注塑工艺及缺陷案例分析(新版)
注塑工艺 注塑成型缺陷分析及不良解决对策
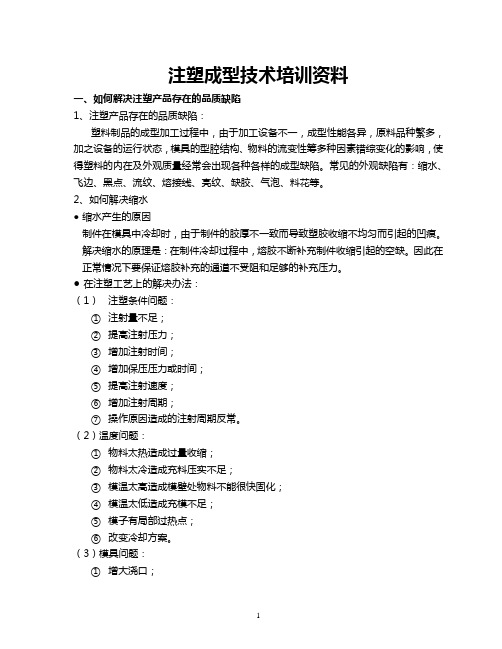
注塑成型技术培训资料一、如何解决注塑产品存在的品质缺陷1、注塑产品存在的品质缺陷:塑料制品的成型加工过程中,由于加工设备不一,成型性能各异,原料品种繁多,加之设备的运行状态,模具的型腔结构、物料的流变性筹多种因素错综变化的影响,使得塑料的内在及外观质量经常会出现各种各样的成型缺陷。
常见的外观缺陷有:缩水、飞边、黑点、流纹、熔接线、亮纹、缺胶、气泡、料花等。
2、如何解决缩水●缩水产生的原因制件在模具中冷却时,由于制件的胶厚不一致而导致塑胶收缩不均匀而引起的凹痕。
解决缩水的原理是:在制件冷却过程中,熔胶不断补充制件收缩引起的空缺。
因此在正常情况下要保证熔胶补充的通道不受阻和足够的补充压力。
●在注塑工艺上的解决办法:(1)注塑条件问题:①注射量不足;②提高注射压力;③增加注射时间;④增加保压压力或时间;⑤提高注射速度;⑥增加注射周期;⑦操作原因造成的注射周期反常。
(2)温度问题:①物料太热造成过量收缩;②物料太冷造成充料压实不足;③模温太高造成模壁处物料不能很快固化;④模温太低造成充模不足;⑤模子有局部过热点;⑥改变冷却方案。
(3)模具问题:①增大浇口;②增大分流道;③增大主流道;④增大喷嘴孔;⑤改进模子排气;⑥平衡充模速率;⑦避免充模料流中断;⑧浇口进料安排在制品厚壁部位;⑨如果有可能,减少制品壁厚差异;⑩模子造成的注射周期反常。
(4)设备问题:①增大注压机的塑化容量;②使注射周期正常;(5)冷却条件问题:①部件在模内冷却过长,避免由外往里收缩,缩短模子冷却时间;②将制件在热水中冷却。
3、如何解决飞边●产生飞边的原因:产品溢边往往由于模子的缺陷造成,其他原因有:注射力大于锁模力、物料温度太高、排气不足、加料过量、模子上沾有异物等。
●如何判断产生飞边的原因:在一般情况下,采用短射的办法。
即在注塑压力速度较低、不用保压的情况下注塑出制件90%的样板,检查样板是否出现飞边,如果出现,则是模具没有配好或注塑机的锁模压力不足,如果没有出现,则是由于注塑条件变化而引起的飞边,比如:保压太大、注射速度太快等。
注塑工艺及常见缺陷分析

响
流动性
螺杆
烘料时间 冷却时间
压力
因
压缩比 长径比
射嘴
射压 保压
素
鱼
成型缺陷
骨
加强筋
纹面
图
排气系统
脱模斜度
形式
型腔系统 大小
R角
温差 分布
顶出系统
流程
冷却系统
平衡性 位置
壁厚
流量
介质
位置 大小
形式 平衡性
流道系统
产品结构 注塑工艺及常见缺陷分析模具
浇口
注塑件缺陷原因及对策
缺陷处理步骤
定义 Define
改善对策:注塑参数调整,提高射速射压、保压,升高料 温;模具改善。
现象:产品翘曲
原因:产品结构问题;注塑前后模温差导致,保压太大, 保压时间长,冷却时间短;顶出不均匀造成;
改善对策:注塑参数调整,调整前后模温,降低保压及时 间,延长冷却时间;
注塑工艺及常见缺陷分析
批峰
批峰(毛边) +短射(缺胶) 短射
c.流痕
d.燒膠
射膠的壓力不夠
保壓不夠
塑膠的乾燥不夠
模具排氣不好
模具排氣不好
射膠壓力不夠
膠料流動性不夠
射膠速度太快
塑膠的流動性不好
產品壁厚不均勻
模溫或膠料溫度 過低
前後模溫差 射膠壓力太高 冷卻時間太短
模具配合不緊
膠料有異物,結 合不良
頂出太快
塑膠流動性太好
模具頂出結構不 良
頂出結構不良
鎖模力不足
射膠及頂出速度 太快
原因:注塑射速射压偏高;保压及保压时间偏高;模具脱 模角度不够,转角处强度不够;顶针设置不对;
图文解说最常见的11例注塑成型缺陷
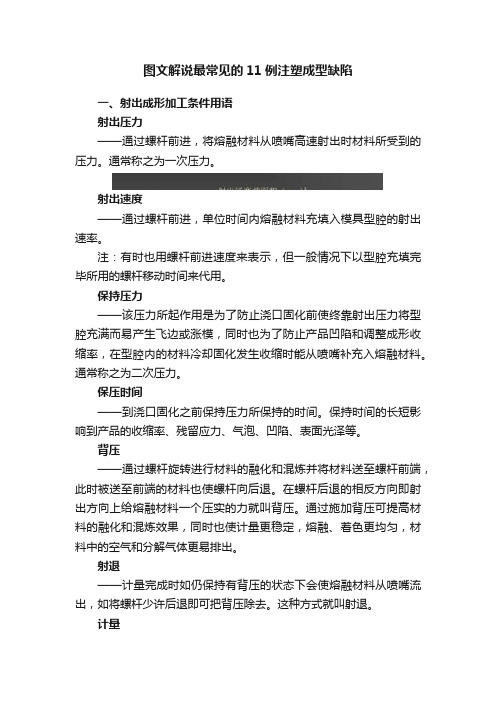
图文解说最常见的11例注塑成型缺陷一、射出成形加工条件用语射出压力——通过螺杆前进,将熔融材料从喷嘴高速射出时材料所受到的压力。
通常称之为一次压力。
射出速度——通过螺杆前进,单位时间内熔融材料充填入模具型腔的射出速率。
注:有时也用螺杆前进速度来表示,但一般情况下以型腔充填完毕所用的螺杆移动时间来代用。
保持压力——该压力所起作用是为了防止浇口固化前使终靠射出压力将型腔充满而易产生飞边或涨模,同时也为了防止产品凹陷和调整成形收缩率,在型腔内的材料冷却固化发生收缩时能从喷嘴补充入熔融材料。
通常称之为二次压力。
保压时间——到浇口固化之前保持压力所保持的时间。
保持时间的长短影响到产品的收缩率、残留应力、气泡、凹陷、表面光泽等。
背压——通过螺杆旋转进行材料的融化和混炼并将材料送至螺杆前端,此时被送至前端的材料也使螺杆向后退。
在螺杆后退的相反方向即射出方向上给熔融材料一个压实的力就叫背压。
通过施加背压可提高材料的融化和混炼效果,同时也使计量更稳定,熔融、着色更均匀,材料中的空气和分解气体更易排出。
射退——计量完成时如仍保持有背压的状态下会使熔融材料从喷嘴流出,如将螺杆少许后退即可把背压除去。
这种方式就叫射退。
计量——射出保压时螺杆前进把材料充满型腔并留有2~5mm的螺杆行程位置(残量)的储料设定量。
如果射出时螺杆位置押到零则会使型腔内的材料冷却固化发生收缩时不能从喷嘴补充入熔融材料而使保压不起作用。
螺杆回转数——单位时间内螺杆回转储料的转数。
螺杆回转的快慢影响到计量储料时间,计量应在冷却时间内完成,如超过冷却时间则要加快回转数。
保压切换——射出压力向保压切换时的时间(螺杆位置)对于成形条件是非常重要的。
通常以充入型腔材料的90~95%作为切换点。
二、射出成形不良原因和对策1. 充填不足--树脂未完全充满型腔使制品有缺损的现象。
[1] 成形品的体积过大i)要使用成形能力大的成形机。
ii)使用成形多腔模具时,关闭部分型腔。
产品缺陷案例分析-产品成型变形.翘曲原因分析

注塑产品成型缺陷分析——产品成型变形,翘曲分析
A.图例
产品变形翘曲偏大
如上图所示,制件变形翘曲约5mm,该产品为汽车立柱,
变形翘曲偏大严重影响组装,达不到客户品质标准,客户确
认不合格质
B.材料主要工艺参数
名称:大众汽车内饰立柱
材料:PP-H1323
模具温度:65℃
成型温度:200-225℃
C..可能原因分析及改善措施
1.模具顶出数量,面积,斜销脱模角度偏大或偏小,导致制件脱模不顺
2.成型工艺条件设定不当,保压偏大或偏小,引起制件残余应力导致制件变形翘曲
3.冷却方法不合适,导致冷却效果不均匀或冷却时间不足时,模具冷却水循环不顺畅,杜塞不通,导致模具温度偏高
D.改善关键控制点.
1.模具冷却水路调整,之前模具前模接模温65℃,且前模两组水路不通畅,将前模模温更改为常温水,控制前模模温偏高导致制件收缩产生的变形
3.成型工艺优化调整,保压压力由之前压力80降低到60.降低保压偏大,导致制件变形产生,产品外观确认合格
3.改善效果:
产品变形改善合格
模具水路不顺畅调整,前模模温调整为常温水,优化成型工
艺后,产品变形翘曲改善,产品变形翘曲检具检测在标准范
围内,客户确认合格!
4.关键点:模具模温是导致此产品变形翘曲主要原因。
注塑工艺及常见缺陷分析 (2)PPT课件

QC
注塑件缺陷种类
注塑件常见缺陷种类
防微杜渐 先生产之忧而忧
• • • • • • • • • • • • •
★★★★★★★★★★★★★
缩变批短黑结烧气料皱蛇顶气
水形峰射点合伤纹花纹纹白泡
(((((线((((((
缩翘毛缺异(烧气气波冷顶
孔曲边胶色熔焦痕花纹料凸
)))))接))))凹)
改善对策:注塑参数调整,调整前后模温,降低保压 及时间,延长冷却时间;
版权:刘新明 请勿转载
QC
批峰
批峰(毛边) +短射(缺胶)
短射
防微杜渐 先生产之忧而忧
现象:批峰,毛边,毛刺,易出现在分型面,镶件位 置,结合线位置,行位夹线位置;
原因:注塑射速射压偏高,保压、背压偏高,料温偏 高;锁模力不足;模具有间隙;
防微杜渐 先生产之忧而忧
版权:刘新明 请勿转载
QC
916注塑件主要缺陷
顶部小孔溢胶
防微杜渐 先生产之忧而忧
版权:刘新明 请勿转载
QC
916注塑件主要缺陷
现象:USB孔、侧壁缺胶 因素: 1,切割缺陷(USB孔位置) 2,注塑参数缺陷 对策:报废;切割改善,调机改善
防微杜渐 先生产之忧而忧
版权:刘新明 请勿转载
QC
916注塑件主要缺陷
916模内注塑工艺
通过将切割后的凯夫拉素材放入模具内注塑成形
白色区域为凯夫拉素材,绿色区域为塑胶部分
防微杜渐 先生产之忧而忧
版权:刘新明 请勿转载
QC
916注塑件主要缺陷
916模内注塑缺陷影响因素
工艺新型
防微杜渐 先生产之忧而忧
产品设计
产品缺陷案例分析-材料分解、断料头
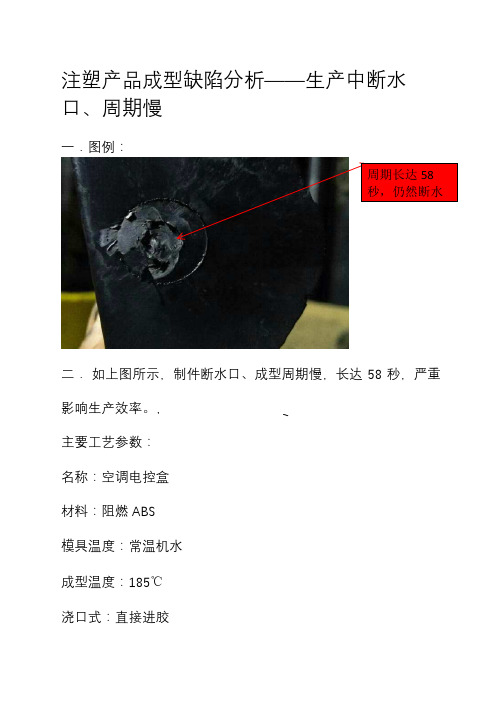
注塑产品成型缺陷分析——生产中断水口、周期慢
一.图例:
二. 如上图所示,制件断水口、成型周期慢,长达58秒,严重影响生产效率。
,
主要工艺参数:
名称:空调电控盒
材料:阻燃ABS
模具温度:常温机水
成型温度:185℃
浇口式:直接进胶
三.可能原用分析及改善措施:
A. 模具方面:制件在脱模中断水口主要原因是模具浇口灌嘴R 角偏小,水口偏长,灌嘴内壁不够光滑造成;
B. 工艺方面:主要存在水口位模具冷却不够,保压太大太长,模具灌嘴与机台射嘴偏差造成;
C.对模具灌嘴进行抛光处理,使水口脱模阻力减小,将水口位水路单接,使模温降低水口处冷却充分,减短冷却时间;
射嘴抛光前后对比
四:改善后效果
通过对水路进行整改,前模温度得到有效降低,水口位得到充分冷却,并对模具灌嘴抛光处理,水口脱模阻力得到有效减小,原来冷却时间38秒减短为20秒,成型周期缩短18秒,制件尺寸及外观合格,产品稳定生产。
五:关键点
制件断水口的关键点是:模具灌嘴要光滑,减小脱模阻力;水口位要充分冷却散热到位;。
产品缺陷案例分析-汽车增压器缩水,拉模
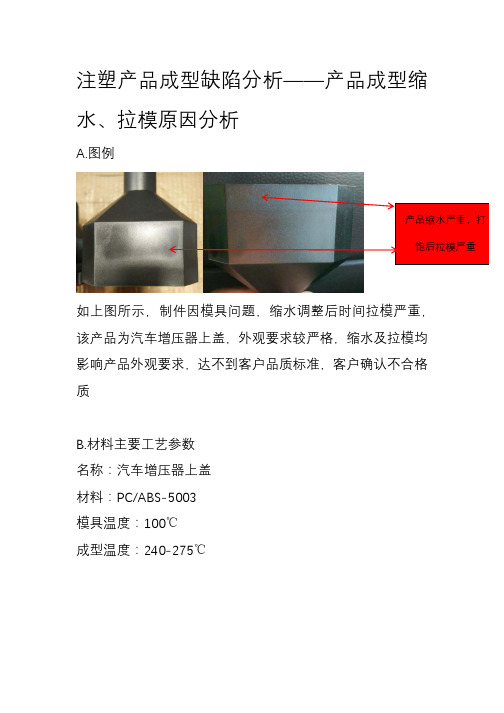
注塑产品成型缺陷分析——产品成型缩水、拉模原因分析
A.图例
如上图所示,制件因模具问题,缩水调整后时间拉模严重,该产品为汽车增压器上盖,外观要求较严格,缩水及拉模均影响产品外观要求,达不到客户品质标准,客户确认不合格质
B.材料主要工艺参数
名称:汽车增压器上盖
材料:PC/ABS-‐5003
模具温度:100℃
成型温度:240-‐275℃
产品缩水严重,打
饱后拉模严重
C..可能原用分析及改善措施
1..该制件边缘壁厚2mm,中间部位直接跳跃至5mm,模具脱模角度偏小,脱模角度约0.5,模具接触面粗糙抛光效果不良,模具温度设定偏高,前模温度设定100℃
2因制件壁厚较厚,且壁厚偏差较大,注塑工艺设定不当,注塑时间13秒,注塑时间偏长,材料至模具型腔已冷却,保压基本无作用
D.改善关键控制点.
1.针对模具进行调整,对模具增加脱模角度由0.5增加至1.5,对模具接触面进行抛光处理,模具温度重新调整,前后模同时接模温,前模80℃后模50℃
3.成型工艺优化调整,降低注塑时间、采用短注塑时间,由13秒降低至3秒,逐步加中后段保压压力,前段低压短时间,中后段保压长时间高压力,拉模现象调整合格,缩水改善合格,产品外观确认合格
4.改善后效果
模具脱模角度增加,优化成型工艺后,产品缩水、拉模改善,客户确认合格!
4.关键点:模具脱模角度是导致拉模主要原因
当前⽆无法显⽰示该图像。
注塑成型类的产品常见的不良的分析案例【范本模板】

注塑成型不良的案例分析一、飞边(披锋)系指从模具分型面拼出熔融树脂的现象,在成形作业当中属于最恶劣的情况,特别是当飞边粘在模具面上,残留下来,直接锁模的话,则损伤模具分型面。
一旦出现这种情况,该损伤部分又会导致产生新的飞边,怎么也没办法,所以需特别注意不要出现飞边,1、不得施加过高的射出压力熔融粘度低的树脂,如尼龙、聚丙烯、聚乙烯、聚苯乙烯等,流动性好,往往从模具缝隙出现“边缘鼓出”现象,因此,不得施加过高的射出压力和保压压力。
当有出现飞边的倾向时,应尽早让保压转换用限位开关动作,减少计量.降低射出压力.另外,保压压力也有过高的时候,对于这些流动好的树脂,不要从一开始就施加高保压压力.应边观察成形品的状况,边一点一点提高压力。
2、最初锁模力不足时,当然会产生飞边,不了解所用模具所需锁模力究竟有多大,就不可能作出断。
先利用锁模力调整手柄,增加锁模力试试看。
上图为在模具接触面(分型面)形成的飞边。
飞边主要是发生在分型面,但其它如在小顶杆周围、抽芯周围有时也出现飞边.所谓纵向飞边,几乎均起因于模具精度不够。
象尼龙之类熔融粘度低的树脂,特别容易产生飞边,如聚碳酸酯之类粘度高的树脂则难于产生飞边。
以最大锁模力锁模,仍然出现飞边时,则应考虑是否是机械能力不足.此时的判断方法是,当模腔内的压力乘以模腔、流道的投影面积所得的数值未超过机械是大锁模力的话,则不属于机械能力不足。
但需正确估计模腔内压力,然而不能把产品目录所列出的射出压力看作是模腔压力。
射出压力充其量是料筒内的理论压力,树脂流入模具,即被冷却,压力急剧下降.平均压力从低粘度部件250kg/cm2到高粘度工业部件800kg/cm2左右,这种压力很难估计,虽然大体上有个基准,但要想保证估计精度,还需要凭经验。
3、在模具接触面产生了伤痕、夹有脏东西或是模具平行度差,当然会产生飞边,模具保管不善,则会使安装面打上伤痕,或是生锈,这样都会导致产生飞边。
所以应该养成习惯妥善保管模具。
- 1、下载文档前请自行甄别文档内容的完整性,平台不提供额外的编辑、内容补充、找答案等附加服务。
- 2、"仅部分预览"的文档,不可在线预览部分如存在完整性等问题,可反馈申请退款(可完整预览的文档不适用该条件!)。
- 3、如文档侵犯您的权益,请联系客服反馈,我们会尽快为您处理(人工客服工作时间:9:00-18:30)。
28
谢谢!
29
产生原因: 1、注射压力、速度低 2、料量不够 3、料温、模温低
4、设备能力不足
5、射嘴对中性差(漏料) 6、止逆阀磨损,损坏
7、模具排气不良
8、模具热流道加热故障 9、模具热流道漏胶
10、原料流动性差
11
2、飞边
产生原因: 1、注射压力、速度大 2、料量太多 3、料温、模温高 4、锁模力小 5、机台模板不平行 6、模具分模面磨损变形产生间隙 7、原料熔融指数太高
5
原材料介绍
PP:用于IP、DP皮纹骨架骨架、立柱、保险杠基材。 ABS:用于散热器格栅、门板扶手等、中控面板。 PC、PC+ABS:门把手等。 PVC:脚踏垫、门板嵌饰板及上装饰板复合。 PA:门板卡子。 PP+GF:IP骨架。 PA+GF:IP骨架。
6
典型注塑缺陷种类
1、缺料 7、烧焦 13、色纹
23
14、 塑丝
产生原因: 1、料温高、模温高 2、冷却时间短 3、背压高、松退小 4、汤口直径大 5、材料流动性太好
24
15、 杂质
产生原因:
1、加料系统清洁不干净
2、材料污染
3、原材料添加物混合不均
25
16、 产品变形
产生原因:
1、注射压力低、速度慢 2、保压压力低、时间短 3、料量不够 4、冷却时间太短 5、料温、热流道、模温高 6、模具顶出不平衡 7、材料收缩率达 8、产品结构加强筋设计不合理
21
12、虎皮纹
产生原因:
1、注射压力、速度低; 2、熔体加工温度(料筒、热流道、模温)低; 3、设备料筒加热圈故障; 4、模具热流道加热圈故障; 5、原材料融指低; 6、进浇口小; 7、产品肉厚设计太薄(影响熔体的流动);
22
13、色纹
产生原因: 1、材料混料 2、料筒清洁不干净 3、背压低 4、干燥筒清洁不干净
前言
在塑料制品注塑成型过程中,由于成型材料、成型模具、 注射机、辅助设备、成型环境等多种因素的影响,注塑制 品的内在及外观质量经常会出现各种各样的问题。
一般来说,制品成型质量主要包括:
1、制品外观; 2、制品尺寸精度; 3、制品的物理性能。 他们都与注射工艺条件密切相关。本次交流对一些典型 注射成型缺陷的成因进行了分析,并提出了相应的解决方 案。
12
3、缩瘪
产生原因:
1、注射压力、速度低、保压压力、速度低 2、储料量不够(背压小) 3、射胶时间短(时间转保压) 4、冷却时间短 5、料温(料筒、热流道)、模温高 6、模温机故障 7、螺杆计量不准 8、材料收缩率大 9、产品肉厚设计太厚
13
4、熔接痕
产生原因:
1、注射压力、速度低、保压压力、 速度低 2、料温(料筒、热流道)、模温低 3、顺序阀打开设置不当 4、浇口设置不当 5、模具排气不良 6、材料流动性差
26
17、 尺寸偏大
产生原因:
1、注射压力高、速度快 2、保压压力高、时间长 3、料量大 4、留模冷却时间太长 5、模具放缩量错误 6、材料加工温度低(收缩小) 7、材料收缩率小
27
18 、 尺寸偏小
产生原因:
1、注射压力低、速度慢 2、保压压力低、时间短 3、料量小 4、留模冷却时间短 5、模具放缩量错误 6、材料加工温度高(收缩大) 7、材料收缩率大
16
7、烧焦
产生原因:
1、注射压力高、速度快 2、料温、热流道、模温 高 3、锁模力大 4、模具排气不良 5、材料流动性好
17
8、冷料
产生原因: 1、料温太低 2、背压高、松退小 3、顺序阀开闭设置位置不 当 4、进浇口无冷料阱 5、材料流动性好
18
9、顶出发白(顶杆印)
产生原因:
1、注射压力高、速度快 2、保压压力高、时间长 3、料量大 4、模温低 5、顶出速度快 6、模具顶出不平衡 7、拔模斜度设计太小
14
5、流动痕(亮斑、气痕)
产生原因:
1、注射压力高、速度快、 2、料温(料筒、热流道)、模温高 3、顺序阀打开设置不当 4、模具排气不良 5、材料流动性太好
15
6、银丝
产生原因:
1、原料干燥温度低、干燥时间短 2、储料背压低 3、后松退位置大 4、料筒及热流道温度高造成原料分解 5、射胶速度快 6、模具排气不良 7、材料水分及低分子含量高
2、飞边
3、缩瘪 4、熔接痕
8、冷料
9、顶出发白 10、拉伤
14、杂质
15、塑丝 16、变形
5、流动痕(亮斑、气痕)
6、银丝
11、气泡
12、虎皮纹
17、尺寸偏大
18、尺寸偏小
7
各种缺陷原因分析及改 善方法
8
成型缺陷影响因素
产品结 构
成型缺陷影响因素
原材料
成型工艺
注塑机及周边设 备
模具
9
10
1、缺料
1
注塑成型工艺
合模 取件 注射(保压) 顶出 冷却(储料) 开模
2
注塑成型机结构介绍
射台: 料斗、料筒、螺杆
开合模系统: 曲肘、动定模板、机械顶 出装置
3
周边设备介绍
吸料机
干燥塔
模温机
气辅控制台
4
注塑模具结构介绍
动模 定模 顶板固定板 顶杆 导柱 斜滑块(斜导柱) 中子 热流道 水路
19
10、产品拉伤
产生原因:
1、注射压力高、速度快 2、保压压力高、时间长 3、料量大 4、模温低 5、开模一段速度过快 6、模具拔模斜度小 7、母模面皮纹太深 8、模具分型线磨损 9、材料收缩率小
20
11、气泡
产生原因:
1、注射压力高、速度快 2、材料加工温度高 3、原料干燥不充分 4、背压低、松退位置大 5、锁模力大 6、模具排气不良 7、材料低分子含量太高