提高铰孔质量的方法
车削加工中钻孔、镗孔和铰孔的质量问题及解决方案

车削加工中钻孔、镗孔和铰孔的质量问题及解决方案摘要:套类零件的车削比轴类零件的车削难度要高,在套类零件车削的过程中,我们会碰到很多零件质量的问题,比如钻孔时孔径偏大或歪斜,镗孔时孔的粗糙度不够理想,铰孔时精度达不到要求,本篇文章介绍钻孔、镗孔及铰孔的质量问题进行分析,从而制定出改进与提高套类零件质量的具体措施。
通过理论教学,使学生掌握套类零件在车削加工中钻孔、镗孔及铰孔的质量问题,为解决问题提供积极方案,有一定的实践意义。
关键词:车削特点问题分析解决方案套类零件车削时,切削情况不能用视力来观察;孔径大小限制刀杆的截面,特别是加工孔径小、长度长的孔,刀杆刚性不足;切屑排出不易,测量套类零件,尤其是测量小孔更加困难。
一、钻孔问题1.孔钻偏歪:问题分析:(1)工件端面没有车平或者有凸台;(2)车平后第二次装夹时工件端面与轴线不垂直;(3)车床装夹钻头的尾座磨损中心降低或者与主轴轴线产生偏移;(4)钻头刚度不好,初钻时手动进给量过大;(5)钢材质量不好,工件内部有硬块。
解决方案:(1)钻孔前必须先车平端面,不能留有中心余头;(2)第二次装夹时校正工件;(3)修配调整车床尾座中心高度并与主轴的同轴;(4)选用较短的钻头或先用中心钻钻中心孔定位导向,初钻时宜采用高速小走刀,或用档铁支顶防止钻头摆动;(5)降低主轴转速,减小进给量;问题2.钻孔直径偏大超差问题分析:(1)由于粗心大意把钻头直径选错,或者选用的钻头过大余量太小;(2)钻头刃磨时切削刃一边长一边短不对称;(3)钻头在钻削时摆动。
解决方案(1)看清图纸,选取的钻头直径需作检查,选用小一点钻头,加大钻削余量。
(2)刃磨钻头必须使切削刃对称,横刃要通过轴心线;(3)初钻时可用档铁支顶钻头头部,防止摆动,并要保证钻头锥柄的配合良好。
问题3.钻孔后孔壁粗糙问题分析:(1)钻头使用过久磨损不锋利;(2)手动进给量过大或不均匀;(3)切削液供应不足或者性能差;(4)排屑不畅,切屑堵塞了螺旋槽;解决方案(1)刃磨钻头,保持钻头锋利;(2)提高钻孔技能,手动进给均匀;(3)随时注意切削液的浇注情况,保持切削液通畅;(4)钻头经常退出到孔外,清除切屑,保持螺旋槽排屑通畅。
铰孔的质量问题及其解决办法

铰孔的质量问题及其解决办法一、背景铰孔广泛应用于各种机械设备中,承担着连接和转动的重要作用。
铰孔的质量问题直接影响整个机械设备的安全性和稳定性。
本文将讨论铰孔常见的质量问题以及解决办法。
二、铰孔常见的质量问题1. 铰孔偏斜铰孔偏斜是指铰孔的中心轴线与设计中心轴线偏离一定的角度。
铰孔偏斜会导致连接件不能正常安装,或者在运行过程中产生振动和噪音等问题。
偏斜的原因铰孔偏斜的原因主要有以下几个方面:1.铰孔施工过程中操作不当。
2.材料强度不够,无法耐受加工过程的应力。
3.设计和制造时的误差。
排除偏斜的方法1.对铰孔进行重复测量,去除误差。
2.优化设计和加工过程。
2. 铰孔尺寸不准铰孔尺寸不准是指铰孔的直径或深度与设计标准不符合。
铰孔尺寸不准可能会使连接件连接时无法安全地嵌入铰孔中,或在连接过程中被卡住,同时还会影响连接件的旋转轨迹。
精度偏差的来源:1.设计不合理或制造过程中的误差。
2.制造设备老化。
3.制造人员技能缺失导致加工精度不高。
解决铰孔尺寸不准的方法:1.通过良好的制造流程和检验来降低尺寸的误差。
2.使用精密检测设备来检查每个铰孔的尺寸和位置。
3. 铰孔表面质量差铰孔表面质量差分为以下两个方面:表面粗糙表面粗糙是铰孔表面的不规则数值。
粗糙表面可能会导致连接件卡住或与铰孔之间产生过多的摩擦力。
表面损伤铰孔表面损伤是指铰孔表面出现划痕或碎壳等现象,可能导致连接件连接不良或摩擦增加。
原因表面粗糙和表面损伤的原因可能是:1.设计不合理或制造工艺错误。
2.制造设备老化。
3.制造人员技能缺失导致加工精度不高。
排除损伤与粗糙的方法1.使用研磨设备将表面粗糙的铰孔表面磨光。
2.合理使用浓缩洁净剂清洗饱和的水泥混凝土表面,保证铰孔的表面水准。
三、铰孔质量问题的解决办法铰孔质量问题的解决办法包括:1. 设计合理化通过优化设计来控制铰孔质量。
合理的设计不仅可以降低生产成本,还可以减少生产过程中的误差。
2. 制造工艺的改进通过改进制造工艺来控制铰孔的质量。
铰孔加工中的工艺参数
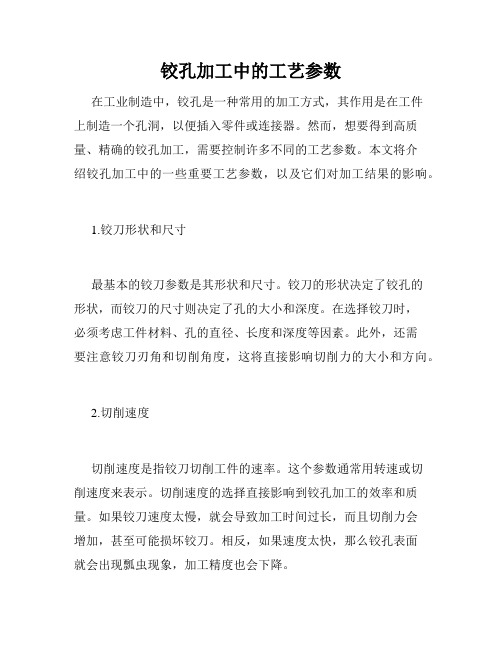
铰孔加工中的工艺参数在工业制造中,铰孔是一种常用的加工方式,其作用是在工件上制造一个孔洞,以便插入零件或连接器。
然而,想要得到高质量、精确的铰孔加工,需要控制许多不同的工艺参数。
本文将介绍铰孔加工中的一些重要工艺参数,以及它们对加工结果的影响。
1.铰刀形状和尺寸最基本的铰刀参数是其形状和尺寸。
铰刀的形状决定了铰孔的形状,而铰刀的尺寸则决定了孔的大小和深度。
在选择铰刀时,必须考虑工件材料、孔的直径、长度和深度等因素。
此外,还需要注意铰刀刃角和切削角度,这将直接影响切削力的大小和方向。
2.切削速度切削速度是指铰刀切削工件的速率。
这个参数通常用转速或切削速度来表示。
切削速度的选择直接影响到铰孔加工的效率和质量。
如果铰刀速度太慢,就会导致加工时间过长,而且切削力会增加,甚至可能损坏铰刀。
相反,如果速度太快,那么铰孔表面就会出现瓢虫现象,加工精度也会下降。
3.进给速度进给速度决定了铰刀在加工过程中每分钟进给的距离。
进给速度与切削速度一样重要,它对加工质量和效率都有影响。
如果进给速度太低,就会导致加工过程中铰孔表面不平滑,甚至出现切削刃痕。
另一方面,如果进给速度过高,则会导致铰刀磨损加速,加工过程中会产生过多的热量,甚至会损坏工件。
4.铰孔深度铰孔深度是铰孔加工的另一个重要参数。
在选择铰刀时,需要根据加工要求确定所需的孔深度,并确保铰孔的深度符合工程要求。
如果铰孔深度过浅,就会导致安装的零件不牢固,而深度过深则会加大工件成本和加工难度。
5.预冲长度预冲长度是指在实际切削铰孔之前,铰刀先在工件上移动的长度。
预冲长度的主要作用是使铰孔与工件表面完全接触,这有利于减少切削刃痕和杂散毛刺等不良现象。
预冲长度的选择应当依据工件材料、孔的直径和深度来确定,并参考铰刀的切削特性和工艺细节。
6.冷却液在铰孔加工过程中,冷却液的选择和使用也是至关重要的工艺参数。
冷却液通过冷却切削区域,降低加工温度,减少摩擦和磨损,并清洗切屑和切屑。
提高铰孔质量的方法

2012年第28期(总第43期)科技视界Science &Technology VisionSCIENCE &TECHNOLOGY VISION科技视界(上接第204页)4结论由表1可知,预试验阶段(16:56~17:26)30min 内管道无漏水、损坏现象,主试验阶段(17:26~17:41)15min 内压力下降0.015MPa,小于规范(GB 50268-2008)规定的允许压力降值0.03MPa,工作压力阶段(18:02~18:32)30min 内管道无漏水、损坏现象,整个加压过程中后背及支墩均无明显异常,依据《给水排水管道工程施工及验收规范》(GB 50268-2008),海棠路管段(K7+224~K7+900)水压试验合格,通过此次试验提出如下建议:1)不宜将水压表安装在进水支管上,以免被高压水流冲坏;2)加压前必须沿途检查并确保管网上排泥阀等配件关死;3)每级加压不宜大于0.1MPa,持压时间不宜少于2min,不能持压时查找漏水点;4)法兰接口位置在加压过程中容易漏水,试验前不宜填埋,漏水后不必整体泄压,可将螺栓拧紧至止水继续试压。
[责任编辑:曹明明]铰孔是利用铰刀对已经用麻花钻头加工过的孔再进行精加工的一道工序。
可加工圆柱形孔(用圆柱铰刀),也可加工圆锥形孔(用圆锥铰刀)由于铰刀的刀刃数量多(6~8个)导向性好,尺寸精度高及刚性好,可达到2~4级精度和▽6~▽9光洁度。
提高铰孔质量须注意以下几点:1铰削用量选择1.1铰削余量(直径余量)是否合适,对铰出孔的表面粗糙度和精度影响很大铰孔余量太大孔铰不光,铰刀负荷过大容易磨损会使刀刃崩碎;铰孔余量太小,不能去掉上道工序留下的刀痕,也达不到要求的表面粗糙度。
铰刀直径小于6mm,铰削余量应在0.05~0.1mm;铰刀直径大于6~18mm,一次铰0.1~0.2mm,二次铰精铰0.1~0.15mm;铰刀直径大于18~30mm,一次铰0.2~0.3mm,二次精铰0.1~0.15mm;铰刀直径大于30~50mm,一次铰0.3~0.4mm,二次精铰0.15~0.25mm。
铰刀铰孔方法【技巧】

在机械制造加工过程常常需要钻孔后铰孔,铰孔要求精度高,铰孔质量直接影响定位孔质量,如何保证孔的精度,铰孔是非常关键的一道工序。
那么铰刀铰孔的方法有哪些呢,下面小编带领大家一同了解一下。
一、铰孔简介1、铰孔是对已经粗加工的孔进行精加工的一种方法。
2、主要目的:纠正上一道工序残留的变形、刀痕,提高孔的精度,多用于紧配螺栓装配前对螺栓孔的修整。
3、铰孔后的精度一般应该达到IT9~IT7级,不应该低于车床加工后的精度。
4、铰刀的种类:手用和机用。
机用较少使用,船厂多数使用手用铰刀,包括:整体式铰刀、手用可调式圆柱铰刀、整体式圆锥铰刀。
目前8200HP轴系、舵系安装中多使用的为手用可调式圆柱铰刀。
二、铰孔时余量的选择1、铰孔时应考虑孔的直径的大小、材料软硬、尺寸精度要求、表面粗糙度、铰刀类型。
2、铰削余量太大,铰孔不光,铰刀磨损很快。
铰削余量太小,无法达到铰孔目的,影响铰孔质量。
3、余量选择孔径小于5mm,余量10到20丝;孔径5到20mm,余量20到30丝;孔径21到32mm,余量30丝;33到50mm,余量半毫米;大于50的孔径,大多留有1毫米以上余量。
像8200HP的齿轮箱底座孔的铰配中,钻孔后的铰配余量在半毫米。
三、铰孔时需要用到切削液1、切削液目的:清除切屑和降低温度,提高孔的光洁度。
2、钢质材料:一般的乳化液;铰孔要求较高时可用机油或液压油。
3、铸铁材料:不用。
煤油可能会引起孔径缩小。
4、铜:一般乳化液稍微稀释。
5、铝:煤油。
四、铰孔具体操作1、准备:(1)孔径测量:卡尺测量孔径,根据铰削余量与精度要求选择合适尺寸的铰刀,一般选用可调式铰刀。
(2)工具:铰刀、手电、破布、扳手(用于转动铰刀或调节铰刀进给量,并根据铰刀后柄合理选择)、切削液、毛刷。
也可以在铰孔前根据所铰孔的位置及立体空间,自行制作扳手,方便操作便于保证精度。
2、方法:(1)调节铰刀:刀体前端靠近刀头部位螺母松开,调节刀体后端朝向刀柄位置螺母,增大或减小进给量。
铰孔加工的质量分析与控制(下)

刀 的垂直 方 向有一个 正确 的视觉 和标 志 。对 于薄壁 稳定 。饺 削连续 ,进 刀量 比较均 匀 ,这些 都有利 于
零 件 的夹 持不要 用力 过大 ,以免将孔 夹扁 ,在 饺孔 提 高铰孔 质量 ,也 是 机动饺 孔应用 比较 普遍 的主要 后 产生 圆度 误 差。 原 因 。机 动饺孔虽 然有 很 多优点 ,但也 存在 一些 问
铰 削加 工。
不大 于 00r .3 m,当最 大 钻 孔 直 径 大 于等 于 2n a 5m ̄
( )注 意变换饺 刀每次 停歌 的位 置 ,以消除饺 时 ,在距 离主轴端 部 30m 处不 大于 0 0 r ̄ 6 0r 5 ቤተ መጻሕፍቲ ባይዱ m 刀常在 同一处停 歌所 造成 的振痕 。 ( )装 夹 工件时 ,要保 证 被饺孔 的 中心线垂 直 2
分全 部出头 ,以免将孔 的下 端划 伤。另外 ,当受 到
工件 装夹或工 件结 构 的限制 时 ,不允许从 孔 的下 面 手工饺 孔时 ,饺刀 受加工孔 的引导 ,在手 的扳 取 出饺 刀 。如果 铰刀 的校准 部分 全部露 出再从 孔 的 动 下进行 断续铰 削 ,其 回转 中心不象 机 铰那样 受到 上方 退 出饺 刀 ,就会将 已加工孔 的表 面刮 伤 ,降低 机床 或其 他工具 的控制 ,但是 由于通 过人 手直 接扳 孔 的精 度 和提高 表面粗 糙度 。 动 铰刀 ,处 于 自由状态 ,稍有 不慎 ,饺刀 就会 左右 ( )铰刀褪 出 时不 能 反转 。因 为铰 刀 有 后角 , 9 摇摆 ,将孔 口扩 大 。同时 ,铰刀 尚需 作周期 性 的停 反转会 使切 屑塞 在铰 刀齿后 砸和孔 壁之 间将 孔壁划 歌 ,这样 在加工 表 面时就会产 生振 痕 ,影响加 工孔 伤 ,同时饺 刀也 容易磨 损 。 的表面粗糙 度 。 因此 ,我们必 须严 格遵 守手 工铰孔 工 艺规程 ,从 而保 证 手工铰孔 的质量 。 2 机 动铰 孔 的方法 夏注 意事 壤 . 当饺孔 的批量 较大且 条 件允 许时 ,应尽量 采 用 ( )工件 装夹要 正 。使操 作者在 铰孔 时 ,对铰 机 动饺孔 。机动 饺孔效 率高 ,饺 刀 的回转 中心 比较 1
铰孔质量的判别及其解决措施

铰孔质量的判别及其解决措施铰孔是半精加工基础上进行的一种精加工。
一般铰孔的尺寸公差等级可达IT8~IT7,表面粗糙度R。
值可达~。
在实际加工中,常见的铰孔质量问题有表面粗糙度和尺寸精度差,孔口呈喇叭状等。
现分析其产生原因和改进方法。
1 表面粗糙度差的原因及其对策铰削速度过大铰削用量各要素对铰孔的表面粗糙度均有影响,其中以铰削速度影响最大,如用高速钢铰刀铰孔,要获得较好的粗糙度µ;m,对中碳钢工件来说,铰削速度不应超过5m/min,因为此时不易产生积屑瘤,且速度也不高;而铰削铸铁时,因切屑断为粒状,不会形成积屑瘤,故速度可以提高到8~10m/min。
如果采用硬质合金铰刀,铰削速度可提高到90~130m/min,但应修整铰刀的某些角度,以避免出现打刀现象。
铰削余量不适当,进给量过大一般铰削余量为~,对于较大直径的孔,余量不能大于,否则表面粗糙度很差。
故余量过大时可采取粗铰和精铰分开,以保证技术要求。
余量过小,不能正常切削也会使表面粗糙度差。
铰孔的粗糙度Ra值随进给量的增加而增大,但进给量过小时,会导致径向摩擦力的增大,引起铰刀颤动,使孔的表面变粗糙。
所以,如用标准高速钢铰刀加工钢件,要得到表面粗糙度µ;m,则进给量不能超过r,对于铸铁件,可增加至r。
铰刀刀刃不锋利,刃带粗糙一般标准铰刀均未经研磨,影响铰孔的表面粗糙度,因此必须对新铰刀进行研磨。
研磨时要注意铰刀的切削部分与校准部分的交界处,因为内孔最后在这里成形,刀具的粗糙度也在该处被反映到铰孔的内壁。
所以研磨铰刀时,应特别注意用油石将该处轻轻地仔细研磨、抛光,使切削部分与校准部分的交接处圆滑过渡。
经研磨的铰刀,切削刃后刀面刃带粗糙度得到改善,切削部分与校准部分交界处的粗糙度也得到改善,实际上是改善了铰刀本身的粗糙度,故有利于改善铰孔的表面粗糙度。
铰孔时未使用润滑液或使用不当的润滑液铰孔时未用润滑液,则铰刀工作部分的后刀面与孔壁会发生干摩擦,使孔的表面粗糙度差。
钳工铰刀铰孔的方法有哪些
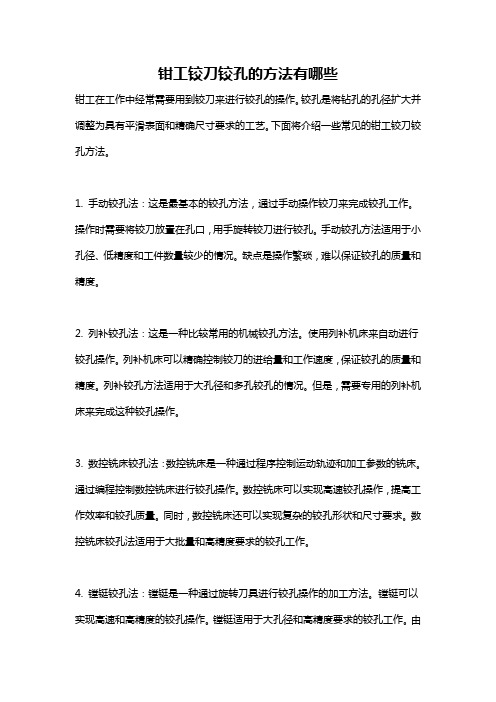
钳工铰刀铰孔的方法有哪些钳工在工作中经常需要用到铰刀来进行铰孔的操作。
铰孔是将钻孔的孔径扩大并调整为具有平滑表面和精确尺寸要求的工艺。
下面将介绍一些常见的钳工铰刀铰孔方法。
1. 手动铰孔法:这是最基本的铰孔方法,通过手动操作铰刀来完成铰孔工作。
操作时需要将铰刀放置在孔口,用手旋转铰刀进行铰孔。
手动铰孔方法适用于小孔径、低精度和工件数量较少的情况。
缺点是操作繁琐,难以保证铰孔的质量和精度。
2. 列补铰孔法:这是一种比较常用的机械铰孔方法。
使用列补机床来自动进行铰孔操作。
列补机床可以精确控制铰刀的进给量和工作速度,保证铰孔的质量和精度。
列补铰孔方法适用于大孔径和多孔铰孔的情况。
但是,需要专用的列补机床来完成这种铰孔操作。
3. 数控铣床铰孔法:数控铣床是一种通过程序控制运动轨迹和加工参数的铣床。
通过编程控制数控铣床进行铰孔操作。
数控铣床可以实现高速铰孔操作,提高工作效率和铰孔质量。
同时,数控铣床还可以实现复杂的铰孔形状和尺寸要求。
数控铣床铰孔法适用于大批量和高精度要求的铰孔工作。
4. 镗铤铰孔法:镗铤是一种通过旋转刀具进行铰孔操作的加工方法。
镗铤可以实现高速和高精度的铰孔操作。
镗铤适用于大孔径和高精度要求的铰孔工作。
由于镗铤操作比较复杂,需要相应的设备和技术支持,因此一般用于专业铰孔加工。
5. 铰孔刀铰孔法:铰孔刀是一种专门用于铰孔操作的刀具。
铰孔刀一般由多刃刀片组成,可以实现高速和高精度的铰孔操作。
铰孔刀适用于各种孔径和尺寸要求的铰孔工作。
同时,铰孔刀还可以实现不同形状和角度的铰孔加工。
6. 内外复合铰孔法:内外复合铰孔是一种通过内外两个铰孔刀进行铰孔操作的加工方法。
通过内外复合铰孔可以实现同时铰削内外两侧的铰孔加工,提高工作效率和铰孔质量。
内外复合铰孔法适用于需要同时加工内外铰孔的工件。
7. 其他特殊铰孔法:还有一些特殊铰孔方法,如刀座铰孔法、补偿铰孔法、动力铰孔法等。
这些方法一般用于特殊的铰孔工艺和特殊的工件加工要求。
- 1、下载文档前请自行甄别文档内容的完整性,平台不提供额外的编辑、内容补充、找答案等附加服务。
- 2、"仅部分预览"的文档,不可在线预览部分如存在完整性等问题,可反馈申请退款(可完整预览的文档不适用该条件!)。
- 3、如文档侵犯您的权益,请联系客服反馈,我们会尽快为您处理(人工客服工作时间:9:00-18:30)。
提高铰孔质量的方法
【摘要】在机械加工中,铰孔是利用铰刀对已经用麻花钻头加工过的孔再进行精加工的一道工序,铰孔质量的优劣决定了工件的质量。
【关键词】铰削用量;铰削速度;铰孔操作
铰孔是利用铰刀对已经用麻花钻头加工过的孔再进行精加工的一道工序。
可加工圆柱形孔(用圆柱铰刀),也可加工圆锥形孔(用圆锥铰刀)由于铰刀的刀刃数量多(6~8个)导向性好,尺寸精度高及刚性好,可达到2~4级精度和▽6~▽9光洁度。
提高铰孔质量须注意以下几点:
1 铰削用量选择
1.1 铰削余量(直径余量)是否合适,对铰出孔的表面粗糙度和精度影响很大
铰孔余量太大孔铰不光,铰刀负荷过大容易磨损会使刀刃崩碎;铰孔余量太小,不能去掉上道工序留下的刀痕,也达不到要求的表面粗糙度。
铰刀直径小于6mm,铰削余量应在0.05~0.1mm;铰刀直径大于6~18mm,一次铰0.1~0.2mm,二次铰精铰0.1~0.15mm;铰刀直径大于18~30mm,一次铰0.2~0.3mm,二次精铰0.1~0.15mm;铰刀直径大于30~50mm,一次铰0.3~0.4mm,二次精铰
0.15~0.25mm。
1.2 机铰铰削速度的选择
为了获得较小的加工表面粗糙度,避免产生积屑瘤,减少切削热及变形,应取较小的切削速度。
用高速钢铰刀:铰钢件时,转速4~8m/min;铰铸件时,转速6~8m/min;铰铜件时8~12m/min。
1.3 机铰进给量的选择
钢件及铸件0.5~1mm/转,铜铝1~1.2 mm/转。
2 铰孔操作方法
2.1 用手用铰刀铰孔时,可用右手通过铰孔轴线施加进刀压力,左手转动。
正常铰孔时,两手用在铰杠上的力要均匀、平稳地旋转,不能有侧向压力,同时适当加压,使铰刀均匀的进给,以保证铰刀正确引进和获得较小的加工表面粗糙度,并避免孔口成喇叭形或将孔径扩大。
2.2 铰孔和退出铰刀时,铰刀均不能反转,铰刀退出后再停车,防止刃口磨钝及切屑嵌入刀具后面与孔壁间划伤孔壁。
2.3 铰尺寸较小的圆锥孔,应先按小端直径并留取圆柱孔精铰余量钻出圆柱孔,再用锥铰刀铰削。
孔径和深度较大的锥孔,为减小铰削余量,先钻出阶梯孔,再用锥铰刀铰。
铰定位圆锥销孔时,因锥度小有自锁性,进给量不能太大,以免铰刀卡死或折断。
锥孔在铰削过程中要用相配的锥销试配检验以达到正确的配合尺寸要求。
2.4 机铰、手铰及铰锥孔,孔口要进行0.5~1mm×45°倒角。
可使铰刀铰孔时容易切入,避免孔口出现毛刺。
机铰时,工件放在平口钳上,平口钳用压板螺丝固定在钻床工作台面上,被铰工件不要装夹牢固,与平口钳钳口要有微小的缝隙,铰刀从钻头入口处开始铰,以保证铰刀中心线与钻孔中心线一致。
3 铰削时的切削液
选用合适的切削液来减小摩擦并降低刀具和工件的温度,防止产生积屑瘤并
减少切屑细末粘附在铰刀刀刃上、孔壁和铰刀的刃带之间,影响孔的表面粗糙度。
工件材料为钢件,铰孔时采用10~20%乳化液或工业植物油;材料为铸铁,铰孔时采用煤油(会引起孔径微量缩小)或用3~5%乳化液,或者不用任何切削液;材料为铝,用煤油或5~8%乳化液;材料为铜,铰孔时采用5~8%乳化液。
【参考文献】
[1]北京第一通用机械厂,编.机械工人切削手册[Z].
[2]钳工技能训练[Z].。