吹塑托盘的成型工艺和问题解决
中空吹塑成型技术分析
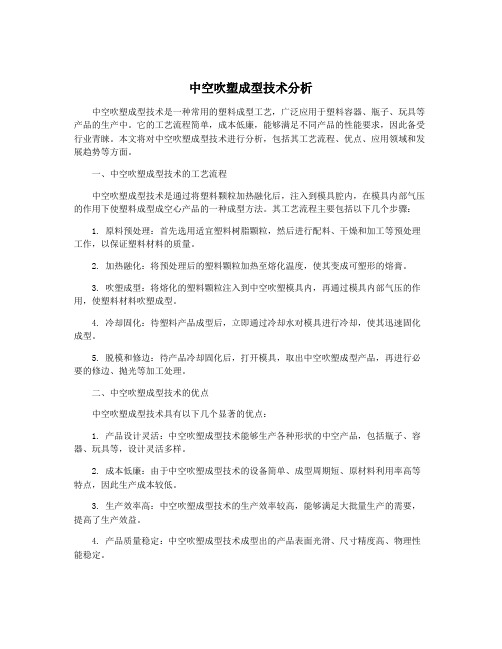
中空吹塑成型技术分析中空吹塑成型技术是一种常用的塑料成型工艺,广泛应用于塑料容器、瓶子、玩具等产品的生产中。
它的工艺流程简单,成本低廉,能够满足不同产品的性能要求,因此备受行业青睐。
本文将对中空吹塑成型技术进行分析,包括其工艺流程、优点、应用领域和发展趋势等方面。
一、中空吹塑成型技术的工艺流程中空吹塑成型技术是通过将塑料颗粒加热融化后,注入到模具腔内,在模具内部气压的作用下使塑料成型成空心产品的一种成型方法。
其工艺流程主要包括以下几个步骤:1. 原料预处理:首先选用适宜塑料树脂颗粒,然后进行配料、干燥和加工等预处理工作,以保证塑料材料的质量。
2. 加热融化:将预处理后的塑料颗粒加热至熔化温度,使其变成可塑形的熔膏。
3. 吹塑成型:将熔化的塑料颗粒注入到中空吹塑模具内,再通过模具内部气压的作用,使塑料材料吹塑成型。
4. 冷却固化:待塑料产品成型后,立即通过冷却水对模具进行冷却,使其迅速固化成型。
5. 脱模和修边:待产品冷却固化后,打开模具,取出中空吹塑成型产品,再进行必要的修边、抛光等加工处理。
二、中空吹塑成型技术的优点中空吹塑成型技术具有以下几个显著的优点:1. 产品设计灵活:中空吹塑成型技术能够生产各种形状的中空产品,包括瓶子、容器、玩具等,设计灵活多样。
2. 成本低廉:由于中空吹塑成型技术的设备简单、成型周期短、原材料利用率高等特点,因此生产成本较低。
3. 生产效率高:中空吹塑成型技术的生产效率较高,能够满足大批量生产的需要,提高了生产效益。
4. 产品质量稳定:中空吹塑成型技术成型出的产品表面光滑、尺寸精度高、物理性能稳定。
5. 符合环保要求:中空吹塑成型技术能有效降低原材料的使用量,减少废料产生,符合环保要求。
三、中空吹塑成型技术的应用领域中空吹塑成型技术广泛应用于食品、饮料、日化、医药、化工等行业,主要用于生产塑料瓶、塑料容器、塑料玩具、化妆品包装等产品。
其产品广泛应用于日常生活和工业生产中,市场需求量大。
分析吹塑制品常见的10个问题
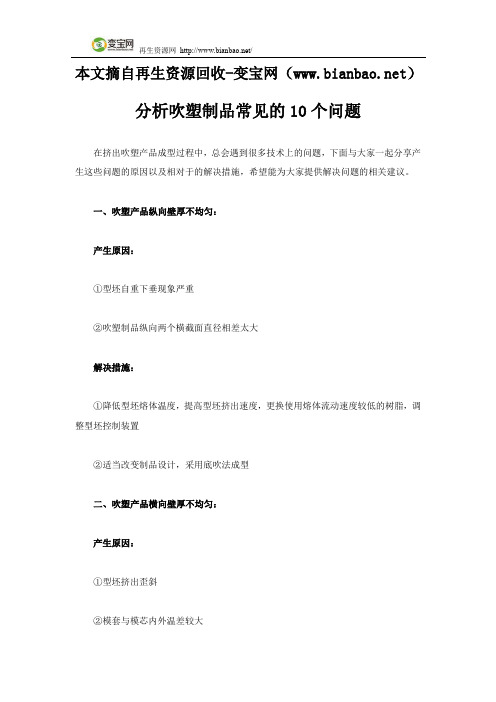
本文摘自再生资源回收-变宝网()分析吹塑制品常见的10个问题在挤出吹塑产品成型过程中,总会遇到很多技术上的问题,下面与大家一起分享产生这些问题的原因以及相对于的解决措施,希望能为大家提供解决问题的相关建议。
一、吹塑产品纵向壁厚不均匀:产生原因:①型坯自重下垂现象严重②吹塑制品纵向两个横截面直径相差太大解决措施:①降低型坯熔体温度,提高型坯挤出速度,更换使用熔体流动速度较低的树脂,调整型坯控制装置②适当改变制品设计,采用底吹法成型二、吹塑产品横向壁厚不均匀:产生原因:①型坯挤出歪斜②模套与模芯内外温差较大③制品外形不对称④型坯吹胀比过大解决措施:①调整口模间隙宽度偏差,使型坯壁厚均匀;闭模前,拉直型坏②提髙或降低模套加热温度,改善口模内外温度偏差③闭模前,对型坯进行预夹紧和预扩张,使型坯适当向薄壁方向偏移④降低型坯吹胀比三、吹塑产品表面出现橘皮状花纹或麻点:产生原因:①模具排气不良②模具漏水或模具型腔出现冷凝现象③型坯塑化不良,型坯产生熔体破裂现象④吹胀气压不足⑤吹胀速度慢⑥吹胀比太小解决措施:①模具型坯进行喷砂处理,增设排气孔②修理模具,调整模具冷却温度到"露点"以上③降低螺杆转速,提高挤出机加热温度④提髙吹胀气压⑤清理压缩空气通道,检査吹气杆是否漏气⑥更换模套、模芯,提高型坯吹胀比四、吹塑产品容积减少:产生原因:①型坯壁厚增大,导致制品壁增厚②制品收缩率增加,导致制品尺寸縮③吹胀气压小,制品未吹胀到型腔设计尺寸解决措施:①调节程序控制装置,使型坯壁厚减小;提高型坯熔体温度,降低型坯离模膨胀比②更换收缩率小的树脂,延长吹气时间,降低模具冷却温度③适当提髙压缩空气的压力五、吹塑产品品轮廓或图文不清晰:产生原因:①型腔排气不良②吹胀气压低③型坯熔体温度偏低,物料塑化不良④模具冷却温度偏低,模具有"冷凝"现象解决措施:①修理模具,型腔喷砂处理或增设排气槽②提高吹胀气压③适当提高挤出机及机头加热温度,必要时添加适量的填充母料④把模具温度调髙到露点温度以上六、吹塑产品飞边太多、太厚:产生原因:①模具胀模,锁模压力不足②模具刀口磨损,导柱偏移③吹胀时,型坯偏斜④夹坯刀口处逃料槽太浅或刀口深度太浅⑤型坯充气启动过早解决措施:①提髙模具锁模压力,适合降低吹胀气压②修理模具刀口,校正或更换模具导柱③校正型坯与吹气杆的中心位置③修整模具,加深逃料槽或刀的深度④调整型坯充气时间七、出现过深的纵向条纹:产生原因:①模口处肮脏②模套,芯边缘有毛刺或缺口③色母料或树脂分解产生深色条纹④过滤网穿洞,物料混入杂质沉积在模口解决措施:①用铜刀清理模口②修整口模③适当降低温度,更换分散性好的色母料④更换过滤网板,使用沾的边角料八、成型时型胚被吹破:产生原因:①模具刀口太尖锐②型坯有杂质或气泡③吹胀比过大④型坯熔体强度低⑤型坯长度不足⑤型坯壁太薄或型坯壁厚薄不均匀⑥容器在开模时胀裂(放气时间不足)⑦模具锁模力不足解决措施:①适当加大刀口的宽度及角度②使用干燥原料,潮湿原料烘干后使用,使用清洁原料;清理模口③更换模套、模芯,降低型坏的吹胀比④更换合适的原料,适当降低熔体温度⑤检查挤出机或储料缸机头的控制装置,减少工艺参数变动,增加型坯的长度⑥更换模套或模芯,加厚型坯壁;检査型坯控制装置;调节模口间隙⑦调整放气时间或延迟模具启模启动时间⑧提髙锁模压力或降低吹胀气压九、吹塑制品脱模困难:产生原因:①制品吹胀冷却时间过长,模具冷却温度低②模具设计不良,型腔表面有毛刺③启模时,前后模板移动速度不均衡④模具安装错误解决措施:①适当縮短型坯吹胀时间,提髙模具温度②修整模具;减少凹槽深度,凸筋斜度为1:50或1:100;使用脱模剂③修理锁模装置,使前后模板移动速度一致④重新安装模具,校正两半模的安装位置十、吹塑制品质量波动大:产生原因:①型坯壁厚突然变化②掺人的边角回料混合不均匀③进料段堵塞,造成挤出机出料波动④加热温度不均衡解决措施:①修理型坯控制装置②采用好的混料装置,延长混料时间;必要时减少边角回料的用量③去除料口处结块物④料或异物。
吹塑成型的缺陷及可能产生原因的分析
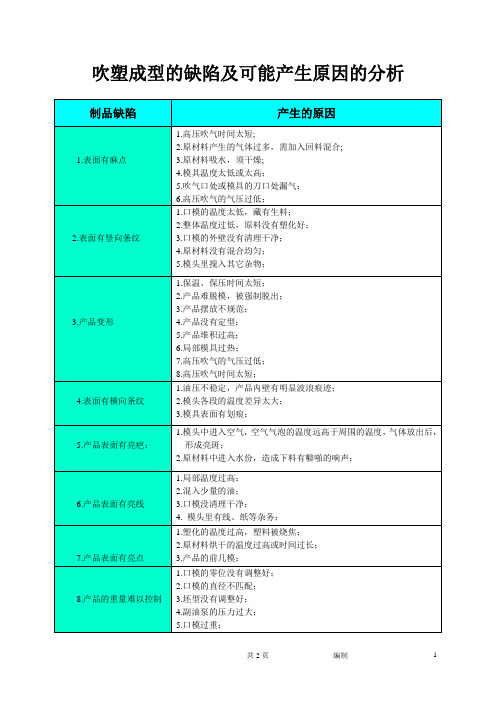
制品缺陷
产生的原因
1.表面有麻点
1.高压吹气时间太短;
2.原材料产生的气体过多,需加入回料混合;
3.原材料吸水,须干燥;
4.模具温度太低或太高;
5.吹气口处或模具的刀口处漏气;
6.高压吹气的气压过低;
2.表面有竖向条纹
1.口模的温度太低,藏有生料;
2.整体温度过低,原料没有塑化好;
3.合模速度太慢;
16.
1.塑化的温度过高,塑料被烧焦;
2.原材产品的重量难以控制
1.口模的零位没有调整好;
2.口模的直径不匹配;
3.坯型没有调整好;
4.副油泵的压力过大;
5.口模过重;
吹塑成型的缺陷及可能产生原因的分析
制品缺陷
产生的原因
9.吹针口不圆
1.模具的吹针部分过小或过长,塑料包死吹针,使其不能脱出;
2.模头各段的温度差异太大;
3.模具表面有划痕;
5.产品表面有亮疤;
1.模头中进入空气,空气气泡的温度远高于周围的温度,气体放出后,形成亮斑;
2.原材料中进入水份,造成下料有噼啪的响声;
6.产品表面有亮线
1.局部温度过高;
2.混入少量的油;
3.口模没清理干净;
4.模头里有线、纸等杂务;
7.产品表面有亮点
2.吹针与活塞配合不紧,产生晃动;
3.脱模时用力过大;
4.气压不稳定;
10.边条过厚
1.锁模力太小;
2.刀口没有合死;
3.分型面没有溢料的地方;
4.气压过高;
5.模具过长,模板不能锁紧模具的两端,造成两端边条过厚;
11.下料翻卷
1.向内翻卷;(模芯温度太低)
吹塑件常出现的吹塑问题及其调教解决方法
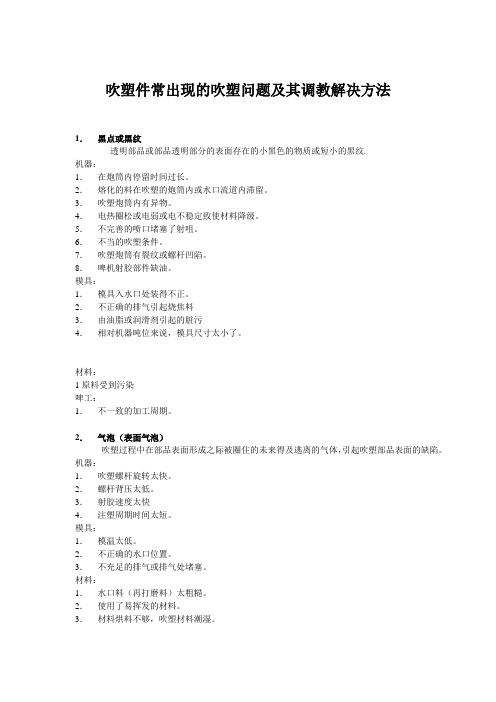
吹塑件常出现的吹塑问题及其调教解决方法1.黑点或黑纹透明部品或部品透明部分的表面存在的小黑色的物质或短小的黑纹.机器:1.在炮筒内停留时间过长。
2.熔化的料在吹塑的炮筒内或水口流道内滞留。
3.吹塑炮筒内有异物。
4.电热圈松或电弱或电不稳定致使材料降级。
5.不完善的喷口堵塞了射咀。
6.不当的吹塑条件。
7.吹塑炮筒有裂纹或螺杆凹陷。
8.啤机射胶部件缺油。
模具:1.模具入水口处装得不正。
2.不正确的排气引起烧焦料3.由油脂或润滑剂引起的脏污4.相对机器吨位来说,模具尺寸太小了。
材料:1原料受到污染啤工:1.不一致的加工周期。
2.气泡(表面气泡)吹塑过程中在部品表面形成之际被圈住的未来得及逃离的气体,引起吹塑部品表面的缺陷。
机器:1.吹塑螺杆旋转太快。
2.螺杆背压太低。
3.射胶速度太快4.注塑周期时间太短。
模具:1.模温太低。
2.不正确的水口位置。
3.不充足的排气或排气处堵塞。
材料:1.水口料(再打磨料)太粗糙。
2.使用了易挥发的材料。
3.材料烘料不够,吹塑材料潮湿。
3.烘印表面云斑的缺陷,常见在水口位置,有时在流道的阻碍周围常见缺陷区有较弱的物理物性。
机器:1.吹塑速度太快。
2.熔温太高或太低。
3.吹塑压力太低4.射咀直径太小。
5.射咀温度太低。
模具:1.模温太低。
2.唧咀直径太小。
3.不正确的水口位置。
4.模壁冷却不足。
5.太尖的转角,特别是水口区。
材料:1材料太潮湿。
啤工:1.不一致的机器吹塑周期。
4.变形弯如弓形状的状态,可以是凸出来或凹进的形状,或由从表面到部品另一面的不同缩水率引起。
机器:1.开模速度过快。
2.顶针系统不平或不平行。
3.冷却时间太短。
4.部品“包装”错误。
模具:1.熔胶温度太低。
2.模温不一致3.水口位置错误。
啤工:1.啤出后部品加工处理不当。
5.断裂(脆裂)塑胶部品在某种非正常环境条件下要断或要裂开的趋势,有时部品边可以被损毁。
机器:1.不正确的吹塑螺杆设计。
2.吹塑周期太短。
吹塑车间工艺流程

吹塑车间工艺流程一、工艺概述吹塑是一种常见的塑料加工工艺,适用于制造各种塑料制品,如瓶子、容器、桶等。
吹塑车间工艺流程包括原料准备、预热、吹塑成型、冷却、修整和包装等步骤。
二、原料准备1. 原料选择:根据产品要求,选择适合的塑料原料,如聚乙烯(PE)、聚丙烯(PP)等。
2. 原料配比:根据产品的要求和配方,按照一定比例将原料混合均匀。
三、预热1. 原料熔化:将原料放入吹塑机的料斗中,通过加热和搅拌,使原料熔化成液态。
2. 温度控制:根据不同的塑料原料,设置合适的加热温度,确保原料达到适宜的熔化状态。
四、吹塑成型1. 模具选择:根据产品的形状和尺寸要求,选择合适的吹塑模具。
2. 吹塑过程:将预热后的塑料原料注入吹塑机的模具中,通过高压气流将塑料原料吹塑成型。
3. 模具冷却:在吹塑过程中,通过冷却水或冷却气体对模具进行冷却,使塑料迅速固化。
五、冷却1. 冷却时间:根据产品的尺寸和厚度,设置合适的冷却时间,确保产品充分固化。
2. 冷却方式:可以采用自然冷却或辅助冷却设备,如冷风机或冷却水槽等。
六、修整1. 去除闪边:在冷却后,将产品上的闪边或毛刺去除,使产品表面光滑。
2. 检查质量:对产品进行外观检查,确保没有缺陷和瑕疵。
七、包装1. 包装材料:选择适合的包装材料,如塑料袋、纸箱等。
2. 包装方式:根据产品的形状和尺寸,选择合适的包装方式,如装箱、封口等。
3. 标签贴附:在包装上贴附产品相关的标签,包括产品名称、规格、生产日期等信息。
八、质量控制1. 原料检验:对进货的原料进行检验,确保原料质量符合要求。
2. 在线检测:在吹塑过程中,通过检测设备对产品进行在线质量检测,如尺寸、重量等。
3. 产品检验:对成品进行全面的检验,包括外观检查、物理性能测试等。
九、设备维护1. 定期保养:定期对吹塑机和模具等设备进行保养,确保设备的正常运行。
2. 故障处理:及时处理设备故障,确保生产不受影响。
以上是吹塑车间的工艺流程,通过严格控制每个环节的质量和工艺参数,可以生产出符合要求的塑料制品。
中空吹塑成型技术分析
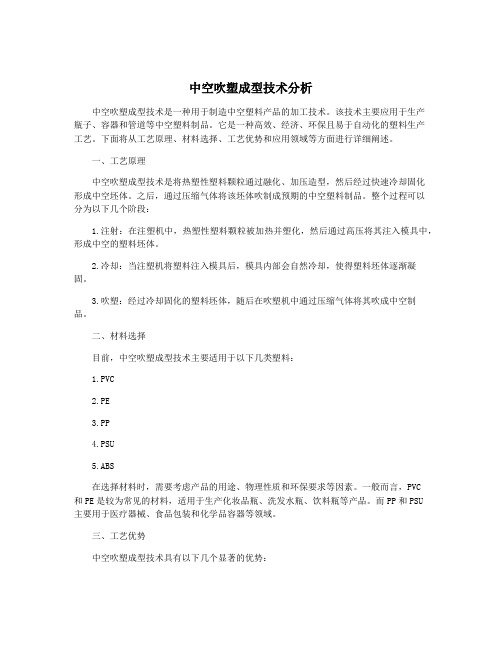
中空吹塑成型技术分析中空吹塑成型技术是一种用于制造中空塑料产品的加工技术。
该技术主要应用于生产瓶子、容器和管道等中空塑料制品。
它是一种高效、经济、环保且易于自动化的塑料生产工艺。
下面将从工艺原理、材料选择、工艺优势和应用领域等方面进行详细阐述。
一、工艺原理中空吹塑成型技术是将热塑性塑料颗粒通过融化、加压造型,然后经过快速冷却固化形成中空坯体。
之后,通过压缩气体将该坯体吹制成预期的中空塑料制品。
整个过程可以分为以下几个阶段:1.注射:在注塑机中,热塑性塑料颗粒被加热并塑化,然后通过高压将其注入模具中,形成中空的塑料坯体。
2.冷却:当注塑机将塑料注入模具后,模具内部会自然冷却,使得塑料坯体逐渐凝固。
3.吹塑:经过冷却固化的塑料坯体,随后在吹塑机中通过压缩气体将其吹成中空制品。
二、材料选择目前,中空吹塑成型技术主要适用于以下几类塑料:1.PVC2.PE3.PP4.PSU5.ABS在选择材料时,需要考虑产品的用途、物理性质和环保要求等因素。
一般而言,PVC和PE是较为常见的材料,适用于生产化妆品瓶、洗发水瓶、饮料瓶等产品。
而PP和PSU主要用于医疗器械、食品包装和化学品容器等领域。
三、工艺优势中空吹塑成型技术具有以下几个显著的优势:1.高效:中空吹塑成型技术是一种高效的生产工艺,能够在短时间内完成大量生产任务。
2.经济:相比于传统的生产工艺,中空吹塑成型技术具有较低的成本,可以降低生产成本并提高企业效益。
3.环保:整个生产过程中,塑料废料可以进行回收,减少环境污染,并且所使用的材料可以根据需要进行再利用。
4.易于自动化:中空吹塑成型技术可以通过自动化系统进行操作和调节,提高生产效率和质量稳定性。
四、应用领域1.食品包装:饮料瓶、食品容器等。
2.医疗器械:医疗瓶、输液瓶等。
3.化学品容器:化学品储存瓶、化妆品瓶等。
4.机械零件:机械配件、汽车零件等。
总之,中空吹塑成型技术是一种高效、经济、环保且易于自动化的生产工艺,具有广泛的应用前景。
吹塑托盘的技巧

吹塑托盘的技巧吹塑托盘是一种常见的包装材料,广泛应用于各个行业的物流和运输过程中。
它具有轻便、坚固、耐用等特点,可以有效地保护货物,提高运输效率。
在生产吹塑托盘的过程中,有一些技巧可以帮助提高生产效率和产品质量。
下面就来详细介绍一下吹塑托盘的生产技巧。
1.材料选择吹塑托盘的主要原料是聚乙烯(PE)和聚丙烯(PP),通常采用再生料和新料的混合使用。
在选择原料时,需要考虑到产品的使用环境和负荷要求,以保证产品的质量和使用寿命。
另外,在选择原料供应商时,需要考虑其产品质量、价格和售后服务等因素,综合考虑选择合适的供应商。
2.模具设计吹塑托盘的模具设计对产品的成型质量和生产效率有着重要影响。
在进行模具设计时,需要考虑产品的结构和尺寸,合理设计产品的形状和壁厚,确保产品在承载力和成型精度方面达到要求。
此外,还需考虑模具的材料选用和加工工艺,以确保模具的使用寿命和成型精度。
3.生产工艺吹塑托盘的生产工艺通常包括挤出、吹塑和冷却三个步骤。
在挤出阶段,需要控制好挤出机的温度、压力和速度等参数,确保原料均匀挤出、预热和塑化。
在吹塑阶段,需要控制好吹塑机的温度、压力和速度等参数,确保产品成型质量和生产效率。
在冷却阶段,需要控制好冷却系统的温度和风量等参数,确保产品冷却速度和质量。
4.质量控制吹塑托盘的质量控制是生产过程中的关键环节。
在生产过程中,需要进行原料、半成品和成品的质量检测,确保原料和产品的质量符合要求。
另外,还需要做好生产记录和追溯,及时处理产品质量问题,确保产品质量稳定和可靠。
5.设备维护吹塑托盘的生产设备需要定期进行维护保养,确保设备的正常运行和生产效率。
在设备维护过程中,需要对设备进行清洁、润滑和部件更换等工作,确保设备的正常运行和使用寿命。
综上所述,吹塑托盘的生产技巧包括材料选择、模具设计、生产工艺、质量控制和设备维护等方面。
通过合理的选择和设计,严格的生产控制和设备维护,可以提高吹塑托盘的生产效率和产品质量,满足客户的需求和要求。
吹塑的工艺技术

吹塑的工艺技术
吹塑是一种将塑料颗粒加热至熔融状态,然后通过空气压力将其吹制
成形的工艺技术。
它被广泛应用于制造各种塑料制品,如瓶子、罐子、桶子、玩具等。
吹塑的工艺流程主要包括以下几个步骤:
1. 塑料颗粒的预处理:在吹塑过程中,需要使用经过预处理的塑料颗粒。
这些颗粒需要经过干燥、筛选和加入色素等处理,以确保最终产
品的质量。
2. 加热和熔融:将经过预处理的塑料颗粒放入吹塑机中,并通过加热
使其达到熔融状态。
通常情况下,加热温度在180-220℃之间。
3. 吹制成型:当塑料达到熔融状态后,就可以开始进行吹制成型了。
首先,在模具内部喷入一定量的空气,使得塑料充满整个模具并形成
所需形状。
随着空气压力不断增加,模具内部的形态也会逐渐变化,
直到最终形成所需产品。
4. 冷却和取出:当产品形成后,需要将其冷却以使其保持形状。
通常
情况下,会使用水或空气进行冷却。
最后,通过取出机器将产品从模
具中取出。
吹塑的优点在于可以制造出各种形状、大小和颜色的产品,并且成本相对较低。
此外,吹塑也比其他制造方法更加环保,因为它可以使用回收材料进行生产。
然而,吹塑也存在一些缺点。
首先是生产速度较慢,因为每个产品都需要单独制造,并且需要一定的冷却时间。
此外,在制造大型产品时可能会遇到困难,并且在某些情况下可能会存在一定的质量问题。
总之,吹塑是一种广泛应用于塑料制品生产中的工艺技术。
通过了解其基本流程和优缺点,我们可以更好地理解它在实际应用中的作用和局限性,并为未来的发展提供有益参考。
- 1、下载文档前请自行甄别文档内容的完整性,平台不提供额外的编辑、内容补充、找答案等附加服务。
- 2、"仅部分预览"的文档,不可在线预览部分如存在完整性等问题,可反馈申请退款(可完整预览的文档不适用该条件!)。
- 3、如文档侵犯您的权益,请联系客服反馈,我们会尽快为您处理(人工客服工作时间:9:00-18:30)。
吹塑托盘的成型工艺和问题解决
1.吹塑托盘的结构特点
吹塑托盘大多为双面使用,主要由立柱和条状的加强筋组成。
产品吹塑成型以后,需要采用后加工设备对其叉口部分进行切割加工,以方便叉车的叉板进出。
而且使用时对吹塑塑料托盘的受力状况有明确的要求。
所以,对吹塑型塑料托盘的加强筋以及叉口的设计的改进,成为该产品近年来技术进步的标志。
吹塑型塑料托盘近年来得到了较快的发展,产品市场的增长幅度较大。
近年来吹塑托盘研制速度在加快,张家港市同大机械有限公司近年来已经研究发明出全新的国际领先的吹塑托盘内加筋技术,该技术可以方便的应用到单、双面吹塑托盘的成型,为吹塑托盘在货架、生产线上使用开拓了较好的市场前景,采用这项成型技术生产时,其扰曲值仅为8-9毫米。
预计这一技术与高强度吹塑托盘将获得较快的使用和市场推广。
2.吹塑托盘的吹胀比
吹塑托盘的形状如扁平状,类似于双重壁的工具箱类的产品成型相近。
它在吹塑成型时的吹胀比不能过大,通常吹胀比选择1-1.5为宜。
3.吹塑托盘的基本参数
(1)加强筋和立柱的脱模斜度由于吹塑托盘的立柱和加强筋比较多,制品脱模的阻力较大,其脱模斜度不能过小,一般脱模斜度选择范围:4-8度,制品厚度方向周边的脱模斜度为1-3度。
(2)加强筋之间的中心距离对于制品的成型和产品的承载能力有较大的关系,中心距过小,产品成型时容易造成产品的壁厚变薄或是不均匀,中心距离过大,则容易造成产品的单位承载能力下降。
在制品单个重量一定的情况下,加强筋的多少及布置方式对于吹塑托盘的质量影响较大。
吹胀比立柱及加强筋脱
模斜度(度)厚度方向周边脱
模斜度(度)
加强筋的中心距
/MM
立柱大端直径
/MM
1-1.5 4-8 1-3 60-120 35-70
4.吹塑托盘的成型工艺
(1)设备基本的工艺参数
主液压系统压力为12-18p/mpa;伺服液压系统压力12-18p/mpa;压缩空气压力0.5-0.9p/mpa;循环水压力0.3-0.4p/mpa;液压油温度25-55度;循环水温度20-35度;模具冷却水温度7-18度。
(2)成型温度参数的设定
加热区间 1 2 3 4 5
设定值储料机头210 210 220 220 220 挤出机身170 180 195 200 210
实际值储料机头215 215 225 225 225 挤出机身175 187 200 205 215
成型温度参数的设定与采用的塑料原料配方以及挤出机螺杆的性能密切相关,在温度参数设定时需要根据具体情况而定。
生产吹塑托盘的中空吹塑设备很大,储料机头的体积相应较大,初次升温的时间相应较长,一般在12-16H。
加温过程中需要注意保障电气控制系统的完好性和储料机头冷却水的畅通。
(3)产品成型周期根据产品形状和模具的冷却速率而定,一般在3-12min.
5.产品的检测与试验
吹塑托盘出模后经过修边并称量及钻孔后,平整堆放在通风的场地上,可以叠放到15个左右,待24小时完全冷却后,将叉口部分再采用专机进行修整并进行全部外观检查以及抽样检查。
检测项目名称测试条件测试结果
角部跌落试验0.5-1.5mm,20℃-25-40℃,48h 三次不损坏
滑动试验20℃,-25-40℃,40℃,48h 无滑动现象
绕曲率弯曲试验12500+—375
6.吹塑托盘设备与新技术
前些年国内应用于吹塑托盘的设备较少,20世纪80年代国内厂家从日本进口一套吹塑托盘生产线,设备型号:IPB-2000C,安装调试生产到现在,设备经过生产厂家多次改进,仍然在生产吹塑托盘,该生产线是国内最早应用于专业生产吹塑托盘的设备。
进入20世纪90年代,国内相继研发成功1000L的吹塑机组,应用于生产1000LIBC塑料桶制品生产厂家初步形成一定批量的生产能力,到近年国内吹塑托盘的年生产能力与销售量仅在60万左右。
随着吹塑托盘应用市场的迅速发展,苏州同大机械有限公司在近年来中研发成功多条吹塑托盘大型生产线,以及吹塑托盘的成型技术。
并且已经在张家港同大吹塑有限公司投入大批量生产各种不同规格的吹塑托盘。
目前该公司采用国内目前最大的TDB-2000L大批量向国内一些大型企业供货,可满足-40-45℃环境下正常使用。
苏州同大机械有限公司研发成功的TDB-2000L、吹塑托盘告诉生产线在储料机头、合模机、液压系统等方面进行了重大技术突破与改进,采用扁平储料机头结构,内部流道设计时经过计算机三维造型设计与计算机工程分析计算,使所设计的扁平制品更为方便与快速,更适合高速生产吹塑托盘。
主液压系统的能耗较大幅度降低,其电动机功率仅为26KW,仅相当于国内普通1000L吹塑机组液压系统电动机功率的1/4左右,并且较大幅度地提高了制品成型速度;使生产效率进一步提高。
张家港同大吹塑有限公司于2011年研发成功具有国际先进水平的内加强筋吹塑技术并成功的应用于吹塑托盘成型工艺,使单面吹塑托盘的绕曲率大为降低,川字形吹塑托盘的饶曲值在货架载荷1000KG时仅为4-6mm.内加强筋吹塑技术将为一些特殊吹塑制品提高刚度与扩大应用市场发挥其独有的作用;该产品与技术已经获得国家多项发明专利权的授权。
7.知识产权方面的注意事项
国内吹塑托盘的生产正在进入一个比较快速的增长期,一些塑料制品企业在进入吹塑托盘制造厂家的初期,在吹塑托盘的设计与开发时,需要特别注意多收集相关知识产权方面的资料,尽量避免发生侵犯相关知识产权与专利权的情况。