使固体推进剂发动机具备多次启动和推力可调功能,同时保留了固体推进剂发动机的固有优势。
▲同轴型微型电控固体推进剂发动机结构示意图电控固体推进剂技术是固体推进剂领域的重大技术革新,由于其独特的电压控制燃烧状态的特性,颠覆了传统的固体推进剂发动机的工作模式,其研究进展及相关动态值得高度关注。
双基推进剂(精)

双基推进剂双基推进剂通常加入燃烧催化剂、制造工艺、燃烧性能和溶剂或助剂性质的不同可分为不同的类型。
按加入燃烧催化剂的不同区分,可分为不同的品号:加入石墨的称为双石推进剂(SS);加入氧化铅的称为双铅推进剂(SQ);加入氧化铅的称为双铅推进剂(SQ);加入氧化钴的称为双钴推进剂(SG);加入氧化镁的称为双芳镁推进剂(SFM)。
这些推进剂统称普通双基推进剂。
按成型工艺不同可分成两种:一种是挤压成型或压伸成型(用螺旋式压伸机或柱塞式压伸机)工艺制成的推进剂称为压伸双基推进剂;另一种浇铸成型工艺制成的推进剂称为浇铸双基推进剂。
按燃烧性能区分,在不定期下的压力范围内实现燃速压力指数小于0.2并接近于零,产生平台燃烧的推进剂称双基平台推进剂;随着发动机工作时间的延长,推进剂燃速下降,其压力在一定范围内蒙古自治区降低产生麦撒燃烧,这种推进剂称为麦撒双基推进剂。
按燃烧速度区分,在常温、压力6.68MPa 条件下,燃烧度速度为25mm/s以上的推进剂称为高燃烧速度推进剂;在常温、6.68MPa条件下,燃烧速度为5mm/s以下的推进剂称为低燃烧速度推进剂,按是否加入挥发性溶剂区分,加入丙酮等挥了性溶剂的称为柯达型双基推进剂或含挥发性溶剂双基推进剂;不加挥发性溶剂的称巴利斯太双基推进剂或无溶剂压伸双基推进剂。
双组分中加入吉纳,称吉纳双基推进剂,如我国171推进剂。
双基推进剂的主要成分是硝化纤维和硝化甘油,它们的性能决定着陆以基推进剂的性能,双基推进剂的突出优点是质地均匀,结构均匀,再现性好,能满足战术火箭和导弹的需要。
双基推进剂具有固体推进剂的一般性能,符合对固体推进剂的一般要求,即能量高,密度一般在1.54~1.65g/cm3,实际比冲一般为1666~2156N.s/kg;良好的燃烧性能、燃烧速度一般为5~40mm/s(6.86MPa),燃烧速度压力指数可接近于零;良好的力学性能;良好的内弹道性能;工艺性能好;较好的安定性;原料来源广泛,价格低廉,经济性好,其他特殊要求,如少烟或无烟,爆温低,低燃烧速度等。
微铝含量推进剂配方与刮涂成型装药工艺

f . 最终选定配方如表 6 所示 。
3 药柱成型研究
从图 1 可见燃烧室药型特殊 ,采用常规的同心 双层药成型工艺很难实施 。9mm 厚内层药嵌在药 型中间 ,先浇外层药预固化后再浇内层药 ,这样对 内嵌薄层药的 Ф100mm 芯模脱模困难 ;用药浆同期 浇注拔隔离筒也不能实现 。综合我国现有复合药 成型技术 ,提出复合药成型新方案 ———刮涂成型装 药工艺 ,其步骤如下 :
压强指数
(10~18MPa 下 ,静态 ,20 ℃) 发动机平均燃速/ (mm·s - 1)
(15. 79MPa 下)
21. 56
1. 341 43. 8 1. 068 38. 7 48. 3 1. 68
0. 396
15. 82
1. 228 44. 8 1. 04 49. 7 51. 2 1. 758
为了保证两层推进剂粘结良好 ,本项目采用经 7a 自然储存考核成功的粘结技术 ,在浇注外层低 燃速药前 ,对内层药外表面刷一层粘合剂 (厚度 ≤ 0. 2mm) [1 ,2] 。该粘合剂与推进剂是同一体系的 。 粘合剂配方中含粘合剂体系 70 % ,偶联剂 0. 5 % , 增塑剂 29. 5 %。
为了减少起飞瞬间发动机燃气中固相粒子高 速冲刷和烧蚀发射筒内壁 ,同时不降低其整体能 量 ,使弹箭达到射程设计要求 ,采用不同燃速 、不同 铝粉含量的推进剂配方 。配方所具备的主要特征 是起飞瞬间燃气中固相粒子少 。两种推进剂在导 弹起飞瞬间 (0. 386s 内) 推进剂的铝粉含量约占燃 烧全过程的铝粉含量的 3. 74 %。该低铝含量 、高 性能特征的两层推进剂配方性能指标要求见表 1 。
/ kPa pmax对应时间 t
/s 平均压强 ptb
/ kPa 压强冲量 Ipb
固体推进剂成型工艺

固体推进剂成型工艺
固体推进剂成型工艺是制造固体火箭发动机必须掌握的核心技
术之一。
固体推进剂成型工艺主要包括混合、成型、固化和加工等环节。
混合阶段是将推进剂原材料按照一定比例混合均匀,以保证推进剂的化学反应符合设计要求;成型阶段通过压制或挤出等方式将混合好的推进剂成型成具有一定形状和尺寸的燃烧体,以满足火箭发动机的空间和重量限制;固化阶段是将成型好的推进剂进行固化处理,以保证其在运输和储存过程中稳定性和安全性;加工阶段则是对成型好的固体推进剂进行必要的加工处理,如切割、钻孔等,以满足火箭发动机的具体需求。
固体推进剂成型工艺的精细化和自动化程度越来越高,将为固体火箭发动机的性能提升和应用领域的拓展提供有力支持。
- 1 -。
国外固体推进剂技术现状和发展趋势
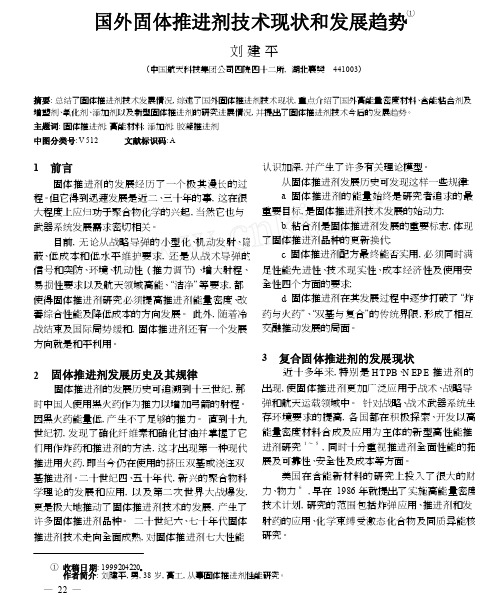
①国外固体推进剂技术现状和发展趋势刘 建 平(中国航天科技集团公司四院四十二所, 湖北襄樊 441003)摘要: 总结了固体推进剂技术发展情况, 综述了国外固体推进剂技术现状, 重点介绍了国外高能量密度材料、含能粘合剂及 增塑剂、氧化剂、添加剂以及新型固体推进剂的研究进展情况, 并提出了固体推进剂技术今后的发展趋势。
主题词: 固体推进剂; 高能材料; 添加剂; 胶凝推进剂 中图分类号: V 512文献标识码: A前言固体推进剂的发展经历了一个极其漫长的过 程。
但它得到迅速发展是近二、三十年的事, 这在很 大程度上应归功于聚合物化学的兴起, 当然它也与 武器系统发展需求密切相关。
目前, 无论从战略导弹的小型化、机动发射、隐 蔽、低成本和低水平维护要求, 还是从战术导弹的信号和突防、环境、机动性 ( 推力调节)、增大射程、 易损性要求以及航天领域高能、“洁净”等要求, 都 使得固体推进剂研究必须提高推进剂能量密度、改善综合性能及降低成本的方向发展。
此外, 随着冷 战结束及国际局势缓和, 固体推进剂还有一个发展 方向就是和平利用。
认识加深, 并产生了许多有关理论模型。
从固体推进剂发展历史可发现这样一些规律: a . 固体推进剂的能量始终是研究者追求的最 重要目标, 是固体推进剂技术发展的始动力;b . 粘合剂是固体推进剂发展的重要标志, 体现了固体推进剂品种的更新换代;c . 固体推进剂配方最终能否实用, 必须同时满 足性能先进性、技术现实性、成本经济性及使用安 全性四个方面的要求; d . 固体推进剂在其发展过程中逐步打破了“炸 药与火药”、“双基与复合”的传统界限, 形成了相互交融推动发展的局面。
1 3 复合固体推进剂的发展现状近十多年来, 特别是 H T PB 、N E P E 推进剂的 2 固体推进剂发展历史及其规律固体推进剂的发展历史可追溯到十三世纪, 那 出现, 使固体推进剂更加广泛应用于战术、战略导 弹和航天运载领域中。
固体推进剂

——美国高能ETPE层状发射药及装药研究为电热化学炮的发展提供了有力支持
从上世纪末开始,美国就在为未来武器系统(电热化学炮)研制采用无溶剂法 制造的高能量、高性能拼合式夹层(co-layered)ETPE发射药。该新型发射药采用 高密度含能热塑性弹性体(ETPE)粘合剂,已制成含BAMO-NMMO、增塑剂 (BDNPA/F)和RDX的4种快燃配方(密度为1.6675g/cm3,火药力为1267.17J/g, 火焰温度为3252K)以及含RDX、NQ和BAMO-NMMO的3种慢燃配方(密度在 1.5923~1.6159g/cm3之间,火药力为1022.45或1050.92J/g,火焰温度为2473K或 2543K)。
赫,现有的防空系统几乎无法防御。
——美国推出多种不敏感推进剂
包括: 端羟基聚醚(HTPE)复合推进剂 钝感NEPE推进剂 钝感低特征信号XLDB推进剂 这些推进剂明显改善钝感特性,能量水平和其他性能无显著下降。 美国研制了HTCE/聚醚推进剂和ARC-9131推进剂(5%Al、65%硝胺、PEG、 混合硝酸酯),它们也具有良好的不敏感特性
此外,美国陆军研制的ETPE层状高能发射药引入纳米含能材料,具有高能量 (火药力约为1300J/g)、低毒和不敏感等优势; 法国成功研制出NENA基高能层状发射药; 荷兰采用计算机软件控制,扩大层状发射药的同步挤出规模。
- 1、下载文档前请自行甄别文档内容的完整性,平台不提供额外的编辑、内容补充、找答案等附加服务。
- 2、"仅部分预览"的文档,不可在线预览部分如存在完整性等问题,可反馈申请退款(可完整预览的文档不适用该条件!)。
- 3、如文档侵犯您的权益,请联系客服反馈,我们会尽快为您处理(人工客服工作时间:9:00-18:30)。
固体推进剂成型工艺
1.原料准备:根据固态推进剂的成分配比,将各种原材料按照一定比例混合,加入适量的添加剂和活性剂,并进行筛选、研磨等前期处理。
2. 烘干:将原材料在一定温度下进行烘干处理,以去除水分和有机溶剂等。
3. 混合:将经过烘干处理的原料进行混合,采用不同的混合方式,如干混、湿混、熔混等。
4. 压制成型:将混合后的原料进行压制成型,通常采用压制成型机进行加压成型,以达到所需的密度和形状。
5. 后续加工:将成型后的固态推进剂进行后续处理,包括烘干、烧结、表面处理等,以获得所需的性能和质量。
固态推进剂成型工艺对于固体火箭发动机的性能和可靠性具有重要影响,因此需要严格控制每个工艺步骤的参数,保证成型质量的稳定性和一致性。
同时,随着工艺技术的不断发展,越来越多的新型材料和加工工艺被应用到固态推进剂成型中,使固态推进剂的性能得到了不断提高和优化。
- 1 -。