中厚板生产 课程设计
30×2100×6000(Q215) 中厚板生产规程设计
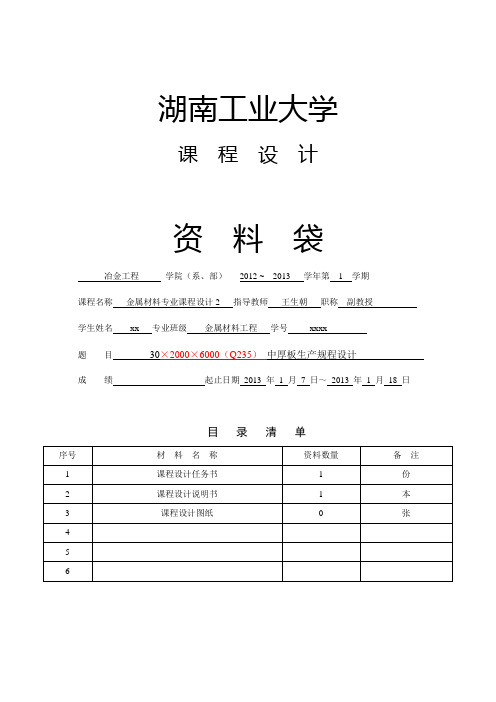
湖南工业大学课程设计资料袋冶金工程学院(系、部)2012 ~ 2013 学年第 1 学期课程名称金属材料专业课程设计2 指导教师王生朝职称副教授学生姓名xx 专业班级金属材料工程学号xxxx题目30×2000×6000(Q235)中厚板生产规程设计成绩起止日期2013 年1 月7 日~2013 年1 月18 日目录清单金属材料专业课程设计2设计说明书30×2000×6000(Q235)中厚板生产规程设计起止日期:2013 年 1 月7 日至2013 年 1 月18 日学生姓名xxx班级金属材料093班学号xxxx成绩指导教师(签字)冶金工程学院2013年1月17 日湖南工业大学课程设计任务书2012 —2013 学年第 1 学期冶金工程学院学院金属材料工程专业金属材料093 班级课程名称:金属材料专业课程设计2设计题目:30×2000×6000(Q235)中厚板生产规程设计完成期限:自2013 年 1 月7 日至2013 年 1 月17 日共两周指导教师(签字):王生朝2013年 1 月7 日系主任(签字):王生朝2013年1 月7 日冶金工程学院课程设计指导教师评阅表冶金工程学院课程设计答辩及最终成绩评定表说明:采用百分制计分,最终评定成绩=答辩评分(20%)+指导教师评分(80%),根据综合分值给出相应等级。
目录1 制定生产工艺 (1)1.1制定生产工艺 (1)1.2制定工艺制度 (1)2 制定压下规程 (1)2.1原料设计 (1)2.1.1原料的质量 (1)2.1.2原料的尺寸 (2)2.2轧制规程的设计 (2)2.2.1坯料的选择 (2)2.2.2道次压下量分配的影响因素 (2)2.2.3道次压下量的分配规律 (3)2.3轧制速度制度 (5)2.3.1轧辊的咬入和抛出转速及轧辊加速度的确定 (5)2.3.2最大轧制转速及最大轧制速度的确定 (5)2.3.3纯轧时间及间隙时间的确定 (6)2.4温度制度的确定 (8)2.5变形制度的确定 (9)2.5.1变形程度的计算 (9)2.5.2平均变形速度 (10)2.5.3变形抗力的计算 (10)2.6轧制力能参数计算 (13)2.6.1轧制压力的计算 (13)2.6.2计算各道传动力矩 (14)典型产品生产规程设计1 制定生产工艺1.1制定生产工艺选择坯料→原料清理→加热→除磷→横轧两道次(使宽度接近成品宽度)→转90°纵轧到底→矫直→冷却→表面检查→切边→定尺→表面尺寸形状检查→力学性能检测→标记→入库→发货。
中厚板课程设计-16Mng中厚板轧制规程的编制

大学课程设计说明书设计题目:16Mng中厚板轧制规程的编制学院:专业班级:学生姓名:指导教师:成绩:2014 年月日1.前言.......................................................................................... 错误!未定义书签。
1.1中厚板产品品种 (3)1.2中厚板用途 (4)1.3 16Mng的特性及用途 (4)2.中厚板生产工艺流程简介 (5)2.1中厚板生产工艺 (5)2.2原料的加热 (6)2.3 除鳞 (6)2.4粗轧 (7)2.5精轧 (7)2.6精整与热处理 (7)3.压下规程设计 (7)3.1选择坯料 (8)3.2坯料尺寸的确定 (9)3.3确定轧制方法 (9)3.4确定轧制道次、压下量及压下率 (10)3.4.1校核咬入能力 (10)3.4.2压下量的分配和压下率 (10)3.5速度制度 (11)3.6温度制度 (13)3.7轧制力计算 (14)3.7.1平均单位压力 (14)3.7.2总轧制力的计算 (15)3.8计算传动力矩 (16)3.8.1轧制力矩的计算 (16)3.8.2附加摩擦力矩的计算 (17)3.8.3 空转力矩的计算 (17)3.8.4动力矩的计算 (18)4.辊型设计计算 (18)4.1辊凸度计算 (19)4.2轧辊的弹性弯曲变形 (19)4.3轧辊的磨损 (21)4.4辊型设计 (21)5 设备校核 (22)5.1 咬入条件的校核 (22)5.2 轧辊强度校核 (23)5.2.1工作辊强度校核 (24)5.2.2 支承辊强度校核 (25)5.2.3 工作辊与支承辊间的接触应力 (27)5.3主电机过载和过热校核 (28)5.3.1 轧机主电机过载校核 (28)5.3.2轧机主电机的发热校核 (29)6.结束语 (30)参考文献 (30)1.前言中厚板带材是机械制造﹑桥梁建设造船和石油化工的容器及管道制造等重要的原材料。
中厚板压下规程课程设计
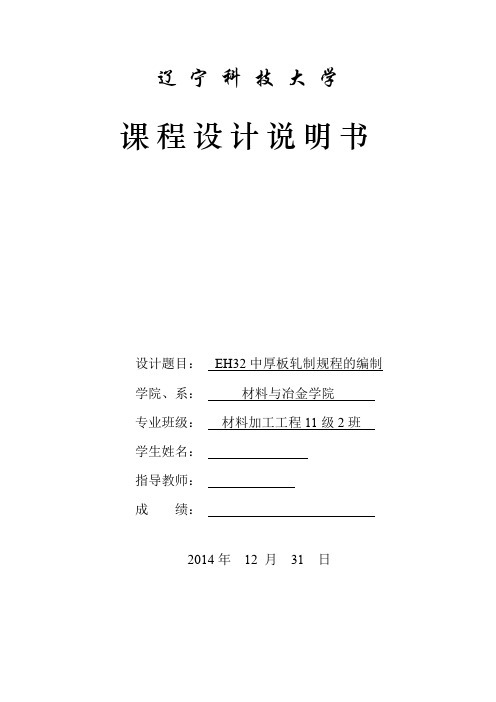
辽宁科技大学课程设计说明书设计题目:EH32中厚板轧制规程的编制学院、系:材料与冶金学院专业班级:材料加工工程11级2班学生姓名:指导教师:成绩:2014年12 月31 日目录1前言 (2)1.1 EH32中厚板产品介绍 (2)1.2 EH32中厚板成分介绍: (2)2中厚板生产工艺流程简介 (2)3. 轧制规程编制 (5)3.1轧制工艺参数设计 (5)3.1.1选择坯料 (5)3.1.2坯料尺寸的确定 (5)3.1.3确定轧制方法 (5)3.1.4确定轧制道次 (6)3.1.5道次压下量的分配 (6)3.1.6速度制度 (8)3.1.7轧制时间 (8)3.1.8温度制度 (9)3.2轧制力的计算 (11)3.2.1平均单位压力 (11)3.2.2总轧制力的计算 (11)3.3计算传动力矩 (12)3.3.1轧制力矩的计算 (12)3.3.2附加摩擦力矩的计算 (12)3.3.3空转力矩的计算 (13)3.3.4动力矩的计算 (13)4辊型设计计算 (15)5设备校核 (18)5.1轧辊强度校核 (18)5.1.1支撑辊强度校核 (19)5.1.2 工作辊强度计算 (19)5.1.3接触应力的计算 (20)5.2主电机功率校核 (21)5.2.1电机过载校核 (21)5.2.2电机的发热校核 (21)6结语 (22)7参考文献 (23)1前言1.1 EH32中厚板产品介绍一般船体结构钢A、B、D、E级是根据钢材冲击温度来区分的,各等级钢的冲击值均相同,不是根据强度等级区分的。
A级钢是在常温下(20℃)所受的冲击力。
B级钢是在0℃下所受的冲击力。
D级钢是在-20℃下所受的冲击力。
E级钢是在-40℃下所受的冲击力。
高强度船体结构钢又可分为AH32 DH32 EH32 AH36 DH36 EH36。
1.2 EH32中厚板成分介绍:EH32化学成分:碳(C)≤0.18锰(Mn)0.90~1.60铝(Al)≥0.015硅(Si)0.10~0.50磷(P)≤0.04硫(S)≤0.04屈服强度σs (MPa)3152中厚板生产工艺流程简介中厚板的生产工艺流程根据每个厂的生产线布置情况、车间内物流的走向以及其主要产品品种和交货状态的不同而具有其各自的特点,但加热、轧制、冷却和精整剪切仍是中厚板生产工艺流程的核心部分,而具体的工艺流程一般可根据成品的交货状态,分为直接轧制交货、热处理交货和抛丸或涂漆交货。
毕业设计(论文)-16MnR_中厚板轧制规程制定

攀枝花学院学生课程设计(论文)题目:16MnR中厚板轧制规程制定学生姓名:学号:200911101052所在院(系):材料工程学院专业:材料成型及控制工程班级: 2011级压力加工班指导教师:肖玄职称:讲师2014年10 月13 日攀枝花学院教务处制攀枝花学院本科学生课程设计任务书目录1 绪论 (5)2中厚板生产工艺 (6)2.2中厚板生产工艺流程的制订 (7)2.3 中厚板生产工艺流程 (7)2.3.1坯料 (7)2.3.1.1坯料的选择 (7)2.3.1.2 铸坯的材质 (8)2.3.1.3 铸坯检查与清理 (8)2.3.2坯料加热 (8)2.3.2.1 加热炉选择 (8)2.3.2.2加热温度 (9)2.3.2.3 加热速度 (9)2.3.2.4 加热时间 (9)2.3.2.5保温时间 (9)2.3.2.6 燃料选择 (10)2.3.3 轧制 (10)2.3.3.1 除鳞 (10)2.3.3.2 粗轧 (10)2.3.3.3 精轧 (11)2.3.4 中厚板轧后冷却 (11)2.3.4.1 冷却方式 (11)2.3.4.2 冷床 (12)2.3.5 精整及热处理 (13)2.3.5.1 热处理 (13)2.3.5.2 矫直 (13)2.3.5.3 翻板、表面检查及修磨 (13)2.3.5.4 划线与剪切 (13)2.3.5.5 钢板的标志与包装 (14)2.3.5.6 钢板的质量检验 (14)3 总结 (15)参考文献 (16)1 绪论中厚板是指厚度4.5-25.0mm的钢板,主要用于制造石油、化工气体分离和气体储运的压力容器和其它类似设备,一般工作压力在常压到320kg/cm2甚至到630kg/cm2,温度在 -20-450°C范围内工作,要求容器钢板除具有一定强度和良好塑性和韧性外,还必须有较好冷弯和焊接性能,如:Q245R 、Q345R、14Cr1MoR、15CrMoR等。
中厚板生产课程设计
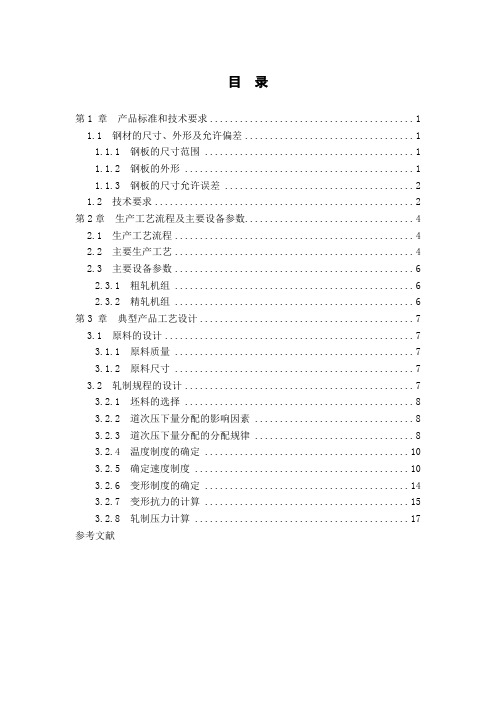
目录第1 章产品标准和技术要求 (1)1.1 钢材的尺寸、外形及允许偏差 (1)1.1.1 钢板的尺寸范围 (1)1.1.2 钢板的外形 (1)1.1.3 钢板的尺寸允许误差 (2)1.2 技术要求 (2)第2章生产工艺流程及主要设备参数 (4)2.1 生产工艺流程 (4)2.2 主要生产工艺 (4)2.3 主要设备参数 (6)2.3.1 粗轧机组 (6)2.3.2 精轧机组 (6)第3 章典型产品工艺设计 (7)3.1 原料的设计 (7)3.1.1 原料质量 (7)3.1.2 原料尺寸 (7)3.2 轧制规程的设计 (7)3.2.1 坯料的选择 (8)3.2.2 道次压下量分配的影响因素 (8)3.2.3 道次压下量分配的分配规律 (8)3.2.4 温度制度的确定 (10)3.2.5 确定速度制度 (10)3.2.6 变形制度的确定 (14)3.2.7 变形抗力的计算 (15)3.2.8 轧制压力计算 (17)参考文献第1 章产品标准和技术要求1.1 钢材的尺寸、外形及允许偏差钢板和钢带的尺寸、外形及允许偏差见国标GBT/709-2006《热轧钢板和钢带的尺寸、外形、重量及允许偏差》如下所示:1.1.1 钢板的尺寸范围钢板公称厚度:4mm~400mm钢板公称宽度:600mm~4800mm钢板公称长度(包括剪切钢板):2000mm~20000mm1.1.2 钢板的外形1.1.2.1 不平度的规定表1.1 剪切钢板的不平度1.1.2.2 镰刀弯的规定表1.2 剪切钢板的镰刀弯1.1.2.3 切斜的规定钢板的切斜应不大于实际宽度的1%1.1.2.4 塔形的规定表1.3 塔形高度1.1.3 钢板的尺寸允许误差1.1.3.1 钢板的厚度允许偏差表1.4 钢板的厚度允许偏差1.1.3.2 钢板的宽度允许偏差表1.5 切边钢板的宽度允许偏差1.1.3.3 钢板的长度允许偏差的规定表1.6 剪切钢板的长度允许偏差1.2 技术要求合金牌号和化学成分可查国标,如碳素结构钢可查GB/T700-2006,低合金结构钢可查GB/T1591,优质碳素结构钢 GB/T 699-1999等另外,技术要求可查找GB 3524-2005《碳素结构钢和低合金结构钢热轧钢带》,GB/T4237-2007《不锈钢热轧钢板和钢带》,GB/T8749-2008《优质碳素结构热轧钢带》等。
年产180万吨厚板车间设计毕业设计

这种轧机有两个值径较小的工作辊和两个直径较大的别离位于工作辊上、下的支承辊。由于较大的支承辊经受轧制压力,减少了工作辊变形,因此这种轧机适于轧制宽度较大且精度要求较高的碳素钢钢板和合金钢钢板。在这种轧机上轧制时,可取得比在三辊劳特式轧机上按宽度散布得更均匀的压下量。这在轧制厚度为4—6毫米的钢板时专门重要。四辊式轧机的工作辊直径比三辊式的小,因此轧制时,轧件作用在轧辊上的压力较小,电能消耗也较少。缺点:利用直流电机,投资费用较高。
1
1.二辊可逆式轧机
二辊可逆式轧机的轧辊直径较大,能增大压下量,以减少轧制道次及轧制间隙时刻,并对原料种类及尺寸的适应性较广。它的要紧缺点是:因为没有支承辊,轧机的刚性较差。换辊比较困难,修磨辊型就不方便,因此轧出钢板的精度和表面质量都较差。可逆式轧机必需采纳带变流设备的直流电动机,投资费用此较高。因此,单机架二辊可逆式中板轧机目前很少应用。个别现存的也只用来轧制较厚的中厚板。
(4)轧制打算的自由性。
PC轧机的缺点: 轧制结构复杂,轴向力大(达到轧制力的8%~10%)将使轴承寿命缩短,使保护工作量加大,并增加了轧制力的测量的滞后性,操作与操纵复杂,投资本钱增加。
另外,有些轧机采纳ORG(在线磨辊)技术,ORG的个砂轮是通过接触旋转中的工作辊来带动旋转,属于非驱动型研磨。在线磨辊机里安装有在线轮廓仪,能够准确测定工作辊的表面形状。ORG技术与PC轧机结合起来,将发挥更大成效。ORG具有操纵板型,板凸度,减少边部减薄与局部高点,提高表面质量,排除工作辊的磨损段差,实现自由轧制,推延换辊时刻,增加轧制量的优势;其缺点是一旦操作保护不妥,ORG设备的故障较多。
生产厚度4mm以下中板时钢板轧制长度要在20m以下因此坯料单重受到很大限制除加热炉炉型受限制外轧制成薄中板的输送也是很大问题辊道辊距为1000mm时钢板塌下到辊道盖板上钢板在辊子上打滑便输送不了
[中厚钢板生产工艺

课时教学计划图1-1 平面布置简图1-板坯二次切割线;2-连续式加热炉;3-高压水除鳞箱;4-精轧机;5-加速冷却装置;6-热矫直机;7-宽冷床;8-特厚板冷床;9-检查修磨台架;10-超声波探伤装置;11-切头剪;12-双边剪和剖分剪;4 工艺技术及装备<1)板坯库及加热炉为实施连铸板坯热送热装工艺,厚板连铸机与宽厚板轧机毗邻火、淬火、回火等热处理工艺.钢板入炉前,先经抛丸处理,除去表面地氧化铁皮.其处理地钢板表面质量好,温度均匀.钢板涂漆线设在涂漆跨内.需涂漆地钢板由成品库上料丸、表面检查和修磨,再经预热、涂漆、烘干、检查和标记处理送入成品库.§2.2中厚钢板生产工艺特殊中厚板与一般中厚板流程地区别是:特殊中厚板流程中有超声波探伤.一、原料选择选择合理地原料种类、尺寸和保证其质量是钢板优质高产地原料地种类用于生产中厚钢板地原料有扁钢锭、初轧板坯、锻压坯、压铸坯和连铸板坯几种.原料地尺寸原料地尺寸即原料地厚度、宽度和长度.原料尺寸地选择原则是:<1)原料地厚度尺寸在保证钢板压缩比地前提下应尽可能小.)原料地宽度尺寸应尽量大,使横轧操作容易.原料地长度尺寸应尽可能接近原料地最大允许长度.)原料地长度应尽可能接近原料地最大允许长度.<受加热炉宽度限制)图2-30 一般中厚板生产流程原料表面缺陷地清理清理方法分热状态下清理和冷状态下清理两种.热状态清理采用火焰清理.冷态清理方法有局部火焰清理铲铲削,砂轮研磨,机床加工,电弧清理等,对缺陷严重部分亦可用切割方法去除.二、加热原料加热地目地:好地塑性和低地变形抗力,良好地组织生产中厚板用地加热炉按其结构分为:连续式加热炉:适用于少品种、大批量生产,加热坯料地重量一般小于30t.室式加热炉:适用于特重、特轻、特厚、特短地板坯,或多品种、少批量及合金钢地坯或锭,生产比较灵活.均热炉:均热炉用于由钢锭轧制特厚钢板加热制度:确定加热温度、加热速度、加热时间、炉温制度保证加热质量,防止加热缺陷.课堂小结]。
中厚板生产课程设计指导书

目录1 产品标准和技术要求1.1.1钢材的尺寸、外形及允许偏差钢板和钢带的尺寸、外形及允许偏差见国标GBT/709-2006《热轧钢板和钢带的尺寸、外形、重量及允许偏差》(国标可从网上下载,下同)。
1.1.2技术要求合金牌号和化学成分可查国标,如碳素结构钢可查GB/T700-2006,低合金结构钢可查GB/T1591,优质碳素结构钢 GB/T 699-1999等另外,技术要求可查找GB 3524-2005《碳素结构钢和低合金结构钢热轧钢带》,GB/T4237-2007《不锈钢热轧钢板和钢带》,GB/T8749-2008《优质碳素结构热轧钢带》等。
(1)钢的牌号、化学成分和力学性能见表1-6。
2 生产工艺流程及主要设备参数2.1生产工艺流程根据车间设备条件及原料和成品的尺寸,生产工艺过程一般如下:原料的加热→除鳞→轧制(粗轧、精轧)→矫直→冷却→划线→剪切→检查→清理→打印→包装。
板坯的轧制有粗轧和精轧之分,但粗轧与精轧之间无明显的划分界限。
在单机架轧机上一般前期道次为粗轧,后期道次为精轧;对双机架轧机通常将第一架称为粗轧机,第二架称为精轧机。
粗轧阶段主要是控制宽度和延伸轧件。
精轧阶段主要使轧件继续延伸同时进行板形、厚度、性能、表面质量等控制。
精轧时温度低、轧制压力大,因此压下量不宜过大。
中厚板轧后精整主要包括矫直、冷却、划线、剪切、检查及清理缺陷,必要时还要进行热处理及酸洗等,这些工序多布置在精整作业线上,由辊道及移送机纵横运送钢板进行作业,且机械化自动化水平较高。
2.2 主要生产工艺(1)加热板坯加热目的:中厚板加热目的是提高钢的塑性,降低变形抗力,利于轧制;生成表面氧化铁皮,去除表面缺陷;加热到足够高的温度,使轧制过程在奥氏体化温度区域内完成;在可能的下并可以溶解在后阶段析出的氮化物和碳化物。
一般厚板加热炉的型式有两种:连续式和半连续式。
比较而言,连续式加热炉的产量高、热效率高,装入,抽出方便间歇式加热炉产量一般在10~20t/h,热效率也低。
- 1、下载文档前请自行甄别文档内容的完整性,平台不提供额外的编辑、内容补充、找答案等附加服务。
- 2、"仅部分预览"的文档,不可在线预览部分如存在完整性等问题,可反馈申请退款(可完整预览的文档不适用该条件!)。
- 3、如文档侵犯您的权益,请联系客服反馈,我们会尽快为您处理(人工客服工作时间:9:00-18:30)。
第一章制定生产工艺及工艺制度1.1制定生产工艺及工艺制度1.1.1制定生产工艺:选择坯料→原料清理→加热→除鳞→纵轧二道(使宽度接近成品宽度)→转90°横轧到底→矫直→冷却→表面检查→切边→定尺→表面尺寸形状检查→力学性能试验→标记→入库→发货。
1.1.2制定工艺制度:在保证压缩比的条件下,坯料尺寸尽量小,加热时出炉温度应在1120-1300℃,温度不要过高,以免发生过热或过烧现象;用高压水去除表面的氧化铁皮;矫直时选用辊式矫直机矫直,开始冷却温度一般要尽量接近纵轧温度,轧后快冷到相变温度以下,冷却速度大多选用5-10°或稍高一些。
切边用圆盘式剪切机进行纵剪,然后用飞剪定尺。
第二章选择坯料设计中厚板产品牌号:12CrNi3A,产品规格:h×b×l=13×1900×12000。
按厚度分:我国分类方法如下:0.001—0.2mm箔材,0.2—4mm薄板,4—20mm中板,20—60mm厚板,60—500mm 特厚板,则所设计的产品为中厚板。
因为连铸坯更加节能,组织和性能好,成材率高;主要用于生产厚度小于80mm中厚板,则产品所选的坯料用连铸坯。
根据所设计的产品的尺寸h×b×l=13×1900×12000,设计坯料的尺寸。
2.1坯料尺寸的确定2.1.1坯料厚度的确定:根据经验,我国压缩比一般在6~8以上,本设计取8,由成品厚度h=13mm,知H=8h=104mm。
2.1.2坯料长度的确定由成品(b+△b)←坯长L,取展宽为700mm,则L=(1900+200)-700=1400mm2.1.3坯料宽度的确定金属烧损系数一般为1%,切头尾取△L=100mm,切边△b=100mm,由体积不变定律可得:99%×H×B×L=(l+2×100)×(b+2×100)×13带入数据解得:B=2310.6mm 。
取B=2310mm,再次校核K=97.26%。
所以最终得到坯料尺寸为:H×B×L=104×2310×1400mm。
第三章变形量分配3.1轧制方法的确定3.2道次压下量的确定坯料尺寸:H×B×L=104×2310×1400mm,则总的压下量为104–13=89mm。
根据经验值选取轧制道次n=12,制定压下规程。
由于开始轧制时受咬入能力限制,所以在轧制前设计一个除鳞箱,保证咬入能力较好,并选取咬入条件较好的经验方法。
道次压下量与道次关系如图1所示。
由图1所示,各道次的压下量逐渐减小,同时幅度也在逐渐减小,所以粗轧的压下量较大,而精轧的压下量较小。
设定总轧制道次为十二道次,粗轧为七道次(选取二辊可逆轧机),精轧为后五道次(选取四辊可逆轧机)。
制定压下规程如表1。
表1第四章变形工具的设计4.1二辊可逆轧机轧辊的确定初轧机轧辊受力较大且有冲击负荷,应有足够的强度,而辊面硬度可放在第二位,含Cr、Ni、Mo等合金的的铸钢轧辊使用于轧制合金钢,所以粗轧选用铸钢轧辊轧制合金钢。
4.1.1辊身长度L由L=bmax+a bmax=2100mm 当b=1000-2500mm a=150-200mm 取a=200mm,所以L=2100+200=2300mm。
4.1.2辊径尺寸中厚板轧机L/D=2.2-2.8取L/D=2.5得D=920mm 取920mm。
4.1.3辊颈尺寸查表3-5取d/D=0.75(轧钢机械邹家祥主编) 得d=690m取d=690mm,辊颈长度l 取d/l=1得l=690mm。
4.1.4辊头设计因为对于中厚板轧机来说轧辊调整行程比较大,倾角在8˚-12˚间所以应选择万向辊头。
各部分的尺寸关系如下Dmin=Dmax-Dmax×重车率中厚板轧机最大重车率5%-8% 取5% Dmin=920-920×5%=874mm D1=Dmin-(5-15mm) 取D1= Dmin-9=865 mm;S=(0.25-0.28)D1取S=0.26D1=224.9 mm;a=(0.5-0.6) D1取a=0.5 D1=432.5 mm;b=(0.15-0.2) D1取 b=0.18 D1=155.7mm;c=b=155.7mm。
4.1.5辊颈与辊身的过度圆角r由r/D=0.1—0.12取0.11得r=0.11×920=101.2mm,图2轧辊示意图4.1.7校核咬入条件咬入角一般α=15~25度,取α=20︒,∆h max =(1-cos20︒)×D=(1-cos20︒)×920=55.48mm,粗轧各道次压下量∆h最大为20mm,满足咬入。
4.2四辊可逆轧机轧辊的确定精轧选用四辊可逆轧机,热轧机工作辊选择轧辊材料时以辊面强度为主多采用铸铁轧辊,而支承辊在工作中主要承受轧制力,且直径较大,要着重考虑强度和轧辊淬透性,多选用含Cr合金锻钢,因此四辊可逆轧机的工作辊选用铸铁轧辊,支承辊选用Cr合金锻钢。
四辊的尺寸设计与二辊相同,其中支承辊不传递扭矩,辊头不需设计。
4.2.1支承辊设计4..2. 1.1辊身长度设计和二辊一样 L=2300 mm。
4.2.1.2辊径D2查表3-3 (轧钢机械邹家祥主编)取L/D2=2.0得D2=1150mm。
4.2.1.3辊颈尺寸取d2=0.75 D d2=0.75×1150=862.5mm 取d2=870mm。
4.2.1.4辊颈长度 l2l2 /d2=1.0得l2=870mm。
4.2.2工作辊设计4.2.2.1辊身设计同前 L=2300mm。
4.2.2.2辊径尺寸据经验当轧件较厚时由于要求较大工作辊直径,取D2/D1较小值由表3-3得(轧钢机械邹家祥主编) 取D2/D1=1.6得D1=718.75mm取D1=720mm。
4.2.2.3辊颈尺寸取d1/D1=0.65 d1=0.65×720=468mm 取d1=470 ,l1/d1=1得l1=470mm。
4.2.2.4辊颈与辊身的过度圆角r1取r1=0.1D1=72mm。
4.2.2.5辊头设计选择万向辊头选择原因同二辊。
各部分的尺寸关系如下所示:Dmin=Dmax-Dmax×重车率中厚板轧机最大重车率5%-8% 取5% Dmin=720-720×5%=684mm D1=Dmin-(5-15mm) 取D1= Dmin-9=675mm;S=(0.25-0.28)D1取S=0.26D1=0.26×675=175.5mm;a=(0.5-0.6) D1取a=0.5 D1=0.5×675=337.5mm;b=(0.15-0.2) D1取 b=0.18 D1=0.18×675=121.5mm;c=b=121.5mm。
4.2.2.6辊颈与辊身的过度圆角r2取r2=0.1D2=0.1×675=67.5mm。
4.2.3校核咬入咬入角一般α=15-25︒,取α=20︒,∆hmax=(1-cos20︒)×=(1-cos20︒)×675=45.43mm,精轧各道次压下量△h最大为1mm,满足咬入。
表2 轧机尺寸表第五章 轧制力的计算5.1 确定速度和时间制度因为轧件较长,各道次均选用梯形图,梯形图如图3所示。
根据经验资料取加速度a=40rpm/s ,减速度b=60rpm/s 。
前两道次为二辊轧制,受咬入能力限制,取咬入速度n 1=10rpm ,稳定轧制速度n 2=30rpm ,抛出速度n 3=20rpm 。
由公式:加速轧制平均速度V 11 =πD (n 1+ n 2)/120=π×920×(10+30)/120=962.93mm /s , 加速轧制时间 t 11 =( n 2- n 1)/a ,t 11 =(30-10)/40=0.5s ;轧辊速度V 12=πDn/60,V 12=π×920×30/60=1444.4mm/s ;稳定轧制时间t 12=⎪⎪⎭⎫ ⎝⎛++-⨯⨯⨯1208012405602321222n n n n D n L π=0.50s ; 减速轧制平均速度V 13 =πD (n 2+ n 3)/120,V 13 =π×920(30+20)/120=1203.67mm/s ;减速轧制时间t 13 =(n 2- n 3)/b ,t 13 =(30-20)/60=0.17s 。
其中l ——该道次轧后轧件长度,其他各道次轧制速度与轧制时间见表3。
中间五道次,随着轧制进行到一定程度,设咬入速度n 1=20rpm ,稳定轧制速度n 2=40rpm ,抛出速度n 3=20rpm ,算法同上见表3 由于第八道次开始为精轧,改为四辊轧制,以工作辊的直径计算D=720mm ,设咬入速度n 1=60rpm ,稳定轧制速度n 2=60rpm ,抛出速度n 3=30rpm 。
稳速轧制速度v 1=πDn/60=π×720×60/60=2260.8 mm/s ;减速轧制平均速度v 2=πD (n 2+ n 3)/120=π×720×(60+30)/120=1507.2 mm/s ;减速轧制时间t 2=(n 2- n 3/b=(60-30)/60=0.5s ;稳速轧制时间t 1=⎪⎪⎭⎫ ⎝⎛++-⨯⨯⨯1208012405602321222n n n n D n L π=4.05s 各道次间的间隙时间t j ,根据经验,轧机往返轧制,一般:L ≤3.5m ,不用推床定心,t j =2.5s ;L ≤8m ,用推床定心,t j =6s ;L >8m ,用推床定心,tj=4s 。
其他各道次轧制速度和时间见表3。
表3 轧制速度时间表道次 速度制度 轧制速度/rpm轧制时间/S 纯轧时间tz/S 间隙时间tj/S 合计/S 加速轧制时间/s 轧件长度/l 减速轧制时间/s总时间/s 咬入/n 1 稳轧/n 2 抛出/n 3稳速 负减110 30 20 1.12 0 1.79 15+2.5 19.29 0.5 2000 0.17 74.00 2 10 30 20 2.27 0 2.93 2.5 5.43 0.5 3439.5 0.17 3 20 40 20 1.92 0 2.76 6 8.76 0.5 4265 0.344 20 40 20 2.41 0 3.24 6 9.24 0.5 5077.3 0.34 5 20 40 20 2.91 0.33 4.086 10.08 0.5 5923.6 0.34 6 20 40 20 3.62 0.33 4.78 6 10.78 0.5 7108.3 0.347 20 40 20 4.27 0.33 5.44 4 9.44 0.5 8201.8 0.34 8 60 60 30 3.67 0.33 4.50 4 8.50 0 8885.3 0.546.04 9 60 60 30 4.03 0.5 5.03 4 9.03 0 9693.1 0.5 1060 60 30 4.480.5 5.48 4 9.480 10662.0.54116060305.010.56.01410.01011847.10.5126060305.690.56.6906.690133280.5由表3知粗轧时间比精轧时间长,可以防止出现堆钢现象,符合生产要求。