高炉停炉降料面方案讲解
马钢3高炉降料面停开炉方案(优.选)
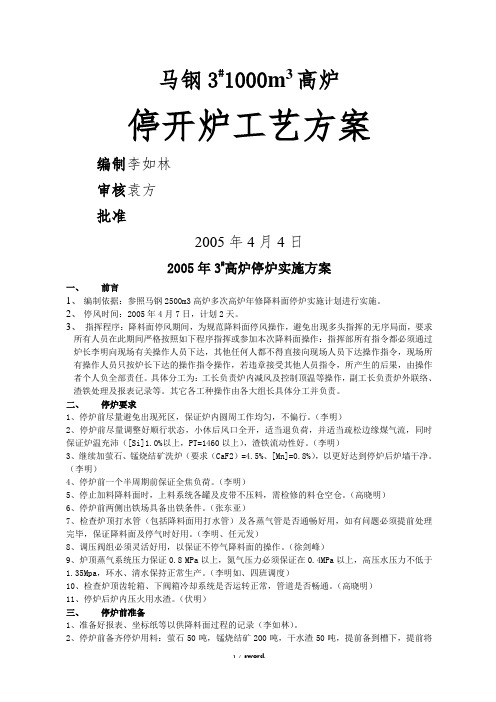
马钢3#1000m3高炉停开炉工艺方案编制李如林审核袁方批准2005年4月4日2005年3#高炉停炉实施方案一、前言1、编制依据:参照马钢2500m3高炉多次高炉年修降料面停炉实施计划进行实施。
2、停风时间:2005年4月7日,计划2天。
3、指挥程序:降料面停风期间,为规范降料面停风操作,避免出现多头指挥的无序局面,要求所有人员在此期间严格按照如下程序指挥或参加本次降料面操作:指挥部所有指令都必须通过炉长李明向现场有关操作人员下达,其他任何人都不得直接向现场人员下达操作指令,现场所有操作人员只按炉长下达的操作指令操作,若违章接受其他人员指令,所产生的后果,由操作者个人负全部责任。
具体分工为:工长负责炉内减风及控制顶温等操作,副工长负责炉外联络、渣铁处理及报表记录等。
其它各工种操作由各大组长具体分工并负责。
二、停炉要求1、停炉前尽量避免出现死区,保证炉内圆周工作均匀,不偏行。
(李明)2、停炉前尽量调整好顺行状态,小休后风口全开,适当退负荷,并适当疏松边缘煤气流,同时保证炉温充沛([Si]1.0%以上,PT=1460以上),渣铁流动性好。
(李明)3、继续加萤石、锰烧结矿洗炉(要求(CaF2)=4.5%、[Mn]=0.8%),以更好达到停炉后炉墙干净。
(李明)4、停炉前一个半周期前保证全焦负荷。
(李明)5、停止加料降料面时,上料系统各罐及皮带不压料,需检修的料仓空仓。
(高晓明)6、停炉前两侧出铁场具备出铁条件。
(张东亚)7、检查炉顶打水管(包括降料面用打水管)及各蒸气管是否通畅好用,如有问题必须提前处理完毕,保证降料面及停气时好用。
(李明、任元发)8、调压阀组必须灵活好用,以保证不停气降料面的操作。
(徐剑峰)9、炉顶蒸气系统压力保证0.8 MPa以上,氮气压力必须保证在0.4MPa以上,高压水压力不低于1.35Mpa,环水、清水保持正常生产。
(李明如、四班调度)10、检查炉顶齿轮箱、下阀箱冷却系统是否运转正常,管道是否畅通。
济钢1750m_3高炉停炉降料面操作实践_芶毅
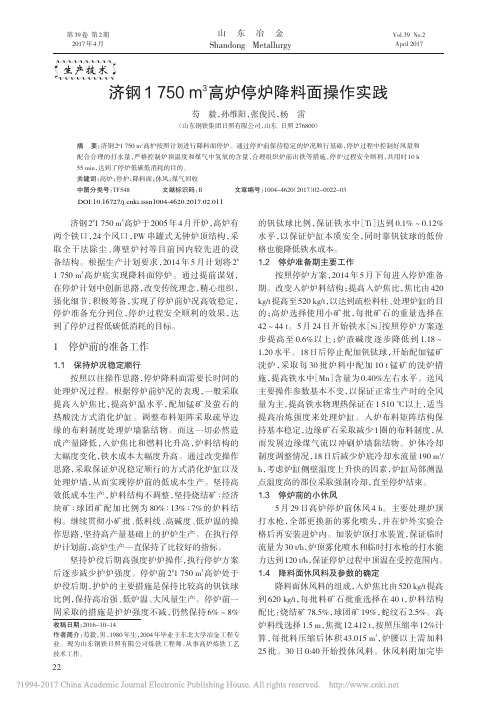
芶毅等
济钢 1 750 m3高炉停炉降料面操作实践
2017 年第 2 期
后,休风前加入盖面焦 60 t,料线 4.6 m。之后至休风 不再上料。
2 停炉降料面过程
本次采取回收煤气打水降温空料线停炉法。 高炉于 5 月 30 日 18:36 复风,降料面正式开始。起步 风量为 1 700 m3/min,逐渐加风至 2 500 m3/min,料面 正常活动后快速加风到 3 200 m3/min。18:45 引煤 气,22:45 放散煤气,期间回收煤气共 4 h。31 日 5:30 开始有部分风口吹空,高炉 6:31 完成休风,降料面 完毕。此次降料线历时近 11 h,料面降到风口中心 线以下,达到预期的停炉效果。 2.1 煤气回收及放散
������������
������������������������������������������������������������
第 39 卷 第 2 期 2017 年 4 月
山东冶金
Shandong Metallurgy
Vol.39 No.2 April 2017
������������
实际降料面过程中,煤气成分的变化趋势见表 1。炉顶混合煤气 H2、O2 含量一直在控制目标范围 内,TRT 发电保持正常。将料线 4 h 后根据雷达探尺 和吨铁耗风计算料面降至炉腰。30 日 22:30 左右判 断料面到 12~13 m,已经到达炉身下部、炉腰位置, 22:45 开放散阀,切断煤气,完成回收煤气过程。
坚持炉役后期高强度护炉操作,执行停炉方案 后逐步减少护炉强度。停炉前 2#1 750 m3高炉处于 炉役后期,护炉的主要措施是保持比较高的钒钛球 比例,保持高冶强、低炉温、大风量生产。停炉前一 周采取的措施是护炉强度不减,仍然保持 6%~8%
三座高炉降料面停炉案例分析
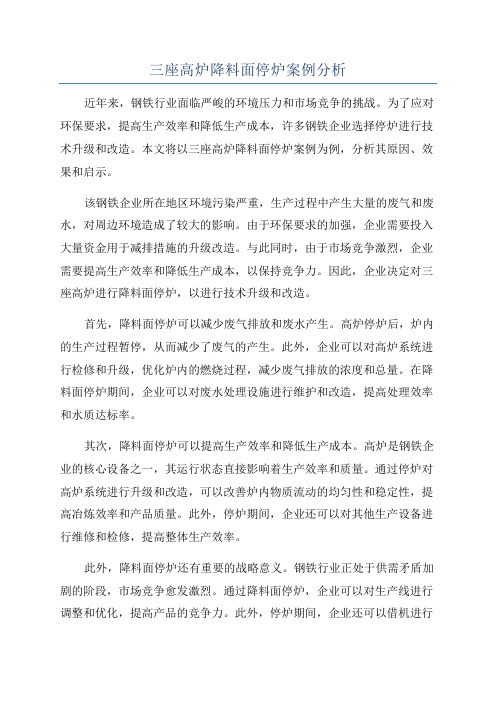
三座高炉降料面停炉案例分析近年来,钢铁行业面临严峻的环境压力和市场竞争的挑战。
为了应对环保要求,提高生产效率和降低生产成本,许多钢铁企业选择停炉进行技术升级和改造。
本文将以三座高炉降料面停炉案例为例,分析其原因、效果和启示。
该钢铁企业所在地区环境污染严重,生产过程中产生大量的废气和废水,对周边环境造成了较大的影响。
由于环保要求的加强,企业需要投入大量资金用于减排措施的升级改造。
与此同时,由于市场竞争激烈,企业需要提高生产效率和降低生产成本,以保持竞争力。
因此,企业决定对三座高炉进行降料面停炉,以进行技术升级和改造。
首先,降料面停炉可以减少废气排放和废水产生。
高炉停炉后,炉内的生产过程暂停,从而减少了废气的产生。
此外,企业可以对高炉系统进行检修和升级,优化炉内的燃烧过程,减少废气排放的浓度和总量。
在降料面停炉期间,企业可以对废水处理设施进行维护和改造,提高处理效率和水质达标率。
其次,降料面停炉可以提高生产效率和降低生产成本。
高炉是钢铁企业的核心设备之一,其运行状态直接影响着生产效率和质量。
通过停炉对高炉系统进行升级和改造,可以改善炉内物质流动的均匀性和稳定性,提高冶炼效率和产品质量。
此外,停炉期间,企业还可以对其他生产设备进行维修和检修,提高整体生产效率。
此外,降料面停炉还有重要的战略意义。
钢铁行业正处于供需矛盾加剧的阶段,市场竞争愈发激烈。
通过降料面停炉,企业可以对生产线进行调整和优化,提高产品的竞争力。
此外,停炉期间,企业还可以借机进行研发和创新,探索新的生产工艺和材料,提高企业的技术创新能力和产品附加值。
然而,降料面停炉也存在一些挑战和问题。
首先,停炉期间的生产线调整和设备维护需要耗费大量的资金和人力资源。
企业需要提前做好充分的准备和计划,确保停炉期间的维护和改造工作能够按时完成,并保证生产线的稳定和可持续运行。
其次,降料面停炉期间,企业的产能将受到一定程度的限制,可能会导致生产能力的下降和订单的延迟。
高炉降料面方案及安全措施

高炉降料面方案及安全措施其次炼铁厂8#高炉目前炉墙结瘤,操作炉型较差,煤气流分布偏析,气流较乱,高炉操作困难,炉况稳定性差,燃耗高,指标差。
公司拟定于2013年5月23日对8#高炉降料面炸熘喷涂造衬,规整炉型,消退影响,提高技术经济指标。
一、领导小组组长:姚克虎副组长:范兴新耿磊李见成组员:冯国祥徐明喜郭辉徐芹来苑少刚王海高刘立辉申立华代红卫田建刚乔治富彭永文二、停炉目标:1、降料面到风口中心线高度;2、排净渣铁;3、平安停炉。
三、停炉方法:采纳炉顶打水空料线法。
四、停炉前各项预备工作:1、停炉前(降料面)保证炉况顺行,降低炉渣碱度,提高铁水含硫以改善铁水的流淌性。
提前两个班加萤石洗炉,每批300kg,用量约30吨,保证炉缸活跃。
本次降料面炸瘤喷涂方案用时4天,更换气密箱2天,烘炉2天。
为保证在重新开炉达产顺当,要求停炉前排净渣铁。
2、停炉前,全面检查各冷却设备、机械设备、电气设备正常,全面进行平安隐患排查,漏水冷却壁改为蒸汽冷却;3、确定煤气在线监测装置可以正常使用;4、重点检查炉顶雾化打水装置,炉顶打水装置安装流量表,保证稳定的供水量。
5、做好热风围管的支撑工作,防止小套拉下后围管变型。
6、预备好扒料工具。
五、停炉料:1、轻负荷料Q1:掌握停炉降料面前到达风口位置。
(焦比460kg/t,煤比100kg/t)矿批:17000kg,焦批(干基):4400kg,调矿配比掌握炉渣碱度在1.05~1.10,镁铝比掌握在0.75。
每批料体积约为17m3,共计12批。
2、轻负荷料Q2:掌握停炉降料面前到达炉身底部位置。
(全焦冶炼,焦比按600kg/t)矿批:17000kg,焦批(干基):5700kg,调矿配比掌握炉渣碱度在1.00~1.05,镁铝比掌握在0.75。
每批料体积为19m3,共计15批。
3、盖面焦Q3:掌握停炉降料面后期顶温,停炉前到达风口位置。
焦批(干基):5700kg。
每批料体积为9.5m3,共计8批。
高炉降料面方案及安全措施

高炉降料面方案及安全措施一、引言高炉降料是指在高炉顶部将原料向下引入高炉中的过程。
这个过程不仅涉及到生产的质量和效率,还需要与安全性密切相关。
因此,合理地设计高炉降料面方案并采取相应的安全措施是非常必要的。
二、高炉降料面方案高炉降料面方案一般需要根据高炉的具体情况来进行合理设计。
下面列出一些常见的高炉降料面方案。
1. 单口式降料口单口式降料口是将全部原料从一个口子中引入高炉,这种方式使用较为普遍。
单口式降料口有以下优点:•系统简单,降料均匀•可以在操作时实现不间断降料•可以对降料流量进行调节但是单口式降料口也有一些缺点:•降料口过小容易造成原料包塞•一旦出现故障难以及时排除2. 双口式降料口双口式降料口是在高炉两侧设置降料口,将原料分别向高炉中心引入。
这种方式使用较少,但有以下优点:•降料口相对较大,不容易造成原料堵塞•可以随时将某一侧降料口关闭维修,不影响生产但是双口式降料口也有一些缺点:•降料口过大容易导致温度分布不均•安装相对复杂,需要较多的空间3. 活动式降料口活动式降料口是指在高炉顶部设置一个稍微大一点的口子,通过可动式的圆锥体控制料流的大小,从而实现控制降料流量和调整降料口位置的目的。
不同于前两种降料口方案,活动式降料口的缺点在于操作相对复杂,但优点也十分明显:•能够实现比较准确的流量调节•可以调整降料口位置•便于维护和检修三、高炉降料面安全措施在高炉降料的过程中,需要特别注意以下安全措施。
1. 卸料前验明卸料道状态在卸料前应按规定进行检验,包括卸料道的通畅情况和卸下料斗的封闭情况,切勿盲目开启卸下料门。
2. 监测房间保持干燥高炉降料的监测房间应保持干燥,以防止电气下短路或因潮湿引起故障。
3. 防止高炉降料中断降料的中断会影响炉内物料的质量,需确保原料的供给充足稳定。
4. 停车前附设安全阀为保证卸下料门的安全性,应在卸下料门处附设安全阀,防止压力过大造成炉芯异常。
5. 根据规定操作在操作高炉降料时,应当按照规定和操作程序进行,避免出现错误操作。
2#高炉大修停炉及残铁排放方案

2#高炉大修停炉及残铁排放方案2#高炉计划2014年11月1日18时开始打水降料面停炉。
要求料线降至风口以下,为确保停炉安全,制定此方案。
一、组织机构二、准备工作1、制作四进四出分配器,放于风口平台,分配器进水管接在风口给水环管上保证全开,出水管接∮25mm白钢阀门,末端作成梢口,各阀门做好标记,降料面过程中力争四个出水管打水均匀。
2、制作喷水枪四支,要形成雾状,安装前必须在取样孔平台处试验喷水情况,打水压力要大于炉顶压力0.05MPa。
打水控制阀门置于风口平台。
所需材料:∮25mm、长4000mm焊管4根,∮32mm胶管160m,∮25mm白钢阀门4个。
喷水枪制作要求:将4000mm焊管一端焊死,一端作成梢口。
从焊死端头开始至另一端1400mm长度内,每隔75mm钻一个∮3mm 的圆孔,交错分布共三排,相临两排之间夹角为45°。
3、休风前校验炉顶温度、荒煤气温度电偶是否准确,如不准预休风时必须处理准确。
4、准备对讲机一对。
5、预休风检查炉顶四个打水枪喷头,并试水调试。
6、制作1把长度15米、标记明确的软探尺。
(由李耀军负责)负责人签字______7、预休风时将通炉顶蒸汽盲板撤掉,并将水排净。
8、提前一周将1#风口捅开,[Si]按0.5%左右控制,按正常风速提高风量,活跃炉缸。
9、提前一天安排清理炉顶油污及易燃物,保持现场整洁。
10、提前3天将所有矿槽轮流倒空一遍。
三、降料面工艺操作2、1日14时左右,变全焦冶炼(考虑预休风送风后风温降低,要多加焦炭)负荷按控制,18时停喷煤。
[Si]按0.6~1.0%控制,[S]按0.030~0.050%控制。
高炉工段提前一天通知喷煤工段,便于喷煤工段做好停煤前的准备工作。
3、停煤粉后即停止富氧,关A、B阀并加盲板。
4、加盖面焦约15t。
5、1日18时左右,开始料车打水降料面,要求提前测量料车打水量,以料车不流水为准。
控制炉顶温度翻料,尽最大能力降料面。
高炉大修降料面停炉方案

黑龙江建龙3#高炉大修降料面停炉方案
编制:孙志强
审批:张显锋
2012年7月10日
方案目录
一、组织机构和职责
二、停炉要求与方法
三、停炉前的准备工作
四、预休风工作安排停炉操作
五、安全规定
六、事故预案
附:1、高炉停炉条件确认表
2、停炉工艺方案
建议公司成立相关机构,帮助炼铁厂协调降料面的相关工作。
需要部门有:生产处、技术处、设备处、安环处、保卫处、能源中心、检修中心。
具体事宜:生产处:优质原燃料的组织生产,降料面停炉方案的审批。
ﻩ技术处:降料面停炉方案的审批,停炉期间混合煤气的现场化验。
行政处:停炉降料面期间消防及辆到达现场
设备处:停、开炉期停炉降料面间控制程序及
称量数据的准确。
安环处:安全方案的审批,协助、督导、指挥安全工作
及救护车车辆的联系。
保卫处:停炉降料面期间警戒,消防车的协调。
能源中心:能源介质用量的保证,煤气防护人员现场的监
护。
高炉降料面总结

2#高炉停炉操作总结一、停炉方案的确定2#高炉于2017年5月1日19:15分降料面停炉。
为确保停炉工作的安全、顺利以及停炉工艺的先进,对停炉方案制定了以下原则。
1、采用空料线打水法;2、空料线期间常压不回收煤气;3、根据安装特殊长探尺;结合煤气成份变化及累计风量分析法判断料面高度。
二、停炉准备工作1、停炉前1天,高炉有计划空仓,保证炉况顺行;2、停炉前1天开始适度发展边缘气流,冲刷炉墙,使渣皮脱落,保持全风作业,保证停炉后炉墙干净,炉缸活跃。
3、停炉前1天生铁[Si]控制水平由0.30-0.50%提高到0.40-0.60%,炉渣碱度由校核1.20降低至1.17±0.02;4、停炉前1天,对高炉冷却设备进行全面检查,严禁向炉内漏水。
5、停炉前2天,制做出一套(4根)打水管,并试验合格;要求水压>1.2Mpa,水量>80t/h(每根打水管水量20t/h)。
6、停炉预休风前5小时7:00改焦比630kg一级焦比例增加到50%,15:00改焦比633kg矿批28t,炉料配比为67%烧结+33%球团,预休风前加盖面焦30吨(15:21休风);7、停炉前预休风(实际5月1日15:21-19:15);7.1 休风后料线控制在7m左右(实际约7.8m);7.2 安装打水装置以及流量计(四个方位安装高压水管及电调控制实现远程控制);7.3 从炉顶东南上升管接煤气取样管并引至风口平台。
三、停炉降料线操作1、预休风复风后开始正式降料面;2. 降料面期间料线和风量之间关系确定吨焦风耗的确定根据对前3天对2#高炉的耗风量进行统计,计算统计吨焦耗风量为2850m3。
考虑随料线的下降,煤气利用和风量的利用率下降的影响,吨焦风耗取2900m3。
(根据计算预休风后炉内共计湿焦319t,焦水取6%则干焦300t,料线将至风口共需耗风710000m3)3、严格控制煤气含H2和O2,要求H2<6%,O2<2%,当炉顶温度300℃时,O2小于1.8%。
- 1、下载文档前请自行甄别文档内容的完整性,平台不提供额外的编辑、内容补充、找答案等附加服务。
- 2、"仅部分预览"的文档,不可在线预览部分如存在完整性等问题,可反馈申请退款(可完整预览的文档不适用该条件!)。
- 3、如文档侵犯您的权益,请联系客服反馈,我们会尽快为您处理(人工客服工作时间:9:00-18:30)。
8#高炉停炉降料面方案依据公司安排,8#高炉定于2011年10月25日停炉,停炉降料面方案制定如下:一、时间及要求1、采用炉顶打水管打水及气密箱冷却水溢流降料面停炉法,料面降到风口中心线以下,降料面前期回收高炉煤气。
2、计划10月25日12:00~13:00停止上料,开始降料面操作,出最后一次铁休风时间安排在风口局部吹空后,预计降料面时间为15~17小时,(考虑最后出铁量多少,影响焦炭燃烧量和送风时间)断风时间根据最后一次出铁时间而定。
3、坚持安全第一、减少污染的方针,严格按照降料面的技术要求,杜绝人身、设备、质量等事故。
二、停炉前的准备工作1、加强铁罐的组织,保证高炉停炉前正常的出铁秩序和降料面期间的渣铁罐安排,根据高炉需要,及时出好渣铁。
(生产科、高炉负责)2、彻底检查风口、冷却壁有无漏水,各阀门是否灵活好用,对破损和怀疑破损的风口套和冷却壁要重点监控,做好记录,出现风口破损要提前安排小修风更换,杜绝漏问题。
(配管负责)3、对炉体跑冒煤气、炉皮、水冷套管根部的开缝情况进行检查确认,提前处理。
(配管)4、加长机械探尺量程。
5、炉顶平台清理整顿,无油污和易燃杂物,杜绝设备漏油。
6、降料面打水系统准备工作:总原则是水量充足,分布均匀,雾化良好,调节灵活(总水量和分区调整)。
(高炉落实)(1)8#高炉目前炉顶打水系统试验最大水量为150t/h,气密箱溢流水量为10~20t/h,总计水量最大为160~170t/h。
检查确认炉顶打水系统的10个打水管及气密箱冷却水溢流系统正常,10个水枪水量均匀畅通,实验核实打水水量,保证打水系统运转正常。
(2)炉顶打水管路必须具备水量调节装置,保证水流量调整灵活可控,并实现在中控室远程操作调整和水量监控。
(自动化部处理)(3)气密性箱冷却水管路串接工业水水源,实现软水和工业水冷却介质切换。
(4)联系水站,确保供水系统正常,高压水供应水压≥1.8MPa,气密箱补水流量满足需求。
7、炉顶打水系统和炉身静压检测点氮气通路通常,降料面期间增大氮气量。
8、料仓腾仓工作由机动科根据检修需要与生产科、高炉协商做安排,提前布置,做好供料方案。
停炉前注意料仓仓位的控制,保证满足高炉上料要求的同时按要求腾空所要求的料仓。
(高炉、生产科、设备动力科负责)9、保证煤气取样管路和设备的正常运转。
高炉降料面期每间隔半小时取一次人工煤气分析,20分钟之出数据。
(化验室)10、降料面正式开始前,重力除尘器放灰,防止含水板结。
11、风口平台区域提前准备好6~8套足够长度的风口打水管,保证降料面期间每个风口位置都可以实现炉外打水。
(配管)12、准备好32套进风短管封堵盲板装置和所需要的石棉绳、铅油等密封用品,钢板厚度8mm。
(作业区)13、风口平台8个方向制作准备好8根打水管,用于炉缸残料打水冷却:打水管使用氧气管,长度6m,前端封死,据前端4米部分,每间隔100mm开孔一个,孔径3~5mm,开孔间错排开,对称分布。
(高炉配管)14、联系能源中心,确保蒸汽氮气等能源介质的供应保证工作,提前做好降料面前期阶段布袋除尘系统对高炉煤气回收的协调工作,预计回收煤气阶段前6个小时炉顶煤气量<600000m3/h,中后期炉顶煤气量<450000m3/h,(高炉煤气量+打水蒸汽量)(生产科)三、停炉前高炉操作调整为保证停炉工作的顺利进行,并为停炉后的炉缸残料清理创造良好工作条件,此次停炉高炉操作按以下步骤调整。
1、停炉前3天,按正常操控标准组织组织生产,全风全氧正常生产,若风量不全、炉温不稳定应及时减轻焦炭负荷。
保炉况稳定顺行、炉缸工作均匀活跃,严禁出现低炉温、炉凉现象,铁水物理热≥1510℃。
2、停炉前1天,调整操作方针:焦丁比≤40kg/tfe,煤比≤100kg/,按风温1100℃、富氧≤8000m3/h, t调整焦炭负荷;可提前吃空生矿,采用全烧结+球团矿炉料结构,矿批85~88t。
炉温碱度控制标准:提炉温降碱度,[Si]0.45~0.60%,R21.15~1.20,铁水物理热≥1510~1520℃,保证渣铁流动性。
3、可提前一天酌情提高铁口角度。
(目前大高炉采用固定角度,一般不再安排此项,小高炉应用较多)4、正式开始降料面前4~5小时,高炉按照[Si]0..55~0.7%,R21.10~1.15核算全停煤负荷和调整熔剂,并在此基础上增加焦比5%变停炉料(焦比+焦丁比540~550kg/t左右)。
5、最终停止上料前,最后加装20吨盖面焦,即进入正式降料面操作。
四、降料面期间操作要求1、降料面期间,每隔半个小时测一次料线(降料面前期使用探尺点测,中后期观察雷达探尺),记录一次顶温、顶压、风压、风量、(风机风量)打水量等操作参数,以及每次爆震的时间,顶压波动情况。
2、主控室安排专人负责打水量调剂工作。
3、煤气取样频次为30分钟取一次,取样后要求20min出化验结果,高炉工长测绘煤气成分变化趋势曲线。
4、降料面期间加强风口巡检,观察风口工作状况,若查出坏风口,加外喷水,尽量不停风,风口平台不断人。
(配管负责)五、降料面期间操控标准5、降料面顶温控制标准:顶温标准300~350℃,瞬时值不得低于250℃或高于400℃,顶温控制主要通过匹配好风量和打水量控制来实现,确保炉顶设备和布袋除尘系统安全,是整个降料面期间的重点核心工作。
6、煤气回收操作:前期回收煤气操作,在保证生产安全的前提下尽可能延长回收煤气时间,减少放散。
7、顶压控制:降料面开始前提前退出TRT,使用高压阀组控制顶压,开始降料面后顶压调节改手动控制操作。
8、风压、风量控制:(1)随着料线加深,透气性增大,总进程是结合顶温控制、爆震现象等因素逐步择机降低风量使用的过程,在降低风量的过程中,同时降顶压,可根据实际情况参考下表进行控制并灵活调整。
注:不同料线状态,风量、风压匹配关系完全不同,本表仅作为调整参考数据(2)降料面初期按全风操作,风量<6000m3/min,料线在炉身上部,风量按5500~5000 m3/min控制,炉身中部,风量按5000~4500 m3/min控制,进入炉腰(全风70%为基准),按风量4500~3500 m3/min控制,切煤气操作后(按炉容送风比1.0为基准调整)风量≤3000m3/min,顶压≤12kpa,减少噪声污染。
风量控制服从顶温爆震状况和煤气回收处理能力。
(3)出于多烧焦炭,减少扒炉量考虑,在料面进入炉缸区之前,应适当加大风量,提高风速多烧中心焦炭,但风量必须服从环保、噪音和安全因素。
9、煤粉控制:根据炉温和停炉负荷料下达情况停止喷煤,提前做好喷煤量估算,停止喷吹后,清空喷吹罐。
10、富氧控制:前期可以富氧,富氧量≤5000m3/h,料线降到炉腰后禁止富氧,氧气手动切断阀关闭,防止煤气温度过高,烧损铜冷却壁。
11、加湿控制:回收煤气前期可加湿平衡理燃,理论燃烧温度小于2300℃,减少风口破损,煤气放散或者料线降到炉腰停止加湿,减少煤气H2含量,手动阀关闭。
12、风温控制:风温控制在1100~800℃之间,根据炉温状况进行调整,总体使用原则是逐步降低风温使用,停止喷煤后,风温<1050℃,料线降到炉腰后风温<900℃,降到炉腹后,风温按800℃控制。
总体风温使用水平不高,热风炉要控制好烧炉,防止风温过高难降。
13、冷却系统控制:(1)炉顶气密箱加强通水同氮冷却,确保气密箱温度<50℃。
(2)保护好冷却壁,料面进入炉身下部区域后,软水系统流量最大,进水温度控制最低,密切关注铜冷却壁温度变化,控制温度点低于130℃,温度高要及时控风。
14、打水和顶温控制:(1)根据顶温调节打水量。
打水要连续进行,尽量早调、少调。
若因特殊情况停止打水,在恢复时,要由小到大逐步开水,防止大量水急剧汽化,引发水蒸汽爆炸事故。
(2)当出现爆震或者增加打水量、顶温仍不能维持在规定围时,应减小风量保证顶温控制在要求之,减小爆震的发生。
15、煤气放散控制标准:(1)当出现以下情况之一时,高炉停止回收煤气。
A、当混合煤气中含H2>12%或O2>0.8%。
爆震频繁,H2含量频繁波动超过10%的时候,要准备切煤气,降低风温和减小风量是降低煤气H2含量的有效措施。
B、料面已经降到炉腰下部和炉腹上部。
可根据探尺和煤气成分综合判定,煤气成分曲线CO2出现明显拐点或H2>CO2时,说明已进入炉腰区域(普遍规律CO2左拐点出现进入炉腰,右拐点出现进入炉腹,左右拐点比较接近进入的是炉腰中部,风量越小,右拐点出现的料线越深)。
C、控制风量通过减风,仍然出现炉顶压力剧烈波动、频繁爆震D、炉皮发生严重跑火冒气现象。
E、布袋除尘系统无法满足高炉回收煤气需求。
(2)开炉顶煤气放散、切煤气前,应先减风到较低水平(风压≤50kpa,,顶压≤15kpa),再进行切煤气操作,防止突发爆震和瞬时炉顶压力骤降引发炉爆震,威胁生产安全。
放散打开后上锁处理,防止关闭,切煤气后重力除尘器放散阀同时打开(3)切煤气完成后,可加风操作,但风量小于3000m3/h,顶压≤12kpa,保证减少噪音和大气排放污染。
开炉顶煤气放散、切煤气前,应先减风到较低水平(风压≤50kpa,,顶压≤15kpa),再进行切煤气操作,防止突发爆震和瞬时炉顶压力骤降引发炉爆震,威胁生产安全。
放散打开后上锁处理,防止关闭,切煤气后重力除尘器放散阀同时打开。
16、出铁控制:(1)降料面前期按正常铁次时间出铁,见风堵口,禁止过喷,降料面中后期,延长铁间隔。
(2)料面降至炉身下部,核算停炉料理论出铁量在炉存留铁量300t后,停止出铁,有利于多烧炉缸焦炭量,减少扒炉工作量。
可以根据降料面进程延后出铁,置换撇渣器存铁,但要留足最后出铁所需铁量及时堵口。
(3)降料面后的炉存铁量按炉腰区域以上矿批和焦批层状下降,炉腰以下全部为焦炭进行计算,炉腰具体分界线的标高,根据实际状况、软融带的高低现场评估确定,一般确定炉腰炉身交界处为宜。
(4)当出现局部风口吹空现象,组织出最后一次铁,双场双铁口出铁,出铁大喷铁口,在铁口喷煤气和渣粒,渣铁基本断流后堵口。
为保证最后一次渣铁出净,在渣铁流变小之后,关闭部分放散提升顶压,可通过半开和调整放风阀开度调整顶压。
17、休风后操作:(1)铁后休风,休风后停止炉顶打水。
(2)炉前组织放碳包。
(3)休风1小时后可以降冷却水压、控水量至全水量的50%,如需停水,安排在停炉72小时以后方可以断水。
有破损的冷却水管必须断水,炉顶打水、蒸汽阀门、气密箱水冷总阀关闭,切断一切可能向炉漏水的水源。
(4)休风后根据计划安排拆除所有的进风吹管,在吹管拆除后,要求所有进风短管封堵盲板,与热风炉系统断开,防止串煤气到炉台。
六、休风后炉缸残料冷却1、炉缸残料打水降温一方面要为炉缸扒炉创造良好温度条件,一方面要保护好炉缸碳素耐材,防止积水浸泡。