液压缸各项检验
液压缸维修标准

液压缸维修标准
液压缸维修标准主要包括以下几个方面:
1. 外观检查:检查液压缸的外观是否有裂纹、变形、腐蚀等缺陷。
2. 内部检查:检查液压缸的内部是否有污垢、异物、磨损等问题。
3. 密封检查:检查液压缸的密封是否完好,是否有泄漏等问题。
4. 活塞杆检查:检查活塞杆是否有弯曲、磨损、腐蚀等问题。
5. 液压缸性能检查:检查液压缸的工作性能是否正常,如推力、速度、行程等。
6. 维修或更换:根据检查结果,对液压缸进行维修或更换。
以上是液压缸维修标准的一些基本内容,具体的维修标准还需要根据不同的液压缸型号和使用环境进行具体分析。
油缸质量鉴定

油缸质量鉴定
1油缸质量鉴定
油缸是非常重要的机械部件,能够帮助润滑机器的活动部件,而且具有较高的承受力,现在油缸类似机械部件仍然被广泛应用在机械制造行业当中。
但是由于不同生产厂家的技术不同,鉴定油缸的质量是非常重要的。
1.1材料分析
首先要做的就是油缸的材料分析,从而判断油缸的质量,一些关键的物理参数都要进行测试,包括抗拉强度、压缩强度、断裂能力等,同时元素分析也要进行检测。
1.2尺寸检查
油缸要符合厂家规定的尺寸,这种尺寸检查要求更加精确,特别是外径和厚度,以确保油缸能够适应机械部件的装配尺寸。
1.3表面检查
检查油缸的表面变形状态和表面粗糙度,可以用一定方式来检测这两个参数,以确保油缸的尺寸精度和外观质量。
1.4压力容极限试验
最后轴承壳体还要经过压力试验,以确保其承受力。
这种试验的目的是测试油封在最大的工作压力下是否能够正常使用,从而确保油封能够正常工作,提高了机械设备的安全性和使用寿命。
通过上述分析,油缸能得到准确而全面的质量鉴定,从而为机械设备提供准确的润滑部件。
液压缸装配出厂试验规范
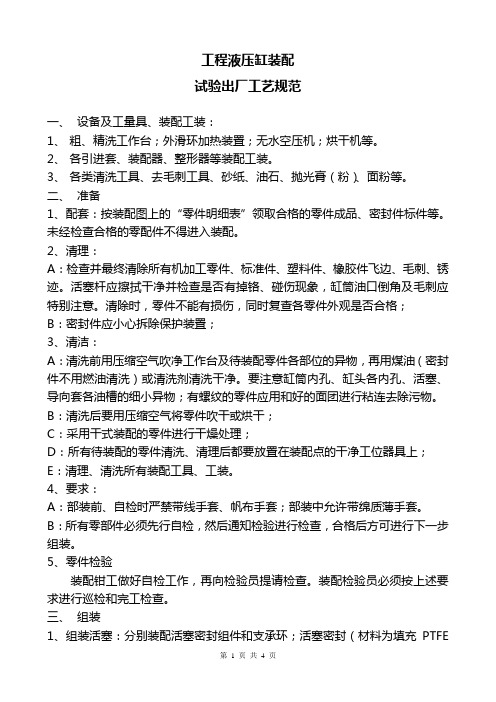
工程液压缸装配试验出厂工艺规范一、设备及工量具、装配工装:1、粗、精洗工作台;外滑环加热装置;无水空压机;烘干机等。
2、各引进套、装配器、整形器等装配工装。
3、各类清洗工具、去毛刺工具、砂纸、油石、抛光膏(粉)、面粉等。
二、准备1、配套:按装配图上的“零件明细表”领取合格的零件成品、密封件标件等。
未经检查合格的零配件不得进入装配。
2、清理:A:检查并最终清除所有机加工零件、标准件、塑料件、橡胶件飞边、毛刺、锈迹。
活塞杆应擦拭干净并检查是否有掉铬、碰伤现象,缸筒油口倒角及毛刺应特别注意。
清除时,零件不能有损伤,同时复查各零件外观是否合格;B:密封件应小心拆除保护装置;3、清洁:A:清洗前用压缩空气吹净工作台及待装配零件各部位的异物,再用煤油(密封件不用燃油清洗)或清洗剂清洗干净。
要注意缸筒内孔、缸头各内孔、活塞、导向套各油槽的细小异物;有螺纹的零件应用和好的面团进行粘连去除污物。
B:清洗后要用压缩空气将零件吹干或烘干;C:采用干式装配的零件进行干燥处理;D:所有待装配的零件清洗、清理后都要放置在装配点的干净工位器具上;E:清理、清洗所有装配工具、工装。
4、要求:A:部装前、自检时严禁带线手套、帆布手套;部装中允许带绵质薄手套。
B:所有零部件必须先行自检,然后通知检验进行检查,合格后方可进行下一步组装。
5、零件检验装配钳工做好自检工作,再向检验员提请检查。
装配检验员必须按上述要求进行巡检和完工检查。
三、组装1、组装活塞:分别装配活塞密封组件和支承环;活塞密封(材料为填充PTFE必须在50°C~60°C的油温中浸泡后才可装配)装配后必须进行整形。
活塞为螺纹式时,将0形圈装入内台阶孔的O形圈槽内。
2、组装导向套:分别装配轴用组合密封、Y型密封圈、防尘圈(或支承环)和O型圈,组装导向套必须采用干式装配。
3、组装活塞杆:A:活塞杆小端为卡键式:将活塞杆小端装上O型圈,然后装配活塞组件,再按图纸要求装轴用卡键、卡键帽、轴用挡圈及其它零件。
液压系统故障的检查与排除(二篇)
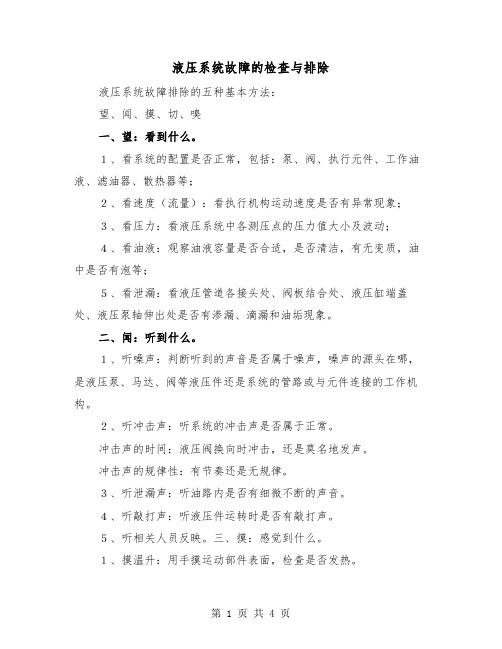
液压系统故障的检查与排除液压系统故障排除的五种基本方法:望、闻、摸、切、嗅一、望:看到什么。
1、看系统的配置是否正常,包括:泵、阀、执行元件、工作油液、滤油器、散热器等;2、看速度(流量):看执行机构运动速度是否有异常现象;3、看压力:看液压系统中各测压点的压力值大小及波动;4、看油液:观察油液容量是否合适,是否清洁,有无变质,油中是否有泡等;5、看泄漏:看液压管道各接头处、阀板结合处、液压缸端盖处、液压泵轴伸出处是否有渗漏、滴漏和油垢现象。
二、闻:听到什么。
1、听噪声:判断听到的声音是否属于噪声,噪声的源头在哪,是液压泵、马达、阀等液压件还是系统的管路或与元件连接的工作机构。
2、听冲击声:听系统的冲击声是否属于正常。
冲击声的时间:液压阀换向时冲击,还是莫名地发声。
冲击声的规律性:有节奏还是无规律。
3、听泄漏声:听油路内是否有细微不断的声音。
4、听敲打声:听液压件运转时是否有敲打声。
5、听相关人员反映。
三、摸:感觉到什么。
1、摸温升:用手摸运动部件表面,检查是否发热。
2、摸振动:感觉是否有振动现象。
3、摸爬行:感觉运动件有无“爬行”现象。
4、摸松紧程度:检验螺纹连接松紧程度。
5、摸密封性:对看不到的地方,检查是否有漏油现象。
四、切:用压力表判断。
1、各处的压力值是否正常:泵的吸油、出油,马达的进油、出油,油缸两腔的油压,阀的工作压力、控制压力等;2、压力是否有波动,波动是否在设计范围内。
五、用嗅觉判断。
1、闻一下油液是否发臭变质;旧车:使用时间长,油液成分会变质,发臭等怪味,新车:检查加油是否有误操作,防止加错油。
2、闻整系统是否有异味,出自何处。
液压系统故障的检查与排除(二)液压系统是一种利用液体传递能量和动量的技术,广泛应用于各种工程和机械设备中。
然而,由于使用条件和设备老化等原因,液压系统可能会出现故障。
本文将介绍液压系统故障的常见检查和排除方法。
首先,对于液压系统故障的检查,我们可以按照以下步骤进行。
液压缸检验规范

1双作用液压缸检验标准
1.1出厂检验项目、内容、方法和要求
1.1.1全检项目(每一台产品上进行的检验)
序号
检验项目
试验方法
检验要求
1
空载运转
被试缸在无载工况下,全行程上进行5次试运转。活塞运源自平稳2最低启动压力
在空载运行时,从无杆腔逐渐施加压力,测其活塞的最低启动压力。
V
其他
Pn≤10MPa
Pn>10 MPa
Pn≤10 MPa
Pn>10 MPa
0.75MPa
0.09Pn
0.5MPa
0.06Pn
0.45MPa
0.06Pn
0.3MPa
0.04Pn
3
耐压试验
在被测缸无杆腔和有杆腔分别施加公称压力Pn的1.5倍(当Pn﹥16MPa时,应为1.25倍)将活塞分别停留在行程的两端,保持2min进行试验
不允许有外部渗油、爬升等不正常现象
2
耐压试验
在被测柱塞缸的柱塞处全部伸出位置,调节溢流阀使缸内的压力为额定压力的1.5倍,保压2min进行试验
1.不得有外部渗漏
2.全部零件均不得有永久变形
3
外部渗漏
全行程运行换向20次,然后测量柱塞杆处的渗漏量
≤0.025mL
2.1.2抽检项目(液压油缸的抽检数量为每批产品的2%,但不得少于2台,若抽检中有不合格项目,则对此项目应加倍复试,如仍不合格,则对该批产品全检)
序号
检验项目
试验方法
检验要求
1
最低启动压力
在无负荷情况下,调节溢流阀逐渐升压至柱塞开始运动时,测量柱塞缸内的压力,即为最低启动压力
≤0.56MPa
2
液压油缸检测报告2-1

日期:2014年10月21日
液压油缸检测报告
产品名称:工程机械液压缸
规格型号:HSG63/35-80
产品数量:16只
试验项目
试验方法
试验要求
检验结果
备注
试运转
液压缸在空负载工况下全行程往复动作5次以上
运转正常
正常
不正常□
最低启动压力
空载工况下,液压缸无杆腔通入液压油,溢流阀从零开始逐渐升压,观察压力表,记录液压缸活塞杆在启动时的最低启动压力
0.3MPa
正常
不正常□
耐压试验
将液压缸的活塞分别停留在行程两端。调节溢流阀使试验腔的压力为额定压力的1.25倍保压5min
全部零件均不得有破坏或永久变形等异常现象
正常
不正常□
内泄漏
液压缸的活塞分别固定在行程的两端,调节溢流阀,使液压缸的试验腔为额定压力,测量另一腔出油口处泄漏量
1.0~2.2ml/min
正常
不正常□
外渗漏
在检查内泄漏和耐压试验Байду номын сангаас观察活塞杆处及其它结合面渗油情况
在耐久性试验的连续运转中测量活塞杆处外渗漏量
活塞杆处无渗油,缸筒焊接无渗油
有□
无
行程
使液压缸的活塞分别停留在行程的两端位置,测量全行程长度
80±0.5mm
正常
不正常□
经检验,此液压缸各项技术指标均符合国家标准GB/T 15622-2005《中高压液压缸试验方法》的规定,质量合格
液压油缸质量检验规范

液压油缸质量检验规范
前言
本规范用于液压油缸的质量检验,旨在保证液压油缸的质量,提高产品的可靠性和安全性。
检验标准
1. 外观检验
液压油缸的外观应该无裂纹、无变形、无划痕、表面无锈蚀,在装配后应该无泄漏。
2. 尺寸检验
液压油缸的内径、外径、活塞杆直径、活塞杆长度应该符合设计要求。
3. 强度检验
液压油缸在压力测试时,应该承受规定压力2倍的测试压力,无破裂、变形和泄漏等现象。
4. 密封性检验
液压油缸在压力测试时,应该保持规定压力10分钟,没有任何泄漏现象,且在经过密封性试验后活塞杆不会出现损坏。
检验方法
1. 外观检验
使用肉眼或放大镜仔细检查液压油缸表面,如果发现异常,应该进行更加细致的检查。
2. 尺寸检验
使用专业的检测设备,比如游标卡尺、外径千分尺、内景千分尺等,测量液压油缸的相关尺寸。
3. 强度检验
沿对称轴向液压油缸施加试验压力,在压力测试过程中观察液压油缸的变形情况和是否有漏油现象。
4. 密封性检验
涂抹液压油缸需要检验的密封部位,将液压油缸放入水中进行压力测试,观察是否有气泡冒出,检查活塞杆样子并观察密封性。
结论
液压油缸的检验可以保障其质量,减少使用过程中出现的故障,确保液压油缸能够在高压下稳定运行,提高设备的工作效率和安全性。
液压缸主要零部件通用检验指导书

液压缸主要零部件通用检验指导书一、液压缸活塞杆通用检验1目的对液压缸活塞杆的检验项目、方法、记录等程序作出规定,以便活塞杆检验得到有效控制。
2适用范围适用于对液压缸活塞杆的检验和试验。
3职责3.1热处理检验员负责热处理调质的硬度、直线度的检验、标识、记录。
3.2车加工检验员负责活塞杆精车后的尺寸、粗糙度、垂直度等项目的测量、标识及记录,并进行首件检验和巡回检验。
3.3铣加工检验员负责活塞杆精镗孔后的尺寸、粗糙度、垂直度等项目的测量、标识及记录,并进行巡回检验。
3.4焊接检验员负责活塞杆焊接后的外观质量、坡口尺寸及焊接位置的检验及标识,并进行首件检验和巡回检验。
3.5试压检验员负责内回油活塞杆的试压检验、标识及记录。
3.6磨加工检验员负责精磨后尺寸、粗糙度的检验、标识及记录,并进行首件检验和巡回检验。
3.7电镀检验员负责活塞杆镀铬抛光后的质量检验并作标识记录。
4工作程序4.1活塞杆的热处理调质的硬度试验、直线度的检验按《热处理通用技术条件》第5条进行检验和试验。
4.2活塞杆精车检验4.2.1活塞杆精车检验项目A大外圆尺寸及圆度;B装活塞处与活塞配合外圆尺寸;C密封沟槽底直径及粗糙度;D同轴度;E密封沟槽装活塞部位外圆粗糙度F活塞部分外径及各沟槽的尺寸、粗糙度;(各种整体活塞的活塞杆检查此项)G其他尺寸(包括未注公差的长度及其他尺寸)。
4.2.2检验用器具、检验方法及判断方法A大外圆尺寸直接用卡尺或千分尺测量,至少测量三处,应符合工艺留量要求;B装活塞处与活塞配合外圆尺寸直接用千分尺测量,应符合工艺留量要求;C密封沟槽槽底直径直接用卡尺或千分尺测量,应符合图纸尺寸要求;D同轴度的检验①小件可在偏摆仪上进行检验;②长度超过1米、直径超过Φ60mm可直接在车床上检验;③采取抽样检验每批不少于20%,批量小的每批不少于1件;④同轴度应符合图纸要求。
E粗糙度直接用粗糙度样块比较,应符合图纸及工艺要求。
F整体活塞活塞杆的活塞部分外径及各沟槽的尺寸、粗糙度的检验①外径尺寸直接用卡尺或千分尺测量,应符合图纸要求;②各沟槽槽底直径尺寸直接用卡尺或千分尺测量,应符合图纸要求;③粗糙度检验用粗糙度样块对比,应符合图纸要求。
- 1、下载文档前请自行甄别文档内容的完整性,平台不提供额外的编辑、内容补充、找答案等附加服务。
- 2、"仅部分预览"的文档,不可在线预览部分如存在完整性等问题,可反馈申请退款(可完整预览的文档不适用该条件!)。
- 3、如文档侵犯您的权益,请联系客服反馈,我们会尽快为您处理(人工客服工作时间:9:00-18:30)。
同表1缓冲试验方法
同表1
5
耐压试验
必测
同表1耐压试验方法
同表1
6
外渗漏
必测
同表1外渗漏试验方法
同表1
7
全行程检查
必测
同表1全行程检查试验
同表1
按GB/T10205-2000规定,见附表1
4
缓冲试验
在额定压力的50%下,以设计的最高速度运行,检测当运行至缓冲位置时的缓冲效果(有缓冲阀的应调节缓冲阀)
有明显缓冲效果
5
负载效率
将测力计装在被试缸的活塞杆上。调节溢流阀2,使进入被试缸的液压油的压力逐渐升高,测出不同压力下的负载效率
按GB/T10205-2000规定,见附表1
按设计要求
8Hale Waihona Puke 外泄漏在整个试验过程中,检测活塞杆密封处的泄漏量;检查缸体各静密封处、结合面处和可调节机构处是否有渗漏现象
按GB/T10205-2000规定,见附表1
9
高温试验
被试缸在额定压力下,通入90℃的油液,连续运转一小时以上
正常工作无异常
10
耐久性试验
在额定压力下,使被试液压缸以设计要求的最高速度连续运行,速度误差为士10%。一次连续运行8h以上。在试验期间,被试液压缸的零件均不得进行调整。记录累计行程。
1
试运转
被试液压缸在空负载工况下全行程往复动作5次以上
运行正常
2
起动压力
特性试验
空载工况下,被试缸无杆腔通入液压油,溢流阀2从零开始逐渐升压,观察压力表6-2,记录被试缸活塞杆在启动时的最低启动压力
按GB/T10205-2000规定,见附表1
3
内泄漏
被试缸的活塞分别固定在行程的两端,调节溢流阀2,使被试缸的试验腔压力为额定压力,测量另一腔出油口处泄漏量
耐久性试验后,进行拆检、全部零件不得有破坏和影响正常使用的异常现象
表2液压缸出厂检验项目与方法(参照GB/T15622—2005)
序号
试验项目
类别
实验方法
试验要求
1
试运转
必测
同表1试运转试验方法
同表1
2
最低启动压力
必测
同表1最低启动压力试验方法
同表1
3
内泄漏量
必测
同表1内泄漏量试验方法
同表1
4
缓冲试验
液压缸技术要求
液压缸在出厂时,必须按照国家规定及现行我国机械行业的有关标准,进行出厂试验。根据我国国家标准GB/T15622—2005<液压缸试验方法>的规定,其型式试验和出厂试验的项目与方法分别如表1和表2所示。
表1液压缸型式试验项目与方法(参照GB/T15622—2005)
序号
试验项目
实验方法
试验要求
6
耐压试验
将被试缸的活塞分别停留在行程两端(不能接触缸盖)。当额定压力≤30MPa时,调节溢流阀 2使试验腔的压力为额定压力的 1.5倍;当额定压力>30MPa时,调节溢流阀 2使试验腔的压力为额定压力的 1.25倍保压2min。
全部零件均不得有破坏或永久变形等任何异常现象
7
全行程检查
使被试缸的活塞分别停留在行程的两端位置。测量全行程长度